Замена в узлах машин трения скольжения трением качения
Лекция
Конструктивные методы повышения износостойкости деталей
Общие аспекты
Развитие конструкций машин происходит при постоянном стремлении к увеличению их производительности, что почти всегда сопровождается повышением механической и тепловой нагрузок подвижных сопряжений деталей. В связи с этим перед конструктором стоит задача создания новых, более совершенных узлов трения. Помимо того необходимо достичь высокой надежности машины, снизить ее массу, сократить расход дефицитных материалов. Это особенно важно при конструировании машин массового производства. Известно, что повышение долговечности машины даже в небольшой степени ведет к большой экономии металла, уменьшению затрат на производство запасных деталей, сокращению объема числа ремонтов, а следовательно, увеличению числа фактически работающих машин.
Поскольку при конструировании машин учитываются экономические факторы производства и эксплуатации, конструктору необходимо проводить перспективный прогноз длительности использования данной машины с учетом продолжительности эксплуатации машин предшествующих моделей. В ряде случаев этот срок составляет 25 лет, а иногда и более, например, для металлообрабатывающих станков, автомобилей, тракторов, транспортных самолетов.
При выборе конструктивного решения необходимо учитывать предстоящие затраты не только на изготовление машины или ее отдельных узлов, но и на обслуживание, и ремонт. Последние затраты при длительной эксплуатации машины во много раз больше стоимости ее изготовления. Поэтому главное внимание конструктора должно быть направлено на то, чтобы уменьшить износ узлов трения машины, сократить время и затраты труда на замену изношенных деталей и на регулировочные работы, снизить силы трения, повысив тем самым КПД машины, и др.
|
|
В конструктивную разработку узлов трения входят:*
Выбор материалов для трущихся деталей
Трущиеся детали в зависимости от назначения изготовляют из конструкционных, фрикционных, износостойких и антифрикционных материалов обширной номенклатуры. Во многих случаях на конструкционный материал наносят износостойкие покрытия, пленки и др. Иногда при особых требованиях к электрической проводимости (скользящие контакты, ламели коллекторов электродвигателей), стойкости к воздействию химически агрессивных сред (газов, в том числе горючих; рабочих жидкостей в системах питания двигателей и ракет; кислот и щелочей) и др. трущиеся детали изготовляют из сталей и сплавов специального назначения, оксидов металлов, спеченных и неметаллических материалов.
|
|
Из конструкционных сталей делают детали, которые, должны удовлетворять условиям высокой прочности, жесткости или податливости, а также имеют поверхности трения. Это – детали типа валов, пальцев, болтов, шарниров, зубчатых колес и т. д. Из стали, а также из чугуна изготовляют силовые цилиндры, поршни, плунжеры и поршневые кольца. Чугун широко распространен как материал для станин, столов кареток, ползунов, направляющие которых подвергаются трению.
Фрикционные материалы – это материалы, которые в контакте с металлической поверхностью имеют высокий и более или менее стабильный коэффициент трения. Материалы, применяемые в тормозах и фрикционных муфтах валов, разделяются на органические (дерево, кожа, пробка, войлок), металлические (чугун, стали У6, У7, марганцовистая сталь и др.), асбестокаучуковые, пластмассовые (текстолит, асбестотекстолит, фибра), спеченные на медной и железной основах.
Износостойкими называют материалы, которые при трении даже в тяжелых условиях нагружения сравнительно мало изнашиваются. К элементам конструкций, материал которых должен обладать высокой износостойкостью, относят плунжерные пары, зубья ковшей экскаваторов и погрузчиков, зубья врубовых машин и угольных комбайнов, лемеха плугов и рабочие органы большинства технологических машин (скребки, цепи, рештаки, штампы и др.). В качестве износостойких материалов используют конструкционные стали, упрочненные по всему объему или по рабочим поверхностям, специальные стали, чугуны, спеченные материалы, резину, пластмассы и др.
|
|
Из всех пар трения подшипники скольжения вызвали в свое время наибольшую трудность в обеспечении их длительной нормальной работы в силу высоких удельных нагрузок при сравнительно больших скоростях скольжения. В целях улучшения работы подшипников скольжения были разработаны сплавы, получившие название антифрикционных, т. е. обладающие низким коэффициентом трения (разумеется, при работе в паре со стальным валом). В дальнейшем антифрикционными материалами стали называть любой подшипниковый материал, как металлический, так и неметаллический, твердость которого меньше твердости сопряженной детали.
Понятие антифрикционность включает комплекс свойств, которым должен удовлетворять подшипниковый материал. Этими свойствами являются:
– достаточная статическая и динамическая прочность при повышенных температурах;
|
|
– способность образовывать прочный граничный слой смазочного материала и быстро восстанавливать его в местах, где он разрушен;
– низкий коэффициент трения при граничной смазке;
– отсутствие заедания на валу в случае перерыва в подаче смазочного материала;
– высокие теплопроводность, теплоемкость, прирабатываемость;
– хорошая износостойкость сопряжения;
– недефицитность материала и высокая технологичность.
Подшипниковых материалов, удовлетворяющих всем этим требованиям, фактически нет. Так, прочность оловянных баббитов резко снижается с повышением температуры, что ограничивает их применение при тяжелых условиях работы; прирабатываемость ряда антифрикционных бронз неудовлетворительна; неметаллические антифрикционные материалы имеют низкую теплопроводность. Каждый из подшипниковых материалов обладает антифрикционными свойствами только при определенных режимах трения.
