Плоскопараллельные концевые меры длины
Плоскопараллельные концевые меры длины (сокращенно ПКМД) выполняют в виде прямоугольного параллелепипеда с двумя плоскими взаимно параллельными измерительными поверхностями, с размерами поперечного сечения a и b.
За длину концевой меры длины в любой точке принимают длину перпендикуляра АВ (рис. 1, б), опущенного из данной точки измерительной поверхности концевой меры на противоположную измерительную поверхность. Обе измерительные поверхности отличаются от других поверхностей ПКМД малой шероховатостью (среднее арифметическое отклонение профиля Ra ≤016 мкм).
ПКМД поставляют в наборах определенных номеров и россыпью по заказам. Наиболее распространенными являются наборы номеров 1, 6 и 16.
В зависимости от точности изготовления ПКМД, т.е. от отклонения длины концевой меры от номинальной и от отклонения от плоскопараллельности измерительных поверхностей, их относятк классам точности: 00; 01; 0; 1; 2 и 3 (меры из стали) и 00; 0; 1; 2 и 3 (меры из твердого сплава). После ремонта ПКМД могут быть отнесены
к классам точности 4 и 5.
Отклонение длины ПКМД от номинальной - наибольшая по абсолютному значению разность между длиной концевой меры в любой точке и номинальной длиной ПКМД.
Отклонение от плоскопараллельности измерительных поверхностей концевой меры - разность между наибольшей и наименьшей длинами концевой меры.
Трудность изготовления ПКМД и быстрый износ определилиособую систему их применения с учетом погрешностиПКМД по аттестату, выданному поверочными органами. В зависимости от точности аттестации в органах метрологической службы ПКМД подразделяют на пять разрядов: первый, второй, третий, четвертый и пятый. Высшим по точности является первый разряд. Особым свойством ПКМД является их притираемоеть - свойство измерительных поверхностей концевых мер, обеспечивающее прочное сцепление между собой, а также с плоской металлической, стеклянной или кварцевой пластинами при прикладывании или надвигании одной концевой меры на другую или концевой меры на пластину. Притираемость ПКМД обусловлена силами сцепления их измерительных поверхностей.
|
|
Она характеризуется нормированными силами сдвига. При работе с ПКМД в общем случае, если в наборе нет меры требуемого номинального размера, составляют блок из возможно меньшего числа мер, для чего сначала рассчитывают и подбирают концевые меры длины.
Плоскопараллельные концевые меры длины предназначены для хранения и воспроизведения единицы длины в соответствии с государственной поверочной схемой, для поверки и градуировки мер и измерительных приборов, для установки приборов на нулевые деления при измерениях методом сравнения с мерой, для непосредственных измерений наиболее точных размеров изделий, для разметки изделий; их используют также при лекальных, слесарных, сборочных и регулировочных работах.
|
|
ПКМД, служащие для поверки и градуировки средств
измерения, называют образцовыми. По образцовым ПКМД 1-го разряда поверяют образцовые ПКМД 2-го разряда, затем по ПКМД 2-го разряда поверяют образцовые ПКМД 3-го разряда, по ПКМД 3-го разряда поверяют меры 4-го разряда и по ПКМД 4-го разряда поверяют меры 5-го разряда.
Щупы – пластины (с параллельными измерительными плоскостями) применяют для измерения зазоров между двумя плоскостями. Щупы комплектуют в наборы классов точности 1 и 2.
Штриховые меры длины
Штриховые меры длины - меры, размер которых определяет расстояние между осями двух штрихов или нескольких, нанесенных перпендикулярно к продольной оси меры. К штриховым мерам длины кроме брусковых мер длины относят также металлические измерительные линейки и ленточные рулетки.
Брусковые штриховые меры длины представляют собой бруски с нанесенными на них штрихами или шкалами (рис. 3, а). Штриховые меры длины подразделяют на однозначные и многозначные. Однозначные меры имеют только два штриха, расстояние между которыми определяет одно значение длины меры. Такие штриховые меры длины применяют в основном в качестве эталонов (например, вторичный эталон метра № 28). Нашли применение многозначные штриховые меры длины, имеющие ряд штрихов (шкалу), нанесенных через интервалы 1 дм, 1 см, 1 мм, 0,1 или 0,2 мм (стеклянные шкалы имеют цену деления 0,1 и 0,01 мм). Многозначные штриховые меры применяют для измерения длины, а также в качестве шкал станков и приборов.
|
|
Образцовые штриховые меры длины служат для передачи единицы длины от эталона к изделию.
По форме сечения брусковые меры делят на четыре типа: I - Н-образной формы (тип IA) или по форме прямоугольного желоба (тип IБ) со шкалой, нанесенной на поверхность, совпадающую с нейтральной плоскостью меры; II — прямоугольной формы на номинальный размер 60 - 1000 мм; III - полусферической, трапецеидальной и прямоугольной формы; у штриховых мер типов II и III штрихи шкалы наносят на верхней поверхности меры; IV -трапецеидальной формы на номинальный размер шкалы 1000 мм со штрихами шкалы, нанесенными на боковой поверхности меры.
Штриховые меры длины изготовляют 0; 1; 2; 3; 4 и 5-го классов точности из инвара (36Н), инварстабиля(58Н), стали марки ЭИ792 и оптического стекла Ф8 и Ф18. На штрихах, соответствующих сантиметровым интервалам, указаны цифры. Начальный штрих шкалы должен находиться на расстоянии не менее 10 мм от торца меры. На рабочей поверхности мер классов точности 0; 1 и 2 наносят две продольные осевые линии с расстоянием между ними 0,2 - 0,3 мм.
|
|
Штриховые меры типа IV о интервалом 0,1 и 0,2 мм комплектуют двумя лупами о увеличением не менее 7*.
