Литьё по выплавляемым моделям
Способ получения фасонных отливок из металлических сплавов в неразъёмной, горячей и негазотворной оболочковой форме, рабочая полость которой образована удалением литейной модели выжиганием, выплавлением или растворением.
При этом способе литья в пресс-формы (обычно металлические) запрессовывают модельный состав, который после затвердевания образует модели деталей и литниковой системы. Модельный состав удаляют, чаще всего выплавляя его в горячей воде (отсюда и название способа - литьё по выплавляемым моделям). Полученные оболочки прокаливают при температуре 800-1000°С и заливают металлом.
Способ обеспечивает получение сложных по форме отливок массой от нескольких г до десятков кг, со стенками толщиной от 0,5 мм и более, с поверхностью, соответствующей 4-6-му классам чистоты, и с высокой точностью размеров по сравнению с др. способами литья. Указанные особенности послужили причиной прежних названий способа - точное, или прецизионное литьё. Размеры отливок, полученных Л. по в. м., максимально приближены к размерам готовой детали, вследствие чего за счёт сокращения механической обработки снижается стоимость готового изделия.
Методом Л. по в. м. изготовляют художественные отливки, ювелирные изделия, зубные протезы и др. изделия. Этот способ литья, являясь одним из древних, получил широкое промышленное применение в результате совершенствования технологии литейного производства и изучения свойств кремнийорганических соединений.
|
|
В СССР Л. по в. м. сосредоточено в больших высокомеханизированных цехах, которые производят до 2,5 тыс. т готовых отливок в год. Достижением советской промышленности является создание комплексно-автоматизированного производства Л. по в. м.
Литьё в оболочковые формы.
Способ получения фасонных отливок из металлических сплавов в формах, состоящих из смеси песчаных зёрен (обычно кварцевых) и синтетического порошка (обычно фенолоформальдегидной смолы и пульвер-бакелита). Предпочтительно применение плакированных песчаных зёрен (покрытых слоем синтетической смолы).
Оболочковую форму получают одним из двух методов. Смесь насыпают на металлическую модель, нагретую до 300°С, выдерживают в течение нескольких десятков сек до образования тонкого упрочнённого слоя, избыток смеси удаляют. При использовании плакированной смеси её вдувают в зазор между нагретой моделью и наружной контурной плитой. В обоих случаях необходимо доупрочнение оболочки в печи (при температуре до 400°С) на модели. Полученные оболочковые полуформы скрепляют, и в них заливают жидкий сплав. Во избежание деформации форм под действием заливаемого сплава перед заливкой их помещают в металлический кожух, а пространство между его стенками и формой заполняют металлической дробью, наличие которой воздействует также на температурный режим охлаждающейся отливки.
|
|
Этим способом изготавливают различные отливки массой до 25 кг. Преимуществами способа являются значительные повышение производительности по сравнению с изготовлением отливок литьём в песчаные формы, управление тепловым режимом охлаждения отливки и возможность механизировать процесс.
Центробежное литьё. Литьё под давлением.
Рис. 11.22. Центробежное литье
Литьё центробежное - изготовление отливок в металлических формах, при котором расплавленный металл подвергается действию центробежных сил. Заливаемый металл отбрасывается к стенкам формы и, затвердевая, образует отливку. Этот способ литья широко распространён в промышленности при получении пустотелых отливок со свободной поверхностью - чугунных и стальных труб, колец, втулок, обечаек и т. п. В зависимости от положения оси вращения форм различают горизонтальные и вертикальные литейные центробежные машины. Горизонтальные машины (рис., 11.22а) наиболее часто применяют при изготовлении труб. При получении отливок на машинах с вертикальной осью вращения (рис., 11.22б) металл из ковша заливают в форму, укрепленную на шпинделе, приводимом во вращение электродвигателем. Центробежная сила прижимает металл к боковой цилиндрической стенке. Форма вращается до полного затвердевания металла, после чего её останавливают и извлекают отливку. Сложные внутренние стенки отливки выполняют при помощи стержней. Стенки форм для отливок со сложной наружной поверхностью покрывают формовочной смесью, которую уплотняют роликами, образуя необходимый рельеф. Отливки, полученные методом центробежного литья, по сравнению с отливками, полученными другими способами, обладают повышенной плотностью во внешнем слое.
|
|
Литьё под давлением металлов, способ получения отливок из сплавов цветных металлов и сталей некоторых марок в пресс-формах, которые сплав заполняет с большой скоростью под высоким давлением, приобретая очертания отливки. Этим способом получают детали сантехнического оборудования, карбюраторов двигателей, алюминиевые блоки двигателей и др. Литьё производят на литейных машинах с холодной и горячей камерами прессования (рис.11.23). Литейные формы, называются обычно пресс-формами, изготовляют из стали. Оформляющая полость формы соответствует наружной поверхности отливки с учётом факторов, влияющих на размерную точность. Кроме того, в пресс-форму входят подвижные металлические стержни, образующие внутренние полости отливок, и выталкиватели.
|
|
При получении отливок на литейных машинах с холодной камерой прессования (рис.11.23а,б) необходимое количество сплава заливается в камеру прессования вручную или заливочным дозирующим устройством. Сплав из камеры прессования под давлением прессующего поршня через литниковые каналы поступает в оформляющую полость плотно закрытой формы, излишек сплава остаётся в камере прессования в виде пресс-остатка и удаляется. После затвердевания сплава форму открывают, снимают подвижные стержни и отливка выталкивателями удаляется из формы. При получении отливок на машинах с горячей камерой прессования (рис.11.23в) сплав из тигля нагревательной печи самотёком поступает в камеру прессования. После заполнения камеры прессования срабатывает автоматическое устройство (реле времени, настроенное на определённый интервал), а поршень начинает давить на жидкий сплав, который через обогреваемый мундштук и литниковую втулку под давлением поступает по литниковым каналам в оформляющую полость формы и кристаллизуется. Через определённое время, необходимое для образования отливки, срабатывает автоматическое устройство на раскрытие формы, и отливка удаляется выталкивателями. У полученных отливок обрубают (обрезают) заливы (облой), элементы литниковых систем, затем их очищают вручную или на машинах; если необходимо, производят термообработку.
Для этого метода литья характерны высокая скорость прессования и большое удельное давление [30-150 Мн/м2 (300-1500 кгс/см2)] на жидкий сплав в форме. Качество отливок зависит от ряда технологических и конструктивных факторов, например выбора сплава, конструкции отливки, литниковой и вентиляционной систем, формы, стабильности температуры сплава и формы, вакуумирования формы для предупреждения образования пористости и т. д. Метод обеспечивает высокую производительность, точность размеров (3-7-й классы точности), чёткость рельефа и качество поверхности (для отливок массой до 45 кг из алюминиевых сплавов - 5-8-й классы чистоты). Производительность машин от 1 до 50 заливок в мин. Применяют многогнёздные формы, в которых за 1 заливку изготовляют более 20 деталей.
Рис.11.23 Литьё под давлением (схема)
Дата добавления: 2018-04-05; просмотров: 491; Мы поможем в написании вашей работы! |
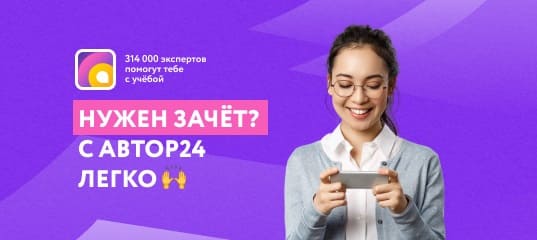
Мы поможем в написании ваших работ!