Базирование заготовок по цилиндрическим поверхностям
Билет 16
1 Составляющие припуска, дефектный слой, шероховатость, погрешность установки.
Rz – шероховатость,
П – глубина упрочненного слоя,
ρ – пространственный отклонения,
Еу – погрешность установки.
Rz и П берутся по справочникам.
ρ берется для конкретной детали и поверхности.
Некоторые замечания к расчету припусков.
1) При односторонней обраотке минимальный припуск опр-ся:
2) При 2-х сторонней обработке торца (симм. припуск):
3) Иногда из формулы минимального припуска отдельные составляющие могут исключаться. Еу = 0 при обработке инструментом, который направляется по обрабатываемой поверхности (плавающая опора).
4) Если необх. сохранить упрочненный поверхностный слой, то Пi = 0.
5) Отклонения расположения и формы учитывают в том случае, если они не связаны с допуском на р-р и имеют самост. значения.
6) После чистовой обработки считается, что ρi-1 = 0.
2 Понятие расчетного припуска при наружн и внутр обраб-ке
Номинальный припуск на обработку поверхностей:
наружных
i ном i min i i Z = Z + H − H −1 ,
i ном i min Di Di Z = Z + H − H −1 2 2 ;
внутренних
i ном i min i i Z = Z + B − B −1 ,
i ном i min Di Di Z = Z + B − B −1 2 2 ,
где Hi-1, HDi-1, Hi, HDi – нижние отклонения по размерам соответственно на
предшествующем и выполняемом переходах; Bi-1, Bi, BDi-1, BDi – верхние от-
клонения по размерам соответственно на предшествующем и выполняемом
переходах.
|
|
Значения номинальных припусков необходимы для определения номи-
нальных размеров заготовок, по которым изготовляют технологическую ос-
настку (штампы, пресс-формы, модели, приспособления и т. д.).
3 Понятие станкоемкости, трудоемкости, время цикла, фактической занятости и перехода
Станкоемкость – время работы оборудования, необходимое для изготовления изделия.
Трудоемкость – время рабочего, потраченное на изготовление единицы изделия.
Цикл технологической операции – величина календарного времени, в течение которого непрерывно осуществляется технологическая операция, независимо от колическтва одновременно обрабатываемых деталей.
Билет 17
1 Влияние режима резания на шероховатость поверхности.
Влияние режимов резания на достижимую шероховатость поверхности.
Высота неровностей зависит в наибольшей степени от величины подачи. При крупных подачах эта высота значительно отличается от расчетной и превышает ее в несколько раз.
Влияние глубины резания на шероховатость поверхности незначительно и не имеет практического значения. Скорость резания существенно влияет на образование шероховатости поверхности. При скорости резания до 3—5 м/мин размеры неровностей незначительны; с увеличением скорости резания неровности возрастают; при повышении скорости резания до 60— 70 м/мин высота неровностей уменьшается, и при скорости около 70 м/мин шероховатость поверхности получается наименьшей. Дальнейшее повышение скорости резания незначительно влияет на шероховатость обработанной поверхности. Наличие нароста на резце увеличивает шероховатость поверхности, обработанной данным резцом.
|
|
2 Влияние шероховатости поверхности на эксплуатационные характеристики детали
1. Влияние качества поверхности на эксплуатационные характеристики детали.
Эксплуатационные свойства деталей машин находятся в прямой связи с геометрическими характеристиками поверхности и свойствами поверхностного слоя. Износ деталей в значительной степени зависит от высоты и формы неровностей поверхности и определяется главным образом верхней частью профиля шероховатости.
