Обобщающая предыдущие теория Бойкова
«Обр-ся при гидр. С3S Ca(OH)2 переходит в р-р, выделяется из р-ра в виде гелевидных фаз, а затем взаимодействует с водой по топохим.механизму.»
В современном представлении механизм и последовательность процессов твердения могут быть представлены следующим образом. После добавления к цементу воды образуется раствор, который пересыщен относительно гидроксида кальция и содержит ионы Са2+, SO42-, ОН-, Na+, К+. Из этого раствора в качестве первичных новообразований осаждаются гидросульфоалюминат и гидроксид кальция. На этом этапе упрочнения системы не происходит, гидратация минералов носит как бы скрытый характер. Второй период гидратации (схватывание) начинается примерно через час с образованием вначале очень тонких кристаллов гидросиликатов кальция.
Гидросиликаты и гидросульфоалюминаты кальция растут в виде длинных волокон, пронизывающих жидкую фазу в виде мостиков, заполняющих поры. Образуется пористая матрица, которая постепенно упрочняется и заполняется продуктами гидратации. В результате подвижность твердых частиц снижается и цементное тесто схватывается. Такая первая высокопористая с низкой прочностью структура, обусловливающая схватывание, состоит главным образом из продуктов взаимодействия с водой С3А и гипса.
В течение третьего периода (твердения) поры постепенно заполняются продуктами гидратации клинкерных минералов, происходит уплотнение и упрочнение структуры цементного камня в результате образования все большего количества гидросиликатов кальция.
|
|
В конечном виде цементный камень представляет собой неоднородную систему — сложный конгломерат кристаллических и коллоидных гидратных образований, непрореагировавших остатков цементных зерен, тонкораспределенных воды и воздуха. Его называют иногда микробетоном.
Экзаменационный билет N 8
1.Химические свойства стекол.
Прозрачность.
Прозрачность стекла обусловлена кристаллизацией молекул кварца.
Хрупкость стекла.
Хрупкость стекла обусловлена поверхностным натяжением в молекулярных решетках. Стекла имеют определенный предел прочности. При критическом воздействии, кристаллическая решетка не выдерживает нагрузок, и междумолекулярные связи рушатся. Стекло трескается или разбивается на острые, опасные для человека осколки, которые имеют режущие торцы и способны повреждать белее мягкие материи.
Для того чтобы стекло, при крушении, не образовывало острых осколков, его закаляют в печах закалки стекла. Процесс закалки происходит под температурой критической точки перехода стекла в жидкое состояние. После достижения этой точки молекулярный состав стекла начинает формировать правильную кристаллическую решетку. Благодаря действию силы тяжести все элементы молекул занимают четко одинаковые позиции. После мгновенного охлаждения молекулярная решетка буквально застывает в правильном положении. Стекло закаленного типа приобретает более высокие показатели прочности и при превышении предела прочности механическими нагрузками в его толще происходит последовательный разрыв всех молекулярных связей. В результате чего листовое стекло рассыпается на мелкие кусочки, которые уже не повредят человеку.
|
|
Водонепроницаемость
Водонепроницаемость стекла. Стекло обладает водонепроницаемостью за счет плотности кристаллической решетки и отсутствия пористых включений. Вся толща стекла имеет высокую степень сплоченности молекул и не пропускает воду, пар, газы и газообразные смеси.
2.Cпособы формования листового стекла и их сравнительная
характеристика.
К листовым видам стекол относится стекла, вырабатываемые в виде плоских листов, толщина которых по отношению к длине и ширине сравнительно не велика.
По способу производства различают листовое стекло: тянутое, получаемое вертикальным вытягиванием ленты стекла из стекломассы; прокатное, вырабатываемое прокатом стекломассы в ленту прокатными валками, и полированное листовое стекло, изготовляемое методом термической полировки.
|
|
При производстве тянутого стекла используют два способа формования: вертикальное вытягивание стекла через лодочку ( ВВС) и вертикальное вытягивание стекла со свободной поверхности стекломассы (БВВС).
Вертикальное вытягивание стекла через лодочку ( ВВС).