На штриховую меру наносят товарный знак, номинальную длину меры, материал, из которого изготовленамера, значение наименьшего деления шкалы, класс точности меры и год выпуска. На штриховых мерах классовточности 0; 1 и 2 на боковой поверхности обозначают точки
опоры.
Измерительные металлические линейки (рис. 3, б и в) являются простейшими штриховыми мерами, широко применяемыми для грубых измерений длин изделий (табл. 7).
Просвет между поверочной плитой и плоскостью линейки, положенной на плиту (шкалой вверх), не должен превышать 0,5 мм для линеек с длиной шкалы до 500 мм и 0,7 мм - для линеек с длиной шкалы 1000 мм.
Измерительные металлические рулетки (ГОСТ 7502-80) представляют собой меры для измерения длины методом непосредственного сравнения определенных расстояний и длин со шкалой рулетки, т. е. ленты с делениями, сворачиваемой в рулон. Различают рулетки в открытом (О) и закрытом (З) корпусах; с плоскими (П) и выпуклыми (В) лентами; с кольцом (К) на конце; см держателем (Д) на конце для закрепления на измеряемом изделии; с грузом (Г) на конце рулетки; с началом шкалы удаленном от торца ленты (А), и с началом шкалы, совпадающим с торцом ленты (Б); с лентами, изготовленными из коррозионно-стойкой (Н) и углеродистой (У) сталей; Стравленными или печатными штрихами шкал; с интервалом шкал в миллиметрах (1) и сантиметрах (10).
Угловые меры длины
Угловые призматические меры являются наиболее точным средством измерения углов в машиностроении. Они предназначены для передачи размера единицы плоского угла от эталонов к образцовым и рабочим угловым мерам и приборам, для поверки и градуировки мер приборов и для измерения углов изделий.
Меры угловые бывают однозначные и многозначные. К однозначным угловым мерам относятся угловые плитки, к многозначным — многогранные призмы (рис.), лимбы и круговые шкалы. Угловые плитки представляют собой стальные плитки толщиной 5 мм с одним или четырьмя двугранными углами, образованными боковыми поверхностями плитки. Плитки с рабочими углами от 1' до 100° комплектуются в наборы из 93, 33 и менее мер с таким расчётом, чтобы из 3—5 мер можно было составлять блоки с интервалами через 1°, 1' или 15’’. Для соединения угловых плиток в блоки служат специальные державки. Угловые плитки изготовляют 3 классов точности: 0; 1; 2 с погрешностями до 3’’ (для класса 0) и до 30’’ (для 2-го класса).
Многогранные призмы изготовляют из стекла, плавленого кварца и стали с числом граней обычно до 36 (иногда до 72). Допускаемые отклонения рабочих углов составляют от ± 5 для класса 0 до ±30 для 2-го класса точности.
Лимбы обычно являются частью различных угломерных приборовгониометров, теодолитов, квадрантов, делительных головок и др. Изготовляют лимбы различной точности с ценой деления от 1 до 10 и более и погрешностями от 1’’ до 10’’.
Рис.10 Угловые призматические меры
Штангенприборы
Штангенприборы являются наиболее распространенными видами измерительного инструмента. Штангенприборы – показывающие измерительные приборы, в которых положение одной или нескольких перемещающихся рамок отсчитывается по штриховой шкале с указателем или нониусом.
По способу снятия показаний штангенприборы делятся на:
- нониусные;
- циферблатные (оснащены циферблатом для удобства и быстроты снятия показаний);
- цифровые (с цифровой индикацией для безошибочного считывания).
Основные детали штангенинструмента с нониусом: штанга, на которой нанесена основная шкала с интервалом 1 мм, и нониус для отсчета долей основного деления с ценой деления 0,1; 0,05; 0,02 мм. Следует указать, что выпуск штангенинструмента с нониусом 0,02 мм прекращен (кроме штангензубомера), так как практически не дает повышения точности по сравнению с нониусом 0,05 мм, поскольку погрешность измерения намного превышает цену деления нониуса.
Нониус был изобретен еще в средние века португальским монахом Педро Нониусом для отсчета долей делений по шкалам навигационных приборов того времени.
Принцип действия нониуса состоит в совмещении соответствующих штрихов двух линейных шкал, интервалы деления которых отличаются на определенную величину. Конструкция нониуса использует то обстоятельство, что невооруженный человеческий глаз, не способный количественно оценить малые значения несовмещения штрихов, в то же время способен фиксировать весьма малые смещения двух штрихов от их симметричного расположения (наименьшее видимое смещение штрихов составляет около 0,012 мм). При использовании нониуса оператор определяет на основной шкале и нониусе пару штрихов, не имеющих взаимного смещения, и по соответствующему штриху нониуса снимает отсчет.
Расчет основных параметров нониуса производится следующим образом. Задаются интервалом деления основной шкалы b(у подавляющего числа штангенприборов он равен 1 мм), величиной отсчета по нониусу с, модулем шкалы нониуса у. Модуль нониуса показывает, через какое число делений основной шкалы будут располагаться штрихи нониуса, смещенные на величину отсчета. Тогда:
• число делений шкалы нониуса составит
n = b/ с;
• интервал деления шкалы нониуса
bl = -by - с;
• полная длина шкалы нониуса
l = nb = n(bу - с) = b(ny- 1).
На рисунке показаны два нониуса с величиной отсчета 0,1 мм, выполненные с модулем 1 и 2. При применении модуля 2 интервал деления нониуса увеличивается почти вдвое, но величины смещения соответствующих штрихов остаются неизменными. В существующих штангенприборах применяются значения модуля 1, 2 и, значительно реже, 5, величины отсчета по нониусу 0,1, 0,05 и 0,02 мм. Последнее значение величины отсчета метрологически не оправдано, поскольку погрешность измерения намного превышает эту величину.