На износоустойчивость поверхности влияют сопротивляемость поверхностного слоя разрушению и макрогеометрические отклонения, которые вызывают неравномерный износ отдельных участков. Волнистость приводит к увеличению удельного давления, так как трущиеся поверхности соприкасаются по выступам волн; то же происходит и при микронеровностях поверхностей, причем выступы микронеровностей могут деформироваться - сминаться или даже срезаться. Вершины микронеровностей могут вызывать разрывы масляной пленки, и в местах разрывов создается сухое трение.
|
|
Прочность деталей также зависит от шероховатости поверхности, так как наличие рисок, глубоких и острых царапин создает очаги концентрации внутренних напряжений, приводящих к разрушению деталей. Такими очагами могут являться и впадины между гребешками микронеровностей, что не относится к деталям из чугуна и цветных сплавов, в которых концентрация напряжений возможна в меньшей степени
От шероховатости поверхности (особенно от высоты микронеровностей) зависит прочность прессовых соединений, поскольку при запрессовке одной детали в другую фактическая величина натяга зависит от шероховатости поверхности и отличается от величины натяга при запрессовке деталей с гладкими поверхностями для тех же диаметров.
Шероховатость поверхности детали оказывает значительное влияние и на ее коррозионную стойкость, так как с уменьшением микронеровностей поверхности уменьшается и площадь соприкосновения с корродирующей средой, следовательно, меньше влияние среды. С увеличением глубины впадин микронеровностей и резкости их очертаний повышается разрушающее действие коррозии, направленное вглубь металла.
|
|
3 Классы погрешностей, влияющие на точность механической обработки
Различают систематические и случайные погрешности.
Систематическая погрешность – это постоянная или закономерно изменяющаяся погрешность, характерная для каждой заготовки из всей обработанной партии. (Δсист, Δп. сист)
Случайная погрешность имеет различные значения для различных заготовок из всей партии. Ее проявление заранее предсказать нельзя. Причин ее возникновения множество. Описать эти погрешности можно лишь с помощью законов математическом статистики.
Причины возникновения систематических погрешностей.
1. Неточность, износ и деформация станков (напр. при точении вала за 2 установа).
2. Неточность настройки инструмента и его износ (начальный, прогназируемый и катастрофический изно).
3. Деформация заготовки под действием сил закрепления.
4. Деформация технологической системы под влиянием нагрева.
5. Влияние внутренних напряжений на форму заготовки. Внутренние напряжения (остаточные напряжения) образуются в заготовках, получаемых: литьем, ковкой, штамповкой, сваркой, в результате термообработки и пр. Перед обработкой заготовка находится в равновесии, но в процессе обработки снимаются слои металла, неравномерные или, напр., с одной стороны. В результате возникает систематическая погрешность.
6. Теоритическая погрешность схемы обработки. Упрощение конструкции режущего инструмента, кинематики станков при изготовлении деталей сложной формы (фасонных) вызывает появление систематической погрешности, которая часто приводит к искажению формы детали.
Случайные погрешности.
В результате возникновения случайных погрешностей происходит рассеяние размеров заготовок, обрабатываемых в одних и тех же условиях. Причин возникновения этих погрешностей множество. Предварительно предсказать возникновение этих погрешностей нельзя. Предсказать их величину тоже нельзя. Распределение (рассеяние) размеров заготовок в партии деталей описывают с помощью законов математической статистики.
Суммирование погрешностей.
Систематические и случайные погрешности суммируются арифметически.
Систематические погрешности суммируются между собой геометрически, т.е. векторно.
Случайные погрешности суммируются по правилу квадратного корня.
к – коэффициент, показывающий несоответствие законов.
к(Δ) = 1,22; к(Π) = 1, 73;
к(норм. распр) = 1.
ΔΣсист – постоянная систематическая погрешность, ΔΣп.сист – переменная систематическая погрешность.
Билет 18
1 Настройка на размер
Основным и, пожалуй, наиболее важным моментом в процессе использования металлообрабатывающих станков является их наладка и настройка - совокупность действий по подготовке и регулированию оборудования: настройка цепей, установка и регулирование приспособлений и инструментов, иными словами, всесторонняя подготовка к выполнению предстоящей работы. Кроме того, со временем может меняться режим работы и настройка токарного станка нарушается, поэтому систематически требуется ее восстановление (подналадка).
