Лабораторная (учебно-исследовательская) работа № 11
ОПРЕДЕЛЕНИЕ МАРКИ УГЛЕРОДИСТОЙ СТАЛИ
ПО ЕЁ КРИТИЧЕСКИМ ТОЧКАМ
I. ЦЕЛЬ РАБОТЫ: ознакомиться с критическими точками сталей, определением критических точек методом пробных закалок и научиться по критическим точкам определять марку углеродистой стали.
II. КРАТКИЕ СВЕДЕНИЯ ИЗ ТЕОРИИ
Наличие критических точек в стали было впервые установлено русским металлургом Д. К. Черновым.
Критические точки – это температуры, соответствующие фазовым или структурным равновесиям в сплавах (равновесные критические точки), или температуры, при которых происходят превращения (неравновесные критические точки). Так же как и для чистого железа, эти точки принято обозначать буквой А с соответствующим равновесию или превращению индексом. Для неравновесных критических точек используются дополнительные индексы. В случае нагревания к обозначению критической точки добавляется индекс “с”, в случае охлаждения – индекс “r”. Критические точки в стали связаны с аллотропными превращениями железа FeaÛFeg , а так же с изменением растворимости углерода в g -железе.
Точка A1 соответствует температуре равновесия аустенита с перлитом (АÛП). Для сплавов Fe-C эта точка лежит на линии РК диаграммы и примерно соответствует 727°С (рис.1).
Точка AC1 обозначает превращение перлита в аустенит при нагревании (П®А). Точка Ar1 характеризует обратное превращение – аустенита в перлит при охлаждении (А®П).
|
|
Точки АC3 и Аr3 характеризуют соответственно окончание превращения феррита в аустенит при нагревании (Ф®А, оконч.) и начало обратного превращения аустенита в феррит (А®Ф, нач.) при охлаждении в доэвтектоидных сталях. В равновесных условиях (т.е. при бесконечно медленном нагревании или охлаждении) эти точки соответствуют линии GS диаграммы Fe-C. Их обозначают A3 (АÛФ). Положение этих точек зависит от содержания углерода в стали.
Равновесные точки Acm характеризуют равновесие аустенита и цементита (АÛЦ) и соответствуют линии SE диаграммы Fe-C.
Точки ACcm и Arcm обозначают соответственно окончание растворения в аустените вторичного цементита при нагревании (Ц2®А, оконч.) и начало выделения вторичного цементита из аустенита при охлаждении (А®Ц2, нач.) в заэвтектоидных сталях.
При проведении операций нагревания или охлаждения в реальных условиях критические точки не соответствуют диаграмме Fe-C и зависят от скорости нагревания или охлаждения. На положение этих точек оказывают влияние также легирующие элементы и различные примеси.
Для углеродистых сталей при условии очень медленного нагревания или охлаждения точки АС лежат немного (на несколько градусов) выше, а точки Аг ниже соответствующей равновесной температуры. В случае реальных условий нагрева для получения устойчивой структуры, соответствующей диаграмме Fe-C, необходимо доэвтектоидные стали перегревать выше критических точек на 30-50°С, а заэвтектоидные стали – на 30-70°С. При ускоренном нагреве процесс образования аустенита смещается в область высоких температур на сотни градусов, а поэтому пользоваться диаграммой состояния Fe-C в качестве единственного источника для выбора температуры нагрева нельзя.
|
|
Легирующие элементы и примеси могут понижать или повышать положение критических точек. Так, например, карбидообразующие элементы (V, Mo, W, Ti, Cr и др.), уменьшают коэффициент диффузии углерода и тормозят превращение перлита в аустенит. И, наоборот, элементы, хорошо растворяющиеся в аустените (Ni, Mn и др.), повышают его устойчивость и снижают положение критических точек. Элементы, хорошо растворяющиеся в феррите (Si, A1 и др.), уменьшают устойчивость аустенита и повышают положение критических точек A1 и А3. В связи с этим в технических сталях, содержащих 0,5-0,6% Si и 0,7-0,8% Mn, а также другие примеси, положение критических точек несколько отличается от диаграммы Fe-C. Более значительны отклонения в легированных сталях.
|
|
Поэтому для каждого конкретного состава стали необходимо определять положение критических точек, исходя из реальных условий нагревания и охлаждения. Полученные в этом случае значения критических точек можно использовать при назначении режимов термической обработки стали.
Для экспериментального определения критических точек используют следующие методы: пробных закалок, дилатометрический, дифференциальный термический, измерения электросопротивления.
Наиболее прост, но менее точен, метод пробных закалок.
III. НЕОБХОДИМЫЕ ПРИБОРЫ, ОБОРУДОВАНИЕ
И МАТЕРИАЛЫ
1. Термические печи с регулирующими потенциометрами.
2. Образцы углеродистой стали.
3. Твердомер Роквелла.
IV. МЕТОДИКА ПРОВЕДЕНИЯ РАБОТЫ
Образцы диаметром 15-20 мм и высотой 10-12 мм (7 шт.), изготовленные из доэвтектоидной стали, закалить с различных температур, повышающихся примерно на 30°С. При этом нижняя температура закалки должна лежать ниже предполагаемой точки А1, а высшая - выше точки А3. В связи с этим принять следующие температуры закалки: 700, 730, 760, 790, 820, 850, 880°С.
Закалка с температуры ниже A1 не влияет на твёрдость образца. Нагрев стали выше A1 приводит к превращению перлита в аустенит, который при закалке превратится в мартенсит. Чем выше температура закалки в пределах между А1 и А3, тем меньше феррита будет в структуре и тем твёрже будет сталь после закалки. Повышение температуры сверх А3 не изменит структуру стали и ее твёрдость в закаленном состоянии.
|
|
Измерение твёрдости закаленных от различных температур образцов позволяет определить положение критических точек. Пример определения точек А1 и А3 и их разницы схематично показан на рис. 2.
При нагревании образцы располагать на середине печи, ближе к горячему спаю термопары. Для сокращения времени на нагрев все образцы заложить в печь, нагретую до наиболее низкой температуры закалки. Выдерживать образцы при каждой температуре не менее 10 мин.
Для определения марки стали нужно рассчитать содержание в ней углерода. На рис.3 приведена расчетная схема, в основе которой лежит участок диаграммы Fe-C. На схеме приняты следующие обозначения: x – среднее содержание углерода в стали, %; – разница между температурами критических точек А3 и А1, т.е. =А3-А1, °С.
Предполагая, что линия GS – прямая (это допущение не вносит существенной погрешности в результат расчета), находим из подобия треугольников GBS и A3A1S:
Так как GB = 911-727 = 184oС, SA1 = (0,8-x), %, SB = 0,8, %, то
отсюда %
После подстановки значения рассчитывается содержание углерода x и округляется до ближайшей марки качественной углеродистой стали в соответствии с ГОСТ 1050-88.
V. СОДЕРЖАНИЕ ОТЧЕТА
1. Описать назначение и порядок проведения работы.
2. Привести описание основных критических точек (равновесных и неравновесных), указать соответствующие им равновесия или превращения и увязать их с диаграммой Fe-C.
3. Построить таблицу, включающие следующие данные:
№№ образцов | Температура нагрева под закалку, °С | Твердость HRC |
4. По данным таблицы построить график изменения твёрдости в зависимости от температуры нагрева под закалку.
5. Определить критические точки A1 и А3 и их разницу .
6. По критическим точкам с использованием диаграммы Fe-C (по расчетной схеме) определить марку стали.
ЛИТЕРАТУРА
1. Ю. М. Лахтин, В. П. Леонтьева. Материаловедение. – М.: Машиностроение, 1980.-С. 121.
2. Ю. А. Геллер, А. Г. Рахштадт. Материаловедение. – М.: Металлургия, 1983. – С. 224-229.
Лабораторная (учебно-исследовательская) работа № 12
ИЗУЧЕНИЕ ВЛИЯНИЯ СКОРОСТИ ОХЛАЖДЕНИЯ
ПРИ ТЕРМООБРАБОТКЕ НА СТРУКТУРУ И СВОЙСТВА
КОНСТРУКЦИОННЫХ СТАЛЕЙ
I. ЦЕЛЬ РАБОТЫ: изучить влияние скорости охлаждения при термической обработке (путем использования различных охлаждающих сред) на структуру и свойства углеродистой и легированной конструкционных сталей.
II. КРАТКИЕ СВЕДЕНИЯ ИЗ ТЕОРИИ
Скорость охлаждения при термической обработке является важным фактором воздействия на структуру и свойства сталей. По мере увеличения скорости охлаждения замедляются диффузионные процессы и происходит измельчение структуры стали. При критической скорости охлаждения диффузионные процессы полностью исключаются и распад переохлажденного аустенита происходит бездиффузионным путем с образованием структуры мартенсита.
