Основное оборудование групповых заправщиков топливом
Выделение стационарных и сборно-разборных систем ГЗТ в обособленные объекты, работающие в комплексе с основными сооружениями и оборудованием складов ГСМ, является для большинства крупных аэропортов наиболее рациональным вариантом, учитывая сложные и многоплановые задачи топливообеспечения аэропорта.
Кроме того, не во всех зарубежных аэропортах владельцами аэродромного склада ГСМ и систем ГЗТ являются одни и те же компании. Аналогичная тенденция отмечается и в аэропортах гражданской авиации РФ, когда в результате приватизации аэропортовое оборудование становится собственностью разных юридических лиц, частных и муниципальных образований. Эти особенности должны учитываться, в том числе в составе оборудования и конструктивных особенностях групповых заправщиков. Отмечаются следующие направления изменения состава и конструкции оборудования.
1. В приемной группе систем ГЗТ дополнительно устанавливаются узлы учета объема нефтепродуктов, поданных в систему ГЗТ из резервуаров основного склада или из автоцистерн.
2. Совершенствуется система измерения уровня топлива в резервуарах:
3. В системах ГЗТ кроме гидрантных топливозаправочных колонок на перронах устанавливаются стационарные, в том числе шахтного типа, агрегаты заправки, а также пункты налива топливом цистерн ТЗА.
4. Устанавливаются системы контроля герметичности трубопроводных коммуникаций, совершенствуется система мониторинга герметичности резервуаров.
|
|
5. Совершенствуется система контроля качества топлива на всем пути его подачи к заправляемым ВС.
6. На смену устройств снижающих опасность гидроударных процессов в коммуникациях ГЗА устанавливаются системы, предотвращающие пульсации и гидроударные процессы в системе при заправке ВС.
7. Совершенствуются мероприятия и способы снижения опасного проявления статического электричества при выполнении технологических операций.
8. Совершенствуется система метрологического обеспечения рабочих операций ГЗТ, в том числе поверки без демонтажа средства измерения из магистралей.
Особенностью современного строительства и реконструкции стационарных ГЗТ является также применение оборудования зарубежного производства, а также нового отечественного оборудования с новыми конструктивными элементами и принципами функционирования.
Узлы учета топлива
В приемных группах современных ГЗТ могут устанавливаться объемные счетчики жидкости, узлы учета и установки перекачки и учета. Зарубежные мотонасосно-измерительные аналоги (например, из Германии) выпускаются с пропускной способностью от 60 до 180 м3/ч, отечественные образцы перекачки и учета нефтепродуктов, которые могут устанавливать в приемной группе ГЗТ, могут быть от 30 до 70 м3/ч с погрешностью счетчика ±25%.
|
|
Современный узел учета модульного типа для приемной группы системы ГЗТ (рис. 15) состоит из объемного счетчика 1 типа ППО или ППВ с погрешностью ±25%, газоотделителя 2, соответствующего счетчику по условному проходу и обеспечивающему отделение паров топлива на заданном расходе, фильтра 3, затворов 4 с механическим или электрическим приводом.
Рисунок 15 – Узел учета топлива
1 – объемный счетчик типа ППО, ППВ; 2 – фильтр; 3 – газоотделитель; 4 – затвор.
По требованию заказчика отечественный узел может быть укомплектован счетчиком с фактической погрешностью ± 0,1% на заданном расходе, плотномером, устройством съема сигналов типа УСС на счетчике вместо механического отсчетного указателя или вместе с ним, контроллером, и пультом дистанционного управления, термодатчиком, клапаном – отсекателем для отпуска определенно дозы топлива, или в случае контроля и поверки счетчика встроенным мерником 2 разряда заданным объемом до2000 дм3 с погрешностью ± 0,05%. При установке на узле указанного оборудования прием топлива в резервуары ГЗТ может осуществляться как в единицах объема, так и в единицах массы.
|
|
Принципиальная схема узла учета с поверкой (контролем) счетчика мерником приведена на рис. 16.
Рисунок 16 - Типовое оборудование приемной группы:
1 – продуктопровод (емкость); 2 – электронасос; 3 – электрозатвор; 4 – газоотделитель; 5 – фильтр; 6 – счетчик; 7 – мерник 2-го разряда (+0,05 – 0,08%); 8 – контроллер; 9 - компьютер.
Узлы учета могут входить в компьютерные системы ГЗТ для учета приема, наличия в резервуарах и выдачи на заправку топлива. Отметим, что узлы аналогичные учета могут устанавливаться в приемных группах АЗС и ТЗП.
Технические характеристики узлов учета для систем ГЗТ, АЗС и ТЗП приведены в таблице 10.
Таблица 10 - Технические характеристики узлов учета топлива
Диапазон расхода, м3/ч | Счетчик | Фильтр | Газоотделитель | Мерник, дм3, погрешность ± 0,05% |
0,7-7,2 | ППО25-1,6 | ФЖУ-25 | Гу-25 | 2-50 |
5-25 | ППО40-0,6 | ФЖУ-40 | Гу-40 | 100-500 |
10-240 | ППВ100-1,6 | ФЖУ-100 | Гу-100 | 2000 |
20-420 | ППВ150-1,6 | ФЖУ-150 | Гу-1 50 | 2000 |
Резервуарная группа
По отечественным и зарубежным нормам в системах ГЗТ должно быть не менее 3-х резервуаров с внутренним антикоррозионным покрытием, оснащенных общим промышленным оборудованием, а также плавающим топливозаборным оборудованием.
|
|
В настоящее время в системах ГЗТ находят применение следующие типы резервуаров:
Вертикальные наземные сварные с избыточным давлением 0,002 МПа и вакуумом до 0,0025 МПа вместимостью от 100 до 1000 м3;
Горизонтальные наземные и подземные сварные, рассчитанные на избыточное давление до 0,04 МПа вместимостью от 3 до 100 м3;
Вместимость каждого из резервуаров, как правило, должна соответствовать суточной потребности в заправке топливом ВС в пиковые периоды использования ГЗТ [20]. В соответствие с отечественной и зарубежной практикой рекомендуется применение одинаковых по вместимости и конструкции резервуаров, оборудование которых должно обеспечивать прием, отстаивание и выдачу топлива [19-20].
В системах ЦЗС высокой и средней производительностиобычно используются вертикальные цилиндрические резервуары (рис. 17-18), а в упрощенных системах с суточным расходом не более 100 м3 – горизонтальные резервуары (рис. 18). Основные характеристики вертикальных резервуаров рулонной сборки со щитовой кровлей приведены в таблице 11.
Таблица 11 - Основные технические характеристики вертикальных цилиндрических резервуаров
Показатель | Условный объем резервуара, м3 | |||||||
200 | 300 | 400 | 700 | 1000 | 2000 | 3000 | 5000 | |
Вместимость резервуара, м3 | 204 | 332 | 421 | 757 | 1056 | 2135 | 3340 | 4832 |
Диаметр, мм | 6630 | 7580 | 8530 | 10430 | 12330 | 15180 | 18980 | 22800 |
Высота, мм | 5920 | 7375 | 7450 | 8940 | 11920 | 11920 | 11920 | 11920 |
Общая масса металла, т | 7,334 | 11,311 | 12,655 | 18,199 | 24,212 | 41,301 | 63,238 | 90,422 |
Вертикальные резервуары устанавливаются только наземно на специальном песчаном основании.
|

Рисунок 17 - Вертикальный резервуар и его оборудование:
1 — корпус; 2 — ограждение; 3 — пеногенератор; 4 — предохранительный (гидравлический) клапан; 5 — дыхательный клапан механический; 6 — замерный люк; 7 — световой люк; 8 — сниженный пробоотборник; 9 — сигнализатор предельного уровня; 10 — лестница; 11 — указатель уровня; 12 — управление хлопушкой; 13 — хлопушка; 14 — приемо-раздаточный патрубок; 15 — плавающее топливозаборное устройство; 16 — песчаное основание; 17 — люк-лаз; 18 — сифонный кран
Наиболее перспективными являются вертикальные резервуары (рис. 18) с конусными днищами и гладкими внутренними поверхностями. Это обеспечивает надежный и удобный сбор и последующее удаление из резервуара продуктов отстоя, а также удобное нанесение на стенки антикоррозионных покрытий. Типовые проекты предусматривают строительство таких резервуаров емкостью 400, 700, 1000, 2000, 3000 и 5000 м3 с внутренними антикоррозионными покрытиями.
Рисунок 18 - Вертикальный резервуар с коническим днищем и дополнительным оборудованием:
1 - приемо-раздаточный патрубок; 2 - днище коническое; 3 - плавающее топливозаборное устройство; 4 - сливная труба; 5 - вентиль; 6 - присоединительное устройство; 7 - плавающий понтон; 8 - огневой предохранитель; 9 - воздушный фильтр; 10 - механический дыхательный клапан
Горизонтальные резервуары устанавливают наземно, полуподземно и подземно. Предпочтение отдается наземной установке, так как создаются благоприятные условия для работы насосных станций (обеспечивается подпор) и отпадает необходимость в применении самовсасывающих насосов. Кроме того, при наземной установке значительно улучшаются условия эксплуатации и обслуживания резервуаров при проведении регламентных работ. При наземной установке резервуары размещаются на фундаментах, а при подземной и полуподземной - на песчаном основании.
Если в местах установки резервуаров имеются грунтовые воды, то при подземной установке размещаются на бетонных фундаментах, к которым они крепятся специальными бандажами. Основные технические данные горизонтальных резервуаров приведены в таблице 12.
Таблица 12 - Основные технические характеристики горизонтальных цилиндрических резервуаров
Показатель | Условный объем резервуара, м3 | |||||
10 | 25 | 50 | 75 | 100 | ||
Вместимость резервуара, м3 | 10,5 - 11,5 (–) | 25,4-28,5 (26,5-28,5) | 50,2-54,4 (51,7-54,6) | 73,4-83,4 (74,6-84,8) | 97,5-100,6 (98,9-101,4) | |
Наружный диаметр, мм | 220 (–) | 2862-2870 (2862-2870) | 2862-2870 (2862-2870) | 3238-3250 (3238-3250) | 3238-3250) (3238-3250) | |
Наружная длина, мм | 2823 - 3073 (–) | 4035-4274 (4645-4924) | 7885-8383 (8545-9130) | 8958-10126 (9590-10758) | 11888-12132 (12520-12764) | |
Общая масса металла, кг | 1013 - 1049 (–) | 1772-1898 (1831-1894) | 3148-3339 (3200-3343) | 4181-4499 (4250-4583) | 5305-5375 (5311-5405) | |
Примечание. В скобках указаны размеры резервуаров с коническими днищами. | ||||||
Для заполнения и опорожнения резервуаров, а также для надежного хранения топлива и правильной эксплуатации резервуаров на них устанавливают специальное оборудование, изготовляемое по соответствующим ГОСТ. Это оборудование включает: световой люк, люк-лаз, дыхательные и предохранительные клапаны, замерный люк, сифонные краны, хлопушки с устройствами для их управления, указатели уровня, огневые предохранители и другое оборудование. Выбор оборудования резервуаров производится в зависимости от их конструкции, пропускной способности приемораздаточных устройств и подачи насосных станций.
