Технические характеристики бетононасосных установок с маслогидравлическим приводом
Показатель | СБ-165 | СБ-161 | СБ-126А | БН-80-20 |
Тип | Прицепной | Стационарный | Автобетононасос | Автобетононасос |
Регулируемая производительность, м3/ч водительность, м3/ч водительность, м3/ч | 5...20 | 5...65 | 5...65 | 0...65 |
Вылет распределительной стрелы, м | - | - | 18 | 17 |
Угол поворота стрелы, град. | - | - | 360 | 360 |
Давление, развиваемое поршнем, МПа | 6 | 6 | 6 | 6 |
Дальность подачи бетонной смеси, м: | ||||
по горизонтали | 300 | 350 | 350 | 200 |
по вертикали | 80 | 80 | 80 | 80 |
Наибольшая крупность заполнителя, мм заполнителя, мм | 40 | 40 | 40 | 40 |
Диаметр бетонопрово-да (внутренний), мм | 125 | 125 | 125 | 125 |
Объем приемного бункера, м3 | 0,5 | 0,7 | 0,7 | 0,4 |
Высота загрузки бетонной смеси, мм | 1400 | 1350 | 1400 | 1400 |
Диаметр транспортного цилиндра, мм | 180 | 180 | 180 | 180 |
Число транспортных цилиндров | 2 | 2 | 2 | 2 |
Ход поршня, мм | 1400 | 1400 | 1400 | 1500 |
Наибольшее давление в | ||||
приводном гидроцилиндре, МПа | 16 | 16 | 16 | 16 |
Габаритные размеры, мм: | ||||
длина | 5000 | 6000 | 10000 | 11000 |
ширина | 1900 | 2500 | 2500 | 2500 |
высота | 1750 | 1950 | 3500 | 3500 |
Масса бетононасоса (технологическое обо- | ||||
(технологическое обо- | ||||
рудование), т | 2,5 | 3 | 8 | 11 |
5.4 Укладка и уплотнение бетонной смеси.
5.4.1 Общие вопросы.
Технологический процесс укладки бетонной смеси состоит из следующих операций:
|
|
- подача к месту укладки;
- распределение бетонной смеси;
- разравнивание и уплотнение бетонной смеси;
Перед началом бетонирования должны быть определены или уточнены:
- способы подачи, распределения и уплотнения бетонной смеси;
- состав бетонной смеси и показатели ее подвижности;
- толщина и направление укладываемых слоев;
- допустимая продолжительность перекрытия слоев;
- необходимая интенсивность подачи бетонной смеси с проверкой обеспеченности ее поставки бетонными заводами и транспортными средствами;
- потребность в механизмах и рабочих для подачи, распределения и уплотнения бетонной смеси, включения рабочих для выполнения подсобных работ в процессе бетонирования.
Перед укладкой бетонной смеси опалубка должна быть очищена от мусора, грязи, льда, снега, масел, при необходимости промыта. Если смесь укладывается на бетонную поверхность, то ее предварительно необходимо подготовить, очистить поверхность бетона от цементной пленки сразу после схватывания цемента (в жаркую погоду через 6-8 часов после окончания укладки, в прохладную погоду – через 12-24часа). Очистка бетонных поверхностей от цементной пленки должна производиться без повреждения поверхности бетона, для чего прочность бетона должна быть в пределах:
|
|
- при обработке водяной или воздушной струей – 2-3кгс/см²;
- при обработке механической металлической щетки – 15…25кгс/см²;
- при обработке пескоструйным агрегатом – 50….100кгс/см²;
Во время укладки бетонной смеси необходимо постоянно следить за состоянием опалубки, при появлении смещения или деформации щитов следует немедленно устранить смещения и деформации.
Бетонирование конструкции должно сопровождаться соответствующими записями в журнале бетонных работ:
- дата начала и окончания бетонирования (по конструкциям, блокам, захваткам);
- заданные марки бетона, рабочие составы и показатели его подвижности (жесткости);
- объемы выполненных работ по отдельным частям сооружения;
- дата изготовления контрольных образцов, их количество, маркировка (с указанием места конструкций, откуда взята бетонная смесь), сроки и результаты испытаний образцов;
- температура бетонной смеси при укладке (в зимних условиях), а также при бетонировании массивных конструкций.
Способы укладки бетонной смеси.
1. Послойная укладка параллельными слоями толщиной, не превышающей 2/3 высоты наконечника вибратора или зоны проработки поверхностными вибраторами;
|
|
2. Укладка наклонными слоями увеличенной толщины в монолитных конструкциях с использованием мощных глубинных вибраторов;
3. Непрерывная послойная укладка подвижных и литых бетонных смесей, транспортируемых бетононасосными установками с применением кратковременной неинтенсивной вибрации;
4. Напорное бетонирование конструкций на полную высоту в замкнутых формах путем нагнетания высокоподвижных и литых смесей в пространство опалубки.
Б6етонную смесь укладывают горизонтальными слоями и, как правило, по площади всей бетонируемой конструкции. При многослойной укладке для обеспечения монолитности бетонной кладки по всей толщине конструкции необходимо укладывать свежую смесь на уплотненный слой до того, как начнется процесс схватывания цемента.
Толщина h слоя, удовлетворяющую данному условию, определяют по формуле:
h = Q* t/F, м
где Q – интенсивность подачи бетона, м³/ч;
t – максимально допустимый срок до перекрытия слоя ранее уложенного бетона, ч;
F – площадь бетонируемой конструкции, м².
Величина t зависит от промежутка времени между затворением и началом схватывания цемента tн. Сх и от продолжительности транспортировки и укладки бетонной смеси:
|
|
tт.у = tн.сх – tт. У
Полученная расчетом толщина слоев бетонной смеси должна соответствовать (но не превышать) установленным нормам пределам:
- при внутреннем вибрировании – длине рабочей части вибратора;
- при поверхностном вибрировании неармированных и армированных одиночной арматурой конструкций – 250мм;
- в конструкциях с двойной арматурой – 120мм, если размеры конструкции не позволяют соблюсти данное условие, то принимают ступенчатый способ укладке бетонной смеси.
Одна из основных технологических операций – это уплотнение бетонной смеси. От качества уплотнения в основном зависит плотность и однородность бетона, его прочность и долговечность. Бетонную смесь уплотняют вибрированием (виброуплотнением), штыкованием и трамбованием.
Самый распространенный и наиболее экономичный способ уплотнения бетонной смеси является вибрирование. Под действием механических колебаний смесь подвергается тиксотропному разжижению, равномерному распределению в опалубке, а также вытеснению содержащегося в бетонной смеси воздуха. Вибраторы применяют глубинные, наружные и поверхностные. В зависимости от типа привода различают вибраторы электромеханические, электромагнитные, пневматические и гидравлические.
5.4.2 Уплотнение глубинными вибраторами.
С помощью глубинных вибраторов можно уплотнять бетонные смеси с подвижностью не менее 2…3см. С применением пластифицирующих добавок применяют кратковременную вибрацию, но с меньшей интенсивностью. Тип вибратора выбирают в зависимости от подвижности смеси, степени армирования и крупности заполнителя. Глубинные вибраторы со встроенным электродвигателем применяют для уплотнения бетонной смеси с подвижностью 1….5см и погружаются в нее на глубину 5…10см. Время вибрирования в одной точке принимают 15…30сек в зависимости от параметров вибратора, подвижность бетонной смеси, степени армирования. Шаг перестановки вибратора не должен превышать 1,5 радиуса его действия (Рис.51).
Рис.51 Работа с глубинными вибраторами.
Уплотнение бетонной смеси считается достаточным, когда прекращаются ее оседание и выделение больших пузырьков воздуха, а на поверхности появляются цементное молоко. Радиус действия вибратора зависит от подвижности бетонной смеси, степени армирования, формы бетонируемой конструкции и др. условий и поэтому уточняется бетонщиком визуально по косвенным показателям. Чем больше толщина вибрируемого слоя, тем дольше должно быть времени для выделения глубоко находящихся пузырьков воздуха.
5.4.3 Уплотнение бетонной смеси поверхностными вибраторами.
Поверхностные вибраторы применяют при уплотнении бетонной смеси, укладываемой в подготовки под полы, плиты перекрытий и другие конструкции, толщина которых не превышает 25см для неармированных конструкций или конструкций, армированных легкой сеткой.
При толщине бетонного слоя более 25см или при наличии арматуры уплотняют смесь глубинным вибратором с последующим уплотнением поверхностным вибратором для уплотнения верхних слоев, выравнивания и заглаживания поверхности. Для поверхностного вибрирования применяют виброрейки и площадочные вибраторы. Виброуплотнение следует вести в 2-3 проходки.
6. Технология возведения основных монолитных конструкций зданий и сооружений.
6.1 Возведение фундаментов и стен подземной части зданий.
Для монолитных и сборно-монолитных зданий различных строительных систем рекомендуется ленточные, столбчатые, плитные и свайные фундаменты, выполняемые из монолитного бетона. В свою очередь в зависимости от расчетной схемы и нагрузки от здания плитные фундаменты имеют разновидности: фундаменты в виде ребристой плиты, в виде плоской (безбалочной) плиты, в виде полой плиты (коробчатое сечение).
Комплексный процесс возведения фундаментов и стен из монолитного бетона включает разбивку осей фундаментов, устройство опалубки, сборку и установку арматуры и непосредственно бетонирование фундаментов.
Выбор технологии возведения фундаментов из монолитного бетона зависит от конструктивного решения фундаментов и зданий, а также от возможных схем комплексной механизации. Как правило, возможные схемы комплексной механизации составляют на стадии проекта производства работ (ППР), исходя из имеющегося технологического оборудования и механизмов.
Трудоемкость и стоимость устройства монолитных фундаментов, выполняемых в опалубке, в значительной степени зависят от модуля поверхности фундамента М.С увеличением модуля поверхности возрастает трудоемкость всех процессов, особенно опалубочных работ.
Для возведения монолитных железобетонных фундаментов используют различные схемы комплексной механизации. В состав механизированного комплекса для устройства фундаментов, независимо от технологии выполнения бетонных работ («кран-бадья», вибропитатель, автобетононасос и др.), включают башенные или стреловые краны для выполнения погрузочно – разгрузочных работ, установки опалубки, арматуры и монтажа арматурно-опалубочных блоков.
Выбор ведущей машины при бетонирований фундаментов определяется прежде всего габаритами подземной части здания, глубиной заложения и конструктивными особенностями возводимых фундаментов, а также темпом укладки бетонной смеси (интенсивностью)
Интенсивность укладки бетонной смеси может быть ориентировочно определена по формуле
где V – объем бетона возведения фундаментов, м3;
T – планируемая продолжительность возведения фундаментов, смены;
k – коэффициент непрерывности укладки бетона;
В зависимости от производительности принятого комплекта машин ведущего потока подбирают комплекты машин для частных потоков по монтажу опалубки и арматуры. Общую продолжительность специализированного потока возведения фундаментов определяют по формуле.
где k – продолжительность работ на захвате (модуль цикличности, дн.);
m – число захваток;
n – число частных потоков, включая распалубливание и ремонт опалубки;
– продолжительность твердения бетона, дн.;
– продолжительность организационных перерывов, дн.
Число захваток определяется количеством комплектов опалубки, которыми располагает производитель. В качестве примера на рисунке 41 приведена схема механизации для устройства ленточных фундаментов с использованием в качестве ведущей машины автобетононасоса.
Рис.41 Схема комплексной механизации.
Частный поток по армированию фундаментов начинают с укладки арматурных сеток их подошвы с помощью крана. Перед укладкой арматурных сеток на них устанавливаются фиксаторы, обеспечивающие формирование проектного защитного слоя. После укладки сеток устанавливают арматурные каркасы фундамента, которые выверяют и временно закрепляют временными креплениями.
Снятие временных креплений каркасов производят после электроприхватки к арматуре подошвы фундамента. Состав частного потока по установке опалубки определяется применяемым типом опалубки. Для использования грузоподъемности крана щиты опалубки укрупняют в панели. Монтаж опалубочных панелей производят после окончательной выверки и закрепления арматурных каркасов в проектном положении. Вначале устанавливают и закрепляют опалубку ступенчатой части фундамента, затем опалубочные панели стен фундамента.
При использовании технологии бетонирование фундамента по схеме «кран-бадья» бетонную смесь из транспортного средства разгружают в переносные бадьи.
Бадьи подают к месту укладки краном и выгружают бетонную смесь непосредственно в опалубку. Кран двигается по верху котлована. Вылет стрелы крана должен обеспечить подачу смеси в любую точку фундамента.
При использовании в качестве ведущей машины вибропитателя бетонную смесь из транспортного средства разгружают в приемный бункер виброиспытателя, откуда она поступает на вибролоток и с его помощью укладывается в опалубку. Вибропитатель перемещается по верху котлована по периметру здания (Рис.42).
Рис.42 Технологические схемы бетонирования фундаментов.
При бетонировании фундаментов с помощью автобетононасоса бетонную смесь из автобетоносмесителя выгружают в приемный бункер бетононасоса. Автобетононасос движется по верху котлована (Рис.41 и 42).