Целое число миллиметров у штангенприборов отсчитывается по шкале штанги слева направо нулевым штрихом нониуса. При нулевом показании штрих нониуса находится от ближайшего справа штриха штанги на расстоянии, равном величине отсчета (0,1 мм), умноженной на порядковый номер нониуса, не считая нулевого, т.е. при перемещении рамки до совпадения какого-либо штриха нониуса со штрихом штанги размер между губками штангенприбора (дробная величина) будет равен величине отсчета (0,1 мм), умноженной на порядковый номер этого штриха нониуса (рис. 2.6).
В группу штангенприборов входят штангенциркули, штангенрейсмусы, штангенглубиномеры и штангензубомеры.
Наиболее распространенными являются штангенциркули, предназначенные для измерения наружных и внутренних размеров и разметки. Штангенциркуль как универсальный измерительный прибор широко применяется при станочных (токарных, фрезерных и т.д.), слесарных, инструментальных, лекальных, разметочных работах и в отделах технического контроля. Конструктивно штангенциркули различаются по величине, форме губок и подвижной рамки, точности. Выпускаемые в настоящее время штангенциркули имеют пределы измерения от 125 до 4000 мм.
В общем случае штангенциркуль состоит из штанги 1 с неподвижной измерительной губкой и рамки 3, перемещающейся по штанге с другой измерительной губкой и нониусом 6.
По форме измерительных губок различают следующие модели штангенциркулей:
• ШЦ-I - с двусторонним расположением губок для измерения наружных и внутренних размеров и с линейкой для измерения глубин; ф
• ШЦ-II - с двусторонним расположением губок для измерения наружных и внутренних размеров для разметки;
• ШЦ-III - с односторонними губками.
Губки для измерения наружных размеров у всех штангенциркулей имеют внутренние измерительные поверхности, доведенные до высокого класса шероховатости и плоскостности. Губки для измерений внутренних размеров имеют два варианта исполнения: в модели ШЦ-I губки 2 имеют ножевидную форму и при их использовании сразу получается измеряемый размер; в моделях ШЦ-П и ШЦ-Ш губки 2, выполненные ступенчатыми, имеют определенный суммарный размер, который следует прибавить к отсчитываемому размеру. Для проведения разметки в штангенциркуле ШЦ-П концы измерительных губок остро заточены, а штангенциркули модели ШЦ-Ш могут снабжаться съемными разметочными устройствами.
Во всех моделях штангенциркулей все подвижные рамки 3 могут быть закреплены в любом положении на штанге зажимным винтом 4. Большинство штангенциркулей оснащаются дополнительной подвижной рамкой 5 (хомутиком) и соединенным с ней микрометрическим винтом, которые служат для точной установки необходимого размера. Для обеспечения поджима подвижной рамки к базовой нижней поверхности штанги в специальный паз рамки устанавливается стальная пружина или слегка изогнутый бронзовый размерный вкладыш. Существуют конструкции, в которых вкладыши выполняются из фторопласта. В настоящее время все модели штангенциркулей выпускаются полностью закаленными (как измерительные губки, так и штанга) и хромированными. Для современной конструкции штангенциркуля характерно выполнение рамки 3 открытой формы, не закрывающей каких-либо участков шкалы. Особенностью современных конструкций является также выполнение утопленной шкалы, что предохраняет ее от истирания подвижной рамкой.
Кроме штангенциркулей с отсчетом по нониусу ряд зарубежных фирм, например «Теза» (Швейцария), выпускают штангенциркули со стрелочным отсчетным устройством, имеющим величину отсчета 0,02 мм. Для этой цели вдоль основной шкалы в специальном пазу штанги установлена зубчатая рейка соединенная с зубчатым трибом2 индикаторного устройства, расположенного вместе с круговой шкалой 3 в подвижной рамке 5. На оси триба установлена отсчетная стрелка 4. Шкала индикаторного устройства выполняется поворотной и оснащается зажимным механизмом.
Штангенциркули такого типа позволяют упростить и ускорить процесс снятия показаний при измерении.
Следует отметить, что, кроме моделей основного исполнения, отечественная промышленность использует ряд моделей штангенциркулей, обладающих дополнительными возможностями.
Микрометрические приборы
Достаточное распространение в цеховых условиях, но более точными по сравнению со штанген приборами, являются микрометрические приборы. К которым относятся микрометры и микрометрические нутромеры. Принцип действия микрометрических приборов основан на преобразовании вращательного движения микрометрического винта, установленного в неподвижную гайку, в его поступательное перемещение вдоль оси. Большинство микрометрических приборов имеют винт с шагом 0,5 мм, поэтому поворот его на 360 вызывает его перемещение на 0,5 мм.
На рис. 12 а показано устройство головки микрометрических приборов.
Рис. 12
Микрометрический винт 4 в сборе с барабаном 3 и механизмом трещотки 6 ввернут во внутреннюю резьбу, выполненную на правом конце стебля2, который запрессован в скобу 1 микрометра или в основание микрометрического глубиномера. Зазор в резьбовом соединении устанавливается с помощью регулировочной гайки 5, навертываемой на коническую резьбу, нарезанную на наружной поверхности стержня. Стопорение микрометрического винта осуществляется устройством 7 или 8. На наружной поверхности стебля имеется продольно отсеченная линия над и под которой нанесены миллиметровые деления. Начальные штрихи шкалы и штрихи, соответствующие каждому пятому миллиметру, отсечены цифрами. Сверху отсеченной линии нанесены деления миллиметровой шкалы, смещенные относительно начального деления ниже расположенной шкалы на 0,5 мм. Указатель отсчёта по шкалам нанесен на стебле, являющимся торцом барабана. На торце барабана выполнен сков на котором нанесены 50 делений. Штрихи шкалы барабана, соответствующие каждому пятому делению, удлинены и отмечены цифрами 0,5,10….45. Поворот барабана вместе с микрометрическим винтом на 1 деление соответствует их перемещению в осевом направлении на 0,01 мм. Таким образом, цена деления микрометра – 0,01мм. На рис. 12 б, в показана величины отсчета равные 3,23 и 3,71 соответственно. При установке на нижний диапазон измерений(нулевая установка) нулевой штрих барабана должен совпадать с продольной линией стебля, а скошенный край барабана находится напротив крайнего левого штриха, который должен быть виден целиком. Но расстояние от конической части барабана до штриха не должно превышать 0,15 мм.