Принцип формования ВВС заключается в том, что в стекломассу, имеющую вязкость порядка 103,3 – 103,7 Па*с, погружают шамотную лодочку ( в виде прямоугольного параллелепипеда со сквозным продольным вырезом, переходящим в верхней части в узкую щель), в процессе чего за счет сил гидравлического напора из щели лодочки выступает стекломасса, оттягиваемая кверху в виде ленты валками машины ВВС. Чтобы лента стекла не сужалась по ширине ( за счет сил поверхностного натяжения), ее края захватывают специальными приспособлениями металлическими бортодержателями, а полотно ленты охлаждают с помощью холодильников.
Далее стекло поступает в шахту высотой около 5м, которую проходит за 4 мин. В нижней части шахты в интервале температур 500-400 0С происходит отжиг ленты. В верхней части шахты скорость охлаждения повышается, и стекло выходит из шахты машины с температурой не более 140 0С. На определенной высоте подмашинной камеры лента окончательно отвердевает и перестает растягиваться, что обеспечивает непрерывность ее движения вверх, а следовательно, и непрерывность процесса формования. С увеличением скорости вращения валков лента растягивается сильнее, что позволяет сравнительно легко получать заданную толщину ленты и изменять ее. По выходе ленты стекла из машины ее разрезают на листы, которые поступают на раскрой , сортировку и упаковку.
|
|
При безлодочном вертикальном вытягивании лента стекла формируется со свободной поверхности стекломассы. Необходимые для формирования ленты значения вязкости получают путем оконтуривания определенного участка зеркала стекломассы подвесными шамотными элементами. В стекломассу на глубину 70-120мм погружают огнеупорное тело. Ориентируя его вдоль оси машины, обеспечивают регулируемое движение потоков стекломассы. Оттягивают ленту кверху, как и при лодочном способе при помощи валиков машины БВВС. Отличительными признаками безлодочного вытягивания являются более интенсивное охлаждение ленты стекла в подмашинной камере, позволяющее вытягивать стекло с большей скоростью, и наличие бортформирующих роликов, способствующих получению ленты стекла заданной геометрии.
К преимуществам лодочного вытягивания следует отнести сравнительную простоту выработочных устройств; меньшую, чем при безлодочном способе, чувствительности процесса формования к колебаниям температурного режима ванной печи, простоту обслуживания машин. Недостатки - это недостаточно высокое качество вырабатываемого стекла ( повышенная полосность), частые обрывы ленты и сравнительно невысокие скорости вытягивания.
Безлодочный способ вертикального вытягивания обладает рядом заметных преимуществ в сравнении с лодочным формованием. При этом способе достигаются более высокие скорости вытягивания, вырабатываемое стекло характеризуется повышенным качеством, увеличивается срок непрерывной работы машин без обновления. К основным недостаткам способа следует отнести: высокую чувствительность процесса формования к колебаниям теплового режима, сложность обслуживания машин. Удельные капитальные затраты на сооружение систем БВВС и зданий для них больше, чем при лодочном способе. Кроме того, из-за большой ширины отрезаемых бортов резко снижается коэффициент использования стекломассы.
Методом проката изготовляют крупноразмерные стеклянные листы, а также узорчатое и армированное стекло. Прокатное стекло вырабатывают периодическим или непрерывным способом. Периодическим прокатом получают листы толщиной до 40-45мм, шириной до 5м и длиной до 8м. Порцию стекломассы выливают на охлаждаемый металлический стол и прокатывают валом, катящимся по столу. Для периодического проката характерна низкая производительность при высокой себестоймости продукции. В настоящее время для производства прокатного стекла применяют непрерывный способ, при котором стекломасса из ванной печи поступает в прокатные валки, которые формируют ее в ленту. Толщину стекла регулируют расстоянием между валками, а скорость проката – изменением скорости вращения валков. Ширина прокатываемой ленты до 3000 мм, толщина 4 – 15 мм, а скорость проката до 240 м/ч. Непрерывный прокат один из самых высокопроизводительных способов производства стекла. Одна прокатная машина вырабатывает до 250 т стекла в сутки, что соответствует примерно 9 машинам ВВС. Недостаток непрерывного проката – невозможность получения стекла тоньше 3 мм и необходимость шлифовки и полировки для получения блестящей полированной поверхности.
