ОСНОВНЫЕ ФОРМУЛЫ ДЛЯ РАСЧЕТОВ
Министерство образования Российской Федерации
Санкт-Петербургская государственная лесотехническая академия
им С.М. Кирова
Сыктывкарский лесной институт
Кафедра «Общетехнических дисциплин»
Технологические процессы изготовления
Промышленных изделий
Курсовая работа
На тему: проектирование технологического процесса
изготовления детали
КР.ЛТФ.Д.170400.4.000220
Курсовая работа выполнена с оценкой:
Выполнил: студент 143 группы, МиОЛК
Мищенко Н. В.
Руководитель к.т.н., доцент: Кульминский А.Ф.
Сыктывкар 2003
Содержание
Введение
1.Размерный анализ
2.Составление технологического процесса механической обработки детали
3.Базирование детали при обработке
4.Определение размеров заготовки для механической обработки
6.Расчет режимов обработки детали
7.Нормирование станочных работ механической обработки детали
Заключение
Список литературы
Введение
Обработка материалов с помощью кремниевых резцов была известна с древних времен. Привод заготовок осуществлялся вручную. Первые токарные и сверлильные станки появились ещё в 12 веке в странах Западной Европы. В России первый станок появился в 1711году.
|
|
Современный уровень технического прогресса, непрерывное создание новых совершенных высокопроизводительных, автоматизированных и высокоточных машин, основанных на использовании новейших достижений науки, требуют подготовки высокообразованных инженеров, и определяет технический прогресс страны и оказывает решающее влияние на создание материальной базы нового общества.
Технология машиностроительного производства представляет собой совокупность различных технологических процессов (литья, ковки, штамповки, термообработки, покраски). Технология машиностроения охватывает заключительные стадии машиностроительного производства, то есть превращение заготовок в готовые изделия и на сборку.
Технологическим процессом называется часть производственного процесса, во время которого происходит изменение качественного состояния объекта производства (материала, заготовки, детали и машины). технологический процесс разделяется на операции. Технологической операцией называется часть технологического процесса, выполняемая на одном рабочем месте и охватывающая все действия оборудования и рабочих над одним или несколькими совместно обрабатываемыми или собираемыми предметами. Технологические операции расчленяются на переходы, установки и позиции. Под переходами применительно к механической обработке резанием применяется законченный процесс получения каждой новой поверхности или их сочетания при обработке одним режущим инструментом. Установкой технологической операции называется изменение положения заготовки относительно оборудования и элементов крепления с последующим закреплением и продолжением обработки на том же станке. Под позицией понимается изменение положения заготовки относительно станка или режущего инструмента совместно с приспособлением с последующим закреплением новой установки (позиции) и продолжение обработки на том же оборудовании.
|
|
Любая деталь при одном и том же виде и форме заготовки может быть обработана по различной технологии. Основная задача технолога заключается в том, чтобы из возможных вариантов выбрать такой, какой бы обеспечивал наименьшую стоимость при выполнении всех требований к точности готовой детали.
Размерный анализ
Содержит расчет размерной цепи способом полной взаимозаменяемости (метод максимума-минимума), а также анализ точности изготовления.
|
|
Определим предельные отклонения основного размера на наиболее ответственный размер детали.
Исходные данные:
Схема размерной цепи:
Уравнение размерной цепи:
Из уравнения размерной цепи определим номинальное значение замыкающего звена
Составим уравнения предельных значений замыкающего звена:
Вычислим предельные значения замыкающего звена:
Допуск замыкающего звена:
Произведем проверку:
Условие выполняется, таким образом, размер замыкающего звена
Разработка маршрута изготовления детали.
Разработка маршрута изготовления детали является основным разделом данной работы. Он выполняется в соответствии с требованиями ЕСКД которая допускает сокращенное описание всех технологических операций в последовательности выполнения. Маршрутное описание технологического процесса обычно является основным в единичном и мелкосерийном производствах и сопроводительным (дополнительным) в других типах производств.