Структурные диаграммы, учитывающие скорости охлаждения стали (т.е. отвечающие условиям непрерывного охлаждения), называют термокинетическими диаграммами распада переохлажденного аустенита. Они отличаются от диаграмм изотермического превращения аустенита, рассматривавшихся в предыдущих работах.
На рис.1 и 2 приведены в сопоставлении изотермические и термокинетические диаграммы распада аустенита в углеродистой стали 45 и легированной стали 45Х. Видно, во-первых, что изотермический распад аустенита происходит быстрее, чем атермический (т.е. в интервале температур), во-вторых, при атермическом процессе структура стали оказывается неоднородной и может сочетать в себе различные составляющие.
Из термокинетических диаграмм видно также, что существуют две критические скорости охлаждения. При первой критической скорости охлаждения предотвращается образование феррита и перлитоподобных структур, формирующихся диффузионным путем. При второй критической скорости охлаждения предотвращается в образование промежуточных (бейнитных) структур. Первой критической скорости охлаждения соответствуют на диаграммах температуры около 550°С, второй критической скорости охлаждения – около 350°С. Поэтому скорости охлаждения в реальных процессах термической обработки обычно дифференцируют по интервалам температур, близким к указанным выше.
Варьирование скоростью охлаждения обеспечивается обычно использованием различных охлаждающих сред. Охлаждающие среды могут быть разделены в зависимости от состава и свойств охлаждающего вещества на несколько групп: вода в водные растворы, масла, расплавы солей в щелочей, водовоздушные смеси, расплавленные металлы и сплавы, синтетические закалочные среды, быстродвижущиеся потоки охлаждающего вещества.
Вода и водные растворы отличаются высокой интенсивностью охлаждения как в области повышенных температур, так и при температурах мартенситного превращения. Последнее неблагоприятно сказывается на структуре в является причиной деформации и трещинообразования вследствие появления больших внутренних напряжений, особенно в крупных изделиях. Различные добавки могут увеличивать или уменьшать охлаждающую способность водных растворов.
Вода и водные растворы являются кипящими жидкостями. При закалке в этих средах различают три периода: 1) пленочное кипение (с образованием "паровой рубашки"), при этом скорость охлаждения сравнительно невелика; 2) пузырьковое кипение (при разрушении паровой рубашки) с быстрым охлаждением; 3) конвективный теплообмен с наименьшей скоростью охлаждения.
При охлаждении в воде комнатной температуры (~20°С) период пузырькового кипения длится от 400 до 100°С; при использовании горячей воды (~80°С) он сужается до 250...100°С; при использовании 10 %-го раствора NaCl в воде (20°С) этот период значительно расширяется (до б50... 100°С), что обеспечивает резкое повышение интенсивности охлаждения по сравнению с обычной водой (~ в 3 раза).
Кипящими жидкостями являются и минеральные масла. Но, в отличие от воды, период пузырькового кипения у них соответствует более высоким температурам (500...250°С). При закалке в масле значительно снижается (по сравнению с водой) скорость охлаждения в интервале температур мартенситного превращения (особенно при 250...100°С). Сопоставление скоростей охлаждения стали в различных средах приведено в табл. 1.
Or скорости охлаждения очень сильно зависит и прокаливае-мость стали. В связи с этим на номограмме прокаливаемости каждой охлаждающей среде соответствует своя графическая зависимость (рис.3). С использованием этой номограммы можно оценить изменение структуры по сечению закаленных образцов и деталей и увязать его с соответствующим изменением свойств. Предварительно по полосам прокаливаемости исследуемых сталей (рис.4,а и 4,6) необходимо определить параметры прокаливаемости этих сталей (расстояния до полумартенситной зоны).
Таблица 1
Охлаждающая способность различных сред
Охлаждающая среда
| Скорость охлаждения, оС/с, при температуре, оС | Охлаждающая среда
| Скорость охлаждения, оС/с, при температуре, оС | |||
б50... 550 | 350... 200 | б50... 550 | 350... 200 | |||
Дистиллированная водя | 250 | 200 | 5%-й раствор марганцовокислого калия | 450 | 100 | |
Вода при температуре, °C
| 18 | 600 | 270 | Глицерин | 135 | 175 |
28 | 500 | 270 | Эмульсия масла в воде | 70 | 200 | |
50 | 100 | 270 | Мыльная вода | 30 | 200 | |
74 | 30 | 200 | Минеральное масло | 150 | 30 | |
10-й водный раствор NaOH при 18°С | 1200 | 300 | Трансформаторное масло | 120 | 25 | |
Раствор NaCl при 18°С | 1100 | 300 | Сплав 75% Sn и 25% Cd, 175°С | 450 | 50 | |
Раствор соды при 18°С | 800 | 270 | Воздух спокойный | 3 | 1 | |
Раствор H2SO4 при 18°С | 750 | 300 | Воздух под давлением | 30 | 10 |
Параллельно в работе производится оценка изменения структуры и твердости по сечению образцов экспериментальным путем, после чего можно провести сопоставление этих данных с определенными по номограмме.
Ш. НЕОБХОДИМЫЕ ПРИБОРЫ, ОБОРУДОВАНИЕ И МАТЕРИАЛЫ
1. Термические печи.
2. Закалочные ванны с разными охлаждающими средами.
3. Твердомеры Бринеля и Роквелла.
4. Установка для приготовления шлифов.
5. Образцы из исследуемых сталей.
IV. МЕТОДИКА ПРОВЕДЕНИЯ РАБОТЫ
1. С использованием номограммы прокаливаемости оценить изменение структуры и твердости изучаемых сталей по сечению образцов, охлаждаемых в разных средах, сведя полученные данные в таблицу.
2. Провести полную термическую обработку образцов изучаемых сталей с охлаждением в разных средах.
3. Разрезать образцы по середине их длины и подготовить поверхности образцов по плоскости реза: на одном образце в виде микрошлифа, на другом образце – для определения твердости.
4. Изучить изменение структуры и распределение твердости по сечению образцов. Полученные данные свести в таблицу 3.
5. По данным, приведенным в таблицах 2 и 3, построить графики изменения твердости по сечению образцов. Сопоставить расчетные и экспериментальные зависимости и в случае необходимости объяснить их отличие друг от друга.
б. С использованием построенных экспериментальных зависимостей и номограммы прокаливаемости сталей оценить скорости охлаждения и построить графики изменения скоростей охлаждения по сечению образцов, охлажденных в разных средах.
7. Сформулировать выводы, включающие: сопоставление сред по охлаждающей способности, изучаемых сталей – по критическим скоростям охлаждения и критическим диаметрам прокаливаемости; рекомендации по использованию охлаждающих сред для каждой марки стали.
V. СОДЕРЖАНИЕ ОТЧЕТА
1. Привести краткие сведения из теории, включая:
- изотермические и термокинетические диаграммы распада аустенита в изучаемых сталях, сопоставление этих диаграмм, определение первой и второй критических скоростей охлаждения;
-описание охлаждающих сред и их особенностей;
- номограмму прокаливаемости сталей;
- полосы прокаливаемости изучаемых сталей.
2. Выполнить и описать все пункта, указанные в разделе 4.
ЛИТЕРАТУРА
1. Ю. М Лахтин, В. П. Леонтьева. Материаловедение. – М.: Машиностроение, 1980. – С.178...183.
2. Ю. А. Геллер, А. Г. Рахштадт. Материаловедение. – М.: Металлургия, 1983. – С.247.,.278.
3. Г. И. Сильман. Конструкционные стали. Рекомендации по выбору марки стали и вида ее обработки. – Брянск: Изд-во БГИТА, 1997. – 68 с.
4. Термическая обработка в машиностроении. Справочник /Под ред. Ю. М. Лахтина и А. Г. Рахштадта. – М.: Машиностроение, 1980. – С.169...187.
Рис. 1. Изотермическая (а) и термокинетическая (б) диаграммы превращения аустенита в стали 45 |
Рис. 2. Изотермическая (а) и термокинетическая (б) диаграммы превращения аустенита в стали 45Х
|
Рис. 3. Полосы прокаливаемости сталей
45 (а) и 45Х (б)
Лабораторная работа № 13
ИЗУЧЕНИЕ МИКРОСТРУКТУР УГЛЕРОДИСТЫХ И
ЛЕГИРОВАННЫХ СТАЛЕЙ ПОСЛЕ ХИМИКО-ТЕРМИЧЕСКОЙ ОБРАБОТКИ
I. ЦЕЛЬ РАБОТЫ: изучить влияние цементации и азотирования на структуру и свойства сталей.
П. КРАТКИЕ СВЕДЕНИЯ ИЗ ТЕОРИИ
Химико-термической обработкой (поверхностным легированием) называют обработку, заключающуюся в сочетании химического и термического воздействий на металлы и сплавы для изменения химического состава, структуры и свойств в поверхностных слоях.
