Общая технология изделий из стекла. Свойства стекол
Материалы и изделия из стеклорасплавов
Стеклянные изделия люди изготавливают с древнейших времен. Почти 6 тысяч лет назад стекло делали в Египте и Месопотамии. В Риме первые стекольные мастерские были созданы в 1 веке до н.э. Римляне умели отливать стекло и изобрели стеклодувную трубку. Из Рима в VII – ХII вв. это ремесло распространилось в европейские страны. Наибольшего расцвета оно достигло в Венеции, которая была мировым центром стеклоделия до ХVI – XVII вв. Венецианские стеклянные изделия отличались разнообразием и имели большую художественную ценность.
В 1635 году в России около Воскресенска был построен первый стекольный завод, на котором выдували оконное стекло и различные стеклянные изделия. Большую исследовательскую работу по химии и технологии стекла вел М.В. Ломоносов. Он заложил научные основы стеклоделия в России, разработал свыше 2 тысяч составов цветной мозаики.
В основном стекло производилось ручным способом, это был тяжелый физический труд. В конце ХIХ – начале ХХ вв. был создан механизированный способ вытягивания листового стекла, построена первая ванная стекловаренная печь непрерывного действия.
В ХХ веке в производстве стекла широко стали применять машинную технику, было создано много новых видов стекла и изделий из него. Сегодня стекло является одним из важнейших искусственных строительных материалов.
В Беларуси стеклоизделия в виде листового оконного и закаленного стекла, стеклянных труб, теплоизоляционных блоков из пеностекла и другие изделия выпускают Гродненский стеклозавод и завод им. Ломоносова в Гомельской области. Номенклатура выпускаемой продукции: листовое стекло, конструкционные, облицовочные и теплоизоляционные стеклянные изделия. На основе стекло- и шлакорасплавов созданы микрокристаллические материалы – ситаллы и шлакоситаллы, сочетающие в себе аморфную и кристаллическую структуру.
|
|
В последние годы быстро развивалось производство специальных видов строительного и технического стекла, а также теплоизоляционных материалов. Получило распространение производство стеклоблоков, профильного стекла, стеклопакетов. Использование стеклоблоков позволяет снизить теплопотери зданий более чем в 2 раза по сравнению с одинарным остеклением.
Стекло и его свойства
Стеклом называют все аморфные тела, получаемые путем переохлаждения расплавов независимо от их химического состава и температурной области затвердевания, обладающие в результате постепенного увеличения вязкости механическими свойствами твердых тел, причем процесс перехода из жидкого состояния в стеклообразное должен быть обратимым.
|
|
Признаками стеклообразного состояния вещества является отсутствие четко выраженной точки плавления, гомогенность и изотропность.
В стеклообразном состоянии могут быть получены многие вещества.
Стекло способно образовывать называемые стеклообразующими оксиды Si02, P2O5 и В2О3 без каких-либо добавок. Однако в большинстве случаев сырьевой массой для производства стекол является многокомпонентная шихта, содержащая помимо стеклообразующего оксида различные добавки.
В строительстве используют почти исключительно силикатное стекло, основным компонентом которого является диоксид кремния Si02.
Стекло не является веществом с определенным химическим составом, который может быть выражен химической формулой, поэтому состав стекла условно выражают суммой оксидов.
Состав строительных стекол в зависимости от вида и назначения содержит оксиды (в % по массе): Si02 — 64-73,4; Na20 — 10-15,5; К20 — 0-5; СаО — 2,5-26,5; MgO — 0-4,5; A1203 — 0-7,2; Fe203 — 0-0,4; S03 — 0-0,5; B203 — 0-5.
Каждый из оксидов играет свою роль в процессе варки формирования свойств стекла. Оксид натрия ускоряет процесс варки, понижая температуру плавления, но уменьшает химическую стойкость стекла. Оксид калия придает блеск и улучшает светопропускание. Оксид кальция повышает химическую стойкость стекла. Оксид алюминия повышает прочность, термическую и химическую стойкость стекла. Оксид бора повышает скорость стекловарения.
|
|
Для получения оптического стекла и хрусталя в шихту вводят оксид свинца, повышающий показатель светопреломления.
