Машина непрерывного литья заготовок
Северский трубный завод производит высококачественную круглую заготовку для изготовления труб, которая поставляется также для Синарского трубного завода (СинТЗ), входящего в состав ТМК. МНЛЗ позволяет повысить уровень экологической безопасности производства, повысить качество получаемой заготовки, снизить расход металла, энергозатраты и трудоемкость.
Пятиручьевая МНЛЗ радиального типа с базовым радиусом 12 м и разгибом непрерывного слитка в трех точках предназначена для отливки заготовок круглого сечения диаметром 150 мм, 156 мм, 400 мм. Производственная мощность МНЛЗ составляет 950 тыс. тонн заготовки в год.
Разливка плавок осуществляется в заготовку одинакового сечения одновременно на 5-ти ручьях и режется с помощью машин газовой резки на мерные длины:
- от 3,5м до 6м для круга 360, 400мм;
- от 6,5м до 12м для круга 150, 156 мм.
Рабочие скорости вытягивания заготовок 0,6 – 3,3 м/мин. и частота колебания кристаллизатора 50-300 циклов в минуту, амплитуда ± 1,0-6,0мм. зависят от диаметра отливаемой заготовки.
Разливка стали осуществляется с обязательным использованием защитной трубы и погружных стаканов (кварцевые или корундографитовые) для защиты металла от вторичного окисления. Также для защиты металла используется продувка аргоном.
После разливки заготовки режутся на мерные длины с помощью машин газовой резки (по одной на каждый ручей), маркируются двумя клеймовочными машинами и передаются на кантующий холодильник. После медленного охлаждения заготовки передаются на склад.
|
|
Описание системы газоочистки ДСП-135
Для обеспечения максимально возможного отвода образующихся пылесодержащих дымовых газов на всех технологических стадиях кожух печи оснащен прямым газоотсосом на своде печи и зонтом в крыше цеха.
Кроме того, отходящие газы собираются в бункерной установке и передаются на общую установку газоочистки.
Общая схема системы пылеулавливания представлена на рис. 4.1.
Рис. 4.1. Схема системы пылеулавливания: 1 – дуговая сталеплавильная печь; 2 – камера дожигания; 3 – водоохлаждаемый газоход; 4 – регулирующие клапаны; 5 – зонт под крышей; 6 – система транспортировки материалов; 7 – дымососы сушки скрапа; 8 – пылеуловитель; 9 – аварийный клапан; 10 – рукавный фильтр; 11 – венткамера; 12 – дымососы; 13 – жалюзийные заслонки; 14 – дымовая труба; 15 – точки отбора проб.
При прямом газоотсосе на своде печи горячие дымовые газы попадают через водоохлаждаемое колено трубопровода на печи в систему трубопроводов с водяным охлаждением, в которой они охлаждаются до температуры около 600 °С. Путем смешивания с газами из зонта под крышей цеха в смесительной колонне газы достигают необходимой входной температуры для очистки в тканевом фильтре.
|
|
Устройство контроля температуры предотвращает повреждения рукавов газами с температурой выше 130 °С.
4.1. Вытяжной трубопровод
Образующиеся во время расплавления отходящие газы отсасываются через четвертое отверстие в своде. Расстояние между закрепленным на своде печи коленом и расположенным перед камерой сгорания поворотным коленом выбрано таким образом, чтобы обеспечить возможность подсоса в систему необходимого для дожигания количества воздуха.
В водоохлаждаемой камере сгорания осуществляется дожиг отходящих газов. Водоохлаждаемые стенки камеры сгорания стоят на камере, облицованной огнеупорным материалом, в которой во время работы печи происходит отделение увлеченных потоком частиц шлака и крупных частиц пыли. Камера имеет большие ворота для выгрузки шлака и пыли с использованием фронтального погрузчика.
Вытяжной трубопровод после камеры сгорания имеет водяное охлаждение и выполнен в виде конструкции труба-к-трубе. Подсоединенный к нему неохлаждаемый трубопровод выполнен из теплостойкой стали.
|
|
Отсос на бункерной установке осуществляется с помощью дополнительной нагнетательной воздуходувки.
4.2. Смесительная колонна
В смесительную колонну подаются потоки отходящих газов различного состава и температуры и путем перемешивания доводятся до состояния, требуемого на входе в фильтр.
4.3. Всасывающий рукавный фильтр с очисткой сжатым воздухом
Тканевой фильтр выполнен в виде всасывающего фильтра, т.е. воздуходувки расположены за фильтром на стороне очищенных газов. Фильтр состоит из нескольких камер, расположенных в 2 ряда друг около друга. Между 4 рядами находится комбинированный канал неочищенных и очищенных газов.
Отдельные камеры фильтра запираются со стороны входа неочищенных газов и выхода очищенных газов для обеспечения возможности технического обслуживания во время эксплуатации. Каждая камера фильтра имеет два пылесборных бункера с ручными запорными заслонками.