Ленточные фундаменты бетонируют в зависимости от конструктивных особенностей в один, два и три этапа. Одноэтапное послойное бетонирование применяется при устройстве ленточных фундаментов прямоугольного или переменного сечения при площади поперечного сечения менее 3 м2. Ленточные фундаменты со ступенями бетонируют в два этапа, сначала ступени, а затем стену. В три этапа бетонируют ленточные фундаменты с подколенниками под каркас здания.
В фундаменты под колоны зданий объемом до 15м3 бетонную смесь подают по виброжелобам, самоходными бетоноукладчиками, в бадьях кранами и бетононасосами.
В ступенчатые фундаменты с общей высотой до 3 м и площадью ступени до 6 м2 смесь подают через верх опалубки, предусматривая меры против смещения анкерных болтов и закладных деталей. При уплотнении глубинные вибраторы погружают в смесь через открытые грани нижней ступени и переставляют их по периметру ступени в направлении к центру фундамента. Аналогично уплотняют бетонную смесь второй и третьей ступени. При небольшой высоте подколонника фундамента применяют малоподвижные бетонные смеси (ОК до 3 см). Подколонники бетонируют сразу после бетонирования ступеней. Уплотнение смеси производят глубинными вибраторами, опуская их сверху.
Рис.43 Бетонирование ступенчатых фундаментов.
При высоте ступенчатых фундаментов более 3 м и площади нижней ступени более 6 м2 бетонную смесь подают сначала в нижнюю ступень по периметру фундамента (Рис.43), а затем через приемный бункер и звеньевые хоботы бетонируют подколонник. При осадке конуса смеси 4-6 см подколонники бетонируют медленно с устройством перерывов (1-1,5 ч) с целью исключения возможного выдавливания бетона, уложенного в ступени.
Технология бетонирования стен подземной части здания зависит от толщины и высоты стен, а также от конструкции опалубки. При бетонировании стен применяют разборно-переставные мелко и крупнощитовые, подъемно-переставные и другие виды опалубок.
Разборно-переставную щитовую опалубку устанавливают в два приема: вначале с одной стороны на всю высоту стены, а после установки арматуры - с другой. При большой высоте и толщине стены опалубку второй стороны устанавливают по-ярусно в процессе бетонирования. Если опалубку устанавливают на всю высоту стены, в опалубке предусматривают окна для подачи смеси. Опалубку стен толщиной более 0,5 м можно возводить на всю высоту стены с подачей смеси сверху с помощью хоботов (Рис.44).
При бетонировании стен в разборно-переставной опалубке высота участков, выполняемых без перерыва, не должна превышать 3 метров. При большей высоте участков стен, бетонируемых без рабочих швов, устанавливают перерывы не менее 40 мин и не более 2 ч для осадки уложенной смеси и предупреждения образования осадочных трещин. При длине стены более 20 м ее делят на участки длиной 7-10 м и на границе участков устанавливают разделительную перегородку с образованием шпоночного сопряжения. Бетонную смесь укладывают непрерывно толщиной 0,3-0,5 м и с обязательным виброуплотнением.
Бетонирование массивных плитных фундаментов многоэтажных зданий со значительными нагрузками может выполняться с использованием бетоноукладчиков, а при интенсивности 50-100 м3/смену могут быть использованы стационарные бетононасосы с распределительными стрелами.
В малоармированные плитные фундаменты укладывают бетонную смесь с осадкой конуса 1-3 см и крупностью заполнителя до 70 мм, в густоармированные - с осадкой конуса 3-6 см и крупностью, не превышающей 1/3 наименьшего расстояния между арматурными стержнями. Для уменьшения температурных деформаций конструкций при твердении бетона в массивные фундаменты и плиты используют бетонные смеси на цементе с низкой экзотермией. Укладывают бетонную смесь в массивные фундаменты горизонтальными слоями толщиной 0,3-0,4 м с обяза тельным виброуплотнением. Большие малоармированные или неармированные фундаменты бетонируют слоями 1-2 м. Уплотняют смесь в них мощными пакетными вибраторами, переставляемыми с помощью кранов.
Рис.44 Схема бетонирования стен подземных сооружений: а – стен толщиной 0.5м и более, высотой 3м; б – тонких стен; в – послойное бетонирование стен бетононасосами;
1 – щиты опалубки; 2 – связи жесткости; 3 – расчалка; 4 – стяжка; 5 – воронка; 6 – звеньевой хобот; 7 – телескопические стойки; 8 – забетонированный участок; 9 – вибратор; 10 – рукав бетононасоса; 11 – разделительная опалубка; 12 – наружный щит опалубки; 13 – арматурный каркас; 14 – бадья; 15 – направляющий щит; 16 – подмости; 17 – подкос.
При бетонировании густоармированних плит бетонную смесь рекомендуется укладывать непрерывно на всю высоту плиты. Плиты толщиной до 0,5 м бетонируют картами шириной 3-4 м. При большей толщине плит карты устраивают шириной 5-10 м с разделительными полосами в 1-1,5 м. Чтобы обеспечить непрерывную укладку смеси на всю высоту, плиты разбивают на блоки без разрезки арматуры с ограждением блоков металлическими сетками. Расположение и конструкция рабочих швов должны быть предусмотрены проектом.
Рис.45 Бетонирование большеразмерных плит.
Участок бетонирования в пределах карты должен быть минимальным. Карты бетонируют подряд. Для уменьшения суммарной усадки бетон в разделительные полосы укладывают враспор с затвердевшим бетоном карт после снятия опалубки на их границах.
Укладку бетонной смеси в пределах карты бетононасосами, с помощью бетоноукладчиков и бадьями на кране рекомендуется выполнять в направлении к ранее уложенному бетону, прижимая тем самым новые порции бетона к ранее уложенным (Рис.46).
Рис.46 Подача бетонной смеси при бетонировании плит.
6.2 Устройство монолитных железобетонных колонн.
В зависимости от высоты колонн в качестве опалубки используют специальные щиты на всю высоту колонны или собираемые из отдельных мелких щитов.
Последовательность установки опалубки:
1. Установка рамки, формирующей сечение колонны и ориентирующей колонну относительно коордиционных осей. Оси, нанесенные на рамке, должны совпадать с осями, нанесенными на бетонной поверхности ранее забетонированной колонны или перекрытия нижнего яруса.
2. Установка короба, формирующий три грани колонны, производится в рамки, закрепляют расчалками или универсальными подкосами. Затем выверяют вертикальность короба. Четвертый щит опалубки колонны и недостающие прижимные устройства, и фиксаторы устанавливают после установки арматурных каркасов. Короб охватывают деревянными или металлическими хомутами.
3. Арматурные каркасы устанавливают с помощью крана. Каркасы выверяют и временно закрепляют с помощью фиксаторов относительно выпусков арматурных стержней нижнего яруса колонны.
4. Колонны высотой до 5м бетонируют непрерывно на всю высоту (Рис.47а). Бетонную смесь загружают сверху с помощью бадьи или гибкого хобота манипулятора бетонопровода и уплотняют глубинными вибраторами, опускаемыми в опалубку на канатах. В колонны высотой 5м бетонную смесь подают через воронки по хоботам и уплотняют ее внутренним или наружными вибраторами(Рис.47б). Высокие густоармированные колонны бетонируют через окна в опалубке и специальные карманы(Рис.47в). Уплотняют смесь с помощи глубинных вибраторов, вводимых через окна и карманы. Колонны бетонируют непрерывно на всю высоту.
5. Демонтаж опалубки производят в обратной последовательности после достижения бетоном распалубочной прочности. Опалубку демонтируют щитами и перемещают на место очистки, смазки и подготовки щитов к последующему использованию.
6. Балки и плиты, монолитно связанные с колоннами, бетонируют не ранее чем через1-2часа после окончания бетонирования колонн. Перерыв необходим для осадки бетона.
Рис.47 Бетонирование колонн.
6.3 Устройство монолитных железобетонных балок, прогонов и плит.
Опалубка балок и прогонов состоит из двух боковых щитов и днища, вставляемого между ними. Боковые щиты снизу крепят прижимными досками, сверху при высоте балок до 45см они удерживаются опалубкой плиты или поперечными схватками. В балках высотой более 45см боковые щиты скрепляются дополнительно стяжками. Днище опирается на оголовники стоек или на другие опоры. Стойки под балками и прогонами устанавливаются обычно на расстоянии 1,5…2м одна от другой.
Опалубка плит ребристых перекрытий состоит из опалубочных щитов, укладываемых на кружала, которые, в свою очередь, устанавливают на подкружальные доски.
При установки опалубки ребристого перекрытия в первую очередь укладывают и закрепляют крепежные рамки в основании колонн, а затем устанавливают опалубку колонн, закрепляют ее временными подкосами.
Порядок установки опалубки ребристых перекрытий:
1. Соединяются короба колонн.
2. Устанавливаются и раскрепляются короба колонн в заранее уложенные рамки.
3. Поднимаются днища прогонов.
4. Устанавливаются стойки под днища прогонов.
5. Поднимаются и укладываются боковые щиты прогонов и раскрепляются треугольниками и распорками.
Рис.48 Расположение рабочих швов при бетонировании.
Плиты бетонируют по маякам. Поверхность их выравнивают и заглаживают. Рабочие швы в плоских плитах устраивают параллельно встроенными блоками, а также в отдельных блоках рабочие швы устраивают в средней трети пролета этих балок (Рис.48,а).
При бетонировании в направлении, параллельном главным балкам, рабочий шов устраивают в пределах двух средних четвертей пролета главных балок и в середине плит (Рис.48,б). Рабочие швы должны быть вертикальными, для этого в плитах устанавливают доски или специальные разделительные устройства, а в балках – щиты с отверстиями для пропуска арматуры.
При продолжении бетонирования перекрытия с поверхности шва удаляют рыхлые слои бетона и цементную корку, очищают его от грязи и мусора. Непосредственно перед укладкой нового бетона поверхность шва следует увлажнить, а также уложить слой жирного раствора на цементе того же вида, что и в основном бетоне.
6.4 Устройство монолитных стен.
Технология возведения стен и перегородок из монолитного бетона в значительной степени зависит от их толщины и высоты, степени армирования, используемой опалубки, методом подачи и уплотнения бетонной смеси, используемого бетона (легкий, тяжелый) с соответственно для ограждающих конструкций.
Щитовую опалубку стен устанавливают, как правило, в два приема: сначала устанавливают опалубку одной стороны стены на всю ее высоту, а после армирования стен монтируют опалубку другой стороны. Опалубку наружной стороны крепят к внутренней стяжными болтами.
Для соблюдения проектной толщины стен внутри них устанавливают распорные устройства совместно со стяжными болтами.
Армирование стен начинают с монтажа каркасов с помощью крана. Вручную устанавливают отдельные стержни и каркасы над проемами и в угловых элементах стен. Установленный каркас выверяют и временно закрепляют с помощью фиксаторов. Для выверки и осевого совмещения каркаса стен применяют струбцины. Снятие временных креплений производят после прихватки электросваркой каркасов к выпускам арматуры ниже расположенного яруса стены.
В стены толщиной более 0,5м при слабом армировании укладывают бетонную смесь с осадкой конуса 4-6см и крупностью заполнителя до 60мм. При длине 15м стены разделяют на участки длиной 7-10м для равномерного (без перерыва) бетонирования в течение определенного времени. Разделительные элементы, устанавливаемые на границе участков без разрезки арматуры, армируют шпоночное сопряжение в стене. Вместо разделительного элемента можно устанавливать сетчатую опалубку и оставляют в бетоне.
При высоте стен до 3м бетонную смесь разгружают непосредственно в опалубку в нескольких точках по длине участка. Для подачи смеси используют бадьи и виброжелоба (Рис.49). Бетонируют стены горизонтальными слоями толщиной 0,35-0,4м (Рис.50). Не рекомендуется подавать бетонную смесь в одну точку с побуждением ее к перемещению внутри опалубки. В этом случае образуются наклонные рыхлые слои, снижающие качество бетона.
В тонкие и густоармированные стены укладывают бетонные смеси с осадкой конуса 6…10см и крупностью заполнителя до 20мм. При толщине до 0,15м. Опалубку таких стен возводят с одной стороны на всю высоту, а с другой – только на высоту яруса. Арматуру устанавливают на всю высоту. Бетонную смесь подают и уплотняют вибраторами со стороны низкой опалубки. При уплотнении бетонной смеси вибраторы не должны касаться опалубки, так как передача колебаний на опалубку разрушает уложенные слои.
Рис.49 Технологические схемы бетонирования стен.
Рис.50 Бетонирование стен.
6.5 Уход за бетоном, распалубливание конструкций и исправление дефектов бетонирования.
В соответствии с указанием СНиП 3.03.01-87 «Несущие и ограждающие конструкции» при выдерживании уложенного бетона в начальный период его твердения необходимо обеспечить:
· поддержание температурно-влажностного режима, необходимого для нарастания прочности бетона;
· предотвращение значительных температурно-усадочных деформаций и образование трещин;
· предохранение твердеющего бетона от ударов, сотрясений, других воздействий, ухудшающих качество бетона в конструкциях.