Исходными данными для разработки маршрута изготовления деталей являются: чертеж детали с техническими требованиями, габаритный чертеж заготовки, ранее установленный тип производства, ранее выполненная отработка технологичности конструкции детали, предварительно определенные маршруты (планы) обработки отдельных поверхностей, ранее выбранные технологические базы с предварительно намеченным планом обработки заготовки. Разработка маршрута - сложная задача с большим количеством вариантов ее решения.
|
|
Деталь – крышка. За исходный материал возьмем .
Технологический маршрут механической обработки детали отображен в таблице 2.1.
|
№ п/п | Наименование операций и переходов | Оборудование | Методы базирования | |
операция | переход | |||
I | 1 2 | Заготовительная Установка, выверка и закрепление Отрезка заготовки | Механический пресс | |
II | 1 2 | Кузнечная Нагрев заготовки Поковка внешнего контура | ||
III | 1 2 3 4 5 | Токарная 1
Установка, выверка и
закрепление
подрезка торца Ø30мм
черновая
подрезка торца Ø30мм
получистовая
снятие фаски 2,5 ![]() | Токарный станок | За наружный диаметр |
IV | 1 2 3 4 5 | Токарная 2 Установка, выверка и закрепление подрезка торца Ø60мм черновая подрезка торца Ø60мм получистовая подрезка торца Ø60мм чистовая подрезка торца Ø60мм тонкая | Токарный станок | За наружный диаметр |
6 | изготовление центрового отверстия | |||
V | 1 2 3 4 5 6 7 8 9 10 11 12 13 14 15 | Токарная 3
Установка, выверка и
закрепление
подрезка торца Ø65мм
черновая с прорезкой канавки 5 ![]() ![]() ![]() ![]() ![]() | Токарный станок | в центрах |
VI VII VIII | 1 2 3 4 5 1 2 1 | Сверлильная
Установка, выверка и закрепление
Разметка отверстия Ø28мм
Разметка отверстия Ø6,3мм
Сверление отверстия Ø28мм
Сверление отверстия Ø28мм
Токарная 4
Установка, выверка и
закрепление
нарезка резьбы М30-6д
нарезка резьбы Tr65 ![]() | Универсальный сверлильный станок | За наружный диаметр |
IX | Контроль ОТК |
Базирование детали при обработке
Для правильной работы каждой машины необходимо обеспечить определенное взаимное расположение ее деталей и узлов.
При обработке деталей на станках заготовки также должны быть правильно ориентированы относительно механизмов и узлов станков, определяющих траектории движения подачи обрабатывающих инструментов (направляющих суппортов, фрезерных и резцовых головок, упоров, копировальных устройств и др.). Погрешности формы и размеров обработанных заготовок определяются отклонениями положений режущих кромок и заготовок от траектории заданного формообразующего движения. Задачи взаимной ориентировки деталей и сборочных единиц в машинах при их сборке и заготовок на станках при изготовлении деталей решаются их базированием.
В общем случае базированием называется придание заготовке или изделию требуемого положения относительно выбранной системы координат (ГОСТ 21495—76). Применительно к проектированию или сборке под базированием понимают придание детали или сборочной единице требуемого положения относительно других деталей изделия. При механической обработке заготовок на станках базированием принято считать придание заготовке требуемого положения относительно элементов станка, определяющих траектории-движения подачи обрабатывающего инструмента.
Для выполнения технологической операции требуется не только осуществить базирование обрабатываемой заготовки, но также необходимо обеспечить ее неподвижность относительно приспособления на весь период обработки, гарантирующую сохранение неизменной ориентировки заготовки и нормальное протекание процесса обработки. В связи с этим при установке заготовок в приспособлениях решаются две различные задачи: ориентировка, осуществляемая базированием, и создание неподвижности, достигаемое закреплением заготовок. Несмотря на различие этих задач, они решаются теоретически одинаковыми методами, т. е. посредством наложения определенных ограничений (связей) на возможные перемещения заготовки (механической системы) в пространстве.
Операции:
“Заготовительная” операция осуществляется на механическом прессе. Базирование осуществляется на плоскости.