Сырье для производства стекла
Сырьевые материалы для производства стекла разделяются на основные и вспомогательные.
Основным сырьем для изготовления стекла является чистый кварцевый песок (72 – 75 %), известняк (СаСО3), доломит (СаСО3; MgСО3), кальцинированная сода (Na2CO3), сульфат натрияи полевой шпат.
Для придания специальных свойств – повышенной термостойкости, прочности, химической стойкости, светорассеивания, цвета – в состав вводят добавки.
В последнее время стали широко использоваться отходы различных отраслей промышленности — доменные шлаки, кварцесодержащие материалы, тетраборит кальция, стеклобой и др.
. Минеральное сырье, как правило, имеет большое количество примесей и непостоянный состав.
Примеси условно разделяются на две группы:
ухудшающие качество стекломассы (оксиды железа, хрома, титана, марганца, ванадия);
|
|
соответствующие основным компонентам состава стекла (оксиды алюминия, кальция, магния, калия, натрия).
Примеси первой группы придают стеклу нежелательную окраску, а также могут привести к образованию пороков в стекле в виде включений.
Примеси второй группы обычно учитываются при расчете рецепта шихты.
Вспомогательные сырьевые материалы (осветлители, глушители, красители и др.) вводят в шихту для ускорения варки стекла и придания ему требуемых свойств.
Осветлители (сульфаты натрия и алюминия, калиевая селитра, мышьяковистый ангидрид) способствуют удалению из стекломассы газовых пузырьков.
Глушители (криолит, плавиковый шпат, двойной суперфосфат) делают стекло непрозрачным.
Красители придают стеклу заданный цвет — соединения: кобальта — синий, хрома — зеленый, марганца — фиолетовый, железа — коричневый и сине-зеленые тона и т.д.
Общая технология изделий из стекла. Свойства стекол
Производство строительного стекла состоит из следующих основных операций: обработка сырьевых материалов; приготовление шихты, варка стекла, формование изделий и их отжиг.
Обработкавключает дробление и помол материалов, поступающих на завод в виде кусков (доломит, известняк, уголь), сушку влажных материалов (песок, доломит, известняк), просеивание всех компонентов через сита заданного размера.
Приготовлениешихты включает операции усреднения, дозирования и смешения. Шихта считается качественной, если отклонение от заданного состава ее не превышает 1%.
Стекловарениепроизводится в специальных стеклоплавильных печах непрерывного (ванные печи) или периодического (горшковые печи) действия.
При нагревании шихты до 1100-1150 °С происходит образование силикатов сначала в твердом виде, а затем в расплаве.
При дальнейшем повышении температуры в этом расплаве полностью растворяются наиболее тугоплавкие компоненты Si02 и А120з— образуется стекломасса.
Эта масса неоднородна по составу и настолько насыщена газовыми пузырьками, чтоее называют варочной пеной.
Для осветления и гомогенизации температуру стекломассы повышают до 1500-1600 °С. При этом вязкость расплава снижается, облегчается удаление газовых включений и получение однородного расплава.
Стекловарение завершается охлаждением (студкой) стекломассы до температуры, при которой она приобретает вязкость, требуемую для выработки стеклоизделий.
Формованиеизделий производится различными методами: вытягиванием, литьем, прокатом, прессованием и выдуванием. Формование листового стекла производится путем вертикального или горизонтального вытягивания ленты из расплава (рис. 4), прокатом или способом плавающей ленты (флоат-способ).
Метод вытягивания применяют для получения стекла толщиной 2-6 мм. Как правило лента вытягивается из стекломассы вращающимися валками машины через лодочку (огнеупорный брус с продольной прорезью).
