Основные типы устройств для сухой механической очистки
МИНИСТЕРСТВО ОБРАЗОВАНИЯ И НАУКИ РОССИЙСКОЙ ФЕДЕРАЦИИ ФЕДЕРАЛЬНОЕ ГОСУДАРСТВЕННОЕ БЮДЖЕТНОЕ ОБРАЗОВАТЕЛЬНОЕ УЧРЕЖДЕНИЕ ВЫСШЕГО ПРОФЕССИОНАЛЬНОГО ОБРАЗОВАНИЯ «ВОЛГОГРАДСКИЙ ГОСУДАРСТВЕННЫЙ ТЕХНИЧЕСКИЙ УНИВЕРСИТЕТ»
КАФЕДРА «ПРОМЫШЛЕННАЯ ЭКОЛОГИЯ И БЕЗОПАСНОСТЬ
ЖИЗНЕДЕЯТЕЛЬНОСТИ»
ОЦЕНКА ЭФФЕКТИВНОСТИ ОЧИCТКИ ВОЗДУХА В ЦИКЛОНЕ
Методические указания к лабораторной работе по дисциплине «Промышленная экология»
Волгоград 2015
Рецензент: | Канд. техн. наук, доцент Козловцев В. А. |
Печатается по решению редакционно-издательского совета
Волгоградского государственного технического университета
Колотова О.В.
Оценка эффективности очистки воздуха в циклоне: методические указания к лабораторной работе по дисциплине «Промышленная экология»/ О.В. Колотова, И.В. Соколова, А.Б. Голованчиков; - Волгоград, ИУНЛ ВолгГТУ, 2015. - 24 с.
Методические указания содержат теоретические основы сухих методов очистки и их применения в процессах очистки воздуха от взвешенных частиц. Приведены методики эксперимента и обработки полученных результатов, а также контрольные вопросы. Предназначено для бакалавров направления 241000.62 — Энерго- и ресурсосберегающие процессы в химической технологии, нефтехимии и биотехнологии, магистров направления 241000.68 – Энерго- и ресурсосберегающие процессы в химической технологии, нефтехимии и биотехнологии
|
|
Ил. . Табл. . Библиогр.: назв.
© Волгоградский государственный технический университет, 2015
___________________________________________
Составители:
Ольга Владимировна Колотова
Ирина Владимировна Соколова
Александр Борисович Голованчиков
Темплан 2015г., поз. №___.
Подписано в печать ___________. Формат 60x84 1/16. Бумага офсетная.
Гарнитура Times. Печать офсетная. Усл. печ. л. 1,5.
Тираж __экз. Заказ ...
Волгоградский государственный технический университет.
400131, Волгоград, просп. им. В. И. Ленина, 28, корп. 1.
Отпечатано в типографии ИУНЛ ВолгГТУ.
400131, Волгоград, просп. им. В. И. Ленина, 28, корп. 7.
ВВЕДЕНИЕ
Сухие методы очистки воздуха от взвешенных частиц широко применяются в экологии на начальной стадии очистки загрязненного воздуха. Большое разнообразие конструкций различных видов аппаратов гравитационного, инерционного и центробежного типов позволяет производить подбор их в зависимости от размера очищаемых частиц, производительности и гидравлического сопротивления. Правильное обоснование выбора необходимого типа аппарата дает повышение эффективности очистки воздуха, что уменьшает количество аппаратов в многоступенчатой системе очистки воздуха до нормативных значений. В методических указаниях приведена методика проведения экспериментального исследования процесса очистки воздуха в циклоне от взвешенных частиц, обработка результатов которого позволяет сделать оценку эффективности очистки воздуха в циклоне при разных расходах подаваемого воздуха.
|
|
ЦЕЛЬ РАБОТЫ
1.Изучить методы сухой очистки воздуха от твердых взвешенных частиц.
2. Изучить принцип действия и устройство циклона.
3. Экспериментально определить эффективность пылеулавливания лабораторной установкой при различных значениях производительности циклона.
ТЕОРЕТИЧЕСКАЯ ЧАСТЬ
В настоящее время загрязнение атмосферы – одна из наиболее острых проблем современной экологической ситуации планеты Земля.
Загрязнение атмосферы имеет природное и антропогенное происхождение.