“Кузнечная ” операция осуществляется в нагревательной печи. Базирование осуществляется за наружный диаметр.
“Токарная 1” операция осуществляется на токарном станке. Заготовка закрепляется в 3-кулачковом патроне. Базирование осуществляетя за наружный диаметр Ø133,26.
“Токарная 2” операция осуществляется на токарном станке. Заготовка закрепляется в 3-кулачковом патроне за наружный диаметр Ø80.
Операция “сверление” осуществляется на универсальном сверлильном станке. Заготовка закрепляется в тисках за наружный диаметр Ø126 мм.
Определение размеров заготовки для механической обработки.
Включает определение размеров заготовки для механической обработки, предусматривает установление межоперационных припусков и допусков на механическую обработку, составление эскиза заготовки и определение коэффициента использования материала.
Необходимо усвоить, что размеры заготовки должны быть достаточными дня качественного изготовления и не слишком большими, чтобы не увеличивать время на механическую обработку и потери металла в стружку.
Расчет промежуточных припусков и допусков при определении размеров выполняется для литых заготовок на поверхности, подлежащей обработке, для стальных заготовок, которые выполняются в виде поковок или сортового проката — на основные поверхности и размеры (максимальный диаметр, длина прутка, диаметр и длина поковки, толщина фланца, диаметр отверстия и т. д.)-
Методика определения припусков и допусков на обработку основывается на использовании имеющегося справочного материала. Согласно этой методике расчет начинается с последней (отделочной) операции, далее последовательно определяются припуски и допуски на всех проходах, которые затем суммируются.
Все данные заносим в таблицу 4.1
Таблица 4.1
Определя- емый раз- мер, мм |
Метод обработки | Припуск, мм | Допуск, мм | ||
частный | общий | частный | общий | ||
Ø30 | Обтачивание черновое получистовое чистовое | | 0,34 0,17 0,085 | 0,595 | |
Ø65 | Обтачивание черновое получистовое чистовое | 2,3 0,5 0,3 | 3,1 | 0,4 0,2 0,1 | 0,7 |
Ø70 | Обтачивание черновое получистовое | 2,3 0,5 | 2,8 | 0,4 0,2 | 0,6 |
Ø6,3 | Растачивание черновое получистовое | 0,24 0,12 | 0,36 | ||
Ø28 | Растачивание черновое получистовое | 0,28 0,14 | 0,42 | ||
Ø60 | Обтачивание черновое получистовое чистовое | 2,3 0,5 0,3 | 3,1 | 0,4 0,2 0,1 | 0,7 |
Ø30 | Подрезка торца черновая получистовая | 0,9 0,45 | 1,35 | 0,34 0,17 | 0,51 |
Ø70 | Подрезка торца черновая получистовая | 1,3 0,65 | 1,95 | 0,4 0,2 | 0,6 |
Размеры заготовки определяются по следующим формулам:
,
“+” – при обточке заготовки;
“ ” – при расточке заготовки;
- диаметр заготовки, мм;
D – номинальный размер детали, мм;
- припуски на отдельные проходы на сторону, мм;
- допуски на отдельные проходы на сторону, мм.
Припуски и допуски назначаем по таблицам 6, 7, 8, 10 .
Определим размеры заготовки:
Определим коэффициент использования материала
где
- масса детали, кг;
- масса заготовки, кг;
где
- плотность материала,
;
V- объем заготовки, ;
Vобщ = 1740987,688 мм3 = 17
Режимы резания при механической обработке.
Раздел содержит выбор и расчет параметров резания в соответствии с разработанным маршрутом изготовления, состоит в определении глубины резания, числа проходов, величин подачи, скоростей резания с последующей проверкой полученных (или принимаемых) значений по имеющейся мощности привода механизма резания и подачи станка и прочности наиболее слабого звена (инструмента, деталей его крепления и др.).
ОСНОВНЫЕ ФОРМУЛЫ ДЛЯ РАСЧЕТОВ
Скорость резания в м/с -при обточке ;
- при расточке ;
- при прорезке и отрезке , где t – глубина резания, мм;
S – подача, мм – назначаем по таблицам 6.1, 6.2, 6.3 ;
- коэффициенты и показатели степени –назначаем по таблице 6. 5
.
