Определение годового объема работ
Содержание расчетно-пояснительной записки 1. Введение 2. Приведение годовой производственной программы 3. Определение трудоёмкости ремонта 4. Определение годового объема работ 5. Конструктивно-техническая характеристика детали 6. Выбор рациональных способов устранения дефектов 7. Сущность выбранных способов восстановления 8. План технических операций 9. Выбор средств технологического оснащения 10. Расчет режимов выполнения основных технологических операций и норм времени 11. Расчет степени загруженности оборудования 12. Заключение 13. Список используемой литературы 1.Введение Восстановление изношенных деталей – сложный организационный технологический процесс, при котором в отличие от производства новых деталей в качестве заготовки используют изношенную, но уже сформированную деталь. В этом случае затраты на выполнение таких операций, как литье, ковка, штамповка и т.п., отсутствуют. В то же время при восстановлении изношенных деталей появляется ряд дополнительных операций: мойка, разборка, дефекация, комплектация, затраты на которые следует учитывать при выборе способа. По данным исследований Е.Л. Воловика, износ различных групп деталей трактатов, автомобилей и сельскохозяйственных машин находится в пределах 0.01-10 мм. При этом около 83% деталей имеют износ до 0.6 мм. Длина цилиндрических деталей составляет 20-2400 мм, при этом преобладают валы длиной 200-400 мм. Способы восстановления деталей условно можно подразделить на две группы: · Износ превышающий 0.6 мм · Износ не более 0.6 мм.
|
|
Список используемой литературы
1. В.И. Карагодин «Ремонт автомобилей и двигателей» М.Академия 2008
2. В.Д. Аришнов «Ремонт двигателей ЯМЗ-240» Москва «Транспорт» 1978
3. В.М. Приходько «Справочник специалиста по ремонту автомобиля» Москва ИКЦ (Академкнига) 2007
Приведение годовой производственной программы
(1.1)
где
- приведенная годовой производственной программы
– количество заданных капитальных ремонтов по автомобилю
-й модели
=450
– коэффициент, приведенный для автомобилей j-й модели
– количество заданных капитальных ремонтов по j-му агрегату
=200
– коэффициент, приведенный для j-ого агрегата
=450*5+200*0,27*5=2250+270=2520(авто)
=2520(авто)
![]() |
Определение трудоёмкости ремонта
(2.1)
где
- коэффициент приведения, учитывающий величину производственной программы
- коэффициент, учитывающий разномарочность ремонтных объектов
=1,06
- коэффициент, учитывающий структуру производственной программы
=1,03
- трудоспособность ремонта объекта в эталонных условиях
|
|
=172 (чел/ч)
(2.2)
где
- соответственно большая и меньшая производительная программа
- коэффициенты, соответствующие
=0,115
=5000
=3000
=0,84
=0,95
=0,84*
*(0,95-0,84)=0,84*1,24*0,11=0,115
=0.115*1.06*1.03*172=22 (чел/ч)
=22 (чел/ч)
Определение годового объема работ
Годовой объем работ – общие затраты времени на выполнение годовой производственной программы предприятия (цеха, участка)
Tr=t*Nnp (3.1)
,где
Tr – годовой объем работ
Т - трудоемкость
Nпр – приведенная производственная программа
Тr=22*2520=55440 (чел/ч)
![]() |
5.Конструктивно-технологическая характеристика детали
5.1.Класс детали – полый цилиндр
5.2.Механические свойства детали:
Сталь – 15ХФ
б=65 бв=75 ф=30
Анв=8кГм/см2
НВ 190
Физические свойства
у 7.8 б/см2; h в пал/см*сек*град*0.95;
5.3.Шестерня свободно устанавливается в полости втулки на резьбе
5.4. Не допускаются трещины, сколы выкрашивание рабочей поверхности зуба, кольцевые риски на торцевых поверхностях. Износ поверхности отверстия втулки измеряется нутрометром НИ 18-50-2. Износ поверхности отверстия под втулку измеряется нутрометром НИ 18-50-2.
6. Выбор рациональных способов устранения дефектов.
|
|
Оценка способов устранения дефектов производится по трём критериям:
- технологическому
- техническому
- технико- экономическому.
6.1 Выбор способов восстановления по технологическому критерию основан на анализе принципиальной возможности, применения того или иного способа устранения дефекта.
Для восстановления износа поверхности отверстия под ось ведомых шестерен можно применить следующие способы:
- Хромирование
- Железнение
- Цинкование
Для восстановления износа торцевых поверхностей гнезд под шестерни можно применить следующие способы:
- Цинкование
- Железнение
- Хромирование
6.2 Оценка способов восстановления по техническому критерию, производится путем расчета оценочного коэффициента.
Кт = Ки Кс КдКп (6.2.1)
Ки Кс Кд- коэффициенты износостойкости, сцепляемости, долговечности.