Любой процесс химико-термической обработки (ХТО) состоит из трех элементарных процессов:
1. Образование во внешней среде активных атомов диффундирующего вещества, например, распад (диссоциация) аммиака с выделением активного азота по реакции:
2NH3 → 2Naт. + 3H2
или диссоциации окиси углерода с выделением атомарного углерода:
2СО → CO2 + Cат.
2. Адсорбция атомов и проникновение части этих атомов с установлением химических связей с атомами металла.
3. Диффузия, т.е. перемещение этих атомов во внутрь основного металла.
Из методов ХТО чаще всего применяют цементацию и азотирование. В данной работе изучаются структуры цементованных и азотированных сталей.
Цементацией (науглероживанием) называется ХТО, заключающаяся в диффузионном насыщении поверхностного слоя стали углеродом при нагреве в соответствующей среде – карбюризаторе. В зависимости от карбюризатора различают цементацию в твердой среде и газовую.
Конечной целью цементации является получение высокой твердости и износостойкости поверхностного слоя при сохранении вязкой и пластичной сердцевины. Поэтому для цементации используют низкоуглеродистые (0,1-0,25 %С), чаще легированные стали. К цементуемым относятся стали 10, 15, 20, 15Х, 18ХГТ, 12ХНЗА, 18Х2Н4ВА и др.
Цементацию проводят при температурах выше критической точки Асз цементуемой стали (870...970оС). Оптимальным поверхностным содержанием углерода в слое считается 0,8...1,1%. При пониженном содержании углерода не будет достигнута требуемая твердость поверхности (обычно более 58 HRC), а при повышенном – слой характеризуется чрезмерной хрупкостью. Глубина слоя чаще всего находится в пределах 0,6...1,3 мм; на крупногабаритных деталях она может достигать 4...6 мм.
Поскольку при цементации стали ее поверхность обогащается углеродом, микроструктура по сечению детали получается неоднородной (рис.1 и 2). У поверхности структура состоит из перлита и цементита (заэвтектоидная зона 1), далее располагается эвтектоидная зона 2 (структура – перлит) и переходная доэвтектоидная зона 3 (структура – перлит и феррит). За глубину цементованного слоя а принимают расстояние от поверхности до полуперлитной зоны 4 (50% перлита). Полуперлитной зоне соответствует содержание углерода ~0,4%. В зоне 5 преобладает структура феррита. В сердцевине детали сохраняются исходное содержание углерода и структура малоуглеродистой стали.
После цементации проводят термическую обработку деталей, которая должна обеспечить не только необходимую твердость и износостойкость поверхности, но и измельчить зерно, а также устранить карбидную сетку в цементованном слое, которая может возникнуть при насыщении его углеродом до заэвтектоидной концентрации.
В зависимости от марки цементуемой стали, температуры цементации, назначения деталей и других факторов возможны следующие основные технологические схемы цементации:
· цементация, медленное охлаждение, однократная закалка от температуры Ac1+(30...50)°C, низкотемпературный отпуск (для малоответственных деталей);
· цементация, медленное охлаждение, двойная закалка (первая – от температуры выше Ас3, вторая – от температуры Ac1+(30...50)°C), низкотемпературный отпуск (для тяжело нагруженных деталей ответственного назначения);
· цементация, подстуживание до оптимальных закалочных температур Ac1 + (30...50)°С, закалка с цементационного нагрева,низкотемпературный отпуск (для наследственно мелкозернистых сталей в случае газовой цементации).
После закалки в цементованном слое образуется структура мартенсита (или мартенсита и карбидов). Структура сердцевины после закалки получается различной в зависимости от химического состава стали. В углеродистых сталях в сердцевине сохраняется исходная структура (феррит + перлит), в легированных сталях образуется малоуглеродистый мартенсит или бейнит, что обеспечивает повышенную прочность деталей.
Заключительной операцией термической обработки цементованных деталей является низкий отпуск при 160…200°С, снимающий напряжения и переводящий мартенсит закалки в отпущенный мартенсит.
Цементация с последующей термической обработкой позволяет не только придать поверхностному слою высокую твердость и износостойкость, но и повысить предел выносливости, резко уменьшить чувствительность к концентраторам напряжений и значительно повысить прочностные свойства по всему сечению (табл.1). В связи с этим цементация рекомендуется для наиболее нагруженных деталей машин (зубчатые колеса, валы, шпиндели, вал-шестерни и др.).
Таблица 1
Механические свойства сталей после цементации
в образцах сечением 50 мм
Марка стали
| Режим обработки
| Свойства | ||||||
sв | s0,2 | s-1 | d | y | КСU, Дж/cм2
| Твердость, не менее | ||
МПа | %,не менее | |||||||
20 | Цементация. 920. ..950оС; .закалка 800…820оС; вода, отпуск 180… 200оС (ж180. 200"С. воздух | 490.. 590 | 290.. 340 | не менее 250 | 18 | 45 | не менее 54 | Сердцевина 156 НВ, поверхность 55 НRС |
18ХГТ | Цементация, 930...95011C•. закали 825...840°С, масло, отпуск 180…200оС, воздух | 1000 | 800 | 600 | 9 | 50 | 75 | Сердцевина 285 НВ, поверхность 57 НRС |
Азотированием называют процесс диффузионного насыщения поверхностного слоя металлов азотом. Цель азотирования – повысить твердость, износостойкость, усталостную прочность и сопротивление коррозии. Азотированию подвергают легированные стали, так как после азотирования углеродистых сталей достигается сравнительно невысокая твердость (до 700 НV). Это объясняется низкой твердостью и малой устойчивостью к коагуляции нитридов железа. В связи с этим азотированию подвергают стали, легированные элементами, образующими высокотвердые специальные нитриды (Мо, Сг, А1 и др.). При этом твердость азотированного слоя легированных сталей достигает 1000...1200 HV.
Азотирование в сравнении с цементацией имеет следующие преимущества: более высокую твердость поверхности, сохраняющуюся при нагреве до 500°С (твердость цементованного слоя снижается при нагреве выше 200°С), высокие сопротивляемость износу, предел выносливости и кавитационную стойкость; хорошую сопротивляемость коррозии в атмосфере, пресной воде и ее парах; небольшие деформации деталей при азотировании. Недостатки: низкая скорость насыщения и повышенная хрупкость азотированного слоя.
Различают два вида азотирования:
1.низкотемпературное (<590°С); используется для упрочнения сталей и чугунов при температурах ниже эвтектоидной на диаграмме Fe-N (рис.3);
2. высокотемпературное (600...1200°С); применяется для упрочнения сталей ферритного и аустенитного классов, тугоплавких металлов (Ti, Мо, Nb, W) и их сплавов.
Первый вид азотирования используется наиболее часто. Упрочнению подвергают среднеуглеродистые (0,3...0,45 %С) легированные стали 38Х2Ю, 38Х2МЮА, ЗОХ2Н2ВФА, 40ХНМА и др. Перед азотированием детали проходят термическую обработку (закалку и высокотемпературный отпуск), цель которой – получить вязкую сердцевину и подготовить структуру к азотированию. Последующее упрочняющее азотирование при 520... 560°С позволит получить слой 0,4...0,6 мм за 60...90 час. По окончании насыщения детали охлаждаются в среде аммиака до 20...200°С и обладают после этого требуемыми свойствами. Поэтому после азотирования термическая обработка не требуется.
Микроструктура азотированного слоя различна при насыщении азотом железа и специальной стали для азотирования (например, 38Х2МЮА). Из диаграммы состояния системы Fe-N (рис. З) видно, что при температуре азотирования выше эвтектоидной(591°С),например при 600°С (t1 на рис.3), образуются последовательно от поверхности к сердцевине следующие фазы:
e ® g ‘ ® g ® a,
где e –нитрид Fe2-3N; g ‘– нитрид Fe4N; g –азотистый аустенит,a –азотистый феррит.
При медленном понижении температуры фазыe иa будут распадаться с выделением избыточной фазы g ‘,а g -фаза будет полностью распадаться на эвтектоид a+g ‘.В связи с такими превращениями микроструктура азотированного слоя при комнатной температуре будет состоять из следующих фаз (от поверхности к сердцевине) (рнс.4):
a+g ‘ ® g ‘ ® a+g ‘.
При азотировании стали 38Х2МЮА образуются легированные фазы e, g ‘ иa;одновременно происходит образование нитридов легирующих элементов (Cr, Мо, А1). Резкого разграничения между фазами не наблюдается.
Микроструктура азотированного слоя стали 38Х2МЮА приведена на рис.5. На поверхности расположен очень тонкий (0,01…0,03 мм) нетравящийся белый слой, состоящий изe -фазы или e +g ‘-фаз(до глубины 0,06…0,1 мм). Далее располагается a -фаза. Основная (серая) часть азотированного слоя имеет сорбитообразное строение и отличается от сорбитной структуры тем, что травится более сильно вследствие высокого содержания азота.
