Определение потребного количества оборудования и
ВВЕДЕНИЕ
Цель курсовой работы – произвести расчет технико-экономических показателей по заданному технологическому процессу обработки детали «гайка» с целью определения эффективного с экономической точки зрения варианта технологического процесса. В работе производится сравнение двух вариантов: базового и проектируемого (конкурирующего). В конкурирующем варианте операция с ручным управлением заменена на операцию с ЧПУ.
В первой части рассматриваются вопросы, связанные с организацией производства: определяется количество оборудования, численность рабочих, их разряд и производительность труда.
Во второй части рассматриваются вопросы по организации рабочих мест, обслуживанию и ремонту оборудования, обеспечению техники безопасности на рабочем месте.
Экономическая часть содержит расчеты по определению расхода и стоимости основных материалов, фонда заработной платы производственных рабочих, а так же расчет полной калькуляции себестоимости детали-представителя.
В результирующей части производится расчет экономической эффективности проектируемого технологического процесса определяется путем экономического сравнения выбранного варианта технологического процесса с базовым вариантом.
При оценке эффективности соизмерение разновременных показателей: капитальных вложений и себестоимости механической обработки осуществляется методом дисконтирования.
|
|
В заключении составляется сводная таблица технико-экономических показателей работы производственного подразделения.
I ПРОИЗВОДСТВЕННЫЕ РАСЧЕТЫ
Расчет приведенного выпуска деталей, годового объема
Выпуска деталей-представителей, количества наименований
Технологически-однородных деталей, обрабатываемых на
Участке. Расчет партии запуска, норм штучно-калькуляционного
Времени и расценок
1. Годовой (объем) приведенный выпуск деталей Nnp, это условное количество типовых деталей, трудоемкость обработки которых равна трудоемкости всех деталей, закрепленных за участком, и который обеспечивает полную загрузку рабочих мест на участке. Он определяется исходя их производственной мощности участка и наиболее рационального использования оборудования по формуле:
, шт. (1)
где
МГ – годовая производственная мощность, в шт.;
К3– коэффициент использования рабочего места при полной загрузке участка (0,80 – 0,85), характеризует достаточно полное использование оборудование и наличие необходимого резерва времени;
tшт.м. – норма штучного времени на ведущей операции для детали-представителя. В качестве ведущей операции принимается операция с наименьшей номой времени. В отдельных случаях является целесообразным объединение операций небольшой длительности (менее минуты) выполняемых на станках одной модели;
|
|
α – коэффициент допустимых потерь рабочего времени на переналадку оборудования:для серийного производства он равен от 0,05 до 0,08;
Ведущая операция 015Токарная :
Принимаем Nnр = 70000(шт.)
2. Годовой объем выпуска детали – представителя Nгод определяется в пределах:
(2)
где
Кз.о.– коэффициент закрепления операций (согласно ГОСТ 3.1108-74 для среднесерийного производства 10…20, для мелкосерийного 20…40)
Принимаем Nгод = 6000 (шт)
3. Количество наименований деталей mд, обрабатываемых на участке рассчитывается по формуле:
(3)
Обозначения прежние.
При равномерном в течение года выпуске продукции и закрепление за каждым рабочим местом одной операции Кз.о = mд
В данном случае mд находится в пределах величины Кз.о = 10…20 для среднесерийного производства, что соответствует заданию проекта.
|
|
4. Определение количества деталей в партии
Минимальное число деталей в партии Пзопределяется по формуле:
, шт. (4)
где:
tпз– подготовительно-заключительное время на ведущей операции.
Принимаем Пз= 200 шт.
Принятое Пз= 200 (шт.) близко к расчетному значению и кратно годовому выпуску :
5. Норма штучно-калькуляционного времени tшт.к на операции определяется по формуле:
, мин. (5)
Пример расчета приводим по операции 005:
6. Сдельная расценка на операцию рассчитывается по формуле:
, руб. (6)
Пример расчета приводим по операции 005
Данные расчетов сводим в таблицу.