Рис. 12.б, в
Микрометры предназначены для измерения линейных размеров прямым абсолютным контактным методом. Они выпускаются следующих типов: МК-гладкие, МЛ – листовые, МТ- трубные, МЗ-зубомерные, МП- проволочные, МГ- горизонтальные настольного типа, МВ- вертикальные настольного типа, МН1,МН2 –настольные со стрелочным отсчетным устройством, - с цифровым электронным устройством.
Гладкий микрометр типа МК состоит из скобы, с одной стороны запрессована пятка 2(рис. 12 г), а с другой стороны скобы микрометра – головка в сборе с микровинтом и механизмом трещотки 6.
Конструкция трещотки выполнена с торцевыми зубьями(рус. 12 е), или с зубьями на кольце(рис.12 д).
В последней конструкции в корпусе трещотки выполнено отверстие в котором помещена пружина 3 со штифтом2, имеющая конец, срезанный под углом. Срезанная часть штифта входит во впадину зуба кольца. Если при измерении сила трения между поверхностью изделия и торцовыми поверхностями пятки и микровинта превышает силу трения между штифтом и корпусом1, то штифт сожмет пружину3 и выйдет из зацепления – перемещение микровинта прекратится. Закрепление микровинта в требуемом положении осуществляется стопорным устройством с зажимным винтом 4. А микрометры некоторых моделей имеют эксцентриковые или цанговые зажимные устройства. Для приведения в соприкосновение измерительных поверхностей микрометра с измерительным изделием пользуются только механизмом трещотки. Нормальная сила измерения обеспечивается при 3-5 щелчках трещотки. После этого микровинт стопорят и осуществляют отсчет по шкалам микрометра. Вращение микровинта за барабан не допускается, т.к. возникают недопустимо большие силы и резьба винта изнашивается.
Листовой микрометр предназначен для измерения толщин листов и лент. В отличие от гладкого микрометра он снабжён неподвижным круговым циферблатом5 (рис 12 з) и указателем стрелкой6 соединённой с барабаном 4. Измерительные пятки 2 выполнены сферической формы. Микровинт имеет шаг равный 1 мм, поэтому при повороте на 1 оборот он перемещается на 1 мм. На циферблате нанесены 100 делений с ценой деления 0,01 мм. На стебле 3 имеется миллиметровая шкала. Вылет скобы составляет 20,40,80 мм при диапазонах 0-5, 0-10,0-25 мм.
Рисунок 12 з.
Трубный микрометр предназначен для измерения толщин стенок труб. От гладкого он отличается сферической пяткой и формой скобы, имеющей выемку( рис.12 и)
Рисунок 12 и.
Зубомерный микрометр предназначен для измерения длины общей нормали зубчатых колес с модулем свыше 1 мм. От гладкого он отличается дисковыми насадками( рис. 12 к)
Рисунок 12 л.
Микрометр типа МК служит для измерения диаметра проволоки, поэтому его скоба имеет соответствующую форму(рис. 12 л)
Настольные микрометры снабжены микрометрической головкой с ценой деления 0,01 мм, имеют на барабане 100 делений. Шаг микровинта равен 1 мм. Они предназначены для измерения размеров малогабаритных деталей небольшой жесткости и применяются в часовой, приборостроительной промышленности. Известны следующие типы таких микрометров: МГ,МВ(горизонтально, вертикально расположенная головка), МН-1(со стрелочным отсчетным устройством и силой измерения не более 50+_20Сн) и МН-2(со стрелочным отсчетным устройством и силой измерения не более 200+_50сН)
Настольные микрометры МГ(рис.13 а, б), МВ(рис.13 в), МН-1 и МН-2(рис.13 г) имеют регулировку по высоте столика 1 для установки на него измеряемых изделий.
Конструкция микрометрической головки (рис 13 а), закрепленной в корпусе 2 унифицирована. На стебле 5 микрометрической головки нанесены миллиметровые деления продольной линией, а на барабане 6 деления с ценой деления 0,01 мм. Начальные штрихи на шкале и штрихи соответствующие каждому пятому элементу на шкале стебля и каждому десятому на шкале барабана удлинены и у них нанесены цифры. Осевое перемещение микрометрического винта при его вращении через фрикционное устройство 7 передается на измерительный стержень 4, который благодаря шпонке ,перемещается без вращения в осевом направлении. Описанное устройство предохраняет измеряемую деталь, расположенную на измерительном столике 1 от поворота и изменения заданного первоначального положения. На конце измерительного стержня закреплен наконечник 3 с измерительной поверхностью различной формы, позволяющими измерять пазы, элементы зубчатых мелкомодульных колес, фрез и т.д. Столик 1 вертикального настольного микрометра МВ(рис 13 в) имеет поворотный диск 2.Настольные микрометры типов МН-1,МН-2 снабжены рычажно-зубчатой головкой 4, которая установлена в корпусе 2 соосно микрометрической головкой. Наконечник головки отводится от измеряемого изделия оритиром 5. Предельно допускаемая погрешность отсчетного устройства микрометров типа МН-1, МН-2 не превышает +_0,5мкм. Предел допускаемой погрешности микроголовки не более +_2 мкм. Рассеяние показаний отсчетного устройства из серии 10 измерений не более 0,25 мкм. При относительных измерениях микрометр настраивают на размер по блоку ПКМ, установленному на столике 1. При этом микрометрическая головка должна быть выставлена на номинальный размер контролируемого изделия, а барабан 6 застопорен с помощью фиксатора 7. Стрелку рычажно-зубчатой головки 4 устанавливают на нулевую отметку. После настройки микрометра измерительный наконечник 3 отводят с помощью рычага оритира 5 заменяют блок ПКМД соответствующим измеряемым изделием. Освободив рычаг оритира 5, отсчитывают по шкале головки 4 отклонения размера от номинального. Действительный размер равен алгебраической сумме номинального размера и показаний, отсчитанных по шкале головки 4.