Все многообразие природных и антропогенных загрязнений атмосферного воздуха можно подразделить на:
- материальные (вещества различных агрегатных состояний - газы, жидкости (туманы) и твердые частицы) и
- энергетические (звуковые и вибрационные загрязнения, излучения тепловой и электромагнитной энергии, различные виды радиации).
|
|
Большую опасность представляет загазовывание атмосферного воздуха, связанное с выбросами газообразных загрязнителей и оказывающее негативное влияние на окружающую природную среду в целом (состояние атмосферы, гидросферных объектов, почвенных угодий, флоры и фауны) и здоровье человека.
Выделяют пять наиболее распространенных групп газообразных загрязняющих веществ (ЗВ) («многотоннажные» - до 10 млн. т. в год):
1. Твердые частицы (пыль, дым, сажа);
2. Оксиды углерода (СО, СО2);
3. Оксиды серы (SО2, SО3,) и Н2S;
4. Оксиды азота (NO и NO2);
5. Углеводороды (СxНу).
На долю вышеназванных ЗВ приходится 90-98 % всех атмосферных выбросов в городах и промышленных центрах.
Запыление связано с поступлением в атмосферу мелкодисперсных частиц твердых веществ. Оно может быть вызвано природными и антропогенными источниками (извержения вулканов, пылевые бури, попадание пылевых частиц, образующихся при производстве цемента, муки, кормовых дрожжей и др.). Данный вид загрязнения приводит к снижению уровня поступления солнечной радиации, тепловой энергии и способствует появлению у людей заболеваний верхних дыхательных путей.
Уровень загрязнения атмосферы промышленными и транспортными источниками определяется следующими основными факторами:
|
|
1) Объемом выброса (количество ЗВ в единицу времени);
2) Направлением и скоростью ветра (чем больше скорость ветра, тем быстрее происходит рассеивание и тем меньше концентрация ЗВ вблизи источника);
3) Градиентом температуры - это разность температуры на 1 единицу высоты (чем выше градиент, тем больше скорость восходящих потоков воздуха, тем больше угол раскрытия дымового факела и эффективнее перемешивание ЗВ с воздухом);
4) Влажностью воздуха (существует прямая зависимость между концентрацией дыма и относительной влажностью: чем больше влажность, тем больше концентрация дыма в нижних слоях атмосферы, т.к. частицы загрязнения - это ядра конденсации для водяных паров);
5) Расстоянием от источника выброса;
6) Высотой выброса (чем выше труба, тем меньше концентрация ЗВ в приземных слоях воздуха).
Практически все виды деятельности человека являются источниками загрязнения атмосферы. Так или иначе, все промышленные и сельскохозяйственные предприятия загрязняют атмосферу. Установлено, что наибольший вклад в загрязнение атмосферы вносят автотранспорт и топливная энергетика, строительная индустрия и химическая промышленность. Например, в автомобиле источник выделения ЗВ - двигатель, а источник выброса ЗВ - выхлопная труба.
Рисунок 1- Классификация источников загрязнения атмосферы.
Более 200 городов России с населением 65 млн. человек испытывают постоянные воздействия вредных веществ в концентрациях, превышающих ПДК в воздухе.
Основное направление охраны окружающей среды сегодня, в том числе и атмосферного воздуха, - это разработка и создание малоотходных и безотходных технологических процессов. В настоящее время наиболее распространенным решением указанной проблемы является разработка эффективных систем очистки, улавливания и переработки всех видов примесей: газообразных, жидких и твердых.
Чтобы правильно выбрать очистное устройство и рассчитать всю систему очистки необходимо знать основные характеристики, такие, как: эффективность, гидравлическое сопротивление и производительность.
Эффективность очистки η определяется по формуле:
, (1)
где Сн , Ск – массовые концентрации примеси в газе до и после аппарата.
Если последовательно соединено несколько аппаратов, то общая эффективность очистки будет
, (2)
где η1, η2, …ηn – эффективность очистки 1-го, 2-го и n-го аппаратов.
Гидравлическое сопротивление Δp – это разность давлений на входе ρвх и ρвых из аппарата. Величина Δp находится экспериментально или рассчитывается по формуле:
, (3)
где ρ и V – плотность и скорость воздуха в расчетном сечении аппарата;
ε – коэффициент гидравлического сопротивления.