Окружная сила и мощность резания
, где
- окружная сила, Н;
- коэффициенты и показатели степени – принимаем по таблице 6. 10
;
- поправочные коэффициенты; их значения условно принимаем равным единице.
, где
- эффективная мощность, Вт.
Результаты вычислений заносим в таблицу 5.1.
|
Размер, мм |
Метод обработки | Глуби-на реза- ния, t,мм | Подача, S,
| Значения коэффици-ентов | Ско- рость реза-ния, | Значения коэффици-ентов | Окруж-ная сила, | Мощ-ность на резание | |||||
![]() | ![]() | ![]() | ![]() | ![]() | ![]() | ![]() | |||||||
Ø Ø 30 | Обточка черновая получистовая чистовая | 0,34 0,17 0,085 | 0,6 0,3 0,15 | 31,6 31,6 31,6 | 0,25 0,25 0,25 | 0,66 0,66 0,66 | 0,966 1,8 3,4 | 300 300 300 | 1 1 1 | 0,75 0,75 0,75 | 0,15 0,15 0,15 | 677,9 221 72,37 | 654,85 397,8 246 |
Ø65 | Обточка черновая получистовая чистовая | 2,7 0,7 0,4 | 1 0,3 0,15 | 31,6 31,6 31,6 | 0,25 0,25 0,25 | 0,66 0,66 0,66 | 0,41 1,27 2,3 | 300 300 300 | 1 1 1 | 0,75 0,75 0,75 | 0,15 0,15 0,15 | 6944,3 864,68 321,17 | 2847 1098 738,69 |
Ø70 | Обточка черновая получистовая | 2,7 0,7 | 1 0,3 | 31,6 31,6 | 0,25 0,25 | 0,66 0,66 | 0,41 1,27 | 300 300 | 1 1 | 0,75 0,75 | 0,15 0,15 | 6944,3 864,68 | 2847 1098 |
Ø6,3 | Расточка черновая получистовая | 0,24 0,12 | 0,08 0,04 | 49,9 49,9 | 0,25 0,25 | 0,33 0,33 | 2,73 4,1 | 300 300 | 1 1 | 0,75 0,75 | 0,15 0,15 | 123,4 38,99 | 336,88 159,86 |
Ø28 | Расточка черновая получистовая | 0,28 0,14 | 0,2 0,1 | 49,9 49,9 | 0,25 0,25 | 0,33 0,33 | 1,9 2,9 | 300 300 | 1 1 | 0,75 0,75 | 0,15 0,15 | 271 85,9 | 514,9 249 |
Ø60 | Обточка черновая получистовая чистовая | 2,7 0,7 0,4 | 1 0,3 0,15 | 31,6 31,6 31,6 | 0,25 0,25 0,25 | 0,66 0,66 0,66 | 0,41 1,27 2,3 | 300 300 300 | 1 1 1 | 0,75 0,75 0,75 | 0,15 0,15 0,15 | 6944,3 864,68 321,17 | 2847 1098 738,69 |
Ø30 | Подрезка черновая получистовая | 1,24 0,62 | 0,4 0,2 | 5,4 5,4 | - - | 0,5 0,5 | 0,1 0,2 | 247 247 | 1 1 | 1 1 | 0 0 | 1200,6 300 | 120 60 |
Ø70 | Подрезка черновая получистовая | 1,7 0,85 | 1 0,5 | 5,4 5,4 | - - | 0,5 0,5 | 0,09 0,13 | 247 247 | 1 1 | 1 1 | 0 0 | 4115 1028,76 | 370,35 133,7 |
Полная мощность, затрачиваемая только на полезную работу, Вт | 16555,7 |
Нормирование станочных работ механической обработки деталей.
