Группы улучшаемых конструкционных сталей по степени нагруженности деталей машин и механическим свойствам после закалки и высокого отпуска
ГЛАВА 4
ЛЕГИРОВАННЫЕ СТАЛИ И СПЛАВЫ
4.1.Влияние легирующих элементов на структуру и фазовые превращения в стали.
При назначении стали следует выбирать по возможности более простую по составу и дешевую сталь, которая может удовлетворить предъявляемым техническим требованиям. Простым и относительно дешевым конструкционным материалом является углеродистая сталь. Однако, углеродистая сталь обладает рядом существенных недостатков и далеко не всегда удовлетворяет требованиям, предъявляемым к деталям современных машин, работающим при высоких скоростях, больших давлениях и повышенных температурах.
Углеродистые стали отличаются малой глубиной закалки и прокаливаются насквозь лишь в сечениях не более 10…20 мм. В таких малых сечениях они имеют высокие механические свойства. При изготовлении деталей больших сечений (20…25 мм и более) углеродистая сталь вследствие малой прокаливаемости получает пониженные механические свойства. Поэтому углеродистые стали непригодны для изготовления ответственных деталей большого сечения.
Закаленные углеродистые стали сохраняют высокую твердость при нагреве до температур не выше 180…200 С. Поэтому инструмент из этих сталей не может работать с высокими скоростями и является малопроизводительным (температура нагрева режущей части инструмента возрастает с увеличением скорости резания металла). Углеродистые стали не имеют высоких особых физических и химических свойств (коррозионная стойкость, особые электрические и магнитные свойства и т. п.).
|
|
Наиболее универсальным способом повышения свойств стали является введение в сталь специальных легирующих элементов – легирование. Легированными сталями называются стали, содержащие один или несколько легирующих химических элементов (хром, никель, вольфрам, молибден, ванадий, титан и т.д.), специально вводимых для придания стали определенных свойств.
Стали, содержащие повышенное против обычного количества марганца (более 1%) или кремния (более 0,5%), такие являются легированными.
Распределение легирующих элементов в структуре стали. В промышленных сталях легирующих элементов в структуре в свободном состоянии не имеется. Эти элементы растворяются в феррите и в цементите или образуют с углеродом специальные карбиды.
Легирующие элементы, не образующие карбидов (никель, кремний, кобальт, медь), полностью растворяются в феррите, образуя легированный феррит. При этом свойства феррита изменяются.
Карбидообразующие легирующие элементы(хром,молибден, вольфрам, титан, марганец и др.) растворяются в карбиде железа Fe C или образуют специальные карбиды WC, TiC, Cr
C
и др.). Эти элементы могут также растворяться в феррите. Следовательно, карбидообразующие элементы в общем распределяются между карбидами и ферритом. Количественно это распределение зависит от сил связи легирующего элемента с углеродом и от относительного содержания углерода и легирующего элемента. Наибольшую устойчивость имеют карбиды титана, ванадия, ниобия.
|
|
Карбидообразующие элементы – хром и марганец – при небольших количествах растворяются в карбиде железа Fe C, частично замещая атомы железа и образуя легированный цементит (Fe,Cr)
C, (Fe,Mn)
С. С увели- чением количества хрома или марганца наряду с легированным цементитом образуется специальный карбид и, наконец, весь углерод связывается с легирующим элементом в специальный карбид (например,Cr
C
).
При нагреве выше критических точек карбиды хрома и марганца легко растворяются в аустените, а карбиды титана, ванадия, циркония и ниобия трудно растворимы в аустените и даже при высоких температурах нагрева они могут не раствориться полностью в аустените.
Влияние легирующих элементов на кинетику изотермического распада переохлажденного аустенита. Легирующие элементы, растворяющиеся в феррите или цементите (никель, марганец, кремний), не изменяют качественно диаграммы изотермического превращения переохлажденного аустенита. Все эти элементы, кроме кобальта, замедляют превращение (кривые распада аустенита смещаются вправо) и уменьшают критическую скорость закалки.
|
|
Карбидообразующие элементы (хром, молибден, вольфрам и др.) качественно изменяют диаграмму изотермического превращения пере- охлажденного аустенита. На диаг- рамме появляются две зоны превра- щений: перлитного и бейнитного (рис.93). Скорость превращения аус- тенита в перлит также замедляется. Наиболее значительное влияние на замедление перлитного превращения и уменьшение критической скорости закалки оказывают молибден, воль- фрам, марганец, хром. | ![]() |
Благодаря меньшей критической скорости закалка легированных сталей происходит при более медленном охлаждении (в масле) и прокаливаемость стали увеличивается. Замедление распада аустенита объясняется более медленной диффузией легирующих элементов, замедлением превращения и др. факторами.
Классификация легированных сталей по микроструктуре после охлаждения на воздухе. В металловедении получила распространение классификация легированных сталей по микроструктуре, которую получают небольшие образцы стали диаметром 20…25 мм после охлаждения на воздухе из области аустенита (900 С). По этой классификации легированные стали разделяются на пять классов: перлитный, мартенситный, аустенитный, ферритный и карбидный. Некоторые стали относятся к промежуточным классам.
|
|
Стали перлитного класса имеют перлито - ферритную, перлитную или перлито-карбидную структуру. К этой группе относятся стали с наибольшим количеством легирующих элементов (до 4…5%), применяемые преиму- щественно в качестве конструкционных сталей и, в меньшей степени, инструментальных сталей. Стали мартенситного класса имеют структуру мартенсита, отличаются высокой твердостью и хрупкостью. К этой группе относятся стали с более высоким содержанием легирующих элементов (4…14%), у которых линии распада аустенита на диаграмме изотермического превращения переохлажденного аустенита значительно сдвинуты вправо. Стали мартенситного класса в практике имеют меньшее применение.
Стали аустенитного класса получают после охлаждения на воздухе структуру аустенита. Эти стали с большим количеством никеля и марганца (до 10…15% и выше). Стали ферритного класса имеют после охлаждения на воздухе структуру феррита. К ним относятся стали с повышенным содержанием кремния, хрома при малом содержании углерода. Эти стали применяются в качестве сталей с особыми физическими и химическими свойствами.
Рис.94. Схемы диаграмм состояния железо - легирующий элемент.
Для выяснения причин образования сталей аустенитного и ферритного классов рассмотрим схемы диаграмм состояния «железо-легирующий элемент» (рис.94). Особенностью этих диаграмм является наличие перек- ристаллизации в твердом состоянии вследствие аллотропических превращений Fe
Fe
. Добавки легирующих элементов по различному влияют на образование областей
и
- растворов на диаграммах состояния. Одна группа легирующих элементов (никель, марганец) способствует образованию расширенной области твердого раствора
. В этом случае сплавы, содержащие большое количество легирующего элемента, при охлаждении из области жидкого раствора до комнатной температуры не испытывают превращений в твердом состоянии
. Такие сплавы при комнатной температуре имеют структуру
- раствора (аустенита).
Другая группа легирующих элементов (кремний, хром, алюминий, молибден, вольфрам и др.) способствует получению на диаграмме состояния «железо - легирующий элемент» суженной области - раствора и расширенной области твердого раствора
. В этих сплавах с повышенным содержанием легирующих элементов
- раствор (феррит) при охлаждении сохраняется до комнатной температуры.
Стали карбидного класса имеют в структуре большое количество специальных карбидов; при этом структура основы может быть различная (сорбит, мартенсит). Эти стали содержат большой процент карби- дообразующих элементов – вольфрам, хрома (до 10…20%) и повышенное количество углерода. Стали применяются для изготовления инструментов с высокой твердостью.
Следует иметь в виду, что рассмотренная классификация действительна лишь для неизменных условий охлаждения (охлаждение на воздухе небольших образцов). При изменении условий охлаждения микроструктура стали будет изменяться в соответствии с диаграммой изотермического превращения переохлажденного аустенита для данной стали.
Классификация по назначению и маркировка легированных сталей. По назначению легированные стали разделяются на следующие классы:
1.Конструкционные стали, применяемые для изготовления деталей машин.
2.Инструментальные стали, применяемые для изготовления инст- румента (режущего, штампового, мерительного).
3.Стали и сплавы с особыми свойствами (жаропрочные, корро- зионностойкие, магнитные и т.д.).
Для маркировки легированных сталей ГОСТ предусмотрена буквенно- цифровая система. Каждый легирующий элемент обозначается буквой : Х-хром, Н-никель, М-молибден, Г-марганец, В- вольфрам, Ф – ванадий, Т – титан, С – кремний, Ц – цирконий, Р – бор, Б – ниобий, Ю – алюминий.