Рукава фильтров выполнены из тяжелого нетканого полиэстрового полотна, опорные короба – секционные.
Очистка рукавов фильтра осуществляется при помощи ударной кратковременной подачи сжатого воздуха/азота через форсунки, расположенные поверх рядов рукавов. Во время этой операции прилипшая к рукавам пыль стряхивается и сбрасывается в пылесборный бункер камер фильтра.
|
|
4.4. Воздуходувная станция
Для гарантированного отсоса на всех стадиях технологического процесса на стороне очищенных газов тканевого фильтра установлены три воздуходувки достаточного размера, выталкивающие очищенные отходящие газы через дымовую трубу в атмосферу.
4.5. Уборка пыли/хранение
Собирающаяся в пылесборных бункерах тканевого фильтра пыль выносится при помощи цепного транспортера и транспортируется при помощи вертикального транспортера в пылесборный бункер.
Разгрузка пыли из бункера осуществляется при помощи ячейкового лопастного затвора в контейнер или в грузовики (силосные).
Библиографический список
1. «Технический каталог Трубной Металлургической компании», 85 стр.
2. «Теория процессов производства стали» - Явойский В.И., 1986, 271 стр.
3. «Внепечная обработка стали на установке печь-ковш» - технологическая инструкция. ТИ 162 – СТ. М – 15, 2004, 44 стр.
4. Руководство по эксплуатации и техническому обслуживанию печь-ковш. Технические данные. Металлургия: Сталеплавильные заводы, 1998, 620 стр.
5. Реконструкция сталеплавильного производства на Северском трубном заводе – Григорьев Ю.Г., Коковин В.Н., Глазырин Г.А.
6. Инструкция по технологии использования пятиручьевой установки для отливки круглых заготовок SMS DEMAG, 2005, 312 стр.
7. «Основы технологии производства стали» - Поволоцкий Д.Я., 2004, 202 стр.
8. Петер М. Вспенивание шлаков в процессе плавки в дуговой печи /М. Петер, К. Кох, Я. Ламут, М. Юхарт //Черные металлы, 2000. № 3. С. 26-33.
9. Дюдкин Д.А. Производство стали на агрегате ковш-печь /Д.А. Дюдкин, С.Ю. Бать, С.Е. Гринберг, С.Н. Маринцев – Донецк: ООО «Юго-Восток, ЛТД», 2003. 300 с.
10. Меркер Э.Э. Исследование переходной зоны шлак-металл в ванне дуговой печи на холодной модели /Э.Э. Меркер, А.А. Кожухов, А.И. Кочетов, В.В.Федина, А.А. Гришин //Известия ВУЗов. Чёрная металлургия, 2005. № 1. С. 24-26.
11. Борнацкий И.И. Производство стали /И.И. Борнацкий, В.Ф. Михневич, С.А. Яргин - М.: Металлургия, 1991. 400 с.
12. Шевцов Е.К. Механизм образования переходной зоны шлак – металл в жидкой мартеновской ванне /Е.К. Шевцов, B.C. Кочо, В.А. Ерошенко и др. //Известия ВУЗов. Чёрная металлургия, 1974. № 1. С. 42-46.
13. Борнацкий И.И. Теория металлургических процессов /И.И. Борнацкий – Киев-Донецк, Изд-во «Вища школа», 1978. 288 с.
14. Увеличение стойкости огнеупоров на ДСП фирмы PACIFIC STEEL //Новости чёрной металлургии за рубежом, 2005. № 1. С. 25-26.
15. Morales R.D. The slag foaming practice in EAF and its influence on the steelmaking shop productivity /R.D. Morales, F. Lopez, J. Camacho, J. Romero //ISIJ International, Vol. 35 (1995), № 9. Pp. 1054–1062.
16. Новиков В.К. Прогнозирование рафинирующих свойств многокомпонентных шлаковых расплавов /В.К. Новиков, В.Н. Невидимов //Известия ВУЗов. Чёрная металлургия, 1997. № 1. С. 5–10.
17. Новиков В.К. Полимерная природа расплавленных шлаков /В.К. Новиков, В.Н. Невидимов - Екатеринбург: ГОУ ВПО УГТУ-УПИ, 2006. 62 с.
Дата добавления: 2018-05-02; просмотров: 1030; Мы поможем в написании вашей работы! |
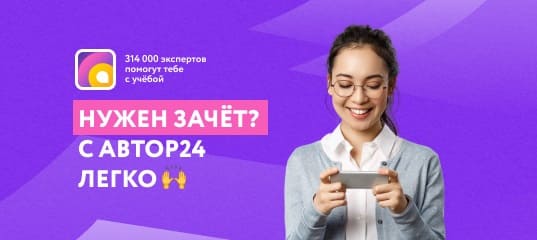
Мы поможем в написании ваших работ!