Мероприятия по выдерживанию и уходу за бетоном предусматривают в проекте производства работ. В летнее время поверхность свежеуложенного бетона защищают от действия прямых солнечных лучей и ветра. Для этого бетонные поверхности укрывают брезентом или мешковиной во влажном состоянии или укрывают слоем влажных опилок или песка, который укладывают через 3-4ч после укладки бетонной смеси и поливают водой до 5раз в день в течение 7-14дней.
В осеннее и весеннее время года при температуре воздуха +5С и ниже устраивают на объекте склад материалов для утепления открытых поверхностей бетона. Время выдерживания бетона при укрытии назначают с учетом прочности уложенного бетона, определяемой строительной лабораторией по результатом испытаний контрольных образцов.
Прочность бетона определяют двумя методами: разрушающим и неразрушающим.
Разрушающий метод – основан на испытании образцов 15*15*15см, изготавливаемых у места бетонирования конструкций и хранящихся в условиях, идентичных условиям выдерживания конструкций.
Для бетона каждого класса изготавливают серию из трех образцов на следующее количество бетона:
· для крупных фундаментов – на каждые 100м3 под конструкции;
· для массивных фундаментов под технологическое оборудование – на каждые 50м3;
· для каркасных и тонкостенных конструкций – на каждые 20м3;
Бетон считается выдержавшим испытания, если средняя прочность контрольных образцов будет не ниже 85% проектной.
Неразрушающий метод - применяют для определения прочности бетона при промежуточным производственном контроле качества бетона, а также для прочности бетона непосредственно в конструкции.
Разновидности неразрушающего метода:
1. Механический – основан на использовании зависимости между прочностью бетона на сжатие и его поверхностной твердостью;
2. Ультразвуковой или импульсный – основанный на измерении скорости распространения в бетоне продольных ультразвуковых волн и степени их затухания (прибор УК «Бетон»).
Распалубливание конструкций.
Распалубливают конструкции после достижения бетоном прочности, обеспечивающей сохранность углов, кромок и поверхностей. Сроки распалубки зависят от режима твердения и марки бетона, вида цемента и конструктивных особенностей элементов.
Минимальная прочность бетона монолитных незагруженных конструкций при распалубке поверхностей установлена СНиП3.03.01-87:
· вертикальных из условия сохранения формы – 0,2-0,3мПа;
· горизонтальных и наклонных при пролете: до 6м – 70% проектной; свыше 6м – 80% проектной.
Минимальная прочность бетона при распалубке загруженных конструкций, в том числе от вышележащего бетона (бетонной смеси), определяется ППР и согласовывается с проектной организацией.
При наличии несущих сварных армакаркасов опалубки снимают при достижении бетоном 25% проектной прочности.
При распалубливании междуэтажных перекрытий под балками, прогонами и плитами оставляют так называемые стойки безопасности на расстоянии не более 3м друг от друга. Опорные стойки нижележащих перекрытий удаляют после достижения бетоном возводимого перекрытия проектной прочности. Опоры опалубки балок, прогонов и ригелей опускают одновременно по всему пролету. Опорные стойки остальных нижележащих конструкций удаляют полностью при достижении бетоном проектной прочности.
Последовательность демонтажа опалубки, как правило, обратная монтажу за исключением случаев, специально оговариваемых в технологических картах и проектах производства работ. Крупнощитовую опалубку массивов, стен и фундаментов снимают кранами с помощью специальных рычажных приспособлений.
Перед повторным использовании элементы опалубки очищают от бетона, осматривают и ремонтируют. Формирующие поверхности щитов покрывают смазкой.
Традиционные методы ухода за бетоном в виде поливки его водой трудоемки и имеют высокую стоимость. Технико-экономическая несостоятельность этого метода стала особо ощутимой с повышением сменных темпов устройства цементнобетонных покрытий.
Такой метод был найден в укрытии поверхности бетонного покрытия водо и паронепроницаемыми материалами (пленкообразующими жидкостями). Их распределение по поверхности свежеуложенного бетона за один или два прохода (разлива) создает оптимальные влажностные условия твердения бетона за счет сохранения (консервации) воды затвердения, введенной в бетонную смесь при ее приготовлении. При скоростнром строительстве цементнобетонных покрытий этот метод наиболее приемлем по простоте технологического процесса и по другим технико-экономическим показателям.
За рубежом промышленность выпускает различные составы для ухода за бетоном в виде растворов водных эмульсий или сухих водорастворимых порошков, их которых готовитося материал для ухода за бетоном на месте производства работ.
Особенно выгодны водорастворимые порошки, позволяющие строителям готовить материал различной окраски в зависимости от погодных условий.
Рекомендуемые пленкообразующие жидкости для ухода за бетоном, их характеристика и методы проверки их качества изложены в ВСН 139-68.
Таблица 15
Показатели | Нормы для пленкообразующих материалов | ||
ПМ-86 | ПМ-100А | ПМ-100АМ | |
Внешний вид и цвет пленки | После высыхания пленкообразующего материала образуется однородная пленка серебристого или серебристо-желтого цвета | ||
Остаток на сите | Не должно оставаться комков | ||
Вязкость при 20С по вискозиметру ВЗ-4, С | 13+2 | 16+3 | 14+2 |
Содержание пленкообразующего вещества, , не менее | 30 | 37 | 33 |
Время полного высыхания при t=18-22С, ч, не более | 12 | 7 | 7 |
Температура вспышки в закрытом тигле, С, не менее | 32 | 37 | 37 |
Водостойкость пленки при t=20+2 С, ч, не менее | 24 | 24 | 24 |
Укрывность, ч/м , не более | 40 | 80 | 55 |
При соблюдении установленных требований к технологии работ по уходу за бетоном во время его твердения, все перечисленные материалы обеспечивают надежную и эффективную его защиту.
Пред использованием пленкообразующего материала – помароли всех марок, его следует испытать, насколько он отвечает установленным требованиям для ухода за бетоном.
В начале каждой смены помароль в металлических бочках доставляют к месту работ и раскладывают вдоль предстоящего фронта работ через 10-150м (в зависимости от емкости бочек). В последствии из этих бочек помароль насосом машины ДС-105 перекачивают в ее расходную часть при непременном усиленном перемешивании помароли находящейся в бочках. Если по ходу выполнения работ видно, что создание шероховатости и уход за бетоном машиной ДС-105 проходи в очень напряженном режиме и возможно запаздывание по уходу за бетоном, перекачку помароли в бак ДС-105 следует вести специальным заправщиком. Рекомендуется пленкообразующую жидкость наносить на бетон за 2 раза.
Норма расхода пленкообразующего материала:
-битумные эмульсии и лак этиноль по 600г/м при t до 25 С и 1000г/м при более высокой t и ветреной погоде
-ПМ-100А – 400г/м
-ПМ-100АМ – 1000г/м
При распределении этого количества за 2 прохода в каждый разлив дается половина нормы.
Пленкообразующий материал наносится на поверхность свежеуложенного бетона, когда его поверхность не имеет блеска, матовая, что определяется отсутствием влаги на ладони при ее приложении к поверхности бетона.
Высота ниппелей распределителя от обрабатываемой площади (высота факеля), должна быть 40-50см.
Продолжительность выполнения работ по уходу за бетоном машиной ДС-105 в сочетании с образованием шероховатости на захватке 150м составляет 67мин, из которых времени:
-20 - на образование шероховатости
-40 - на заполнение помаролью бака машиной ДС-105 насосом
-40 - на распределение жидкости
Повышение производительности труда машины ДС-105 во многом зависит от уменьшения длительности ее заправки используемой жидкости.
В процессе распределения материала по уходу за бетоном следует систематически проверять его расход и не допускать участков бетона, не покрытых защитной пленкой. Если они образовались, их необходимо немедленно обработать ручным пистолетом – распределителем, имеющемся при ДС-105. Машина ДС-105 обрабатывает не только основную поверхность покрытия, но одновременно ее боковые грани. В случае обнаружения пропусков защиты вертикальных плоскостей, их также следует обработать из пистолета – распределителя.
В условиях сухого жаркого климата для уменьшения температурного напряжения в бетонной плите устанавливают термозащитный слой толщиной не менее 5 см.
Песок укладывают на покрытие сразу после сформирования защитнгй пленки с необходимыми предосторожностями, исключающими нарушения целостности пленки и ровности покрытия.
Качество защитной пленки на свежеуложенном бетоне проверяют не менее 1 раза в смену. Проверка производится фенолфталеином (1 - раствор) или соляной кислотой (10 - раствор).
Участок сформировавшейся пленки размером 20 х 20см после его промывки и осушения ветошью обрабатывают (разливают) одним из указанных растворов.
Пленка считается качественной, если после применения фенолфталеина не будет ее покраснения и вспенивания при обработке соляной кислотой.
Все виды пленкообразующего материала ПОМАРОЛЬ поставляют в чистых, плотно закрытых металлических бочках (по ГОСТ 6247-52) весом (нетто) до 200 кг и должны храниться под навесом с предохранением от прямого воздействия солнечных лучей при t в пределах от -35 до +40 С. Срок хранения 12 месяцев.
Пленкообразующие материалы всех марок, которые хранились в бочках, перед закачкой их в емкость машины для ухода за бетоном, необходимо тщательно механически перемешать, а в процессе распределения на поверхность покрытия парамоль также следует систематически перемешивать.
Дефекты бетонирования и способы их устранения.
После снятия опалубки с железобетонных конструкций нередко обнаруживаются дефекты бетонирования.
Причины дефектов:
· Применение некачественных материалов;
· Изношенность опалубки;
· Нарушение технологии производства бетонных работ;
· Недостатки конструктивных решений.
После распалубливания производитель работ должен тщательно осмотреть состояние открытых поверхностей бетонных и железобетонных конструкций, проверить конструкции на наличие скрытых дефектов путем простукивания обычным молотком. Выявленные дефекты устраняются.
Две основные группы дефектов:
1. Гравелистая поверхность бетона в отдельных местах; неглубокие раковины; незначительные неровности и наплывы.
2. Глубокие и сквозные раковины; пустоты; трещины; отклонения конструкций от проектной размеров.
Эти дефекты исправляют только после тщательного осмотра конструкций и, как правило, после согласования метода устранения дефектов с проектной организацией. Применение опалубки, которая в процессе многократной оборачиваемости постепенно изнашивалась и своевременно не ремонтировалась, приводит к тому, что в процессе бетонирования через ее щели и неплотности при интенсивной вибрации вытекает цементное молоко, что вызывает гравелистую поверхность и раковины.
· Гравелистую поверхность бетона очищают металлическими щетками, промывают струей воды, а затем оштукатуривают цементно-песчаным раствором состава 1:2 – 1:3 (по объему) на портландцементе марки 400-500.
· Неглубокие раковины расчищают от неплотного бетона зубилом и металлической щеткой, промывают или зачеканивают жидким раствором.
· Наплывы на бетонной поверхности удаляют вслед за распалубливанием, когда бетон еще не набрал проектной прочности, для чего применяют кельмы, молотки-кирочки, зубила и отбойные молотки.
· Раковины образуются в результате сбрасывания бетона с большой высоты из-за недостаточного уплотнения, применения жесткой бетонной смеси, в результате длительного транспортирования, во время которого бетонная смесь расслоилась и начала схватываться. Чаще всего раковины появляются в местах наибольшей насыщенности арматурой, труднодоступных и неудобных для укладки и уплотнения бетона.
· Пустоты устраняются следующим образом: - поверхность стыков очищают от рыхлого старого бетона;
- затем стыки тщательно промывают водой;
- через карманы в установленной опалубке подают бетон на мелком щебне, а затем уплотняют.
- Для ускорения твердения бетона в местах заделок применяют электропрогрев или устраивают тепляки с подачей внутрь его горячего воздуха, а также могут быть использованы установки инфракрасного излучения.
При обнаружении трещин, являющимися результатом усадки, температурных напряжений или различных напряжений, создается комиссия с участием представителя проектной организации. В процессе обследования выявляются причины появления трещин, обозначают их на конструкции, измеряют величину раскрытия трещин и устанавливают наблюдение за их состоянием.
Стабилизировавшиеся трещины в зависимости от величины их раскрытия заделывают с поверхности цементным раствором набрызгом или давлением. Все выполненные работы по исправлению дефектов оформляются специальным актом.
В сильно загруженных колоннах раковины последовательно расчищают, удаляя уплотненный бетон с каждой стороны колонны затем их промывают водой и подготовленные поверхности бетонируют (Рис.52).
Рис.52 Исправление дефектов бетонирования.
Для заделки раковины применяют раствор или бетон с крупностью заполнителя до 20мм. В качестве вяжущего используют портландцемент марки 400-500. Раствор или бетон готовят небольшими порциями вблизи места производства ремонтных работ. Чтобы обеспечить сцепление нового бетона со старым и с арматурой и получить повышенную прочность на ослабленном участке в раннем возрасте, рекомендуется применять бетон, марка которого на одну ступень выше марки бетона ремонтируемой конструкции.
