Отстойники с наклонными полками. Одно- и многоярусные отстойники непрерывного действия.
Конструкции фильтров: нутч-фильтр, плиточно-рамный фильтр-пресс, ФПАКМ, барабанный вакуум-фильтр с наружной фильтрующей поверхностью, ленточный вакуум-фильтр
Конструкции фильтровального оборудования весьма разнообразны. По режиму работы различают фильтры периодического и непрерывного действия. Для процессов фильтрования суспензий, частицы которых значительно закупоривают поры фильтрующей перегородки, используется периодическая фильтрация с очисткой (регенерацией) перегородки после каждой стадии фильтрации. Фильтры непрерывного действия работают, как правило, при постоянной разности давлений по обе стороны от фильтрующей перегородки.
По способу создания разности давлений различают вакуум-фильтры, в которых со стороны разделяемой суспензии давление атмосферное, а с другой стороны перегородки поддерживается разрежение, и фильтры, работающие под избыточным давлением, создаваемым со стороны суспензии, при этом со стороны фильтрата давление обычно бывает атмосферное.
Простейший фильтр периодического действия, так называемый нутч-фильтр, работающий чаще всего за счет создаваемого под перегородкой вакуума.
Как и при любой периодической фильтрации, после основного процесса фильтрования (или после также периодической промывки осадка, если она необходима) производится выгрузка осадка. В нутч-фильтрах эта операция совершается сверху вручную, поэтому такие фильтры используются в технологических линиях небольшой производительности по разделяемой суспензии.
|
|
Еще одна конструкция для периодической фильтрации, работающая под избыточным давлением до 1,0–1,2 МПа – это плиточно-рамный фильтр-пресс.
Аппарат состоит из чередующихся рам и плит , плотно прижимаемых друг к другу с помощью ручного или гидравлического устройства. Между каждой парой плита – рама зажата фильтрующая ткань (салфетка). В верхних частях плит и рам имеются отверстия, образующие при сборке всех плит и рам сплошной канал, по которому под избыточным давлением в полые объемы рам подается исходная суспензия.
Подействием избыточного давления сплошная жидкая фаза фильтруется через салфетки и оказывается в вертикальных канавках, по которым жидкость стекает вниз и выводится через отверстия в нижних частях плит. Твердая фаза откладывается на каждой салфетке в виде вертикального слоя осадка, толщина которого непрерывно увеличивается. Фильтрация прекращается, когда каждая пара слоев заполнит весь объем рамы.
Преимущества плиточно-рамных фильтр-прессов– значительная поверхность фильтрования, приходящаяся на единицу объема конструкции, возможность использования высоких избыточных давлений и отсутствие движущихся частей. Недостатки – ручное обслуживание, низкое качество промывки осадка и быстрый износ фильтровальной ткани в результате частой разборки и сборки всей конструкции.
|
|
Наиболее распространенной конструкцией фильтра непрерывного действия является барабанный вакуум-фильтр, основным элементом которого является полый барабан с перфорированной цилиндрической поверхностью, покрытой фильтровальной тканью. Внутренний объем барабана разделен на несколько секторов, каждый из которых имеет свой вывод внутри вращающейся вместе с барабаном центральной его части. Нижняя часть медленно вращающегося барабана постоянно погружена в корыто с суспензией. Внутри тех секторов, наружная цилиндрическая поверхность которых погружена в суспензию, поддерживается давление ниже атмосферного. Поэтому жидкая фаза суспензии фильтруется через ткань на барабане, попадает внутрь соответствующих секторов и непрерывно отводится через отверстия неподвижной распределительной головки и нижний фигурный вырез; фильтрат собирается в сборник; вакуум создается насосом. На наружной поверхности фильтровальной ткани откладывается слой осадка, непрерывно срезаемый ножом, который плотно прижимается к ткани.
|
|
Барабанные вакуум-фильтры имеют диаметр барабана до 2,5 м,длину – до 4 м, частота вращения барабана 1–10 мин–1.
Преимущества барабанных фильтров – относительная простота конструкции, удобство обслуживания, непрерывность работы, хорошие условия промывки осадка. Недостатки – значительная металлоемкость конструкции, небольшая движущая разность статических давлений, всегда меньшая атмосферного давления (DP< 0,1 МПа).