Рисунок 13
Микрометрический глубиномер
Микрометрический глубиномер предназначен для измерения глубины пазов, глухих отверстий и высоты уступов. Он представляет собой микрометрическую головку рис. 13.е.
Рисунок 13 е.
Он представляет микрометрическую головку, запрессованную в основание 1, перпендикулярную поверхности основания. В глухое отверстие, выполненное в торце микровинта, могут быть плотно вставлены сменные стержни 2, обеспечивающие измерение размеров от 0 до 150 мм, через 25 мм на стебле микрометрической головки. Деления нанесены от 25 до 0 мм, т.к. при ввинчивании микровинта по часовой стрелке, показание глубиномера увеличивается. Фиксирование микрометрического винта осуществляют винтом 3. Нулевую установку глубиномера проверяют на поверочной плите. Схема измерения глубиномера, высоты уступа, приведена на рис. 13.ж.
Левой рукой основание глубиномера прижимают к базе, а правой вращают трещетку 1 до соприкосновения измерительного стержня с контролируемой поверхностью и осуществляют отсчет.
Микрометрический нутромер- это накладной прибор, для измерения внутренних размеров с двухточечной схемой, при которой одна точка неподвижна, а вторая подвижна при измерении.
Нутромер имеет микрометрическую головку 2, рис. 14.а один или несколько удлинителей 3 и измерительный наконечник.
Рисунок 14 а.
Микрометрическая головка рис.13 е, аналогично микро-головке микрометра. В ее корпус 4 запрессован неподвижный измерительный наконечник 5 и муфта 1, с внутренней резьбой. Микровинт 6 ввертывается в корпус головки и фиксируется в требуемом положении стопором 2. Зазор в резьбовом соединении регулируется гайкой 10, с конической резьбой. Микровинт 6, с гайкой 7, барабаном 8 и контргайкой 9, является единой сборочной единицей. На барабане нанесена шкала с 50 делениями, с ценой деления 0,01мм. Мм шкалы выполнены на наружной поверхности стебля 3. Удлинитель, рис. 14.в, стальной стержень 1, устанавливаемого размера, со сферическими поверхностями.
Рисунок 14 в.
Он помещен в металлическую трубу 2, с резьбовыми муфтами 3,4 на концах. Удлинители свинчиваются один за другим до получения требуемого размера. Их размеры: 13, 25, 50, 75, 100, 150, 200, 300, 400, 500, 1000, 2000мм.
Настройка нутромера осуществляется по установочной мере 1, рис. 14 г, представляющей собой скобу с двумя взаимно параллельными поверхностями.
Рисунок 14г.
К каждому нутромеру придается одна установочная мера, размером 63, 75, 150, 350мм. В соответствии с размерами микрометрической головки. Головку 2, с наконечником 3, устанавливают между измерительными поверхностями установочной меры 1. Придерживая меру и головку левой рукой, находится наикратчайшее расстояние между поверхностями установленной меры. Застопорив микровинт стопором 4, микрометрическую головку вынимают и проверяют нулевую установку по шкалам головки. Если нулевая установка сбита, то ее восстанавливают, освободив контргайку 9, рис.14 г и повернув барабан, до совпадения его нулевой отметки с нулевым штрихом стебля.
После проверки микро-головки, по установленной мере, рассчитывают удлинители, стремясь к наименьшему их числу, при сборке. Для измерения диаметра отверстий рис. 14.д. нутромер вводят в контролируемое отверстие, прижимая его измерительную поверхность левой рукой, а правой вращает барабан, вывинчивают микровинт, до соприкосновения его с противолежащей поверхности отверстия.
Рисунок 14 д.
Нутромер при этом необходимо слегка покачивать, до ощущения легкого трения поверхности нутромера и изделия. Застопорив, нутромер выводят из отверстия и отсчитывают по шкалам результат измерения, прибавив размеры удлинителей. Микрометрический нутромер не имеет центрирующего мостика, поэтому необходимо измерять диаметр в плоскости перпендикулярной к оси отверстия положения 2 и в плоскости осевого сечения положение 1.
Наибольший размер в положении 1 и наименьший размер в положении 2, должны совпадать. Только после такого совпадения размеров, проводят отсчет по шкалам нутромера. Расстояние между двумя внутренними взаимно параллельными плоскостями, измеряют в двух положениях. Отсчет по шкалам нутромера проводят при совпадении наименьших показаний положений 1 и 2. Нутромеры с пределами измерений 1250-4000мм и более, могут иметь кроме микрометрической головки индикатор, с ценой деления 0,01мм. При измерении микрометрическими нутромерами, погрешность центрирования и перекоса нутромера в отверстии, достигают одной – 0,02мм каждая. Применение индикаторной головки, значительно облегчает нахождение диаметрального размера в осевой и диаметральных плоскостях при измерении больших отверстий, и уменьшает погрешность центрирования и перекоса в 2-3 раза.
