СПИСОК РЕКОМЕНДУЕМОЙ ЛИТЕРАТУРЫ
СЛОВАРЬ ТЕРМИНОВ
Братухин А.Г., Сироткин О.С., Сабодаш П.Ф. Материалы будущего и их удивительные свойства. - М.: Машиностроение, 1995. - 128 с.
Бушуев Ю.Г., Персии М.И., Соколов В.А. Углерод-углеродные композиционные материалы: Справочник. — М.: Металлургия, 1994. - 138 с.
Волоконная технология переработки термопластичных композиционных материалов / Головкин Г.С, Гончаренко В.А., Дмитриенко В.П. и др.; Под ред. Г.С. Головкина. - М.: Изд-во МАИ, 1993. - 232 с.
Воробей В.В., Сироткин О. С. Соединения конструкций из композиционных материалов. — М.: Машиностроение, 1985. — 166 с.
Воробей ВВ., Морозов Е.В., Татарников О.В. Расчет термонапряженных конструкций из композиционных материалов. - М.: Машиностроение, 1992. -238 с.
Калинчев В.А., Буланов И.М. Прогрессивные материалы в машиностроении: Учебное пособие для СПТУ. — М.: Высш. шк., 1988. — 71 с.
Композиционные материалы: Справочник / Васильев В.В., Протасов В.Д., Болотин В.В. и др.; Под общей редакцией В.В. Васильева, Ю.М. Тарнополь-ского. — М.: Машиностроение, 1990. — 512 с.
Крысин В.Н., Крысин М.В. Технологические процессы формования, намотки и склеивания конструкций. - М.: Машиностроение, 1989. - 240 с.
Основы проектирования и изготовления конструкций летательных аппаратов из композиционных материалов / Васильев В.В., Добряков А.А., Дуд-ченко А.П. и др. - М.: Изд-во МАИ, 1985. - 218 с.
Справочник по композиционным материалам: В 2 кн./ Пер. с англ. А.Б. Геллера и др.; Под ред. Дж. Любина. — М.: Машиностроение, 1988. -584 с.
|
|
506
Абляция— процесс массо- и теплопереноса, обеспечивающий отвод большого количества теплоты из поверхностных слоев материала, которая поглощается, рассеивается или преобразуется окружающим пространством посредством различных физических механизмов.
Автоклав— герметически закрывающийся аппарат, позволяющий проводить отверждение композитов при нафеве и под действием давления выше атмосферного.
Адгезия- прилипание. Явление, при котором две поверхности разнородных тел соединены вместе за счет поверхностных сил или других механизмов сцепления.
Анизотропия— неодинаковость количественных характеристик физико-механических и тепловых свойств материала по различным направлениям.
Антиадгезив— химическое покрытие или пленка, которые используются для существенного уменьшения прилипания одного твердого тела к другому, проявляющегося при контакте.
Армирование— усиление материала, заключающееся во введении в пластмассу армирующего материала для регулирования ее физико-механических и тепловых характеристик.
Волокно первичное— гибкое и прочное протяженное тело с малыми поперечными .размерами, не бывшее в контакте с какими-либо другими волокнами или твердыми материалами.
|
|
Волокно штапельное— волокно, получаемое резкой непрерывного жгута, состоящего из множества нитей, на отрезки определенной длины (обычно от 12 до 50 мм).
Время отверждения(полимеризации) — отрезок времени, необходимый для перехода жидких олигомеров в твердые поли-
507
Словарь терминов
меры, в течение которого формуемый материал подвергается воздействию теплоты или давления либо того и другого вместе.
Гель- дисперсная, желеобразная система, обладающая некоторыми своствами твердых тел, образующаяся из жидких компонентов связующей полимерной матрицы в процессе полимеризации.
Геодезическая кривая- наикратчайшее расстояние между двумя точками поверхности.
Герметизирующие материалы- материалы, обеспечивающие непроницаемость жидкостей или газов в конструкциях.
Грат— излишки материала, остающиеся на кромках изделий после операции формования. Приспособление к пресс-форме для удаления из полосы формы избытка материала.