Величина гидравлического сопротивления аппаратов имеет большое значение для расчета этого параметра всей системы. Производительность систем очистки показывает, какое количество воздуха проходит через нее в единицу времени (м3/ч).
Наиболее полная классификация очистных аппаратов основана на использовании следующих способов обеспыливания:
— физические способы включают: механический (аэродинамический, гидродинамический, фильтрационный), электрический, магнитный, акустический, оптический, ионизирующий, термический;
— химический способ;
— физико-химический способ;
— биохимический способ.
Каждый из указанных способов имеет определенную область применения и широту использования. Для обезвреживания аэрозолей (пылей и туманов) используют физический способ - сухие, мокрые и электрические методы. В основе сухих методов лежат гравита
ционные, инерционные, центробежные механизмы осаждения или фильтрационные механизмы. При использовании мокрых методов очистка газовых выбросов осуществляется путем тесного взаимодействия между жидкостью и запыленным газом на поверхности газовых пузырей, капель или жидкой пленки. Электрическая очистка газов основана на ионизации молекул газа электрическим разрядом и электризации взвешенных в газе частиц.
При обработке выбросов, содержащих твердые аэрозольные загрязнители, низких величин проскока (1...2% и менее) можно достичь, как правило, только двухступенчатой очисткой. Для предварительной очистки могут быть применены жалюзийные решетки и циклонные аппараты (иногда для небольших выбросов - пылеосадительные камеры), а для окончательной – пористые фильтры, электрофильтры или мокрые пылеосадители.
Рассмотрим аппараты для сухой очистки от твердых взвешенных частиц более подробно.
Основные типы устройств для сухой механической очистки
К сухим пылеуловителям можно отнести следующие типы газоочистных аппаратов:
А) механические: | Б) фильтрующие: |
осадительные камеры | волокнистые фильтры |
инерционные аппараты | тканевые фильтры |
центробежные аппараты | зернистые фильтры |
При гравитационном осаждении взвешенных частиц из газовой фазы используется способность частиц оседать под действием силы тяжести в ламинарном потоке газа.
При инерционном осаждении наряду с действием сил тяжести используются также силы инерции. Они возникают при резком изменении скорости или направления движения газового потока. Таким образом, инерционное пылеулавливание основано на использовании комбинации сил, действующих на частицу в потоке аэрозоля. Примерами устройств для сухой механической очистки газов с использованием гравитационных и инерционных сил являются пылеосадительные камеры, жалюзийные пылеуловители, циклоны (одинарные и батарейные) и другие типы аппаратов.
Устройства всех этих типов характеризуются простотой конструкции и принципа работы. Они относительно дешевы по сравнению с другими типами осадителей. В общем случае они не имеют движущихся частей, а для обеспечения рабочих условий можно использовать любой материал. Затраты энергии на работу также относительно малы, что обусловлено малым перепадом давления при течении газа через устройство. Осадители рассматриваемого типа используются для первичного удаления грубых частиц газового потока. В большинстве случаев для защиты воздуха от загрязнения требуется улавливание гораздо более мелких частиц (размером около 1 мкм), поэтому обычно необходимо применять осадители других типов. Однако механические осадители можно использовать как предварительные, сочетая их с устройствами других типов, чтобы уменьшить нагрузку на последние. Это особенно необходимо при сильно запыленных газовых потоках. Механические осадители могут работать долгое время без обслуживания с малыми энергетическими затратами.
Описанные аппараты применяются как самостоятельные (в одноступенчатых пылеулавливающих установках) при достаточно высокой начальной запыленности газа С0 = 2-3 г/м3 и менее.
При запыленности более 3 г/м3 применение аппаратов сухой механической очистки (СМО) оказывается неэффективным, так как на выходе сохраняется достаточно высокая запыленность газа, тогда данные аппараты используют как первую ступень очистки для удаления наиболее крупных частиц. Оборудование для сухой механической очистки нельзя применять в случае очистки увлажненных газов из-за образования трудноудаляемых отложений.
Подробнее остановимся на группе аппаратов для сухой механической очистки.
Пылеосадительные камеры. Это простейшие и наименее эффективные устройства, применяемые в пылеочистке. Используются только для предварительной ступени очистки, если размеры частиц составляют не менее 50 мкм. Эффективны в случае горизонтального движения потока частиц. Пылеосадительная камера (рис.2) – это длинный бункер с установленными на входе диффузором и газораспределительной решеткой. Технические характеристики пылеосадительных камер: скорость газа
ωг =0,2 -1,5 м/с; потери давления ΔР = 50-150 Па; диаметр dч = 50 мкм; эффективность улавливания η = 40-50 %.