Для расходных резервуаров систем ЦЗС этого оборудования недостаточно, так как к ним предъявляются более жесткие требования к обеспечению выдачи топлива из верхних, наиболее отстоявшихся слоев; надежной защите топлива от попадания в него пыли и влаги из атмосферы, а также продуктов коррозии, которые могут образовываться на внутренних стенках резервуаров. Для выполнения этих требований на расходных резервуарах необходимо устанавливать дополнительное специальное оборудование, а внутренние их поверхности покрывать антикоррозионными материалами.
В качестве дополнительного оборудования используются: плавающие топливозаборные устройства для верхнего забора топлива, воздушные фильтры, устройства для удаления отстоя, а также плавающие крыши и понтоны (см. рис. 19).
Рисунок 19 - Типовая: схема размещения технологического оборудования на наземном горизонтальном цилиндрическом резервуар:
1 - дыхательный клапан (на группу резервуаров); 2 - воздухопровод; 3 - уровнемер; 4 - мостик; 5 - болт крепления тросом управления заборной трубой; 5 - патрубок; 7 - аварийный клапан (дыхательный); 8 - трос управления заборной трубой; 9 - люк-лаз (500 мм); 10 - поплавок заборной трубы; 11 - заборная труба; 12 - всасывающая магистраль; 13 - 25 мм клапан слива отстоя; 14 -опора; 15 - стальная накладка; 16 - приемный трубопровод
В международных требованиях [26] не предусматривается применение для ГЗТ резервуаров с плавающими крышами и понтонами. Авиатопливо должно храниться в горизонтальных и вертикальных резервуарах с неподвижной крышей. Новые резервуары должны быть сконструированы таким образом, чтобы не допустить попадание в них воды и грязи, также должен быть обеспечен легкий слив отстоя из резервуаров. Для горизонтальных резервуаров должен быть предусмотрен минимальный угол наклона в отношении 1:50 в сторону устройства слива отстоя, а вертикальные резервуары должны иметь конусообразное днище с наклоном 1:30 к центру отстойника.
Для внутренних поверхностей резервуаров в качестве антикоррозионных покрытий применяются: металлизация, эмалирование, лакокрасочные материалы, стеклопласт на основе полиэфирных и эпоксидных смол.
Резервуары, имеющие антикоррозионные покрытия из диэлектрических материалов, оборудуются устройствами для отвода статического электричества с поверхности топлива. Ниже рассматривается основное стандартное и дополнительное оборудование резервуаров.
Приемо-раздаточный патрубок 1 (рис. 20) предназначен для заполнения резервуара или выдачи из него топлива. Он вваривается в нижний пояс корпуса 3 резервуара. Диаметр патрубка выбирается с учетом расхода, с которым заполняется резервуар. Зависимость диаметра патрубка от расхода представлена в таблице 13.
Таблица 13 – Основные характеристики оборудования резервуаров
Оборудование | Марка | Размеры, мм | Пропускная | |
Условный диаметр | Диаметр фланца | |||
Приемо-раздаточные патрубки | ППР-80 | 80 | 220 | До 50 |
ППР-100 | 100 | 240 | 50—100 | |
ППР-150 | 150 | 300 | 100-200 | |
ППР-200 | 200 | 350 | 200 - 300 | |
ППР-300 | 300 | 520 | 600 - 1200 | |
Плавающие | ПУВ-100 | 100 | 210 | 70 - 120 |
топливозаборные устройства | ПУВ-150 | 150 | 265 | 150 - 200 |
ПУВ-250 | 250 | 371 | 300 - 500 | |
Хлопушки | Х-80 | 80 | 190 | – |
Х-100 | 100 | 210 | – | |
Х-150 | 150 | 265 | – | |
Х-200 | 200 | 320 | – | |
Х-250 | 250 | 371 | – | |
Х-300 | 300 | 440 | – | |
Механические дыхательные | КД-50 | 50 | 450 | До 25 |
клапаны | КД-100 | 100 | 500 | 60-72 |
КД-150 | 150 | 550 | 118 - 142 | |
КД-200 | 200 | 600 | 206 - 240 | |
КД-250 | 250 | 650 | 244 - 304 | |
Гидравлические | КПСА-100 | 100 | 205 | 50 |
предохранительные клапаны | КПСА-150 | 150 | 260 | 100 |
КПСА-200 | 200 | 315 | 200 | |
КПСА-250 | 250 | 370 | 300 | |
КПСА-350 | 350 | 485 | 600 | |
Огневые предохранители | ОПЛ-50 | 50 | 140 | – |
ОПЛ-80 | 80 | 190 | – | |
ОПЛ-100 | 100 | 210 | – | |
ОПЛ-150 | 150 | 265 | – | |
ОПЛ-200 | 200 | 320 | – | |
ОПЛ-250 | 250 | 375 | – |
Количество приемо-раздаточных патрубков может быть различным и зависит от расчетного расхода или обусловливается технологическими требованиями.
Рисунок 20 – Приемно-раздаточное оборудование резервуаров
В расходных резервуарах систем ЦЗС на раздаточном патрубке должно быть установлено плавающее топливозаборное устройство 10. Это требование для вертикальных резервуаров является обязательным. Плавающее топливозаборное устройство ПУВ (рис. 21) предназначено для выдачи из резервуара наиболее чистого, отстоявшегося топлива из верхнего слоя. Оно представляет собой подъемную трубу 5, один конец которой соединен шарниром 6 с приемо-раздаточным патрубком 1 и хлопушкой 2, а другой оборудован поплавком 4, удерживающим трубу в верхнем слое топлива. Плавающие топливозаборные устройства изготовляются с диаметром условного прохода 100, 150 и 250 мм, с пропускной способностью соответственно 70 - 120, 150 - 200 и 300 - 500 м3/ч.
Рисунок 21 – Плавающее топливозаборное устройство
Хлопушка (см. рис. 20) предназначена для предотвращения утечки топлива из резервуара в случае неисправности задвижки на трубопроводе. Она устанавливается на приемо-раздаточном патрубке внутри резервуара. Хлопушка перекрывает проходное сечение патрубка под действием собственной силы тяжести и давления столба топлива. Диаметр хлопушки определяется диаметром приемо-раздаточного патрубка. В таблице 13 приведены марки хлопушек и размеры их диаметра. При выдаче топлива из резервуара хлопушка открывается при помощи механизма бокового управления.
Рисунок 22 - Приемо-раздаточное оборудование резервуаров
Механизм бокового управления хлопушкой (см. рис. 22) имеет вал 7, на наружном конце которого закреплен штурвал 4, а на внутреннем - барабан 8, соединенный тросом с хлопушкой 12. В месте прохода вала 7 через стенку резервуара установлено сальниковое устройство 6. При вращении штурвала 4 вращается барабан 8, на который наматывается прикрепленный к нему трос 11, и открывает хлопушку 12. Для удержания хлопушки в открытом положении имеется стопор 5, фиксирующий штурвал. В случае обрыва троса 11 пользуются аварийным тросом, один конец которого прикреплен к хлопушке, а другой выведен и закреплен у светового люка.
Перепускное устройство (см. рис. 22) предназначено для облегчения открытия хлопушки за счет выравнивания давления топлива по обе стороны хлопушки. Перепускное устройство устанавливают на резервуарах высотой более 5 м. При меньшей высоте устанавливать его нецелесообразно, так как давление столба жидкости будет небольшим. Перепускное устройство состоит из трубки 2 диаметром 25 мм и вентиля. Один конец трубки вварен в приемо-раздаточный патрубок, а другой - в стенку резервуара. Перепускное устройство выпускают одного типа независимо от диаметра приемо-раздаточного патрубка.
Световой люк предназначается для доступа обслуживающего персонала, проветривания и освещения резервуара при ремонтных и зачистных работах. Кроме того, он используется при подъеме хлопушек при повреждении троса управления. Световой люк устанавливают на кровле резервуара над приемо-раздаточным патрубком с хлопушкой. В резервуарах емкостью свыше 2000 м3 делают два световых люка. Для резервуаров других объемов количество световых люков принимают по числу приемо-раздаточных патрубков. Диаметр люка в свету 500 мм.
Люк-лаз предназначен для доступа обслуживающего персонала в резервуар при его осмотре, зачистке и ремонте. Он также служит для вентиляции резервуара. Люк-лаз расположен диаметрально противоположно световому люку. Узлы люк-лаза в отличие от светового усилены, так как он расположен в нижнем поясе корпуса резервуара, где имеется значительное гидростатическое давление. Резервуары емкостью свыше 2000 м3 имеют два люка-лаза. Диаметр люка-лаза ПЛ-500 в свету 500 мм. Световые люки и люки-лазы должны быть прочными и герметичными, обычно их делают сварными, а для уплотнения применяют специальные прокладки.
Замерный люк (рис. 23) предназначен для замера уровня топлива в резервуаре рулеткой, а также для взятия проб пробоотборниками. Он устанавливается на кровле резервуара и крепится к его замерному патрубку фланцем 7. Замерный люк состоит из корпуса 5, кулисы 4, крышки 3, маховика 2, прокладки 1 и педали 6. Крышка 3, подвешенная к кулисе 4, прижата к корпусу маховичком 2. Отведя в сторону маховичок и нажав ногой на педаль 6, открывают отверстие люка. Замерные люки выпускаются с диаметром условного прохода 100 мм для горизонтальных резервуаров и 150 мм - для вертикальных резервуаров.
Рисунок 23 – Замерный люк
Механический дыхательный клапан (рис. 24) предназначен для поддержания внутри резервуара установленной величины избыточного давления или разрежения, которые образуются при заполнении резервуара и выдаче из него топлива, а также при изменении объема газов в паровом пространстве резервуара вследствие колебания температуры. Величина избыточного давления и вакуума зависит от прочности крыши и не должна превышать допустимых пределов. На рис. 24 изображен наиболее распространенный дыхательный клапан, допускающий повышение давления в паровоздушном пространстве резервуара не более чем на 190 мм вод. ст. и разрежения не более 25 мм вод. ст. Необходимо также учитывать, что пропускная способность дыхательного клапана при прохождении через него паровоздушной смеси должна соответствовать пропускной способности приемо-раздаточного патрубка. Если пропускная способность дыхательного клапана будет меньше пропускной способности приемо-раздаточного патрубка, создадутся условия для возрастания избыточного давления или разряжения выше допустимых, что может привести к разрушению кровли резервуара. Если максимальная пропускная способность одного дыхательного клапана недостаточна, устанавливают два клапана.Величины пропускной способности клапанов приведены в таблице 13.