Рис. 4. Схема работы машины вертикального вытягивания стекла: 1 — лента стекла; 2 — стеклянный расплав; 3 — валики; 4 — шахта машины; 5 — камера; 6 — - горелка для поддержания высокой температуры в камере; 7 — холодильники
Флоат-способ является наиболее совершенным и высокопроизводительным из всех способов, известных в настоящее время. Он позволяет получать стекло с высоким качеством поверхности.
При этом стекло получают из стекломассы вертикальным вытягиванием, горизонтальным прокатом между двумя вращающимися валиками и флоат-способом.
Сущность флоат-способа в том, что струя стекломассы (1000 оС) непрерывно подается на поверхность расплавленного олова (232 оС), растекается по ней слоем определенной толщины и в результате охлаждения превращается в ленту стекла с полированной поверхностью.
Поверхности листового стекла получаются ровными и гладкими и не требуют дальнейшей полировки.
Отформованные изделия охлаждают в специальных печах и камерах.
Если охлаждать медленно (отжиг), то возникающие при формовке остаточные напряжения ослабевают до нормы, что обеспечивает длительную и надежную эксплуатацию стеклянных изделий.
Если повторно нагреть полученное изделие, а затем резко охладить, то можно получить равномерно распределенные остаточные напряжения сжатия во внешних слоях и растяжения во внутренних. Такой режим охлаждения называют закалкой.
Его применение обеспечивает стеклу повышенную механическую прочность при ударе (в 5 – 7 раз) и изгибе, термостойкость (в 3 – 5 раз) и твердость (с 5 до 7 по шкале Мооса).
При разрушении закаленного стекла образуются мелкие осколки с тупыми нережущими краями.
Если в исходную шихту ввести некоторые добавки (оксиды металлов или соединения фтора), то при повторном нагревании полученных изделий в стекле начинается процесс кристаллизации.
Добавки, представляющие собой кристаллические вещества, играют роль катализаторов. В результате образуется сложная структура, содержащая 90 – 95 % беспорядочно ориентированных микрокристаллов (размером менее 1 мк), остальное – стекловидная фаза.
По свойствам стеклокристаллические материалы (ситаллы) занимают промежуточное положение между стеклом и керамикой. Они прочнее стекла, тверже высокоуглеродистой стали, легче алюминия, химически и термически устойчивы, обладают хорошими диэлектрическими свойствами, по коэффициенту расширения некоторые из ситаллов близки к кварцевому стеклу.
Если в качестве исходного сырья используют шлаки черной металлургии, то получают шлакоситаллы с аналогичными свойствами.
Строительное стекло представляет собой биостойкий, негорючий твердый материал, обладающий высокой стойкостью к действию влаги, солнечной радиации и отрицательных температур.
Свойства стекол зависят от химического состава. Так, их плотность изменяется в пределах 2200 – 8000 кг/м3, прочность при сжатии составляет 100 – 700 МПа, при растяжении 30 – 80 МПа.
Стекло обладает низкой термической устойчивостью (перепад температуры составляет не более 80 оС) и прочностью на удар (хрупкое разрушение). С увеличением толщины изделия сопротивление удару, тепло- и звукозащитные свойства возрастают.
По электрическим свойствам стекла относятся к диэлектрикам. Силикатные строительные стекла отличаются высокой химической стойкостью за исключением действия плавиковой и фосфорной кислот. Этот материал обладает уникальными оптическими свойствами: светопропусканием, которое достигает 92 %, светопреломлением, отражением и рассеиванием света.
Дата добавления: 2018-04-15; просмотров: 410; Мы поможем в написании вашей работы! |
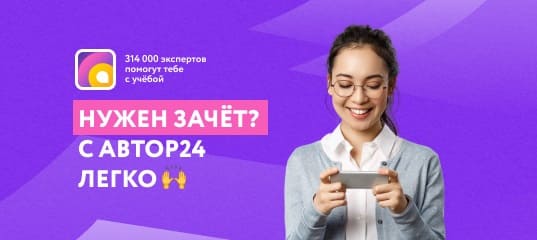
Мы поможем в написании ваших работ!