Конструкция сочлененных самосвалов
Лабораторная работа № 2
Тема: Транспортные средства – тракторы, автомобили,
Тягачи
Введение:
Одним из основных этапов технологического процесса современного индустриального городского строительства является доставка к месту производства работ строительных материалов, изделий, конструкций и оборудования, осуществляемая транспортными машинами — грузовыми автомобилями и колесными тягачами, прицепными и полуприцепными специализированными или общего назначения транспортными средствами. Выбор типа транспортных средств определяется характером и количеством перемещаемых грузов, дальностью перевозок, состоянием дорог и временем, отведенным на их доставку. Кроме грузоперевозок автомобили, тракторы и тягачи используют как тяговые средства прицепных и полуприцепных строительных машин, а также в качестве унифицированной базы навесных строительных машин — экскаваторов, кранов, погрузчиков, бульдозеров, скреперов, бурильных и сваебойных установок и т. п. Отдельные узлы автомобилей, тракторов и тягачей используют в строительных машинах
Задание 1: Изучите классификацию тракторов и автомобилей.
Грузовые автомобили обладают сравнительно большой скоростью передвижения (до 80 км/ч), маневренностью, малым радиусом поворота, могут преодолевать довольно крутые подъемы и спуски, приспособлены для работы с прицепами, полуприцепами общего и специального назначения, а также могут быть оснащены погрузочно-разгрузочными механизмами. Различают автомобили общего назначения и специализированные. К автомобилям общего назначения относят машины с кузовом в виде открытой сверху платформы с бортами, бортовые автомобили повышенной проходимости со всеми ведущими колесами и увеличенным количеством осей, а также автомобили-тягачи, оборудованные сцепными устройствами для работы с прицепами, полуприцепами и роспусками.
|
|
Грузовые автомобили массового производства имеют единую конструктивную схему и состоят из трех основных частей (рис. 2.1, а, б): двигателя 7, шасси 3 и кузова 2 для груза. Кузова бортовых авто-мобилей представляют собой деревянную или металлическую платформу с откидными бортами и предназначаются для перевозки преимущественно штучных грузов. Вместе с одноосными прицепами бортовые автомобили применяют для перевозки длинномерных грузов — труб, свай, бревен, проката металлов и т. п. Грузоподъемность отечественных бортовых автомобилей 0,8... 14 т.
На базе стандартных шасси с укороченными базой и задним свесом рамы промышленностью выпускаются автомобильные тягачи седельного типа (рис. 2.1, в), работающие в сцепе с одно- и двухосными полуприцепами. На раме шасси такого тягача крепится опорная плита и седельно-сцепное устройство 4, воспринимающее силу тяжести груженого полуприцепа и служащее для пере-дачи ему тягового усилия, развиваемого автомобилем. Применение автомобильных тягачей седельного типа с полуприцепами позволяет лучше использовать мощность двигателя и значительно увеличить грузоподъемность автомобиля. Седельные автотягачи способны работать с гружеными полуприцепами массой 4...25 т.
|
|
На грузовых автомобилях применяют двигатели внутреннего сгорания — карбюраторные и дизели (наиболее распространены). Шасси состоит из гидромеханической или механической трансмиссии (силовой передачи), ходовой части и механизмов управления машиной. Мощность двигателя автомобилей 50... 220 кВт.
Тракторы применяют для транспортирования на прицепах строительных грузов и оборудования по грунтовым и временным дорогам, вне дорог, в стесненных условиях, а также передвижения и работы навесных и прицепных строительных машин. Они делятся на сельскохозяйственные, промышленные и специальные (для горных, подводных, подземных и других специальных работ). По конструкции ходового оборудования различают гусеничные и колесные тракторы. Главным параметром тракторов является максимальное тяговое усилие на крюке, по величине которого (в тс) их относят к различным классам тяги. В строительстве используют тракторы сельскохозяйственного типа классов тяги 1,4; 2; 3; 4; 5; 6; 9; 15 и 25 (по сельскохозяйственной классификации) и промышленного типа классов тяги 10; 15; 25; 35; 50 и 75 (по промышленной классификации). Тракторы промышленного типа по своим конструктивно-эксплуатационным параметрам наиболее полно соответствуют требованиям, предъявляемым к тяговым средствам и базовым машинам в строительстве. Класс тяги по промышленной классификации означает максимальную силу тяги без догрузки навесным оборудованием на передаче со скоростью 2,5...3 км/ч для гусеничных и
|
|
3...3,5 км/ч для колесных тракторов, обеспечивающей эффективную работу с землеройным оборудованием.
Пневмоколесные тракторы обладают сравнительно большими (до 40 км/ч) скоростями передвижения, высокой мобильностью и маневренностью. Их используют как транспортные машины и как базу для установки различного навесного оборудования (погрузочного, кранового, бульдозерного и землеройного), применяемого при производстве землеройных и строительно-монтажных работ небольших объемов на рассредоточенных объектах. Наиболее эффективно пневмоколесные тракторы используют на дорогах с твердым покрытием. Сравнительно высокое удельное давление на грунт (0,2...0,4 МПа) снижает проходимость машин. Мощность их двигателей 47...220 кВт.
|
|
Гусеничные тракторы характеризуются значительным тяговым усилием на крюке (не менее 30 кН), надежным сцеплением гусеничного хода с грунтом, малым удельным давлением на грунт (0,02...0,06 МПа) и высокой проходимостью. Их скорость не превышает 12 км/ч. Мощность двигателей гусеничных тракторов 55...600 кВт.
Основные узлы пневмоколесных и гусеничных тракторов — двигатель, силовая передача (трансмиссия), остов (рама), ходовое устройство, система управления, вспомогательное и рабочее оборудование. Рабочее оборудование предназначено для использования полезной мощности двигателя при работе трактора с навесными и механическими, трансмиссиями.
Расположение двигателя может быть передним (рис. 2.3, а), средним и задним (рис. 2.3, б). Наибольшее распространение получили гусеничные тракторы с передним расположением двигателя и механическими трансмиссиями. Трансмиссия служит для передачи крутящего момента от вала двигателя к ведущим звездочкам гусеничных лент (гусениц), плавного трогания и остановки машины, изменения тягового усилия трактора в соответствии с условиями движения, изменения скорости и направления его движения, а также привода рабочего оборудования.
Пневмоколесные тракторы оснащаются дизелями, механическими и гидромеханическими трансмиссиями. По типу системы поворота различают тракторы с передними управляемыми колесами (рис. 2.5, а), со всеми управляемыми колесами и с шарнирно сочлененной рамой (рис, 2.5, б). Наиболее распространены пневмоколесные тракторы с дизелями, механической трансмиссией и передними управляемыми колесами.
Размещение, назначение и устройство основных узлов пневмоколесного трактора с механической трансмиссией и передними управляемыми колесами примерно такие же (за исключением рабочего оборудования), как у рассмотренного выше автомобиля. Пневмоколесные тракторы с шарнирно сочлененной («ломающейся» в плане) рамой обладают высокой маневренностью, малым радиусом поворота и применяются для работы в стесненных условиях. Рама такого трактора (см. рис. 2.5, в) состоит из двух полурам — передней 1 и задней 2, соединенных между собой универсальным шарниром 3. Маневрирование машины производится путем поворота передней полурамы относительно задней вокруг вертикальной оси шарнира на угол до 40° в плане от продольной оси машины с помощью двух гидроцилиндров двустороннего действия. Каждая из полурам опирается на ведущий мост с управляемыми колесами. Трансмиссия тракторов с шарнирно сочлененной рамой — механическая и гидромеханическая.
Задание 2: Представьте кинематическую схему трактора и автомобиля.
Справка из википедии:
«Принципиальная кинематическая схема — это такая схема, на которой показана последовательность передачи движения от двигателя через передаточный механизм к рабочим органам машины (например, шпинделю станка, режущему инструменту, ведущим колёсам автомобиля и др.) и их взаимосвязь.
На кинематических схемах изображают только те элементы машины или механизма, которые принимают участие в передаче движения (зубчатые колёса, ходовые винты, валы, шкивы, муфты и др.) без соблюдения размеров и пропорций.»