Наладку и настройку станков осуществляют исключительно используя руководство по эксплуатации. Как правило, настройку режимов резания проводит специалист-станочник либо перед началом работы, либо в ее процессе, устанавливая необходимые параметры - частоту вращения шпинделя, подачу и глубину резания. Иногда подобные режимы резания устанавливаются сразу путем установки сменных колес в цепях главного движения и подач.Заключительным этапом накладки является регулировка инструментов на размер и пробными работами.
Выделяют следующие методы наладки металлорежущих станков:
а) метод пробных подходов - проводится снятие стружки с заготовки пробными проходами, после чего измеряется деталь. Получается нужный размер. При наладке инструмент, установленный в шпиндель пиноли агрегатного станка, выдвигают вместе с пинолью в крайнее переднее положение так, чтобы он коснулся поверхности обрабатываемой детали. Затем пиноль (или многошпиндельную насадку) отводят в исходное положение, а силовую головку подают вперед на нужную или несколько меньшую глубину подачи. После замера обработанной поверхности наладчик определяет, на какую величину нужно подать силовую головку, чтобы получить годную деталь. Метод пробных проходов применяют обычно при первичных наладках, когда отсутствуют готовые детали, эталон или наладочные шаблоны. Такая работа выполняется опытными наладчиками.
б) наладка по готовой детали - в данном случае используют ранее обработанную деталь с размерами, примерно равными наименьшему предельному размеру, предусмотренному чертежом. Различают наладку по готовой детали или всех позиций станка, или промежуточных переходов и наладку по детали, обработанной на данной позиции или переходе.
в) наладка по эталону, по шаблону - наиболее точный и легкий способ, созданный при этом эталон полностью соответствует конфигурации детали, но отличается от нее своими размерами, которые определяются расчетно-аналитическим методом на основании факторов, оказывающих влияние на точность обработки, или на основании данных после проведения замеров обработанных деталей. Положение инструментов определяют, касаясь их режущими кромками поверхностей эталона, или устанавливают с зазорами по щупу, размер которого определяется на базе распределения припусков на промежуточные и окончательные переходы с учетом отжатий во время обработки. Так, например, для растачивания отверстия диаметром 40+0,02 на глубину 30+0,05 оправка с резцом подводится с шпинделем головки до того, как режущая кромка резца коснется торца эталона, и закрепляется, когда шпиндель находится в правом крайнем положении.
Метод пробных ходов и измерений. Применяется в единичном производстве. Преимущества: на неточном оборудовании можно получить достаточно высокую точность детали; исключается влияние износа режущего инструмента на точность; при неточной заготовке можно предотвратить появление брака. Недостатки: зависимость точности от внимания и квалификации работников, от толщины минимального срезаемой стружки, низкая производительность => высокая себестоимость.
2. Метод автоматического получения размера на станке. Применяется при массовом и крупносерийном производстве. Заключается в предварительной настройке станка на заданных размер по упорам, конечным выключателям, датчикам положения и другими средсвами. Преимущества: повышение точности (обеспечение заданной точности) не зависит от минимальной величины среза; один наладчик настраивает 8-12 станков; время настройки сокращается = > себестоимость уменьшается. Недостатки: при настройке станка используются конечные элементы, т.е. если система, отслеживающая положение суппорта относительно координатной системы станка, не надежна, то невозможно обеспечить высокую точность размера.
2 Базирование детали с цилиндрической поверхностью в призме.
. Установка наружными цилиндрическими поверхностями.
Размеры валов в обрабатываемой партии всегда имеют некоторый разброс по диаметру. Так при фрезеровании лысок и шпоночных пазов на валах размеры последних могут быть заданы как h1, h2 или h3.
