РЕКОМЕНДУЕМЫЕ УСЛОВИЯ УПРОЧНЕНИЯ
Глава 5. ТЕХНОЛОГИЧЕСКИЕ МЕТОДЫ ПОВЫШЕНИЯ ДОЛГОВЕЧНОСТИ ДЕТАЛЕЙ 5.1. КАЧЕСТВО ИСХОДНОГО МАТЕРИАЛА Прочность и эксплуатационные свойства деталей машин в значительной степени определяются факторами, связанными с процессом плавки и методом получения формы детали. При этом механические свойства стальных и чугунных деталей зависят не только от химического состава металла и последующей термообработки, но и от способа выплавки стали, структуры и свойств участка слитка, из которого изготовлена деталь. Известно, например, что так называемая кипящая сталь полному раскислению при выплавке не подвергается, слиток отличается значительным количеством газовых пузырей, образующихся в процессе затвердевания и при последующей горячей обработке - прокатке - газовые пузыри, расположенные недалеко от поверхности слитка, могут дать опасный поверхностный дефект волосовины. Особое влияние на служебные свойства отливок оказывают литейные напряжения, являющиеся результатом совместного действия температурных, усадочных и структурных факторов. Уменьшение прочности отливок под влиянием литейных напряжений часто имеет место у крупных литейных валов, плит и корпусов с тонкими ребрами, больших шкивов, маховиков и т.д.
Основными мероприятиями по борьбе с литейными напряжениями являются такие, как обеспечение равномерного охлаждения всех частей отливки (путем подвода питателей литников к тонким частям или установления холодильников в толстых частях), изготовление отливки из нескольких частей, высокотемпературный отпуск, нормализация и термическое улучшение (закалка и отпуск) - (табл. 5.1 для стали 35Л).
|
|
Таблица 5.1
ВЛИЯНИЕ ВИДОВ ТЕРМООБРАБОТКИ НА СВОЙСТВА СПЛАВОВ
Термическая обработка | sв, МН/м2 | sт, Н/м2 | d, % | y, % | ак, МДж/м2 |
Литой образец | 612 | 237 | 8,5 | 7,9 | 0,245 |
Отжиг при 950 °С | 543 | 267 | 22,6 | 38,1 | 0,578 |
Нормализация при 950 °С | 536 | 253 | 21,7 | 37,5 | 0,618 |
Улучшение (закалка с 850 °С и отпуск при 600 °С) | 667 | 451 | 22,0 | 54,0 | 1,03 |
Значительное влияние на механические свойства отливок оказывают различные присадки, вводимые непосредственно в жидкую сталь с целью улучшения (модификации) ее структуры. У стали 30Л, например, после модификации 0,2% Са предел прочности при разрыве повышается с 568 МН/м2 до 644 МН/м2, а относительное удлинение - с 17 до 22 %.
Для изготовления высоконапряженных зубчатых колес горных машин применяют в основном высокопрочные цементуемые стали 12ХНЗА, 25ХГТ, 18ХГТ, 20X2Н4А. Возможности существенного повышения прочности колес из этих сталей в значительной степени использованы. Это обусловлено недостаточной пластичностью и высокой чувствительностью этих сталей к концентрации напряжений, вызванной неметаллическими включениями.
|
|
Известно, что качество стали и сопротивление усталости деталей, при прочих равных условиях, обусловлены количеством неметаллических включений в слитке, пластичностью и анизотропией (различием в разных направлениях) механических свойств. Оптимальное сочетание этих факторов может быть достигнуто на основе применения современных металлургических процессов: электрошлакового (ЭШП) или вакуумного дугового переплава стали, рафинирования стали синтетическими шлаками (СШ), применение которых позволяет получить металл высокой чистоты, освободиться от вредных примесей. Стали, выплавленные этими методами, превосходят обычную сталь по плотности, пластичности и ударной вязкости. Испытания таких сталей показывают, что долговечность зубчатых колес из стали ЭШП в среднем в 7 раз, из стали СШ - в 5 раз превышает этот показатель для серийной стали 20Х2Н4А.
Для придания металлическому слитку желаемой формы применяется обработка давлением: прокатка, волочение, прессование, свободная ковка, горячая или холодная штамповка, выдавливание. С помощью этих способов из слитков получают листы, прутки, трубы, поковки, штамповки - заготовки для деталей. Пластическая деформация металла при этом изменяет их структуру и оказывает большое влияние на механические свойства деталей, происходит изменение макроструктуры и образование текстуры - определенной ориентации зерен на поверхности. Поэтому существует определенное правило, согласно которому расположение волокон должно в возможно большей степени повторять конфигурацию детали и не «перерезываться» стенками детали.
|
|
Так, зубчатые колеса получают правильную ориентировку (без перерезывания волокон) (рис. 5.1, 6) в том случае, если их изготовляют путем ковки осадкой в торец. Если это условие нарушается и волокна направлены поперек или вдоль зубьев (рис. 5.1, а), то они могут в эксплуатации отламываться вследствие расслоения между волокнами.
Рис. 5.1. Различное расположение волокон
Особенно благоприятное расположение волокон в ответственных деталях (шарошках бурильных долот, звездочках, в резьбовых соединениях буровых штанг и т.п.) достигается при горячей или холодной накатке зубьев, резьб, шлицев и т.п. (см. рис. 5.1, 6). У деталей типа валов, осей, штоков, шатунов, разрушающихся в результате циклических напряжений изгиба, кручения, сжатия-растяжения и т.д., оптимальным является расположение волокон вдоль направления максимальных растягивающих напряжений и одновременно под углом 45° к направлению максимальных касательных напряжений, т.е. вдоль оси вала.
|
|
Большое значение расположение волокон имеет для деталей, разрушающихся вследствие контактной усталости металла. Так, контактная усталостная прочность у роликов подшипников с продольным расположением волокон в 3-5 раз выше, чем у таких же роликов с поперечным (перпендикулярно оси) расположением волокон.