Числа после буквы показывают примерное содержание легирующих элементов (при содержании легирующего элемента 1% и менее число не ставится). В конструкционных сталях число в начале марки показывает среднее содержание углерода в сотых долях процента; в высокоуглеродистых инструментальных сталях это число обозначает среднее содержание углерода в десятых долях процента. При содержании углерода более 1% число не ставится. Высококачественные стали с пониженным содержанием серы (менее 0,03%) и фосфора (менее 0,03%) обозначаются буквой А в конце марки (например, 30ХГСА).
Некоторые стали выделены в отдельные классы, например, ШХ15 – шарикоподшипниковая сталь с содержанием 1,5% хрома,Р18-быстрорежущая сталь с содержанием 18% вольфрама. Нестандартные опытные стали обозначаются буквами ЭИ (исследовательская) и порядковым номером (ЭИ 276 и др.).
Конструкционные стали
Механические свойства сталей.
Конструкционные стали, применяемые для изготовления деталей машин, должны обладать комплексом высоких механических свойств (прочностью, пластичностью и вязкостью). Простые углеродистые стали имеют высокие механические свойства в деталях малых сечений (10…15 мм). Так, стали 40, 45 имеют после закалки и высокого отпуска =590…680 МПа;
= 390…580 МПа;
=40…50%; КСU=0,4…0,5 Мдж/м
. Однако, в деталях с сечением более 20…25 мм их механические свойства понижаются из-за малой прокаливаемости. Для изготовления тяжелонагруженных деталей большого сечения применяют легированные стали, обладающие лучшим комплексом механических свойств. Повышение свойств при легировании стали объясняется следующими причинами:
1.Легирующие элементы увеличивают прокаливаемость стали и тем самым повышают механические свойства деталей большого сечения. Для получения комплекса высоких механических свойств в качестве окончательной термической обработки деталей машин обычно применяют закалку и высокий отпуск при 500…650 С (улучшение). При малой прокаливаемости (углеродистые стали) в результате термообработки в сердцевине образуется структура троостита, сорбита или даже феррита и перлита. Сталь с такими структурами имеет пониженные предел текучести, относительное сужение и ударную вязкость, т. е. свойства в сердцевине будут меньше свойств поверхностного слоя. Типовая схема изготовления деталей машин на машиностроительном заводе дана на рис. 95.
Легирующие элементы, особенно марганец, молибден, хром, замедляют скорость изотермического превращения переохлажденного аустенита, уменьшают критическую скорость закалки и, следовательно, увеличивают прокаливаемость. При сквозной прокаливаемости сталь имеет одинаковую микроструктуру по всему сечению (сорбит после высокого отпуска) и одинаковые механические свойства. Легированные стали имеют после улучшения =980…1070 МПа; КСU = 0,8…1,2 Мдж/м
. Эти свойства обеспечиваются в деталях больших сечений (80…120 мм и выше). Изменение прочности сталей различных марок после закалки и высокого отпуска (при равных величинах
=40% и КСU=0,6 Мдж/м
) в зависимости от поперечного сечения (по С. М. Баранову) приведено на рис. 96.
2.Легирующие элементы замедляют превращения при отпуске закаленной стали. С повышением температуры отпуска происходит распад мартенсита, выделение углерода из мартенсита и образование карбидов. Легирующие элементы замедляют скорость диффузии углерода и задерживают распад мартенсита; мартенсит сохраняется до более высоких температур нагрева. Особенно значительно затормаживают легирующие элементы (ванадий, молибден, вольфрам, хром) процессы роста и коагуляции
Рис.95.Типовая схема изготовления деталей машин на машиностроительном заводе.
карбидов. Поэтому при одинаковой температуре отпуска легированная сталь имеет более дисперсные карбиды по сравнению с углеродистой сталью.
Вследствие замедления превращения при отпуске легированные стали при одинаковых температурах отпуска отличаются большей прочностью и твердостью и пониженной пластичностью. Для достижения заданного снижения прочности или повышения пластичности и вязкости необходимо применять более высокую температуру отпуска. С повышением температуры отпуска улучшается сочетание прочности и пластичности легированных сталей.
![]() ![]() | 3.Легирующие элементы уп- рочняют...феррит. Конструкционные стали яв- ляются преимущественно сталями перлитного класса с содержанием углерода до 0, 45…0,50 %. В таких сталях около 95 % по объему составляет феррит и лишь 5% составляют карбиды, поэтому свойства феррита оказывают большое влияние на свойства стали. Легиру- ющие элементы, растворяясь в феррите, увеличивают его прочность и при содержании |
более 1…2% снижают ударную вязкость. Влияние легирующих элементов на свойства феррита показано на рис.97. Исключение составляет никель, который упрочняет феррит, увеличивает ударную вязкость феррита и понижает температуру перехода стали из вязкого состояния в хрупкое. Поэтому никель является особо ценным легирующим элементом в конструкционных сталях. Вследствие упрочнения феррита механические свойства легированных сталей при одинаковом режиме отпуска выше свойств углеродистых сталей.
4. Легирующие элементы измельчают зерно аустенита. Все леги- рующие элементы, за исключением марганца, замедляют рост зерна аустенита, особенно карбидообразующие элементы: титан, ванадий, цирконий, вольфрам, молибден, хром. Эти элементы образуют устойчивые карбиды, которые располагаются по границам зерен и задерживают рост зерна аустенита. Мелкозернистые стали имеют большую ударную вязкость по сравнению с крупнозернистыми сталями.
Дефекты легированных конструкционных сталей.
Легированные стали в большей степени, чем углеродистые, склонны к образованию различного рода дефектов. Важнейшими дефектами являются дендритная ликвация, флокены и отпускная хрупкость. Дендритная ликвация заключается и неоднородности распределения легирующих элементов в объеме дендрита: оси дендрита содержат меньшее количество легирующих элементов, а междуосные пространства – наибольшее количество этих элементов. После горячей обработки давлением сталей с развитой дендритной ликвацией наблюдается пониженная пластичность и ударная вязкость поперек волокон.
Уменьшение дендритной ликвации достигается диффузионным отжигом слитков при температуре 1000…1200 С с длительными выдержками.
-
![]() ![]() | Флокенами называются внут- ренние трещины в стали, наблю- даемые на поверхности макро- шлифов в виде волосовини в изломе в виде светлых овальных пятен. Флокены наиболее часто встре- чаются в хромоникелевых, хромо- никельвольфрамовых и хромони- кельмолибденовых сталях после ковки и прокатки сталей при диаметре заготовок более 30 мм. Наличие флокенов, играющих роль внутренних надрезов, резко ухуд- шает механические свойства сталей.
Образованию флокенов спо- собствует растворившийся в жидкой стали водород. При ускоренном охлаждении в интервале температур ниже 200 ![]() |
Внутренние напряжения, возникающие под влиянием давления выделяющегося в микропорах водорода и вследствие ускоренного охлаждения, вызывают образование трещин (флокенов) в малопластичной стали. Для предупреждения образования флокенов необходимо проводить медленное охлаждение стали после ковки и прокатки по особым режимам ; при этом водород успевает выделится из стали.
Отпускная хрупкость проявляется в понижении ударной вязкости при температурах отпуска закаленной стали 250…400 С (отпускная хрупкость
рода) и 500…650
С (отпускная хрупкость
рода) (рис.98). Отпускная хрупкость
рода наблюдается у всех конструкционных сталей и не устраняется путем изменения состава стали и термической обработкой. Предполагают, что наиболее вероятной причиной возникновения отпускной хрупкости
рода является неоднородность распада пересыщенного твердого раствора углерода в
- железе (мартенсита) и неравномерность выделения карбидов по границам и в объеме бывшего зерна аустенита. На практике избегают проводить отпуск конструкционных сталей в интервале температур возникновения отпускной хрупкости
рода.
Отпускная хрупкость рода обнаруживается при медленном охлаждении от температуры отпуска 500…650
С. В случае быстрого охлаждения в масле хрупкость отсутствует.
![]() | Образующаяся при медленном охлаждении хрупкость может быть устранена путем повторного отпуска с быстрым охлаждением.
К отпускной хрупкости ![]() ![]() |
рен аустенита при медленном охлаждении стали. Эти частицы и вызывают хрупкость стали. В случае быстрого охлаждения стали выделения дисперсных частиц не происходит и хрупкости не наблюдается. Отдельные исследователи объясняют отпускную хрупкость рода обогащением границ бывших зерен аустенита атомами некоторых элементов (особенно фосфора). При повторном отпуске до более высоких температур концентрация фосфора выравнивается по объему и хрупкость устраняется.