В ленточном вакуум-фильтреповерхностью фильтрации является плоская горизонтальная поверхность пористой, покрытой фильтрующей тканью бесконечной ленты, под которой создается разрежение. На горизонтальной поверхности легко производятся последовательные операции фильтрования и промывки; осадок сбрасывается с фильтрующей поверхности в месте ее перегиба за счет собственного веса либо относительно простоснимается ножом. Ширина ленты достигает 3 м, а ее длина – 9 м. Преимущество ленточного фильтра – отсутствие распределительной головки, а существенный недостаток – большие габариты по отношению к полезной поверхности фильтрации.
Автоматический камерный с механическим зажимом плит фильтрпрес (ФПАКМ)предназначен для фильтрования тонкодисперсных суспензий, содержащих от 5 до 500 кг/м3 твердых частиц, размерами не более 3 мм при температуре суспензий от 5 до 90 °С. Фильтр можно применять в химической, нефтяной, угольной, пищевой, .горнорудной и других отраслях промышленности.
|
|
Преимущества фильтра: развитая фильтрующая поверхность при незначительной занимаемой производственной площади; фильтрация и отжиме осадка в оптимальном слое под гидравлическим давлением до-15МПа. через гибкие диафрагмы, что резко снижает затраты сжатого воздуха на просушку осадка; незначительное время 1-2 мин - на вспомогательные операции ( раскрытие плит, выгрузка осадка, закрытие пресса и др.), причем достигается хорошая регенерация фильтровальной ткани.
Фильтр полностью автоматизирован и механизирован, что позволяет быстро настраивать его на оптимальный технологический режим. Металлоемкость фильтрпресса ФПАКМ, отнесенная к единице производительности по фильтруемой суспензии в 2-3 раза меньше, чем у рамных прессов, а металлоемкость, ниже, чем у барабанных фильтров непрерывного действия.
Применение ФПАКМ позволяет увеличить производительность труда в 4-10 раз по сравнению с рамными фильтр-прессами периодического действия и резко сократить расход фильтровальной ткани.
Автоматический фильтрпресс типа ФПАКМ состоит из набора горизонтально расположенных одна над другой фильтрующих рам, между которыми зигзагообразно протянута бесконечная лента фильтровальной ткани, приводимой в движение механизмом.
Съем осадка при движении ленты выполняют ножи по обе стороны фильтр-пресса, после снятия осадка лента проходит камеру регенерации.
Цикл работы фильтра включает стадии фильтрации промывки и отжима или просушки и выгрузки осадка.
Конструкция центрифуг
Рис. 27 Центрифуга с пульсирующим поршнем для выгрузки осадка
Суспензия по трубе 1 поступает в узкую часть конической воронки 2, вращающейся с такой же скоростью, как и перфорированный ротор 3, покрытый изнутри металлическим щелевым ситом 4. поршень 5. штуцеру 6. Осадок удаляется из кожуха через канал 7. Поршень укреплен на штоке 8, находящейся внутри полого вала 9, который соединен с электродвигателем На другом конце штока насажен перпендикулярно его оси диск 10, на противоположные поверхности которого в особом устройстве попеременно воздействует давление масла, создаваемое шестеренчатым насосом.
Конструкция мешалок
Рис 4 Перемешивающие устройства
а-г – быстроходные; д-з –тихоходные
а-лопастное; б-шестилопастное с наклонными лопастями; в-турбинное открытого типа; г-пропеллерное; д-якорное; е-рамное; ж-ленточное; з-шнековое
Лопастная. Условия работы: перемешивание взаимо-растворимых жидкостей, взвеши-вание твердых и волокнистых частиц в жидкости, взмучивание легких осадков, медленное растворение криста-ллических и волокнистых веществ
Рамная. Условия работы: перемешивание вязких и высокоплот-ных жидкостей, предотвращение выпадения осадка на стенках и днище, суспензирование в вязких средах, интенсификация теплообмена
Турбинная. Условия работы: взвешивание и растворение твер-дыхкристалллических частиц (с массовым содержанием до 80%); эмульги-рование жидкостей с большой разностью плотностей, дисперги-рование газа в жидкости; переме-шиваниеньютоновских жидкостей
Пропеллерная. Условия работы: взвешивание твердых (с массовым содержанием до 50%) и волокнистых частиц; взмучивание шламов; эмульгирование жидкостей; интенсификация теплообмена
Ленточные мешалки представляют собой конструкцию, состоящую из вертикального вала, на котором на равном расстоянии одна от другой установлены цилиндрические втулки. К каждой втулке приварены две цилиндрические траверсы, на периферийную часть которых опираются две плоские ленты.