Если при проверке обнаружены сквозные раковины, расчистка которых вызовет значительное снижение несущей способности нагруженных колонн, устраивают железобетонные обоймы или накладки с последующим нагнетанием в пустоты цементно-песчаного раствора через установленные заранее трубы. На месте каждого дефекта рекомендуется устанавливать не менее двух трубок, по одной под давлением подают раствор, а второй – продувают раковины.
Распространены и опасный для несущей способности железобетонных конструкций дефект – пустоты, которые часто появляются вследствие непрохождения бетона на данном участке. Часто при этом оголяется арматура, образуются сквозные разрывы в конструкциях, и нарушается их монолитность.
6.6 Контроль качества железобетонных работ на строительной площадке.
На строительной площадке контролируют прежде всего неукоснительное выполнение требований проекта, а также строительных норм и правил при производстве бетонных работ (СНиП3.03.01.-87 «Несущие и ограждающие конструкции»).
Виды контроля:
· контроль за соответствием проекту точности установки опалубки, арматуры и закладных деталей – при необходимости с применением геодезических приборов;
· контроль качества бетонной смеси, а также прочности бетона в процессе бетонирования – испытанием контрольных образцов;
· контроль за соблюдением технологии бетонирования, а также точности возведения зданий и сооружений – при необходимости с применением средств геодезического инструментального контроля;
· контроля прочности бетона в готовых конструкциях (при необходимости).
По назначению контроль различают:
· Входной – проверка качества поступающих материалов, полуфабрикатов и изделий.
· Операционный – контроль состоит в изменении и корректировке параметров технологического процесса, а также в наблюдении за формированием качества продукции в процессе ее производства;
· Приемочный;
Опалубочные работы.
Требования к качеству применяемых материалов (конструкций).
1. Опалубка должна изготовляться в соответствии с требованиями ГОСТ23478-79
ГОСТ23477-79 и технических условий на опалубку.
2. Древесные, металлические, пластмассовые и другие материалы для опалубки должны отвечать требованиям ГОСТ 23478-79; деревянные, клееные конструкции – ГОСТ 20850-84 или ТУ; фанера ламинированная – ТУ 18-649-82; ткани пневматических опалубок ТУ.
3. Опалубка должна обладать: прочностью, жесткостью, неизменяемостью формы, устойчивостью в рабочем положении и в условиях монтажа и транспортирования.
4. На палубе щитов не должно быть щелей, заусенец и местных отклонений.
5. При приемке опалубки необходимо проверить: - наличие паспорта с инструкцией по монтажу и эксплуатации опалубки; - геометрические размеры, качество рабочих поверхностей, защитной окраски поверхностей не соприкасающихся с бетонами; - защиту торцевых поверхностей неметаллической палубы; электрического сопротивления изоляции потребляемой мощности, оптического сопротивления для греющей опалубки.
6. Установка и приемка опалубки, рапалубливание монолитных конструкций, очистка и смазка производятся по ППР.
Технические требования.
1. Точность изготовления инвентарной опалубки по ГОСТ 25347-82, ГОСТ 25346-82;
2. Точность установки инвентарной опалубки по ГОСТ 25346-82; ГОСТ 25347-82;
3. Перепады поверхности для конструкций, готовых под окраску < 2мм, под обои – 1мм.
4. Прогиб собранной опалубки не должен превышать: - для опалубки и вертикальных поверхностей – 1/400пролета; - для опалубке перекрытий – 1/500пролета.
5. Минимальная прочность бетона при распалубке монолитных незагруженных конструкций: – вертикальных поверхностей конструкций должна быть не менее 2-3 кгс/см2 - горизонтальных и наклонных поверхностей при пролете до 6м не менее 70% от проектной; при пролете более 6м не менее 80% от проектной.
6. Минимальная прочность бетона при распалубке загруженных конструкций определяется в ППР и согласовывается с проектной организацией
Снятие всех типов опалубки должно производится после предварительного отрыва от бетона.
Арматурные работы.
Требования к качеству применяемых конструкций.
1. Сварные арматурные изделия и закладные детали должны изготовляться по рабочим чертежам в соответствии с требованиями ГОСТ 10922-75, ГОСТ 8478-81 и технической документацией, утвержденной в установленном порядке.
2. Предельные отклонения размеров арматуры изделий от проектных не должны превышать нормативных.
3. Кромки плоских элементов закладных деталей не должны иметь заусенцев, завалов и шероховатостей, превышающих 2мм. Кромки плоских элементов после огневой резки должны быть очищены от грата, шлака, брызг и наплывов.
4. На элементах арматурных изделий и закладных деталей не должно быть отслаивающихся ржавчины и окалины, а также следов масла, битума и других загрезнений.
5. При входном контроле на строительной площадке необходимо проверить наличие паспорта или сертификата на поступившую партию изделия, провести на поступившую партию изделий, провести внешний осмотр и требуемые замеры.
Технические требования.
1. Арматурная сталь и сортовой прокат, арматурные изделия и закладные элементы должны соответствовать проекту и требованиями соответствующих стандартов.
2. Транспортирование и хранение арматурной стали должно осуществляться согласно требованиям ГОСТ 7566-81*.
3. Заготовку стержней мерной длины из стержневой и проволочной арматуры и изготовление ненапрягаемых арматурных следует выполнять в соответствии с требованиями СНиП 3.09.01-85, а изготовление несущих арматурных каркасов из стержней диаметром более 32мм, прокатных профилей – согласно разделу 8 СНиП 3.03.01-87.
4. Изготовление пространственных крупногабаритных арматурных изделий следует производить в сборочных кондукторах.
5. Заготовка, установка и напряжение напрягаемой арматуры должны выполняться по проекту в соответствии с требованиями СНип 3.09.01-85.
6. Монтаж арматурных конструкций следует производить преимущественно из крупноразмерных блоков или унифицированных сеток заводского изготовления с обеспечением защитного слоя.
7. Бессварочные соеденения стержней следует производить: стыковые-внахлестку или обжимными гильзами и винтовыми муфтами с обеспечением равнопрочности стыка; крестообразные – дуговыми прихватками или вязкой отожженной проволокой.
8. Форма и размеры закладных изделий и их положение в конструкциях должны соответствовать проектной документации.
9. Предельные отклонения в отметках закладных элементов, служащих опорами для металлических или сборных железобетонных колонн и других сборных элементов, не должны превышать минус 5мм. Поверхности закладных изделий должны иметь антикоррозийное покрытие и при нарушении покрытия оно должно быть восстановлено. Данные о выполнении антикоррозионной защиты оформляются актом освидетельствования скрытых работ.
Бетонные работы.
Требования к качеству бетонной смеси.
1. Бетонные смеси готовят в соответствии с требованиями ГОСТ 7473-85.
2. Каждая партия бетонной смеси, отправляетсмая потребителю должна иметь документ о качестве.
3. Результаты испытаний контрольных образцов бетона изготовитель должен сообщить потребителю не менее чем через 3 суток после проведения испытаний.
4. Готовые бетонные смеси должны доставляться специализированным транспортом согласно ППР. Должно быть исключено: попадание в смесь осадков, нарушение однородности, потери цементного раствора, воздействия в пути вредного воздействия ветра и солнечных лучей.
5. При входном контроле бетонной смеси на строительной площадке необходимо: - проверить наличие паспорта на бетонную смесь и требуемые в нем данных; - путем внешнего осмотра убедиться в отсутствии признаков расслоения бетонной смеси, в наличие бетонной смеси требуемых фракций крупного заполнителя в соответствии с требуемой её пластичностью;
- при возникающих сомнениях в качестве бетонной смеси потребовать контрольной проверки ее соответствия требованиям государственного стандарта и проекта.
Технические требования.
1. Транспортирование и подача бетонных смесей осуществляется специализированными средствами;
2. Состав бетонной смеси, приготовление, правила приемки, методы контроля и транспортирования по ГОСТ 7473-85.
3. Перед бетонированием скальные основания, бетонные поверхности рабочих швов должны быть очищены от мусора, грязи масел, снега и льда, цементной пленки и др. Непосредственно перед укладкой бетонной смеси очищенные поверхности должны быть промыты и просушены струей воздуха.
4. Бетонные смеси должны укладываться в бетонируемые конструкции горизонтальными сломи одинаковой толщины без разрывов, с последовательным направлением укладки в одну сторону во всех слоях.
5. При уплотнении бетонной смеси не допускается опирание вибраторов на арматуру и закладные детали, тяжи и другие элементы крепления опалубки. Глубина погружения вибратора должна обеспечивать углубление его в ранее уложенный слой на 5-10см. Шаг перестановки глубинных вибраторов не должен превышать полуторного радиуса их действия. Укладка следующего слоя бетонной смеси допускается до начала схватывания бетона предыдущего слоя. Верхний уровень уложенной бетонной смеси должен быть на 50…70мм ниже верха щитов опалубки.
6. Поверхность рабочих швов, устраиваемых при укладке бетонной смеси с перерывами, должна быть перпендикулярна к оси бетонируемых колонн, балок, поверхностей плит и стен.
7. рабочие швы допускаются устраивать при бетонировании:
· колонн – на отметке верха фундаментов, прогонов, балок и подкрановых консолей, верха подкрановых балок, низа капителей колонн;
· балок больших размеров, монолитно соединенных с плитами – на 20…30мм ниже отметки нижней поверхности плиты;
· плоских плит – в любом месте параллельно меньшей стороны плиты;
· ребристых перекрытий – в направлении, параллельном второстепенным балкам;
· отдельных балок – в пределах средней трети части пролета балок, в направлении параллельном главным балкам (погонам) в пределах двух средних четвертей пролета прогонов и плит.
7. Технология и организация монолитного домостроения при отрицательных температурах.
7.1 Особенности производства бетонных работ при отрицательных температурах.
При возведении зданий в зимних условиях к твердению бетона предъявляются два основных требования:
· бетон должен достигать распалубочной прочности в оптимальные сроки;
· подвергаться первым воздействиям отрицательных температур только после достижения устойчивости к замораживанию;
Особенности производства работ:
· при превращении воды в лед ее объем увеличивается на 9%. Если вода замерзла в порах, то в результате возникающего гидравлического давления происходит частичное разрушение цементного камня;
· нарушение сцепления цементного камня с заполнителем приводит к потери устойчивости;
· бетон до момента замерзания должен набрать минимальную (критическую) прочность для каждой марки бетона;
Прочность, после набора которой дальнейшее воздействие замерзания не влияет на физико-механические характеристики бетона, называется критической. Значение критической прочности зависит от марки бетона:
Марка бетона: 200 и ниже. 200…300 400 и выше.
Критическая прочность, % от 28 суточной прочности: 50 40 30
Для бетонов с химическими противоморозными добавками:
Марка бетона: 200 300 400 и выше.
Критическая прочность, % от Rб: 30 25 20
Следует четко различать стойкость к одноразовому замораживанию, стойкость к попеременному замораживанию и оттаиванию молодого бетона и морозостойкость. Бетон лишь тогда морозостоек, когда он выдерживает большое число циклов попеременного замораживания и оттаивания без значительного снижения прочности.
Поэтому для конструкций, подвергающихся сразу после распалубки большому числу циклов замораживания - оттаивания, бетон уже при распалубке должен иметь прочность, соответствующую его марке. Для этого требуются либо более длительные сроки нахождения в опалубке и более высокая температура бетона, либо избыточный расход цемента.
В случае использования конструкций, подвергающихся расчетным нагрузкам, относительная прочность бетона к моменту замерзания должна составлять не менее 100% прочности.
Если бетон подвергается действию температур ниже 0 ºС непосредственно после распалубки, то он должен к этому моменту быть устойчивым к замораживанию. Особенно тщательно необходимо защищать от мороза поверхности, не заключенные в опалубку, теплозащитными материалами (прошивными минераловатными матами, пенопластом и др.), пока не будет достигнута требуемая прочность при замораживании.
Производство бетонных работ при отрицательных температурах требует дополнительной подготовки и расходов.
Величина критической прочности зависит также от класса бетона, вида и условий эксплуатации и составляет:
· для бетонных и железобетонных конструкций с ненапрягаемой арматурой 50%-проектной прочности для бетона классов до В15; 40%-для бетонов классов В15 и В22; 30%-для бетонов классов В30 и В40;
· для конструкций с предварительно напрягаемой арматурой и особо ответственных железобетонных конструкций – 70% проектной прочности;
· для конструкций, подвергающихся многократному замораживанию и оттаиванию или действию давления воды, а также для всех конструкций, к которым предъявляются специальные требования по морозостойкости, газо- и водонепроницаемости – 100% проектной прочности.
Продолжительность твердения бетона и его конечные свойства в значительной степени зависит от температурных условий, в которых выдерживают бетон.
Для предварительного определения сроков выдерживания бетона для приобретения требуемой прочности при различных температурах твердения следует пользоваться графиками.
7.2 Подготовка к бетонированию.