Сталь 38Х2МЮА применяется для ответственных деталей тур-бино- и моторостроения, деталей точного машиностроения и приборостроения. Свойства этой стали приведены в табл.2.
Таблица 2
Механические свойства стали 38Х2МЮА до и после азотирования
в деталях толщиной до 60 мм
Состояние | Предварительная термообработка | sв | s0,2 | s-1 | d, % | KCU, Дж/см2 | Твердость | |
МПа | ||||||||
1 | 2 | 3 | 4 | 5 | 6 | 7 | 8 | |
До азотирования | Закалка 940оС, отпуск 640оС
| 850 | 1000 | 630 | 14 | 90 | Не более 229 НВ | |
После азотирования | 900 | 1050 | 630 | 18 | 90 | Сердцевина 269 НВ, поверхность 850…1050 HV | ||
Ш. НЕОБХОДИМЫЕ ПРИБОРЫ, ОБОРУДОВАНИЕ
И МАТЕРИАЛЫ
1. Микроскопы МИМ-7.
2. Микрошлифы сталей.
IV. МЕТОДИЧЕСКИЕ УКАЗАНИЯ И СОДЕРЖАНИЕ ОТЧЕТА
1. Привести краткие сведения из теории с характеристикой различных видов ХТО и процессов, протекающих при насыщении поверхности сталей углеродом и азотом. Указать основные свойства сталей после диффузионного насыщения и применение ХТО.
2. Посмотреть под микроскопом микроструктуры сталей после химико-термической обработки.
3. Зарисовать по две микроструктуры для каждой стали и каждого вида химико-термической обработки (в поверхностном слое и в сердцевине). По микроструктурам определить глубину цементованного и азотированного слоев.
4. Под каждой микроструктурой указать марку стали, вид обработки, наименование структуры и увеличение микроскопа, соответствующее зарисованной структуре. На каждом рисунке указать стрелками структурное состояние соответствующей зоны.
5. Графически представить изменение содержания углерода в зависимости от расстояния от поверхности цементованной стали. Обозначить каждую зону и дать ее краткую характеристику.
6. Изобразить диаграмму состояния Fe-N и дать описание происходящих превращений.
ЛИТЕРАТУРА
1. Ю. М Лахтин, В. П. Леонтьева. Материаловедение. – М: Машиностроение, 1980.
2. Б. Г. Гринберг, Т. М. Иващенко. Лабораторный практикум но металловедению и термической обработке. – М.: Высшая школа, 1968.
3. А. И Самохоцкий, М. Н. Кунявский. Лабораторные работы по металловедению. – М.: Машиностроение, 1971.
4. А. К. Минкевич. Химико-термическая обработка металлов и сплавов. – М.: Машиностроение, 1965.
Лабораторная работа № 14
ИЗУЧЕНИЕ ТЕРМИЧЕСКОЙ ОБРАБОТКИ, СТРУКТУРЫ
И СВОЙСТВ БЫСТРОРЕЖУЩИХ СТАЛЕЙ
I. ЦЕЛЬ РАБОТЫ: изучить особенности быстрорежущих сталей и формирование их структуры в свойств в процессе термической обработки.
П. КРАТКИЕ СВЕДЕНИЯ ИЗ ТЕОРИИ.
Быстрорежущие стали относятся к классу инструментальных и предназначены для изготовления режущего инструмента, работающего при повышенных скоростях резания. Быстрорежущие стали должны обладать рядом особых свойств:
- высокой горячей твердостью (т.е. в горячем состоянии);
- высокой теплостойкостью (или красностойкостыо), т.е. способностью сохранять достаточно длительное время высокую твердость и режущие свойства при нагреве инструменте в процессе работы до высоких температур;
- высокой прокаливаемостыо, обеспечивающей возможность использования этих сталей для изготовления массивного и сложного инструмента;
- малой деформацией при закалке;
- хорошими технологическими свойствами (хорошей обрабатываемостью резанием в отожженном состоянии, малой склонностью к перегреву и обезуглероживанию при нагреве);
- достаточно высокими механическими свойствами, прежде всего, прочностью и сопротивлением хрупкому разрушению.
Быстрорежущие стали сохраняют мартенситную структуру и соответственно высокую твердость, прочность, износостойкость и режущие свойства при нагреве до 600...620°С (т.е. имеют теплостойкость 600...620°С). Достигается это за счет особого химического состава стали и специальной термической обработки инструмента.
Быстрорежущие стали относятся к группе сталей карбидного класса (называемых иногда ледебуритными). Содержание углерода в них составляет обычно 0,7...1,0%, хотя в некоторых марках сталей повышено до 1,2...1,5%. Основным легирующим элементом в быстрорежущих сталях является вольфрам. Во всех марках этих сталей присутствует также хром (около 4%) и ванадий (1,0...2,5%). В некоторых сталях вольфрам частично заменен молибденом. В последнее время разработаны и используются также безвольфрамовые стали с молибденом. Для повышения теплостойкости и горячей твердости стали дополнительно легируют кобальтом или повышенным количеством ванадия (т.н. "сверхбыстрорежущие стали").
Быстрорежущие стали маркируют буквой Р (от слове “рапид” – скорость). Первое число показывает содержание вольфрама в процентах, затем после букв M, Ф или K указывается содержание в процентах соответствующих элементов (молибдена, ванадия или кобальта).
В табл.1 приведены составы наиболее часто применяемых быстрорежущих сталей в соответствии с ГОСТ 19265-73.
Таблица 1
Марки и химические составы быстрорежущих сталей
Марки сталей
| Содержание элементов, %
| |||||
С | Cr | W | Мo | V | Со | |
Р18 | 0,73...0,83 | 3,8...4,4 | 17...18,5 | <1,0 | 1,0...1,4 | - |
Р12 | 0,80...0,90 | 3,1...3,6 | 12...13 | <1,0 | 1,5…1,9 | - |
Р9 | 0,85...0,95 | 3,8...4,4 | 8,5...10 | <1,0 | 2,0…2,6 | - |
P6M5 | 0,82...0,90 | 3,8...4,4 | 5,5…6,5 | 4,8...5,3 | 1,7…2,1 | - |
Р12ФЗ | 0,95...1,05 | 3,8...4,4 | 12...13 | <1,0 | 2,5...3,0 | - |
Р9К5 | 0,90...1,00 | 3,8...4,4 | 9...10 | <1,0 | 2,3...2,7 | 5...6 |
Р6М5ФЗ | 0,95...1,05 | 3,8...4,3 | 5,7...6,7 | 4,8...5,3 | 2,3...2,7 | - |
Р6М5К5 | 0,86...0,94 | 3,8...4,3 | 5,7...6,7 | 4,8..5,3 | 1,7...2,1 | 4,7...5,2 |
Р6М5Ф2К8 | 0,95...1,05 | 3,8...4,4 | 5,5...6,6 | 4,6..5,2 | 1,8...2,4 | 7,5...8,5 |
Наиболее широко используется в настоящее время экономно легированная сталь Р6М5.
В литом состоянии структура быстрорежущих сталей состоит обычно из перлита и сложной эвтектики, напоминающей ледебурит и располагающейся в виде сетки по границам зерен перлита (рис.1). Для разрушения сетки эвтектики и достижения равномерного распределения карбидов эти стали подвергают ковке в отжигу, после чего они получают дисперсную сорбито-карбидную структуру (рис.2,а).
Для получения высоколегированного мартенсита инструмент из быстрорежущей стали нагревают под закалку до высоких температур (обычно 1210...1290°С). Во избежание образования трещин нагрев стали производят медленно, чаще всего с одним-двумя подогревами (при 350...450 и 800...845°С).
Длительность выдержки при максимальной температуре (1210 ...1290°С) рассчитывают по упрощенной формуле
,
где – время сквозного прогрева, – время изотермической выдержки после прогрева. Для одномерного инструмента при нагреве в соляных ваннах (при L/D > 3, где L - длина, D - диаметр)
, мин.,
где n – коэффициент, зависящий от температуры нагрева и формы инструмента. Для инструмента цилиндрической формы при tзак= 1210...1230°С и нагреве в расплаве BaCl2 принимают n = 7,8...7,4.
Величину рассчитывают, исходяиз химического состава стали:
,
где W, V и Мо характеризуют содержания соответствующих элементов в процентах.
Для сталей с повышенным содержанием ванадия может быть увеличено до 1,5 раз. Время изотермической выдержки иногда увеличивают на 20... 30% по сравнению с расчетным, например, для мелкопрофильного инструмента, а также для инструмента, от которого требуется повышенная теплостойкость.