Нахождение диаметрального размера облегчает торцовые упоры, которыми снабжаются микрометрические нутромеры иностранного производства. Недостаточная жесткость нутромера на изгиб, является одной из причин возникновения существующих погрешностей, при измерении больших размеров по ГОСТу 10-58, для микрометрического нутромера, при длине 4000-5000мм, допускается погрешность от изгиба до 55 мкм. Поэтому в тяжелом машиностроении, для измерения больших размеров, преимущественно используют микрометрические нутромеры, со специальными удлинителями повышенной жесткости. ГОСТ устанавливает допустимые погрешности микрометрических нутромеров от ± 6 мкм для интервалов размеров от 50-125мм и до ±180мкм, для интервала 9000-10000мм. Допустимые погрешности установочных мер от ± 2 до ± 4мкм. Поверка микрометрической головки производится на горизонтальном оптиметре, при показаниях 50; 55,12; 55,24; 55,36; 62 мм.
Погрешности не должны превышать 6 мкм. Кроме того на измерительной машине, проверяется погрешность микрометрической головки в сочетании с различными на всем диапазоне измерений.
Швейцарская фирма «Teza» выпускает микрометрические нутромеры с трех линейным касанием рис.15.
Рисунок 15.
Принцип работы прибора основан на взаимодействии измерительного конуса 1 и трех измерительных стержней 2, причем самой важной частью всей замкнутой системы, является измерительный конус конструкции. На конусе, из закаленной стали, нанесена отшлифованная измерительная резьба, несущая боковая сторона профиля которой расположены параллельные оси конуса 3, измерительный стержень 2, установлены в измерительной головке, перпендикулярной оси прибора и смещены на 120о каждый. Принудительный контакт стержня с измерительной резьбой, осуществляется благодаря пружинам, правильная позиция которых обеспечена направляющей резьбой. Благодаря использованию удлинителей, глубина измерений достигает нескольких метров, а в трех контактном микрометрическом нутромере, применены различной по форме наконечники, которые позволяют измерить сквозные, глухие отверстия и диаметр выточек разной формы и измерять внутреннюю резьбу.
Индикаторы
Индикаторами называют механические или электронные конструктивно обособленные измерительные головки, содержащие корпус с передаточным механизмом, шкалой и указателем (стрелкой) или электронный преобразователь и цифровой дисплей, подвижный стержень с измерительным наконечником и элементы крепления.
Индикаторы можно условно разделить на следующие группы:
- механические индикаторы часового типа (с зубчатой передачей), шкалой и стрелкой;
- механические индикаторы с рычажно-зубчатой передачей, шкалой и стрелкой;
- электронные индикаторы с встроенным цифровым дисплеем.
Также выпускают отдельную группу индикаторов бокового действия.
Механические индикаторы с круговой шкалой и стрелкой появились в 50-е годы прошлого века. Это были довольно точные приборы для относительных измерений. Они привели к существенным изменениям в линейных измерениях того времени, когда в машиностроении применялись калибры, штангенциркули и микрометры
С использованием индикаторов разрабатывали контрольные приспособления, позволяющие измерять самые разные детали в цехах и лабораториях и даже в процессе обработки на станках. Механические индикаторы доминировали в измерительной технике до появления пневматических и индуктивных приборов, имевших более высокую точность, крупные шкалы и возможность выдавать сигналы для управления контрольными сортировочными автоматами и станками.
Но и в настоящее время механические индикаторы широко применяют для простых относительных измерений. Достоинством механических индикаторов является высокая надежность и низкая стоимость.
Электронные индикаторы появились сравнительно недавно. Их отличает высокая точность, большие диапазоны измерений, цифровой отсчет, дружественная конструкция и удобство в эксплуатации.
Механические индикаторы
Механические зубчатые и рычажные индикаторы широко применяют для сравнительных измерений размеров деталей, малых перемещений и отклонений формы (например, биений). При измерениях индикаторы устанавливают на стойки или штативы или в контрольные приспособления, (например, широко распространенные приспособления для проверки размеров деталей подшипников качения), на приборы для проверки зубчатых колес и зацеплений, на индикаторные нутромеры, а также на магнитные стойки при наладке металлорежущих станков и др.
Механические индикаторы выпускают ведущие зарубежные фирмы США, Европы и Японии - Tesa (Швейцария), Mahr (Германия), MITUTOYO (Япония), и др. В России механические индикаторы выпускает Кировский инструментальный завод (г. Киров). Каждая фирма предлагает большую гамму индикаторов для решения различных измерительных задач.
Индикаторы часового типа (рис. 33) являются измерительными головками с зубчатой передачей.
Рис.33. Механический индикатор часового типа
Механические индикаторы часового типа выпускают по международному стандарту ISO 463:2006 с учетом требований стандарта ISO 14978:2006.
Принципиальная схема индикатора часового типа показана на рис. 34.