Кп- поправочный коэффициент учитывающий фактическую работоспособность восстанавливаемой детали в условиях эксплуатации(0,7- 0,9)
Кт= 1,6*1*1*0,9= 1,44
Кт= 0,84*1*0,5*0,9= 0,378
Кт= 0,7*1*0,42*0,9= 0,265
Кт= 1*0,8*0,6*0,9= 0,432
Кт= 1,67*0,9*1*0,9= 1,352
|
|
Кт= 0,8*1*0,42*0,9= 0,302
6.3. Оценка способов устранения по технико- экономическому критерию, производится путем определения коэффициента технико-экономической эффективности.
Кэ= (6.3.1)
где:
Cв- удельная себестоимость способа восстановления.
По результатам расчетов из возможных вариантов выбираем один, способ для которого Кэминемально.
Кэ=61:1,44=42,36
Кэ=65:0,378=171,96
Кэ=71:0,256=277,34
Кэ=80:0,432=185,19
Кэ=145:1,352=107,25
Кэ= 81:0,302=268,21
Для восстановления износа поверхности отверстия под ось ведомых шестерен наиболее оптимальным является хромирование, потому что
Кэ=42,36.
Для восстановления износа поверхности отверстия под ось ведомых шестерен наиболее оптимальным является железнение, потому что
Кэ=107,25.
7. Сущность выбранных способов восстановления.
Железнение.
Проточное железнение. С помощью приспособлений изношенное отверстие детали превращают в закрытую местную гальваническую ванну. В ее центре устанавливается анод и через нее прокачивают насосом электролит. Анод и деталь неподвижны. При их подключении к источнику постоянного тока на поверхности отверстия осаждается железо. Электролит протекает в катодно-анодном пространстве со скоростью 15…18см/сек. Температура электролита 75-80°С. Осаждаются качественные гладкие покрытия со скоростью 0,3мм/ч, толщиной до 0,7мм и твердостью 4000.. .4500 МПа. Износостойкость восстановленных данным способом посадочных поверхностей на 25...50% выше износостойкости новых.
Хромирование.
Хромирование применяется как для восстановления деталей и повышения их износостойкости, так и для декоративных и противокоррозионных целей.Преимущество электромагнитного хрома: электрический хром – металл серебристого белого цвета с высокой микротвердостью 400-1200 мн/м2, близкой микротвердости новой детали.
Обладает высокой износостойкостью особенно в абразивной среде; устойчивостью в отношении химических и термических воздействий причем высокая коррозионная стойкость сочетается с красивым внешним видом; имеет низкий коэффициент трения (на 50% ниже, чем у стали и чугуна) высокую прочность сцепления покрытия с поверхностью детали.Недостатки хромирования и хромового покрытия; низкий выход металла по типу (8…42%) небольшая скорость отложения осадков (0,03 мм/г);высокая рессивность среды электролита; большое количество ядовитых выделений образующихся при электролизе, толщина отложения покрытия практически не превышает 0,3 мм;В качестве электролита используют хромовую кислоту (СО3) с небольшими добавками серной кислоты (Н2SO4) и растворы их солей, как при осаждении других металлов. Концентрация хрома в электролите может колебаться в пределах 100…400 г/л, серной кислоты 1…4г/л.
8. План технологических операций.
8.1 Износ поверхностей отверстия под ось ведомых шестерен.
а) Внутреннее шлифование;
б) Гальваническая операция – хромирование отверстия под ось;
в) Внутреннее шлифование для восстановления формы и размеров отверстия.
8.2Износ торцевых поверхностей гнезд под шестерни.
а)Шлифовальная опирация – подготовка поверхности;
б) Гальваническая операция – железнение торцевых поверхностей;
в) Шлифовальная операция – обработка поверхности после железнения.
N операции | Наименование и содержание операции |
1 | Внутреннее шлифование. |
2 | Гальваническая операция – хромирование отверстия под ось. |
3 | Внутреннее шлифование для восстановления формы и размеров отверстия. |
4 | Шлифовальная опирация – подготовка поверхности. |
5 | Гальваническая операция – железнение торцевых поверхностей. |
6 | Шлифовальная операция – обработка поверхности после железнения. |
9.Выбор средств технологического оснащения.
Оборудование для гальванической операции.
Процесс гальваники в сильной степени зависит от температуры электролита и плотности тока. Оба фактора влияют на внешний вид и свойства покрытия, а также на выход метала по току. Необходимо помнить, что с повышением температуры выход по току снижается; с повышением плотности тока выход по току возрастает; при более низких температурах и постоянной плотности тока получаются серые покрытия, а при повышенных - молочные. Практическим путем найден оптимальный режим: плотность тока 50-60 А/дм2 при температуре электролита 52° - 55° ±1°.
Чтобы быть уверенным в работоспособности электролита, в приготовленной ванне можно покрыть несколько деталей, подобных по форме и размерам рабочим образцам. Подобрав режим и узнав выход по току простым замером размеров до и после гальванической операции можно приступать к покрытию детали.