Быстрорежущие стали обладают хорошей прокаливаемостыо, имеют невысокую критическую скорость закалки. Поэтому их можно охлаждать в масле или даже в струе воздуха. Для уменьшения закалочных деформаций рекомендуется ступенчатая закалка в солевых расплавах при 1б0...200°С.
Точка Мк для быстрорежущих сталей лежит при отрицательных температурах. Поэтому структура стали после закалки содержит кроме мартенсита и карбидов большое количество остаточного аустенита (25...30%) (рис.2,б). Для устранения остаточного аустенита инструмент после закалки подвергают многократному (чаще всего трехкратному) отпуску (рис.3,а) или обработке холодом с последующим одно- или двукратным отпуском при 560°С (рис.3,б). Микроструктура стали после окончательной термической обработки состоит из мартенсита отпуска и специальных карбидов Fe3(W,Mo)3C, упрощенно обозначаемых как М6С, где М – металл (см. рис.2,в). Перевод остаточного аустенита в мартенсит отпуска обеспечивает повышение общей твердости стали на 2...3 единицы HRC (рис.4). Это явление повышения твердости стали при отпуске называют вторичным твердением, а саму термическую обработку инструмента – обработкой на вторичную твердость.
Перед изготовлением инструмента заготовка из быстрорежущей стали должна быть хорошо отожжена. Обычно проводят изотермический отжиг: сталь нагревают до 860...900°С, выдерживают, охлаждают до 700...750°С и выдерживают в этом интервале температур до окончания превращения аустенита (обычно 1,5...2 часа). После такого отжига твердость вольфрамовых и вольфрамомолибденовых сталей должна составлять 207...255 НВ. У сталей, дополнительно легированных кобальтом или ванадием, твердость после отжига может быть повышенной до 269 НВ.
В плохо отожженной стали после закалки наблюдается особый вид брака, называемый нафталиновым изломом. Такая сталь при нормальной твердости оказывается очень хрупкой, а ее излом – грубозернистым, чешуйчатым, напоминающим нафталин.
Другим видом брака, зависящим от предварительной обработки, является карбидная ликвация (карбидная неоднородность), представляющая собой остатки участков эвтектики, не разбитых ковкой. Карбидная ликвация увеличивает хрупкость инструмента и понижает его стойкость в работе. Методика определения карбидной неоднородности приведена в приложении.
Рекомендуемые режимы термической обработки и свойства некоторых быстрорежущих сталей приведены в табл.2.
Таблица 2
Термическая обработка и твердость некоторых
быстрорежущих сталей
Марка стали
| Вид термической обработки
| ||||||
Отжиг | Закалка
| Отпуск*
| |||||
Тверд. НВ, не более | Температура, "С | Колич. Aост., % | Тверд.HRCЭ | Темпе-ратура, оС | Число отпус- ков | Тверд НRСЭ | |
Р18 | 255 | 1270... 1290 | ~30 | 62...64 | 560... 580 | 3 | 64...66 |
Р12 | 255 | 1240... 1260 | 25...30 | 62...64 | 550... 570 | 3 | 64...66 |
Р9 | 255 | 1220... 1240 | 25...30 | 62..64 | 550... 570 | 3 | 64...66 |
Р6М5 | 255 | 1210... 1230 | 25...30 | 62...64 | 550... 560 | 2...3 | 64...66 |
Р6М5К5 | 269 | 1210... 1230 | 25...30 | 63...65 | 560... 580 | 3 | 67...68 |
Ш. НЕОБХОДИМЫЕ ПРИБОРЫ, ОБОРУДОВАНИЕ
И МАТЕРИАЛЫ
1. Термические печи.
2. Микроскопы МИМ-7.
3. Установка для приготовления шлифов.
4. Образцы из быстрорежущей стали.
IV. МЕТОДИКА ПРОВЕДЕНИЯ РАБОТЫ
При проведении работы используются образцы, вырезанные из заготовок, прошедших предварительную обработку (ковку и отжиг). Два образца исследуются в отожженном состоянии: определяется твердость и проводится микроанализ для оценки карбидной неоднородности. Остальные образцы подвергаются закалке и отпуску (отпуск от одно- до трехкратного) по средним режимам, приведенным в табл.2. После каждого вида термической обработки определяется твердость и изучается микроструктура (оценивается наличие в структуре стали мартенсита, карбидов и остаточного аустенита). Результаты испытаний заносятся в табл.3.
Таблица 3
Результаты экспериментального исследования стали
Вид термообработки | Режим термообработки | Твердость | Особенности микроструктуры | |
Температура, оС | Время выдержки, мин. | |||
Отжиг | Карбидная неодно-родность, балл … | |||
Закалка | ||||
Отпуск однократный | ||||
Отпуск двукратный | ||||
Отпуск трехкратный |
По результатам исследований строятся график режима термической обработки (по аналогии с рис.3) и график изменения твердости стали.
V. СОДЕРЖАНИЕ ОТЧЕТА
1. Дать краткое описание особенностей химического состава, маркировки, термической обработки и свойств быстрорежущих сталей.
2. Зарисовать микроструктуры быстрорежущей стали в литом состоянии, после отжига, в закаленном состоянии и после окончательной термической обработки. На каждом рисунке указать структурные составляющие.
3. Провести расчет длительности выдержки при температуре нагрева под закалку.
4. Привести таблицу 3, заполненную результатами исследований.
5. По данным таблицы 3 построить графики режима термической обработки и изменения твердости стали.
6. Сопоставить полученные экспериментальные данные с известными данными, приведенными в табл.2 в на рис.4. В случае заметных различий объяснить их причину.
ЛИТЕРАТУРА
1. Ю. М. Лахтин, В. П. Леонтьева. Материаловедение. – М.: Машиностроение. 1980. – С.310-315.
2. А. П. Гуляев. Металловедение. – М.: Металлургия. 1986. –С.360-369.
3. Ю. А. Геллер. Инструментальные стали. – М: Металлургия. 1968. – С.316-340.
ПРИЛОЖЕНИЕ
Карбидная ликвация в быстрорежущей стали (ГОСТ 19265-73)
В быстрорежущей стали карбидная неоднородность оценивается по трем шкалам при увеличении 100: по шкале №1 – для прутков из сталей с высоким содержанием вольфрама (Р12, Р18, Р18Ф2, Р14Ф4, Р18К5Ф2, Р10К5Ф5, Р9К10, Р9М4К8); пo шкале №2 – для прутков из низковольфрамовой и вольфрамомолибденовой сталей (Р6МЗ, Р6М5, Р9К5, Р6М5К5); по шкале №3 – для шайб толщиной 10...12 мм, вырезанных из сортового проката. Характеристика первых двух шкал приведена в таблице.
Балл карбидной ликвации
| Описание карбидной составляющей
| Допустимая ширина полос* или скоплений карбидов, мм, по шкале
| |
№ 1 | № 2 | ||
1 | 2 | 3 | 4 |
1 | Тонкая полосчатая структура с короткими разорванными полосами | 2 | 1 |
2 | Полосчатая структура, единичные или множественные полосы. Карбиды внутри полос раздроблены | 4 | 2 |
3 | А. Полосчатая структура, единичные или множественные полосы. Карбиды внутри полос раздроблены Б. Остатки карбидной сетки. Сетка с раздробленными карбидами | б | 4 |
4 | А. Полосчатая структура, единичные или множественные полосы. Карбиды внутри полос раздроблены Б. Слабо выраженная разорванная сетка со скоплениями | 8 | 5 |
5 | А. Грубополосчатая структура, еди-ничные или множественные полосы. . Б. Отчетливо выраженная сетка со скоплениями | 13 | 6 |
1 | 2 | 3 | 4 |
6 | А Грубополосчатая структура, еди-ничные или множественные полосы. Б. Явно выраженная разорванная сетка с малоразорванными ячейками, скопления | 15 | 9 |
7 | Сетка, разорванная в отдельных местах, скопления | 20 | 14 |
8 | Малодеформированная разорванная сетка и скопления | 25 | 18 |
Примеры структур стали Р6М5 с разным баллом карбидной неоднородности приведены ниже на рисунках при стандартном увеличении 100 раз. Балл карбидной неоднородности указан в правом нижнем углу каждой структуры
Лабораторная работа № 15
ИЗУЧЕНИЕ ОСОБЕННОСТЕЙ ТВЕРДЫХ СПЛАВОВ
I. ЦЕЛЬ РАБОТЫ: изучить особенности химического состава, структуры, свойств, получения и применения твердых сплавов.
II. КРАТКИЕ СВЕДЕНИЯ ИЗ ТЕОРИИ
К твердым инструментальным сплавам обычно относят гетерогенные материалы, получаемые путем спекания из порошков и состоящие из зерен тугоплавких высокотвердых соединений (карбидов, реже нитридов или боридов переходных металлов), связанных между собой пластичным металлом (кобальтом, никелем, реже железом, или их сплавами). В качестве тугоплавкой фазы твердых сплавов чаще всего используются карбиды вольфрама, титана, тантала, хрома или их смеси.