Термическая обработка конструкционных сталей.
На машиностроительных заводах вначале проводится предварительная термическая обработка заготовок деталей машин (поковок,штамповок и т.д.), а после механической обработки режущими инструментами - окончательная термическая обработка для придания деталям требуемых по техническим условиям физико - механических свойств. В качестве предварительной термической обработки для углеродистых сталей 20, 30, 40, 45 и малолегированных сталей 20Х, 40Х, 45Г2, 18ХГТ и др. применяют нормализационный отжиг со скоростью охлаждения 100…200 градусов в час. В условиях массово-поточного производства такая термическая обработка ведется в печах непрерывного действия.
Высоколегированные стали 40ХНМА, 35ХМА и др. имеют устойчивый аустенит, поэтому операция нормализационного отжига для этих сталей неприемлема. В случае применения отжига охлаждение необходимо вести с малой скоростью (20…30 градусов в час.). Для таких сталей с устойчивым аустенитом в качестве предварительной термической обработки применяется изотермический отжиг. При этом сталь нагревается выше критической точки А на 30…50
, охлаждается до температуры малой устойчивости аустенита и выдерживается при этой температуре до полного превращения аустенита в сорбит. Схема изотермического отжига приведена на рис. 99. Высоколегированные стали мартенситного класса (18Х2Н4ВА, 25ХНВА и
![]() | др.) смягчаются путем высокого отпуска при температурах 640…680 ![]() ![]() |
ческой точки А на 30…50
с последующим высоким отпуском для получения структуры сорбита (улучшение). Для деталей из углеродистых сталей 40, 45, 50 диаметром 10…15 мм применяется закалка в воде, а для легированных сталей типа 40Х, 45Г2, 30ХГТ, 40ХН и др.-закалка в масле. Более медленное охлаждение легированных сталей уменьшает внутренние напряжения в деталях. В термических цехах массового производства для проведения улучшения стали применяются агрегаты из закалочной печи, конвейерного закалочного бака, моечной машины и отпускной печи. Следует подчеркнуть, что при равном пределе прочности улучшаемая сталь со структурой сорбита отпуска по сравнению со структурой феррит + перлит имеет более низкую температуру перехода от вязкого разрушения к хрупкому (порог хладноломкости), т. е. обладает большей конструктивной прочностью.
В ряде случаев кроме улучшения применяются и другие варианты окончательной термической обработки среднеуглеродистых конструк- ционных сталей.
В случае необходимости получения более высокой прочности некоторые легированные стали (30ХГСА, 18Х2Н4ВА и др.) подвергаются закалке и низкому отпуску при температуре 200…250 С. После такой термической обработки стали имеют повышенную прочность при пониженной пластичности и вязкости.
В некоторых легированных сталях сочетание высокой прочности и вязкости достигается путем изотермической закалки. Распад аустенита производится при температурах 300…400 С, т.е. несколько выше линии М
в области бейнитного превращения аустенита. Это превращение у большинства легированных сталей не идет до конца, и структура состоит из бейнита и 10…20% остаточного аустенита. Если при последующем охлаждении остаточный аустенит не превращается в мартенсит и сохраняется до комнатной температуры, то сталь получает высокую прочность при хорошей вязкости.
Наиболее высокий предел прочности 2450…2900 МПа при ударной вязкости 0,3…0,4 Мдж/м достигается путем термомеханической обработки (ТМО), при которой совмещаются, пластическая деформация стали в аустенитном состоянии с ее закалкой. Разработано два варианта ТМО (рис. 100). При высокотемпературной ТМО (ВТМО) изделия нагреваются выше критической точки А
в область аустенита, деформируются при этих температурах и закаливаются, а затем подвергаются низкотемпературному отпуску. В случае низкотемпературной ТМО (НТМО) после выдержки при температуре выше А
сталь быстро охлаждается до температуры относительной устойчивости аустенита (400…500
С) и при этих температурах деформируется. Далее проводится окончательное охлаждение (закалка) и низкотемпературный отпуск.
![]() | Сталь упрочняется при ТМО в результате образования при закалке деформированного аустенита скоп- лений дислокаций с высокой плот- ностью в мартенсите и измельчения кристаллов мартенсита на отдельные фрагменты (объединения блоков), повернутые на угол 10…15 ![]() |
Таблица 9.
Механические свойства стали 30ХГСА после различной термической обработки.
№ п/п | Термическая обработка | Механические свойства | |
![]() | KCU,Мдж/м ![]() | ||
1 | Закалка с высокотемпературным отпуском ( улучшение) | 980…1170 | 0,8…1,2 |
2 | Закалка с низкотемпературным отпуском | 1560…1760 | 0,4 …0,6 |
3 | Изотермическая закалка | 1560…1700 | 1,0…1,1 |
4 | Термомеханическая обработка с низкотемпературным отпуском | 2450…2900 | 0,3…0,4 |
Цементуемые стали.
Цементуемые стали содержат 0,10…0,25% углерода, иногда до 0,3%. Эти стали получают высокую твердость и износостойкость поверхностного слоя, и высокие механические свойства сердцевины путем цементации с последующей закалкой и низкотемпературным отпуском. Упрочнение сердцевины сталей при термической обработке определяется характером диаграммы изотермического превращения переохлажденного аустенита.
Рис.101.Схема диаграмм изотермического превращения переохлажденного аустенита цементуемых сталей (обозначения в тексте).
Положение С-образных кривых распада аустенита зависит от содер- жания легирующих элементов в стали. Схемы диаграмм изотермического превращения переохлажденного аустенита для цементуемых сталей приве- дены на рис.101: а–углеродистые стали;б-малолегированные стали; в-высоколегированные стали.
Цементуемые стали разделяются на следующие основные группы:
1.Углеродистые стали 10,15,20. У этих сталей при термической обработке упрочняется только поверхностный слой. Вследствие малой устойчивости аустенита в сердцевине деталей аустенит превращается в феррит + перлит и упрочнения сердцевины почти не происходит. Эти стали применяются для изделий небольших размеров, не требующих высокой прочности сердцевины деталей.
2.Малолегированные стали 15Х, 20Х, 20ХН и др. имеют сквозную закалку в сечениях до 15…20мм; при этом вследствие большей устойчивости аустенита в сердцевине аустенит превращается в бейнит и предел прочности сердцевины возрастает до 730…830 МПа. Эти стали применяются для более нагруженных изделий, сердцевина которых должна иметь высокую прочность.
3.Высоколегированные стали 20Х2Н4, 20ХГР, 18ХГТ, 18Х2Н4ВА и др. (высокопрочные цементуемые стали) имеют прокаливаемость 25…100мм.
При закалке в сердцевине аустенит превращается в бейнит или в малоуглеродистый мартенсит и предел прочности сердцевины составляет 980…1250 МПа. Стали применяются для деталей ответственного назначения, испытывающих значительные динамические нагрузки.
Данные о цементуемых сталях приведены в табл.10.
Таблица 10.
Группы цементуемых конструкционных сталей по степени нагруженности деталей машин и механическим свойствам сердцевины деталей после цемента- ции, закалки и низкого отпуска.
Некоторые типовые примеры марок цементуемых сталей | Механические свойства сердцевины детали | ||
Предел прочности,
![]() | Предел текучести, ![]() | Ударная
вязкость,
мДж/м ![]() | |
1.Малонагруженные детали машин (прокаливаемость при закалке малая) | |||
Углеродистые стали марок:10,15,20 | 380…460 | 245…295 | малая (не приводится) |
2.Средненагруженные детали машин (прокаливаемость при закалке в сечениях 10…20мм) | |||
Легированные стали марок 15Х,20Х, 15ХР, 20ХР и др. | 730…830 | 590…690 | 0,8…1,2 |
3.Высоконагруженные детали машин (прокаливаемость при закалке в зависимости от марки стали от 20 до 100мм) | |||
Легированные стали марок 12ХГМ, 20ХГР, 25ХГМ, 12ХН3А, 15ХГН2ТА, 20ХН2М и др. | 980…1270 | 830…1080 | 0,7…1,0 |
Данные об основных типах конструкционных цементуемых сталей рассмотрены ниже.
Хромистые стали 15Х,20Х предназначены для изготовления изготовления небольших изделий простой формы, цементируемых на глубину 1,0…1,5 мм. Хромистые стали по сравнению с углеродистыми обладают более высокими прочностными свойствами при некоторой меньшей пластичности в сердцевине и лучшей прочности в цементируемом слое, прокаливаемость низкая.
