Относительные удлинения материалов, применяемых для изготовления оснастки при температуре до 204 С
Перед использованием формы покрывают антиадгезионным покрытием. В качестве антиадгезионных смазок, как и при контактном формовании, используют пастообразный парафин (до температуры 121 °С).
Фторированные углеводороды образуют на поверхности оправки сплошную пленку. Их эксплуатируют до температуры 177 °С, поскольку при более высоких температурах выделяется фтор, вредный как для здоровья, так и для материала формы.
Хорошим разделителем является политетрафторэтилен (тефлон). Частички тефлона, перешедшие в композит, легко удаляются с его поверхности растворителем.
При использовании термопластичных связующих (типа полиимидных), которые требуют высоких температур отверждения (до 300 °С), используют смазку на основе силановой смолы, которая стабильна до температуры 482 °С. Силиконовые смазки можно использовать только до температуры 204 °С, но они загрязняют отформованный композит.
Смазки антиадгезивом обычно возобновляют после 4—5 запрессовок. Во избежание прилипания изделия на поверхность формы можно наносить смазку на основе ПВС или пленку
2, ТЕХНОЛОГИЯ КОНСТРУКЦИЙ ИЗ ПОЛИМЕРНЫХ КОМПОЗИЦИЙ
целлофана. Целлофан рекомендуется укладывать полосами, чтобы получить хорошее прилегание к поверхности, имеющей кривизну. Обычно целлофан приклеивают раствором ПВС в смеси воды с этиловым спиртом, после чего его смачивают водой. При высыхании вследствие усадки целлофана последний натягивается и плотно облегает форму. На подготовленную таким образом поверхность наносят поочередно слои предварительно пропитанной ткани или мата, которые тщательно прикатываются роликом к форме и между собой с целью создания контакта и удаления оставшегося воздуха.
|
|
На уложенную поверхность заготовки изделия выкладывают разделительные дренажные ткани или пленки, которые могут выполнять функции наружной поверхности отформованного изделия 'или абсорбировать избыток смолы из материала в процессе его отверждения. В некоторых случаях на разделительный слой помещают пористые впитывающие слои стекло-матов или стеклотканей, а поверх них — перфорированные слои пленки или грубой ткани, выполняющие вентиляционные функции и обеспечивающие неприлипаемость эластичного мешка к пакету.
Иногда в качестве разделительного слоя используют цулагу. Цулага представляет собой тонкую обшивку (0,5...1,5 мм) из алюминиевого сплава типа АМЦ, у которой поверхность соответствует контурам формуемого изделия. Для цулаги возможно также применение текстолита или стеклотекстолита толщиной 0,8...2 мм. Собранную таким или иным образом форму с заготовкой помещают либо в эластичный мешок, либо закрывают чехлом, прижимая его по периферии на плите формы, обеспечивая герметичность собранного пакета. Схема подготовленного к вакуумному формованию изделия показана на рис. 2.11.
|
|
Вакуумный мешок — это многослойная система, которая обеспечивает равномерное распределение давления во всех зонах формуемого изделия и исключает образование застойных зон, вызывающих недопрессовку материала. Материал диафрагмы прежде всего должен выдерживать температуру горячего отверждения и обладать невысокой газопроницаемостью для обеспечения постоянства давления при формовании и в конечном счете качества изделия. Наиболее пригодными материалами для эластичной диафрагмы являются резины, однако
142 143
2.4. Формование с эластичной диафрагмой
их срок службы небольшой, так как они разрушаются под воздействием смол и высоких температур. Особенно важна проблема создания термостойких вакуумных мешков для формования термопластичных ПКМ, так как их температура формования находится в диапазоне от 250 до 340 °С.
|
|
10 10 8 7 6
Рис. 2.11.Схема вакуумирования формуемого изделия:
/ — оправка (вакуумный стол); 2 - формуемое изделие; 3 - ограничивающие бобышки; 4 — герметизирующий жгут-паста; 5 — разделительные дренажные пленки; 6 — вакуумный мешок; 7 - цулага с дренажными отверстиями; 8 — дренажный слой; 9 — компенсирующая складка; 10 — клапан вакуумной системы
На практике для изготовления эластичных диафрагм применяют резины особых марок, прорезиненные ткани, силок-сановый каучук, армированный стекловолокном, которые выдерживают температуру в диапазоне до 200 °С. В качестве материалов вакуумных мешков и чехлов можно использовать различные термостойкие пленки: полиимидные (до температур 316 °С), пленки полиамидные (до температур 230 °С), пленки из нейлона (до температуры 204 °С), пленки из поливинилового спирта (до температуры 121 °С).