Принцип работы клапана заключается в том, что при достижении в паровоздушном пространстве резервуара избыточного давления выше установленного клапан 8 под воздействием этого давления открывается и выпускает паровоздушную смесь и атмосферу через правую камеру, прикрытую огнезащитной сеткой.
Рисунок 24 – Механический дыхательный клапан:
1 - седло клапана; 2 - клапан впускной; 3 - крышка; 4 - прокладка; 5 - маховичок;
4 - рычаги крышек, 7 - корпус; 8 - клапан выпускной; 9 - сетка.
При разряжении клапан 2 под давлением наружного воздуха поднимается, обеспечивая поступление воздуха в резервуар через левую камеру. Как только внутри резервуара установится расчетная величина избыточного давления или разрежения, соответствующие клапаны закрываются под воздействием силы тяжести.
Конструкция указанного дыхательного клапана имеет недостаток: тарелки клапана при работе в условиях низких температур могут примерзать к седлам и клапан окажется неработоспособным. Этот недостаток может быть устранен путем изоляции смерзающихся поверхностей фторопластом. Для этого на каждой тарелке клапана закрепляется фторопластовая пленка, седла изолируются фторопластовыми пластинами, штоки обертываются фторопластовыми пластинами и устанавливаются в направляющих трубках, изготовленных из фторопласта.
Кроме указанных дыхательных клапанов, используются непримерзающие мембранные дыхательные клапаны типа НДКМ, которые отличаются от существующих дыхательных клапанов типа КД тем, что имеют другое конструктивное исполнение и обладают в 3 - 5 раз большей пропускной способностью при одинаковом диаметре присоединительного патрубка. Это позволяет сократить число клапанов, устанавливаемых на резервуаре. Конструкция клапана позволяет производить широкое регулирование пределов его срабатывания: при вакууме от 20 до 70 мм вод. ст., а при давлении от 100 до 200 мм вод. ст. Дыхательные клапаны НКДМ имеют присоединительные патрубки с диаметром условного прохода 150, 200, 250 и 350 мм.
Предохранительный гидравлический клапан (рис. 25) предназначен для тех же целей, что и механический дыхательный клапан и выполняет его роль при выходе последнего из строя или при нарушении технологического режима. Он работает по принципу гидравлических затворов, т. е. столб малоиспаряющейся жидкости препятствует свободному выходу паровоздушной смеси из резервуара и входу в него атмосферного воздуха. В качестве такой жидкости может быть использовано соляровое масло или дизельное топливо. Клапан срабатывает при избыточном давлении 200 мм вод. ст. и при разрежении 40 мм вод. ст.
Рисунок 25 - Предохранительный гидравлический клапан:
1 – пробка; 2 - сливная труба; 3 - корпус клапана; 4 - колпак; 5 - труба; 6 - растяжка; 7 - крышка; 8 - воронка; 9 - щуп
Клапан в резервуаре должен устанавливаться строго горизонтально (по присоединительному фланцу). Он заливается жидкостью после установки его на резервуар, причем до уровня, определенного предварительной регулировкой на давление и разрежение сжатым воздухом. Зависимость пропускной способности предохранительного клапана от диаметра его условного прохода представлена в таблице13.
Огневой предохранитель (рис. 26) предназначен для предотвращения попадания внутрь резервуара открытого пламени или искр, которые могут проникнуть в резервуар вместе с атмосферным воздухом через механический дыхательный или предохранительный гидравлический клапан. Он устанавливается на патрубках между резервуаром и указанными клапанами. Огневой предохранитель состоит из корпуса 2 с фланцами 1, и съемными боковыми крышками 3. Внутри корпуса помещен пакет из пластин, изготовленных из латуни или другого металла, обладающего высокой теплоемкостью. Принцип работы огневого предохранителя заключается в том, что при попадании в него пламени или искр от них отбирается пакетом тепло и их огнеопасность теряется.
Рисунок 26 – Огневой предохранитель
Огневые предохранители выпускаются с условным диаметром 50, 100, 150, 200 и 250 мм. Выбор размеров огневых предохранителей производится с учетом размеров дыхательных и предохранительных клапанов.
Сифонный кран (рис. 27) предназначен для слива отстоя воды и остатка топлива из резервуара и устанавливается в нижнем поясе резервуара на расстоянии 350 мм от днища. Существуют два типа сифонных кранов: СК-50 и СК-80 с диаметрами условного прохода 50 и 80 мм соответственно. На вертикальных резервуарах емкостью до 4000 м3 используются сифонные краны СК-50, а на резервуарах большей емкости - краны СК-80.
Рисунок 27 – Сифонный кран
Для горизонтальных резервуаров сифонные краны промышленностью не выпускаются. Для них используются сифонные краны вертикальных резервуаров с. незначительной доработкой.
Конструктивно сифонный кран для вертикальных резервуаров представляет собой составную трубу с изогнутым коленом 6. В месте прохода прямого участка трубы через стенку резервуара установлен сальник 5. На наружной части трубы смонтирован кран 2 и поворотная рукоятка 3. Наружная часть сифонного крана закрывается кожухом 1, снабженным замком 4. На конце изогнутого колена приварен кольцевой козырек 7. В нерабочем положении сифонный кран, как правило, устанавливается изогнутым коленом вверх, это исключает случаи примерзания колена 6 в слое отстоявшейся воды и обеспечивает промывку крана топливом от возможных остатков воды по окончании слива. В рабочем положении при сливе отстоя из резервуара сифонный кран с помощью рукоятки 2 устанавливается изогнутым коленом вниз, а кран 2 открывается.
Отстоявшаяся вода под воздействием давления столба топлива будет вытекать из резервуара. Кольцевой козырек 7 препятствует вытеканию чистого топлива вместе со сливаемой водой.
На рис. 28 показаны индивидуальные дренажные устройства наземных горизонтальных резервуаров. Слив отстоя производится в передвижную емкость при открытом вентиле. Дренажное устройство для подземных горизонтальных резервуаров показано на рис. 28, в. В этом случае слив отстоя осуществляется принудительно, т. е. с помощью насосов в передвижную емкость.
Рисунок 28 - Дренажные устройства горизонтальных резервуаров (уклон 1:40):
а ,б – для наземных резервуаров, в – для подземных резервуаров ; 1 – вентиль; 2 - сливная труба; 3 - присоединительные устройства
Система централизованного слива обеспечивает: своевременный контроль образования продуктов отстоя; освобождение резервуаров от остатков топлива перед их зачисткой или ремонтом; сокращение потерь топлива при сливных операциях; снижение пожароопасности, улучшение санитарного состоя-бия территории резервуарного парка и облегчение условий труда обслуживающего персонала при производстве сливных работ, особенно в осенне-зимний период.
Система централизованного слива (рис. 29) включает сливной узел резервуара А; узел слива отстоя Б и трубопроводы, связывающие их. Сливной узел резервуара предназначен для герметичного соединения сифонного крана с трубопроводом при слипе отстоя или остатка топлива из резервуара. Они изготовляются двух типов: с герметичной и негерметичной воронкой. В парном случае воронка изготавливается из труб, а во втором - из листового металла.
Рисунок 29 - Принципиальная схема системы централизованного слива отстоя
из резервуаров
Сливной узел резервуара с герметичной воронкой (рис. 30) состоит из хвостовика 5, сифонного крана 8, передвижной крышки 9 с рукояткой 2, воронки 10 и переходника 4 со штифтом 7. Герметичность соединения переходника 4 с хвостовиком 5 обеспечивается резиновыми уплотнительными колодками 6, герметичность соединения передвижной крышки 9 с переходником - резиновыми кольцами 3, а с воронкой 10 - резьбовым соединением с прокладкой 1. Нижняя часть воронки приварена к сливному трубопроводу 11.
При сливе отстоя из резервуара крышка 9 должна быть передвинута в верхнее положение. По окончании сливных работ, а также при освобождении резервуара от остатка топлива крышку 9 следует установить в нижнее положение и плотно навинтить на воронку 10.
Рисунок 30 - Сливной узел резервуара с герметичной воронкой
Сливной узел резервуара с негерметичной воронкой (рис. 31) предусматривает подвижное соединение верхнего конца переходника 6 с хвостовиком 8 сифонного крана 11, а нижнего со сливным трубопроводом 1 - жесткое. Крышка 4 воронки 3 в этом случае выполняется съемной. При сливе отстоя из резервуара крышка 4 снимается и открываются задвижки 2 и 7. При освобождении резервуара от остатка топлива открывается только задвижка 5. Переходник 6 фиксируется на хвостовике 8 с помощью штифта 10, а герметичность соединения достигается резиновыми кольцами 9. Конструкция обоих типов сливных узлов резервуаров позволяет производить поворот сифонных кранов в рабочее и нерабочее положения с помощью поворотной рукоятки.
Рисунок 31 - Сливной узел с негерметичной воронкой
Узел слива отстоя (см. рис. 29) предназначен для: приема отстоя, сливаемого из резервуаров 1 и 25; забора остатка топлива и прием его из резервуаров 1 и 25 при подготовке их к зачистке или ремонту и других операций, о которых будет сказано ниже. Он состоит из горизонтальных подземных резервуаров 7, самовсасывающего насоса 8 (например, типа СВН-80), сетчатого фильтра 11, фильтра 13 типа ТФ-2М, присоединительных наконечников 9, сливных воронок 14, 19 и задвижек 10, 12, 15, 16, 17, 18, 20, 21, 22 и 23. -
Принцип работы централизованной системы со сливным узлом, имеющим герметичную воронку, заключается в том, что при сливе отстоя из резервуаров 1 и 25 сифонные краны 2 и 24 устанавливаются в рабочее положение, задвижки 20, 16, 18 открываются, крышка переходника свинчивается с воронки и передвигается в рабочее положение, затем открывается запорная арматура, установленная на сифонных кранах. Продукты отстоя под действием столба топлива будут поступать из резервуаров 1 и 25 по трубопроводу 6 в резервуар 7. Одновременно осуществляется визуальный контроль сливаемого продукта.