Трансмиссия грузового автомобиля (рис. 2.2) передает крутящий момент от вала двигателя 1 к ведущим колесам 8, а также приводит в действие различное оборудование, установленное на автомобиле. В него входят:
• постоянно замкнутая дисковая фрикционная муфта (сцепление) 2 для плавного соединения и быстрого разъединения работающего двигателя с трансмиссией;
• ступенчатая коробка передач 3 с переменным передаточным числом для изменения величины крутящего момента, подводимого к ведущим колесам в зависимости от условий движения, обеспечения движения автомобиля задним ходом и разъединения работающего двигателя с трансмиссией при длительных остановках машины;
• карданный вал 4, передающий крутящий момент под меняющимся углом от коробки передач к подрессоренному заднему мосту;
• главная передача 5 (одинарная или двойная), передающая движение под прямым углом к полуосям 7 и увеличивающая тяговую силу на ведущих колесах;
• дифференциал 6 для распределения крутящего момента между ведущими колесами, обеспечивающий их вращение с различными угловыми скоростями при движении автомобиля на поворотах и по неровной поверхности;
• полуоси (валы) 7, передающие крутящий момент к закрепленным на них ведущим колесам 8.
Главную передачу, дифференциал и полуоси, заключенные в кожух, называют ведущим мостом.
Составными частями дифференциала (рис. 2.2, г) являются полуосевые шестерни 15, закрепленные на полуосях 7, сателлиты 13 и коробка 14, на которой закреплена ведомая шестерня главной передачи 5. При прямолинейном движении автомобиля по ровной дороге полуоси 7 с шестернями 15 вращаются с одинаковой скоростью, равной скорости вращения коробки 14, а сателлиты остаются неподвижными относительно своих осей. Если одно из ведущих колес будет испытывать большее сопротивление дороги, сателлиты начнут перекатываться по замедлившей свое вращение полуосевой шестерне, при этом вторая полуосевая шестерня за счет вращения сателлитов относительно своих осей начнет вращаться быстрее.
Трансмиссия гусеничного трактора:
В состав механической трансмиссии (рис. 2.4) входят: фрикционная дисковая муфта сцепления 2, коробка передач 3, соединительные валы 5, главная передача 6, механизм поворота с тормозами и бортовые редукторы 9, соединенные с ведущими звездочками 10 гусениц 4. Муфта сцепления и коробка передач выполняют те же функции, что и одноименные узлы автомобиля. Главная передача (аналогичная автомобильной) и бортовые редукторы увеличивают крутящий момент, подводимый от двигателя 1 к ведущим звездочкам гусениц.
На поперечном валу трансмиссии между главной передачей и бортовыми редукторами установлен фрикционный или планетарный механизм поворота, предназначенный для изменения направления движения трактора. Наиболее распространенный фрикционный механизм поворота (рис. 2.4, а) выполнен в виде двух постоянно замкнутых многодисковых фрикционных муфт (бортовых фрикционов) 7. При обоих включенных фрикционах ведущие звездочки 10 гусениц вращаются синхронно, что обеспечивает прямолинейное движение машины. Частичным или полным включением одного из фрикционов уменьшают скорость движения соответствующей гусеницы, в результате чего происходит поворот трактора в сторону отстающей гусеницы. На наружные (ведомые) барабаны фрикционов действуют ленточные тормоза 8, осуществляющие торможение отключенной от трансмиссии гусеницы для более крутого поворота трактора, а также торможение обеих гусениц при движении трактора на уклонах и затормаживание его на месте.
Прямолинейное движение трактора с планетарным механизмом поворота (рис. 2.4, 6) обеспечивается при затянутых тормозах 13 до полной остановки солнечных шестерен 12. При этом водила 14 и вал 11 будут вращаться с одинаковой скоростью. Для поворота трактора необходимо отпустить правый или левый тормоза 13, в результате чего один из планетарных механизмов полностью или частично прекратит передавать крутящий момент ведущей звездочке 10 гусеницы. Включением тормоза 8 достигается уменьшение радиуса поворота трактора. При одновременном включении обоих тормозов 8 обеспечивается снижение скорости или полная остановка машины. Планетарный механизм поворота одновременно выполняет функции редуктора.
Механические трансмиссии серийных гусеничных тракторов, используемых в качестве базы строительных машин, передвигающихся при работе на пониженных (до 1 км/ч) рабочих скоростях, дооборудуются гидромеханическими ходоуменьшителями, состоящими из аксиально-поршневого гидромотора и зубчатого редуктора. Гидромеханические ходоуменыиители позволяют плавно (бесступенчато) регулировать скорость движения машины в зависимости от меняющейся внешней нагрузки.
В гидромеханической трансмиссии используется механическая ступенчатая коробка передач и гидротрансформатор, заменяющий муфту сцепления. Гидротрансформатор обеспечивает автоматическое бесступенчатое изменение крутящего момента, а также скорости движения трактора в пределах каждой передачи коробки в зависимости от общего сопротивления движению машины. Это позволяет снизить число переключений передач, повысить долговечность двигателя и трансмиссии, уменьшить вероятность остановки двигателя при резком увеличении нагрузки.
В электромеханической трансмиссии крутящий момент дизеля передается через постоянно замкнутую фрикционную муфту, карданный вал и ускоряющий редуктор силовому генератору, питающему постоянным током тяговый электродвигатель. Крутящий момент якоря тягового электродвигателя передается главной конической передачей планетарным механизмам поворота, бортовым редукторам и ведущим звездочкам гусеничных лент. Электромеханическая трансмиссия по сравнению с механической и гидромеханической имеет простую кинематику (отсутствует ступенчатая коробка передач) и обеспечивает высокие тяговые качества трактора за счет плавного бесступенчатого регулирования скоростей движения машины в зависимости от нагрузки. Основные недостатки такой трансмиссии — сложность конструкции, сравнительно большие габаритные размеры и масса, высокая стоимость.
Задание 3: Приведите формулы для определения главного параметра трактора, автомобиля и тягача.
Тяговые расчеты. При движении автомобиля, трактора или тягача возникает общее сопротивление движению машины (Н):
W = Wo + Wi,
где Wo — основное сопротивление движению на прямом горизонтальном участке пути, представляющее собой сумму сопротивлений качению колес (гусениц) и трения в трансмиссии, Н; Wi — дополнительное сопротивление движению на подъеме (со знаком плюс) или на уклоне (со знаком минус), Н.
Такие виды сопротивлений, как сопротивление воздуха, сопротивление при движении на криволинейных участках пути и сопротивление ускорения при тяговых расчетах средств горизонтального транспорта, используемых на строительстве, обычно не учитываются. При выполнении тяговых расчетов, как правило, пользуются величинами удельных сопротивлений движению w. Значения основного удельного сопротивления движению автомобилей, тракторов, тягачей и п
рицепов приводятся в справочниках. Значение дополни-тельного удельного сопротивления , на подъеме принимают равным величине уклона пути i (в тысячных долях).Полное сопротивление движению автомобиля, перевозящего груз (Н):
где Ga и Gr — соответственно вес автомобиля и груза, Н.
Для тракторов и пневмоколесных тягачей, буксирующих прицепы:
где Gт— собственный вес трактора или тягача, Н; Gn — вес прицепа с грузом, Н; n — число прицепов; w'0 — основное удельное сопротивление движению трактора или тягача; w” — то же, прицепа.
Для движения автомобиля, трактора или тягача необходимы следующие условия:
где Fт — сила тяги на ведущих колесах (гусеницах), возникающая в результате работы двигателя и взаимодействия колес (гусениц) с дорогой, Н; Ссц — сцепной вес, т. е. вес машины с грузом, приходящийся на ведущие колеса (гусеницы), Н; Ф — коэффициент сцепления колес (гусениц) с поверхностью дороги, равный 0,3...0,6 для пневмоколесных и 0,5...0,9 для гусеничных машин. Если последнее условие не соблюдается, то возникает пробуксовывание колес (гусениц).
Задание 4: Изучите виды ходового оборудования применяемого для передвижных строительных машин, особенности, область применения, преимущества и недостатки этого оборудования.
Ходовое оборудование предназначено для передачи на опорную поверхность (грунт, дорожное покрытие, рельсы) веса машины и внешних нагрузок, действующих на нее при работе, передвижения машины на рабочих (при выполнении рабочего процесса) и транспортных скоростях, а также стопорения машины при работе. Ходовое оборудование включает гусеничное, пневмоколесное, гусенично-колесное или рельсовое ходовое устройство и механизмы для его привода. Каждое ходовое устройство состоит из движителя и подвески. Движитель находится в постоянном контакте (сцеплении) с опорной поверхностью и обеспечивает поступательное движение машины. Подвеска соединяет движитель с опорной рамой машины и выполняется жесткой у тихоходных машин, полужесткой и упругой — у быстроходных. Самоходные строительные машины монтируют на базе серийных грузовых автомобилей, колесных и гусеничных тракторов, пневмоколесных тягачей и специальных гусеничных и пневмоколесных шасси с приводом от общей трансмиссии машины или от индивидуальных электрических и гидравлических двигателей. Специальные шасси современных строительных машин унифицированы.