Шнековая мешалка состоит из цилиндрической втулки или вала, к наружной поверхности которых приварена по винтовой линии плоская лента, имеющая шаг . Шнековые мешалки, как правило, устанавливают в циркуляционной трубе
$
Конструкции теплообменников. Кожухотрубчатые: одно- и многоходовые, с линзовым компенсатором, с U-образными трубами, с плавающей головкой, испарители с паровым пространством. Погружные змеевиковые, оросительные, двухтрубные («труба в трубе»), спиральные, с оребренными трубами (аппараты воздушного охлаждения), пластинчатые
Теплообменники — это аппараты, в которых осуществляется теплообмен между греющей и нагреваемой средами. Греющие и нагреваемые среды называют теплоносителями.
В теплообменных аппаратах могут происходить различные тепловые процессы: нагревание, охлаждение, испарение, конденсация, кипение и др. Теплообменники могут выполнять разные функции. В зависимости от назначения различают подогреватели испарители, конденсаторы, скрубберы, кипятильники, выпарные аппараты и др.
Теплообменные аппараты по принципу взаимодействия фаз разделяют на поверхностные, смесительные и регенеративные.
В поверхностных теплообменниках теплообмен между средами может осуществляться через трубчатую, плоскую или иную поверхность (соответственно в кожухотрубчатых, пластинчатых и других аппаратах).
В смесительных теплообменниках теплоноситель смешивается непосредственно с рабочей средой. К таким теплообменникам относятся градирни, конденсаторы смешения и аппараты с барботажем газа.
В регенеративных теплообменниках проводят нагревание керамических твердых тел, размещенных в аппарате, а затем применяют их для нагревания рабочей среды.
Кожухотрубчатыетеплообменники.Эти аппараты наиболее широко используются в химической и нефтехимической промышленности.
Рис. 14.2. Способы размещения труб в трубных решетках: а — по периметрам правильных шестиугольников; б — по окружностям; в — коридорное расположение
Трубы в решетках обычно размещают равномерно по периметрам правильных шестиугольников (рис. 14.2, а),что обеспечивает компактность их расположения, или по концентрическим окружностям (рис. 14.2, б). Для облегчения очистки наружных поверхностей труб иногда применяется коридорное расположение — по сторонам квадратов (рис. 14.2, в).
Для интенсификации процесса теплоотдачи в ряде конструкций теплообменных аппаратов предусмотрено размещение перегородок, увеличивающих число ходов для теплоносителей, что приводит к возрастанию скорости их потоков. Такие теплообменники называют многоходовыми.
При малом удлинении труб приемлема конструкция теплообменника с линзовым компенсатором 2 (рис. 14.3, а), расположенным на кожухе 1. При большой длине труб и значительных перемещениях применяют теплообменники с плавающей головкой (рис. 14.3, б). Верхняя часть кожуха 1 теплообменника этой конструкции присоединена к верхней трубной решетке, а нижняя трубная решетка имеет самостоятельное днище — плавающую головку Таким образом, пучок труб может свободно перемещаться относительно наружного корпуса, не вызывая в деталях механических напряжений.
На рис. 14.3, в приведена конструкция теплообменника с компенсирующим устройством в виде U-образных труб. Кожух / не связан жестко с трубами 4, и каждый элемент может удлиняться, не вызывая напряжений в месте присоединения.
Рис. 14.3. Кожухотрубчатые теплообменники с компенсирующими устройствами:
а — с линзовым компенсатором; б — с плавающей головкой; в — с U-образными трубами; 1 — кожух; 2 — линзовый компенсатор; 3 — плавающая головка;
4 — U-образные трубы; I, II — потоки теплоносителей
Трубы в трубной решетке укрепляют различными способами: развальцовкой, сваркой, склеиванием или пайкой. Иногда их крепят с помощью разъемных сальниковых устройств, благодаря которым при необходимости трубы легко заменить. Выбор способа крепления зависит от свойств материалов, из которых изготовлены трубы и решетка, а также рабочего давления.