Указанные пленки имеют низкую газопроницаемость даже по гелию (не более 0,7 м3/сут).
Применение пленочных мешков обеспечивает: стабильность параметров формования ПКМ; надежную герметичность мешка при формовании; целостность вакуумного мешка; достаточно высокую технологичность при демонтаже вакуумного мешка; высокую технологичность при изготовлении вакуумного мешка.
|
|
Для обеспечения герметизации заготовки, собранной под вакуумным мешком, разработано несколько конструктивно-
2. ТЕХНОЛОГИЯ КОНСТРУКЦИЙ ИЗ ПОЛИМЕРНЫХ КОМПОЗИЦИЙ
технологических схем. Необходимое уплотнение диафрагмы, обеспечивающее герметичность, реализуется вследствие применения герметизирующих жгутов и лент с двусторонней липкой основой (рис. 2.12, а), многоканавочных уплотнений (рис. 2.12, б) и наружной уплотняющей рамы (рис. 2.12, в).
Рис. 2.12.Конструктивно-технологические схемы обеспечения герметичности вакуумного мешка:
а — приклеивание с помощью жгута: / — вакуумный мешок; 2 - материал пористый; 3 — ткань разделительная; 4 — изделие формуемое; 5, 7 — плиты; 6 — жгут герметизирующий; б — многоканавочное уплотнение: 1 — взаимосвязанные канавки; 2~ компенсационный сальник; 3 - диафрагма из армированного стекловолокном силоксанового каучука; 4 — оснастка; 5 — вакуумная линия; 6 — вкладыш из мягкого силоксанового каучука; в - уплотняющая рама: / - вакуумная линия; 2 - винт; 3 - верхняя рама; 4 - нижняя рама; 5 -диафрагма; 6 — компенсационный сальник; 7 — оснастка; 8 - резиновые уплотнения
Основное внимание перед формованием следует уделить ликвидации утечек из-под диафрагмы путем герметизации ее по всему периметру термостойкими герметиками или мягкими хомутами. Штутцера для подсоединения к вакуумной линии обычно вплавляют или вклеивают внутрь диафрагмы при ее изготовлении. Количество штуцеров на вакуумном мешке определяется из условия равномерного обжатия формуемого из-
144
10-243
145
2.4. Формование с эластичной диафрагмой
делия. Для обеспечения равномерного вакуумирования под мешком на прилегающей к формуемому изделию торцевой части штуцера выполняют сквозные перекрестные пазы - вакуумные "ручьи".
При формовании под давлением диафрагмы используют в качестве емкости для сжатого газа, который выделяется из композита при отверждении. Если давление под диафрагмой соизмеримо с действием внешнего давления, диафрагма остается инертной, и уплотнение материала не происходит. Для создания пониженного давления под формуемым материалом предусмотрена система выпускных отверстий. Однако применение препрегов при формовании заготовок позволяет отверж-дать изделие под вакуумом без системы выпускных отверстий, что значительно снижает сложность и стоимость форм.
Дата добавления: 2018-05-02; просмотров: 619; Мы поможем в написании вашей работы! |
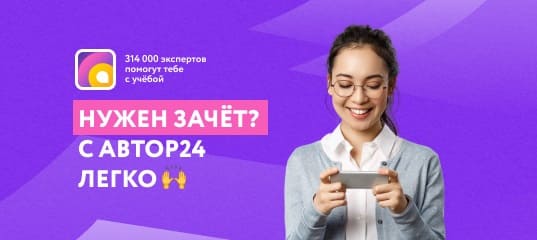
Мы поможем в написании ваших работ!