После окончания слива отстоя сифонные краны 2 и 24 устанавливаются в нерабочее положение и закрываются, передвижная крышка плотно навинчивается на воронку, а задвижки 20, 16 и 18 закрываются.
Освобождение резервуаров 1 и 25 от остатков топлива при их подготовке к зачистке или ремонтным работам осуществляется принудительно: сифонные краны устанавливаются в рабочее положение и открываются задвижки 20, 17 и 18, затем включается насос 8. Сливаемый остаток подается насосом 8 в заранее подготовленный чистый резервуар 7, емкость которого должна соответствовать объему сливаемого остатка топлива.
Кроме указанных операций система централизованного слива обеспечивает слив отстоя из ТЗ (открыты задвижки 15, 17, 18 или 10, 17 и 18); выдачу отстоя или остатков топлива из резервуаров 1 и 25 в передвижные резервуары (открыты задвижки 10 или 12), (открыты задвижки 12, 16, 18 или 10, 16, 22); забор и выдачу отстоя или остатка топлива из резервуаров 1 и 25 в передвижные резервуары (открыты задвижки 10 или 12).
Указатель уровня (рис. 32) предназначен, для контроля уровня топлива в резервуаре с отсчетом показаний у резервуара или на пульте дистанционного управления склада ГСМ аэропорта.
Указатель уровня типа УДУ-5П состоит из счетного механизма 1, трубы 2, системы блоков 3 с гидравлическим затвором, приставки для дистанционного отсчета показаний, металлической ленты 6, поплавка 7, направляющих тросов 5. Направляющие тросы крепятся к резервуару верхним 4 и нижним 8 креплениями. Поплавок 7 соединен со счетным механизмом 1 лентой 6, которая выведена к нему через герметичную блочную систему 3 и трубу 2. Принцип действия указателя заключается в том, что при заполнении или опорожнении резервуара поплавок 7 перемещается по вертикальным направляющим тросам 5 вместе с уровнем топлива.
Рисунок 32 - Указатель уровня типа УДУ-5П
С поплавком перемещается и лента, которая приводит в движение маховик счетного механизма и его стрелку. Одновременно с этим передается вращение и на контактный механизм дистанционной приставки, сигналы от которой поступают на пульт дистанционного управления. В настоящее время выпускается аналогичный прибор более совершенной и надежной конструкции УДУ-10.
Сниженный пробоотборник предназначен для полуавтоматического отбора средней пробы из вертикальных резервуаров. Они выпускаются трех типов: ПСР-4, ПСР-5 и ПСР-7. На наземных вертикальных резервуарах с максимальной высотой 12 м и резервуарах с понтонами с такой же высотой устанавливаются пробоотборники ПСР-4, ПСР-7 соответственно, а на заглубленных резервуарах с максимальной высотой 7 м - пробоотборник ПСР-5.
Пробоотборник ПСР-4 (рис. 33) состоит из сливного крана 1, пробоотборной трубки 2, воздушной трубки 3, воздушного насоса 7, сильфонного клапана 9 с входным отверстием 8. Для монтажа пробоотборника в резервуаре предусматривается монтажный люк 6 и горловина 4. Нижняя часть пробоотборника монтируется в нижнем поясе резервуара 5. Пробоотборная трубка 2 в верхней части сообщается с паровоздушным пространством резервуара, а нижний конец ее выведен из резервуара и перекрыт краном 1. Верхняя часть трубки 3 заглушена, а нижняя выведена из резервуара и присоединена к насосу 7.
Рисунок 33 – Сниженный пробоотборник ПСР-4
При отборе проб в трубку 3 с помощью воздушного насоса 7 нагнетается воздух и создается давление, под воздействием которого открываются сильфонные краны 9, обеспечивая поступление топлива через отверстие 8 в трубку 2. Снизив давление в трубке 3, открывают кран 1 и сливают в сосуд топливо, находящееся в трубке 2.
Насосные станции
Насосные станции (насосные агрегаты) систем ЦЗС располагаются непосредственно за группой расходных резервуаров на расстояниях, обоснованных гидравлическими расчетами и противопожарными требованиями. Они предназначены для забора топлива из расходных резервуаров и подачи его по трубопроводной сети системы ЦЗС через фильтрационные пункты к заправочным агрегатам с определенными расходом и избыточным давлением, необходимым для заправки обслуживаемых типов самолетов.
Для каждой насосной станции количество насосов определяется из расчета обеспечения одновременной заправки самолетов в часы пик, а типы насосов подбираются в зависимости от характера трубопроводной сети, применяемого оборудования и приемистости заправочных точек (горловин или штуцеров) обслуживаемых типов самолетов.
В насосных станциях систем ЦЗС используются преимущественно центробежные насосы, причем независимо от производительности системы как минимум предусматриваются два насоса, один из которых может быть резервным и при необходимости - рабочим. Устанавливать один насосный агрегат, рассчитанный на максимальную производительность системы, неэкономично, так как при меньшем количестве одновременно заправляемых самолетов работа такого агрегата будет нерентабельной, если в его конструкции не предусмотрено изменение подачи с соответствующим уменьшением затрат электроэнергии.
Наибольшее распространение получили насосные станции с группой параллельно установленных насосов, автоматически включающихся для подачи топлива в зависимости от количества одновременно заправляемых самолетов.
Современные стационарные ГЗТ работают по принципу высокого и низкого давления в топливоподающих трубопроводах. Соответственно рассчитываются и подбираются насосные группы ГЗТ, их напорные характеристики и суммарная подача топлива. В системах ГЗТ с высоким давлением в магистралях напор, создаваемый насосами, должен обеспечивать необходимое давление в трубопроводных магистралях, раздаточных колонках и агрегатах заправки до бортовых штуцеров ВС включительно с учетом их приемных способностей при групповой заправке нескольких ВС.
В системах ГЗТ с низким давлением насосная станция должна поддерживать постоянное давление, компенсируя потери в трубопроводах до приемного рукава агрегата заправки, который должен иметь собственный топливный насос, обеспечивающий заправку топливом ВС. В системах обоих типов потеря давления на участках между входом в приемный рукав агрегата заправки и бортовым штуцером ВС составляет около 80% суммарный потери напора насосных станций.
Для расчета требуемой подачи насосной станции ГЗТ и определенного внутреннего диаметра магистрального трубопровода и всей трубопроводной сети в начале определяется требуемая производительность системы ГЗТ. Согласно отечественным нормативным документам производительность системы ГЗТ определяется по формуле:
(2.1)
где Qгзт – истинная производительность ГЗТ, м3/ч;
q – расчетная производительность заправки топливом ВС по группам или типам, м3/ч;
Uз – максимальная интенсивность поступления ВС по группам или типам, ед/ч;
tз – расчетная продолжительность заправки топливом ВС каждой группы или типа, ч;
I = 1,2,3 …n – количествогрупп или типов ВС, подлежащих заправке топливом из системы ГЗТ;
По зарубежному опыту при выборе насосов, их количества и характеристик рекомендуется учитывать следующие аспекты [28]:
Максимальная производительность системы ГЗТ в расчете на один насос или подача одного насоса не должны превышать 4500 л/мин;
Число насосов в группе, включенных по параллельной схеме не должно превышать шести;
При необходимости развития на ГЗТ большой производительности создаются две групп насосов, соответственно подключаемых к разным участкам раздаточных систем, например, на перронах для разных типов ВС.
В составе каждой группы насосов один из них или дополнительный насос меньшей производительности должны поддерживать постоянно расчетное давление в трубопроводных магистралях системы, чтобы компенсировать потери и обеспечивать готовность системы к работе.
На входе во всасывающую линию каждого насоса должен быть установлен фильтр грубой очистки топлива от твердых частиц загрязнения для защиты оборудования насоса, а в напорной линии после каждого насоса в отечественной и зарубежной практике, как правило, устанавливаются фильтры-водоотделители с пропускной способностью, равной подаче насоса и необходимая арматура. Таким образом, образуется автономный насосно-фильтрационный блок, который для технического обслуживания насоса или фильтра-водоотделителя можно временно перекрыть, не прерывая работу всей системы ГЗТ. Кроме того, в зависимости от конкретных условий могут устанавливаться индикаторы контроля температуры корпуса насоса. Типовая схема компоновки одной из групп насосов приведена на рис. 34.
|
|
|
|
|
|

Рисунок 34 - Схема компоновки одной группы насосов на центральной
насосной станции:
А – реле давления; В – расходомер; F – устройство контроля потока; ФВ – фильтр-водоотделитель; G – выключатель предельного значения; Т – реле времени; М – электродвигатель; Р1 – Р6 – главные насосы; S – насос для поддержания постоянного давления; MU – преобразователь измеряемых величин
Насосные агрегаты работают в следующем порядке (рис. 35). При отсутствии расхода топлива на заправку вся система заполнена топливом и находится под некоторым избыточным давлением, оставшимся после предшествующей работы насосов, которое поддерживается гидроаккумуляторами (гидроамортизаторами) или за счет включения подкачивающих насосов, когда давление в сети станет ниже установленного.
Рисунок 35 - Принципиальная схема группы фильтрации, регулирования и
подачи топлива:
1- приемный трубопровод; 2 – задвижки; 3 – расходный резервуар; 4 - сетчатые фильтры; 5 - перепускные клапаны; 6 - фильтры-водоотделители; 7 - клапан отсечения потока; 8 - отключающие задвижки; 9 - напорный трубопровод; 10 - задвижка: 11 - расходомер-регулятор; 12 - электроконтактный манометр; 13 - пульт управления; 14, 16 - насосные агрегаты; 15 - кабели управления
Как только в какой-либо точке раздаточной сети трубопроводов откроют клапан для заправки самолета, давление в сети снижается, вследствие чего смещается стрелка электроконтактного манометра 12 и замыкает пусковой контакт. Импульс передается на пульт управления 13, последний через систему вторичных приборов включает один из насосов 1 - 6 с подачей 1250 л/мин и одновременно в канале минимального расхода открывается задвижка с электроприводом 10. Так как диаметр канала минимального расхода невелик, то даже при незначительных расходах в канале устанавливаются достаточные скорости, чтобы привести в действие расходомер-регулятор 11.
Если расход топлива в распределительной сети не превышает 1000 л/мин, то работает только один насос 16 и открыт только канал минимального расхода. Если же расход топлива начинает возрастать, то при достижении критического значения для данного канала срабатывает расходомер-регулятор 11, посылая импульс на пульт управления 13.