Графитизация- стадия технологического процесса получения углеродных волокон и углерод-углеродных композиционных материалов, при которой волокно и матрица подвергаются высокотемпературной обработке в инертной среде при 2600...2800 °С с образованием графитной структуры.
|
|
Диффузионная сварка -процесс получения неразъемного соединения, при котором под воздействием нагрева и давления формования происходит диффузия атомов контактирующих материалов и образуется структура, близкая к структуре соединяемых материалов.
Длина базовая— длина той части образца, на которой измеряются его характеристики при испытаниях.
Жгут- совокупность (пучок) крученых или некрученых нитей различной линейной плотности.
Карбонизация— стадия технологического процесса получения углеродных волокон и углерод-углеродных композиционных материалов, при которой волокно и матрица подвергаются обработке в инертной среде при температуре 1000... 1500 °С, в результате чего из материала удаляются все элементы, кроме углерода.
Когезия- сцепление. Явление притяжения между частицами одного и того же твердого тела или жидкости, приводящие к объединению этих частиц в единое тело.
Комплексная нить - нить, состоящая из совокупности (сложений) отдельных первичных волокон.
Крутка- число витков волокна или нитей на 1 метр их длины.
Ламинат - слоистый пластик, полученный горячим прессованием связующей и армирующей компонент композиционного материала в виде листового материала.
|
|
Лейнер- внутренняя оболочка бака, сосуда давления, трубопровода (металлическая, эластичная, термопластичная, пленочная и др.), предназначенная для предотвращения утечек жидкости или газа из конструкции.
Мат- волокнистый нетканый материал, состоящий из произвольно ориентированных волокон или спутанных нитей и пропитанный соответствующим связующим.
Опрессовка:1) технический способ уплотнения намотанного на жесткую оправку КМ посредством внутреннего или наружного давления; 2) нагружение готового изделия давлением, меньшим чем рабочее давление или равным ему.
Отверждение послойное— частичное или полное отверждение намотанного слоя перед намоткой следующего слоя с целью уменьшения податливости намотанных витков.
Пиролиз - высокотемпературное превращение органических соединений, сопровождающееся их деструкцией и вторичными процессами.
Подложка - твердое тело, на которое одним из технологических методов, например напылением, осаждением и т.п., наносится материал, связанный с твердым телом только адгезионными связями. Подложка может быть частью конструкции, оправкой, формой.
Пористость - отношение объема пор и пустот, содержащихся в объеме материала, к общему объему тела, выраженное в процентах.
Премикс- термореактивная формовочная композиция, армированная волокном, которая не нуждается в дальнейшем отверждении, сушке или других технологических операциях и готова для переработки на литьевом прессе.
508
509
Словарь терминов
Проницаемость— диффузия газа, паров или жидкости через материал без физического или химического воздействия на него.
Разнодлинность(провис) — разница в длинах прядей волокон, составляющих ровинг (жгут) на определенном отрезке, которая возникает в результате неравномерного натяжения. Визуально отдельные составляющие пряди в жгуте провисают при его горизонтальном натяжении.
Ровинг— жгут, образованный пучками непрерывных нитей в виде некрученых жгутов или крученых нитей. При намотке используется в виде лент с минимальной круткой.
Сварка взрывом— процесс получения неразъемного соединения КМ под воздействием импульса высокого давления, развиваемого взрывчатым веществом.
Сосуд модельный— конструкция в виде цилиндра с днищами, изготавливаемая методом намотки и предназначенная для отработки технологии изготовления и оценки физико-механических характеристик материала.
Стренги(пучки) — первичный пучок непрерывных нитей (или лент), собранных в единый компактный жгут без крутки.
Усадка- уменьшение объема тела при переходе из жидкого состояния в твердое при полимеризации.
Усы— нитевидные искусственные монокристаллы, выращенные в специальных условиях и имеющие механическую прочность, эквивалентную прочности связи между атомами.
Фильера— тип экструзионного приспособления. Обычно металлическая пластина со множеством мелких отверстий (до 7 мкм), через которые продавливается расплав или раствор полимера для получения волокон. В пултрузии — формующая матрица; в намотке — направляющее очко для пряди нитей, ленты.
Химическая сварка - процесс получения неразъемного соединения пластмасс или КМ, образуемого химическими связями либо непосредственно между функциональными группами контактирующих поверхностей полимеров, либо с помощью
промежуточных молекулярных образований (присадочных реагентов), вводимых в зону сварного шва.