Термически полированное стекло. Принцип формования заключается в том, что строго дозируемое количество стекломассы из выработочной части стекловаренной печи по сливному лотку стекает на зеркальную поверхность расплавленного олова и , растекаясь по нему, превращается в ленту равновесной толщины. Отформованная лента стекла далее продвигается по поверхности олова, постепенно охлаждаясь и передается в отжигательную печь. Хорошее качество нижней поверхности ленты достигается при контакте с идеально ровной поверхностью расплавленного олова, а верхняя поверхность получается полированной за счет сил поверхностного натяжения ( огненная полировка).
Флоат-ванна имеет длину 45-55м, ширину при выработке стекла 3.5м, в передней части 6-7м, и глубину 50-100м. Ванна футерована огнеупорным материалом и заключена в металлический кожух, по длине разделена перегородками на три части, в каждой из которых поддерживают свой тепловой и газовый режим. Пространство между бассейном и сводом по всей длине флоат-ванны заполнено смесью азота и водорода, выполняющей функцию защитной атмосферы и предохраняющей олово от окисления. Затраты на производство стекла на 50% ниже, чем при производстве стекла механическим способом. Удельная производительность флоат установок, отнесенная к 1м ширины ленты, в 6.5 – 7 раз больше, чем при безлодочном способе вертикального вытягивания.
3.Технологическая схема производства портландцемента по
мокрому способу. Назначение каждой технологической операции
Мокрый способ производства.
На отечественных цементных предприятиях при подготовке сырьевой смеси по мокрому способу в большинстве случаев используют твердый карбонатный (известняк) и мягкий глинистый (глина) компоненты. Принципиальная технологическая схема получения портландцемента.
Известняк как более твердый материал предварительно подвергается дроблению, а пластичная глина измельчается в присутствии воды в специальных аппаратах (болтушках или мельницах-мешалках). Окончательное тонкое измельчение с получением однородной смеси известняка, глиняного шлама и корректирующих добавок происходит в шаровых трубных мельницах. Хотя компоненты дозируют в мельницы в заданном соотношении, из-за колебаний их химико-минералогических характеристик не удается получить в мельнице шлам состава, отвечающего установленным параметрам. Поэтому необходима специальная технологическая операция по корректировке его состава. После проверки соответствия состава шлама заданным показателям его подают на обжиг во вращающуюся печь, где завершаются химические реакции, приводящие к получению клинкера. Затем клинкер охлаждается в холодильнике и поступает на склад, где также хранятся гипс и активные минеральные добавки. Эти компоненты предварительно должны быть подготовлены к помолу. Активные минеральные добавки высушивают до влажности не более 1 %, гипс подвергают дроблению. Совместный тонкий размол клинкера, гипса и активных минеральных добавок в шаровых трубных мельницах обеспечивает получение цемента высокого качества. Из мельниц цемент поступает в склады силосного типа. Отгружают его либо навалом (в автомобильных и железнодорожных цементовозах), либо упакованным в многослойные бумажные мешки.
При приготовлении шлама из двух мягких (мела и глины) и двух твердых компонентов (известняка и глинистого мергеля) последовательность основных технологических операций не меняется. Однако особенности свойств измельченного сырья и стремление к выбору наименее энергоемких технических решений обусловливают существенные отличия способов измельчения компонентов. При использовании двух мягких компонентов принципиальная технологическая схема будет следующей.
