Наиболее распространенные технологические схемы отбензинивания газа
На рис. 8.2 приведена технологическая схема массовой маслоабсорбционной установки для отбензинивания газа.
Технологическая схема маслоабсорбционной установки
2 |
1 |
I |
II |
III |
3 |
IV |
V |
VI |
4 |
VII |
8 |
7 |
5 |
6 |
VIII |
IX |
11 |
12 |
X |
13 |
14 |
15 |
XI |
XII |
10 |
16 |
17 |
9 |
в11 |
из17 |
ХIII |
1, 9, 11 – водяной холодильник; 2 – тарельчатый абсорбер; 3 – газовый сепаратор; 4 – выветриватель; 5, 8 - теплообменник; 6 – печь; 7 – тарельчатый десорбер; 10, 14, 15, 17 – насос; 12 – сепаратор; 13 – рефлюксная ёмкость; 16 – градильня.
I – исходный газ; II – минеральное масло; III – отбензиненный газ; IV – товарный газ; V – отработанное масло; VI – уловленное масло; VIII – увлеченный газ; IX – десорбированная газо – паровая смесь; Х – остаточный газ; XI – бензин стабилизации на орошение; XII – бензин стабилизации; XIII – вода.
Рис. 8.2
Нефтяной газ потоком I через водяной холодильник 1 подается в кубовую часть тарельчатого абсорбера 2, орошаемого лёгким веретенным или трансформаторным маслом с температурой порядка 30 0С. Давление в абсорбере не ниже 10 атм.
В результате массообмена углеводороды С3+высш. Растворяются в масле, а отбензиненный газ потоком II через газовый сепаратор 3 покидает установку.
Отработанное масло (поток V) смешивается с маслом уловленным в газовом сепараторе (поток VI) и направляется в выветриватель 4, где вследствии снижения давления до 1,5 – 2 атм из него выделяются увлеченные углеводороды С1 и С2, которые после подогрева регенерированным маслом в теплообменнике 8, подаются в нижнюю часть десорбера 7 для интенсификации процесса регенерации за счет интенсивного кипения и перемешивания.
|
|
Жидкая фаза из выветривателя тоже подогревается в теплообменнике 5 и печи 6 и с температурой порядка 250 0С подается в среднюю часть тарелчатого десорбера, работающего при атмосферном давлении.
В подобных термобарических условиях от масла отгоняются все ранее поглощенные компоненты, после чего регенерированное масло с помощью насоса 10 прогоняется через теплообменники 8 и 5, где отдает свое тепло продуктам из выветривателя и после охлаждения в водяном холодильнике 9 возвращается в процесс.
Газо – паровая фаза с верхней части десорбера 7 проходит водяной конденсатор – холодильник 11 и поступает на разделение в сепаратор 12, из которого углеводороды С1 и С2 выводятся на местные нужды (поток Х), а бензин стабилизации накапливается в рефлюксной ёмкости 13, откуда насосами 14 и 15 частично подается на орошение десорбера, а частично выводится как товарный продукт.
Хладоагентом во всех холодильниках служит хим. Обессоленная вода, циркулирующая с помощью насоса между ними и градильней 17.
|
|
Опытным путем установлено, что чем легче абсорбент, тем с более высокой селективностью идёт процесс, хотя для этого требуются все более жесткие условия, да и потери в десорбере становятся выше.
Поэтому, в последнее время масло в подобных установках стали заменять на дизельное топливо, стабильный конденсат и даже реактивное топливо, что позволило при 10 – 30 0С и давлении 30 – 70 атм в абсорбере довести степень извлечения С3Н8 до 40 – 50 %; С4Н10 до 95 – 100 %.
Адсорбционный метод
Адсорбция – это объёмное поглощение газов и паров поверхностью твёрдого тела (адсорбентом) с образованием обновлённой поверхности.
Процесс обратный абсорбции называется десорбцией.
Различают физическую, химическую и так называемую промежуточную адсорбцию.
Физическая адсорбция связана, как правило, с Ван – дер – Ваальсовыми силами, удерживающими молекулы газов и паров у поверхности твёрдого тела и не сопровождается химическим взаимодействием между поглощаемым компонентом и поглотителем.