Но так как диаметральные размеры обрабатываемых валов изменяются от некоторого минимального до максимального значений, положение из осей может быть расположено в точках C′ или C′′. Соответственно положение верхней точки А также может изменяться.
Требуется проанализировать возникающие погрешности базирования когда размер задан одним их трех способов: как h1, h2 или h3.
а) выдерживаемый размер задан как h3.
Составим размерную цепь
h = ОА - ОМ
АО - настроечный размер (отрезок), АО = const и на погрешность базирования не влияет.
После тригонометрических преобразований получим, что погрешность базирования будет определяться формулой
б) выдерживаемый размер задан как h2
Строим размерную цепь
H2 = Б1 - Б2
Б1 - является настроечным размером, значит вся погрешность связана с размером Б2.
в) размер задан как h1 (от верхней точки) и, проведя аналогичные рассуждения получим:
Таким образом, рассмотрев три возможных варианта простановки размеров: h1, h2 или как h3 делаем вывод, что минимальная погрешность базирования будет иметь место, если выдерживаемый размер задан как .
Базирование заготовок по цилиндрическим поверхностям
Для базирования заготовок по цилиндрическим поверхностям применяют призмы. Призмы изготовляют главным образом с углом 90°, хотя в отдельных случаях встречаются призмы с углами 60 и 120°, но их следует применять в особых случаях. При базировании в призмах ось цилиндрической поверхности заготовки независимо от отклонения в величине ее диаметра устанавливается в плоскости симметрии призмы.
На рис. 188 дана типовая схема базирования заготовки цилиндрической формы. Заготовку устанавливают наружной поверхностью в две призмы А и Б, играющие роль опорной и направляющей базовых поверхностей, и прижимают к упору В, являющемуся упорной базовой поверхностью. В отличие от базирования призматических заготовок приведенная на рис. 188 схема не исключает возможности поворота заготовки вокруг ее продольной оси. При необходимости поворот может быть исключен постановкой упора в отверстие или канавку, специально изготовленные в заготовке.
Применение призм в самоцентрирующих приспособлениях обеспечивает базирование заготовок независимо от диаметра в двух взаимно перпендикулярных плоскостях (рис. 189). Призмы сдвигаются одновременно к центру О.
На рис. 190 даны схемы базирования вала на призму для фрезерования площадки, причем по рис. 190, а измерительной базой является верхняя образующая вала, связанная размером h1 с обрабатываемой поверхностью, по рис. 190, б измерительная база — нижняя образующая (размер h2) и по рис. 190, в измерительная база — ось вала (размер h). Так как во всех трех случаях валы базируют на установочную базу, погрешность базирования неизбежна. Погрешности базирования, т. е. колебания размеров h1, h2 и h зависят от допуска на диаметр вала δD и от угла призмы α.
Для выяснения погрешностей базирования допустим, что на призму поочередно установлены два вала, причем один с наибольшим предельным диаметром D1 а другой — с наименьшим D2 (рис. 191), и последовательно определим: расстояние Δh1 между верхними образующими валов; расстояние Δh2 между нижними образующими валов; расстояние Δh между осями валов.
Эти расстояния и будут погрешностями базирования при установке по схемам, приведенным на рис. 190.
В табл. 13 приведены значения коэффициентов К, К1, К2 для различных углов α призмы.
Таблица 13
Значения коэффициентов К, К1 и К2 при различных углах α призмы
Коэффициенты | Углы призмы α° | |||
60 | 90 | 120 | 180 | |
К К1 К2 | 1,0 1,5 0,5 | 0,7 1,21 0,2 | 0,58 1,07 0,08 | 0,5 1,0 0,0 |
Если угол призмы, как это часто бывает, принять равным 90°;. то погрешности базирования по рис. 190 составят:
Δh1 = 1,21 δD; Δh2 = 0,2 δD; Δh = 0,7 δD.