Такая технологическая схема позволяет эффективно использовать способность мягкого сырья распускаться в воде. Применение мощного оборудования для предварительного измельчения сырья (например, мельниц "Гидрофол") позволяет отказаться от его дробления. Однако на стадии предварительного измельчения часть сырья остается недоизмельченной, и получение шлама также должно завершаться в шаровой трубной мельнице. При использовании двух твердых компонентов принципиальная технологическая схема приобретает новый вид. В данной технологической схеме повышенная твердость глинистого сырья обусловливает необходимость его предварительного дробления. Тонкое измельчение всех компонентов происходит в одну стадию в шаровой мельнице. Очевидно, что этот вариант технологической схемы связан с большими трудностями получения
В водной среде облегчается измельчение материалов и улучшается их перемешивание. В результате снижается расход электроэнергии (при мягком сырье экономия может достигать 36 МДж/т сырья) и получается более однородная шихта, что в конечном счете приводит к росту марки цемента. Кроме того, при мокром способе упрощается транспортировка шлама и улучшаются санитарно-гигиенические условия труда. Сравнительная простота мокрого способа и возможность получения высокомарочной продукции на сырье пониженного качества обусловили его широкое распространение в цементной промышленности нашей страны. В настоящее время этим способом выпускается около 85 % клинкера. В то же время введение в шлам значительного количества воды (30-50 % массы шлама) обусловливает резкое повышение расхода теплоты на ее испарение. В результате расход теплоты при мокром способе (5,8-6,7 МДж/кг) на 30-40 % выше, чем при сухом способе. Кроме того, при мокром способе возрастают габариты и соответственно металлоемкость печей.
4.Твердение известково-кремнеземистых композиций при гидротермальной обработке.
Твердение известково-кремнеземистых материалов в условиях обработки паром в автоклавах — следствие ряда сложных физических и физико-химических процессов. Изучением этих процессов интенсивно занимались и занимаются в нашей стране Н. Н. Смирнов, И. Ф. Пономарев, П. П. Будников, Ю. М. Бутт, П. И. Боженов, Т. М. Беркович, Л. С. Болквадзе, Б. Н. Виноградов, X. С. Воробьев, К. Э. Горяйнов, Г. И. Книгииа, С. А. Кржемин-ский, М. Я. Кривицкий, К. К. Куатбаев, К- Ф. Ломунов, Л. А. Малинина, С. А. Миронов, А. П. Меркни, А. В. Са-талкин, К. И. Саснаускас, Е. С. Силаенков, А. А. Федии, Л. М. Хавкин, М. С. Шварцзайд и другие исследователи.
Некоторые из основных положений теории автоклавной обработки нзвестково-кремнеземистых материалов разработаны А. В. Волженским в 1932—1935 гг. Согласно этой теории, автоклавная обработка состоит из трех стадий. Первая включает период с момента впуска пара в автоклав до достижения заданной температуры обрабатываемых изделий. Вторая характеризуется постоянством температуры и заданного давления пара в автоклаве. При этом максимальное развитие получают все те химические и физико-химические процессы, которые обусловливают возникновение цементирующих новообразований и твердение известково-песчаных или бетонных изделии. Третья начинается с момента прекращения доступа пара в автоклав и включает время остывания изделий в нем до их извлечения.
Пар, впускаемый в автоклав с отформованными изделиями, охлаждается и конденсируется от соприкосновения с ними и холодными стенками котла. До создания в автоклаве давления пара конденсат образуется преимущественно на гранях изделий, но при постепенном подъеме давления пар начинает проникать в мельчайшие поры материала и превращаться в воду. Таким образом, к воде, введенной при изготовлении изделия, присоединяется еще вода от конденсации пара. Вода в порах растворяет присутствующий здесь гидроксид кальция и другие растворимые вещества, входящие в состав изделия, что также способствует конденсации пара (закон Ф. Рауля), поэтому при обработке изделий паром низкого или высокого давления образование цементирующих веществ протекает в присутствии воды в жидком состоянии. Роль пара при запаривании сводится только к сохранению жидкой воды в материале в условиях повышенных и высоких температур. В отсутствие пара вода испарялась бы, материал высыхал и полностью бы прекращались реакции, связанные с образованием цементирующих веществ.
Дата добавления: 2018-04-04; просмотров: 139; Мы поможем в написании вашей работы! |
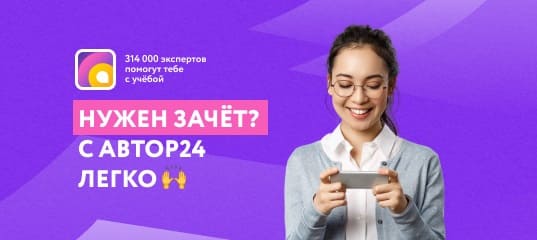
Мы поможем в написании ваших работ!