Основные достоинства осадительных камер заключаются в простоте конструкции, низкой стоимости, в небольших расходах энергии и в возможности улавливания абразивной пыли. Кроме того, работа камер не подвержена влиянию температуры и обеспечивает улавливание пыли в сухом виде. При этом необходимы громоздкие аппараты и большие производственные площади, что является одним из главных недостатков.
Для достижения приемлемой эффективности очистки газов данными аппаратами необходимо, чтобы частицы находились в пылеосадительных аппаратах возможно более продолжительное время, а скорость движения пылевого потока была незначительной. Кроме того, необходимо обращать внимание на турбулентность газового потока, которая снижает эффективность осаждения частиц с малым размером в пылеосадительных камерах. При проектировании пылеосадительных камер обязательно принимают в расчет равномерное распределение газового потока. Для этого устанавливают диффузоры или распределительные решетки. Степень очистки частиц с размером менее 5 мкм в камерах с большим размером близка к нулю. Поэтому данное оборудование относится к категории экстенсивного оборудования, рабочие объемы таких аппаратов весьма значительны, что требует больших производственных площадей. Однако пылеосадительные камеры обладают таким преимуществом, как незначительное гидравлическое сопротивление (50-300 Па). В настоящее время данный вид аппаратов применяют только на стадии предварительной очистки при высокой начальной концентрации пыли.
Инерционные пылеуловители. Принцип действия аппаратов данного типа основан на резком изменении направления движения газового потока. Пылевые частицы под воздействием инерционной силы будут стремиться двигаться в прежнем направлении и после поворота потока газов выпадают в бункер (рис. 3, а).
На принципе резкого изменения направления газового потока работает целый ряд пылеуловителей, некоторые из которых показаны на рисунке 3.
а б в г
Рисунок 3 - Инерционные пылеуловители:
а — камера с перегородкой; б — камера с плавным поворотом газового потока; в — камера с расширяющимся конусом; г — камера с заглубленным бункером
Камера с перегородкой (рис. 3, а) по эффективности ненамного отличается от обычной осадительной горизонтальной камеры, но имеет более высокое гидравлическое сопротивление. Плавный поворот в камере (рис. 3, б) позволяет снизить гидравлическое сопротивление. На рисунке 3, в представлен осадитель, в котором запыленный газовый поток направляется сначала вниз по расширяющемуся конусу, а затем поворачивает на 180° и выводится сверху. В результате этого частицы пыли подвергаются дополнительному усилию, направляющему их в сторону бункера камеры. Это усилие обеспечивает дополнительное ускорение. Расширяющийся конус позволяет постепенно снизить скорость газового потока и препятствует вторичному уносу частиц.
В подобных пылеуловителях скорость газов в свободном сечении камеры составляет примерно 1,0 м/с, а во входной цилиндрической трубе — около 10 м/с. Для частиц пыли размером 25-30 мкм достигается степень улавливания 65-80%. Такие камеры применяют на заводах черной и цветной металлургии. Гидравлическое сопротивление их равно 150-390 Па.
Жалюзийные аппараты.Разновидностью инерционных пылеуловителей являются жалюзийные пылеулавливающие аппараты. Особенность их конструкции - жалюзийная решетка, состоящая из рядов пластин или колец. Загрязненный поток делает резкие повороты, проходя через решетку. Под действием сил инерции в камере происходит отделение крупных частиц из газового потока, тому же способствуют их удары о наклонные плоскости решетки, от которых они отражаются и отскакивают в сторону от щелей между лопастями жалюзи (рис. 4). В результате газы делятся на два потока. Пыль в основном содержится в потоке, который отсасывают и направляют в циклон, где его очищают от пыли и вновь сливают с основной частью потока, прошедшего через решетку. Эти аппараты широко применяются для предварительной очистки газов перед подачей в циклоны или рукавные фильтры.
В жалюзийном аппарате около 90 % газов частично очищается от пыли при прохождении через жалюзи, а остальной газовый поток с уловленной пылью отводится на очистку в циклон.