Хромоникелевые стали применяются для крупных деталей ответственного значения, испытывающих при эксплуатации значительные динамические нагрузки. Повышенная прочность, пластичность и вязкость сердцевины и цементированного слоя. Стали малочувствительны к перегреву при длительной цементации и не склонны к перенасыщению поверхностных слоев углеродом (12Х2Н4А и др.)
Хромомарганцевые стали применяют во многих случаях вместо дорогих хромоникелевых. Однако они менее устойчивы к перегреву и имеют меньшую вязкость по сравнению с хромоникелевыми. В автомобильной и тракторной промышленности, станкостроении применяют стали 18ХГТ и 25ХГТ.
Хромомарганцевоникелевые стали. Повышение прокаливаемости и прочности хромомарганцевых сталей достигается дополнительным легированием их никелем. На ВАЗе широко применяют стали 20ХГНМ, 19ХГН и 14ХГН. После цементации и термообработки эти стали имеют высокие механические свойства.
Улучшаемые среднеуглеродистые стали.
В качестве улучшаемых сталей применяются стали с содержанием 0,3…0,5% углерода. Для получения комплекса высоких механических свойств (прочности в сочетании с вязкостью и конструктивной прочностью) эти стали обычно подвергаются закалке с высокотемпературным отпуском (улучшением). В зависимости от условий нагружения деталей машин и прокаливаемости улучшаемые конструкционные стали разделяются на три группы (табл. 11).
Таблица 11
Группы улучшаемых конструкционных сталей по степени нагруженности деталей машин и механическим свойствам после закалки и высокого отпуска
Улучшаемые стали (основные разно- видности и примеры марок)
| Механические свойства | |||
Предел прочности, МПа | Предел текучести, МПа. | Ударная
вязкость,
мДж/м ![]() | ||
1.Малонагруженные детали машин (прокаливаемость при закалке в сечениях до 10…12мм) | ||||
Углеродистые стали:35, 40,45 | 600…700 | 400…600 | 0,4…0,5 | |
2.Средненагруженные детали машин (прокаливаемость при закалке в сечениях до 20…50мм) | ||||
Хромистые: 40Х,45Х Марганцовистые: 45Г2 Хромомарганцовистые (дополнительно вводят титан или бор): 30ХГТ, 40ХГР | 900…1100 | 700…850 | 0,6…0,9 | |
3.Высоконагруженные детали (прокаливаемость при закалке в сечениях до 75… 100мм) | ||||
Хромоникелевые: 40ХН Хромомагранцевоникелевые: 40ХГН Хромоникельмолибденовые: 40ХНМ Хромоникельмолибденованадиевые:38ХГ3МФ | 1000…1200 | 800…1100 | 0,7…1,0 | |
К сталям первой группы относятся углеродистые стали марок 35,40,45. Эти стали имеют малую прокаливаемость (10…18 мм) и используются для изготовления деталей с небольшим поперечным сечением или работающих при небольших нагрузках (валики, втулки, гайки и т.д.).
Во вторую группу входят хромистые, марганцовистые и хромомарганцовистые стали, имеющие прокаливаемость 20…40 мм. Одним из важнейших легирующих элементов в конструкционных сталях является хром, вводимый в количестве 0,5…1,8%. Введение хрома увеличивает устойчивость аустенита на диаграмме изотермического превращения и повышает прокаливаемость стали. Широко используются хромистые стали марок 30Х,40Х,45Х, применяемые для изготовления коленчатых валов, шестерен, валов ответственного назначения. Дополнительное увеличение прокаливаемости достигается путем присадки 0,002…0,004% бора в хромистые стали (стали марок 35ХР, 40ХР).
Марганцовистые стали (40Г2, 45Г2) имеют повышенную прока- ливаемость по сравнению с углеродистыми сталями. Недостатком этих сталей является их крупнозернистость и склонность к отпускной хрупкости. Из марганцовистых сталей изготовляются шатуны, оси и другие детали, подвергающиеся высоким нагрузкам.
Дополнительное увеличение прокаливаемости конструкционных сталей достигается при одновременном легировании хромом и марганцем (40ХГ и др.). К числу недостатков этих сталей относятся большая склонность к росту зерна аустенита и отпускной хрупкости. Для предотвращения роста зерна аустенита в хромомарганцовистые стали вводится небольшое количество титана (стали 30ХГТ, 40ХГТ).
Широкое распространение, особенно в самолетостроении, получили хромомарганцовокремнистые стали типа хромансил 30ХГС, 35ХГС. Эти стали имеют повышенную прокаливаемость, высокую прочность и хорошую свариваемость.
К улучшаемым сталям третьей группы относятся хромоникелевые стали 40ХН, 45ХН, 50ХН, 30ХН3А и др. Эти стали вследствие малой критической скорости закалки имеют большую прокаливаемость при закалке в масле (более 40 мм) и позволяют получать однородную структуру сорбита в крупных изделиях. Никель является важнейшим легирующим элементом в конструкционных сталях. Введение никеля упрочняет сталь и снижает температуру перехода стали из вязкого состояния в хрупкое (порог хладноломкости). Хромоникелевые стали применяются для крупных изделий сложной конфигурации, работающих при высоких динамических нагрузках. Недостатком этих сталей является большая склонность к отпускной хрупкости второго ряда.
Отпускная хрупкость устраняется дополнительным введением в сталь молибдена. Хромоникелемолибденовые стали (40ХНМ и др.) обладают наибольшей прокаливаемостью вследствие большой устойчивости аустенита. Эти стали применяются для наиболее ответственных и крупных деталей машин. Молибден в стали 40ХНМ может быть заменен вольфрамом. Дальнейшее повышение прочности хромоникелемолибденовых сталей достигается введением 0, 10…0,15% ванадия.
Данные о механических свойствах некоторых улучшаемых сталей приведены в табл.12.
Таблица 12.
Механические свойства некоторых типовых конструкционных среднеугле- родистых сталей после закалки и высокого отпуска при температуре 540…600 С.
Марка улучшаемой стали | Оптовая цена (усл.ед.) | Среднее значение критического | Предназначены для деталей с максимальным поперечным сечением,мм | Механические свойства | ||
![]() | ![]() | НВ | ||||
40 | 1,0 | 12 | 15…20 | 450 | 660 | 167…207 |
45 | 1,0 | 12 | 15…20 | 490 | 730 | - |
45Х | 1,2 | 15 | 25…35 | 800 | 900 | 197…235 |
40ХН | 1,6 | 25 | 50…75 | 800 | 1000 | 300…325 |
30ХГС | 1,4 | 25 | 50…75 | 980 | 1080 | HRC 32…38 |
40ХН2МА | 2,1 | 100 | 75…100 | 950 | 1050 | HRC 29…33 |
38ХН3МФА | 2,6 | 100 | 100…200 | 1070 | 1150 | - |
Краткая характеристика основных видов конструкционных улучшаемых легированных сталей приведена ниже.
Хромистые стали 30Х, 38Х и 50Х применяют для средненагруженных деталей небольших размеров. С увеличением содержания углерода возрастает прочность, но снижаются пластичность и вязкость. Прокаливаемость хромистых сталей невелика.
Хромомарганцевые стали. Совместное легирование хромом (0,9…1,2%) и марганцем (0,9…1,2%) позволяет получить стали с достаточно высокой прочностью и прокаливаемостью (40ХГ). Однако хромо- марганцевые стали имеют пониженную вязкость, повышенный порог хладноломкости (от 20 до -60 С), склонность к отпускной хрупкости и росту зерна аустенита при нагреве.
Хромокремнемарганцевые стали. Высоким комплексом свойств обладают хромокремнемарганцевые стали (хромансил). Стали 25ХГС и 30ХГС обладают высокой прочностью и хорошей свариваемостью. Стали хромансил применяют также в виде листов и труб для ответственных сварных конструкций (самолетостроение). Стали хромансил склонны к обратимой отпускной хрупкости и обезуглероживанию при нагреве.
Хромоникелевые стали обладают высокой прокаливаемостью, хорошей прочностью и вязкостью. Они применяются для изготовления крупных изделий сложной конфигурации, работающих при динамических и вибрационных нагрузках (40ХН и др.).
Хромоникелемолибденовые стали. Хромоникелевые стали обладают склонностью к обратимой отпускной хрупкостью, для устранения которой многие детали небольших размеров из этих сталей охлаждают после высокого отпуска в масле, а более крупные детали в воде. Для устранения этого дефекта стали дополнительно легируют молибденом (40ХН2МА) или вольфрамом.