Для получения изделий из твердых сплавов используют методы порошковой металлургии. Из дисперсных смесей порошков тугоплавкой фазы и связки изделия прессуют, а затем прессовки подвергают спеканию при температурах ниже температуры плавления тугоплавких соединений. При спекании связующая фаза оплавляется, растворяя некоторую долю тугоплавкой фазы.
Металлокерамические (спекаемые) твердые сплавы имеют высокую твердость (80–92 HRA) и теплостойкость (до 900–1000 оС), что обеспечивает им существенно более высокие режущие свойства по сравнению с быстрорежущими сталями.
Твердые сплавы подразделяют на вольфрамосодержащие и безвольфрамовые. В свою очередь, вольфрамосодержащие сплавы в соответствии с ГОСТ 3882–74 делятся на три группы: вольфрамовые, титановольфрамовые и титанотанталовольфрамовые. В качестве связки в этих сплавах используется кобальт.
Сплавы вольфрамовой группы изготавливают из смеси порошков карбида вольфрама и кобальта (WC + Co). Их маркируют буквами ВК и числом, показывающим содержание кобальта в процентах (остальное – карбид вольфрама). По ГОСТ 3882–74 основными сплавами этой группы являются ВК3, ВК3-М, ВК4, ВК4-В, ВК6, ВК6-М, ВК6-ОМ, ВК8, ВК10, ВК10-М, ВК10-ОМ, ВК15, ВК20, ВК25.
Титановольфрамовые сплавы (WC + TiC + Co) маркируют буквами ТК. Числа после букв Т и К показывают соответственно содержание карбидов титана и кобальтовой связки в процентах (остальное – карбид вольфрама). По ГОСТ 3882–74 к этой группе относятся сплавы Т30К4, Т15К6, Т14К8, Т5К10, Т5К12.
Сплавы титанотанталовольфрамовой группы (WC + TiC + TaC + Co) маркируют буквами ТТК. После букв ТТ указывают суммарное содержание карбидов титана и тантала, а после буквы К – содержание кобальта в процентах. К сплавам этой группы относятся ТТ7К12, ТТ8К6, ТТ10К8, ТТ20К9.
В маркировке некоторых сплавов имеются дополнительные обозначения. Если в марке стоит буква “М” (например, ВК6-М), сплавы изготовлены из мелких порошков (с размером зерен 1-2 мкм), если “В” (ВК4-В) – из крупнозернистого карбида вольфрама (2-3 мкм), если “ОМ” – из особо мелких порошков (до 1 мкм), если “ВК” – из особо крупного карбида вольфрама (до 5 мкм).
Чем меньше в сплавах группы ВК кобальта и мельче карбидные частицы, тем выше их износостойкость, но ниже прочность и сопротивление ударам. Сплавы ВК3 и ВК3-М используются для чистовой обработки с высокой скоростью резания чугунов, цветных металлов и неметаллических материалов.
Сплавы ВК4, ВК6, ВК6-М, ВК8 рекомендуются для чернового точения, фрезерования, рассверливания, зенкерования при обработке чугуна, жаропрочных сплавов, цветных сплавов и неметаллических материалов. Сплав ВК8 применяют также для волочения и калибровки труб, прутков и проволоки.
Сплавы ВК10 и ВК15 используют для изготовления быстроизнашивающихся деталей различных конструкций. Сплавы ВК20 и ВК25 применяются для изготовления изнашиваемых деталей штампов. Эти сплавы характеризуются высокой эксплуатационной прочностью, но износостойкость их ниже, чем у малокобальтовых сплавов.
Из сплавов группы ТК наибольшей износостойкостью и допустимой скоростью резания обладает сплав Т30К4. У сплавов Т15К6 и Т5К10 износостойкость и скорость резания ниже, но эксплуатационная прочность выше. Сплавы этой группы применяют для чистовой (Т30К4) и черновой (Т15К6, Т5К10) обработки стали.
Сплавы группы ТТК применяют для черновой и чистовой обработки труднообрабатываемых материалов, в том числе жаропрочных сталей и сплавов.
Безвольфрамовые твердые сплавы являются более экономичными, так как не содержат соединения дорогостоящего и дефицитного вольфрама. Их выпускают на основе карбида титана (TiC + Ni + Mo), например, сплав ТН20 (где 20 – суммарное содержание никеля и молибдена, остальное – карбид титана), или карбонитрида титана (Ti(C,N) + Ni + Mo), например, КНТ16. Никель и молибден играют роль связки. Применяют эти сплавы при получистовом и чистовом точении и фрезеровании сталей и цветных сплавов.
К безвольфрамовым относятся также карбидохромовые сплавы КХН (где КХ – карбид хрома, Н – никель), например, КХН-10…КХН-35 (число показывает содержание никеля в процентах). Эти сплавы не окисляются на воздухе при нагреве до 1000–11000С, обладают хорошей коррозионной стойкостью и износостойкостью. Область применения примерно та же, что и сплавов ТН и КНТ.
Твердые сплавы выпускают в виде многогранных неперетачиваемых пластин, которые крепят к корпусу или державке инструмента механическим методом или припаивают.
Примеры микроструктуры сплавов приведены на рис.1. В структуре сплава ВК3 (рис.1,а) кристаллы карбида WC имеют вид светлых угловатых зерен; кобальтовая прослойка располагается по границам зерен и при оптической металлографии четко не выявляется; темные участки на шлифе – преимущественно поры.
В микроструктуре сплава Т15К6 (рис.1,б) более 50% занимает карбид (Ti,W)C (темные крупные карбидные частицы). Из диаграммы состояния WC–TiC, приведенной на рис.2, видно, что в карбиде титана может растворяться значительное количество вольфрама. По этой же диаграмме можно оценить микроструктуру и других сплавов типа ТК. Так, например, в структуре сплава Т30К4 (рис.1,в) присутствует только комплексный карбид (Ti,W)C в виде округлых зерен. Темные прослойки на фотографии микроструктуры представляют собой кобальтовую связку и мелкие поры.
III. НЕОБХОДИМЫЕ ПРИБОРЫ И МАТЕРИАЛЫ
1. Микроскопы МИМ-7.
2. Микрошлифы твердых сплавов.
IV. МЕТОДИЧЕСКИЕ УКАЗАНИЯ И СОДЕРЖАНИЕ
ОТЧЕТА
1. Привести классификацию и дать краткую характеристику каждой группы сплавов. Разобраться с маркировкой сплавов и привести ее в отчете. Указать области применения каждого вида сплавов.
2. Привести диаграмму WC – TiC и указать на ней положение сплавов групп ВК и ТК.
3. Посмотреть под микроскопом и зарисовать микроструктуры твердых сплавов. На каждом рисунке стрелками указать структурные составляющие. Под каждой микроструктурой указать марку сплава и увеличение микроскопа.
Л И Т Е Р А Т У Р А
1. Лахтин Ю.М., Леонтьева В.П. Материаловедение. – М.: Машиностроение, 1990. – С.364–366.
2. Конструкционные материалы. Справочник./ Под общей ред. Б.Н.Арзамасова. – М.: Машиностроение, 1990. – С.613–626.
3. Гуляев А.П. Металловедение. – М.: Металлургия, 1986. – С.379–382.
4. Энциклопедия неорганических материалов. Т.2. – Киев: Главная редакция украинской советской энциклопедии, 1977. – С.505–508.
Рис.1. Микроструктура твердых сплавов, х100:
а – ВК3; б – Т15К6; в – Т30К4.
Лабораторная работа № 16
МЕДЬ И СПЛАВЫ НА ЕЕ ОСНОВЕ.
ПОДШИПНИКОВЫЕ СПЛАВЫ
I. ЦЕЛЬ РАБОТЫ: изучить микроструктуру, свойства и применение медных и подшипниковых сплавов, а также связь между структурой сплавов и соответствующими диаграммами состояния.
II. КРАТКИЕ СВЕДЕНИЯ ИЗ ТЕОРИИ
Медь– металл, имеющий температуру плавления 1083°С, плотность 8,94 г/см3, кристаллическую решетку ГЦК. Медь имеет ряд ценных технических свойств: высокую пластичность, высокие электро- и теплопроводность, малую окисляемость. В зависимости от химического состава установлены следующие марки меди: MOO (99,99%Cu), МО (99,95%Cu), M1 (99,90%Сu), М2 (99,70%Cu), МЗ (99,50%Cu), M4 (99,0°/oCu), остальное – примеси (висмут, свинец и др.).
Механические свойства меди приведены в табл. 1.