1. Утепление бетоносмесительных установок, галереи транспортиров и трубопроводов.
2. Подготовка подъемно-транспортных средств, оснастку.
3. завоз противоморозных добавок.
4. Комплекс работ по подготовке опалубки, арматуры, поверхностей основания и ранее уложенного бетона.
5. Устройство закрытых помещений.
6. Складирования в штабели заполнителя. Перед укладкой в бетонированные массивы заполнитель обогревают до температуры не ниже 0 ºС, предварительно очистив от снега и льда. Иногда заполнители обрабатывают противоморозными добавками.
7. Подготовка грунта перед укладкой бетонной смеси: - удаление всех глинистых, растительных, торфяных и прочих слоев грунтов органического происхождения, подверженных пучению. Их отогревают в тепляках из брезента, полиэтилена, фанеры до положительной температуры на глубине до 50см и защищают от промерзания. Кроме того, пучинистые основания отогревают электрическими нагревателями или воздухонагревателями, приборами с колпаком. Не- пучинистые не отогревают, если их влажность не превышает 10% по массе. – выполняют песчаную подготовку и составляют акт.
8. Арматуру очищают от грязи, отслаивающейся ржавчины и налипших кусков раствора с помощью пескоструйного аппарата или проволочными щетками. При температуре ниже -15 ºС арматуру из стержней диаметром более 25мм и прокатных профилей отогревают до +5 ºС тепловыми калориферами, а выступающие за пределы утепленной опалубки металлические элементы утепляют затем. Установленные арматурные конструкции проверяют, контролируют местоположение, диаметр и число арматурных стержней, а также расстояние между ними, наличие перевязок и сварных прихваток в местах пересечения стержней, наличие поддерживающих устройств: фиксаторов, прокладок и подкладок. Проверяют заданную толщину защитного слоя бетона.
9. Опалубку очищают от грязи, наледи и снега: опалубку накрывают брезентом и под него пускают пар. Щели и отверстия в опалубке заделывают. Опалубку и поддерживающие леса тщательно осматривают и проверяют надежность установки стоек и лесов, а также клиньев под ними, креплений, отсутствие щелей в опалубке наличие закладных частей и пробок, предусмотренных проектом.
Работы по установке и закреплению опалубки и поддерживающих ее конструкций оформляют записью в журнале производства работ. Кроме того, перед укладкой бетонной смеси двухсторонним актом на скрытые работы оформляют работы по сооружению конструктивных элементов, закрываемых последующим производством работ – гидроизоляцию, армирование, установку закладных деталей и т. д.
Если бетонирование ведется с перерывом, то для прочного соединения ранее уложенного и свежего бетона горизонтальные поверхности ранее уложенного затвердевшего бетона перед укладкой бетонной смеси очищают от мусора, грязи и цементной пленки. Цементную пленку удаляют воздушной струей под давлением сразу после схватывания цемента. Вертикальные поверхности очищают от цементной пленки, если это предусмотрено проектом. Места выгрузки и укладки бетонной смеси защищают от ветра и снега брезентовым или фанерным шатром.
7.3 Приготовление бетонной смеси.
Особенностью приготовления бетонной смеси в зимних условиях является необходимость обеспечения установленной расчетом температуры смеси по выходе ее из бетоносмесителя, чтобы после теплопотерь, связанных с транспортировкой от завода к объекту, и неизбежных перегрузок на строительной площадке температура бетонной смеси была не ниже расчетной, необходимой для принятого режима выдерживания бетона.
Температуру бетонной смеси по выходе из бетоносмесителя или температуру предварительного электоразогрева смеси, определяют по формуле:
tсм= (tб.н. –tн.в. ·∑∆tтр)/(1-∑∆tтр), где
tб.н.- начальная температура бетона после укладки в опалубку (определяется в зависимости от способа выдерживания бетона), ºС;
tн.в.- температура наружного воздуха, ºС;
∑∆tтр- суммарное снижение температуры бетонной смеси при всех операциях – от приемки из бетоносмесителя до укладки и укрытия в конструкции, ºС;
∆tтр – относительное снижение температуры бетонной смеси на каждой операции при разнице температур наружного воздуха и бетонной смеси в 1 ºС.
Для обеспечения заданной температуры бетонной смеси ее составляющие в момент загрузки в бетоносмеситель также должны иметь соответствующую температуру, которая устанавливается теплотехническим расчетом с учетом потерь тепла.
В практике строительства:
· воду подогревают до 40-90 ºС (преимущественно паром в водоподогревателях)
· оттаянные или подогретые заполнители подогревают дополнительно до температуры 20…60 ºС чаще всего в бункерах горячим воздухом, либо в специальных бункерах с паровыми регистрами или во вращающихся сушильных барабанах (на крупных бетонных заводах); иногда заполнители нагревают путем продувки топочных газов;
· цемент и тонкомолотые добавки вводят без подогрева.
Однако при высокой температуре бетонной смеси снижается ее подвижность, что существенно усложняет выгрузку и уплотнение. Поэтому при выходе из смесителя температура бетонной смеси в зависимости от вяжущего не должна превышать следующих максимально допустимых величин:
· шлакопортландцемент марок 200-300 + 45 ºС
· портландцемент марки 300 и пуццолановый портландцемент марки 300 и выше + 40 ºС
· портландцемент марки 400 и выше и пуццолановый цемент марки 300 и выше + 35 ºС
· глиноземистый цемент + 25 ºС
При всех способах зимнего бетонирования особо ответственных конструкций и стыков, требующих быстрого загружения, для приготовления бетонных смесей используют наиболее эффективные особо быстротвердеющие портландцементы с малым количеством (до10%) молотых добавок с продолжительностью хранения не более 2-х месяцев.
При подборе состава бетонных смесей для укладки в зимних условиях водоцементное отношение В/Ц уменьшают при повышении требований по морозостойкости и увеличивают при использовании предварительного электроразогрева бетонной смеси, а также на возможность применения пластификаторов.
При приготовлении бетонной смеси соблюдают следующую очередность загрузки материалов в бетоносмеситель:
· одновременно с началом подачи воды загружают щебень или гравий;
· после заливки половины требуемого количества воды и перемешивания в течение некоторого времени – песок, цемент и оставшуюся воду.
Продолжительность перемешивания бетонной смеси в зимних условиях увеличивают, как правило, в 1,5 раза по сравнению с летними условиями. Подвижность и температуру бетонной смеси систематически контролируют непосредственно на выходе смеси из бетоносмесителя.
Если температура наружного воздуха опускается ниже 0ºС температуру бетонной смеси необходимо повышать, по меньшей мере, на число градусов мороза (т.е. +15 ºС плюс число градусов мороза).
Для минимального снижения температуры бетонной смеси переносить ее в опалубку следует как можно быстрее и при минимальном числе рабочих операций. Бетонирование с применением бетононасосов обеспечивает быструю подачу бетонной смеси в опалубку. Бетонирование насосом целесообразно применять для непрерывного бетонирования больших опалубочных форм. Этот метод требует хорошей предварительной подготовки:
· бетононасосы следует устанавливать в теплых помещениях;
· при морозах до -10ºС звенья бетонопроводов следует утеплять минераловатными скорлупами; при более низкой температурах магистральный бетонопровод прокладывают в утепленном коробе. Перед началом работ бетонопровод прогревают острым паром или горячей водой;
· промывать бетононасос и бетонопровод промывают горячей водой.
Открытые поверхности свежеуложенного бетона сразу же по окончании бетонирования укрывают гидроизоляционным рулонным материалом и слоем утеплителя для предохранения верхних слоев бетона от раннего замораживания.
Принципы организации теплозащиты:
· организация теплозащиты должна планироваться и подготавливаться заранее;
· материалы и оснастка теплозащитных устройств по размерам должны быть так, чтобы обеспечить сборку сплошного теплозащитного устройства, укрывающего всю бетонную конструкцию;
· теплозащита должна быть наложена непосредственно на поверхность уложенного бетона;
· теплозащиту устанавливают непосредственно после окончания работ по бетонированию;
· должен быть контроль за выполнением теплозащиты;
· должна соблюдаться техника безопасности;
· теплозащитные устройства должны оставаться на своих местах до разборки опалубки и после этого.
7.4 Методы выдерживания бетона в зимних условиях.
I группа - метод, основанный на использовании начального теплосодержания, внесенного в бетонную смесь при ее приготовлении или перед укладкой в конструкцию.
II группа - метод, основанный на использовании тепловыделения цемента, сопровождающего твердение бетона (метод «термоса»)
III группа - методы, основанные на искусственном прогреве бетона, уложеного в конструкцию:
· электропрогрев;
· индукционный обогрев;
· инфракрасный и контактный нагрев;
· паро - и воздуообогрев.
IV группа - методы, использующие эффект понижения эвтектической точки воды в бетоне с помощью специальных противоморозных химических добавок.
Методы можно комбинировать. Выбор метода зависит от:
- вида и массивности конструкции;
- вида, состава и требуемой прочности бетона;
- метеорологических условий производства работ;
- энергетической оснащенности строительной площадки и т. д.
7.5 Метод «Термоса».
Суть метода: уложенный бетон, при строго определенных условиях (температуре наружного воздуха, скорости ветра, коэффициенте теплопередаче ограждений, массивности конструкций, тепловыделении цемента и начальной температуре бетона), может приобрести заданную прочность во время остывания от своей начальной температуры (tб. н) до некоторой конечной (tб.к.). Количества тепла в бетоне, полное при нагреве составляющих и выделенное цементом в период твердения, должно быть не меньше количества расходуемого тепла (теплопотерь) при остывании конструкций до конечной температуры, т.е. до получения заданной прочности бетона.
В таблице 16 приведен рекомендуемый вид конструкций, выдерживаемый методом «термоса». За начальную температуру (tб. н) принимается температура бетона, уложенного в опалубку сразу после его уплотнения и открытия.
Таблица 16
Рекомендуемый вид конструкций, выдерживаемый методом «термоса».
Мп
|
tH.B. 0С
|
Конструкция
| При укладке бетонной смеси | |||||
с температурой до t б.с. =35 С и t б.н. =25-30°С | предварительно разогретой до t б.с. =70°С при t б. н. =50°С | |||||||
Метод выдерживания бетона | Цемент | Марка цемента | Метод выдерживания бетона | Цемент | Марка цемента | |||
1 | 2 | 3 | 4 | 5 | 6 | 7 | 8 | 9 |
До 3
| До-20 | Массивные фундаменты, гидротехнические сооружения | Термос | ШПЦ, порт-ланцемент | 300-400 300 | Термос с укладкой разогретой бетонной смеси в ядро конструкции | ШПЦ, пуццо-лановый портландцемент, портландцемент | 300-400 300 |
От-21 до-40 | То же | Термос с добавками-ускорителями | Портландцемент, ШПЦ | 400 500 | То же | ШПЦ, порт-ланцемент | 400-500 400 | |
4-5
| До-20 | Фундаменты зданий, массивные фундаменты под оборудование, монолитные стены толщиной 40-50 см, балки высотой > 70 см | То же | Портландцемент, ШПЦ | 400 500 | Термос | ШПЦ, портландцемент | 400 300 |
От-21 до-40 | То же | Термос с проти-воморозными добавками | Портландцемент | 500-600 | Термос с добавками-ускорителями твердения | Портландцемент | 500 | |
6-8
| До-20 | Фундаменты под колонны и оборудование. Колонны сечением 50-70 см и балки высотой 50-70 см, стены и плиты толщиной 25-30 см | Термос с добавками- ускорителями твердения или противомороз-ными добавками | Портландцемент | 500-600 | Термос с добавками-ускорителями твердения | ШПЦ, портландцемент | 400-500 |
От-21 до-40 | То же | То же или в сочетании с предразо-гревом | То же | 600 | Термос с ускорителями твердения | Портланце-мент | 500-600 | |
8-12
| До 20 | Рамные конструкции, колонны сечением 30-40 см, плиты и стены толщиной 20-25 см, балки сечением 30-40 см, покрытие дорог | Термос в сочетании с греющей опалубкой | Портландцемент | 500-600 | Термос с добавками- ускорителями твердения и нитритом натрия | Портландцемент | 500-600 |
От-20 До 40 | Не рекомендуется | Термос в сочетании с греющей опалубкой | То же | 500-600 |
Продолжительность остывания бетона от начальной температуры до конечной в конструкции с модулем поверхности Мп>3 определяется расчетом по формуле Б.Г. Скрамтаева:
Сб – удельная теплоемкость бетона, принимается равной 0,25ккал/кг·ºС;
γб – плотность бетона, кг/м3;
Э – тепловыделение цемента за время твердения бетона, принимается по таблице 17;
tн. в – температура наружного воздуха принимается средняя за время остывания бетона, ºС;
tб.к. – температура бетона к концу остывания, для бетонов без противоморозных добавок рекомендуется принимать не ниже +5 ºС;
Ц – расход цемента в бетоне, кг/м3;
К – коэффициент теплопередачи опалубки или укрытия опалубочных поверхностей, Вт/м2·ºС (Табл.18);
tб.н. – начальная температура бетона после укладки, ºС;
tб.ср. – средняя температура за время остывания бетона, ºС определяется по формуле:
tб.ср. = tб.к. + (tб.н.- tб.к.) /1,03+0,181·Мп+0,006·(tб.н.- tб.к.), где
Мп – модуль поверхности:
Мп = F/V, где
F – площадь охлаждаемых поверхностей конструкций;
V – объем конструкций;
Таблица 17
Тепловыделение цемента «Э» различных видов и марок в зависимости от температуры твердения и времени.