При получении импульса автоматическая система пускает один из более мощных насосных агрегатов 14 с подачей до 2150 л/мин, открывается задвижка 10 с электроприводом в канале среднего расхода, выключается электродвигатель насоса 16 и закрывается задвижка 10 в канале минимального расхода. Если расход топлива продолжает возрастать, срабатывает расходомер 11 в канале среднего расхода, включается второй насос 14 с подачей 2150 л/мин, открывается задвижка с электроприводом 10 в канале максимального расхода и закрывается задвижка 10 в канале среднего расхода.
При подключении на заправку еще одного самолета расход топлива в сети начнет возрастать и при достижении 4200 л/мин импульсный расходомер 11 в канале максимального расхода срабатывает, посылая импульс на пульт управления, начинает работать третий насос 14 с подачей 2150 л/мин. При снижении расхода в распределительной сети происходит обратный процесс последовательного отключения насосов. Некоторые схемы предусматривают последующее включение насосных агрегатов и подключение расходомеров без отключения насоса 16 и канала минимального расхода.
Подача топлива в системы ЦЗС осуществляется чаще всего стационарными, реже подвижными и передвижными насосными станциями.
К стационарным относятся станции (рис. 36), оборудование которых монтируется на стационарных фундаментах и опорах и устанавливается, как правило, в зданиях. Оборудование подвижных насосных станций монтируется па шасси автомобилей, а оборудование передвижных на автоприцепах или специальных тележках.
Рисунок 36 - Оборудование стационарной насосной станции:
1 - насосы системы ЦЗС; 2 - насосы для внутрискладских перекачек; 3 - вакуумный насос; 4 - щитовая; 5 - вентиляционная камера; 6, 10 - фильтры предварительной очистки; 7 - сетчатые фильтры; 8 - обратный клапан; 9 - предохранительный клапан; 11 - задвижки;
12 - фильтры тонкой очистки
Здание насосной станции обычно включает: машинный зал, фильтрационный пункт (если он совмещен с насосной станцией), вентиляционную камеру, помещение для обслуживающего персонала и другие вспомогательные помещения.
Материалы стен, покрытий и полов насосной должны обладать соответствующей огнестойкостью. Полы делаются из материалов, не впитывающих нефтепродукты и обеспечивающих хорошее смывание пролитых нефтепродуктов. В полах предусматриваются стоки, по которым пролитые нефтепродукты удаляются в промышленную канализацию через гидравлические затворы.
В системах ЦЗС с небольшими расходами топлива насосные агрегаты могут устанавливаться на открытых площадках, под навесами или в специальных камерах и кожухах, если позволяют местные условия.
В комплекс основного оборудования стационарных насосных станций входит: насосы, двигатели, средства фильтрации, трубопроводная обвязка с запорной и предохранительной арматурой, контрольно-измерительные приборы, электрооборудование, вентиляционное и грузоподъемное оборудование. Насосные станции рекомендуется оборудовать однотипными, взаимозаменяемыми центробежными насосами с приводом от электродвигателей во взрывобезопасном исполнении. Не исключается использование для этих целей двигателей внутреннего сгорания и газотурбинных двигателей с соблюдением требований по пожарной безопасности.
В насосных станциях, как правило, устанавливаются рабочие и резервные насосы. Как исключение, работа без резервного насоса допускается в том случае, если количество рабочих насосов больше двух, а работа без резерва обоснована. Резервные насосы используются при выходе из строя или проведении профилактических работ рабочим насосам. Для каждой насосной станции количество рабочих насосов определяется расчетом исходя из того, что их суммарная подача должна соответствовать расходу топлива в час максимальной интенсивности вылета самолетов. Включение и выключение насосов может осуществляться дистанционно, с мест заправки или автоматически.
Одним из возможных вариантов современной компоновки насосной станции является исключение вспомогательного насоса, но при этом, по крайней мере, один из «дежурных» насосов группы должен иметь регулируемую подачу, в том числе и за счет изменения оборотов электропривода.
Насосные агрегаты в зависимости от их количества размещаются в машинном зале в один или два ряда, при этом должен быть обеспечен свободный доступ для их обслуживания.
Соединение насосов между собой и с трубопроводной сетью системы ЦЗС осуществляется с помощью трубопроводной обвязки, которая с установленной на ней запорной и предохранительной арматурой образует технологическую схему трубопроводов насосной станции. Выбор технологической схемы насосной станции производится с учетом обеспечения: возможности отключения любого насоса на период проведения регламентных (ремонтных) работ без прекращения работы станции или значительного уменьшения ее суммарной подачи; одновременной работы нескольких насосов в группе с требуемым суммарным расходом; оперативного управления задвижками в аварийных случаях; возможности подключения подвижных и передвижных средств перекачки при выходе из строя насосной станции.
Для обеспечения безопасности работы системы ЦЗС и поддержания а ней требуемого давления напорные липни трубопроводов соединяют со всасывающими байпасами, на которых устанавливаются предохранительные клапаны, отрегулированные на определенное давление.
Трубопроводы насосной станции в основном укладываются в специальных каналах, сделанных в полу. Запорную арматуру насосных станций рекомендуется сосредоточивать по возможности в одном месте.
Электрооборудование насосных станций (пусковые электроприборы, выключатели, телефонные аппараты и т.д.) изготавливают взрывобезопасными. Освещение насосных станций - электрическое внутреннее во взрывобезопасном исполнении или наружное с применением рефлекторных светильников и наружной электропроводкой.
Необходимо учитывать, что правильное устройство освещения и достаточная освещенность обеспечивают наибольшую безопасность труда и предотвращают аварии. При внутреннем освещении насосных станций допускается общая освещенность не менее 30 лк. Местное освещение, устраиваемое для электродвигателей и насосов, должно быть не менее 30 лк, для измерительных приборов - не менее 50 лк.
Насосные станции оборудуют естественной вентиляцией с применением дефлекторов или искусственной вентиляцией с применением взрывобезопасных вентиляционных установок.
Необходимая для насосной станции величина кратности обмена воздуха в 1 ч определяется расчетным путем. Так, для помещения насосной станции высотой 6 м, перекачивающей авиатопливо с содержанием сернистых соединений, кратность воздухообмена равна 10, а без сернистых соединений - 8. Для помещений меньшей высоты кратность воздухообмена увеличивается на 16% на каждый метр снижения высоты здания насосной станции.
Для обеспечения надежной работы насосов необходимо тщательно производить расчет фундаментов, на которые они устанавливаются. Фундаменты устанавливают в виде массивов с колодцами для анкерных болтов. Основанием под фундаменты служит грунт, плотно утрамбованный щебнем, под давлением не менее 1,5 кгс/см2.
Фундаменты под агрегаты не должны опираться или жестко связываться с элементами здания насосной во избежание передачи на них вибраций.
Для облегчения и удобства монтажа и демонтажа оборудования насосные станции рекомендуется оснащать грузоподъемными устройствами: при массе отдельного оборудования до 500 кг - переносными треногами и талями, при большей массе - монорельсами с кошками или талями.
Трубопроводная сеть ГЗТ
Трубопроводная сеть современных стационарных ГЗТ состоит из магистральных, распределительных и раздаточных магистралей. В проектах ГЗТ в начале их строительства магистральный трубопровод является главной топливоподающей линией большого диаметра, однако по экономическим и другим соображениям более рациональным в настоящее время рассматривается строительство двух параллельных главных линий меньшего диаметра, обеспечивающих подачу топлива от насосной станции к распределительным трубопроводам, например, кольцеобразного типа [6,28]. Этот вариант имеет следующие преимущества:
Более низкие скорости потока топлива;
Возможность переключения насосных групп с линии на линию при выходе из строя одной магистрали;
Возможность расширения трубопроводной сети;
Лучшие условия для гидравлических испытаний и промывки трубопроводов, особенно на начальной стадии строительства.
Трассирование трубопроводной сети и технологическая схема ГЗТ во многом зависят от конкретных условий аэропорта, поэтому важным является определение вида распределительной трубопроводной сети, которая обеспечивает распределении потока топлива по раздаточным трубопроводам. Трубопроводная сеть может быть выполнена по типу кольцевой, тупиковой и смешанной схем. Предпочтение для высокопроизводительных стационарных ГЗТ отдается кольцевым и смешанным схемам [28]. Трубопроводная сеть с тупиковой схемой используется главным образом для упрощенных и сборно-разборных ГЗТ малой производительности.
Раздаточные трубопроводы являются концевыми участками трубопроводной сети, по которым топливо подается к отдельным гидрантным колонкам (агрегатам заправки).
Трубопроводная сеть современных стационарных ГЗТ обычно включает трубопроводы байпасных линий, в том числе для периодических испытаний и промывки трубопроводной сети. На рис. 37 приведена типовая схема промывочных трубопроводов по «малому» и «большому» кольцам.
Распределительные трубопроводы могут обеспечивать также подвод топлива к пунктам налива цистерн аэродромных топливозаправщиков при смешанном виде заправки топливом ВС. Это существенно сокращает пробег топливозаправщика по сравнению с их наливом на пунктах склада ГСМ.
Рисунок 37 – Технологическая схема промывочных колец ГЗТ:
1 - фильтр предварительной очистки; 2,9,14 - фильтры-сепараторы; 3 - насосный агрегат; 4 - индикатор потока топлива; 5,8,15 - штуцера для отбора проб; 6 - расходные резервуары; 7 - насосы; 10 -датчик расхода; 11 - устройства для автоматического включения насосов; 12 - устройство для автоматического включения первого насоса; 13 - устройства для налива автотопливозаправщиков; 16 - расходомер; 17 - посты заправки; 18 - вторичный регулятор; 19 - первичный регулятор; 20 - пантограф; 21 - раздаточный рукав; 22 - наконечник закрытой заправки; 23,24,25,26 - переходники для испытания трубопровода на герметичность
Магистральную и распределительную части трубопроводной сети рассчитывают на максимально возможный расход в часы пик с учетом одновременной заправки максимального расчетного количества самолетов. Раздаточные трубопроводы рассчитывают исходя из максимально возможной приемистости топливной системы обслуживаемых самолетов. Гидравлические расчеты производятся с учетом наименьшего уровня топлива в расходном резервуаре и наибольшей вязкости топлива, соответствующей средней температуре самой холодной пятидневки для района, в котором размещен аэропорт. Вязкость топлив в зависимости от температуры окружающего воздуха приведена в таблице 15.