Если вал устанавливать по плоскости (α = 180°), то возможны те же три схемы, что и на рис. 190. Эти схемы даны на рис. 192, а, б и в. Погрешности базирования по рис. 192 составят: Δh1 = δD; Δh2 = 0 (здесь измерительная и установочная базы совпали); Δh = 0,5 δD.
На рис. 192, г дана схема, при которой обеспечиваются получение размера h2 и симметричное расположение паза относительно оси вала; последнее зависит от колебаний размера h. По аналогии со схемами на рис. 192, б и 192, в погрешности базирования будут Δh2 = 0 и Δh = 0,5 δD.
3 Технологические методы обработки поверхности(точен, фрезер, шлиф, сверлен, доводка, суперфиниш)
) Лезвийная обработка (точение, сверление, рассверливание, зенкерование, развертывание, фрезерование, строгание, долбление, протягивание, прошивание).
2) Абразивная обработка (шлифование, хонингование, притирка, суперфиниширование, микрофиниширование, полирование).
3) ППД (Обкатывание роликами, калибрование, размерное совмещенное обкатывание).
4) Эл-физ. и эл-хим. методы (Анодно-механич. обработка, электроискровая, лазерная).
5) Спец. методы (нарезание резьб, обработка шлицев, обр-ка шпоночных пазов, обр-ка зубчатых венцов).
1)Лезвийная обработка.
Точение в массовом пр-ве выполняется на многорезцовых токарных автоматах и п/автоматах, на гидрокопировальных авт. и п/авт., на станках с ЧПУ и на спец. токарных станках для тонкого точения.
Многорезцовые токарные авт. и п/авт имеют прод. и попер. суппорты. На прод. суппорте устанавливаются резцы для обработки цилиндрических поверхностей. На попер. суппорте – для обработки плоскостей и фасок. tM – основное (машинное) время. tM = Lp.x./S · n.
Гидрокопировальные станки имеют в своем составе продольный (копировальный) и попер. суппорт. Lp.x. больше => больше время обработки и точность, меньше стойкость инструмента.
Станки с ЧПУ не имеют попер. суппорта, что компенсируется наличием многоревольверной головки (можно управлять резцом под углом).
Сверление применяется для образования отверстий в сплошном металле.
Рассверливание – для увеличения диаметра отверстия, просверленного ранее.
Зенкерование – для увеличения точности просверленного отверстия.
Цековка – разновидность зенкера.
Развертывание – для окончательной обработки отверстий, предварительно просверленных или прозенкерованных. Развертки бывают ручные и машинные. У ручных заходный конус более длинный.
Фрезы бывают концевые (цилиндрические) и торцевые. Цилиндрические устанавливают в оправку, а торцевые в шпиндель с помощью конусов Морзе.
Строгание – после прохождения резцом всей длины заготовки, он возвращается в исходное положение.
Долбление – аналогично строганию, но применяется для получения зубчатых венцов.
Протягивание – используют для получения отверстий различной формы и для обработки плоских поверхностей.
Прошивание - как и протягивание, только прошивку проталкивают сквозь отверстие.
2) Абразивная обработка.
Шлифование – вращение детали и круга + поперечная подача. (отверстий, патронное шлиф-е, планетарное, плоское шлиф-е).
Выхаживание - Sпопер. = 0.
Хонингование – для обработки отверстий. Брусков может быть 2 и более. Их кол-во определяется габаритами. При обр-ке необх. длина перебега (1/3...1/4 от длины бруска) и колебания (асцеляция). Для коротких деталей можно не создавать поступат. движение. За счет винтового движения на обработанной пов-ти есть царапинки для уменьшения трения. Длинными хонами можно одновременно обрабатывать несколько деталей (предварительная обработка).
Суперфиниширование – возвратно-поступательное движение круга, давление на заготовку (0,05...0,15 МПа), асцеляция (для повышения производительности) и вращение детали. Зернистость брусков различна для разных видов обработки (предварит. или окончат). Процесс идет по времени. Активный контроль не нужен.