Рис. 34 Кинематическая схема индикатора часового типа
Индикатор имеет жесткий цилиндрический корпус, в котором размещен измерительный механизм. Измерительный стальной закаленный стержень установлен в точной направляющей скольжения. Стержень перемещается в бронзовых втулках и притерт к ним без зазора. На измерительном стержне нарезана зубчатая рейка, зацепляющаяся с трибом. На одной оси с ним посажено зубчатое колесо, передающее вращение другому трибу, на оси которого закреплена основная стрелка. На оси первого триба насажена маленькая стрелка указателя числа оборотов основной стрелки. С первым трибом зацепляется также зубчатое колесо, на ось которого напрессована втулка с пружинным спиральным волоском. Волосок создает натяг во всех зубчатых зацеплениях индикатора, заставляя их работать одной стороной профиля зуба, устраняя тем самым влияние зазоров в зацеплении на показания индикатора. В современных индикаторах часового типа оси зубчатых колес и трибов установлены на твердокаменных опорах (рубиновых подшипниках) и повышена точность изготовления профиля зубчатых колес. Это обеспечивает большой срок службы и высокие метрологические характеристики. Измерительное усилие создается пружиной растяжения. На измерительном стержне закреплена шпонка с большим вылетом, исключающая возможность поворота измерительного стержня. Во многих моделях циферблат-шкала может повертываться с целью установки индикатора на нуль при настройке его на размер. Большинство индикаторов снабжено противоударной защитой измерительного механизма.
Передаточное отношение индикатора определяют как отношение линейного перемещения конца стрелки к вызвавшему его перемещению измерительного стержня
i=R α / S,
где R - радиус стрелки;
α - угол поворота стрелки в радианах;
S - перемещение измерительного стержня, вызвавшее поворот стрелки на угол α.
Угол поворота стрелки определяют как произведение угла β поворота триба z1 на передаточное отношение следующей зубчатой пары, равное отношению чисел зубьев ведущего и ведомого колес:
α = β z2 / z3.
Так как β =2S/ m z1 рад,
то
α =2S z2 / m z1 z3 , рад.
Следовательно, передаточное отношение индикатора будет
i=2R z2/m z1 z3
Индикаторы, у которых стрелка совершает полный оборот или несколько оборотов, первое и последнее деления на круглой шкале индикатора совпадают, т.е. при перемещении измерительного стержня на 1 мм стрелка совершала ровно один оборот. Для выполнения этого условия числа зубьев и модуль зацепления выбраны так, чтобы при S = 1 мм получился угол поворота стрелки α = 2π рад:
2π = 2 z2/m z1 z3
или
m = z2 / π z1 z3
Цену деления шкалы определяют по формуле
c = a /I,
где a интервал деления шкалы.
Расстояние между штрихами шкалы выбирают в зависимости от диаметра шкалы 1,5 или 2,3 мм.
Индикатор часового типа не имеет погрешности схемы, и ход его кривой погрешности зависит от эксцентриситета колес и от местных дефектов контактных элементов передачи (главным образом, реечной пары).
Выпускают большое количество моделей индикаторов часового типа различного назначения с:
- ценой деления шкалы - 0,001; 0,002; 0,01; 0,1 мм;
- диапазоном измерения - 1,0; 3,0; 5,0; 10,0; 30,0; 50,0 100,0; 200,0 мм;
- диаметром шкалы - 40; 57; 58; 82 мм;
- с измерительным усилием - от 0,7 до 2,2 Н.
Индикаторы выпускают со степенью защиты от IP52 – до IP63 по стандарту DIN EN 60529 и ГОСТ 14254-96.
У индикаторов с большим диапазоном измерения измерительное усилие и его перепад больше.
Крепление индикаторов в стойках и приспособлениях производится за гильзу диаметром 8h6.
В настоящее время выпускают несколько моделей индикаторов с рычажно-зубчатым механизмом с ценой деления 0,5; 1,0 и 2,0 мкм, предназначенных для точных относительных измерений в небольших диапазонах. Индикатор на входе имеет один - два элементарных рычажных механизма, а на выходе одну-две зубчатых передачи. В качестве контактных звеньев рычажных переда используют шар-плоскость или цилиндр-цилиндр, изготовленных из закаленной стали или твердого сплава.
Пример кинематической схемы рычажно-зубчатого индикатора показан на рис. 35.
Рис. 35 Кинематическая схема рычажно-зубчатого индикатора
Механизм индикатора состоит из двух рычажных и одной зубчатой пары. Последняя расположена в конце кинематической цепи механизма. Поэтому погрешности зубчатого зацепления почти не влияют на суммарную погрешность прибора. В рычажной системе механизма индикатора предусмотрены регулировки передаточного отношения изменением длины малого плеча первого рычага и выбором участка с минимальной ошибкой - изменением положения опорного штифта второго рычага. Сначала изменением положения штифта добиваются симметричности погрешностей при наибольших отклонениях стрелки. Затем регулируется малое плечо первого рычага путем поворота втулки с эксцентричной сферической опорой до устранения погрешностей в заданных точках. Погрешность схемы правильно отрегулированного индикатора не превышает 0,1 мкм.
Передаточное отношение индикатора определяют по аналогии с индикатором часового типа
і= R·α/S
α = β r2 z1 /r3 z2
где β - угол поворота рычага r1 при перемещении измерительного стержня на величину S;
r2 /r3 - передаточное отношение рычажной пары;
z1/z2 - передаточное отношение зубчатой пары.
Так как
β =S/ r1.
То і = R r2 z1/ r1 r3 z2.
Цена деления
c = a / i.
Для повышения точности и износоустойчивости механизма индикатора опоры всех передач выполнены на часовых твердокаменных камнях. Направляющие измерительного стержня выполнены на насыпных шарах. Измерительный стержень имеет свободный ход, предохраняющий механизм индикатора от повреждений при ударах по наконечнику.
Фирмы выпускают ограниченное число моделей механических индикаторов с рычажно-зубчатой передачей для точных относительных измерений в небольшом диапазоне:
- с ценой деления шкалы - 0,5; 1,0; 2,0 мкм;
- с диапазоном измерения - ± 40; ± 50; ±100 мкм.
Измерительное усилие не более 2,0 Н.
Установку прибора на нуль производят поворотом шкалы в пределах ±5 делений с последующим креплением стопорным винтом. Головка снабжена арретиром и указателями полей допусков. Головку устанавливают в стойку или приспособление за гильзу диаметром 8h6.