Таблица 14 - Вязкость топлив в зависимости от температуры окружающего воздуха
Температура, °С | Вязкость, см2/с | |||
Т-1 | ТС-1 | РТ | Т-8В | |
+20 | 0,016 | 0,013 | 0,013 | 0,018 |
+ 10 | 0,02 | 0,015 | 0,014 | 0,022 |
0 | 0,023 | 0,018 | 0,018 | 0,028 |
-10 | 0,038 | 0,023 | 0,022 | 0,036 |
-20 | 0,051 | 0,03 | 0,028 | 0,048 |
-30 | 0,07 | 0,042 | - | - |
-40 | 0,1 | 0,06 | 0,049 | 0,09 |
-50 | 0,14 | 0,08 | - | - |
Расчетные диаметры участков трубопроводов определяются по формуле:
(2.2)
где d - диаметр трубопровода ,м;
W - расчетная скорость движения топлива в трубопроводе, м/с;
Q - максимальный расход топлива, м3/ч.
Исходя из технико-экономических соображений, а также снижения вероятности возникновения статического электричества и гидравлических ударов рекомендуемая расчетная скорость движения топлива в системах ЦЗС-1,5-1,7 м/с. По полученному расчетному диаметру подбирается в соответствии с ГОСТом фактический диаметр трубопровода dф и по его величине рассчитывается или определяется по номограмме (рис. 38) фактическая скорость движения топлива Wф, величина которой необходима для дальнейших расчетов. Суммарные потери напора определяются исходя из условий подачи топлива через наиболее удаленную гидрантную колонку (заправочный агрегат):
Hå = hтр + hм + hо + рк + Dz (2.3)
где Hå - суммарные потери, м;
hтр - потери на трение по длине трубопровода, м;
hм - местные потери, м;
hо - потери в оборудовании, м;
рк - максимальное конечное давление при заправке, м;
Dz - разность геодезических отметок оси насоса и заправочной точки ВС, м.
Рисунок 38 - Номограмма определения скорости движения топлива в зависимости
от условного диаметра трубопровода и расхода ,(t = 20°C, Y = 0,01i5 см2/с)
Потери напора на трение hтр по длине рассчитываются для каждого участка определенного диаметра:
hтр = iL (2.4)
где i - гидравлический уклон;
L — длина расчетного участка трубопровода, м;
Величина гидравлического уклона рассчитывается по формуле или определяется по номограмме рис. 39.
(2.5)
где l - коэффициент гидравлического сопротивления;
Wф - скорость движения топлива в трубопроводе, м/с;
dф - внутренний диаметр трубопровода, м;
g - ускорение силы тяжести (9,81 м/с2).
В гидравлике различают два режима движения жидкости в трубопроводе: ламинарное и турбулентное. Характер движения определяют по значению числа Рейнольдса:
(2.6)
где W - скорость движения жидкости по трубопроводу, см/с;
d - внутренний диаметр трубопровода, см;
g - кинематическая вязкость, см2/с.
Рисунок 39 - Номограмма определения гидравлического уклона в зависимости от условного диаметра трубопровода и скорости движения топлива (t = 20°С, g = 0,015 см2/с)
При Re < 2320 движение считается ламинарным, а при Re ³ 2320 - турбулентным.
При ламинарном движении жидкости (Re < 2320) коэффициент гидравлического сопротивления определяется по формуле l = 64/Re, при турбулентном режиме:
(2320 £ Re < Re1 = 8000) коэффициент .
При турбулентном режиме ( коэффициент l определяется по формуле:
(2.7)
Относительная шероховатость стенок труб e рассчитывается по формуле:
(2.8)
где e - абсолютная высота выступов, мм;
d - внутренний диаметр, мм.
При турбулентном режиме (Re2 < Re) коэффициент .
В трубопроводах наряду с потерей напора на трение по длине происходят местные потери hм, обусловленные местными сопротивлениями в задвижках, угольниках, тройниках, в местах изменения диаметра трубопровода и т. д. Для простоты расчета величину местных потерь hм допускается принимать равной 10% от величины потерь напора по длине. Потери напора в оборудовании hо принимаются с учетом его гидравлических характеристик.
Величины потерь в основных видах оборудования при максимальном расходе топлива следующие:
р, кгс/см2 | |
Фильтр | 0,5 - 1,5 |
Гидрантный регулятор | 1,5 - 2,5 |
Заправочный агрегат | 3,5 - 4,5 |
Датчик расхода | 0,3 - 0,5 |
Дозатор жидкости «И» | 0,3 - 0,5 |
Счетчик | 0,3 |
Стояк для налива топлива в ТЗ (без оборудования) | 0,25 |
Максимальное конечное давление заправки рк определяется типом обслуживаемых самолетов. При гидравлических расчетах величина рк принимается в пределах от 3 до 4,5 кгс/см2. Разность геодезических отметок оси насоса и заправочной точки самолета Dz зависит от рельефа местности и высоты расположения заправочной точки от аэродромного покрытия.
Для обеспечения бесперебойной подачи топлива на заправку в системах ЦЗС может использоваться не один, а два трубопровода. В этом случае гидравлический расчет ведется исходя из одновременной работы обоих трубопроводов, причем каждый рассчитывается на расход, равный 75% общего расхода топлива. Для трубопроводных сетей используются стальные бесшовные и электросварные трубы со спиральным швом, имеющие внутреннее и внешнее антикоррозионное покрытие. Для внутренней противокоррозионной защиты стальных труб используются специальные топливостойкие эмалированные или лакокрасочные покрытия холодной сушки.
При подземной укладке внешняя поверхность труб защищается от коррозии путем нанесения изоляции на основе битумов или полимерных материалов, а при наземной - путем окраски. Кроме того, при подземной укладке внешняя поверхность труб защищается от воздействия блуждающих токов. При монтаже трубопроводной сети соединение труб осуществляют при помощи неразъемных и разъемных соединений. В качестве неразъемных соединений используется сварка, а разъемных - фланцевые и муфтовые соединения. Необходимо отметить, что существуют два вида муфтовых соединений: нарезные и ненарезные. Применять в трубопроводных сетях систем ЦЗС нарезные соединения не рекомендуется [20].
Сварные соединения прочны, экономичны и надежны в эксплуатации. Неразъемность сварных соединений является их основным недостатком. Фланцевые и муфтовые соединения легко собираются и разбираются, однако по сравнению со сварными соединениями имеют следующие недостатки: они дороже сварных, требуют большего расхода металла, так как на концах соединяемых труб необходимо приваривать фланцы или специальные манжеты (при муфтовом соединении); не исключена возможность нарушения герметичности соединения, так как при эксплуатации может произойти ослабление болтов или пробивка прокладочного материала при его «старении»
Сварные и фланцевые соединения обычно используют в стационарных трубопроводных сетях, причем фланцевые соединения применяют на тех участках, где требуется устанавливать трубопроводную арматуру и оборудование систем ЦЗС (задвижки, обратные клапаны, фильтры и т. д.). Муфтовые соединения, как правило, применяются в сборно-разборных трубопроводных сетях, создаваемых на базе комплекта сборно-разборного трубопровода РТ-100-1,5 или из труб и оборудования комплекта сборно-разборного трубопровода МТ-150.
В комплектах сборно-разборных трубопроводов используются стальные электросварные трубы длиной 6 м с диаметром условного прохода 100 и 150 мм. Внутренняя и внешняя поверхности труб должны иметь покрытие [49]. К концам труб приварены манжеты, имеющие кольцевые выточки под соединительные муфты типа МПТ.
Соединительная муфта МПТ (рис. 40) состоит из двух полумуфт: верхней и нижней 3. На нижней полумуфте имеются два откидных болта 2 с гайками 5. Откидные болты крепятся к нижней полумуфте с помощью осей 4. Герметичность соединения обеспечивается с помощью резинового уплотнительного кольца, изготовленного из маслобензостойкой резины и поставляемого в комплекте с муфтой.
Монтаж соединения осуществляется в следующей последовательности: резиновое кольцо с некоторым натягом надевают на венчики манжет соединяемых труб, затем на резиновое кольцо надевают нижнюю и верхнюю полумуфты и затягивают откидные болты (рис. 41). Предварительный натяг резинового уплотнительного кольца обеспечивает герметичность соединения при отсутствии в трубопроводе избыточного давления. При возрастании давления в трубопроводе топливо давит на внутреннюю полость кольца и плотнее прижимает его рабочие поверхности к венчикам манжет, в результате чего герметичность соединения улучшается.
Рисунок 40 - Соединительная муфта МПТ
Рисунок 41 - Муфтовое соединение в сборе:
1 – труба; 2 – муфта МПТ; 3 – резиновое уплотнительное кольцо
Такое соединение обеспечивает: необходимую прочность и герметичность соединения; самокомпенсацию изменения длины трубопровода при температурных колебаниях; поворот одной трубы относительно другой в пределах 3 - 4° и оперативную замену труб и оборудования на собранном трубопроводе.
Трубопроводы РТ-100-1,5 т укомплектовываются муфтами МПТ-10-4 с условным проходом 100 мм, а трубопроводы МТ-150 - муфтами МПТ-15-4 с условным проходом 150 мм. Трубы трубопроводных сетей систем ЦЗС могут прокладываться наземно, подземно или в специальных коллекторах [20]. Наземная укладка трубопроводной сети является наиболее экономичной и удобной в эксплуатации, в этом ее основное преимущество. Однако, по климатическим и архитектурно-планировочным соображениям этот способ прокладки не везде может быть использован, так как он имеет ряд существенных недостатков. При наземной укладке трубопроводная сеть загромождает территорию аэропорта и стесняет свободу маневрирования средств наземного обслуживания самолетов. Кроме того, наземные трубопроводы в большей степени, чем подземные, подвержены температурным колебаниям атмосферы, поэтому для них должны предусматриваться устройства для разгрузки от температурных напряжений.
Таблица 15
Диаметр труб, мм | Толщина стенки, | Расстояние между опорами, м | ||
условный | наружный | Неизолированные трубопроводы | Изолированные трубопроводы | |
20 | 25 | 2,5 | 3 | 2 |
25 | 32 | 2,5 | 4,5 | 2 |
40 | 45 | 3 | 5,5 | 3 |
50 | 57 | 3,5 | 6 | 3,5 |
70 | 76 | 4 | 6,5 | 4 |
80 | 89 | 4 | 7 | 4,5 |
100 | 108 | 4 | 7,5 | 5 |
125 | 133 | 4 | 8 | 5,5 |
150 | 159 | 4,5 | 8,5 | 6 |
200 | 219 | 6 | 10 | 7 |
250 | 273 | 7 | 10 | 7 |
300 | 325 | 9 | 11,5 | 9,5 |
350 | 377 | 10 | 13 | 11 |
400 | 426 | 11 | 13 | 11 |
450 | 478 | 9 | 13 | 11 |
500 | 529 | 9 | 13 | 12 |
При наземной укладке трубопроводы рекомендуется прокладывать на кирпичных, бетонных или металлических опорах. Крепление труб к опорам должно обеспечить продольное перемещение, которое возникает при температурных изменениях длины трубопровода. Расстояние между опорами можно определить по таблице 15 или рассчитать по формуле [20]:
(2.8)
где l - расстояние между опорами, м;
Е - модуль упругости, кгс/см2;
I - момент инерции поперечного сечения трубы, м4;
f - стрела прогиба, м (принимается 3 - 5 мм);
m - масса одного погонного метра трубопровода с топливом, изоляцией и снеговой нагрузкой, кг.