Микрофиниш-е – способ окончательной обработки наружных цилиндрический поверхностей, подобен суперфиниш-ю. Разница в том, что используются более сильные удельные давления (≈ в 10 раз), что дает возможность снимать не только гребешки микронеровностей, но и снимать припуск.
Притирка – применяется для тонкой и отделочной обработки с целью достижения высокой точности р-ра и формы поверхности. Выполняется свободным абразивом на масляной основе или с помощью спец. паст. а) притирка тв. абразивными частицами (материа притира мягче обрабатываемой поверхности), б) притирка мягкими абр. частицами (тверже), в) притирка с помощью химически активных паст. Шероховатость после притирки зависит от размера зерна.
Полирование – для достижения минимальной шероховатости, выполняется с помощью войлочных или тканевых кругов, а также абразивными лентами (из кожи). Контролируется по времени.
3) Методы ППД. Обработка ведется без снятия припуска. Обеспечивается высокое качество поверхности, достаточная точнойть р-ров и формы, а также создается большой упрочненный слой. Обработка бывает наружной или внутренней.
4) Чистовая и отделочная обработка. Все методы условно разбиваются на 3 группы: а) полирование, гидрохонингование, дробеструйная обработка (признак группы: отсутствие жесткой связи между заготовкой и инструментом, точность обработки не улучшается, но уменьшается шероховатость), б) свободное развертывание, своб. (плавающее) протягивание, бесцентровое шлиф-е, хонингование, калибрование и др (признак группы: инструмент направляется по обрабатываемой поверхности, результат: обеспечение точности формы, р-ра и шероховатость. Точность взаим. расположения поверхностей не улучшается), в) тонкое точение, тонкое фр-е, шлифование в центрах, плоское шлиф-е и др (признак группы: жесткое направление инструмента относительно детали, результат: улучшение точности размера, формы, взаим. расположения поверхностей и шероховатость).
4) Спец. методы обработки.
Резьбообработка – образование резбы. Осн. недостаток: большое время обработки, низкая стойкость резцов, сложность получения высокой точности резьбы, рваный профиль вершины резьбы. Метчики, плашки, накатывание резьб. Машинные метчики чаще применяются для нарезания резьб в сквозных отверстиях. Их тело и заходный конус меньше, чем у ручных метчиков. Изогнутый хвост предотвращает вращение метчика.
Шлифование резьб – применяют для изготовления точных резьб, резьбонарезного инструмента и резьбовых калибров. Резьбу шлифуют после предварительной обработки. Одно- и многониточные круги.
Накатывание резьб – плоскими накатниками (нельзя накатывать резьбы с большими диаметром и шагом), круглым и дугообразным накатниками, роликами с радиальной подачей (можно накатывать крупную резьбу на больших деталях, корпус соединяющий ролики должен быть жестким), накатывание резьб в отверстиях (метчиками-накатниками, нет процесса резания, а идет пластическое деформирование, только для проходных отверстий).
Обработка шпон. пазов – полуоткрытый шп. паз, закрытая форма, открытая форма, сегментная форма. Обработка ведется шпоночными фрезами (торцевыми), а сегментный шп. паз получается дисковой фрезой.
Шпоночные пазы в отверстиях – долблением (долбежным резцом), протягиванием (протяжкой для массового пр-ва).
Образование шлицев – используются дисковые и торцевые фрезы. При малом крутящем моменте используются эвольвентные шлицы.
Шлифование шлицев – стойкость кругов выше, т.к. углы не работают (для этого есть канавка, освобождающая углы круга от работы).
Билет 19
1 Погрешность настройки
погрешность настройки, возникающая от неправильности взаимного расположения инструмента и заготовки, а также от неточности регулировки упоров и остановов.