Электронные индикаторы
Сравнительно недавно начали выпускать электронные индикаторы оснащенные как правило инкрементными преобразователями. Достоинство таких индикаторов состоит в том, что они имеют цифровой отсчет и большие диапазоны измерений. Цифровой отсчет удобен по сравнению с отсчетом по двум аналоговым шкалам механических индикаторов часового типа. Также электронный индикатор в отличие от механического, не требует настройки на нуль с помощью концевых мер. Его настройка на нуль производится нажатием кнопки -0- в любом месте диапазона измерений.
В электронных индикаторах применяют бесконтактные преобразователи: емкостные, индуктивные, фотоэлектрические. В них соблюдается принцип Аббе, что повышает точность измерений.
Электронные индикаторы выпускают ведущие зарубежные фирмы: «Митутоя» (Япония); «Махро» (Германия); «Teza» (Швейцария).
Электронные индикаторы выпускают по международному стандарту ISО 463-2006, с учетом требований стандарта ISО 14978-2006. Электронные индикаторы выпускают трех типов: инкрементные емкостные и индуктивные преобразователи.
Инкрементные преобразователи измеряют приращение измеряемой координаты, при перемещении измерителя (отсюда их название increment- приращение).
Подобные преобразователи, благодаря возможности интерполирования результатов измерения, относительно периода шкалы измерителя, обладают высокой разрешающей способностью.
Инкрементные емкостные преобразователи отличаются небольшой мощностью потребляемой для считывания информации со шкалы. Поэтому емкостные преобразователи удобны для применения в измерительных системах с жесткими ограничителями на потребляемую мощность (штангенциркуль, микрометр и др.).
Емкостной инкрементный преобразователь состоит из гибкой линейки и съемника, выполненных из фольгированного диэлектрического материала. Линейка представляет собой многослойную гибкую ленту с нанесенным на ней фольгированным слоем. На изнаночной стороне нанесен клей и линейка (лента) приклеивается к стеклянной пластине, закрепленной неподвижно на корпусе индикатора или его механизма. На фольгированном слое, выполнены прямоугольные штрихи (электроды). Ширина прямоугольных электродов и промежутков между ними, обычно одинакова и определяет чувствительность и точность измерительной системы. На стержне индикатора расположена небольшая считывающая шкала (съемник), с электродами, нанесенными на фольгированном слое, наклеенном на стеклянную пластину.
В корпусе электрического индикатора расположена микропроцессорная схема и ЖК дисплей с цифровым отсчетам. Высота цифр дисплея составляет 7-9мм. На корпусе индикатора имеются две кнопки вкл/откл, установка нуля. Установка нуля возможна в любом месте диапазона измерений, некоторые модели имеют дополнительную функцию: сортировка по размерам, кодовый выход на внешнее устройство.
Вся электрическая система питается от литеевой батарейки. Срок службы 20 тысяч часов. Индикаторы снабжены точной беззазорной направляющей скольжения измерительного стержня.
Электрические индикаторы выпускаются со степенью защиты от IP52 до IP67 (герметичные), по стандарту DINEN 60529.
Особенность инкрементных преобразователей в том, что их собственная погрешность практически не зависит от диапазона измерений, а зависит от дискретности линейки и качества их изготовления.
Метрологические характеристики электрических индикаторов с инкрементным емкостным преобразователем:
- диапазон измерений: 5,0; 10,0; 12,5; 25,0; 30,0; 50,0; 100,0; 150 мм;
- измерительное усилие: 0,7-2,2Н;
- предельно допустимая погрешность показаний: при дискретности отсчета 1мкм-4мкм; для дискретного отсчета 10 мкм-10мкм;
- воспроизводимость для дискретного отсчета 1мкм-2мкм; для дискретного 10мкм-2мкм;
- гистерезис для дискретного отсчета 1мкм-0,3мкм; 10мкм-0,3мкм.
Индуктивные индикаторы имеют линелизованную выходную характеристику и измерительный стержень, установленный на насыпных шариках. Индуктивные индикаторы имеют хорошие метрологические характеристики, но более сложную конструкцию и более высокую цену. Выпускают несколько моделей электронных индикаторов с индуктивными преобразователями с дискретностью отсчета 0,5; 1; 5; 10 мкм с диапазонам измерения ± 2мм, с предельно допустимой погрешностью показаний 0,25-0,5% от диапазона измерений.
Фирма «Teza» выпускает несколько моделей индикаторов с фотоэлектрическим инкрементным преобразователем рис.37.
Рис. 37. Электронный индикатор с фотоэлектрическим инкрементным преобразователем
Поверку метрологических характеристик индикаторов осуществляют двумя способами:
- с помощью концевых мер длины 1-го, 2-го классов;
- на горизонтальном компараторе.
Компаратор снабжен подвижным столиком на шариковых беззазорных направляющих. Более точным образцовым аттестованным средством измерения, показание которых сравнивают с показаниями поверяемого индикатора при совместном перемещении измерительных стержней индикатора и образцового средства.
Второй способ более производительнее и не требует высокой квалификации контролера.
Дата добавления: 2018-04-15; просмотров: 5150; Мы поможем в написании вашей работы! |
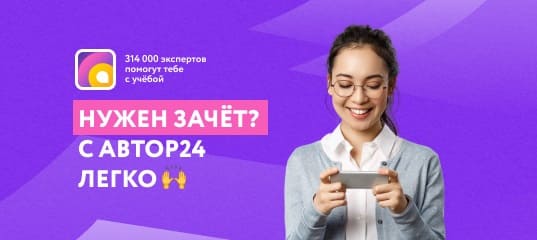
Мы поможем в написании ваших работ!