Вид и марка цемента | Темпера- тура, град. | Тепловыделение Э, ккал/кг, в возрасте, сут. | |||||||
0,25 | 0,5 | 1 | 2 | 3 | 7 | 14 | 28 | ||
Портландцемент 300 | 5 | - | - | 6 | 14 | 21 | 40 | 49 | 56 |
10 | 2 | 5 | 10 | 20 | 30 | 47 | 55 | 65 | |
20 | 7 | 10 | 18 | 30 | 40 | 55 | 60 | 70 | |
40 | 12 | 20 | 35 | 48 | 55 | 60 | 70 | - | |
60 | 20 | 35 | 46 | 58 | 63 | 70 | - | - | |
Портландцемент 400 | 5 | - | _ | 7 | 15 | 20 | 40 | 50 | 60 |
10 | 3 | 6 | 12 | 25 | 33 | 50 | 60 | 70 | |
20 | 11 | 16 | 25 | 40 | 50 | 65 | 75 | 80 | |
40 | 13 | 30 | 45 | 55 | 65 | 75 | 80 | - | |
60 | 25 | 40 | 55 | 65 | 75 | 80 | - | - | |
Портландцемент 500 | 5 | 3 | 5 | 10 | 20 | 30 | 45 | 55 | 60 |
10 | 5 | 10 | 15 | 25 | 38 | 60 | 68 | 75 | |
20 | 12 | 20 | 30 | 45 | 60 | 70 | 80 | 90 | |
40 | 25 | 40 | 50 | 64 | 70 | 85 | 90 | - | |
60 | 45 | 55 | 65 | 75 | 83 | 90 | - | - | |
Портландцемент быстротвердею- щий 600 | 5 | 4 | 8 | 13 | 22 | 35 | 50 | 60 | 75 |
10 | 8 | 12 | 18 | 30 | 40 | 65 | 80 | 90 | |
20 | 15 | 25 | 35 | 50 | 70 | 80 | 90 | 100 | |
40 | 28 | 45 | 55 | 70 | 80 | 90 | 100 | - | |
60 | 50 | 60 | 70 | 80 | 90 | 100 | - | - | |
Шлакопортландцет и пуццолановый портландцемент 300 | 5 | - | 3 | 5 | 10 | 17 | 30 | 40 | 45 |
10 | - | 5 | 8 | 15 | 23 | 39 | 50 | 55 | |
20 | - | 9 | 15 | 30 | 33 | 49 | 58 | 65 | |
40 | 10 | 18 | 28 | 40 | 48 | 59 | 65 | - | |
60 | 15 | 25 | 35 | 48 | 53 | 65 | - | - |
Относительная величина тепловыделения за время достижения цементами прочности R28 может приниматься пропорционально достигнутой прочности (например, 50% Э28 соответствует 50% R28).
Коэффициент теплопередачи опалубки или укрытия неопалубленных поверхностей определяется по формуле:
Таблица 18
Коэффициент теплопередачи опалубки различной конструкции.
Тип опалубки
|
Материал
|
Толщина слоя, мм
| К, Вт/м2°С | ||
Скорость ветра, м/с | |||||
0 | 5 | 15 | |||
I | Доска | 25 | 2,44 | 5.2 | 5,98 |
II | Доска | 40 | 2,03 | 3,6 | 3,94 |
III | Доска Рубероид | 25 25 25 | 1,8 | 3 | 3,25 |
IV | Доска Пенопласт Фанера | 25 30 4 | 0,67 | 0,8 | 0,82 |
V | Доска Рубероид Вата минеральная Фанера | 25 50 4 | 0,87 | 1,07 | 1.1 |
VI | Металл Вата минеральная Фанера | 3 50 4 | 1,02 | 1,27 | 1,33 |
VII* | Фанера Асбест Фанера | 10 4 10 | 2,44 | 5,1 | 5,8 |
VIII | Рубероид Опилки | 100 | 0,74 | 0,89 | 0,9 |
IX | Рубероид Шлак | 150 | 1,27 | 1,77 | 1,87 |
X | Рубероид Вата минеральная | 50 | 1,01 | 1,31 | 1,37 |
,
где δi – толщина каждого слоя ограждения, м;
λi – коэффициент теплопроводности материала каждого слоя ограждения, ккал/м·ч·ºС
α – коэффициент теплопередачи у наружной поверхности ограждения, ккал/ м·ч·ºС
Величина коэффициента теплопередачи наиболее часто применяемых конструкций опалубки и укрытий не опалубленной поверхности бетона приведена в таблице 18.
Прочность бетона, определяемая по графикам, за период остывания τ должна быть не менее установленной проектом производства работ. Если эта прочность окажется ниже проектной и нельзя увеличить продолжительность остывания до набора бетоном заданной прочности за счет снижения К и повышения tб.н. до максимально возможной, применение способа «термоса» недопустимо.
Метод «термоса» применяют при бетонировании массивных конструкций с Мп<6 при укладке смесей на портландцементе и с Мп<10 на быстротвердеющем портландцементе.
Если при конкретных условиях способ «термоса» не обеспечивает приобретения бетоном заданной прочности, следует рассмотреть возможность и целесообразность термосного воздержания с введением в бетонную смесь ускорителей твердения бетона:
- хлорид кальция – CaCl2
- хлорид натрия – NaCl
- сульфат натрия – Na2SO4
- нитрат кальция Ca(NO3)2
- нитрит натрия NaNO3
Химические добавки добавляют до 2% массы цемента; они существенно ускоряют процесс твердения в начальный период выдерживания бетона.
Такие бетоны применяют при температуре наружного воздуха -15….-20 ºС. Укладывают их в утепленную опалубку и после виброуплотнения закрывают слоем теплоизоляции. Твердение бетона происходит как результат термосного выдерживания в сочетании с положительным воздействием химических добавок. Этот метод применяют для конструкций с Мп≤8 (бетоны на обычных портландцементах).
7.6 Метод «Горячий термос».
Этот метод заключается в кратковременном разогреве бетонной смеси до температуры 60…80 ºС, уплотнении ее в горячим состоянии и выдерживании – термосном или
с дополнительным обогревом. В условиях строительной площадки бетонную смесь разогревают, как правило, электрическим током в основном в электробадьях или в кузовах автосамосвалах.
Разогрев ведут в течении 10…15минут до температуры смеси:
· на быстротвердеющих портландцементах - 60 ºС.
· на портландцементах - 70 ºС.
· на шлакопортландцементах - 80 ºС.
Метод «горячий термос» применяют для конструкций с Мп≤12.
7.7 Бетон с противоморозными добавками.
Сущность способа: введение в бетонную смесь при ее приготовлении добавок, понижающих температуру замерзания воды, обеспечивающих протекания реакции гидратации цемента и твердение бетона при температуре ниже 0 ºС.
Добавки:
- хлористые соли NaCl и CaCl2
- нитрит натрия NaNO3
- поташ K2CO3
Бетонная смесь с противоморозными добавками укладывается в конструкции при Мп>3, если она удовлетворяет требованиям проекта.
Ограничения (СНиП 3.03.01-87) применения бетонов с противоморозными добавками:
- в конструкциях с предварительно напряженной арматурой;
- в стыках сборных и сборно-монолитных конструкциях;
- в конструкциях, эксплуатируемых при переменном уровне воды, в агрессивных средах, в зонах блуждающих токов и под напряжением постоянного тока.
В таблице 19 приведены рекомендуемые виды конструкций, при бетонировании которых целесообразно применять бетоны с противоморозными добавками, а также в сочетании с другими способами бетонирования.
Таблица 19
Рекомендуемый вид конструкций для возведения из бетонов
с противоморозными добавками.
Мп
|
Конструкции
|
tB средняя, °С
| Метод выдерживания бетона до набора прочности, % от проектной | ||||
20-30
| 50-70 | 80-100 | |||||
28 сут. и менее | более 28 сут. | 28 сут. и менее | более 28 сут. | ||||
4-8
| Фундаменты под здания, ‘ колонны и оборудование (колонны сечением 50 - 70 см, балки высотой 50 -70 см, стены и плиты толщиной 25 - 50 см)
| До-25 | 1 | 1;2 | 1; 2 | 2 | 1; 2 |
Ниже -25 | 1;2 | 2;3 | 2 | 2; 3 | 2 | ||
8-12
| Рамные конструкции, колонны сечением 30 - 40 см, балки высотой 30 - 40 см, стены и плиты толщиной 20 -25 см, дорожные и другие наземные покрытия толщиной 20 -25 см
| До-25 | 1; 2 | 1; 2 | 1; 2 | 2;3 | 1; 2 |
Ниже -25 | 2; 3 | 2; 3 | 2 | 3 | 2 | ||
12-16
| Монолитные участки сборно-монолитных конструкций, стыки сборных конструкций, наземные покрытия толщиной 10- 15 см
| До-25 | 1;2;3 | 2;3 | 1; 2 | 2;3 | 1; 2 |
Ниже -25 | 2;3 | 3 | 2 | 3 | -- | ||
Свыше 16
| Стыки сборных конструкций
| До-25 | 1;2;3 | 2;3 | 1; 2 | 3 | 1; 2 |
Ниже -25 | 3 | 3 | - | 3 | - |
Количество и вид противоморозной добавки назначается в зависимости от:
· факторов окружающей среды;
· модуля поверхности;
· темпов строительства;
· технико-экономических показателей.
В таблице 20 приведены температурный диапазон применения противоморозных добавок и интенсивность нарастания прочности бетона с добавками.
Бетон с противоморозными добавками разрешается применять в том случае, если до приобретения критической прочности температура бетона с добавками не опускается ниже:
± 15°С при применении НН;
± 20°С при применении ХК+ХН, НК+М, НКМ, ННК+М;
± 25°С при применении П, ХК+НН, ННХК, ННХК+М;
Полное наименование добавок приведено в приложении 8 СНиП 3.03.01-87.
После набора критической прочности бетона с добавками при положительной температуре приобретают прочность 100% от R28.
Бетоны с хлористыми солями могут применяться в изделиях и конструкциях, армированных нерасчетной арматурой с защитным слоем не менее 5см.
Если интенсивность набора прочности не соответствует требованиям ППР, рекомендуется повысить расчетную (среднюю) температуру твердения за счет утепления конструкции.
В таблице 21 приводится рекомендуемое количество противоморозных добавок от массы цемента.
Таблица 20
Нарастание прочности бетона с противоморозными
добавками на портландцементах.
Добавка
| tб. твердения, °С | Прочность, при твердении, % от R28 | |||
Возраст, сут. | |||||
7 | 14 | 28 | 90 | ||
Хлористый натрий | -5 | 35 | 65 | 80 | 100 |
Хлористый натрий с хлористым кальцием | -10 | 25 | 35 | 45 | 70 |
-15 | 15 | 25 | 35 | 50 | |
Нитрит натрия | -5 | 30 | 50 | 70 | 90 |
-10 | 20 | 35 | 55 | 70 | |
-15 | 10 | 25 | 35 | 50 | |
Поташ | -5 | 50 | 60 | 75 | 100 |
-10 | 30 | 50 | 70 | 90 | |
-15 | 25 | 40 | 60 | 80 | |
-20 | 20 | 30 | 50 | 75 | |
-25 | 15 | 25 | 40 | 65 | |
СПП | -5 | 40 | 50 | 70 | 95 |
-10 | 30 | 40 | 65 | 90 | |
-15 | 20 | 30 | 60 | 80 | |
-20 | 15 | 20 | 30 | 50 | |
ННХКМ | -5 | 50 | - | 85 | 100 |
-10 | 30 | - | 60 | 90 | |
-15 | 25 | - | 55 | 80 | |
-20 | 20 | - | 45 | 70 | |
-25 | 12 | - | 30 | 45 | |
Аммиачная вода | -1 | - | 25 | 55 | 100 |
-20 | - | 20 | 45 | 90 | |
-25 | - | 15 | 30 | 70 |
Таблица 21
Рекомендуемое количество противоморозных добавок.
tн. в | Количество безводных солей в % от массы цемента | Концентрация NH4OH (аммиачная вода), % | ||||
NaCl +CaCl2 | NaNO2 | Ca(NO3)2+НКМ | K2CO3+СДБ | ННХК+М | ||
-5 -10 -15 -20 -25 -30 | 3+0 3,5+1,5 3+4,5 - - - | 5 7 10 - - - | 2,5+2,5 4,5+4,5 9+3 11,25+3,7 - - | 5 7 10 12 15 - | 4 8 10 12 15 15 | - 8 - 12 - 15 |
Бетоны с противоморозными добавками требуют меньшего расхода воды на единицу объема, чем обычные бетоны.