Пневмоколесное ходовое оборудование обеспечивает машинам маневренность, мобильность, высокие скорости (до 60...70 км/ч) и плавность передвижения. Пневмоколесный движитель состоит из ведомых и ведущих (приводных) колес, вращательное движение которых преобразуется в поступательное движение машины. У большинства строительных машин все колеса — ведущие. Количество колес зависит от допускаемой на каждое колесо нагрузки, условий и режимов работы машины, требуемых скоростей ее движения. Ходовые устройства строительных машин имеют обычно от 4 до 8 одинаковых взаимозаменяемых колес. Основным элементом каждого пневмоколеса является накачанная воздухом упругая резиновая шина, смонтированная на о боде. Шины могут быть камерными и бескамерными. В камерных шинах (рис. 1.39, а) воздух накачивается в камеру 3, в бескамерных (рис. 1.39 б) — между герметично соединенными покрышкой 2 и ободом 4.
Взаимодействующий с дорогой протектор 1 шин может иметь мелкий рисунок для дорог с твердым покрытием и крупный — для грунтовых дорог (рис. 1.39, в). Для повышения проходимости машин, работающих и передвигающихся по грунтам с пониженной несущей способностью, применяют шины с большой опорной поверхностью — широкопрофильные и арочные (рис. 1.39, г). Такие шины имеют высокие грунтозацепы, их удельное давление на грунт не превышает 0,05...0,14 МПа. Многие машины оборудуют устройствами для регулирования давления в шинах из кабины машиниста (каждой в отдельности или всех вместе) в зависимости от условий работы и передвижения машины. С уменьшением давления в шинах до 0,05...0,08 МПа увеличивается площадь контакта их с грунтом и соответственно уменьшается удельное давление на грунт и повышается проходимость машины; наряду с этим растут сопротивление движению машины и интенсивность износа шин. При движении в хороших дорожных условиях давление в шинах повышают до 0,5...0,7 МПа.
На пневмоколеса опираются приводные (ведущие) и неприводные мосты, соединяемые с рамой машины жесткой, балансирной или упругой подвеской. Общее количество мостов обычно не превышает трех. Наиболее нагруженные мосты имеют сдвоенные пневмоколеса. Направление движения машины меняется путем поворота управляемых колес, поворотом мостов с колесами в плане, обеспечением различной скорости движения правых и левых колес и т.п. Привод ведущих колес может быть общим от механической трансмиссии машины, от самостоятельного ходового электродвигателя или низкомоментного гидромотора через систему передач и валов, а также индивидуальным от приводных ступичных блоков, встроенных в ступицу каждого колеса (мотор-колеса) и включающих электродвигатель или гидромотор, планетарный редуктор и тормоз. Скорость машины с мотор-колесами можно плавно регулировать в широком диапазоне в зависимости от дорожных условий и действующих на нее нагрузок. Каждое мотор-колесо может быть поворотным, за счет чего улучшается маневренность машины. Для разгрузки ходовых устройств строительных экскаваторов, стреловых самоходных кранов, бурильных и других машин при работе применяют выносные опоры-аутригеры. Масса пневмоколесных ходовых устройств составляет 10... 12% общей массы машины.
Гусеничное ходовое оборудование характеризуется хорошим сцеплением с грунтом, высокой тяговой способностью, большой опорной поверхностью, низким удельным давлением на грунт (0,04...0,1 МПа), определяющими в комплексе его высокую проходимость, и применяется в машинах, передвигающихся в условиях плохих дорог и бездорожья. Недостатки гусеничного оборудования — тихоходность (не более 10...12 км/ч), сравнительно большая масса (30...40% от массы машины), сложность конструкции. Гусеничные машины обычно обслуживают объекты с большими объемами работ. Для транспортирования их с одного объекта на другой применяют пневмоколесные прицепы-тяжеловозы (трайлеры). В городском строительстве используют машины с двухгусеничным ходовым оборудованием. Гусеничный движитель (рис. 1.40, а) состоит из гусеничной ленты (цепи 2 в виде шарнирно соединенных между собой звеньев (пластин, траков), огибающей приводное 1 и направляющее (натяжное) 9 колеса. Последние установлены на концах рамы 7. Нагрузки от машины передаются на нижнюю ветвь гусеничной ленты через движущиеся по ней опорные катки 6. Холостую верхнюю ветвь гусеницы поддерживают и предохраняют от провисания ролики 3. Натяжение гусеничной ленты регулируют винтовым натяжным устройством 8, перемещающим натяжное колесо 9. Для машин, работающих и передвигающихся на слабых, переувлажненных и заболоченных грунтах, применяют уширенно-удлиненные движители с увеличенной опорной поверхностью гусениц и удельным давлением на грунт 0,02...0,03 МПа.
По приспособляемости к неровностям опорной поверхности различают мягкие и полужесткие движители. У жестких движителей опорные катки соединяются непосредственно с рамой (см. рис. 1.40, а), у мягких — через пружины и рессоры. При полужесткой подвеске жесткие движители крепятся к раме машины шарнирно одним концом и через упругие элементы — другим. Скорость движения машин с жесткой подвеской 5...8 км/ч.
Рамы жестких движителей строительных экскаваторов, стреловых самоходных кранов, погрузчиков и других машин жестко соединены между собой поперечными балками, на которые опирается ходовая рама 5, несущая опорно-поворотный круг 4 и воспринимающая вес и внешние нагрузки машины. Привод ведущего колеса каждой гусеницы может быть общим (рис. 1.40, б, в) от электродвигателя или двигателя внутреннего сгорания через систему передач, а также раздельным (индивидуальным) — от электродвигателя (рис. 1.40, г) или низкомоментного гидромотора через редуктор. Автоматические и управляемые тормоза привода гусениц обеспечивают торможение, остановку и маневрирование машины. Движение по кривой достигается притормаживанием одной из гусениц, а разворот — движением гусениц в противоположные стороны или полным торможением одной из гусениц.
Рельсовое ходовое оборудование имеет башенные, козловые, мостовые и специальные стреловые самоходные краны, элсктротали — тельферы, сваебойные .установки и др. (рис. 1.41). Оно характеризуется простотой конструкции, небольшими сопротивлениями передвижению, а также малыми маневренностью и скоростью передвижения. Основными элементами рельсового ходового устройства являются размещаемые на рельсах стальные колеса с гладким ободом с одной или двумя ребордами. Привод ведущих колес может быть общим от электродвигателя или двигателя внутреннего сгорания через систему валов и передач и индивидуального электродвигателя через редуктор. Приводы оборудуют управляемыми и автоматическими тормозами.
Одно или несколько колес с общей рамой, двигателем, редуктором и тормозом образуют приводную ходовую тележку. Количество колес в тележке определяется действующей нагрузкой. Приводные и неприводные (без привода) ходовые тележки кранов шарнирно соединяются с опорной рамой и оборудуются противоугонными клещевыми захватами.
Многие строительные машины (стреловые краны, строительные экскаваторы, погрузчики и др.) имеют поворотное в плане рабочее оборудование, установленное, как правило, на поворотной платформе. Платформа опирается на раму ходового устройства через опорно-поворотный круг (ОПК) и поворачивается в плане поворотным механизмом. Широко применяются унифицированные роликовые ОПК. Их составными частями являются (рис. 1.42, а): наружные подвижные кольца 2 и 3, скрепленные болтами, ролики 1, используемые в качестве тел качения, и внутреннее неподвижное кольцо 5 с зубчатым венцом 6. Кольца 2 и 3 жестко крепятся к поворотной платформе, а кольцо 5 — к раме ходового устройства. Расположенные между кольцами ролики имеют взаимно перпендикулярные оси (рис. 1.42, б) и наклонены к вертикали под углом 30 или 60°, в результате чего половина их, катящаяся по дорожкам В, воспринимает опорные нагрузки, а другая половина, катящаяся по дорожкам Г, — отрывные, удерживая поворотную платформу от опрокидывания.