Шпулярник— приспособление для установки необходимого количества паковок (бобин, шпуль) с волокнистым материалом, часть технологического оборудования процессов намотки, пултрузии, автоматизированной выкладки и т.п.
510
ОГЛАВЛЕНИЕ
Предисловие........................................................................................................ 5
Основные сокращения и условные обозначения..................................... 7
Введение.............................................................................................................. 9
1. Композиционные материалы и их компоненты............................................... 14
1.1. Общие понятия и определения..................................................... 14
1.2. Армирующие волокнистые наполнители.................................... 18
1.3. Матричные материалы.................................................................. 47
1.4. Полимерные композиционные материалы.................................. 66
1.5. Металлические композиционные материалы.............................. 76
1.6. Углерод-углеродные композиционные материалы.................... 90
1.7 Керамические композиционные материалы ......................... 106
1.8. Гибридные композиционные материалы.................................... 109
Ключевые вопросы.............................................................................. 115
2. Технология изготовления конструкций из полимерных
композиционных материалов.............................................................................. 117
2.1. Понятие о конструкторско-технологическом решении . . . . 117
2.2. Общая характеристика технологических процессов.................. 122
2.3. Контактное формование............................................................... 130
2.4. Формование с эластичной диафрагмой....................................... 140
2.5. Особенности конструирования деталей с учетом технологии контактного формования и формования
с эластичной диафрагмой ............................................................... 149
2.6. Формообразование давлением..................................................... 152
2.7. Формообразование прессованием в формах ......................... 156
2.8. Формообразование намоткой...................................................... 175
2.9. Формообразование пултрузией................................................... 216
2.10. Технологии предварительного формования заготовок,
деталей и матов ................................................................................. 223
Ключевые вопросы.............................................................................. 229
3. Технология изготовления конструкций из металлических и углерод-
углеродных композиционных материалов. Способы обработки.......... 231
3.1. Жидкофазные методы изготовления деталей
из металлокомпозитов.......................................................................... 231
3.2. Твердофазные методы изготовления деталей
изметаллокомпозитов......................................................................... 238
3.3. Газофазные методы изготовления деталей из композитов . . 253
3.4. Технология изготовления конструкций из углерод-углеродных материалов 264
3.5. Механическая обработка композитов.......................................... 273
Ключевые вопросы............................................................................... 287
4. Технология выполнения соединений конструкций из композиционных
материалов ........................................................................................................ 289
4.1. Классификация соединений........................................................... 289
4.2. Сплошные соединения.................................................................. 293
4.3. Механические соединения............................................................. 296
4.4. Комбинированные соединения..................................................... 309
4.5. Технология образования отверстий, резьб и гнезд..................... 311
4.6. Технологические процессы клепки............................................... 326
4.7. Методы клепки .......................................................................... 327
4.8. Технология выполнения комбинированных клееклепаных соединений 330
4.9. Примеры выполнения соединений высоконагруженных узлов
и деталей................................................................................................ 332
Ключевые вопросы.............................................................................. 337
5. Методы испытаний и контроль качества конструкций
из композиционных материалов ....................................................................... 339
5.1. Общая характеристика испытаний............................................... 339
5.2. Определение свойств волокнистых армирующих
наполнителей .................................................................................... 345
5.3. Определение свойств матричных материалов............................ 349
5.4. Определение физических и структурных свойств композиционных материалов 352
5.5. Определение механических свойств композитов....................... 357
5.6. Контроль герметичности изделий из композиционных материалов 376
5.7. Определение теплофизических свойств композиционных материалов ....,, 383
512
513
5.8. Неразрушающие методы контроля деталей и узлов
из композитов....................................................................................... 390
Ключевые вопросы.............................................................................. 406
Дата добавления: 2018-05-02; просмотров: 394; Мы поможем в написании вашей работы! |
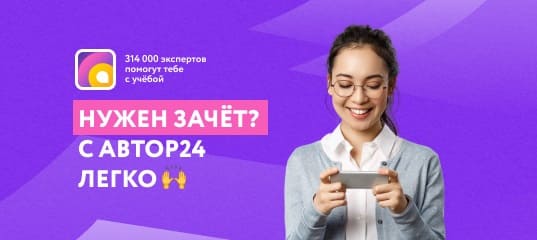
Мы поможем в написании ваших работ!