Хромоникелемолибденованадиевые стали обладают высокой прочностью, пластичностью, вязкостью и низким порогом хладноломкости. Этому способствует высокое содержание никеля. Недостатками сталей являются трудность их обработки резанием и большая склонность к образованию флокенов. Стали применяют для изготовления наиболее ответственных деталей турбин и компрессорных машин (38ХН3МФ).
Мартенситно-стареющие высокопрочные стали.
Применение в технике получила высокопрочная мартенситно-стареющая сталь Н18К9М5Т (масс.%: 0,03 С, 18Ni, 9Со, 5Мо, 0,6 Тi). Кроме стали Н18К9М5Т нашли применение менее легированные мартенситно-стареющие стали: Н12К8М3Г2, Н10Х11М2Т (
=1400…1500 МПа), Н12К8М4Г2, Н9Х12Д2ТБ (
=1600…1800 МПа). Мартенситно-стареющие стали имеют высокий предел упругости.
Детали из этих сталей подвергаются закалке на мартенсит и последующему отпуску при температуре 480…540 С. В процессе отпуска (старения) из высоколегированного мартенсита выделяются очень дисперсные частицы интерметаллидов, упрочняющие сталь.
Мартенситно-стареющие стали применяют в авиационной промышленности, ракетной технике, судостроении, приборостроении для упругих элементов, в криогенной технике и т. д. Эти стали дорогостоящие.
Хладностойкие материалы.
Хладностойкими называют материалы, сохраняющие достаточную вязкость при низких температурах от 0 до -269 С (температура жидкого гелия). Высокую пластичность и вязкость при отрицательных температурах сохраняют стали аустенитного структурного класса с кристаллической решеткой гранецентрированного куба. К ним относятся стали марок 03Х13АГ19, 12Х18Н10Т, 10Х11Н23Т3МР и др. Эти стали применяют в холодильной и криогенной технике.
Материалы для атомного машиностроения.
Конструкции ядерных реакторов, к которым относятся корпуса реакторов, системы трубопроводов, защитные оболочки тепловыделяющих элементов, регулирующих стержней и др., работают в условиях радиационного облучения нейронами и другими тяжелыми частицами ( - частицы, осколки ядер и т.д.). При этом возникают структурные повреждения, смещение положительно заряженных ионов, образование вакансий и межузельных атомов. В результате происходит возрастание прочности и снижение пластичности материала.
Материалами, способными к длительной работе при температурах до 500…600 С в контакте с жидким натрием и другими расплавленными металлами, являются коррозионностойкие хромоникелевые аустенитные стали.
Для работы при более высоких рабочих температурах используются сплавы циркония с оловом, содержащие 1,3…1,6% олова, 0,03…0,05% гафния, не более 0,06% кислорода и азота.
Рессорно-пружинные стали.
Стали для пружин и рессор должны иметь высокий предел упругости (текучести) и предел выносливости; пластические свойства стали имеют меньшее значение. Для изготовления пружин и рессор применяются конструкционные стали с повышенным содержанием углерода ( 0,5…0,7% ) марок 65, 65Г, 60С2, 50ХФА и др. Окончательная термическая обработка пружин и рессор заключается в закалке от температуры выше критической точки А в масле или в воде с последующим средним отпуском при температуре 400…500
С. Средний отпуск применяется для получения высокого предела упругости, т.к. при этих температурах отпуска предел упругости имеет максимальное значение. Рессорно-пружинные стали имеют после термической обработки предел прочности 980…1850 МПа и предел текучести 780…1650 МПа.
Усталостная прочность пружин и рессор может быть повышена путем поверхностного наклепа с помощью обдувки дробью. При этом поверхность
изделия подвергается наклепу на глубину 0,2…0,4 мм стальной или чугунной дробью. Возникающие в этом слое напряжения сжатия повышает предел усталости, и уменьшают вредное действие различных дефектов поверхности рессор и пружин. Дробеструйная обработка применяется и для других деталей, работающих в условиях знакопеременных нагрузок (зубья шестерен, галтели коленчатых валов, полуоси автомобилей, пальцы гусеничные и др.).
Шарикоподшипниковые стали.
Стали для подшипников качения должна иметь высокую твердость, износостойкость, прочность и предел выносливости. В качестве шарикоподшипниковой стали применяются высокоуглеродистые стали с содержанием 0,95…1,15%С, легированные хромом (ШХ6, ШХ9, ШХ15; число в обозначении марки указывает среднее содержание хрома в десятых долях процента). Стали должны иметь минимальное количество металлургических дефектов (неметаллических включений, пор и др.). Эти дефекты служат концентраторами напряжений и могут привести к образованию трещин и выкрашиванию стали.
Термическая обработка шарикоподшипниковых сталей включает две основные операции – закалку от температуры выше критической точки А и низкотемпературный отпуск при 150…160
С. После закалки сталь получает структуру из мартенсита, избыточных карбидов и до 10…12 % остаточного аустенита. При последующей эксплуатации подшипников остаточный аустенит может превратиться в мартенсит и размеры подшипников будут увеличиваться. Для уменьшения количества остаточного аустенита и предотвращения изменений размеров закаленная сталь подвергается обработке холодом при температурах (-10)…(-20)
С.
Очень крупные роликовые подшипники диаметром 0,5…2,0 м из- готовляются из цементуемой хромоникелевой стали 20Х2Н4А.
Аустенитная сталь высокой износостойкости.
В качестве износостойкой стали, когда изнашивание происходит при одновременном приложении сильного давления или ударов, применяется марганцовистая литая сталь марки 110Г13Л (1,1% углерода и 13% марганца) аустенитного класса (сталь Гадфильда). Литая сталь имеет структуру из аустенита и карбидов, как видно из схемы микроструктуры (рис. 102).
Путем закалки с 1100 С в воде получают однофазную структуру аустенита. Закаленная сталь отличается высоким пределом прочности (до 1080 МПа) при значительной пластичности и вязкости (
до 60…80%).
![]() | Вследствие высокой пластичности сталь имеет резко выраженную спо- собность к упрочнению (наклепу) при холодной пластической деформации. При этом твердость возрастает, что и обуславливает хорошую износостой- кость стали. Сталь 110Г13Л применяется в тех случаях когда необходимо иметь высо- кую износостойкость и большую вяз- |
кость при воздействии значительных давлений и ударах (траки гусеничных машин, крестовины железнодорожных путей, щеки дробилок для измельчения камней, зубья ковшей экскаваторов, броня несгораемых шкафов и др.). Механическая обработка такой стали затруднена, т.к. при резании возникает наклеп и сталь упрочняется. Поэтому детали из стали 110Г13 часто изготавливают способами литейного производства.
4.3. Инструментальные материалы.
В зависимости от назначения и условий работы в машиностроении различают, стали и сплавы для режущего инструмента, штампов и мерительного инструмента.
Стали для режущего инструмента. Эти стали в готовом инструменте должны иметь следующие свойства:
1.Высокую твердость (НRС 60…65) и износостойкость для сохранения формы и размеров режущих кромок при резании.
2.Высокую прочность для предотвращения выкрашивания и поломок инструмента.
3.Удовлетворительную вязкость для предупреждения поломок при вибрациях и ударах.
В качестве инструментальных сталей применяют углеродистые, легированные и быстрорежущие стали. Углеродистые стали У10, У11, У12 (число показывает среднее содержание углерода в десятых долях процента) используются для изготовления инструментов, работающих с небольшими скоростями (метчики, развертки, плашки и др.). Из легированных сталей преимущественно применяются хромистые стали и стали с дополнительными добавками марганца и других элементов (Х, ХГ, 9ХС, ХВГ и др.). Они используются для изготовления фасонного инструмента (сверла, фрезы, протяжки и др.).
Окончательная термическая обработка инструмента состоит из закалки и низкого отпуска. Нагрев под закалку рекомендуется проводить в аннах с расплавленными солями (например, 50% NaCl и 50%KCl), что обеспечивает защиту от окисления и обезуглероживания, большую скорость нагрева (20…30 с на 1 мм толщины). Температура нагрева принимается выше линии А на 50…70
С (~780…830
С). Охлаждение в зависимости от состава стали и типа инструмента ведется различными способами. Инструмент из углеродистой стали вследствие большой критической скорости закаливается через воду в масло или в масле (инструмент малых сечений). Прокаливаемость углеродистых сталей небольшая (10…12 мм при закалке в воде). Для инструментов из легированных сталей, у которых критическая скорость меньшая, применяется закалка в масле, расплавленных солях и щелочах (ступенчатая и изотермическая закалка). Легирование позволяет значительно увеличить прокаливаемость (до 75…100 мм при закалке в масле).