Трубопроводную сеть сборно-разборных систем ЦЗС рекомендуется прокладывать на высоте не менее 0,35 м от уровня земли на опорах, расстояние между которыми не должно превышать 6 м. Опоры располагаются вблизи мест соединений труб между собой.
Подземная укладка трубопроводов дороже наземной, так как требует выполнения большого объема земляных работ.
При подземной укладке затрудняется наблюдение за состоянием трубопроводов, обнаружение дефектов, ремонт и ликвидация аварий.
На трассе подземного трубопровода предусматриваются технологические колодцы в местах, исключающих попадание в них дождевых и талых вод. В технологических колодцах размещается трубопроводная арматура и оборудование. Для исключения возможности попадания в колодец атмосферных осадков корпус колодца закрывают крышкой. При расположении колодцев на перроне или МС корпус и крышка колодца рассчитываются на максимальную удельную нагрузку от самолета. При пересечении подземных трубопроводов с другими коммуникациями рекомендуются следующие расстояния по вертикали в свету: до технических трубопроводов, трубопроводов теплофикации, водопровода - не менее 0,15 м, до силовых и телефонных кабелей - не менее 0,6 м.
Расстояния по горизонтали между подземными трубопроводами и другими сетями рекомендуются следующие:
Расстояние до сетей, м | |
Водопроводы и канализация | 1,5 |
Дренажи и водостоки | 1,0 |
Газопроводы различного давления, кгс/см2: до 0,5 » 3 от 3 до 6 » б » 12 | 1,0 1,5 2,0 5,0 |
Тепловые сети | 2,0 |
Кабели силовые » связи | 1,0 1,5 |
Стационарные трубопроводы прокладываются с равномерным уклоном не менее 1:300. В самых нижних точках каждой линии (рис. 42) устанавливаются гидрантные стояки для забора топлива и отстоя воды, в верхних точках – стояки для выпуска воздуха.
Рисунок 42 - Типовая схема размещения оборудования на напорном
трубопроводе системы ЦЗС:
1,4 - гидрантные стояки; 2- рулежная дорожка; 3 - гидрантный стояк для забора топлива и отстоя из нижней точки трубопровода; 5,6 - подающие трубопроводы с уклоном минимум 0,1° к нижней точке
Для компенсации тепловых удлинений наземных трубопроводов ГЗТ целесообразно использовать его повороты и изгибы, а в отдельных случаях П-образные компенсаторы.
На трассе подземного трубопровода для установки арматуры и оборудования в стационарных системах ГЗТ предусматриваются технологические колодцы. Размер и глубина колодцев определяется при проектировании ГЗТ в зависимости от диаметра трубопроводов, габаритных размеров и количества арматуры, требований удобства ее обслуживания и ремонта [20].
Технологические колодцы располагают, как правило, вне бетонных покрытий, в местах, исключающих их залив паводковыми и талыми водами. Технологические колодцы целесообразно размещать в местах разветвлений трубопроводных линий, чтобы в случае технического обслуживания и устранения неисправностей не приходилось останавливать все трубопроводные сети. Технологические колодцы по трассе трубопровода должны иметь указатели на случай заноса их снегом.
При размещении колодцев на перроне и местах стоянок ВС корпуса и крышки должны быть рассчитаны на максимальную нагрузку ВС. Крышки технологических колодцев должны исключать возможность попадания в колодец атмосферных осадков, обеспечивать удобство и легкость открывания и иметь запорное устройство. Арматура и оборудование, размещенное в технологических колодцах должно пломбироваться. [20]
В новых проектах стационарных ГЗТ для обеспечения обслуживания подземного трубопровода размещают также гидрантные стояки в верхних и нижних частях участков напорных трубопроводов по трассе. Типовая схема размещения оборудования гидрантного стояка в верхней части напорного трубопровода показана на рис. 43.
Рисунок 43 - Типовая схема размещения оборудования гидрантного стояка в верхней части напорного трубопровода системы ГЗТ:
1 – восходящая ветвь трубопровода; 2 – 102,5 мм трубчатый стояк;
3 – 102,5 мм фланец; 4 – переходник 102,5х19,5 мм; 5 – задвижка;
6 – запорная муфта типа Комлок с крышкой и заземлением; 7 – крышка люка; 8 – 19,5 мм фланец
Гидрантные стояки с арматурой используются для выпуска воздуха из трубопроводов, а также для подключения оборудования промывки трубопроводов и испытаний, в том числе герметичности.
Типовая схема размещения оборудования гидрантного стояка в нижней части напорного трубопровода системы ГЗТ приведена на рис. 44. Гидрантные стояки такого типа предназначены для забора отстойной воды из трубопроводов и отсоса загрязнений. Для этого также могут использоваться вспомогательные средства обслуживания трубопроводов ГЗТ.
Рисунок 44 - Типовая схема размещения оборудования гидрантного стояка в нижней части напорного трубопровода системы ГЗТ:
1 – падающая ветвь трубопровода; 2 – стальная пластинчатая шайба 102 мм х 3,2 мм приваренная к трубе 19,1 мм; 3 – бетонная площадка; 4 – крышка люка; 5 – запорная муфта типа Комлок с крышкой и заземлением; 6 – задвижка; 7 – переходник 102,5х19,5 мм; 8 – 102,5 мм фланец; 9 – трубопровод диаметром 19,5 мм; 10 – 102,5 мм трубчатый стояк; 11 – отстойник
Трубопроводная арматура на трубопроводных сетях ГЗТ подразделяется на запорную, предохранительную и регулирующую. запорная арматура предназначена для разобщения примыкающих к ней участков трубопровода, а также может быть использована для регулирования расхода протекающего через нее топлива. В качестве запорной арматуры используются задвижки и краны как с ручным, так и с электрическим приводом во взрывобезопасном исполнении, условный диаметр которых может составлять 50-300 мм.
Проходное сечение задвижек обычно закрывается шибером, который перемещается в вертикальном направлении с помощью выдвижного шпинделя. Корпуса отечественных задвижек изготавливаются из чугуна и стали. Присоединительные патрубки корпусов имеют фланцевую оконцовку или манжетную муфту (для сборно-разборных трубопроводов). Задвижки обеспечивают плавность и точность регулирования потока, имеют небольшое гидравлическое сопротивление и строительную длину (рис. 45). Однако задвижки уступают вентилям и шаровым кранам по герметичности, имеют большую массу, что затрудняет их монтаж, они из-за большого хода шпинделя медленно закрываются, поэтому не могут применяться для экстренного закрытия линии трубопровода [ ].
Рисунок 45 - Задвижка с электроприводом типа ЗКЛПЭ
В вентилях проходное сечение закрывается золотником, который перемещается также шпинделем, движущегося по направлению оси перекрываемого золотником прохода [28]. За рубежом находят применение двухблочные запорные вентили с контролем утечек. За счет эластичных уплотнений на двух золотниках таких вентелей достигается высокая степень герметичности [30].
В последние годы в трубопроводных системах ГЗТ находят применение шаровые краны, имеющие ряд преимуществ по сравнению с задвижками и одноблочными вентилями [3-6].
Предохранительная арматура предназначена для предотвращения аварий на трубопроводах. Она включает предохранительные и обратные клапаны, а также клапаны сброса давления. Предохранительный клапан (рис. 46) устанавливается в трубопроводной обвязке между всасывающей и нагнетательной линиями насоса [3].
Рисунок 46 - Предохранительный клапан пружинный фланцевый 17с12НЖ
Он регулируется на максимально допустимое рабочее давление в системе ГЗТ. При давлении выше регулировочного клапан срабатывает и перепускает топливо из нагнетательной линии во всасывающую, вынуждая насос работать «на себя». Предохранительный клапан 17с12НЖ состоит из корпуса 1, крышки 2, колпака 3, регулирующей втулки 4, штока 6, пружины 7 и золотника 8. Верхняя часть клапан закрыта колпаком 3, в котором имеется регулирующий винт для установки пружины на заданное давление. После настройки регулирующая втулка стопорится гайкой 5. Предохранительные клапаны этого типа выпускаются промышленностью с диаметром условного прохода от 50 до 100 мм. Предохранительные патрубки предохранительного клапана имеют фланцы.
Клапан устанавливается в вертикальном положении колпаком вверх. При этом допускается отклонение не более 30°. В зависимости от пружины, которая является сменным элементом, клапан может быть отрегулирован на рабочее давление 2-4; 4-8 и 8-16 кгс/см2. обратные клапаны применяются на тех участках трубопроводной сети, где согласно принятой технологической схеме не допускается движение потока топлива в обратном направлении.
В системах ГЗТ применяются обратные клапаны подъемные фланцевые типа 16ч6р и с захлопкой. Обратный клапан (рис. 47) состоит из корпуса 1, пружины 2, крышки 3 и золотника 4.
Рисунок 47 - Обратный клапан типа 16ч6р
Принцип его работы заключается в том, что золотник 4 открывается под воздействием давления перекачиваемого топлива и пропускает топливо в нужном направлении, а при прекращении перекачки или обратном потоке он закрывается под воздействием пружины 2. Присоединительные патрубки клапана имеют фланцевую оконцовку.
Обратные клапаны 16ч6р выпускаются с диаметром условного прохода от 70 до 200 мм и рассчитаны на рабочее давление 10 кгс/см2, а клапаны 16ч6бр – на 16 кгс/см2. Обратный клапан с захлопкой (рис. 48) имеет присоединительные патрубки с манжетами под соединительную муфту МПТ с условным проходом 100 и 150 мм и используется в сборно-разборных системах ГЗТ.
Рисунок 48 - Обратный клапан с захлопкой
Клапан состоит из корпуса 1, крышки 2, прокладки 3 и запорного устройства, включающего шпиндель 8, рычаг 7 и захлопку 5, которая свободно подвешивается к рычагу 7 с помощью рычага 4. Захлопка 5 в зависимости от направления движения потока топлива может находиться в крайнем левом или крайнем правом положении. Нужное положение захлопки устанавливается вращением шпинделя.