Недостаточное количество добавок может привести к преждевременному замерзанию, а избыточное – к снижению темпа набора прочности и неоправданному увеличению его стоимости.
В таблице 22 приведены ориентировочные данные по продолжительности выдерживания бетона до набора им критической прочности. При этом количество противоморозных добавок следует назначать согласно данным таблицы 23 с учетом расчетной температуры твердения бетона.
Производство бетонных работ с противоморозными добавками требует соблюдение следующих правил:
1. после окончания бетонирования поверхность конструкции, не защищенную опалубкой, необходимо укрыть слоем гидроизоляционного материала и утеплить изоляционным материалом (минераловатными плитами, пенопластом, спилом, шлаком и др.);
2. термическое сопротивление опалубки и утеплителя должно обеспечивать в бетоне температуру не ниже расчетной до набора прочности не менее критической;
Таблица 22
Продолжительность выдерживания бетона с противоморозными добавками
до набора критической прочности.
Добавка
| tб. средняя, °С
| Время выдерживания, сут. | ||
Марка бетона | ||||
200 | 300 | 400 | ||
НН | -5 -10 -15 | 7 12 19 | 6 3 14 | 4 7 11 |
ХК + ХН | -5 -10 -15 -20 | 6 9 19 58 | 5 7 14 45 | 4 5 10 28 |
ННХК ННХК +М ХК+НН | -5 -10 -15 -20 -25 | 5 9 11 14 40 | 4 7 9 11 28 | 3 5 7 9 20 |
НКМ НК+М ННК+М | -5 -10 -15 -20 | 7 12 19 28 | 6 9 14 19 | 5 7 10 14 |
П | -5 -10 -15 -20 -25 | 3 7 9 11 14 | 2 5 7 9 10 | 1 4 5 6 7 |
Таблица 23
Рекомендуемое количество противоморозных добавок в зависимости
от расчетной температуры твердения бетона.
tб, расчёт- ная°С | Количество безводных добавок, % от массы цемента | |||||||
от | До | НН | ХК+ХМ | НКМ НК+М | ННК+М НК+М | ННХК ХК+НН* | ННХК+М | П |
0 | -5 | 4-6 | 0+3-2+3 | 3-5 | 3+1-4+1,5 | 3-5 | 2+1-4+1 | 5-6 |
-6 | -10 | 6-8 | 3,5+3,5-2,5+4 | 6-9 | 5+1,5-7+2,5 | 6-9 | 4,5+1,5-7+2,5 | 6-8 |
-11 | -15 | 8-10 | 4,5+3-5+3,5 | 7-10 | 6+2-8+3 | 7-10 | 6+2-8+3 | 8-10 |
-16 | -20 | - | 6+2,5-7+3 | 9-12 | 7+3-9+4 | 8-12 | 7+2-9+4 | 10-12 |
-21 | -25 | - | - | - | - | 10-14 | 8+3-10+4 | 12-15 |
3. толщина утеплителя задается из расчета равномерности температурных полей по сечению конструкций в зависимости от различных толщин, углов, выступов и других частей.
Снятие теплоизоляционного укрытия, распалубливание и загружение конструкций должно производиться с соблюдением следующих требований:
· распалубливание несущих железобетонных конструкций следует производить после достижения бетоном прочности, полученной испытанием контрольных образцов;
· конструкции, подвергаемые попеременному оттаиванию и замораживанию, следует распалубливать после достижения 70% прочности от проектной;
· если разность температур поверхностного слоя бетона и наружного воздуха превышает 20°С для конструкции с Мп до 5 и 30°С с Мп>5, распалубленные конструкции должны укрываться на время, необходимое для выравнивания температур.
7.8 Электоротермообработка бетона.
7.8.1 Общие сведения.
Электротермообработка бетона основана на преобразовании электрической энергии в тепловую непосредственно внутри бетона путем пропускания через него электрического тока с помощью электродов (электродный прогрев) или различного рода электронагревательных устройствах (Тэнах, сетчатых, коаксиальных, инфракрасных и других нагревателях), тепло от которых подводится к бетону конвективно, контактно или радиоционно (электропрогрев).
Количества тепла, выделяемого в бетоне при прохождении через него тока, определяют по формуле Джоуля-Ленца:
Q = 3,61·J2·R = 3,61·U·J = 3,61· (U2/R) Дж,
где J – величина тока, А;
R – омическое сопротивление участка бетона, Ом;
U – напряжение, В;
Для перевода электрической мощности Р в тепловую применяют электрический эквивалент тепла, составляющий 3628,8 Дж/кВт: Р = Q/3628,8кВт
Электротермообработка бетона при возведении монолитных конструкций в зимних условиях применяется для предотвращения замораживания бетона и ускорения его твердения при любой температуре наружного воздуха до приобретения прочности, требующейся по проекту производства работ.
Наиболее эффективный – электродный прогрев с ограничением для густоармированных конструкций из-за трудности обеспечения равномерного температурного поля.
Электродный прогрев армированных конструкций должен производиться при напряжении не свыше 127В.
Электродный прогрев неармированных конструкций, а также обогрев внешними электрообогревателями и греющей опалубкой может производиться при напряжении 220-380В, в соответствии с ППР. Предварительный электроразогрев бетонной смеси выполняется при напряжении 220-380В.
Электотермообработка бетона наиболее эффективна до приобретения бетоном прочности 50-60% R28. При дальнейшей тепловой обработке интенсивность твердения замедляется, расход электроэнергии соответственно возрастает. При необходимости получения прочности бетона сразу после прогрева до 70% R28 рекомендуется, как правило, применять составы с минимально возможным В/Ц, вводить в бетон добавки – ускорители твердения. Для получения сразу после прогрева 80-100% R28 следует повышать фактическую марку бетона.
Режимы электротермообработки марку бетона.
а) Разогрев и изометрический прогрев (Рис.53,а), при котором требуемая прочность бетона должна быть достигнута к моменту окончания изотермического прогрева, а прирост прочности за время остывания не учитывается; этот режим рекомендуется применять для конструкций с модулем поверхности 10 и выше;
б) Разогрев и изометрический прогрев и остывание (Рис.53,б), при котором необходимая прочность бетона обеспечивается к концу его остывания, применяется для конструкции с модулем поверхности в пределах 6 – 15;
в) Разогрев и остывание (Рис.53,в) – заданная прочность обеспечивается к концу остывания; применяется для конструкций с модулем поверхности до 8;
г) Ступенчатый подъем температуры (Рис.53,г), при котором сначала производится прогрев 40 – 500 С, выдерживание при этой температуре в течение 1 – 3 ч, а затем быстрый подъем до максимально допустимой для данной конструкции температуры изотермического прогрева;
д) Саморегулирующий режим (только при электродном прогреве), который осуществляется при постоянном напряжений на электродах; изменение температуры в конструкции при этом обратно пропорциональному характеру изменения удельного электрического сопротивления бетона в процессе его твердения; температура бетона вначале возрастает, затем плавно снижается.
Рис.53 Температурные режимы электротермообработки бетонов.
Температурные режимы электротермообработки бетона характеризуется следующими параметрами:
- продолжительностью предварительного выдерживания бетона;
- скоростью подъема температуры;
- температурой изотермического прогрева;
- продолжительностью изотермического прогрева
- скоростью остывания
До начала подключения электрического тока бетон целесообразно выдерживать в течение 2-4часов. Разогрев бетона в конструкции во всех случаях должен начинаться при его температуре не ниже +2°С.
Скорость подъёма температуры не должна превышать:
· в конструкциях с модулем поверхности от 2 до 6 - 8°С в час;
· в конструкциях о модулем поверхности более 6 - 10°С в час;
· в каркасных и тонкостенных конструкциях небольшой протяженности (до 6 м), а также в конструкциях, возводимых в скользящей опалубке, - 15°С в час.
Изотермический прогрев должен производиться по возможности при максимально допустимой температуре, но не свыше значений, приведенных в таблице 24.
Таблица 24
Наивысшие допустимые температуры бетона при электропрогреве
Цемент | Наивысшие температуры (°С) для конструкций с модулем поверхности | |
до 10 | свыше 10 | |
Шлакопортландцемент и пуццо-лановый портландцемент Портландцемент Быстротвердеющий портландцемент | 90 80 75 | 80 70 70 |
Примечания: 1. При периферийном электропрогреве конструкций с модулем поверхности менее 6 наивысшая температура не должна превышать 40°С (в наружных слоях).
2. Максимальная температура прогрева монолитных каркасных и рамных конструкций с жесткой заделкой узловых сопряжений не должна превышать 40°С во избежание возникновения больших температурных напряжений.
Продолжительность изотермического прогрева (ти) в зависимости от требуемой после прогрева прочности и вида цемента ориентировочно может назначаться по графикам. Окончательный режим прогрева для конкретного состава бетонной смеси устанавливается строительной лабораторией по результатам опытных прогревов.
Выдерживание температуры бетона в соответствии с заданным режимом электротермообработки, должно осуществляться следующими способами:
· изменением величины напряжения, подводимого к электродам или электронагревательным устройствам;
· отключением электродов или электронагревателей от сети по окончании подъёма температуры;
· периодическим включением и отключением напряжения на электродах и электронагревателях, в том числе в режиме импульсного прогрева бетона путем чередования коротких импульсов тока с паузами.
Во всех случаях температура бетона является основным параметром, по которому регулируется подача электроэнергии и заданный режим. При этом максимально допустимые значения скорости подъёма температуры не должны быть превышены на наиболее нагретых участках, а продолжительность изотермического прогрева необходимо определять по температуре наименее нагретых участков.
Расчет электротермообработки бетона заключается в определении (теплотехническом расчете) требуемой мощности на нагрев бетона, опалубки и на восполнение теплопотерь в окружающую среду, с учётом тепловыделения цемента, и в последующем определении электрических параметров (напряжения, силы тока, типа и размещения электродов), которые обеспечивают выделение тепла соответственно величине требуемой мощности.
Требуемая удельная мощность Рп, необходимая по теплотехническому расчету для нагревания 1 м3бетона до заданной температуры, и мощность Ридля изотермического прогрева могут быть приняты по табл. 25 и 26 (применительно к бетону с объёмной массой 2400-2500 кг/м3) или подсчитаны по формулам
![]() |
![]() |
где Р1, Р2, Р3 - соответственно мощности для нагревания бетона, опалубки, восполнения потерь в окружающую среду;
Р4 = 0,8 кВт/м3 - среднее значение мощности, эквивалентное
экзотермическому теплу;
Р -скорость подъёма температуры бетона, град./ч;
Со -удельная теплоёмкость материала опалубки, ккал/град. * кг;
tи -температура изотермического выдерживания бетона или максимальная температура прогрева при отсутствии изотермического выдерживания, град.
Таблица 25
Удельная мощность, необходимая в период подъёма температуры бетона
Температура воздуха, оС
| Скорость подъёма температуры бетона, град/ч
| Удельная мощность, кВт/м3, при модуле поверхности | |||||||||||
6 | 10 | 15 | 20 | ||||||||||
Температура изотермического прогрева, °С | |||||||||||||
40 | 60 | 80 | 40 | 60 | 80 | 40 | 60 | 80 | 40 | 60 | 80 | ||
-10 | 5 10 15 | 3,5 7,4 11 | 3,7 7,5 11,2 | 3,8 7,6 11,4 | 4 8 12 | 4,3 8,3 12,2 | 4,6 8,6 12,5 | 4,7 8,9 13,0 | 5,1 9,3 13,5 | 5,6 9,7 13,9 | 5,4 9,7 11,2 | 5.9 9,8 14,7 | 6,5 10,9 15,3 |
-20 | 5 10 15 | 3,7 7,4 11,2 | 3,8 7,6 11,4 | 4 7,8 11,7 | 4,3 8,3 12,2 | 4,6 8,6 12,5 | 4,9 8,7 12,8 | 5,1 9,3 13,5 | 5,5 9,7 13,9 | 6 10,1 14,3 | 5,9 10,3 14,7 | 6,5 10,9 15,3 | 7,1 11,5 15,9 |
-30 | 5 10 15 | 3,8 7,6 11,4 | 4 7,8 11,6 | 4,2 7,9 11,7 | 4,6 8,6 12,5 | 4,9 8,8 12,8 | 5,07 9,1 13,1 | 5,5 9,7 13,9 | 6 10,1 14,3 | 6,4 10,6 14,7 | 6,5 10,9 15,3 | 7 11,1 15,8 | 7,6 .12 16,4 |
Требуемая мощность Р1 для подъёма температуры бетона с плотностью, не равной 2400 кг/м3, определяется по формуле
![]() |
где Pn – значение мощности по табл.25, кВт/м3
С1 – удельная теплоемкость легкого бетона, ккал/кг·град
γ1 – объемная масса легкого бетона, кг/м3
Величины требуемой мощности могут приниматься по таблице 26.
Удельный расход электроэнергии для прогрева бетона определяется по формулам
; ,
где Тn и Тu – соответственно продолжительность подъема температуры и изотермического прогрева, r.