Погрешность настройки складывается из:
неточности настройки режущего инструмента;
износа режущего инструмента;
упругих деформаций технологической системы станок—приспособление—инструмент—деталь (СПИД); температурных деформаций узлов станка, обрабатываемой заготовки и режущего инструмента.
При смещении резца на размер вверх-вниз относительно оси станка диаметр D заготовки увеличивается. Биение вращающихся центров станка приводит к биению обрабатываемых поверхностей заготовки относительно оси центральных отверстий. При перестановке обработанной заготовки на другой станок с другим биением центров может возникнуть отклонение от соосности у заготовок, обрабатываемых в разных условиях.
2 Качество поверхности
КАЧЕСТВО ПОВЕРХНОСТИ
деталей машин - комплексный показатель, определяемый след. хар-ками детали: макрогеометрией (отклонение формы на больших участках поверхности - см. Точность обработки); шероховатостью поверхности; волнистостью поверхности (с отношением шага к высоте волны 50 - 1000, т. е. значительно большим, чем у шероховатости); состоянием поверхностного слоя (его физ.-механич. и хим. св-ва - ваклёп, остаточные напряжения, микротвёрдость, фазовый состав и др.). Хар-ки К. п. оказывают существенное влияние на эксплуатац. св-ва деталей машин: износостойкость, сопротивление усталости, контактную жёсткость, коррозионную стойкость, виброустойчивость, прочность прессовых соединений, плотность соединений.
3 Кз.о.
Коэффициент закрепления операций и его роль в классификации типов производства.
Тип производства определяется комплексной характеристикой технических, организационных и экономических особенностей производства, обусловленных широтой номенклатуры, регулярностью, стабильностью и объемом выпуска продукции. Основным показателем, характеризующим тип производства, является коэффициент закрепления операций Кз. Коэффициент закрепления операций для группы рабочих мест определяется как отношение числа всех различных технологических операций, выполненных или подлежащих выполнению в течение месяца, к числу рабочих мест. для единичного производства — больше 40;
для мелкосерийного производства — 20-40;
для среднесерийного производства — 10-20;
для крупносерийного производства — 1-10;
для массового производства — не больше 1.
Билет 20
1 Мероприятия по компенсации упругих деформаций в системе СПИД.
Технологическая система (станок, приспособление, инструмент, деталь) представляет собой упругую систему, в которой влияние сил резания и закрепления, инерционных и других сил приводит к образованию погрешностей форм и размеров обрабатываемых деталей.
На рисунке представлены две схемы обработки цилиндрической детали: с закреплением в центрах ("а") и в трехкулачковом токарном патроне ("б"), которые иллюстрируют возникающие упругие деформации , а также обусловленные ими погрешности формы детали (бочкообразность и конусообразность).
Упругие деформации обусловлены отжатиями основных узлов и отдельных элементов технологической системы, а также контактными деформациями и в общем случае могут достигать 20…40% от суммарной погрешности обработки.
Нестабильность сил резания (из-за колебаний снимаемого припуска твердости материала даже в пределах обрабатываемой партии деталей), различная жесткость детали при обработке (в каждый из моментов времени обработки поверхности детали) - обуславливают и неравномерность упругих деформаций.
Для количественной оценки упругих деформаций технологической системы используют понятия жесткость и податливость.
Жесткостью системы называется способность системы оказывать сопротивление деформирующим силам.
По А.П. Соколовскому, жесткость технологической системы определяется как отношение составляющей силы резания, направленной по нормали к обрабатываемой поверхности, к смещению режущей кромки инструмента относительно обрабатываемой поверхности заготовки в том же направлении:
где jсист - жесткость технологической системы, Н/мм;
РУ - радиальная составляющая силы резания, Н;
У - упругие деформации технологической системы (смещение режущей кромки инструмента), мм.
Для удобства расчетов часто используется величина обратная жесткости, которая называется податливостью.