Роликовые ОПК выпускают одно- и двухрядными, с внутренним и наружным зубчатым венцом. В постоянном зацеплении с зубчатым венцом ОПК находится ведущая (обегающая) шестерня поворотного механизма, которая обегает венец, поворачивая платформу. Поворотный механизм располагается на поворотной платформе. У машин с электрическим, гидравлическим и комбинированным приводом поворотный механизм включает зубчатый или червячный редуктор с обегающей шестерней на выходном валу, индивидуальный приводной электродвигатель или низкомоментный гидромотор и тормозное устройство. При использовании высокомоментного гидромотора редуктор отсутствует, а обегающая шестерня крепится непосредственно на валу гидромотора. У машин с механическим приводом поворотный механизм (редуктор с обегающей шестерней и тормозом) приводится в действие от общей трансмиссии машины. Тормоза поворотных механизмов могут быть управляемыми и автоматическими.
Задание 5: Представьте, какие типы систем управления контроля и защиты применяют в строительных машинах. Укажите область их применения, преимущества и недостатки.
Системы управления строительных машин по конструктивным признакам разделяют на механические, гидравлические, пневматические, электрические и смешанные (комбинированные).
Механическая система обеспечивает связь руки или ноги машиниста с муфтами и тормозами через рычаги и тяги. Такая конструкция надежна в эксплуатации и имеет высокую чувствительность управления. Основные ее недостатки — необходимость приложения значительных мускульных усилий машиниста к рычагам и педалям, быстрая утомляемость машиниста, ведущая к снижению производительности машины, необходимость частых смазок и регулировок быстроизнашивающихся шарнирных соединений тяг и рычагов. Обычно механическая система используется как вспомогательная — для управления механизмами, не принимающими участия в выполнении рабочего процесса.
Поворот колес машины в этом случае осуществляется с помощью рулевого управления посредством приложения усилия машиниста к рулевому колесу 4 и через механическую передачу 3 (цилиндрическую или червячную пару), сектор 2, взаимодействующий с винтовым устройством, перемещает поперечные тяги 1, соединенные с управляемыми колесами (рис. 1.43, а). Для облегчения труда машиниста в передаточный механизм рулевого управления включают усилители в виде гидравлического или пневматического цилиндра с поршнем. Действие усилителя основано на том, что при повороте рулевого колеса 4 и наличии нагрузки на тяге рулевой трапеции 9 червяк 6 перемещается в осевом направлении и золотник распределителя 5 открывает доступ жидкости или воздуху в цилиндр усилителя 7, шток которого, взаимодействуя с рейкой 8, передает усилие на тягу 9, соединенную с рулевой трапецией (рис. 1.43, б).
В гидравлической системе управления рычаги полностью или частично заменены исполнительными гидроцилиндрами одно- и двустороннего действия, создающими необходимое усилие включения муфт, тормозов и других механизмов. Различают насосную и безнасосную системы управления. В насосной системе рабочая жидкость подается под давлением в исполнительный гидроцилиндр от насоса через распределитель, которым управляет машинист.
Вбезнасосной системе (рис. 1.44) давление рабочей жидкости в исполнительном гидроцилиндре одностороннего действия 2 создается перемещением поршня гидроцилиндра-преобразователя (датчика) 5, на который через рычаг или педаль 3 воздействует машинист. При снятии усилия с педали поршень датчика возвращается в исходное положение пружиной 4, поршень исполнительного гидроцилиндра—пружиной 1. Безнасосная система проста по конструкции, надежна в эксплуатации, но так как для ее привода требуется мускульная сила, имеет ограниченное применение.Преимущественное распространение получила насосная система управления.
Пневматическая система управления отличается от гидравлической насосной тем, что в ней вместо жидкости используется сжатый до 0,7...0,8 МПа в компрессоре воздух. Исполнительными органами такой безнасосного управления системы (рис. 1.45) являются пневмоцилиндры 4 и пневмокамеры 5 одностороннего действия, подвижные элементы которых — поршень или диафрагма со штоком — передают усилие включаемому механизму. Возврат штока в исходное положение обеспечивается пружиной при снятом давлении. Работой пневмоцилиндров и камер управляют с помощью регулируемых и нерегулируемых пневмоаппаратов 3. Нерегулируемый крановый пневмоаппарат соединяет ресивер 2 компрессора 1 с рабочей полостью пневмоцилиндра (камеры) без изменения давления сжатого воздуха. Регулируемый пневмоаппарат позволяет изменять давление воздуха в исполнительном органе, обеспечивая повышенную плавность включения механизма. По сравнению с гидравлической пневматическая система управления обеспечивает более высокую плавность включения. Основные ее недостатки — сравнительно большие размеры исполнительных органов из-за низкого давления в системе и возможность замерзания конденсата, содержащегося в сжатом воздухе.
Электрическая система управления применяется в машинах с индивидуальным электрическим приводом механизмов и обеспечивает пуск и останов электродвигателей, регулирование частоты и вращения, реверсирование, безопасную работу и т.п. В состав такой системы входят магнитные пускатели, контроллеры, реле различных типов, автоматические выключатели, кнопки управления «Пуск» и «Стоп», блокирующие устройства, тормозные электромагниты и т.п. Электрические системы управления надежны, просты и удобны в эксплуатации, обеспечивают дистанционное управление механизмами и всей машиной в целом, создают возможность автоматизации работы машин.
С целью частичной или полной автоматизации управления машинами применяют комбинированные системы — гидропневматические, гидроэлектрические, гидропневмоэлектрические и т. п.
Системы защиты. При проектировании строительных машин и механизмов необходимо предусмотреть применение защитных устройств или устройств, исключающих возможность контакта человека с опасной зоной. Такого рода устройствами являются средства защиты работающих, используемые для предотвращения или уменьшения воздействия на работающих опасных и вредных производственных факторов. Средства защиты можно классифицировать на две большие группы: а) коллективные, обеспечивающие безопасность строительных машин и оборудования; б) индивидуальные, обеспечивающие безопасность производственных процессов.
Все применяющиеся защитные устройства в строительных машинах можно разделить на следующие основные группы: оградительные, предохранительные, блокирующие, сигнализирующие, а также системы дистанционного управления строительными машинами и специальные устройства.
Общими требованиями к средствам защиты являются: максимальное снижение опасностей и вредностей на рабочих местах; учет индивидуальных особенностей оборудования, инструмента, приспособлений или технологических процессов, для которых они предназначены: надежность, прочность, удобство обслуживания машин и механизмов в целом, включая средства защиты.
Оградительные устройства — средства защиты, препятствующие попаданию человека в опасную зону. Оградительные устройства применяют для изоляции систем привода машин и агрегатов, ограждения токоведущих систем; ограждаются также рабочие зоны, расположенные на высоте. Конструктивные решения оградительных устройств разнообразны. Они зависят от вида строительной машины, расположения человека в рабочей зоне, специфики опасности и вредности. Оградительные устройства делят на три основные группы: стационарные (несъемные, подвижные (съемные) и переносные.
Стационарные ограждения лишь периодически демонтируют для выполнения вспомогательных операций (смены рабочего инструмента, смазки, проведения контрольных измерений и т. п.). Такое ограждение может быть полным, когда локализуется опасная зона вместе с самой машиной, или частичным, когда изолируется только опасная зона машины. Примерами полного ограждения являются ограждения распределительных устройств электрооборудования, корпуса электродвигателя и т. д.
Подвижное (съемное) ограждение представляет собой устройство, сблокированное с рабочим органом машины или механизма, вследствие чего оно закрывает доступ в рабочую зону при наступлении опасного момента. В остальное время доступ в указанную зону открыт.
Переносные ограждения являются временными. Их используют при ремонтных и наладочных работах для защиты от случайных прикосновений к токоведущим частям, а также от механических травм и ожогов. Кроме того, их применяют на постоянных рабочих местах сварщиков для защиты окружающих от воздействия электрической дуги и ультрафиолетовых излучений.
В качестве материала ограждений используют металлы, пластмассы, дерево. Чтобы выдерживать нагрузки от случайных воздействий, ограждения должны быть достаточно прочными и хорошо крепиться к фундаменту или частям машины.
Приборы и устройства безопасности. Предохранительные защитные средства предназначены для автоматического отключения агрегатов и машин при отклонении какого-либо параметра, характеризующего режим работы оборудования, за пределы допустимых значений. Таким образом, необходимым условием безопасной эксплуатации грудоподъемных кранов и других строительных машин является оснащение их устройствами и приспособлениями, ограничивающими возможность возникновения опасных ситуаций.