Таблица 1 – Нормы штучно-калькуляционного времени и расценки по операциям
№ опер. | tшт мин | tпз мин | Пз шт | tшт.к мин | Разряд работ | Счас руб. | Rсд руб. |
005 | 6,3 | 21 | 200 | 6,40 | 3 | 85,903 | 9,16 |
010 | 5,5 | 19 | 5,58 | 2 | 75,904 | 6,93 | |
015 | 4.1 | 33 | 4,26 | 6 | 115,475 | 5,33 | |
025 | 2,7 | 21 | 2,80 | 6 | 123,557 | 5,76 | |
030 | 5,1 | 10 | 5,19 | 4 | 96,888 | 8,38 | |
Итого | 23,7 | - | 24,23 | - | - | 35,56 |
|
|
Итого трудоемкость детали:
, н/ч (7)
где
mоп – количество операций по технологическому процессу
Общая трудоемкость годового приведенного выпуска детали:
, н/ч (8)
Определение потребного количества оборудования и
Коэффициента его загрузки
Исходя из трудоемкости обработки годового приведенного выпуска на каждой операции потребное количество станков рассчитывается по формуле:
,шт. (9)
Расчетное количество станков (Ср) дробное округляется в большую сторону, таким образом, получают принятое количество станков Спр.
Коэффициент загрузки оборудования Кз на конкретной операции определяетсяпо формуле:
(10)
При этом
Пример расчета приводим для операции 005 Токарная (станок 1А616):
;
Спр = 2 (шт.);
Результаты расчетов по остальным операциям сводятся в таблицу.
Таблица 2 – Расчет количества оборудования и коэффициента его загрузки по участку
№ | Наименование | Модель | Nпр шт | Fд | Tшт.к. | Ср | Спр | Кз |
1 | Токарно-винторезный | 1А616 | 70000 | 3948 | 6,40 | 1,89 | 2 | 0,93 |
2 | Радиально-сверлильный | 2Н125 | 70000 | 3948 | 5,58 | 1,65 | 2 | 0,82 |
3 | Горизонтально-сверлильный с ЧПУ | 2Р135Ф2-1 | 70000 | 3948 | 4,26 | 1,26 | 2 | 0,63 |
4 | Токарно-винторезный | 1К62 | 70000 | 3948 | 2,80 | 0,83 | 1 | 0,83 |
5 | Вертикально-сверлильный | 2В55 | 70000 | 3948 | 5,19 | 1,53 | 2 | 0,76 |
| Итого |
|
|
| 24,23 | 7,16 | 9 |
|
Средний коэффициент загрузки оборудования по участку определяется по формуле:
(11)
Определим коэффициент загрузки по данному участку:
Далее строим график загрузки оборудования.
Рис1 – График загрузки оборудования
На основании расчетов количества потребного оборудования составляется сводная ведомость оборудования.
Таблица 3 – Сводная ведомость оборудования
№ п/п | Тип и модель станка | Габаритные размеры (мм) | Кол-во станков | Коэф-нт загрузки обрудов | Мощность, кВт | Категория рем. сложности одного станка | Сумма рем. сложности на все станки | Цена, тыс руб. | Балансовая стоимость всего оборудования, тыс. руб. | ||||
един | всего | мех. часть | электр. часть | мех. часть | электр. часть | един | всего | ||||||
1 | Горизонтально-резерный с ЧПУ 6Б75ВФ1 | 1250х1690 | 3 | 0,93 | 1,5 | 5 | 8 | 4,5 | 30 | 25,5 | 2800 | 2800 | 3080 |
2 | Токарно-винторезный 1К62 | 2812х1324 | 6 | 0,87 | 7,5 | 45 | 16 | 11,5 | 32 | 23 | 550 | 300 | 330 |
3 | Плоскошлифовальный 3М636 | 2450х2170 | 4 | 1,015 | 5 | 20 | 7 | 11 | 15 | 22 | 480 | 400 | 440 |
ИТОГО | 13 | 70 | 77 | 70,5 | 3500 | 3850 |
Балансовая стоимость оборудования определяется умножением цены по прейскуранту на коэффициент, учитывающий затраты на транспортировку и монтаж оборудования, который принимается равным 1,1.
Дата добавления: 2018-04-05; просмотров: 348; Мы поможем в написании вашей работы! |
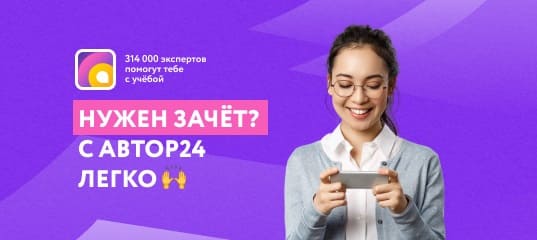
Мы поможем в написании ваших работ!