Принцип действия обратного клапан заключается в том, что захлопка 5, свободно подвешенная на рычаге 7 под воздействием напора потока топлива, открывает проходное сечение и пропускает его только в одном направлении. При обратном потоке топливо будет прижимать захлопку к седлу и тем самым перекроет проходное сечение трубопровода. Клапан сброса давления типа КСД относится к оборудованию упрощенных систем ГЗТ и предназначен для ограничения давления в трубопроводах сверх допустимой величины за счет сброса топлива в трубопровод обратного слива. Он устанавливается перед заправочными агрегатами по ходу движения потока топлива на заправку и присоединяется к раздаточному трубопроводу с помощью двух боковых патрубков (правым и левым), а третьим (нижним) – к трубопроводу обратного слива. Схема включения КСД в систему изображена на рис. 49.
Рисунок 49 - Схема включения в трубопроводную сеть КСД
1, 2 – заправочные агрегаты; 3 – раздаточный трубопровод; 5 – клапан сброса давления
Техническая характеристика клапана КСД-ГЗТ
Диапазон настройки регулируемого давления, кгс/см2:
минимального 3
максимального 5
Пропускная способность, л/мин 000
Условный проход, мм 100
Тип присоединительных патрубков ТК-100
Габаритные размеры, мм:
длина 460
высота 485
ширина 400
Масса, кг 16
Клапан сброса давления КСД (рис. 50) состоит из перепускного клапана Б и золотникового устройства А. На корпусе 12 перепускного клапана расположены три присоединительных патрубка: два боковых (правый и левый) и нижний. Все три патрубка имеют фланцевую оконцовку под муфту ТК-100.
Рисунок 50 - Клапан сброса давления КСД
Внутри корпуса 12 в нижней его части размещен клапан, соединенный штоком с мембраной 10. В верхней части корпуса над мембраной установлены две пружины, воздействующие на систему мембрана – шток – клапан. Сила нажатия пружин изменяется регулировочной гайкой. С помощью пружин создаются условия для нормальной работы клапана при наличии в трубопроводе обратного слива давления до 2,2 кгс/см2.
Регулировка пружин производится в заводских условиях, после чего клапан пломбируется.
Принцип работы клапана сброса давления заключается в том, что топливо из внутренней полости корпуса 12 поступает по трубке 2 под поршень 4, который при повышении давления сверх допустимого будет перемещаться в верхнее, крайнее положение, открывая отверстие штуцера трубки 1 и закрывая отверстие штуцера 6 трубки 3. в этом положении поршня 4 топливо поступает по трубке 1 под мембрану 10, которая под воздействием давления топлива прогибается вверх и увлекает за собой шток вместе с клапаном, открывая при этом проходное сечение нижнего патрубка, и топлива сбрасывается из раздаточного трубопровода в трубопровод обратного слива.
При достижении в раздаточном трубопроводе давления заданной величины поршень 4 под воздействием пружины 5 перемещается в нижнее крайнее положение (исходное) и топливо из-под мембраны 10 сливается по трубкам 1 и 3 в трубопровод обратного слива, а мембрана под воздействием двух пружин возвращается в исходное положение. Клапан перекрывает отверстие нижнего патрубка и сброс топлива из раздаточного трубопровода в трубопровод обратного слива прекращается. Регулировка пружины 7 производится в заводских условиях на минимальное (3 кгс/см2) и максимальное (5 кгс/см2) давления открытия клапана. На шпинделе регулировочного винта 9, размещенного в корпусе 8, нанесены две риски – нижняя и верхняя, соответствующие минимальному и максимальному давлению открытия клапана.
В зарубежных стационарных системах ГЗТ в качестве запорно-регулирующей арматуры широко используются клапаны типа «Муэско» [28-30]. На рис. 51 приведена типовая схема участка стационарной системы ГЗТ с технологическим колодцем, в котором размещена основная арматура, в том числе клапан на базе клапанов «Муэско».
Рисунок 51 - Типовая схема участка стационарной системы ГЗТ:
1 - Линейный фильтр; 2 - Разгрузочный клапан; 3 - Ручной запорной вентиль; 4 - Клапан регулирования заправки; 5 - Клапан регулирования расхода; 6 - Клапан регулирования слива; 7 - Насос слива топлива; 8 - Гидрантный вентиль; 9 - Муфта присоединения приемного рукава заправочного агрегата.
Технологический колодец подключен к магистральному напорному трубопроводу и к общему трубопроводу слива топлива из системы ГЗТ. Оборудование обеспечивает подвод и автоматическое регулирование расхода и давления в трубопроводе к гидрантной или присоединительной колонке, гашение гидроудара (пульсации) в напорном трубопроводе сбросом давления в сливную магистраль, слив топлива из трубопровода, в том числе из гидрантной или присоединительной колонки, кольцевание напорной и сливной трубопроводных магистралей, например при промывке системы. Для выполнения этих рабочих операций и процедур обслуживания на напорном трубопроводе установлены два вентиля 3 с ручным управлением и клапан 4 автоматического регулирования расхода и давления. На отводе трубопровода к сливному трубопроводу установлен клапан 2 сброса давления, на втором отводе к сливному трубопроводу установлен фильтр 1, клапан 5 регулирования расхода при сливе топлива, топливный насос 7 с электроприводом, клапан 6 регулирования слива. Таким образом, в схеме технологического колодца использовано четыре клапана «Муэско» с дополнительными устройствами, обеспечивающими в комплексе выполнение функциональных процедур каждого клапана.
На рис. 52 представлен типовой клапан «Муэско», обеспечивающий регулирование расхода и давления топлива, подаваемого в раздаточную магистраль к гидрантной или распределительной колонке ГЗТ [28].
Рисунок 52 - Типовой клапан «Муэско»:
1 – корпус базового клапана; 2 - клапан регулирования расхода; 3 - позиционный датчик 50; 4 - обратный клапан; 5 - регулирование расхода/уставка скорости открытия; 6 - эжектор с нерегулируемым соплом отсечки потока; 7- пластина сопла; 8 - вставной фильтр.
Базовый элемент – перепускной клапан состоит из корпуса 1 с двумя присоединительными патрубками: входного 9 и выходного 10, крышки 11 корпуса с двумя штуцерами в верхней части и регулировочным устройством 3. В нижней внутренней части корпуса 1 размещено клапанное устройство 12, объединенное с мембраной 13 в верхней части. Клапанное устройство в исходном нижнем положении перекрывает канал в корпусе по седлу 14, разобщая входную и выходную полости корпуса. Клапанное устройство 12 закреплено на штоке 15 с направляющим концевиком в нижней части. В верхней части на штоке герметично устанавливается крышка 3, прижимающая мембрану 13 к клапанному устройству 12. Мембрана 13 герметично закреплена между корпусом 1 и крышкой 11. Над крышкой 14 мембраны по штоку 15 установлена пружина 16 с прижимной втулкой 17. Следует отметить, что клапан «Муэско» выпускаются в зависимости от требуемой пропускной способности и по присоединительным патрубкам – соответственно типоряду диаметров трубопроводов (до 400 мм). Для всех клапанов «Муэско» характерным является небольшой ход клапанного устройства 11 и использование для его управления, кроме регулировки пружины 10, давления топлива в линии, поступающего в полость под и над мембраной 13. Для этого, например, клапан (рис. 52) дополнительно оснащен двумя байпасными линиями – трубками диаметром 6-12 мм. На трубках установлены: фильтр 8 в штуцере на входном 9 патрубке, два обратных клапана 4 и тройник 6 с эжектором 18, игольчатый регулируемый клапан 5, мембранный регулятор 2 потока поданного топлива в байпасных линиях. Важным элементом клапана «Муэско» в варианте регулятора расхода и давления, приведенного на рис. 52, является диафрагма 7, установленная во входном 9 патрубке корпуса и соединенная трубками 14 и 20 с полостями мембранного регулятора.
Топливо при подаче давления из входного 9 патрубка через фильтр 8, заполняет трубку 21, проходит через обратный клапан 4, эжектор в тройнике и далее разделяется на два циркулирующих потока. Часть топлива по трубке 22 через игольчатый клапан 5 поступает в надмембранную полость «А» и далее через обратный клапан 4 в выходной 10 патрубок корпуса. Вторая часть потока топлива поступает через клапанную часть мембранного регулятора и далее по трубке к выходному 10 патрубку.
Принцип работы клапан «Муэско» – автоматическое регулирование постоянного расхода и давления топлива условно «за собой», независимо от изменений расхода и давления в напорном трубопроводе до клапана и изменений указанных параметров в расходном трубопроводе при заправке топливом ВС через гидрантную колонку. Это обеспечивается следующим образом. При подаче топлива во входной патрубок 9 под воздействием давления на мембранную часть перепускного клапана 12 пружина 16 сжимается, клапан 12 поднимается, обеспечивая проход основного потока топлива под седлом в выходной патрубок. Скорость открытия клапана (подъема его над седлом 14) зависит от скорости выхода топлива и снижения давления в надмембранной полости А.
Регулирование пружины 16 производится в заводских условиях, после чего регулировочный узел пломбируется, поэтому основное управление скоростью и высотой подъема перепускного клапана осуществляется только за счет перепуска топлива по байпасным линиям и изменения давления в надмембранной полости А. При этом скорость перемещения перепускного клапана обеспечивается игольчатым клапаном, регулировка которого в основном проводится в заводских условиях с возможностью подрегулирования (с последующим пломбированием) в условиях эксплуатации, учитывая удаление установленного клапана от насосной станции ГЗТ. Также в заводских условиях в зависимости от диаметра установленной диафрагмы 7 во входном 9 патрубке выполняется регулирование мембранного клапана 2. Этот комплекс дополнительного оборудования обеспечивает управление перепускным клапаном 12 за счет изменения давления в надмембранной полости в зависимости от изменения давления «до» и «после» диафрагмы клапана 2. Зарубежные специалисты считают, что дополнительное оборудование перепускных клапанов диафрагмами и мембранными клапанами на байпасной линии обеспечивается своевременное регулирование процесса, например, при включении дополнительных насосов и подаче давления в напорном трубопроводе или при прекращении заправки топливом ВС через гидрантную колонку [3-6, 28-30].
Дата добавления: 2018-04-15; просмотров: 1114; Мы поможем в написании вашей работы! |
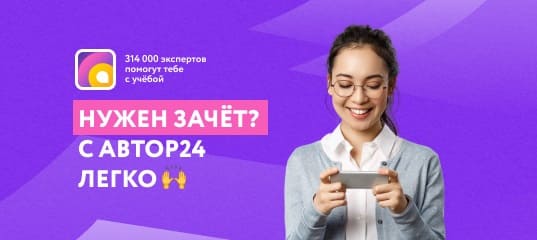
Мы поможем в написании ваших работ!