Приборы и устройства безопасности по их назначению можно подразделять на следующие: 1) ограничители движения (высоты подъема груза, передвижения крана, вращения крана, вылета стрелы, вылета грузовой каретки); 2) устройство, обеспечивающее устойчивость машин (ограничители грузоподъемности и грузового момента, противоугонные захваты, выносные опоры); 3) приборы, сигнализирующие состояние устойчивости (анемометры, указатели вылета стрелы, указатели кранов); 4) приборы освещения и сигнализации (указатель приближения к ЛЭП, приборы звуковой сигнализации).
Задание 6: Изучите принципиальные схемы панелевозов, фермовозов, цементовозов и
других специальных транспортных средств различного вида.
Такие транспортные средства приспособлены для перевозки одного или нескольких однородных грузов, отличающихся специфическими условиями их транспортировки, и оборудованы различными приспособлениями и устройствами, которые обеспечивают сохранность и качество доставляемых на строительные объекты грузов и комплексную механизацию погрузочно-разгрузочных работ. Применение специализированного транспорта способствует повышению эффективности и качества строительства, позволяет снизить себестоимость перевозок, свести к минимуму потери строительных материалов и полуфабрикатов, а такте повреждение строительных изделий и конструкций, которые весьма значительны при использовании транспортных средств общего назначения. В настоящее время без применения специализированного транспорта практически невозможна доставка многих грузов на объекты строительства. Большинство специализированных транспортных средств представляют собой сменные прицепы и полуприцепы к грузовым автомобилям, пневмоколесным тягачам и тракторам, что позволяет более эффективно использовать базовую машину.
В условиях городского строительства широко применяется автомобильный специализированный транспорт. Современные специализированные транспортные средства для строительства выпускаются в соответствии с утвержденным Госстроем «Типажом специализированных автотранспортных средств для строительства» и предназначены для перевозки грунта, сыпучих и глыбообразных грузов (самосвалы), жидких и полужидких (битумовозы, известко- возы, бетоно- и растворовозы), порошкообразных (цементовозы), мелкоштучных и тарных грузов (контейнеровозы), длинномерных грузов (трубовозы, металловозы, лесовозы), железобетонных конструкций (панелевозы, фермовозы, плитовозы, балковозы, блоковозы, сантехкабиновозы), технологического оборудования и строительных машин (тяжеловозы).
Для перевозки керамзита и других сыпучих материалов с небольшой плотностью применяют специализированные прицепы и полуприцепы — керамзитовозы грузоподъемностью до 12 т, т. е. самосвалы с увеличенной вместимостью кузова.
При перевозках на строительные объекты мелкоштучных и тарных грузов (санитарно-технической и вентиляционной аппаратуры, отделочных, изоляционных и кровельных материалов, кирпича, оконных и дверных блоков, небольших по массе и размерам сборных железобетонных конструкций и т. п.) все шире используют контейнеризацию и пакетирование. Для доставки контейнеров и пакетов применяют бортовые автомобили, прицепы и полуприцепы общего назначения и специализированные транспортные средства — автомобили-самопогрузчики и контейнеровозы.
Автомобили-самопогрузчики наряду с выполнением транспортных функций могут осуществлять погрузку и разгрузку перевозимых тарных грузов, перегружать грузы на рядом расположенные автомобили и прицепы с помощью гидравлических погрузочно-разгрузочных устройств, установленных на самом автомобиле. Автомобили-самопогрузчики оборудуют бортовыми манипуляторами, качающимися порталами, грузоподъемными бортами и навесными грузоподъемными устройствами.
Автомобили-самопогрузчики с качающимся порталом (бокового или заднего расположения, рис. 2.8, а) предназначены для перевозки, погрузки и разгрузки контейнеров массой до 5 т. Рабочий орган — качающийся портал 1 шарнирно соединен с платформой для установки контейнеров и может поворачиваться в вертикальной плоскости на угол до 120° двумя синхронно действующими длинноходовыми гидроцилиндрами 2 двустороннего действия. Качающиеся порталы используют также для погрузки-разгрузки сменных кузовов-контейнеров. Для перевозки, погрузки и разгрузки контейнеров большой грузоподъемности (20 т и более) применяют полуприцепы, оборудованные боковыми гидравлическими перегружателями (рис. 2.8, б).
Автомобили-самопогрузчики и контейнеровозы оборудуют выдвижными и откидными гидравлическими опорами 3, действующими при выполнении погрузочно-разгрузочных работ и обеспечивающими устойчивость машины и разгрузку ее ходовой части.
Автомобили-самопогрузчики с бортовыми гидравлическими манипуляторами осуществляют самопогрузку и саморазгрузку базового автомобиля и прицепа, погрузку-разгрузку других расположенных рядом транспортных средств, а также могут быть использованы на строительно-монтажных работах небольшого объема.
Манипулятор грузоподъемностью 2,5 т состоит (рис. 2.9) из поворотной колонки, шарнирно сочлененного стрелового оборудования, двух выносных гидравлических опор 6, механизма поворота стрелы в плане, двух пультов управления 4 и комплекта сменного рабочего оборудования.
Стреловое оборудование смонтировано на поворотной колонке 10, установленной на опорной раме 5 шасси, и состоит из рукояти 11, рычага 13, телескопической стрелы 14 с основной 17 и выдвижной 18 секциями, гидроцилиндров 12, 15 и 16 управления, крюковой подвески 19 или ротатора 20. Ротатор обеспечивает манипулирование грузом в горизонтальной плоскости через реечную передачу и гидроцилиндр 21 двустороннего действия, штоком которого являйся рейка 22 ротатора, входящая в зацепление с шестерней 23.В комплект сменного рабочего оборудования манипулятора входят удлинитель стрелы, выдвигаемый вручную, вилочный подхват, клещевой захват для пакетированных грузов и захват для контейнеров. Поворот стрелового оборудования в плане на угол 400° обеспечивается реечным поворотным механизмом, включающим два попеременно работающих гидроцилиндра, рейку 7 и шестерню 8, жестко закрепленную на валу 9 поворотной колонки. Привод аксиально-поршневого насоса 3 гидросистемы манипулятора осуществляется от двигателя 1 автомобиля через коробку отбора мощности 2. Управление манипулятором может осуществляться с любого из двух пультов управления 4, расположенных по обеим сторонам автомобиля.
Конструкции отечественных бортовых манипуляторов выполнены по единой принципиальной схеме и различаются между собой грузовым моментом, грузоподъемностью, высотой подъема и опускания крюка, массой, габаритными размерами. Компоновочные схемы размещения бортовых манипуляторов на автотранспортных средствах показаны на рис. 2.10.
Для перевозки жидких вяжущих материалов (битум, гудрон, эмульсии) в разогретом состоянии от предприятий-изготовителей к местам производства дорожных, кровельных и изоляционных работ применяют битумовозы и автогудронаторы. Они представляют собой цистерны эллиптической формы, смонтированные на шасси автомобилей или на полуприцепах к седельным тягачам, и оснащаются системами подогрева (для поддержания температуры перевозимого материала не ниже 200°С) и выдачи мастики. Вместимость цистерн гудронаторов 3500...7000 л, битумовозов — 4000...15000 л.
Для перевозки труб длиной 6... 12 м диаметром до 1420 мм и сварных секций из труб (плетей) длиной 24...36 м применяют специальные автопоезда — трубовозы и плетевозы. В состав трубовоза входят автотягач, одноосный прицеп-роспуск с жестким дышлом или полуприцеп. Тяговое усилие на груженый прицеп-роспуск передается у трубовозов через тягово-сцепное устройство и дышло, у плетевозов — непосредственно трубами (плетями), закрепленными на тягаче и двухосном прицепе-роспуске. Количество одновременно перевозимых труб устанавливается, исходя из грузоподъемности автопоезда. При многорядной укладке трубы увязывают предохранительным канатом. Для перевозки изолированных труб в городских условиях обычно применяют специализированные полуприцепы-трубовозы о гидравлическими разгрузочными механизмами, обеспечивающими сохранность изолирующего слоя и подготовленных для сварки торцов труб при транспортировке, погрузке и разгрузке.
На рис. 2.11, а показан седельный тягач 1 с полуприцепом-трубовозом 5 грузоподъемностью 7 т, оборудованным двумя (передним и задним) гидравлическими разгрузочными механизмами 2. Рама полуприцепа выполнена раздвижной и на передней и задней ее частях имеются деревянные опорные плоскости и боковые стойки.