Энергия взаимодействия в этом случае никогда не превышает нескольких десятков кДж/моль поглощаемого вещества.
|
|
Химическая адсорбция (хемосорбция) связана с протеканием определённых поверхностных химических реакций между поглощаемым компонентом и адсорбентом, которые для своего осуществления требуют преодоления определенного активационного барьера.
Энергия взаимодействия в этом случае достигант нескольких сотен кДж/моль поглощаемого вещества.
Промежуточная адсорбция связана с образованием между молекулами поглощаемого вещества и поверхностью адсорбента слабых координационных связей (например, водородных) с промежуточными значениями энергии взаимодействия.
При физической адсорбции поглощающая способность адсорбента (разумеется при достижении равновесия) определяется температурой, давлением, концентрацией поглощаемого компонента и удельной поверхностью поглотителя.
Чем выше температура, тем меньше поглощающая способность адсорбента, т.е. физическая адсорбция экзотермична.
С ростом давления, наоборот, поглощающая способность адсорбента нарастает (разумеется, речь идёт о парциальном давлении поглощаемого компонента).
Влияние концентрации поглощаемого компонента и удельной поверхности адсорбента аналогичны влиянию давления.
При химической адсорбции поглощающая способность адсорбента (разумеется, при достижении равновесия) определяется константой равновесия конкретной химической реакции.
|
|
Константа равновесия химической реакции подчиняется принципам Ля – Шателье.
Поскольку поглощение идёт с уменьшением объёма, то с ростом давления количество вещества, поглощаемого единицей поверхности, увеличивается.
Поскольку хемосорбция может идти как с выделением, так и с поглощением тепла, причём, в гораздо больших количествах, чем при физической адсорбции, то с ростом температуры количество вещества, поглощаемого единицей поверхности, будет уменьшаться, если реакция идёт с выделением тепла, и, наоборот, будет возрастать, если реакция идёт с поглощением тепла.
Кроме того, при хемосорбции особую роль приобретает состав исходной смеси.
Если в ней присутствует ингибитор или катализатор данной реакции, то их наличие может привести либо к полному прекращению реакции, либо к её стремительному протеканию.
С точки зрения термодинамики химическая адсорбция особо выгодна для удаления из газа компонентов с малыми концентрациями, в то время как для грубой очистки пригодны оба метода.
Существует множество технологических приёмов проведения адсорбционных процессов.
Наибольшее распространение получили так называемые циклические (периодические) установки с неподвижным слоем адсорбента, основной узел которых – один или несколько адсорберов, выполненных в виде полых колонн, заполненных гранулированным адсорбентом.
Газовый поток, содержащий адсорбируемые компоненты, пропускается через слой адсорбента до проскока.
После этого, адсорбент в адсорбере регенерируют, а газовый поток направляют в другой адсорбер. Регенерацию проводят снижением давления, нагреванием, вытеснением или комбинацией этих методов.
Т.к. время адсорбции и регенерации не совпадает, то подбирают такое число адсорберов, чтобы в целом процесс шел непрерывно.
При этом возможно два варианта:
- целевой продукт адсорбируется и может быть выделен только при регенерации;
- адсорбируются нецелевые компоненты. В этом случае, целевой продукт получают непосредственно при адсорбции.
Менее распространены установки с движущимся слоем адсорбента.
Последний, под действием силы тяжести медленно опускается по адсорберу, выводится из его нижней части и попадает в так называемый эрлифт, представляющий собой вертикальную трубу, параллельную адсорбционной колонне.
По этой трубе снизу вверх движется поток воздуха, который поднимает зерна адсорбента в верхнюю часть колонны.
Сырьевой газовый поток поступает в среднюю часть адсорбера и движется вверх противотоком к адсорбенту.
В верхней части колонны непрерывно происходит адсорбция, в нижней регенерация.
Возможны и другие конструкции:
- десорбер располагается над адсорбером;
- десорбер расположен параллельно адсорберу. В этом случае необходимы два эрлифта.
Наконец, существуют установки с псевдоожиженным (кипящим) слоем адсорбента, при котором, газовый поток, поступающий в адсорбер снизу, приводит адсорбент во взвешенное состояние.