Теплообменники типа «труба в трубе». Теплообменник этого типа (рис. 14.4) представляет собой несколько отрезков труб 2, каждый из которых заключен в трубу 1 большего диаметра. Внутренние трубы соединены друг с другом последовательно «калачами» 3, наружные — патрубками с фланцами. Отдельные элементы теплообменника собирают в вертикальные секции. В такой конструкции благодаря малой площади сечения внутренней трубы и узкому кольцевому зазору даже при небольшом расходе теплоносителей достигается высокая скорость их потоков, что обеспечивает эффективную теплоотдачу. К недостаткам таких конструкций можно отнести громоздкость и металлоемкость.
Змеевиковые теплообменники. Змеевик 3 (рис. 14.5) изготавливают из труб, свернутых в спирали, и заключают в кожух 1. Для увеличения скорости потока среды, омывающей наружную поверхность змеевика, в некоторых конструкциях предусмотрен внутренний стакан 2. Основными недостатками таких теплообменников являются малый коэффициент теплоотдачи теплоносителя II, омывающего змеевик, и незначительная площадь поверхности теплообмена.
|
|
Спиральные теплообменники.В таких теплообменниках (рис. 14.6) поверхность теплообмена образуется двумя металлическими листами — 1 и 2, свернутыми в спирали. Внутренние концы листов приварены к глухой разделительной перегородке 3, а их наружные концы сварены друг с другом. С торцов спирали закрыты крышками 4, установленными на прокладках. Таким образом, внутри аппарата образуются два изолированных спиральных канала шириной 8 и 12 мм, по которым противотоком движутся теплоносители. Теплоноситель / входит в верхний штуцер и удаляется через правый боковой штуцер, а теплоноситель II поступает в левый боковой штуцер и отводится через нижний штуцер. Эти теплообменники компактны, имеют малое гидравлическое сопротивление, но не могут быть использованы при большом давлении рабочей среды.
Рис. 14.6. Горизонтальный спиральный теплообменник:
1, 2 — листы; 3 — разделительная перегородка; 4 — крышки; I, II — потоки теплоносителей
Теплообменники с оребренными трубами. В том случае, когда один из теплоносителей имеет низкий коэффициент теплоотдачи (например, газы, вязкие жидкости), применяют теплообменники с оребренными трубами. Оребрение позволяет интенсифицировать процесс за счет увеличения площади поверхности теплообмена. На рис. 14.7 представлена конструкция такого теплообменника. Теплообменники, собранные из секций оребренных труб, широко используются для нагрева воздуха и других газов и носят название калориферов. Греющий теплоноситель (например, водяной пар) поступает в трубы калорифера, а воздух подается вентилятором вдоль ребер перпендикулярно трубам.
Рис. 14.7. Оребренный холодильник-калорифер
Конденсатоотводчики
Для быстрого автоматического удаления конденсата из парового пространства аппарата без потери острого пара применяют специальные приспособления - конденсатоотводчики (рис. 3.1). Имеются десятки раз личных конструкций конденсатоотводчиков, которые по принципу действия запорного элемента классифицируются по трем большим группам: поплавковые, приводимые в действие изменением уровня конденсата; термостатические, приводимые в действие изменением температуры конденсата; термодинамические, в которых открытие или закрытие клапана обусловлено изменением перепада давления между входом в конденсатоотводчик и камерой давления.
Конденсатоотводчики с закрытым поплавком (рис. 3.1, а)
При поступлении в корпус 3 конденсата поплавок 2 всплывает, поднимая клапан 1 для выпуска конденсата. С выходом конденсата поплавок опускается, и клапан закрывает выходное отверстие. При непрерывном поступлении конденсата клапан открыт соответственно постоянному расходу. Вертикальное положение поплавка с клапаном фиксируется стержнем 4 и направляющим стаканом 5.
Термостатический конденсатоотводчик с давлением пара (рис. 3.1, б) имеет термостат - деформируемый элемент (сильфон) 6, на котором закреплен клапан 1. Термостат заполнен легкокипящей жидкостью. При заполнении конденсатоотводчика паром жидкость вскипает, давление в термостате возрастает, и он расширяется; при этом клапан закрывает выходное отверстие. При заполнении конденсатоотводчика конденсатом пары легкокипящей жидкости в термостате конденсируются, давление уменьшается, термостат сжимается, и клапан открывает выходное отверстие для конденсата.
Отстойники с наклонными полками. Одно- и многоярусные отстойники непрерывного действия.