Полуприцеп оборудован передним и задним металлическими предохранительными щитами 5, предотвращающими осевое перемещение труб 4 при перевозке. Разгрузочный механизм состоит из телескопической стрелы 9 (рис. 2.11, в), раздвигаемой встроенным гидроцилиндром, и двух телескопических гидроцилиндров 7 для поворота стрелы с грузовым захватом 8 для труб в вертикальной плоскости. На рис. 2.11, б, в показаны положения стрелы соответственно перед разгрузкой и в конце разгрузки. Устойчивость автопоезда обеспечивается откидными опорами 6. Пульт управления разгрузочными механизмами расположен в передней части полуприцепа. Трубовозы и плетевозы оборудуют габаритными сигналами. Грузоподъемность автомобильных трубовозов 9...12 т, плетевозов — 6...19 т.
Для перевозки крупноразмерных железобетонных конструкций и деталей с заводов-изготовителей на строительные площадки применяют специализированные прицепы и полуприцепы: панелевозы, фермовозы, балковозы, плитовозы, блоковозы и сантехкабиновозы. Выбор типа транспортного средства определяется габаритами, массой и условиями перевозки изделий.
Панелевозы (рис. 2.12, а) выполнены в виде полуприцепов к седельным автотягачам и предназначены для перевозки в вертикальном или крутонаклонном положении стеновых панелей, перекрытий, перегородок, плит, лестничных маршей и т. п. Различают ферменные и рамные полуприцепы-панелевозы. Несущий металлический каркас ферменных панелевозов выполняют в виде пространственной фермы («хребта») трапециевидного (рис. 2.12, б) или прямоугольного сечения или в виде двух плоских продольных ферм, соединенных между собой передней и задней опорными площадками и горизонтальными связями (рис, 2.12, в). Хребтовая ферма располагается по продольной оси симметрии полуприцепа, а перевозимые панели — в кассетах по обеим сторонам от нее под углом 8... 12° к вертикали. Передняя и задняя площадки фермы имеют поручни для такелажников. У панелевозов с плоскими несущими фермами панели располагаются в несколько рядов вертикально в кассете между фермами. Некоторые конструкции панелевозов имеют также дополнительные боковые наклонные кассеты для перевозки укороченных панелей в один ряд (рис. 2.12, г), что позволяет лучше использовать грузоподъемность автопоезда. Для крепления панелей используют винтовые зажимы, прижимные планки и канаты, затягиваемые с помощью ручной лебедки.
Рамные прицепы-панелевозы (рис. 2.12, д) имеют раму, несущую кассету и воспринимающую основную нагрузку. Панели устанавливаются внутри кассеты на деревянный настил и удерживаются от бокового перемещения зажимными винтами. Передняя часть полуприцепов-панелевозов опирается на седельно-сцепное устройство тягача, а задняя — на одноосную или двухосную тележку с управляемыми или неуправляемыми колесами. В стесненных условиях городской застройки обычно применяют панелевозы с управляемыми задними тележками, улучшающими маневренность автопоезда. Современные полуприцепы-панелевозы оборудуются раздельно управляемыми гидравлическими опорами с гидроцилиндрами двустороннего действия, работающими от гидросистемы автомобиля, и имеют автоматическую сцепку с тягачом, что позволяет вести монтаж непосредственно с панелевозов (монтаж с «колес»), более эффективно использовать базовый автомобиль, который может обслуживать несколько сменных полуприцепов (челночный метод работы) и осуществлять погрузку-разгрузку панелевоза на неровных площадках. Грузоподъемность полуприцепов-панелевозов 9...22 т.
Ферменные и рамные панелевозы можно переоборудовать в полуприцепы платформенного типа и использовать для перевозки плит, балок, фундаментных блоков и других грузов. Это повышает их универсальность и коэффициент использования пробега за счет возможности загрузки машины при движении в обратном направлении.
Длиннобазовые полуприцепы-фермовозы предназначены для перевозки ферм длиной 12...30 м, установленных и закрепленных в положении, близком к рабочему. Полуприцепы-фермовозы имеют ферменную или балочную конструкцию с кассетной платформой и двухосной со сдвоенными колесами управляемой и неуправляемой тележками. В условиях стесненных строительных площадок применяют полуприцепы-фермовозы с гидравлическим управлением тележки, у которой каждое колесо поворачивается на соответствующий угол в зависимости от угла «складывания» автопоезда.
На рис. 2.13 показан автопоезд-фермовоз для перевозки ферм любой конструкции длиной до 24 м и высотой до 2,5 м. Рама 2 полуприцепа кассетного типа ферменной конструкции передней частью опирается на седельно-сцепное устройство тягача, а задней — на седельно-опорное устройство двухосной задней управляемой тележки 4. Колеса тележки управляются автоматически с помощью следящей системы с гидравлическим приводом. Переднюю передвижную опору 5 полуприцепа устанавливают вдоль рамы в зависимости от длины перевозимых ферм и передвигают с помощью ручной лебедки 1. Ферма 3 опирается на грузовые площадки рамы и закрепляется в верхнем ее поясе прижимными винтами. Грузоподъемность полуприцепов-фермовозов 10...22 т.
Полуприцепы-сантехкабиновозы и блоковозы предназначены для перевозки объемных элементов жилых и промышленных зданий (унифицированных санитарно-технических кабин, блок-комнат, маршей), технологического оборудования (секций лифтов, трансформаторов, котлов, бункеров, баков и др.) и контейнеров. По конструкции они имеют много общего с панелевозами рамного типа и отличаются низким расположением грузовой площадки и отсутствием специальных средств крепления.
Полуприцеп-сантехкабиновоз (рис. 2.14) представляет собой сварной из гнутых и прокатных профилем каркас кассетного типа, передняя часть которого опирается на седельно-сцепное устройство автомобиля-тягача, а задняя — на одно- или двухосную тележку с управляемыми или неуправляемыми колесами. Оборудуются они механическими или управляемыми гидравлическими опорными устройствами. Грузоподъемность 4...30 т.
Полуприцепы-плитовозы применяют для перевозки плит перекрытий и покрытий в горизонтальном положении, а также балок, колонн, ригелей, пиломатериалов и др. Несущей частью грузовой площадки плитовоза является хребтовая рама с консолями для настила и выдвижными боковыми стойками. Полуприцепы имеют одноосную или двухосную заднюю тележку. Некоторые конструкции плитовозов выполняют с раздвижной телескопической рамой. Грузоподъемность плитовозов до 22 т.
Для перевозки тяжеловесного крупногабаритного оборудования и строительных машин применяют трех-, четырех- и шестиосные многоколесные прицепы и полуприцепы-тяжеловозы грузоподъемностью 20...120 т с низкорасположенной платформой. Прицепы транспортируют балластными автомобильными тягачами, а полуприцепы — седельными. Прицепы и полуприцепы большой грузоподъемности оборудуют гидравлическими подъемными механизмами для опускания платформы при погрузке и подъеме ее при транспортировке грузов. Для погрузки и выгрузки грузов на тягаче устанавливают лебедку с приводом от коробки отбора мощности автомобиля.
Основными направлениями развития специализированных транспортных средств являются: расширение их серийного производства и номенклатуры с одновременным снижением количества типоразмеров, создание транспортных средств многоцелевого назначения, совершенствование механизмов крепления грузов, опорных, зажимных и погрузочно-разгрузочных устройств, повышение единичной грузоподъемности и широкая унификация машин.
Задание 7: Представьте, каким прицепным и навесным оборудованием можно оснащать автомобили, тракторы и пневмоколесные тягачи.
Прицепы для грузовых автомобилей:
Большинство прицепного оборудования для автомобилей и тягачей, описанных выше, также могут использоваться вместе с тракторами.
Навесные агрегаты для тракторов:
Баровые грунторезные машины, траншейные экскаваторы, буровые машины, кабелеукладчики, корчеватели, пропорщики, сваебойные машины, трубоукладчики, краны тракторные, подъемники, установки для ремонта скважин и тракторы для подземных работ.
Задание 8: Изучите чем отличаются двухосные тягачи от одноосных, а также классические самосвалы от шарнирно-сочлененных, приведите область их применения.
Пневмоколесные тягачи предназначены для работы с различными видами сменного навесного и прицепного строительного оборудования. По сравнению с гусеничными тракторами они более просты по конструкции, имеют меньшую массу, большую долговечность, дешевле в изготовлении и эксплуатации. Большие скорости тягачей (до 50 км/ч) и хорошая маневренность в значительной мере способствуют повышению производительности агрегатированных с ними строительных машин.