Нагрев в ваннах с расплавленными солями и охлаждение в смеси щелочей NaOH и KOH позволяет сохранять почти без изменения цвет поверхности закаливаемого инструмента («светлая» закалка).
Для уменьшения напряжений и хрупкости при сохранении высокой твердости инструмента после закалки проводится низкий отпуск при 160…180 С с выдержкой 0,5…1,0 час. Инструмент из углеродистых и легированных сталей сохраняет высокую твердость, полученную в результате термической обработки, при нагреве до температур 200…250
С.
Быстрорежущие стали по химическому составу являются высоколегированными с содержанием 5,5…18% вольфрама, 3…4%хрома, 1…5% ванадия и 0,5…5,5% молибдена. Характерным свойством этих сталей является теплостойкость-способность сохранять мартенситную структуру, высокую твердость и износостойкость при нагреве до повышенных температур (600…650 С). Высокая твердость мартенсита сохраняется до таких температур, пока не произойдет распад мартенсита и выделение мелкодисперсных карбидов. У углеродистых сталей распад мартенсита и выделение частиц карбидов железа происходит при температурах 80…300
С и твердость понижается. В высоколегированных быстрорежущих сталях эти превращения замедляются. Специальные карбиды Fe
W
C в этих сталях выделяются из мартенсита и укрупняются при более высоких температурах (выше 500
С), поэтому твердость сохраняется при нагреве до этих повышенных температур.
Температура разогрева инструмента при резании металлов возрастает с повышением скорости резания. При механической обработке инструментом из быстрорежущей стали благодаря свойству теплостойкости можно применять более высокие скорости резания по сравнению с обработкой инструментами из углеродистой и легированной сталей.
Литая быстрорежущая сталь имеет структуру из ледебурита (смесь карбидов Fe W
C и перлита) и перлита (смесь феррита и мелких карбидов) (рис. 103,а). При горячей обработке давлением хрупкая сетка ледебурита (эвтектики) раздробляется и карбиды измельчаются. Структура кованой и отожженной стали состоит из крупных первичных карбидов и мелких карбидов, распределенных по всему объему феррита (структура типа сорбита) (рис. 103,б).
Рис.103. Схема микроструктуры быстрорежущей стали в литом состоянии (а) и после ковки и отжига (б).
Окончательная термическая обработка инструмента из быстрорежущей стали состоит из операций закалки и отпуска (рис.104). Закалка быстрорежущей стали в отличие от других инструментальных сталей проводится от высоких температур 1260…1280 С, т.е. значительно выше критической точки А
(800…850
С). Нагрев под закалку проводится в соляных ваннах или в печах с защитной атмосферой. На первой стадии до температуры 850…900
С нагрев ведется медленно во избежание образования трещин вследствие малой теплопроводности стали. При этом карбиды почти не растворяются в аустените. Вторая стадия нагрева в интервале температур 900…1280
С проводится очень быстро для предотвращения роста зерна аустенита и обезуглероживания поверхностного слоя. При этом происходит частичное растворение карбидов Fe
W
C в аустените, количество карбидов уменьшается с 25 до 15…17% и, соответственно, содержание вольфрама в аустените возрастает с 1 до 8%. Следовательно, нагрев при закалке до высоких температур применяется для получения высоколегированного вольфрамом аустенита. Охлаждение при закалке ведется в масле для инструмента простой формы или в соляных ваннах (ступенчатая и изотермическая закалка для фасонного инструмента). При охлаждении высоколегированный аустенит превращается в высоколегированный мартенсит: Fe
(C,W)
Fe
(C,W).
![]() | Микроструктура закаленной стали состоит из мартенсита, остаточного аустенита (20…30%) и карбидов (15…17%). Для повы- шения твердости закаленная быстрорежущая сталь подвергается отпуску при 560 ![]() |
Для полного превращения остаточного аустенита в мартенсит отпуск проводится два - три раза. В результате отпуска твердость стали повышается от НRС 63 до 65 и прочность на изгиб возрастает от 1950 до 3150 МПа.
Различают две группы быстрорежущих сталей:
1.Стали нормальной производительности (умеренной теплостойкости) Р6М5, Р12 и др. для механической обработки резанием материалов средней твердости ( буква Р означает быстрорежущую сталь, число после буквы Р – среднее содержание вольфрама в процентах).
2.Стали повышенной производительности (высокой теплостойкости) Р14Ф4, Р9К5, Р9К10, Р18К5Ф2 и др., дополнительно легированные ванадием или кобальтом ( буквы Ф и К означают ванадий и кобальт, числа после букв – среднее содержание этих элементов в процентах). Эти стали применяются для механической обработки резанием жаропрочных и коррозионностойких сталей, титановых сплавов и других труднообрабатываемых резанием материалов.
Особую группу вольфрамосодержащих сталей составляют порошковые быстрорежущие стали, изготовляемые способами порошковой металлургии (МП). По одному из способов порошок, полученный распылением струи расплавленной быстрорежущей стали аргоном, прессуют при давлении 700…800 МПа, спекают при 1230…1270 С 1 час, получая заготовки с относительной плотностью 99,9…100,0%. После дополнительной горячей ковки нагретых до 1140…1180
С заготовок при давлениях 600…800 МПа или применения способов горячего изостатического прессования (ГИП), из них изготовляют режущие инструменты.
Такие стали марок Р6М5К5 МП, Р6М5Ф3 МП и др. в виде прутков диаметром до 150 мм и длиной до 500 мм отличаются мелкозернистой однородной структурой. Стойкость режущих инструментов из этих сталей в 1,5…3 раза выше, чем у сталей, полученных обычным металлургическим способом.
Дополнительное увеличение стойкости инструментов (до шести раз) достигают введением в состав порошковой быстрорежущей стали до 10% карбидов титана, ниобия или карбонитрида титана. Такие материалы называют карбидосталями.
В целях экономии вольфрама и, частично, молибдена в конце 1970-х и 1980-е гг. были разработаны быстрорежущие безвольфрамовые стали. Эти стали имеют такие химические составы, которые обеспечивают возможность упрочнения путем проведения закалки от высоких температур и отпуска аналогично вольфрамосодержащим сталям. Отпуск при повышенных температурах 580 С обеспечивает выделение дисперсных карбидов, что приводит к росту твердости («вторичная» твердость) (рис.105).Это стали марок 11М5Ф, 11М5ФЮ , 12МФ№СЮ, 95Х6М3Ф3Т и др.
Рис.105.Зависимость твердости закаленной стали 11М5Ф от температуры отпуска (закалка от температуры 1020 С): а – « вторичная» твердость.
Сравнительные характеристики некоторых быстрорежущих сталей даны в табл. 13.
Таблица 13
Марка стали | Твердость HRC | ![]() | t ![]() ![]() |
Р6М5 | 64…66 | 3150…3550 | 620 |
Порошковая: Р6К5 МП | 68…69 | 3000…3300 | 630 |
95Х6М3Ф3Т | 66 | 3100…3500 | 620 |
11М5ФЮ | 65…67 | 4000 | 630 |
Быстрорежущие стали относятся к сталям с карбидным упрочнением. Разработаны дисперсионно-твердеющие быстрорежущие стали с интерметаллидным упрочнением, например, Co W
.Это стали марок В14М7К25 (ЭП723), В11М7К23 (ЭП831) и др. В обозначении таких сталей впереди записывается заглавная буква «В» (вместо «Р») , а число показывает содержание вольфрама в процентах.
Абразивные материалы.
Абразивные материалы используются в виде порошков в связанном или свободном состоянии. Инструментами при обработке различных изделий машиностроения являются шлифовальные круги, ленты, бруски, притиры. Материалы для абразивной обработки должны обладать высокой твердостью и прочностью в сочетании с некоторой хрупкостью, а также физико-химической инертностью к обрабатываемому материалу.
В качестве абразивных материалов применяются тугоплавкие безкислородные химические соединения: карбиды и нитриды кремния, алюминия, бора. Используются также металлоподобные химические соединения ряда металлов с неметаллами: кремнием, углеродом, бором, азотом.
Различают естественные (наждак, корунд, гранит и др.) и искусственные (электрокорунд нормальный, карбид кремния зеленый, карбид бора и др.) абразивные материалы.
Абразивные порошкообразные материалы принято подразделять в зависимости от величины микротвердости на три группы (табл.14).
Таблица 14
Классификация абразивных материалов.
№ группы | Микротвердость абразивов, МПа | Примеры абразивных материалов |
1 | Менее 19600 | Крокус Кварц |
2 | От 19600 до 49000 | Наждак Электрокорунд Карбид кремния Карбид бора |
3 | Более 49000 | Кубический нитрид бора Вюрцитный нитрид бора Алмазы |
Материалы группы 3 выделяют в особый класс сверхтвердых материалов (см. ниже).