Таблица 1
Состояние меди | sв , МПа (кгс/мм2) | d , % |
Литая | 147,2-196,2 (15-20) | 15-25 |
Отожженная | 245,3-264,9 (25-27) | 40-50 |
Прокатанная | 392,4-421,8 (40-43) | 1-2 |
Сплавы меди
Важнейшими медными сплавами являются латуни и бронзы.
Латуни – это сплавы меди с цинком. Цинка в латунях содержится до 45% . Различают двойные и многокомпонентные (специальные) латуни, содержащие дополнительные (легирующие) элементы.
Двойные латуни маркируются буквой Л, следующая за ней цифра обозначает содержание меди. Например, Л96 (Л - латунь, 96% Cu, остальное – Zn).
Фазовое состояние латуней описывается диаграммой состояния системы Cu-Zn (рис.1). Структура латуней состоит изa или a +b¢ -фаз, где a -фаза – твердый раствор замещения цинка в меди, имеет решетку ГЦК, высокую пластичность, низкие значения прочности и твердости; b¢-фаза – упорядоченный твердый раствор на базе химического соединения CuZn с кристаллической решеткой ОЦК. Эта фаза характеризуется более высокой твердостью, чем a-фаза, и хрупкостью. При нагреве в интервале 454...468°С нарушается упорядоченное расположение атомов в ОЦК-решетке b¢-фазы и она обозначается как b-фаза. Нарушение упорядоченности повышает пластичность b-фазы.
Таким образом, в зависимости от содержания цинка латуни подразделяются на 2 группы:
1) однофазные a -латуни (до 39 % Zn);
2) двухфазные a +b¢-латуни (от 39 до 45 % Zn).
Однофазные латуни хорошо обрабатываются давлением в горячем и холодном состояниях. Двухфазные латуни имеют более высокую прочность и износостойкость, чем однофазные. Присутствие в двухфазных латунях хрупкой b¢-фазы затрудняет ее деформацию в холодном состоянии. Поэтому они подвергаются пластической деформации при высоких температурах.
Микроструктуры однофазной и двухфазной латуней приведены на рис.2.
Для повышения механических и технологических характеристик и придания латуням специальных свойств их легируют. Легирующие элементы обозначаются буквами: А – А1, Ж – Fe, Мц – Мп, К – Si, Н – Ni, О – Sn, С – РЬ, Т – Ti, Ф – Р, Ц – Zn и т. д. В марке многокомпонентной латуни после букв следуют цифры через дефис. Первая цифра указывает среднее содержание меди, остальные – содержания соответствующих легирующих элементов. Содержание цинка определяется по разности до 100%. Например, латунь ЛМцЖ55-3-1 содержит (в среднем) 55% Сu, 3% Мn, 1% Fe, остальное – Zn.
Вследствие небольшого интервала кристаллизации латуней дендритная ликвация у них выражена слабо, но они склонны к образованию концентрированной усадочной раковины. Двойные латуни применяют чаще как деформируемые(а не литейные) сплавы для изготовления труб, фольги, листов, лент и изделий из них.
Специальные латуни используют как деформируемые и литейные сплавы в машиностроении (гайки нажимных винтов, подшипники, антифрикционные детали, арматура) и других отраслях промышленности.
Бронзы - сплавы меди с оловом, свинцом, алюминием, никелем, фосфором, марганцем, железом, бериллием и другими элементами, вместе с которыми может присутствовать и цинк. По основному легирующему элементу их подразделяют на оловянные (оловянистые), алюминиевые, бериллиевые и т. д.
Маркируют бронзы буквами Бр, а затем, как и в латунях, указывают основные легирующие элементы и их среднее содержание в сплаве. Например, бронза БрАЖН 10-4-4 содержит в среднем 10%Al, 4%Fe, 4%Ni, остальное Сu. Различают литейные и деформируемые бронзы. В оловянистых литейных бронзах сумма легирующих элементов составляет от 11 до 30% (БрОФ 10-1, БрОЦС 3-12-5, БрОС 5-25), а в деформируемых – лишь 4…11% (БрОФ 4-0,25, БрОЦС 4-4-2,5).
На рис.3 приведена часть диаграммы состояния сплавов Сu-Sn. В структуре сплавов в равновесном состоянии можно выделить следующие фазы:
a -фаза – твердый раствор замещения Sn в Сu;
b, d и e -фазы – соединения Cu5Sn, Cu31Sn8 и Cu3Sn соответственно.
Как видно из диаграммы, сплавы системы Сu-Sn имеют ряд перитектических превращений и два превращения эвтектоидного типа.
Оловянистые бронзы склонны к ликвации, при ускоренном охлаждении они получают резко выраженное дендритное строение (рис.4).
В практике применяют лишь сплавы с содержанием до 10...12% Sn. Сплавы, более богатые оловом, очень хрупки.
Бронзы, содержащие до 4...5% Sn, являются однофазными (со структурой a -фазы), при большем содержании олова – двухфазными со структурой a + эвтектоид a +d.
Обработке давлением подвергаются только однофазные бронзы.
Оловянные литейные бронзы применяются для сложного фасонного литья, шестерен, втулок, гаек, ходовых винтов, корпусов кранов, червячных колес, арматуры для водяных и паровых систем. Деформируемые бронзы используют для сеток целлюлозно-бумажной промышленности, лент, полос, пружинной проволоки.
Подшипниковые сплавы
К наиболее распространенным подшипниковым материалам относятся антифрикционные сплавы на оловянистой и свинцовистой основах. Эти сплавы называютсябаббитами.
Баббиты на основе олова являются сплавами тройной системы Sn-Sb-Сu. Маркируют их буквой Б, за которой следует цифра, показывающая содержание основного компонента – олова (остальное – сурьма и медь). Например, Б83 – баббит, содержащий 83%Sn (остальное – 10…12%Sb и 5...7%Сu). Структура оловянистого баббита Б83 (рис.5) состоит из матричной фазы a (твердого раствора сурьмы и меди в олове), первичных кристаллов промежуточной фазы Cu3Sn и многогранных (полиэдрических) кристаллов фазы SnSb.
Баббит Б83 применяется для заливки подшипников тяжело нагруженных машин (например, турбин). Дешевым заменителем его является свинцовистый баббит Б16 (15...17%Sn, 15...17%Sb и 1,5...2%Cu, остальное – свинец). Он используется для изготовления подшипников скольжения высокоскоростных двигателей, хорошо воспринимает ударные и знакопеременные нагрузки.
Ш. НЕОБХОДИМЫЕ ПРИБОРЫ, ОБОРУДОВАНИЕ И МАТЕРИАЛЫ
1. Микроскопы МИМ - 7.
2. Микрошлифы меди, латуней, бронз, баббитов.
IV. МЕТОДИЧЕСКИЕ УКАЗАНИЯ И СОДЕРЖАНИЕ ОТЧЕТА
1. Привести краткую характеристику изучаемых сплавов, а также принципы маркировки меди, ее сплавов и баббитов. Указать области применения каждого вида сплавов.
2. Изобразить диаграммы состояния Сu-Zn и Сu-Sn, провести на них вертикальные линии, соответствующие рассматриваемым сплавам и проанализировать превращения, происходящие в сплавах.
3. Просмотреть под микроскопом и зарисовать микроструктуры меди, латуней, бронз и баббитов в кругах диаметром 30мм или квадратах со стороной 30мм.
4. На каждом рисунке микроструктур стрелками указать структурные составляющие.
5. Под каждой микроструктурой указать марку сплава и увеличение микроскопа.
ЛИТЕРАТУРА
1. Ю. М. Лахтин, В. П. Леонтьева. Материаловедение. – М.: Машиностроение, 1990. – С. 406-422.
2. Р. Н. Худокормова, Ф. И. Пантелеенко. Материаловедение. Лабораторный практикум. – Минск: Вышэйшая школа, 1988. – С. 180-192.
3. И. Л. Порода и др. Методические указания к лабораторным работам по материаловедению. – Запорожье, Изд-во ЗМИ, 1983. – С. 104 -108.
Рис.1 Диаграмма состояния сплавов медь-цинк и график влияния цинка на механические свойства медно-цинковых сплавов |
Рис. 2. Микроструктуры медно-цинковых сплавов (слева) и схемы их зарисовки (справа), х 200: а – однофазная латунь Л80; б – двухфазная латунь ЛС59-1
|
Рис. 3. Диаграмма состояния сплавов медь-олово |
Рис. 4. Микроструктура бронзы БрОЦ4-3 (слева) и схема зарисовки (справа), х 200: а – после литья (дендриты твердого раствора), б – после ковки и диффузионного отжига (однородные зерна твердого раствора) |
Рис. 5. Микроструктуры баббитов, х 200: а – оловянистого Б83, б – свинцовооловянистого Б16 |
Лабораторная работа № 17
ИЗУЧЕНИЕ ОСОБЕННОСТЕЙ АЛЮМИНИЕВЫХ СПЛАВОВ
I. ЦЕЛЬ РАБОТЫ: изучить особенности химического состава, структуры, свойств, получения и применения алюминиевых сплавов.
II. КРАТКИЕ СВЕДЕНИЯ ИЗ ТЕОРИИ.
Алюминий относится к легким металлам, т.к. его плотность менее 3 г/см3 (2,7 г/см3). Характерными свойствами алюминия являются высокая пластичность, сравнительно малая прочность, высокие теплопроводность, электропроводность, стойкость против окисления. Маркируется алюминий по степени чистоты, например, А99, где А – алюминий, 99 – степень чистоты 99,99%.