Основные формулы для вычислений:
Норма технического времени
-при точении и растачивании напроход
где
l – длина обрабатываемой поверхности, мм;
- длина врезания, мм;
- длина перебега резца, мм;
t – глубина резания, мм;
S – подача, мм;
i – число проходов, принимаем i=1;
-главный угол в плане, град. , принимаем
n –частота вращения обрабатываемой детали, об/мин,
где
- скорость, м/мин;
r – радиус заготовки, на котором производится операция, м.
-при точении и растачивании в упор
-при отрезании и подрезании торца
, где
или
,
Норма оперативного времени для данной операции , мин
, где
- норма вспомогательного времени на той же операции или переходе, мин.
Вспомогательное время – часть штучного времени, затрачиваемое на выполнение приемов, которые необходимы для обеспечения изменения и для последующего определения состояния предмета труда.
Штучное время – это интервал времени, равный отношению цикла технологической операции к числу одновременно изготовляемых или ремонтируемых изделий.
Норма штучного времени , мин
, где
х – количество деталей, которое можно выполнить за смену;
- норма времени на отдых;
=15мин/смена - норма времени на обслуживание рабочего места.
, где
- время одной смены, мин.
Техническая норма времени операции , мин
, где
|

Расчетные данные заносим в таблицу 6.1.
Размер, мм | Метод обработки | Ско-
рость реза-ния, ![]() | Частота враще-ния, n, об/мин | Подача, S,
![]() | Норма техноло-
гическо-го време-
ни, ![]() | Норма оперативного вре-
мени,
![]() | Норма штучного време-ни, ![]() | Норма технического време-ни, ![]() |
Ø Ø 30 | Обточка черновая получистовая чистовая | 0,966 1,8 3,4 | 603 1136 2158,39 | 0,6 0,3 0,15 | 0,15 0,156 0,16 | 1,27 1,276 1,28 |
47,7 |
48,2 |
Ø65 | Обточка черновая получистовая чистовая | 0,41 1,27 2,3 | 113,8 362 671,66 | 1 0,3 0,15 | 6,496 4 4,368 | 7,6 5,12 5,49 | ||
Ø70 | Обточка черновая получистовая | 0,41 1,27 | 106,68 343 | 1 0,3 | 1,77 1,07 | 2,89 2,19 | ||
Ø60 | Обточка черновая получистовая чистовая | 0,41 1,27 2,3 | 122,7 396,97 727,3 | 1 0,3 0,15 | 0,4 0,42 0,46 | 1,52 1,54 1,58 | ||
Ø30 | Подрезка черновая получистовая | 0,1 0,2 | 59,9 124,7 | 0,4 0,2 | 0,79 0,75 | 1,91 1,87 | ||
Ø70 | Подрезка черновая получистовая | 0,09 0,13 | 23,69 35 | 1 0,5 | 3,8 5,1 | 4,92 5,22 |
Принимаем 8-ми часовую смену.
Принимаем х=8
Заключение
При выполнении данной курсовой работы были выполнены следующие задачи: анализ чертежа и составление размерной цепи, разработка маршрута изготовления детали.
Определение размеров заготовки для механической обработки, определение параметров резания при механической обработке, нормирование станочных работ механической обработки.
Список литературы
1.“Технологические процессы изготовления промышленных изделий” –методические указания по выполнению курсовой работы / Составитель: Кульминский А. Ф.; Сыктывкар; 2003г.
2.“Технология машиностроения” – лабораторный практикум / Под редакцией Малышева Ю. В.; Ленинград; 1989г.
3.“Технология машиностроения”-учебник для ВУЗов / Под редакцией Металина А. А.; Ленинград; 1985г.
Дата добавления: 2018-05-02; просмотров: 310; Мы поможем в написании вашей работы! |
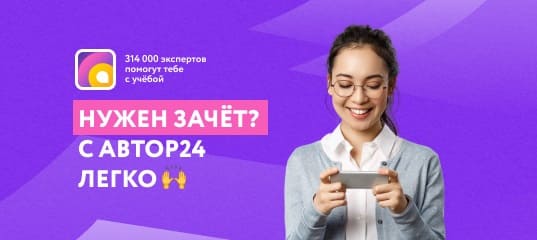
Мы поможем в написании ваших работ!