5.2. ВЛИЯНИЕ МЕХАНИЧЕСКОЙ ОБРАБОТКИ РЕЗАНИЕМ НА СВОЙСТВА ДЕТАЛИ
Опыт эксплуатации машин подтверждает, что основными факторами, определяющими долговечность машин, являются не только механические свойства материала, из которого изготовлены детали, но и качество поверхностного слоя (см. гл. 4, § 4). В процессе механической обработки со снятием стружки происходят физические процессы, которые существенно изменяют свойства поверхностного слоя. Качество поверхностного слоя детали может характеризоваться геометрическими факторами и физико-механическими свойствами. К геометрическим факторам относятся: макрогеометрия, волнистость и шероховатость, направление штрихов; к физико-механическим - твердость, тонкая кристаллическая структура, наклеп, остаточные напряжения. Причинами появления неровностей на поверхности обрабатываемой детали являются: неравномерность самого процесса резания, дисбаланс вращающихся элементов (деталь, патрон и т.п.), копирование неровностей на режущей кромке инструмента и ее движения, оставляющие на поверхности остаточные гребешки, и др.
Геометрические параметры, образующиеся после срезания стружки, оказывают большое влияние на износостойкость, выносливость, сопротивление ударным нагрузкам, коррозионную усталость. Впадины микронеровностей являются концентраторами напряжений, причем тем больше, чем глубже впадина t и меньше ее радиус r:
, где a - коэффициент концентрации напряжения для процессов механической обработки составляет 1,5¸2,5 . На рис. 5.2 показано влияние величины шероховатости и направления штрихов на износ. С увеличением волнистости эксплуатационные свойства сопряженных деталей ухудшаются, так как площадь прилегания поверхностей друг к другу уменьшается, увеличиваются контактные напряжения.
Влияние геометрических параметров на усталостную прочность деталей машин особо ощутимо для высококачественных сталей. Чем прочнее материал, тем больше сказывается вредное влияние шероховатости на предел выносливости (рис. 5.3).
Однако фактор шероховатости не всегда оказывает преобладающее влияние на предел выносливости детали. Так, дробеструйная обработка детали (см. рис. 5.3, кривая 4), не улучшая чистоту, существенно повышает предел выносливости. Это объясняется появлением при дробеструйной обработке наклепа поверхностного слоя, при котором твердость металла в наружных слоях может повыситься в 1,5 раза. При механической обработке в процессе срезания стружки также может создаваться наклепанный слой глубиной до 0,5мм, который может влиять на усталостную прочность детали (рис. 5.4), т.е., управляя процессом резания, можно влиять и на прочность обработанной детали. Как видно из рис. 5.4, с величины переднего угла g=-30° фактор шероховатости уже не влияет на предел выносливости. Таким образом, в некоторых случаях отпадает необходимость в чистовых отделочных процессах.
Например, грубо обработанные точением торсионные валики дают в два раза пониженную усталостную прочность по сравнению с полированными. Обточка этих валиков резцом с g=- 30° привела к тому, что их прочность стала выше прочности полированных валиков.
Анализ напряженного состояния металла впереди резца дает возможность установить, что в поверхностном слое обработанной поверхности, в зави симости от направления силы резания, могут образовываться как сжимающие, так и растягивающие остаточные напряжения (рис. 5.5). Если остаточные напряжения сжатия, складываясь с опасными растягивающими рабочими напряжениями (рис. 4.7), понижают их и за счет этого повышают усталостную прочность валов, например, в 2-3 раза, то остаточные напряжения растяжения могут привести к преждевременному отказу детали.
Действие остаточных напряжений следует рассматривать совместно с наклепом, так как эти два явления неразрывно сопутствуют один другому.
Рассматривая процесс резания как процесс, влияющий на качество поверхностного слоя, создающий определенные физико-механические свойства этого слоя, необходимо представлять, что процесс резания изменяет свойства тонкого поверхностного слоя от 0,05 до 0,25 мм. Такие слои могут влиять на ограниченную номенклатуру некрупных деталей с особыми требованиями к качеству поверхностного слоя. Для крупных деталей, когда требуется упрочнить поверхностный слой 0,5¸5 мм, разработаны и применяются специальные методы упрочнения, которые описаны ниже.
Рис. 5.5. Влияние геометрии резца: sсж, sраст – остаточные напряжения сжатия и растяжения соответственно, h – расстояние от поверхности в глубь детали
5.3 ТЕРМИЧЕСКАЯ ОБРАБОТКА ДЕТАЛЕЙ
Термическая обработка металлов и сплавов - один из самых эффективных и распространенных методов улучшения их свойств. В основе процессов термической обработки лежит явление полиморфизма - существования одного и того же металла в различных кристаллических формах. Полиморфные превращения происходят, как правило, при нагреве или охлаждении до определенных температур (так называемых критических точек) и вызывают образование структур с теми или иными свойствами. Изменяя температуру нагрева (или охлаждения), выдержку при этой температуре и скорость последующего охлаждения, можно либо приблизиться к равновесному структурному состоянию, либо зафиксировать соответствующие метастабильные структуры.