Алюминиевые сплавы подразделяют на несколько групп. Основными из них являются:
1). Деформируемые сплавы, не упрочняемые термической обработкой. Это сплавы систем Al-Mn и Al-Mg. Их маркируют соответственно АМц или АМг с цифрой в конце марки, означающей среднее содержание растворенного элемента, например, АМг2 (около 2%Mg).
Микроструктура сплавов в равновесном состоянии и их свойства увязываются с диаграммой состояния. Из диаграммы Al-Mg (рис.1) видно, что в равновесном (отожженном) состоянии структура сплавов, содержащих 2%Mg и более, имеет двухфазный характер, т.е. состоит из твердого раствора (a–фазы) и включений химического соединения Al3Mg2 (b-фазы).
Сплавы этой группы легко обрабатываются давлением, хорошо свариваются и обладают высокой коррозионной стойкостью. Применяют их для изготовления сварных и клепаных конструкций в судостроении, строительстве, для трубопроводов, емкостей для жидкостей и т.д. Для средненагруженных деталей и конструкций применяют сплавы АМг5 и АМг6 (в вагоностроении, судостроении и т.д).
2). Дюралюминий (дюралюмин) и другие деформируемые сплавы, упрочняемые термической обработкой. Дюралюминием называют сплав Al-Cu-Mg-Mn. Основой для рассмотрения структуры дюралюминия является диаграмма Al-Cu (рис.2). Маркируют его буквой Д и номером (например, Д1, Д16). Прочность дюралюминия после термической обработки, состоящей из закалки и старения, увеличивается более чем в 2 раза. Основными упрочняющими фазами в дюралюминах являются химические соединения CuAl2 и CuAl2Mg. Температура нагрева под закалку принимается в соответствии со схемой, приведенной на рис.2, и составляет для сплава Д16 485…5050С. Закалка обычно проводится в воде. Для этих условий критический диаметр прокаливаемости дюралюмина составляет 120…150 мм. Старение дюралюмина может быть как естественным (несколько суток), так и искусственным (10…20 часов при 150…2000С). Микроструктура сплава Д16 после закалки и старения приведена на рис.4, а химические составы и свойства некоторых термообрабатываемых алюминиевых сплавов – в табл.1.
3). Алюминиевые ковочные сплавы, применяемые для изготовления поковок и штамповок (иногда эти сплавы применяют и для изготовления отливок). Это сплавы многокомпонентной системы Al-Cu-Si-Mn-Mg (см. табл.1). Маркируют их буквами АК и цифровым номером (например, АК6, АК8). Обычно эти сплавы подвергают закалке и естественному старению.
4). Литейные алюминиевые сплавы. В основном это сплавы систем Al-Si (силумины), Al-Cu, Al-Mg, иногда с дополнительными элементами (см. табл.1). Наиболее часто используют силумины АЛ2, АЛ4, АЛ9 (здесь А – алюминиевый, Л – литейный, цифра – номер сплава). Из диаграммы Al-Si (рис.3) видно, что силумины чаще всего являются эвтектическими или доэвтектическими сплавами. Для измельчения микроструктуры и соответствующего повышения свойств силумины модифицируют (добавками титана, бора, солей натрия и др.). Модифицирование влияет на положение линий диаграммы (см. рис.3) и на характер микроструктуры (например, переводя эвтектический или даже заэвтектический силумин в доэвтектический) (рис.4).
Таблица 1
Сплав | Содержание элементов, % | Механические свойства | |||||||
Cu | Mg | Mn | Si | Другие элементы | sВ | s0,2 | d | ||
МПа | % | ||||||||
1 | 2 | 3 | 4 | 5 | 6 | 7 | 8 | 9 | |
Д ю р а л ю м и н ы | |||||||||
Д1 | 3,8-4,8 | 0,4-0,8 | 0,4-0,8 | - | - | 490 | 320 | 14 | |
Д16 | 3,8-4,9 | 1,2-1,8 | 0,3-0,9 | - | - | 540 | 400 | 11 | |
Продолжение таблицы 1
1 | 2 | 3 | 4 | 5 | 6 | 7 | 8 | 9 |
Ковочные сплавы | ||||||||
АК6 | 1,8-2,6 | 0,4-0,8 | 0,4-0,8 | 0,7-1,2 | - | 420 | 300 | 12 |
АК8 | 3,9-4,8 | 0,4-0,8 | 0,4-1,0 | 0,6-1,2 | - | 480 | 380 | 10 |
Литейные сплавы | ||||||||
АЛ2 | - | - | - | 10-13 | - | 180 | 90 | 5 |
АЛ4 | - | 0,17 -0,3 | 0,25 –0,5 | 8-10,5 | До 0,1 Ве | 260 | 200 | 4 |
АЛ7 | 4-5 | - | - | - | До 0,2 Ti | 260 | 200 | 3 |
АЛ8 | - | 9,5-11,5 | - | - | До 0,07 Ti, до 0,07 Be | 250 | 170 | 10 |
АЛ9 | - | 0,2-0,4 | - | 6-8 | До 0,15 Ti, до 0,1 Be | 220 | 160 | 3 |
Примечание: свойства сплава АЛ2 приведены в отожженном состоянии, для остальных сплавов – после закалки и старения.
III. НЕОБХОДИМЫЕ ПРИБОРЫ И МАТЕРИАЛЫ
· Микроскопы МИМ-7.
· Микрошлифы алюминиевых сплавов.
IV. МЕТОДИЧЕСКИЕ УКАЗАНИЯ И СОДЕРЖАНИЕ
ОТЧЕТА
1. Привести классификацию и дать краткую характеристику каждой группы сплавов. Разобраться с маркировкой сплавов и привести ее в отчете. Указать особенности химического состава, упрочняющей обработки (в том числе и термической), микроструктуры и свойств каждого вида сплавов.
2. Привести диаграммы состояния сплавов Al-Mg, Al-Cu, Al-Si и использовать их для объяснения структурных особенностей сплавов.
3. Посмотреть под микроскопом и зарисовать микроструктуры дюралюмина и силуминов. На каждом рисунке стрелками указать структурные составляющие. Под каждой микроструктурой указать марку сплава и увеличение микроскопа.
ЛИТЕРАТУРА
1. Ю. М. Лахтин, В.П. Леонтьева. Материаловедение. – М.: Машиностроение, 1990. – С.364–401.
2. Конструкционные материалы. Справочник./ Под общей ред. Б. Н. Арзамасова. – М.: Машиностроение, 1990. – С.234–272.
3. Гуляев А.П. Металловедение. – М.: Металлургия, 1986. – С.478–504.
Рис.1. Часть диаграммы состояния сплавов Al–Mg.
|
Рис.2. Часть диаграммы состояния сплавов Al–Cu.
|
Рис.3. Часть диаграммы состояния сплавов Al–Si
Рис.4. Микроструктуры сплавов, x300:
а – дюралюмин Д16 после закалки и старения,
б – силумин АЛ2 до модифицирования,
в – силумин АЛ2 после модифицирования.
* Конодой называется отрезок прямой линии, соединяющей точки, характеризующие составы фаз (или структурных составляющих), находящихся в равновесии.
* Под концентрацией понимается содержание одногоизкомпонентов в рассматриваемой фазе или в сплаве.
* Критической скоростью охлаждения называют минимальную скорость охлаждения, обеспечивающую только бездиффузионное превращение аустенита.
* Длительность выдержки при каждом отпуске составляет 60 минут.
* За полосу принимается скопление карбидов, длина которого больше или равна пятикратной ширине. Две лежащие рядом полосы принимаются за одну, если расстояние между ними меньше ширины более узкой полосы.
Дата добавления: 2018-04-05; просмотров: 356; Мы поможем в написании вашей работы! |
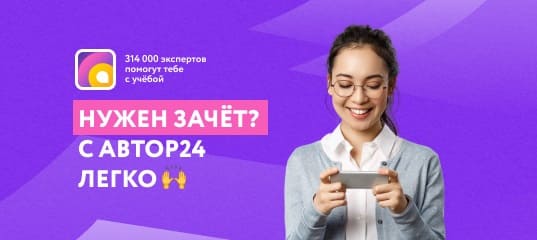
Мы поможем в написании ваших работ!