При изготовлении абразивных инструментов (шлифовальных кругов, брусков, притиров) твердые и хрупкие зерна абразивов размещают в более пластичных полимерных, керамических, металлических и иных связках – матрицах. Для шлифовальных кругов наибольшее применение получили керамическая (К), бакелетовая (Б) и вулканитовая (В) связки.
Керамическая связка состоит из огнеупорной глины, полевого шпата, кварца с добавками талька, мыла и жидкого стекла.
Основу бакелетовой связки составляет фенолоформальдегидная смола.
В состав вулканитовой связки входят каучук и 25…30% серы. При изготовлении кругов происходит вулканизация каучука.
Способность связки удерживать абразивные зерна на поверхности инструмента в процессе резания называется твердостью круга. Абразивные инструменты имеют ряд групп и подгрупп твердости, рассматриваемых в специальной литературе. Правильно выбранная твердость круга обес- печивает самозатачивание, т. е. обновление в процессе резания режущей способности круга за счет выкрашивания затупившихся абразивных зерен.
Сверхтвердые материалы.
К классу сверхтвердых материалов относят такие материалы, главным образом с ковалентными связями, у которых микротвердость выше, чем у природного корунда, то есть выше 19600 МПа. В зависимости от микротвердости они классифицируются на пять подклассов. ( табл.15).
Таблица 15
Классификация сверхтвердых материалов.
№ п/п | Наименование материала | Микротвердость HV, МПа |
1 | Природные алмазы | 98100 |
2 | Синтетические алмазы | 99290…98100 |
3 | Кубический нитрид бора BN ![]() | 68670…78480 |
4 | Вюрцитный (гексагональный) нитрид бора BN ![]() | 49050…78480 |
5 | Композиционные материалы | ≤49050 |
Алмазы характеризуются высокой твердостью, хорошей тепло- проводностью ( =137,9…146,3 Вт/(
К). С нагревом выше температур ~800…900
С алмазы начинают графитизироваться.
Синтетические алмазы получают из углеграфитовых материалов в специальных камерах высокого давления при р =5000…7000 МПа и температурах не ниже 1400…1500 К. Высокая температура достигается пропусканием электрического тока через нагревательное устройство.
Кубический нитрид бора КНБ имеет более низкую твердость по сравнению с алмазом и теплопроводность ( =41,86 Вт/ (
К). Он сохраняет свою структуру и твердость при нагреве до температуры ~1200…1400
С.
Композиционные сверхтвердые материалы в виде поликристаллов получают различными способами. Так, материалы типа баллас (АСБ) и карбонадо (АСПК) изготовляют пропиткой пористых прессовок, с формованных из алмазных порошков с металлическими покрытиями. По аналогичной технологии получают материалы эльбор - Р из кубического нитрида бора. Для изготовления лезвийного режущего инструмента, например резцов, разработаны композиционные материалы типа ПТНБ из смесей кубического и вюрцитного нитрида бора.
Алмазные порошки, выпускаемые промышленностью, классифи- цируются в зависимости от метода получения и размера зерен на следующие группы:
1.Алмазные шлифпорошки с размером зерен от 40…50 мкм до 630…800 мкм. Они выпускаются следующих основных марок: АС2, АС4, АС6, АС15, АС20, АС32, АС50. Чем выше число, тем больше прочность зерен алмазов.
Рекомендуются для инструментов на металлических, органических и керамических связках, используемых при разрезании и обработке стекла, керамики, камня, гранитов, горных пород, корунда и др.
2.Алмазные шлифпорошки с покрытиями поверхности зерен.
Применение покрытий повышает стойкость инструментов и снижает расход алмазов. В качестве стандартных используются следующие виды покрытий зерен:
покрытие типа К пленкой карбида металла;
покрытие типа КМ пленками сплавов, содержащих кремний;
покрытие типа НТ, являющееся карбидо-металлическим;
покрытие типа А, при котором совокупность агрегатов из нескольких алмазных зерен имеет карбидо - металлическую пленку;
покрытие типа АН – модификация покрытия А, отличающаяся введением в агрегаты из алмазных зерен дополнительно наполнителя (карбид бора, карбид титана, электрокорунд и др.).
3.Алмазные микропорошки с размером зерен от < 1,0 мкм до 40…60 мкм двух разновидностей:
марок АМ из природных алмазов и марок АСМ из синтетических алмазов;
марок АН из природных алмазов и марок АСН из синтетических алмазов.Они имеют более высокую абразивную способность (на 25…30%) по сравнению с микропорошками АМ и АСМ.
Микропорошки выпускаются зернистостью 60/40, 40/28, 28/20, 20/14, 14/10, 10/7 и др. до 1/0 мкм. В обозначении марок числитель показывает максимальный, а знаменатель минимальный размеры основной фракции порошка в микрометрах.
Микропорошки применяются для изготовления абразивных инстру- ментов, а также использования в свободном незакрепленном состоянии в пастах и суспензиях.
Микропорошки АМ и АСМ используют при доводочных работах изделий из закаленных сталей, стекла, керамики и др. Для обработки изделий из более твердых материалов (корунда, керамики, природных алмазов и других труднообрабатываемых материалов) рекомендуются микропорошки АН и АСН.
Твердые порошковые сплавы состоят из карбидов вольфрама, титана и тантала (WC, TiC, TaC) с небольшими добавками кобальта. Карбиды очень тугоплавки и имеют большую твердость. В отличие от сталей твердые сплавы имеют более высокую теплостойкость (твердость сохраняется при нагреве до 1000 С). Благодаря хорошей теплостойкости скорость резания инструментами, оснащенными твердым сплавом, в 5…10 раз выше, чем у быстрорежущей стали.
Твердые порошковые сплавы изготовляются методами порошковой металлургии, т. е. путем прессования смеси порошков карбида и кобальта с последующим спеканием при температуре 1400…1450 С. В Российской Федерации производятся твердые сплавы трех групп:
1.Вольфрамовые марок ВК2, ВК3М, ВК6, ВК8, ВК20, ВК30 с разным содержанием кобальта (в сплаве ВК2 – 2% Со и т.д.) для обработки хрупких материалов (чугун, стекло и др.).
2.Титановольфрамовые Т30К4, Т15К6, Т14К8, Т5К10, Т5К12В с разным содержанием кобальта и карбидов титана (например, в сплаве Т15К6-15%TiC, 6%Со, WC – ост.) для обработки вязких материалов (сталей и др.).
3.Титанотанталовольфрамовые ТТ7К12 (4%TiС, 3%ТаС, 12%Со – ост.) для тяжелого чернового точения стальных поковок, штамповок, отливок.
В соответствии с международной классификацией ИСО твердые порошковые инструментальные сплавы для обработки резанием разделяются на три группы:
Р – при обработке дают «сливную» стружку ( например, Т15К6);
К – при обработке дают дробленую стружку (например, ВК6);
М – универсальные для обработки сталей и чугунов (например, ТТ8К6, ВК6-ОМ).
Эти группы разделяют на подгруппы для конкретных условий резания, которые дополнительно обозначают двухзначным числом, например, Р01 – чистовая обработка точением и сверление; Р25 – фрезерование.
Для улучшения эксплутационных свойств режущих пластин твердых сплавов на их поверхность наносят износостойкие покрытия из TiC, TiN, Ti(C,N). Покрытия толщиной пять – десять микрометров наносят из газовой фазы при температуре 1000…1300 С. Применяют также многослойные покрытия из последовательности слоев TiN и TiC, ZrB
.
Средний размер зерен карбидов в твердых сплавах равен 1…2 мкм, микротвердость составляет 12800 МПа (ВК6), 17700 МПа (Т15 К6).
Твердые безвольфрамовые сплавы созданы на основе карбида титана и карбонитрида титана. На основе TiC разработаны сплавы марок ТН20, ТН30 и др. В качестве связки используются никелемолибденовые сплавы. Так сплав ТН20 содержит 79% TiC, 15%Ni, 6% Мо.
Твердый сплав марки КНТ16 на основе карбонитрида титана имеет 90%Ti (C,N) и 10% связки (Ni-Мо) (3:1). Микротвердость материала равна 12200 МПа.
Такие безвольфрамовые твердые сплавы по своим свойствам при чистовом и получистовом точении с малой глубиной резания на токарных станках близки к вольфрамосодержащим твердым сплавам.
Режущая керамика (РК). Она характеризуется высокой твердостью, в том числе при нагреве, износостойкостью, химической инертностью к большинству металлов в процессе резания. По комплексу этих свойств керамика превосходит традиционные режущие материалы – быстрорежущие стали и твердые сплавы.