При повышении скорости подачи газов к пластинам решетки степень улавливания пыли в жалюзийном пылеуловителе сначала быстро растет, а начиная со скорости около 10 м/с, этот рост замедляется. Обычно скорость газов в жалюзийном пылеуловителе составляет 12-15 м/с.
На степень очистки влияет также скорость движения газов, отсасываемых в циклон. Для того, чтобы в циклон было отведено возможно больше пыли, эта скорость должна быть не меньше скорости газов при подходе к решетке. Гидравлическое сопротивление решетки составляет 100-500 Па. Обычно жалюзийные пылеуловители применяют для улавливания пыли с размером частиц >20 мкм. Недостаток применения данных аппаратов - износ пластин при высокой концентрации пыли. Эффективность улавливания частиц зависит от эффективности самой решетки и эффективности циклона, а также от доли отсасываемого из аппарата газа.
Недостатками жалюзийного пылеуловителя являются: износ пластин решетки при высокой концентрации особенно крупной пыли и возможность образования отложений при охлаждении газов до точки росы.
Циклонные аппараты. Наибольшее распространение в системах пылеочистки получили циклоны. Они широко применяются для очистки от пыли вентиляционных и технологических выбросов во всех отраслях народного хозяйства. На практике система улавливания частиц создается путем придания запыленному потоку закрученного или вращательного движения, ограниченного цилиндрическими стенками. Частицы осаждаются при отбрасывании на стенки. Такое устройство называется циклоном.
В рассматриваемых аппаратах частицы пыли движутся вместе с вращающимся газовым потоком и под воздействием центробежных сил оседают на стенках. Отделение частиц от газа происходит за счет поворота газового потока в бункере на 1800: газ отражается от дна и двигается вверх, а потерявшие начальную скорость частицы в широком бункере оседают вниз под действием силы тяжести.
Возникающая в циклоне центробежная сила обратно пропорциональна радиусу циклона, поэтому эффективность обеспыливания возрастает с уменьшением радиуса циклона. В современных установках эти силы в 5 - 2500 раз превышают действующую на пылинку силу тяжести, чем и определяется большая эффективность циклонов по сравнению с осадительными камерами.
Вместе с восходящим газовым потоком, как видно на рис. 5, возможен унос частиц пыли из бункера, что приведет к понижению эффективности очистки. Поэтому нецелесообразно повышать скорость > 20-25 м/с во входном патрубке (обычно она ≈15 м/с). Скорость газа в полном сечении должна составлять при этом 2,2-5,0 м/с (в зависимости от типа циклона).
Циклонные пылеуловители имеют следующие преимущества:
1) отсутствие движущихся частей в аппарате;
2) надежное функционирование при температурах газов вплоть до 500 °С без каких-либо конструктивных изменений (в случае применения более высоких температур аппараты можно изготовлять из специальных материалов);
3) возможность улавливания абразивных материалов при защите внутренних поверхностей циклонов специальными покрытиями;
4) пыль улавливается в сухом виде;
5) гидравлическое сопротивление аппаратов почти постоянно;
6) аппараты успешно работают при высоких давлениях газов;
7) пылеуловители весьма просты в изготовлении;
8) рост запыленности газов не приводит к снижению фракционной эффективности очистки.
Правильно спроектированные циклоны могут эксплуатироваться надежно в течение многих лет.
В промышленности используется около 20 типов циклонов. Наиболее перспективными являются разработки НИИОГАЗ - цилиндрические (например, ЦН-1, ЦН-15) и конические (напримерСДК-ЦН-33, СК-ЦН-34). Отличительная черта циклонов типа ЦН – наклонный входной патрубок. Цифра в маркировке показывает, на сколько градусов к горизонту наклонен патрубок. Цилиндрические циклоны относят к высокопроизводительным аппаратам, конические – к высокоэффективным.
Эффективность очистки в циклоне определяется крупностью улавливаемых частиц, т. е. дисперсным составом пыли, и их плотностью, а также вязкостью очищаемого газа; кроме того, она зависит от диаметра циклона и скорости газа в нем.
Эффективность циклонов резко снижается при наличии подсосов, в частности, через бункер.
Движение газов в циклоне носит весьма сложный характер и, несмотря на большое число теоретических работ, изучено еще недостаточно.
Средняя эффективность обеспыливания газа в циклонах составляет около 98 % для частиц пыли размером 30-40 мкм, до 80 % для частиц размером 10-20 мкм, 60 % - для частиц размером 4-5 мкм.