По предложенной методике можно восстановить: стальные, бронзовые и латунные детали. Подготовка их заключается в промывке поверхностей, подлежащих под восстановление, бензином и затем мылом (с помощью зубной щетки) в горячей воде, зарядке в оправку и размещении в ванне. После погружения в электролит нужно подождать 3-5 с и затем включить рабочий ток. Задержка нужна для того, чтобы деталь прогрелась. Одновременно происходит активирование поверхности деталей из латуни и меди, так как эти металлы хорошо травятся в электролите. Однако больше 5 с ждать не следует - в составе этих металлов есть цинк, присутствие которого в электролите недопустимо.
Шлифовальный станок 3Б740.
Наибольший диаметр шлифуемой детали 400 мм; Наибольшая высота шлифуемой детали 175 мм; Размеры шлифовального круга 230... 350*40*100 мм; Скорость вращательно – поступательного движения ствола 0,2…5,0 м/мин; Частота вращения шлифовального круга 1900 мин-1 ; Частота вращения ствола (бесступенчатое регулирование) 15,0…37,5 мин-1 ; Автоматическая подача шлифовальной бабки 0,002…0,05мм/мин; Расположение шпинделя – горизонтальное; Мощьность электродвигателя привода шлифовального круга 7,5 кВт; КПД станка 0,95; Габаритные размеры, мм: 2055*1565*1935.
10. Расчет режимов выполнения основных технологических операций и норм времени.
Гальваническая операция
Сила тока: I=Дк*Fк где , (10.1)
Дк- катодная плотность тока А/дм2 , определяется условиями работы детали, видом покрытия, температурой и концентрацией и концепцией электролита.
Принимаем Дк=25 А/дм2
Fк-площадь покрываемой поверхности, дм2
Fк=3,14*18*22=1243,44мм2 =0,1243дм2
I=0,1243*25=3,11A
Норма времени определяется
Tn= (10.2)
где,
To-продолжительность электролического осаждения металлов в ванне
T1-время на загрузку деталей
Т1=(0,1-0,2), принимаем Т1=0,16
Knз-коэффициент учитывающий дополнительное и подготовительно-заключительное время (при работе в одну смену Kn3=1,1-1,2)
Принимаем Knз=1,1
nд- число деталей, одновременно наращиваемых в ванне, принимаем nд=40
- коэффициент использования ванны (
=0,8-0,95) принимаем
=0,9
Время выдержки деталей в ванне определяем по формуле:
Tо=, где (10.3)
h- толщина наращивания, мм, принимаем h=0,2
j - плотность осаждаемого металла г/см3 принимаем j=7,9
С- электрохимический эквивалент металла г/А*г принимаем С=1,042
ƞm-выход металла по току принимаем ƞm=85%
Ок – коэффициент электролита (принимаем =25)
Tо= =71,36 мин
Tn= =2,19 мин
Шлифовальная операция
Оно осуществляется с поперечной подачей до достижения необходимого размера поверхности.
Шлифовальный круг перекрывает всю ширину (длину) обрабатываемой поверхности
Основное время при шлифовании
Tо= где, (10.4)
Snon- поперечная подача
(Snon=0,00025-0,02)мм/об принимаем Snon=0,02
nд= (10.5)
Vд=2-5м/мин (для чистового шлифования) принимаем Vд=3
nд= об/мин
принимаем nд=40 об/мин
To= мин
Вспомогательное время - Tв
принимаем Tв=0,7 мин
Дополнительное время (Тдоп) при шлифовании можно принять 7% от Ton
Ton=To + Tв
Ton=0,16 + 0,7=0,76 мин
Тдоп=0,76*0,07=0,05 мин
Подготовительно-заключительное время принимаем Тnз=16 мин
Нормативное время
Тн = То +Тв+Тдоп+.
Тн=0,16+0,7+0,05+16/18=1,8 мин
11.Расчет степени загруженности оборудования.
Гальваническая операция
Х0 = (11.1)
X0 = = 2,46
Принимаем х0=3
Коэффициент использования
η = = 0,82
Шлифовальный станок.
Х0 =
X0 = = 2,1
Принимаем х0=5
Коэффициент использования
η = = 0,42
Дата добавления: 2018-04-15; просмотров: 157; Мы поможем в написании вашей работы! |
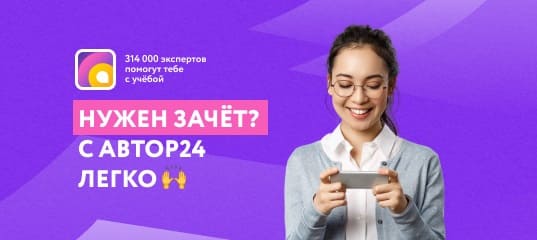
Мы поможем в написании ваших работ!