Механические характеристики неупрочненных металлических материалов настолько далеки от требований современного машиностроения, а эффективность упрочнений настолько велика, что все детали, подчиненные критериям прочности и износа, должны упрочняться. Как метод упрочнения наиболее широкое распространение в практике получила закалка в сочетании с отпуском для снятия остаточных закалочных напряжений и приведения структуры металла в равновесное состояние. Закалка повышает прочность углеродистых сталей в 1,5-2 раза. Существует объемная закалка деталей, при которой термической обработке (закалке и отпуску) подвергается весь объем металла детали, и поверхностная закалка, при которой термической обработке подвергаются отдельные элементы (зубья шестерен, шлицы и т.п.) или поверхностные слои (шейки валов, зубьев крупных шестерен и т.п.). Объемной закалке подвергаются некрупные детали, равномерно нагруженные, сравнительно простые по конфигурации. Для уменьшения закалочных напряжений в деталях, которые могут привести к появлению закалочных трещин, применяются специальные способы закалки (рис. 5.6): прерывистая (кривая 2), ступенчатая (кривая 3), изотермическая (кривая 4), закалка с подстуживанием (кривая 5).
Рис. 5.6. Варианты охлаждения при закалке стали:
1 - обычная, 2 - прерывистая, 3 - ступенчатая, 4 - изотермическая,
5 - подстуживание, 6 - высокотемпературная обработка, 7 - низкотемпературная термомеханическая обработка
Конечным процессом термической обработки является отпуск. Различают низкий отпуск (150-200°), средний (300-450°) и высокий (500-650°). Низкий отпуск обеспечивает максимальную твердость в поверхностном слое (HRc 59-63) и применяется для деталей, от которых требуется высокая износостойкость (подшипники, зубчатые колёса, пальцы, рабочий инструмент и др.). При среднем отпуске достигается твердость НRс 44-54, он применяется для деталей, которые наряду с высокой прочностью и упругостью должны обладать достаточной вязкостью (рессоро-пружинные стали, звездочки и др.) Высокому отпуску подвергают главным образом детали, работающие при знакопеременных нагрузках (валы, шатуны и др.).
Для крупных деталей, когда необходимо закалить отдельные быстроизнашивающиеся или особо нагруженные элементы, при необходимости сохранить вязкую сердцевину элемента, применяют поверхностную закалку с нагревом поверхности газовым пламенем или токами высокой (или промышленной) частоты.
Поверхностной закалке с нагревом газовым пламенем подвергаются детали из средне- и высокоуглеродистых сталей и чугунов (серого, модифицированного, легированного и ковкого, в которых содержание связанного углерода находится в пределах 0,4-0,85 %). Детали нагревают специальными горелками до закалочной температуры на глубину 1-6мм и быстро охлаждают. Этот способ закалки наиболее эффективен и целесообразен при местном упрочнении главным образом крупных деталей в индивидуальном и мелкосерийном производстве. К преимуществам этого метода относится простота оборудования и легкость выполнения операции закалки.
Выполнение этой операции может производиться непрерывным или циклическим методом. При циклическом методе можно производить закалку цилиндрических деталей: шеек коленчатых валов, роликов и шестерен небольшого диаметра, шеек крупных валов, зубьев крупных колес с m>24 и плоских деталей больших размеров: листов погрузочных машин и ковшей экскаваторов, направляющих элементов станин горных машин и т.п. Часто такую закалку можно осуществить на месте сборки машины.
При термической обработке деталей с применением нагрева токами высокой и промышленной частоты цикл ее значительно сокращается. Процесс приспособлен для автоматизации, управления и контроля параметров, поверхностный закаленный слой получается более твердым, чем при закалке с нагревом в печи или газовыми горелками.
По условиям нагрева различают одновременный метод закалки, когда индуктор охватывает всю нагреваемую поверхность, и непрерывно-последовательную закалку, когда в процессе нагрева деталь и индуктор все время перемещаются относительно друг друга. Одновременный метод применяют, как правило, для закалки мелких деталей и деталей с небольшой поверхностью (звездочек, зубчатых колес небольшого модуля и т.п.), непрерывно-последовательный - для закалки длинных и тонких деталей (валов, осей, штанг и т.п.) или крупных деталей (для колес с m>6). Применение упрочнения трубных буровых штанг с нагревом ТВЧ обоих концов заготовки на специальной полуавтоматической установке обеспечивает высокую производительность (35 штанг в час) и повышает эксплуатационную стойкость штанг в 4-4,5 раза. Закалка с нагревом ТВЧ успешно используется для упрочнения внутренних поверхностей отверстий (в т.ч. глубоких отверстий более 11 мм). Внутренние поверхности цилиндров закаливают в воде отпусканием индуктора внутрь с зазором »1мм. При включении индуктора вода между индуктором и стенкой детали быстро испаряется, а стенка нагревается до температуры закалки. При выключении тока или продвижении индуктора вдоль оси вода заливает и закаливает нагретую поверхность.
На Уралмашзаводе для непрерывно-последовательной закалки валов и валов-шестерен длиной до 6000 мм, при закаливаемой части до 3100 мм, диаметром до 800 мм, весом до 10 т изготовлен специальный станок, снабженный гидравлическим приводом для движения индуктора со скоростью до 20 мм/сек. Изготовлен также станок для закалки зубчатых колес с модулем 10-500 мм, диаметром 300-5000 мм, весом до 15 т. Разработан и внедрен полуавтомат для поверхностного упрочнения глубинно-насосных штанг, на котором можно упрочнять детали до 8 м и диаметром до 300 мм. Создана установка для последовательной закалки валов и корпусов турбодувов диаметром 100-265 мм и длиной до 12 м, шестипозиционный полуавтомат для упрочнения деталей замков и приводных концов к бурильным трубам, на котором могут обрабатываться детали диаметром 140-215 мм, длиной до 500 мм при производительности 8-10 деталей в час.