При этом, резко увеличивается эффективность массообмена между адсорбентом и газом, а так же сокращается длительность адсорбции и десорбции, проводимой, обычно, в отдельном аппарате.
В качестве адсорбентов чаще всего используют γ – Al2O3 , боксит, флюорит, силикагель; либо различные цеолиты, например, клиноптилолит, NaX, NaY, CaA и т.д.
На рис. 8.3 приведена технологическая схема типичной адсорбционной установки с неподвижным слоем поглотителя для отбензинивания газа.
Технологическая схема адсорбционной установки
1 |
2 |
3 |
I |
II |
III |
4 |
5 |
6 |
IV |
7 |
V |
8 |
VI |
VI |
1, 2 – абсорберы; 3 – задвижка; 4 – регулятор давления; 5 – АВО; 6 – сепаратор; 7 – газодувка; 8 – печь.
I – исходный газ на отбензинивание; II – отбензиненный газ; III – отбензиненный газ на циркуляцию для регенерации; IV – газовый бензин; V – газ из сепаратора; VI – газо – паровая смесь после регенерации.
Рис. 8.3
Исходный газ потоком I поступает в один из адсорберов 1 или 2, находящихся в ванный момент на стадии адсорбции.
Пройдя сверху вниз через слой адсорбента, отбензиненный газ потоком II покидает установку.
Цикл адсорбции обычно продолжается 12 – 16 часов, после чего адсорбер переключают на регенерацию, осуществляемую отбензиненным газом или воздухом.
При использовании отбензиненного газа незначительную часть его отбирают и потоком III через регулятор давления 4, понижающего давление почти до атмосферного, подают на газодувку 7, прогоняющую газ через печь 8, а затем в соответствующий адсорбер.
Газы регенерации поступают в АВО 5, а затем в сепаратор 6, где и происходит отделение газового бензина.
Цикл регенерации обычно длится 6 – 7 часов.
В последние годы адсорбционный процесс отбензинивания газа стали совмещать с адсорбционной очисткой его от агрессивных примесей.
В этом случае, используются отечественные цеолиты марок:
NaA-ч – 1236; NaX- ч -1232 ; АцС – 1530; СаА АБ – 16; NaX – 362 и т.д.
Или импортные цеолиты марок:
А – 4 (фирма Tojo Soda – Япония); SP – 1335 (фирма Tojo Soda – Япония); СаА (фирма Union Carbide – США) и т.д.
Компрессорный метод
В основу метода положено явление выпадения конденсата из газа при повышении давления и последующем охлаждении.
Конечным продуктом является нестабильный газовый бензин, содержащий большое количество низкомолекулярных углеводородных компонентов газа и отбензиненный газ с значительным содержанием высокомолекулярных компонентов газового бензина.
В связи с этим, самостоятельно метод применяется редко, как не обеспечивающий необходимой глубины извлечения необходимых углеводородов; а вот в сочетании с другими методами он используется довольно часто.
Типичная принципиальная схема метода приведена на рис. 8.4.
1 |
III |
I |
II |
2 |
IV |
3 |
V |
VI |
VII |
4 |
5 |
VIII |
IX |
6 |
V |
X |
XI |
XII |
7 |
VIII |
8 |
14 |
XIII |
18 |
XIV |
9 |
XV |
10 |
XII |
12 |
11 |
V |
13 |
XVI |
VIII |
15 |
XVII |
16 |
17 |
1 – приёмный сепаратор; 2 – двухступенчатый компрессор; 3, 6, 11 – масло отделитель; 4 – водяной холодильник; 5 – водяной сепаратор; 7, 12 – холодильники с хладоагентом; 8, 13 – бензосепаратор, 9 – осушительный адсорбер; 10 – одноступенчатый компрессор; 14, 15 – ёмкости нестабильного газового бензина; 16, 17, 18 – насосы.
I – исходный газ; II – газ из приемного сепаратора; III – конденсат; IV – газ первой ступени компримирования; V – масло; VI - газ первой ступени компримирования после отделения масла; VII – вода на охлаждение; VIII – сконденсировавшаяся вода; IX – газ на вторую ступень компримирования; Х – газ после второй ступени компримирования; XI - газ после второй ступени компримирования, освобожденный от масла; XII – хладоагент; XIII, XVII – газовый бензин; XIV – газ в адсорбер; XV – газ после адсорбера; XVI – высушенный отбензиненный газ; XVIII – газовый бензин.