Отстаивание проводят в аппаратах, называемых отстойниками, или сгустителями. Различают аппараты периодического, непрерывного и полунепрерывного действия, причем непрерывно действующие отстойники, в свою очередь, делятся на одноярусные, двухъярусные и многоярусные.
Рис. V-3. Отстойник с наклонными перегородками:
1 — штуцер для ввода исходной суспензии, 2— корпус, 3—наклонные перегородки,4-бункера для осадка, 5- штуцер для отвода осветленной жидкости.
На рис. V-3 показан отстойник полунепрерывного действия с наклонными перегородками. Исходная суспензия подается через штуцер 1 в корпус 2 аппарата, внутри которого расположены наклонные перегородки 3, направляющие поток попеременно вверх и вниз. Наличие перегородок увеличивает время пребывания жидкости и поверхность осаждения в аппарате. Осадок собирается в конических днищах (бункерах) 4, откуда периодически удаляется, а осветленная жидкость непрерывно отводится из отстойника через штуцер 5.
Рис 11. Отстойник непрерывного действия с гребковой мешалкой:
1-корпус; 2- днище; 3- гребковая мешалка; 4- нож (гребок); 5- кольцевой желоб для стока осветленной жидкости.
В резервуаре установлена мешалка 3 с наклонными лопостями, на которых имеются гребки 4 для непрерывного перемещения осаждающегося материала к разгрузочному отверстию 7. Одновременно гребки слегка взбалтывают осадок, способствуя этим более эффективному его обезвоживанию. Мешалка делает от 0,015 до 0,5 об/мин, т.е. вращается настолько медленно, что не нарушает процесса осаждения.
+ Непрерывность действия ; большая производительность. В них достигается равномерная плотность осадка, имеется возможность регулирования ее путем изменения производительности, обеспечивается более эффективное обезвоживание осадка вследствие легкого взбалтывания его мешалкой. Работа таких отстойников может быть полностью автоматизарована.
- Громоздкость.
В целях уменьшения площади применяют многоярусные отстойники, состоящие из нескольких аппаратов, установленных друг на друга. Различают многоярусные отстойники закрытого и сбалансированного типов.
Простейший многоярусный отстойник закрытого типа (рис. V-6, а) представляет собой несколько отстойников, поставленных друг на друга и имеющих общий вал для гребковых мешалок и соответственно — общий привод. В местах прохода вала сквозь днище каждого отстойника установлены уплотняющие сальники. Таким образом, в этих отстойниках слив осветленной жидкости и выгрузка осадка осуществляются раздельно из каждого яруса.
Рис. V-6. Многоярусные отстойники закрытого (а) и сбалансированного (б) типов.
1—распределитель исходной суспензии 2 — труба стакан для ввода суспензии в каждый ярус; 3 — коллектор для сбора осветленной жидкости, 4 — сборник осадка (шлама)
Многоярусные отстойники сбалансированного, или уравновешенного, типа (рис. V-6, б) также имеют общие вал и привод, но, в отличие от отстойников закрытого типа, их ярусы последовательно соединены по шламу: стакан для удаления шлама из каждого вышерасположенного яруса опущен нижним концом в слой сгущенного шлама нижерасположенного яруса.
Отстойники работают следующим образом: исходная суспензия из распределительного устройства 1 подается через стаканы 2 в каждый ярус. Осветленная жидкость через сливные патрубки собирается в коллектор 3. Сгущенный осадок при применении отстойника закрытого типа удаляется раздельно из каждого яруса в сборники 4, а в случае отстойника сбалансированного типа — только из нижнего яруса.
Таким образом, в аппаратах закрытого типа дно каждого яруса воспринимает давление всей массы находящейся в нем суспензии, а у отстойников сбалансированного типа нагрузку на дно испытывает только нижний ярус. В отстойниках сбалансированного типа не требуется специальных уплотнений в местах прохода вала сквозь днища ярусов.
Дата добавления: 2018-04-15; просмотров: 1584; Мы поможем в написании вашей работы! |
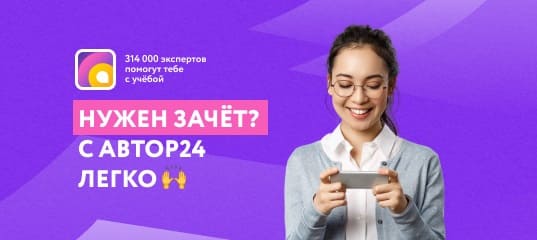
Мы поможем в написании ваших работ!