В последние годы появился метод термической обработки (термомеханическое упрочнение), совмещающий преимущества упрочнения пластической деформацией металла с термическим упрочнением - закалкой. Прочность легированных сталей при этом может быть повышена в 5-6 раз. Характерно большое внимание к этому упрочнению в США. При этом может применяться пластическая деформация при высокой температуре - ВТМО[1] - для углеродистых и легированных сталей (см. рис. 5.6, кривая 6) и низкотемпературная пластическая деформация с термоупрочнением (см, рис. 5.6, кривая 7). В первом случае трудностью является проведение пластической деформации (на прессе) заготовки, нагретой до высокой температуры. А второй способ применим только для легированных сталей при устойчивом аустените. И тот и другой способы пока применяются для деталей простой формы (лента, пластины, трубки и т.п.), но практика показывает, что при этом долговечность детали повышается в 2,5-3 раза по сравнению с закалкой ТВЧ.
К термическому упрочнению деталей относится и химико-термическая
обработка, которая в результате совместного действия температуры и актив
ной внешней среды позволяет изменять химический состав поверхностных
слоев металла с целью повышения служебных свойств деталей машин. В основе химико-термической обработки поверхностей деталей лежит способность поверхностного слоя изменять свойства при насыщении углеродом, азотом, бором, кремнием, хромом и другими элементами. Азотирование (насыщение азотом) обеспечивает особо высокую поверхностную твердость, износостойкость и сопротивление заеданиям, а также значительное повышение прочности (особенно при больших общих циклах нагружений), но чувствительна к ударным нагрузкам. Зубья шестерен после азотирования в связи с минимальным короблением после этой обработки можно не шлифовать, что способствует применению азотирования для колес с внутренними зубьями и других, для которых шлифование трудно осуществимо. Наибольшее применение этот метод получил для упрочнения поверхностей деталей машин, работающих в условиях трения и знакопеременных нагрузок изгиба (шейки валов, седла клапанов, толкатели двигателей внутреннего сгорания, шестерни, гильзы цилиндров, трущиеся пазы насосов и компрессоров). Так, азотирование рабочих поверхностей втулок грязевых насосов в 4 раза повышает их стойкость.
Существуют и другие методы химико-термической обработки деталей: борирование - создающее тонкий слой высокой твердости, цианирование и нитроцементация - насыщение углеродом и азотом, силицирование - насыщение кремнием для повышения коррозионной стойкости, сульфидирование - насыщение серой для предотвращения задиров и как способ ускорения приработки, сульфоцианирование - для деталей, у которых затруднена смазка. Все эти методы предназначены для повышения срока службы деталей, что замедляет старение машин.
5.4. УПРОЧНЕНИЕ ПОВЕРХНОСТНОГО СЛОЯ НАКЛЕПОМ
Значительный эффект повышения долговечности деталей, работающих в условиях циклических нагрузок и имеющих концентраторы напряжений, места прессовых посадок, а также работающих в коррозионных средах, достигается за счет поверхностного наклепа, получающегося в результате пластической деформации поверхностных слоев деталей. Пластическая деформация металла повышает прочность и твердость поверхностного слоя (наклеп) и, кроме этого, создает в наружных слоях весьма благоприятные для циклических нагрузок остаточные напряжения сжатия (см. рис. 4.6).
Существует много различных видов поверхностного упрочнения (рис. 5.7). Один из самых распространенных видов - дробеструйная обработка - пластическое деформирование поверхностного слоя под действием кинетической энергии потока дроби, создаваемой или воздушной струей (см. рис. 5.7, а), или центробежной силой (см. рис. 5.7, б). Этот метод широко применяется для пружин, рессор, зубчатых колес, шатунов, штанг, буровых шарошек и др. деталей. Он повышает ресурс пружин и рессор почти в 10 раз, а зубчатых колес - в 5-14 раз.
Ротационно-ударный наклеп шариками (см. рис. 5.7, в) осуществляют с помощью вращающихся оправок-упрочнителей, в профильных канавках которых помещаются шарики, которые имеют возможность после удара об упрочняемую поверхность утапливаться в пределах радиального натяга. Этот вид упрочнения дает очень чистую поверхность и применим для упрочнения тонкостенных деталей. Испытания направляющих втулок пневмо-молотков, обработанных центробежно-шариковым методом, показывают, что их износ в 2 раза меньше по сравнению с обработкой развертыванием.
Рис. 5.7. Виды поверхностного упрочнения
Одним из самых простых методов упрочнения наклепом является обкатывание упрочняемой поверхности роликами и шариками (см. рис. 5.7, г, д), при котором не требуется специального оборудования, а эффект от упрочнения весьма значителен. Этот метод широко применяется на многих заводах. В табл. 5.2 представлены различные схемы упрочнения деталей горных машин, осуществляемые на Уралмаше. Долговечность таких деталей увеличивается в 2-4 раза. Обкатывание роликом поверхностей труб разведочного бурения приводит к повышению их стойкости в эксплуатационных условиях в 3 раза по сравнению с трубами, обработанными шлифованием. Разработаны приспособления и режимы упрочнения обкаткой крупных зубьев шестерен: так, бортовые шестерни экскаватора ЭКГ-4,6 (m=26 мм) при этом увеличивают долговечность в 3-4 раза, конические шестерни привода конусных дробилок (m=30 мм) - до 10 раз. Горные машины, работающие в тяжелых эксплуатационных условиях под воздействием абразивных сред, требуют иногда глубокого слоя упрочнения, который не может быть получен при рассмотренных выше методах. В этом случае может применяться чеканка обработанной поверхности (см. рис. 5.7, е, ж), при которой глубина упрочнения может достигать 35 мм. Наклеп при этом получается с помощью пневматических молотков или специальных приспособлений, установленных на обычные универсальные станки (токарные, строгальные, фрезерные). Применение чеканки для упрочнения ступенчатых валов обеспечивает равнопрочность их элементов и в 1,5-2 раза повышает несущую способность валов.Таким методом могут упрочняться зубчатые колеса, шлицевые соединения, сварные швы, крупные резьбы. Так, упрочнение резьбы валов конусных дробилок позволяет увеличить предел выносливости на 50%, упрочнение корня шпицев полуосей экскаваторов ЭКГ-5 увеличивает долговечность этих деталей в 2 раза.