Групповые и батарейные циклоны. В зависимости от объема очищаемого газа циклоны устанавливают либо по одному (одиночные циклоны), либо объединяют в группы по 2, 4, 6, 8 (реже по 14) элементов (групповые циклоны).
Особый вид циклонов — батарейные, представляющие собой набор смонтированных в общем корпусе циклонных элементов небольшого диаметра (примерно до 250 мм) при этом в корпусе размещается общий для всех элементов распределительный коллектор запыленного газа, а также и общий собирающий коллектор очищенного газа.
При больших расходах очищаемых газов применяют групповую компоновку аппаратов. Это позволяет использовать аппараты с малыми диаметрами, что положительно сказывается на эффективности очистки. Схема групповых циклонов дана на рис 6, а. Запыленный газ входит через общий коллектор, а затем распределяется между циклонными элементами.
![]() |
![]() б) |
Рисунок 6 - Групповой (а) и батарейный (б) циклоны:
а): 1 — входной патрубок; 2 — камера обеспыленных газов; 3 — кольцевой диффузор; 4 — циклонный элемент; 5 — бункер; 6- пылевой затвор;
б): 1— корпус; 2 — распределительная камера; 3 — решетки; 4 — циклонный элемент.
Схема батарейного циклона приведена на рис. 6, б. Снижение диаметра циклонного элемента преследует цель увеличения эффективности очистки. Элементы батарейных циклонов имеют диаметр 100, 150 или 250 мм. Оптимальная скорость газов в элементе лежит в пределах от 3,5 до 4,75 м/с, а для прямоточных циклонных элементов от 11 до 13 м/с.
Важным фактором, характеризующим центробежные аппараты, является отношение ускорения центробежной силы к ускорению силы тяжести, численно равное отношению величины центробежной силы к силе веса данного тела. Это отношение, которое является безразмерной величиной, называется фактором разделения Кр:
(4)
Фактор разделения является критерием, характерным для поля центробежных сил. Определяющим линейным размером фактора разделения является радиус вращения r.
Осаждение пыли под действием сил тяжести происходит по тем же законам, что и осаждение под действием центробежных сил с тем отличием, что скорость осаждения во втором случае будет намного больше, чем в отстойных аппаратах. Увеличение скорости осаждения определяется числовым значением фактора разделения Kp.
Степень очистки газа в циклонах тем больше, чем больше фактор разделения Кр. Этот фактор можно увеличить либо путем уменьшения радиуса вращения газового потока, либо увеличением его скорости, что сопряжено со значительным возрастанием гидравлического сопротивления и увеличением турбулентности газового потока (которая ухудшает процесс осаждения и способствует перемешиванию очищенного газа с запыленным).
Ещё более эффективными по степени улавливания мелких частиц (по сравнению с циклонами) являются так называемые центриклоны. Такое название они получили вследствие сочетания принципов работ циклона (неподвижный корпус с вращающимся газовым потоком) и центрифуги (вращающийся вместе с газовым потоком внутренний патрубок для выброса очищенного газа). Большим преимуществом центриклона (по сравнению с циклоном) является снижение гидравлического сопротивления за счет уменьшения силы трения газового потока о внутренний патрубок. Эти преимущества центриклона по сравнению с циклоном (увеличение степени очистки и снижение гидравлического сопротивления), достигаются за счет усложнения конструкции - установки подшипника под внутренний вращающийся патрубок. Однако недостатком центриклонов является необходимость частой замены подшипников, т.к. вследствие выхода их из строя не достигается заданная степень очистки газового потока.
ЭКСПЕРИМЕНТАЛЬНАЯ ЧАСТЬ
Дата добавления: 2018-04-15; просмотров: 1199; Мы поможем в написании вашей работы! |
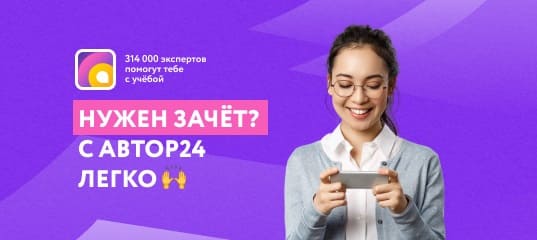
Мы поможем в написании ваших работ!