Рис. 8.4
Исходный газ потоком I поступает в приемный сепаратор 1, где освобождается от капельной жидкости, представляющей собой сконденсировавшиеся наиболее тяжелые углеводороды, направляемые насосом 18 в ёмкость 14.
Оставшийся газ попадает на первую ступень компримирования компрессора 2 и, пройдя маслоотделитель 3, через водяной холодильник 4 направляется в водяной сепаратор 5, где и происходит отделение сконденстровавшеся воды.
Оставшийся газ поступает на вторую ступень компримирования компрессора 2 и через маслоотделитель 6 и холодильник глубокого охлаждения 7 попадает в бензосепаратор 8, где и происходит отделение сконденсировавшегося газового бензина, так же направляемого в ёмкость 14. В этом же аппарате отделяется сконденсировавшаяся вода.
Оставшийся газ дополнительно высушивается в адсорбере 9 и окончательно поджимается на компрессоре 10. Пройдя маслоотделитель 11 и холодильник глубокого охлаждения 12 он попадает в бензосепаратор 13, где и происходит отделение сконденсировавшегося газового бензина, направляемого в ёмкость 15. В этом же аппарате отделяется сконденсировавшаяся вода.
Газовый бензин из емкостей 14 и 15 смешивается с помощью насосов 16 и 17, откачиваясь с установки потоком XVIII как товарный продукт.
Низкотемпературный метод
Метод известен в двух разновидностях:
- метод низкотемпературной ректификации;
- метод низкотемпературной конденсации.
Метод низкотемпературной ректификации
Это один из наиболее эффективных методов. Он основан на том, что скомпримированный и осушенный газ смешивается с конденсатом и подается в ректификационную колонну, где, в следствии массообмена, происходит разделение исходной смеси.
Метод позволяет более четко и глубоко извлекать из газа целевые углеводороды.
Типичная принципиальная схема метода приведена на рис. 8.5.
1 |
I |
II |
2 |
6 |
IV |
III |
V |
VI |
VII |
VIII |
3 |
4 |
5 |
IX |
1 – теплообменник; 2 – ректификационная колонна; 3 – холодильник; 4 – рефлюксная ёмкость; 5 – насос; 6 – рибойлер.
I – исходная смесь; II – отбензиненный газ; III – нестабильный газовый бензин; IV – пар; V – стабильный газовый бензин; VI – пары стабилизации газового бензина; VII – газо – паровая смесь; VIII – хладоагент; IX – конденсат.
Рис. 8.5
Исходная смесь потоком I после охлаждения отбензиненным газом в теплообменнике 1 поступает в ректификационную колонну 2, где и происходит отбензинивание газа.
Газовый бензин выводится потоком III и после стабилизации в рибойлере 6, обогреваемом паром, потоком V покидает установку. Газы стабилизации газового бензина потоком V возвращаются в колонну, принося необходимое тепло и турбулизируя кубовую жидкость, ускоряя процесс испарения газовых компонентов.
Газовая составляющая отбензинивания уходит сверху колонны 2 и после глубокого охлаждения в холодильнике 3 поступает в рефлюксную ёмкость 4, где происходит отделение от газа остатков сконденсировавшегося бензина.
Бензин с помощью 5 –го насоса возвращается в колонну, а отбензиненный газ отдает свой холод в теплообменнике 1 и покидает установку в качестве товарного продукта (поток II).
Дата добавления: 2018-04-15; просмотров: 515; Мы поможем в написании вашей работы! |
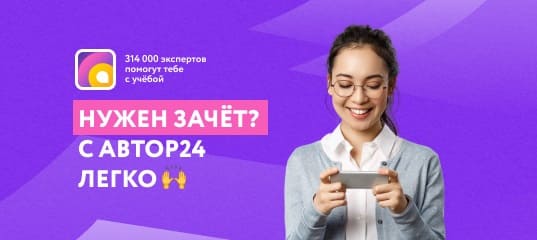
Мы поможем в написании ваших работ!