Податливость технологической системы - способность этой системы упруго деформироваться под действием прикладываемых к ней внешних сил:
Суммарная податливость системы равна сумме податливостей элементов технологической системы:
Откуда жесткость системы будет равна:
Жесткость - величина непостоянная J = const
Ру - рассчитывается по формулам теории резания, а величина у определяется экспериментально.
Jст - жесткость станка и т. д.
W - податливость (величина, обратная жесткости).
Жесткость новых станков токарной группы составляет Jст = 20000 - 40000 Н/мм, для некоторых типов станков Jст = 100000 Н/мм (шлифовальные и координатно-расточные станки).
Таким образом, погрешности от упругих деформаций зависят, и определяется жесткостью технологической системы СПИД.
В практических расчетах учитывают только податливость станка и обрабатываемой детали
Величина упругих деформаций обрабатываемых деталей в значительной степени зависит от схемы обработки, ее можно рассчитать по известным зависимостям из курса сопротивления материалов. Так, для заготовки, закрепленной в патроне и поддерживаемой центром, максимальные упругие деформации определяют по формуле:
где, l - длина заготовки, мм;
E - модуль упругости 1-го рода, H/мм2;
J - момент инерции поперечного сечения заготовки, мм2 (для круглых заготовок J = 0,05d4);
d - номинальный диаметр детали, мм.
Тогда жесткость заготовки будет равна:
Величину радиальной составляющей силы резания рассчитывают по одной из формул курса "Теория резания" или находят по справочнику технолога-машиностроителя. Например, для токарных операций:
где Су - эмпирический коэффициент;
S - подача, мм/об;
t - глубина резания, мм;
HB - твердость материала заготовки;
x, m, n - показатели степени.
Жесткость всех составляющих элементов технологической системы, как правило, определяют экспериментально или по паспортным данным станка. Среднестатистическая жесткость новых станков составляет jст = 2000 - 40000 Н/мм (до 100000 Н/мм), а для выработавших свой ресурс - менее 10000 Н/мм.
Производственные методы оценки жесткости.
Различают понятия "статическая жесткость" и "динамическая жесткость".
Статическая жесткость оценивается на неработающем станке (в статике), а динамическая жесткость - при работающем станке (в динамике).
Оценка динамической жесткости технологической системы применяют три метода: ступенчатого резания; прямой и обратной подачи; фактической глубины резания.
Применение многокулачковых патронов позволяет повысить жесткость системы
2 Методы оценки шероховатости поверхности с использованием параметров объёмной оценки
Делается объемный снимок поверхности, по возможности увеличивается, проводятся базовые линии под разными углами, для комплексной оценки шероховатости
3 Режимы резания
1. Глубина резания (t) – величина срезаемого слоя за один проход, измеренная в направлении, перпендикулярном. Глубина резания всегда перпендикулярна направлению движения подачи.
2. Подача (s) – величина перемещения режущей кромки относительно обработанной поверхности в единицу времени в направлении движения подачи.
Для Ra = 1,25 ÷ 0,63 мкм при обработке стали резцом с радиусом при вершине r = 1 мм
s = 0,06 ÷ 0,12 мм/об.
Для достижения максимальной производительности берем s = 0,12 мм/об.
3. Скорость резания (ν) – величина перемещения точки режущей кромки относительно поверхности резания в единицу времени в процессе осуществления движения резания.
, м/мин
Дата добавления: 2018-05-02; просмотров: 997; Мы поможем в написании вашей работы! |
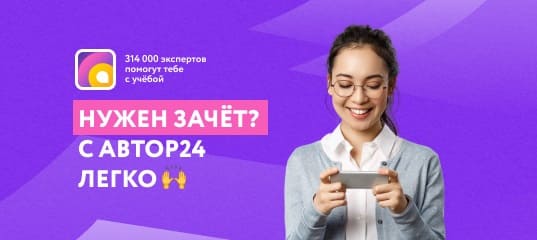
Мы поможем в написании ваших работ!