Таблица 26
Удельная мощность, необходимая в период изотермического прогрева бетона
Температура воздуха, °С
| Удельная мощность, кВт/м3, при модуле поверхности | |||||||||||||
6 | 10 | 15 | 20 | |||||||||||
Температура прогрева, оС | ||||||||||||||
40 | 60 | 80 | 40 | 60 | 80 | 40 | 60 | 80 | 40 | 60 | 80 | |||
-10 | 0,8 | 1,1 | 1,4 | 1,4 | 1,9 | 2,4 | 2,0 | 2,3 | 3,6 | 2,8 | 3,7 | 4,8 | ||
-20 | 1,0 | 1,3 | 1,6 | 1,7 | 2,1 | 2,7 | 2,4 | 3,2 | 4,0 | 3,2 | 4,3 | 5,3 | ||
-30 | 1.1 | 1,4 | 1,8 | 2,0 | 2,4 | 2,9 | 2,8 | 3,6 | 4,4 | 3,7 | 4,8 | 5,9 | ||
Примечания:
1. Таблица составлена для скорости ветра V = 0 м/с.
2. Данные таблицы приведены для деревянной опалубки толщиной 40 мм и укрытия неопалубленной поверхности с аналогичным коэффициентом теплопередачи.
3. Для опалубки из досок толщиной 25 мм и укрытия неопалубленной поверхности с аналогичным коэффициентом теплопередачи значения удельной мощности будут превышать величины, указанные в таблице:
при скорости подъёма температуры 5° в час примерно в 1,2 раза;
при скорости подъёма температуры 10° в час примерно в 1,15 раза;
при скорости подъёма температуры 15° в час примерно в 1,08 раза.
Электродный прогрев
Для подведения напряжения используют электроды различной конструкции и схем расположения, между которыми протекает ток. В зависимости от расположения электродов и места прохождения тока прогрев подразделяют на сквозной и периферийный. При сквозном прогреве ток протекает через массу бетона и тепловая энергия выделяется в теле конструкции. В случае периферийного прогрева ток протекает через бетон между электродами, установленными по наружной поверхности конструкции. Бетон прогревается теплопередачей тепловой энергии от периферии внутрь конструкции.
Способ сквозного прогрева применяют для ускорения твердения бетонных и малоармированных железобетонных конструкций, так как арматура, являясь хорошим проводником, значительно искажает линии тока, создавая неравномерность температурных полей. Периферийный способ прогрева применяют для прогрева конструкций с одной стороны при толщине их до 20 см и с двух сторон при толщине более 20 см.
Интенсивность и количество выделяемой тепловой энергии в бетоне при прохождении тока зависит от электрической мощности, напряжения и электрического сопротивления бетона. Величина удельного электрического сопротивления бетона определяется главным образом количеством воды в единице объёма, концентрацией в ней электролитов и температурой. Удельное электрическое сопротивление изменяется в процессе электропрогрева бетона: в течение первых 2-5 ч оно снижается до минимальной величины ρмин которая составляет 0,5-0,85 от начальной величины в момент подачи напряжения на электроды ρнач.., затем ρначинает возрастать.
На рисунке 54 приведены основные типы электродов и схемы размещения электродов.
Рис. 54 Схемы размещения электродов.
Величины ρнач и ρмин колеблются в пределах соответственно от 400 до 2500 Ом * см и от то 200 до 1800 Ом * см. Увеличение содержания воды в бетоне вызывает существенное снижение ρ.Чем меньше испарения влаги в процессе электропрогрева, тем ниже ρмин и тем медленнее растет удельное электрическое сопротивления бетона после достижения минимального значения.
Величины ρнач и ρмин уменьшаются с увеличением расхода цемента. На величины ρ существенно влияет содержание в цементе водорастворимых щелочей, в связи с чем удельное сопротивление бетона одного состава на портландцементах разных заводов может различаться в 5 и более раз.
Повышение температуры снижает величину ρнач, однако через несколько часов после начала электропрогрева это снижение может оказаться менее значительным, чем увеличение р, вследствие процессов, происходящих за счет соответствующего ускорения твердения бетона, а также в результате испарения влаги.
Остывание свежеуложенного бетона вызывает повышение удельного сопротивления, а замерзание - настолько сильное повышение р, что бетон при обычно используемых величинах напряжения на электродах практически перестает проводить электрический ток.
При расчете электродного прогрева бетона и предварительного электроразогрева бетонной смеси в качестве расчётного параметра ρрасч следует принимать полусумму величин начального и минимального удельного электрического сопротивления.
При предварительных расчётах, если ρнач. известно, можно принимать для бетона ρрасч = 0,85 ρнач Определение удельного электрического сопротивления бетона каждого конкретного состава производится экспериментальным путем в лабораторных условиях.
При выборе типа электродов необходимо руководствоваться следующими правилами:
- электроды должны быть расположены, по возможности, на наружной поверхности прогреваемой конструкции, чтобы они не оставались в бетоне после прогрева; в случае применения внутренних электродов расход стали должен быть минимальным;
- установку и подключение электродов (без подачи напряжения) предпочтительнее осуществлять до начала бетонирования, что упрощает и ускоряет производство работ.
Схемы размещения электродов и графики для расчета электропрогрева приведены на рисунках 54...56
Графики позволяют:
- по заданному напряжению на электродах U, расстоянию между разноименными электродами b и известному удельному электрическому сопротивлению р найти величину электрической мощности;
- по заданным величинам электрической мощности Р и напряжения U, по известному удельному сопротивлению р - найти необходимое расстояние между разноименными электродами b;
- по заданным величинам электрической мощности Р и расстоянию между разнесенными электродами b, по известному удельному сопротивлению р найти требуемое напряжение U.
Для сквозного прогрева полосовыми электродами искомые величины определяются с учетом известной ширины полосовых электродов а и толщины прогреваемой конструкции В; в случае прогрева стержневыми электродами - расстояния между одноименными электродами h или ширины сечения тонкой конструкции H; при прогреве струнными электродами - диаметра струны d и диаметра арматурных стержней d1.
Следует учитывать, что арматурные стержни, расположенные вдоль направления движения тока, т.е. от электрода к электроду, искажают электрическое и соответственно температурное поле в бетоне, что может привести к местным перегревам и снижению прочности конструкции.
Во избежание недопустимых местных перегревов бетона у электродов и арматуры и увеличения фактической величины электрической мощности более чем на 15-20% по сравнению с расчетной необходимо соблюдать следующие расстояния между электродами и арматурой при напряжении в начале прогрева: 51В - не менее 3 см; от 60 до 70В - не менее 5 см; от 87 до 100В - не менее 7 см. При прогреве пластинчатыми электродами эти ограничения не принимаются во внимание.
Пластинчатые электроды (Рис.54) располагаются снаружи бетона на двух противоположных плоскостях конструкции, расстояние между которыми не превышает 40 см. Они обеспечивают равномерное температурное поле, подключаются до начала бетонирования, изготавливаются из кровельной стали, которая крепится к деревянной опалубке. Эти электроды применяются для прогрева неармированных конструкций, а также конструкций с негустой арматурой - колонн, балок, прогонов прямоугольного сечения, стен, перегородок и т.п.
Полосовые электроды располагаются снаружи бетона, изготавливаются из полосовой или кровельной стали шириной 2-5 см; крепятся к деревянной опалубке. Полосы при отсутствии соответствующего металла могут быть заменены круглыми стержнями при соблюдении соотношения d> а/2 (а - ширина полосы).
Полосовые электроды с двусторонним расположением для сквозного прогрева бетона (Рис.55,а) применяются вместо пластинчатых с целью экономии металла электродов.
Рис.55 Прогрев бетона полосовыми электродами.
Они обеспечивают достаточно равномерное температурное поле в бетоне, подключаются до начала бетонирования.
Полосовые электроды для периферийного прогрева конструкций располагаются снаружи бетона (Рис.55,б, в). Электрический ток проходит между соседними разноименными электродами, главным образом в периферийном слое бетона, толщина которого составляет около половины расстояния между соседними электродами.
Периферийный прогрев конструкции толщиной менее 30-40 см (предпочтительнее менее 20 см) можно, как правило, осуществлять полосовыми электродами с односторонним расположением (Рис.55,б) при негустой арматуре. Он особенно эффективен для конструкций, доступ к которым открыт только сверху: полов, днищ, перекрытий, бетонных подготовок и др. В этом случае полосовые электроды крепятся к нижней поверхности инвентарных деревянных щитов, укладываемых на верхнюю поверхность конструкции по мере бетонирования.
Периферийный прогрев конструкции толщиной менее 30 – 80 см можно осуществлять полосовыми электродами с двухсторонним размещением, а более массивных – размещением по всей поверхности конструкции.
Рис.56 Схемы размещения электродов.
При этом температура периферийных слоев бетона не должна превышать температуру в ядре конструкции во избежание неблагоприятного термонапряжённого состояния конструкции и образование трещин на её поверхности.
Следует учитывать, что температура в слое бетона, при одностороннем расположении полосовых электродов, будет на 15 – 20 0 С выше, чем на противоположной поверхности бетона.
Стержневые электроды из круглой стали диаметром 6 мм и более устанавливаются в бетон по мере или после окончания бетонирования конструкции, после прогрева они остаются в бетоне. Подключение производится по мере установки электродов или по окончании их установки. В зависимости от вида армирования конструкции и схемы размещения электродов температурное поле в бетоне может быть как достаточно равномерным,, так и обладать значительной степенью неравномерности.
Стержневые электроды могут быть применены для прогрева любых конструкции. При выборе электропрогрева с использованием стержневых электродов следует учитывать расход металла на электроды, остающиеся в бетоне, трудоёмкость их подключения и необходимость значительного разрыва во времени от окончания бетонирования до начала прогрева.
Наиболее целесообразно применять стержневые электроды в виде плоских групп (Рис.56), обеспечивающих достаточную равномерность температурного поля. Чем меньше расстояние h между одноименными электродами в плоской группе, тем равномернее температурное поле, но больше расход металла на электроды, трудоёмкость их установки и подключения.
Для электропрогрева бетонных и железобетонных элементов малой толщины и значительной протяженности используют одиночные стержневые электроды , которые устанавливают в бетон и подключают к разным фазам.
При прогреве конструкций с весьма густой арматурой, когда невозможно использовать плоские группы, применяют одиночные стержневые электроды, размещаемые в шахматном порядке на равных расстояниях b = h, которые составляют 20-40 см. Такое размещение приводит к значительной неравномерности температурного поля в бетоне.
К стержневым относятся и так называемые плавающие электроды - стальные прутки, втапливаемые на глубину 3-4 см в бетон конструкций малой толщины - подливок, набетонек и т.п., либо при периферийном прогреве верхних неопалубленных поверхностей массивных конструкций. Расчет прогрева тонких элементов плавающими электродами производится по графику, а при периферийном прогреве - на рисинке 55,б.
Струнные электроды представляют отдельные прутки, установленные в бетоне вдоль оси конструкции и подключаемые, как правило, до начала бетонирования. Они остаются в бетоне после прогрева. Температурное поле при этом способе электропрогрева характеризуется неравномерностью. Применяются для прогрева конструкций, длина которых во много раз больше размеров поперечного сечения колонн, балок, прогонов и т.п.
При прогреве конструкций прямоугольного сечения с четырьмя продольными арматурными стержнями в углах струну, устанавливаемую по оси конструкции, подключают к одной фазе, а арматурный каркас - к другой (Рис.57,а). Вместо одной струны в конструкциях значительной длины возможна установка двух или трех струн, подключенных к разным фазам (Рис.57,б, в).
Использование в качестве электродов арматуры прогреваемой конструкции, как правило, не рекомендуется во избежание пересушивания приэлектродных слоев и, следовательно, уменьшения сцепления арматуры с бетоном. В случае необходимости использования арматуры в качестве электродов следует принять меры во избежание перегрева бетона в приэлектродных слоях путем уменьшения скорости подъёма температуры.
Перед началом бетонирования производится осмотр установленных электродов, соединений проводов, отпаек и др. Перед подачей напряжения на электроды следует проверить правильность их установки и подключения, качество контактов и отпаек, которые могли быть нарушены при бетонировании; расположение температурных 'скважин или установленных в бетоне датчиков температуры; правильность укладки утеплителя; установить ограждение зоны электропрогрева, обозначенной плакатами и сигнальными лампами.
Рис.57 Прогрев бетона струнными электродами.
Дата добавления: 2018-04-05; просмотров: 855; Мы поможем в написании вашей работы! |
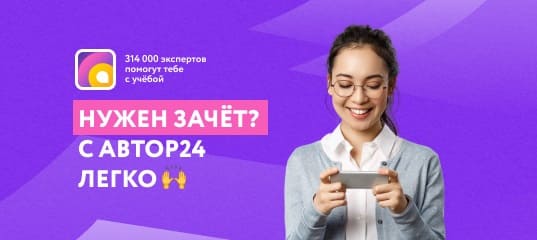
Мы поможем в написании ваших работ!