Таблица 5.2
СХЕМЫ ОБКАТКИ РОЛИКАМИ
Радиус галтели, мм | Способ упрочнения | Схема упрочнения | Упрочняемые детали (примеры) |
До 5 | Обкатывание роликом без подачи | ![]() | Валы напорного механизма стрелы экскаватора |
До 10 | Обкатывание шариком | ![]() | Валы конусных дробилок 220 |
До 25 | Обкатывание наклонным роликом | ![]() | Центральные цапфы экскаватора ЭКГ-4,6 |
50 и более | Обкатывание роликом с подачей по дуге | ![]() | Беговые дорожки шариковых опор экскаваторов |
более 200 | Обкатывание роликом с подачей по хорде | ![]() | Виды конусных дробилок |
любой | Чеканка ударником или вибрирующим роликом | ![]() | Резьбы валов конусных дробилок |
В последние годы все большее применение для упрочнения поверхностного слоя находит способ вибрационного обкатывания - виброобкатывание. Этот способ обеспечивает образование на поверхности деталей регулярного, управляемого микрорельефа (см. рис. 5.7, г, д). Виброобкатывание применяют с целью улучшения таких эксплуатационных характеристик сопряженных пар, как износостойкость, противозадирные свойства, прочность посадок с натягом, контактная жесткость, гидроплотность, уменьшение длительности приработки, устранение адгезии и схватывания. Виброобкатывание позволяет снизить требования к точности и шероховатости обработанных поверхностей, исключить термохимическую обработку, а также применение покрытий, снизить сортность и уменьшить количество подаваемой смазки, заменить дефицитные материалы менее дефицитными. Так, например, виброобкатывание лопасти ротационного компрессора, изготовленного из стали 9ХТС, повысило износостойкость этой детали в 1,4 раза, исключило случаи схватывания при работе; при виброобкатывании подшипниковой втулки из бронзы ДЦС 5-5-5 износостойкость повысилась в 1,6 раза, и т.п. Недостатком этого метода является ограниченная область его применения: для точных деталей небольшого размера, т.к. глубина наклепа достигает всего десятых долей миллиметра.
Вибрационная обработка для отделочных и упрочняющих методов может осуществляться в специальных камерах (рис. 5.8), в барабанах, в которые загружают детали и абразивные наполнители с упрочнителями в виде твердосплавных шаров. Барабану сообщают вибрации в двух или трех направлениях. В качестве упрочняемых деталей в барабан могут быть помещены пружины, буровые коронки, штанги, соединительные муфты и др. Так, виброупрочнение буровых коронок КДП-40 показывает, что эта операция уменьшает удельный расход коронок на один шпурометр на 27 %, а стойкость виброупрочненных коронок возрастает на 23 %.
5.5. НАПЛАВКА ИЗНОСОСТОЙКИХ МАТЕРИАЛОВ
Твердость и износостойкость рабочих поверхностей деталей, изготовленных из обычных конструкционных металлов, повышают путем наплавки материалов с заданными свойствами. Наплавка производится путем сплавления основного металла с наносимым на него слоем другого металла (рабочего слоя), толщина которого практически не ограничена. Все применяемые наплавочные материалы можно разделить на 5 групп:
1) стали - углеродистые, марганцевые, хромомарганцевые, хромистые,
хромоникеливые, вольфрамовые и молибденовые;
2) сплавы на основе железа - высокохромистые, вольфрамовые и молибденовые чугуны, сплавы с бором и хромом, с кобальтом и молибденом или вольфрамом;
3) сплавы на основе никеля и кобальта - нихромы и нимоники, сплавы с бором и хромом (колмоной), с молибденом (хастемон), кобальта с хромом и вольфрамом (стелгиты);
4) карбидные псевдосплавы - сплавы с карбидом вольфрама, с карбидом хрома;
5) сплавы на основе меди - алюминиевые и оловянно-фосфористые
бронзы.
Выбор наплавочных материалов производится с учетом работы рабочего органа, характеристики абразивности грунтов, характера изнашивания рабочей поверхности, динамических нагрузок на рабочий орган и экономических показателей.
Марганцевые, хромистые и хромомарганцевые наплавочные материалы (Т590, Т620 и др.) обеспечивают повышение долговечности деталей в 2-3 раза. Сплавы второй группы обладают высокой твердостью и износостойкостью за счет карбидов хрома, вольфрама и молибдена, их обычно называют твердыми сплавами (сормайтом У35Х28Н4С4). В последние годы получают все большее распространение дисперсионно-твердеющие сплавы, представляющие собой чаще всего композиции на основе железа, кобальта, вольфрама или молибдена. Преимуществом этих сплавов является возможность механической обработки, поскольку непосредственно после наплавки твердость невысокая - НRс 30-35. Высокую твердость - до НRс 65-70 - эти сплавы приобретают после термообработки, в результате чего происходит распад пересыщенного твердого раствора и выделение из него упрочняющей фазы.Примером такого сплава является сплав К30М18ТСН. Из сплавов третьей группы чаше применяются стеллиты - кобальтовые сплавы (В2К, ВЗК и др.), которые обладают высокой износостойкостью, жаропрочностью, коррозионной стойкостью, повышенной вязкостью. Применяются для наплавки наиболее ответственных деталей. Износостойкость деталей, наплавленных этими материалами, повышается в 2-10 раз.