Различают одно- и двухосные тягачи, на которых применяют дизели, и два вида трансмиссий — механическую и гидромеханическую. Наиболее распространены тягачи с гидромеханической трансмиссией.
Одноосный пневмоколесный тягач состоит из двигателя, трансмиссии и двух ведущих управляемых колес. Самостоятельно передвигаться или стоять на двух колесах без полуприцепного рабочего оборудования одноосный тягач не может. В сочетании с полуприцепным рабочим оборудованием такой тягач составляет самоходную строительную машину с передней ведущей осью. Управление сцепом тягач-полуприцеп осуществляется путем поворота на 90° вправо-влево относительно полуприцепа с помощью гидроцилиндров двустороннего действия.
Двухосный тягач в отличие от одноосного имеет возможность самостоятельно перемещаться без прицепа, работать в агрегате с двухосными прицепами при незначительных затратах времени на их смену. Двухосные четырехколесные тягачи имеют один или два ведущих моста и шарнирно сочлененную раму. Схема поворота полурам такая же, как и у пневмоколесного трактора (см. рис. 2.5, в). Гидромеханическая трансмиссия одно- или двухосных тягачей имеет раздаточную коробку, от которой основной крутящий момент через гидротрансформатор, коробку передач и соединительные валы сообщается ведущему мосту (или двум мостам). Часть мощности, отдаваемой двигателем через раздаточную коробку и карданный вал, может передаваться к исполнительным органам управления рабочим оборудованием. Все агрегаты привода, отбора мощности и трансмиссии ходовой части тягачей унифицированы и могут быть использованы для различных модификаций машин той же или смежной мощности. Мощность дизеля тягача составляет до 880 кВт.
В конструкциях двухосных тягачей применяют гидро- и электромеханические трансмиссии с мотор-колесами.
На базе колесных тягачей, используя различное сменное рабочее оборудование, возможно создание многих строительных и дорожных машин (рис. 2.6).
Автомобили-самосвалы перевозят строительные грузы в металлических кузовах с корытообразной, трапециевидной и прямоугольной формой поперечного сечения, принудительно наклоняемых при разгрузке с помощью подъемного (опрокидного) механизма назад, на боковые (одну или две) стороны, на стороны и назад. По назначению различают специальные карьерные и универсальные общестроительные самосвалы. В условиях городского строительства применяют универсальные самосвалы (рис. 2.7) грузоподъемностью 4...12 т, предназначенные для перевозки грунта, гравия, щебня, песка, асфальта, бетонной смеси, строительного раствора и т. п. Современные универсальные самосвалы выпускают на шасси грузовых бортовых автомобилей общего назначения (иногда с укороченной базой) и оборудуют однотипными гидравлическими системами, обеспечивающими быстрый подъем и опускание кузова, высокую надежность и безопасность работы.
Основными узлами таких систем является масляный бак, гидравлический насос с приводом от коробки отбора мощности автомобиля, один или несколько (в зависимости от грузоподъемности) телескопических гидроцилиндров одностороннего действия, непосредственно воздействующих на кузов, распределитель или кран управления, соединительные трубопроводы и предохранительные устройства. Гидроцилиндры подъемных механизмов могут иметь горизонтальное, наклонное и вертикальное расположение и устанавливаются на раме автомобиля под передней частью кузова или на переднем его борту (рис. 2.7, а). Разделитель или кран управления направляет поток рабочей жидкости от насоса к гидроцилиндру (или синхронно работающим гидроцилиндрам) при опрокидывании кузова, соединяет полости гидроцилиндров со сливным баком при опускании кузова, ограничивает давление в системе и обеспечивает фиксацию кузова в определенных положениях (крайних или промежуточных).
Наиболее распространены в строительстве самосвальные автопоезда в составе автомобиля-самосвала и прицепа-самосвала или седельного тягача и полуприцепа-самосвала (рис. 2.7, 6). Автомобиль-самосвал разгружается на стороны, а прицеп-самосвал — на стороны и назад. Прицепы-самосвалы могут иметь разъемные (сдвоенные) кузова, передний из которых разгружается на две (боковые), а задний — на три (боковые и назад) стороны. Современные автомобили-самосвалы и самосвальные прицепы имеют унифицированные кузова, ходовую часть, подъемные механизмы и оборудуются системой автоматического открывания и закрывания бортов с управлением из кабины водителя.
Шарнирно-сочлененные самосвалы —это самосвалы с шарнирно-сочленённой рамой, используемые на строительных и карьерных площадках, где требуется повышенная проходимость и маневренность. Сочлененный самосвал — универсальная машина для перевозки грузов по труднопроходимой местности в суровых климатических условиях.
Применяются в следующих отраслях:
· горнодобывающая промышленность;
· щебеночная промышленность;
· строительство.
Конструкция сочлененных самосвалов
Рамы выполнены из двух секций, шарнирно связанных между собой. Конструкция сочленения позволяет секциям не только складываться в горизонтальной плоскости, но и поворачиваться друг относительно друга. Это исключает сильные нагрузки на раму при переезде через большие неровности, а также позволяет постоянно сохранять контакт колес с грунтом. Заметим, что некоторые фирмы выпускают машины, передняя и задняя части которых могут складываться, но не имеют возможности отклоняться относительно горизонтальной поверхности. Естественно, проходимость от этого страдает, правда, цена уменьшается.
За счет сочленения самосвал может маневрировать в узком пространстве. У него очень малый для большой машины радиус поворота. При этом самосвал очень легок в управлении.
Большинство сочлененных самосвалов имеет грузоподъемность от 10 до 50 т. При этом больше выпускается машин грузоподъемностью до 30 т. В большинстве своем автомобили трехосные, хотя встречаются и двухосные. Производители предлагают машины колесной формулы 6х4 и 6х6. Наиболее оснащенные варианты имеют привод на все шесть колес, возможность блокировки дифференциалов всех осей плюс межосевую блокировку. В сочетании с автоматической трансмиссией, подвеской колес с большими ходами и шарнирным сочленением полурам это придает очень высокую проходимость. Кузов «плывет» над неровностями, не теряя горизонтального положения.
Движение по пересеченной местности связано с преодолением подъемов и спусков. Поэтому самосвалы, особенно большой грузоподъемности, оснащают тормозными механизмами, охлаждаемыми маслом. Полностью закрытая конструкция предотвращает попадание в них грязи и воды. На младшие модели охлаждаемые маслом тормоза предлагают за доплату. Кроме того, машины часто оснащают гидравлическими тормозами-замедлителями (ретардерами). Кузова спроектированы таким образом, что разгрузка происходит на значительном расстоянии от задних колес. При этом кузов поднимается почти вертикально. Обычно грунт сваливают под откос или в бункер, что избавляет от необходимости использовать дополнительную технику для подчистки площадки.
Область применения.
Шарнирно-сочлененные самосвалы, или, как у нас их еще называют, землевозы, оказываются практически незаменимыми в условиях, когда необходимо перемещать значительные объемы инертных или иных материалов, но подъезды к месту погрузки проходят по слабым грунтам — заболоченным или песчаным. Пустить по таким путям обычные дорожные самосвалы, значит утопить их в первом же заезде, а укреплять для них дорогу — занятие дорогое и неблагодарное. Сочлененные самосвалы нашли применение в крупных строительных проектах. На Севере самосвалы неплохо показали себя на строительстве газопроводов.
Самосвалы с шарнирно-сочлененной рамой позволяют перевозить сыпучие грузы с малым временем рабочего цикла и максимальной экономией топлива, тем самым обеспечивая минимальные затраты на тонну груза. Превосходное соотношение «грузоподъемность / вес» увеличивает мощность и маневренность. Кроме того, благодаря шарнирам качающейся рамы, рамному управлению и шинам высокой проходимости карьерный самосвал оптимально справляется с работой на крутых склонах, неровной или скользкой поверхности. Современная элетроника, эффективно оснащенные кабины и простые средства управления обеспечивают все условия, необходимые для повышения производительности и увеличения времени безотказной работы.
Задание 9: Представьте основные положения по безопасному применению транспортных средств.
В соответствии с п. 6.2.6 СНиП 12-03-2001 внутренние автомобильные дороги на территории стройплощадки должны соответствовать требованиям строительных норм и правил.
Порядок движения транспортных средств на внутренних автомобильных дорогах строительных площадок устанавливается Правилами дорожного движения, утвержденными МВД Российской Федерации.
Схемы движения транспортных средств и пешеходов должны быть вывешены перед входом и въездом на площадку у предприятия, а также на видных местах на участках работ.