Как установлено практикой, исчерпывающих, всеохватывающих рекомендаций в отношении выбора материалов для трущихся деталей не существует. Только на основании тщательного сопоставления условий службы трущихся деталей, исходных свойств материалов и тех изменений, какие они претерпевают на поверхностях трения, можно подобрать для каждого случая наиболее подходящий материал. Тем не менее, можно сформулировать некоторые руководящие правила при выборе материалов для пар трения скольжения.
1. Сочетать твердый материал с мягким, имеющим температуру рекристаллизации ниже средней температуры поверхности трения. Такая пара металлов хорошо противостоит заеданию и характеризуется высокой надежностью. Хорошие результаты дают пары хром-резина при смазывании минеральным маслом и водой и хром-бронза при пластичных смазочных материалах.
2. Сочетать твердый металл с твердым (сочетание пар из азотированной, хромированной и закаленных сталей). Такие пары трения обладают высокой износостойкостью вследствие малого взаимного внедрения их поверхностей. Нанесение приработочных покрытий повышает надежность в наиболее опасный период работы – во время приработки. Применение этих пар ограничивается скоростями скольжения. Высокая точность изготовления и сборки, значительная жесткость конструкции, тщательная приработка, улучшение условий смазки значительно расширяют область применения пар трения из твердых материалов.
3. Избегать сочетаний мягкого материала по мягкому, а также пар из одноименных материалов (незакаленная сталь по незакаленной стали, алюминиевый сплав по никелевому сплаву, медный сплав по алюминиевому, хром по хрому, хром по алюминию, никель по никелю, пластмасса по пластмассе), за исключением политетрафторэтилена и полиэтилена, каждый друг по другу. Подобные пары имеют низкую износостойкость и ненадежны в работе. При незначительных перегрузках в парах образуются очаги схватывания, и происходит глубинное вырывание материалов с взаимным их налипанием на поверхность трения.
4. Применять в труднодоступных для смазывания конструкциях пористые спеченные материалы и антифрикционные сплавы.
5. Применять в качестве фрикционных и антифрикционных материалов пластические массы. В ряде случаев они повышают надежность и срок службы узла трения, в других случаях снижают массу конструкции и расход дефицитных цветных металлов, уменьшают вибрации и улучшают акустические свойства машин.
6. Стремиться путем выбора материалов пары трения, смазочных материалов или присадок к ним создавать при работе пары условия реализации режима ИП при трении.
7. При выборе материалов учитывать возможность наводороживания трущихся поверхностей при эксплуатации, что резко снижает износостойкость и надежность работы узла трения. Применять материалы, трудно поддающиеся наводороживанию.
8. Стальные детали узлов трения при окончательной доводке их поверхности подвергать финишной антифрикционной безабразивной обработке.
Замена в узлах машин трения скольжения трением качения
Такая замена во многих случаях целесообразна с точки зрения повышения надежности работы деталей и экономичности машин.
Каждому виду опор (скольжения и качения) свойственны как положительные, так и отрицательные качества. Подшипники качения имеют следующие преимущества:
1. Уменьшаются потери на трение по сравнению с потерями у подшипников скольжения, работающих при граничной смазке или при жидкостной смазке. Применение подшипников качения, как правило, повышает КПД машины. Коэффициент трения подшипника качения сравнительно мало изменяется в большом диапазоне нагрузок и окружных скоростей.
2. Экономится большое количество цветных металлов – меди, олова, свинца, расходуемых на изготовление вкладышей подшипников скольжения.
3. Уменьшается расход смазочных материалов.
4. Отпадает надобность в принудительном охлаждении.
5. Упрощается уход.
6. У валов при правильно назначенных посадках отсутствует износ шеек, что исключает необходимость ремонта последних.
7. Шарико- и роликоподшипники стандартизованы, что упрощает конструирование подшипникового узла. Поступление подшипников качения в сборочный цех в виде собранного комплекта ускоряет изготовление и монтаж машины.
8. Применение подшипников качения уменьшает стоимость машины.
Перечисленные преимущества подшипников качения обусловили их широкое распространение. Диапазон их размеров широк: от 0,25 мм (по диаметру) в приборах и свыше 1000 мм в четырехрядных конических подшипниках валков прокатных станов.
Недостатками подшипников качения являются:
1. Недостаточная надежность при высоких окружных скоростях и динамических нагрузках.
2. Иногда существенным недостатком являются большие диаметральные размеры при меньшей длине, чем у подшипников скольжения.
3. Неудовлетворительная работа в условиях вибрационной нагрузки, а также при качательном движении с малыми углами поворота.
4. Большой шум при работе.
5. Недостаточная коррозионная и тепловая стойкость.
6. Значительно меньшая грузоподъемность и долговечность упорных подшипников качения, чем подшипников скольжения.
7. Недостаточная пригодность в случаях, когда для удобства монтажа либо по особенностям конструкции вала требуются разъемные опоры.
Дата добавления: 2018-04-15; просмотров: 432; Мы поможем в написании вашей работы! |
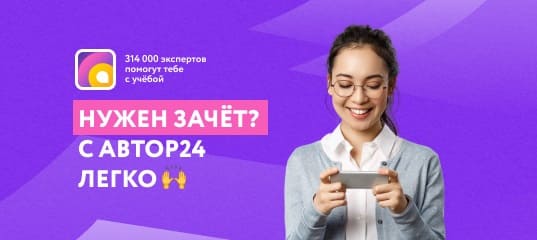
Мы поможем в написании ваших работ!