Широкое применение для повышения долговечности деталей, контактирующих в процессе работы с абразивной средой, нашли материалы четвертой группы с большим содержанием карбидов вольфрама и феррохрома: ПС-4 (40 % сормайта+60 % феррохрома); ПС-5 (40 % сормайта, 58 % феррохрома, 2 % ферротитана). Износостойкость деталей при этом методе повышается на порядок (в 10-12 раз).
Наплавочные работы могут вестись различными способами в зависимости от места выполнения работ, серийности наплавки деталей, геометрической формы наплавленной поверхности, производительности способа и т.д. Основными разновидностями наплавки являются электродуговая (ручнаяи автоматическая), электрошлаковая, газопламенная, индукционная и др.
Ручная электродуговая наплавка - наиболее простая, обеспечивает нанесение практически всех видов износостойких наплавочных материалов, но не всегда обеспечивает высокое качество и имеет низкую производительность (см. табл. 5.3). Перспективной является механизированная наплавка под слоем флюса, обеспечивающая высокую производительность наплавки, экономичность и стабильность наплавленного слоя.
Широкое применение имеет механизированная наплавка в среде защитных газов, которая дает высокое качество наплавки при удовлетворительной производительности (табл. 5.3).
Ручная наплавка ацетилено-кислородным пламенем наиболее рациональна при использовании трубчатых электродов с релитом (ТЗ-2, ТЗ-3) и литых прутков твердого сплава (стеллиты и др.). Ниже дается табл. 5.3 для сравнения различных способов наплавки по их производительности.
Выбор марки материала и метода упрочнения определяется условиями работы детали в эксплуатации, а также особенностями ее изготовления в условиях производства. Выбранный способ упрочнения должен обеспечивать выполнение технических условий на изготовление детали. На выбор того или иного метода оказывают влияние также технико-экономические показатели, которые определяются стоимостью упрочнения и степенью повышения долговечности детали и всей машины. Большое количество разработанных методов, а также многообразие факторов, влияющих на выбор оптимального способа упрочнения, часто не позволяет однозначно решить эту задачу.
Таблица 5.3
СПОСОБЫ НАПЛАВКИ ТВЕРДЫМИ СПЛАВАМИ
Способ наплавки | Производительность, кг/ч | Преимущества |
Ручная электродуговая | 0,8-3 | Простота метода, наплавка любых профилей |
Автоматическая под флюсом | 2-15 | Высокое качество наплавки |
Многоэлектродная электрошлаковая | 15-25 | Высокая производительность при наплавке больших толщин |
Плавящимся электродом в углекислом газе | 1,5-8 | Наплавка боковых и внутренних поверхностей |
Газопламенная | До 1,5 | Наплавка сложных конфигураций в труднодоступных местах |
Вибродуговая | 1,2-2,8 | Наплавка малых толщин слоя |
Индукционная | 1-20 | Высокая производительность и качество |
Плазменная | До 27 | Наплавка тугоплавких материалов |
В табл. 5.4 в соответствии с условием работы быстроизнашивающихся деталей приведены некоторые рекомендации с указанием конкретных примеров из практики упрочнения.
Таблица 5.4
РЕКОМЕНДУЕМЫЕ УСЛОВИЯ УПРОЧНЕНИЯ
Назначение наплавки или условия работы детали | Материал электрода | Способ наплавки | Область применения |
Абразивное изнашивание при слабом ударном воздействии
| ПП-У15Х12М-О ПП-У25Х17Т-О | Механизированная электродуговая | Детали грязевых и торфяных насосов. Зубья и стенки ковшей экскаваторов
|
Сталинит, БХ, КБХ | Угольной дугой | ||
Абразивное изнашивание, умеренные удары
| Сормайт, сплавы ПС-4, ПС-5 | Индукционная | Рабочие органы почвообрабатывающих машин |
ПП-Х12ВФ | Электродуговая под слоем флюса | Шарошки буровых долот. Зубья и стенки ковшей экскаватора. Щеки дробилок, ножи скреперов | |
Абразивное изнашивание в условиях больших ударных нагрузок и высоких удельных давлений
| ПП-У50Х25ГВТ ПП-У15Х12М-О ПП-13Н4 ПП-У25Х17Т-О | Механизированная электродуговая под флюсом и в среде защитных газов | Долота ударного бурения, брони шаровых мельниц, молотки молотковых дробилок, зубья ковшей экскаваторов и врубовых машин |
ОЗН-400 ТТ-540 | Ручная электродуговая | Черпаки драг, козырьки ковшей землечерпалок | |
Релит | Трубчатым электродом | Буровой инструмент | |
Восстановление размеров деталей, не требующих высокой износостойкости
| 65Т, Св-08А, Св-10Т2, Св-10ХМ, СВ-18ХГСА, НП-40 | Вибродуговая | Валы, оси, фланцы, штоки, шпиндели, толкатели клапанов |
НП-50ХФА | Вибродуговая | Шлицевые валы, муфты |
5.6. ЗАЩИТА ОТ КОРРОЗИИ
В процессе эксплуатации горных машин многие детали, работая в агрессивных средах, разрушаются вследствие коррозионных процессов. Для защиты таких деталей от коррозии применяются металлические покрытия и лакокрасочные покрытия. Лакокрасочные покрытия более универсальны, дешевы и более технологичны, поэтому из общего объема покрытий 65-80 % - это покрытия лаками и красками.
Металлические покрытия от коррозии совмещают с нанесением износостойкого слоя (хромирование, никелирование, борирование), который наносят на поверхность детали гальваническим методом путем осаждения металлов из водных растворов их солей под действием постоянного электрического тока (U=6-12V, I=250-500А). Нанесенный слой имеет толщину от нескольких микрометров (при защите только от коррозии) до 0,5мм при совмещении с износостойким покрытием. При нанесении, например, слоя хрома 30-50 мкм на шейки валов и осей их износостойкость повышается в 5 раз, при нанесении слоя бора толщиной 0,2-0,4 мм на рабочие поверхности втулок грязевого насоса позволяет увеличить их долговечность в 4 раза по сравнению со втулками, закаленными токами высокой частоты.