Безопасность при эксплуатации транспортных средств
Основными причинами опасностей, аварий и несчастных случаев, связанных с эксплуатацией транспортных средств является:
нарушение требований правил дорожного движения на улицах и дорогах, а также во всех местах, где возможно движение транспортных средств, например, внутризаводские территории;
- нарушение требований правил техники безопасности;
- неосторожные действия исполнителей работ;
- отсутствие механизации выполняемых работ;
- неправильный и опасный прием труда, работа в опасной зоне;
- неисправность оборудования, приспособлений, инструмента, машин;
- выполнение несвойственной работы;
- скользкость полов, территорий, платформ, кузовов, лестниц, буферов, подножек автомобилей;
- незнание правил безопасности выполнения работ, устройства автомобиля, оборудования.
При эксплуатации автомобильного транспорта, тракторов, погрузчиков, других транспортных средств необходимо руководствоваться Межотраслевыми правилами по охране труда на автомобильном транспорте. При эксплуатации автомобилей, тракторов и других мобильных машин возникновение опасных факторов отмечается при выполнении почти всех производственных операций.
Следствием травматизма является нарушение требований безопасности при их выполнении: техническое обслуживание, текущий ремонт и хранение подвижного состава автотранспорта; вождение подвижного состава автотранспорта по улицам и дорогам; обслуживание и текущий ремонт автомобилей в пути; погрузка и разгрузка грузовых автомобилей.
Техника безопасности при эксплуатации бульдозера
Помимо общих требований техники безопасности, выполнение отдельных видов бульдозерных работ требует соблюдения определенных правил.
При производстве любых работ уклоны на подъемы и спусках, а также крены в поперечном направлении не могут превышать предельных значений, указанных заводом-изготовителем в инструкции по эксплуатации. Обычно эти значения не превышают для подъемов 25, спусков 35, для боковых кренов – 12-15є.
При сбросе грунта под откос поперечными ходами нельзя выдвигать отвал за край насыпи, так как в этом случае машина может сползти вниз. При движении бульдозера вдоль откоса или насыпи его ходовая часть не должна выходить за их края. Такие же требования соблюдают при засыпке траншей поперечными, косыми и продольными ходами бульдозера. Нарушение этих правил может вызвать обрушение стенок траншеи и сползание в неё всей машины.
Высота перемычек между траншеями при производстве любых работ траншейным способом не должна превышать высоту отвала, так как в противном случае возможно случайное обрушение грунта .
Сбрасывать грунт под откос методом работы через вал следует без заезда ходовой частью на разрыхленный грунт, находящийся за краем откоса, иначе вместе с рыхлым грунтом машина может сползти вниз по откосу.
При работе на косогорах следует создавать небольшой (3-7є) обратный уклон полки или террасы, что исключит возможность сползания трактора по склону или обрушения края разработанной полки или террасы вниз.
Расчищать местность от кустарника и мелколесья, а также сооружать пионерные дороги и пробивать трассы следует с большой осторожностью, так как при выполнении таких работ возможно повреждение радиатора, кабины, облицовки и других узлов базового трактора деревьями, корнями и другими препятствиями.
При корчевке пней и удалении крупных камней возможны наезд на корчуемый предмет поддоном картера двигателя, корпусами заднего моста и бортовых передач и их повреждение, что особенно опасно при отсутствии защитных кожухов снизу.
По той же причине опасно работа бульдозера на разработке взорванных и разрыхленных скальных пород. При этом особенно надо следить за тем, чтобы отдельные камни не попадали между отвалом, брусьями и ходовой частью и остовом базовой машины, а также между отдельными узлами и деталями ходовой части.
При валке деревьев после того, как дерево начало наклоняться, бульдозер останавливают, отводят назад, подводят отвал под корневую систему дерева и продолжают операцию валки одновременным действием напорного усилия базовой машины и подъемного усилия на отвале. В противном случае корни падающего дерева, попав под трактор могут повредить его или даже опрокинуть. При валке дерева от ударов могут обломиться крупные сучья, поэтому эту операцию выполняют с той стороны, где такие сучья отсутствуют.
Работы в воде можно производить при глубине, не выше указанной в инструкции заводом-изготовителем. Обычно эта глубина равна высоте гусеницы или радиусу колеса. При большей глубине вода может попасть внутрь отдельных узлов базового трактора.
Контакт бульдозерного отвала с буфером скрепера для толкания его при наборе следует производить на передаче, близкой к скорости движения скрепера. В противном случае возможно повреждение конструкций обеих машин. При толкании недопустимо движении бульдозера под углом к скреперу, так как при этом возможно повреждение конструкции скрепера и его шин ножам и отвала бульдозера. Нельзя вывешивать бульдозер на буфере скрепера, так как это перегружает конструкцию скрепера.
Загружать бульдозером транспортные средства с помощью лотков и эстакад следует постепенно, учитывая, что падение большой массы грунта или какого-либо материала в кузов автомашины может вызвать её повреждение.
Погрузо-разгрузочные работы
Погрузочно-разгрузочные работы должны производиться, как правило, механизированным способом с помощью подъемно-транспортного оборудования и средств малой механизации. Безопасность труда при выполнении погрузочно-разгрузочных работ обеспечивается выбором способов производства работ, предусматривающих предотвращение или снижение до уровня допустимых норм воздействия на работающих опасных и вредных производственных факторов.
Погрузочно-разгрузочные, транспортные и складские работы должны выполняться в соответствии с технологическими картами, утвержденными руководителем предприятия.
Технологические карты (или проекты производства) погрузочно-разгрузочных, транспортных и складских работ должны включать:
- схемы укладки различных материалов, полуфабрикатов и готовой продукции; порядок разборки штабелей, предельную высоту складируемых различных грузов;
- кратчайшие и безопасные пути транспортирования материалов, полуфабрикатов, готовой продукции;
- требования безопасности при проведении погрузочно-разгрузочных работ;
- предельно допустимую массу грузов при подъеме и транспортировании грузов мужчинами, женщинами, подростками;
- фамилию, имя, отчество и должность лиц, ответственных за проведение работ.
Погрузочно-разгрузочные, складские и транспортные работы следует выполнять под руководством ответственного лица, назначаемого приказом руководителя предприятия и несущего ответственность за безопасную организацию и соблюдение требований безопасности на всех участках технологического процесса.
При погрузке (разгрузке) особо тяжелых, крупногабаритных и опасных грузов на месте работ должен постоянно находиться ответственный за безопасное выполнение работ.
Работники, занятые на погрузочно-разгрузочных, складских и транспортных работах, должны проходить предварительные при поступлении на работу и периодические медицинские осмотры.
Механизированный способ погрузочно-разгрузочных работ является обязательным для грузов массой более 20 кг, а также при подъеме грузов на высоту более 3 м. Поднимать и перемещать грузы вручную необходимо при соблюдении норм, установленных действующим законодательством.
Контрольные вопросы:
Вопрос 11: Определите понятие транспортная работа, в каких единицах она измеряется?
Транспортная работа - это количество перевезенного груза или пассажиров на расстояние перевозки за определенное время, определяется в тонно-километрах или в пассажиро-километрах. Транспортная работа подсчитывается умножением перевезенного груза ( пассажиров) на расстояние ездки или нескольких ездок за рабочий день. Транспортную работу грузового автомобиля, работающего с почасовой оплатой, оценивают по валовому доходу, а автомобиля-такси - по величине платного пробега.
Транспортная работа определяется умножением нагрузки в тоннах на пробег в километрах и потому для каждого случая будет равна соответственно: 400 ткм ( 4 X 100), 300 ткм ( 3 X 100), 200 ткм ( 2 X 100), 100 ткм ( 1 X 100) и О ткм.
Транспортная работа, выполненная автомобилем за день работы, будет равна сумме тонна-километров по всем ездкам с грузом.
Дата добавления: 2018-04-15; просмотров: 2745; Мы поможем в написании вашей работы! |
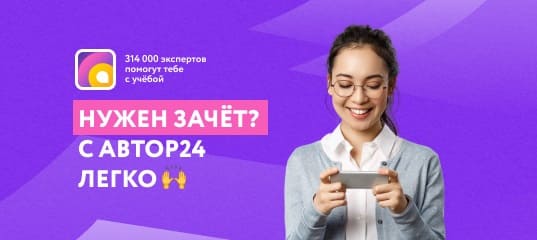
Мы поможем в написании ваших работ!