Покрытие деталей лакокрасочными материалами - широко распространенное технологическое средство защиты металлов от коррозионного разрушения. Чтобы надежно предохранить поверхность металла от воздействия атмосферного воздуха и агрессивных сред, лакокрасочные покрытия должны обладать комплексом различных свойств: «сплошностью» пленки, хорошей сцепляемостью с металлом, механической прочностью, сопротивлением истиранию, стойкостью к изменению температур и воздействию солнечной радиации. Чтобы правильно удовлетворить этим требованиям и обеспечить высокую долговечность защищаемых деталей машин, необходимо правильно выбрать лакокрасочное покрытие и технологию его нанесения. Выбор лакокрасочного покрытия производят исходя из условий эксплуатации и свойств материала детали. Для обеспечения надежной защиты горных машин, работающих в атмосферных условиях, применяют защитно-декоративные перхлорвиниловые эмали ХВ-124, ХВ-113, пентафталевую эмаль ПФ-115, меламиноалкидную эмаль МЛ-113, МЛ-11 и другие, которые наносят после грунтовки и шпатлевки деталей. Для защиты деталей, подверженных влиянию агрессивных сред, применяют химически стойкие эмали, которые способны длительное время не разрушаться при контакте с различными химически активными жидкостями и препятствуют проникновению их к поверхности деталей. К таким покрытиям относятся лаки ХСЛ-3, ХС-76, КФ-252, эмали ЭП-255, ПХВ и др.
Лакокрасочные материалы могут наноситься различными методами: кистью, пульверизацией, окунанием, струйным обливом, распылением в электростатическом поле, безвоздушным распылением. Сушка после окраски может производиться естественным способом, искусственным (горячим воздухом), конвекционным, инфракрасными лучами и даже токами высокой частоты.
5.7. КОНТРОЛЬ КАЧЕСТВА ИЗГОТОВЛЕНИЯ
Долговечность любой машины зависит не только от конструктивных решений, заложенных в проект, но в значительной степени (40-45 %) от качества использованного материала, качества изготовления детали, качества сборки машины. И поэтому качество определяется соответствующими техническими и технологическими документами: сертификатом на металл, допусками на размеры, показателями качества поверхностного слоя, требованиями к сборке узлов и всей машины и т.п., в зависимости от выполнения всех этих требований и будет меняться долговечность отдельных деталей и всей машины. Соответствие всех деталей и собранной машины нормативным документам и требованиям определяется соответствующими методами контроля и подтверждается документами.
При изготовлении, модернизации, ремонтах горных машин существуют следующие виды технического контроля:
- входной контроль поступающих на предприятие от предприятий-поставщиков сырья, материалов, комплектующих элементов и приборов;
- операционный контроль заготовок, деталей, сборочных единиц и других видов изготовляемой продукции после завершения одной или нескольких промежуточных технологических операций;
- приемочный контроль готовых машин, который может сопровождаться испытанием машин перед эксплуатацией.
Все эти виды технического контроля носят явно выраженный профилактический характер: они ставят своей конечной целью своевременно обнаруживать, не допускать до сборки детали с дефектами, а собранные машины с отклонениями от технических условий - не допускать к эксплуатации. По результатам технического контроля могут быть приняты решения, корректирующие технологический процесс, не допуская в дальнейшем таких дефектов.
В зависимости от возможности обнаружения дефекты делятся на явные и скрытые. Явные - могут быть обнаружены существующими методами, и для них контрольной документацией предусматриваются соответствующие правила, методы и средства. Но возможно наличие в деталях дефектов, для выявления которых предусмотренных контрольной документацией средств недостаточно - дефекты остаются скрытыми. Условно скрытыми можно назвать и дефекты, которые не выявлены, а могли бы быть выявлены существующими средствами (при не 100 % - ном, а выборочном контроле).
Скрытые дефекты могут резко снижать качество машин, так как машина состоит из тысяч деталей, и если из них лишь 1 % деталей окажется с дефектами, это приведет к увеличению вероятности отказа машины на один порядок. Влияние скрытых дефектов на качество выпускаемых изделий можно показать на примере буровых коронок.
Перфораторные коронки состоят из двух деталей - корпуса и пластинки твердого сплава, припаянных к корпусу. На завод - изготовитель бурового инструмента одно время пошли рекламации: в работе быстро разрушается твердый сплав. Стали разбираться: причиной может быть плохой твердый сплав или плохая технология изготовления, при которой можно испортить твердый сплав (пайкой, заточкой). Проверили технологию - все в порядке. Стали проверять твердый сплав: по ГОСТ он должен иметь определенную твердость, удельный вес, предел прочности на разрыв и определенную микроструктуру. С твердостью и удельным весом - все в порядке, а вот прочность и структура не соответствуют ГОСТ. Пришлось на всех заводах-изготовителях буровых коронок внедрять входной контроль пластинок твердого сплава, поставляемых на завод-изготовитель. Оказалось, что недостаток в изготовлении твердого сплава не обеспечивал необходимую микроструктуру, что в свою очередь резко снижало прочность пластин твердого сплава (вместо sв>130 в партиях были пластины с sв=90-100). Входной контроль помог обнаруживать и возвращать дефектные партии твердого сплава, через некоторое время после упорядочения технологии на заводе-изготовителе твердого сплава буровой инструмент приобрел необходимое качество.
Контрольные операции весьма трудоемки, требуют дорогого и точного оснащения, высокой квалификации контролеров, поэтому необходимо внедрять активные методы контроля, которые совмещают контроль с изготовлением детали, и статистические методы контроля, которые дают возможность исключить случаи появления дефектов при изготовлении.
Активный контроль, при котором по результатам проверки параметров качества дается команда на подналадку оборудования, изменение режимов его работы, сортировку бракованной детали или приостановку технологического процесса, дает гарантию обеспечения точности и стабильности технологического процесса. Средства активного контроля могут иметь различную степень развития - от использования визуальных сигналов для подналадки оборудования до самонастраивающихся систем.
Одной из важных задач, которую необходимо решить при организации контроля продукции, является выбор метода контроля - сплошной или выборочный контроль продукции. Сплошной контроль в большей степени гарантирует выпуск бездефектной продукции, однако он не всегда экономически оправдан (а иногда и невозможен: для того, чтобы определить sв пластинки твердого сплава нужно ее сломать). В этом случае применяют статистические методы контроля качества продукции. Суждение о годности изделия осуществляется по альтернативному или количественным признакам. При контроле по альтернативному признаку все изделия в выборке разбиваются на две категории - годные и негодные (дефектные). Оценка партии производится по величине доли дефектных изделий от общего числа проверенных. При контроле изделий по количественному признаку у каждого изделия определяется один или несколько параметров и оценка партии изделий производится по статистическим характеристикам распределения этих параметров, поскольку каждое значение параметра является случайной величиной.
Оценка уровня качества изготовленных деталей - необходимый, но недостаточный вид статистического контроля для обеспечения высокой стабильности технологического процесса. Возможность получения дефектных деталей (пусть даже в допустимом минимальном количестве) является следствием того, что статистическими методами анализируется результат данного технологического процесса - полученное качество деталей, а не характеристики самого процесса, которые определяют это качество.
Статистические методы контроля параметров технологического процесса позволяют следить за изменением его и принимать меры по предотвращению дефектов. Для статистической оценки точности и стабильности технологических процессов обработки деталей стандартами предусмотрены показатели:
коэффициент точности
коэффициент стабильности
где D=хд-хн - величина отклонения действительного значения параметра хдот номинального хн, а Dн - поле допуска на изготовление рассматриваемого параметра.
Зная эти коэффициенты, по разработанным таблицам находят вероятный процент брака q, свойственный данному процессу. Полученное значение q не должно превышать допустимых значений для конкретной продукции или данного показателя качества, подлежащего статистическому регулированию.
В готовой машине могут оказаться технологические дефекты, которые относятся к недопустимым, но либо пропущены из-за несовершенства методов контроля, либо вообще не регламентированы. Это может привести к тяжелым последствиям при эксплуатации машины вплоть до возникновения аварийных ситуаций. Для предотвращения тяжелых последствий отказов, связанных с технологическими дефектами, необходимо иметь средства для обнаружения дефектов. Для этого применяется широкий диапазон как разрушающих, так и неразрушающих методов контроля. Разрушающие методы контроля, такие, как испытание механических свойств, являются выборочными и не позволяют отделить в партии годные детали от дефектных. Неразрушающие методы контроля позволяют осуществить сплошную проверку ответственных изделий и полностью гарантировать их бездефектность. Эти методы называются дефектоскопией и базируются на применении различных физических методов, позволяющих обнаруживать и оценивать внутренние и поверхностные дефекты. В табл. 5.5 представлены методы, применяемые для дефектоскопии, и область их применения.
Применение того или иного метода, например, для отливок или сварных ответственных деталей, позволяет предупредить появление внезапных отказов от внутренних даже мелких дефектов.
Грубые ошибки технологического процесса и соответственно значительные дефекты, как правило, проявляются при обкатке или контрольных испытаниях машины и могут быть устранены в среде производства. Поэтому испытание машин с точки зрения их соответствия технологическим условиям и проверки всех основных параметров машины является заключительным этапом ее изготовления. Испытание делится на две стадии:
1) механическое испытание (обкатка) - производится для проверки правильности взаимодействия частей и приработки трущихся поверхностей дета
лей;
2) испытание под нагрузкой - производится в соответствии с техническими
условиями, как правило, на режимах и в условиях, соответствующих эксплуатационным.
Испытания проводят на специальных стендах. Испытываются или отдельные функциональные самостоятельные единицы и составные части (пневмоударник, буровые коронки, гидродвигатели, гидростойки механизированных крепей, насосы и т.п.), или машина в сборе (шахтные вентиляторы, карьерные экскаваторы, погрузочные машины, проходческие и очистные комбайны и т.д.).
При испытаниях под нагрузкой оцениваются: степень шума, вибрации и нагрев движущихся частей, наличие утечки масла, рабочие характеристики машин, указанные в ее паспорте. Испытания под нагрузкой должны воспроизвести реальный спектр по мощности и усилию, которое испытывает данное оборудование в процессе использования по назначению. В случае обнаружения во время испытаний каких-либо дефектов они устраняются, после чего проводится повторное испытание. Результаты испытания вносятся в паспорт (формуляр) на машину.
В случае отсутствия стенда для громоздких объектов (шагающий экскаватор и др.) испытание может быть проведено в местах эксплуатации машин.
Таблица 5.5
Дата добавления: 2018-05-02; просмотров: 335; Мы поможем в написании вашей работы! |
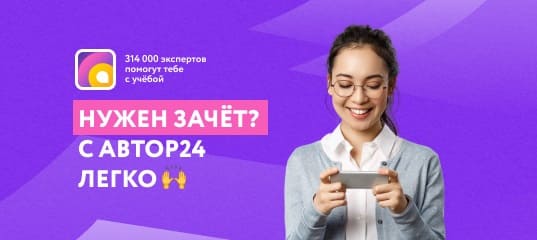
Мы поможем в написании ваших работ!