Различают нитридную и оксидную керамику. Современная РК являет- ся композиционным материалом с матрицей из Si N
(t
≤1200
С) или Al
О
(1500
С). Наполнителем служат мелкие частицы TiN, TiC, ZrO
.
РК изготовляется в виде небольших пластин, на поверхность которых наносят два и более слоев покрытий Al O
, TiC, TiN, TiCN. Используют также «градиентные» покрытия, состав которых постепенно изменяется от керамики к рабочей поверхности. Покрытия имеют своей целью «залечивание» дефектов поверхностного слоя керамического материала.
Оксидная режущая керамика Al O
, Al
O
+ZrO
, Al
O
+TiN, используется для черновой и чистовой токарной обработки деталей из сталей, реже чугунов.
Керамика Al O
+ZrO
(«белая» керамика) имеет следующие свойства:
HV =22000МПа; =650 МПа; Е= 340000МПа; вязкость разрушения К
=5,3 МПа
.
Нитридная режущая керамика Si N
,Si
N
+ZrO
,Si
N
+TiN приме- няется для чернового и чистового точения, фрезерования чугунов и суперсплавов.
Керамика Si N
имеет следующие свойства:
HV=18000 МПа; =720 МПа; Е=300000 МПа; вязкость разрушения К
=7,0 МПа
.
Режущая керамика по своим свойствам занимает промежуточное положение между твердыми сплавами и сверхтвердыми материалами (алмазами).
ГЛАВА 5
ЦВЕТНЫЕ МЕТАЛЛЫ И СПЛАВЫ
Многообразные металлические материалы в материаловедении принято подразделять на черные (основа – железо) и цветные (все остальные). Цветные металлы и сплавы классифицируются на следующие виды:
легкоплавкие с невысокой температурой плавления (Zn, Sn, Sb, Pb, Bi и др.);
легкие с пониженной плотностью (Be, Mg, Al, Ti и др.);
тугоплавкие с высокой температурой плавления (Nb, Ta, Mo,W и др.);
благородные (Au, Ag, Pt, Pd, Cu и др.);
редкоземельные (Ce, Nd, Y и др.);
урановые (U, Th, Pu и др.).
В промышленности в качестве основы для конструкционных мате- риалов используют алюминий, титан, медь, магний. Сплавы олова и свинца применяют для изготовления антифрикционных легкоплавких материалов.
Ниже рассмотрены основные цветные металлы и сплавы машино- строительного назначения.
Алюминий и его сплавы
Алюминий является одним из важнейших промышленных металлов. Характерными свойствами алюминия являются малая плотность (2,7 г/см ), большая пластичность, хорошая электропроводность и коррозионная стойкость. Ввиду малой плотности алюминий является основой легких конструкционных материалов; большая пластичность позволяет применять к алюминию различные виды обработки давлением. Электропроводность чистого алюминия составляет 65% от электропроводности меди и поэтому алюминий широко применяется в электротехнике в качестве материала для проводников электрического тока. Высокая химическая стойкость алюминия объясняется образованием на поверхности алюминия тонкой и прочной пленки. Ввиду малой прочности (
=800 МПа) алюминий, как конструкционный материал, применяется в машиностроении ограниченно и используются алюминиевые сплавы.
Промышленные сплавы алюминия по способу получения изделий делятся на две основные группы: деформируемые, предназначенные для изготовления изделий различными методами обработки давлением, и литейные для производства фасонных отливок. Большинство элементов имеет ограниченную растворимость в алюминии и границей между деформируемыми и литейными сплавами является предел растворимости данного элемента в алюминии. В качестве деформируемых применяются сплавы со структурой твердого раствора, имеющие хорошую пластичность. Литейные сплавы, как правило, содержат в структуре существенное количество эвтектики, что обеспечивает хорошие литейные свойства (жидкотекучесть, хорошая заполняемость литейных форм, образование плотных отливок при кристаллизации).
Деформируемые сплавы
Деформируемые сплавы алюминия являются основными конструкци- онными материалами, широко применяющимися в авиастроении и различ- ных областях машиностроения. Основные виды полуфабрикатов, обрабаты- ваемых давлением: листы и ленты, прессованные профили и прутки, трубы, проволока и заклепки, поковки и штампованные фасонные детали.Все дефор- мируемые сплавы делятся на две группы: 1-сплавы, не упрочняемые термической обработкой, 2-сплавы, упрочняемые термической обработкой.
Сплавы, не упрочняемые термической обработкой. К этой группе относятся сплавы алюминия с 1,0…1,6% марганца и с 2,0…6,8% магния. Структура сплавов Al – Mn состоит из твердого раствора и небольшого количества частиц соединения MnAl , а структура сплавов Al – Mg – из одного твердого раствора. В отожженном состоянии такие сплавы имеют высокую пластичность и сравнительно небольшую прочность. Дополнительное упрочнение сплавов и повышение твердости достигается холодной деформацией. Эти сплавы применяются для изделий, которые должны обладать высокой пластичностью, способностью к глубокой вытяжке, хорошей свариваемостью и высоким сопротивлением коррозии (баки, трубопроводы бензина и масла).
Сплавы, упрочняемые термической обработкой. Сплавы этой группы являются двухфазными. Все они упрочняются путем термической обработки – закалки и старения. Возможность термической обработки обусловлена наличием переменной растворимости соединений CuAl , Mg
Si, Al
CuMg (фаза S) и др. в алюминии.
Рассмотрим термическую обработку алюминиевых сплавов на примере сплавов алюминия с медью. Из диаграммы состояния алюминий – медь (рис.112) видно, что медь ограниченно растворяется в алюминии и образует с ним твердый раствор замещения . Максимальная растворимость меди в алюминии составляет 5,6% при 548
С; с понижением температуры растворимость меди в алюминии уменьшается и при комнатной температуре составляет 0,5%. Вследствие уменьшения растворимости из
- раствора выделяются кристаллы CuAl
. Закалка сплавов проводится путем нагрева в
![]() | область ![]() ![]() ![]() ![]() ![]() |
новесным состоянием перенасыщен медью и является термодинамически неустойчивым.
При последующем вылеживании закаленного сплава при комнатной температуре в течение 4…5 суток (естественное старение) происходит диффузия атомов меди и образование в решетке - раствора особых зон пластинчатой формы толщиной в несколько атомных слоев, обогащенных медью. Эти зоны получили название зон Гинье – Престона. Схема строения твердого раствора после закалки (а) и естественного старения (б) (по М.Е. Блантеру) приведена на рис.113.
При нагреве закаленного сплава (искусственное старение) до 100…150 С подвижность атомов увеличивается и в объемах, обогащенных
![]() ![]() ![]() | медью, образуются тонкоплас- тинчатые кристаллы промежу- точной фазы ![]() ![]() ![]() ![]() |
туре происходит укрупнение, коагуляция уже выделившихся мелких кристаллов. При этом твердость и прочность сплава снижаются. Изменение прочности дюралюминия при старении показано на рис. 114.
![]() | Повышение механических свойств при термической обра- ботке сплава объясняется следу- ющим образом. В закаленном сплаве структура представляет собой твердый раствор отдель- ных атомов меди в решетке алюминия. Наличие атомов ме- ди приводит к увеличению сил межатомной связи и некоторому искажению кристаллической ре- шетки; при этом несколько по- |
вышается сопротивление движению дислокаций через твердый раствор и сплав упрочняется.
Дальнейшее повышение прочности происходит при старении. В процессе старения в зависимости от теплового режима образуются зоны Гинье – Престона, обогащенные медью, или дисперсные включения фаз. Около включений новых фаз и, особенно, зон Гинье – Престона кристаллическая решетка твердого раствора сильно искажается вследствие различий диаметров атомов меди и алюминия и движение дислокаций затрудняется. В этом случае дислокации не могут проходить через сами зоны Гинье – Престона и включения, а перемещаются между ними через твердый раствор с искаженной кристаллической решеткой.
Чем мельче включения и меньше расстояния между ними, тем больше сопротивление движению дислокаций и, соответственно, в большей степени сплав упрочняется. Максимальная прочность достигается в случае образования зон Гинье – Престона. По мере образования включений фаз и CuAl
и роста этих включений расстояние между ними увеличивается, степень искажения кристаллической решетки твердого раствора уменьшается. Это приводит к снижению сопротивления движению дислокаций и разупрочнению сплава.
Таким образом, увеличение прочности при старении объясняется большим сопротивлением движению дислокаций, которое оказывает группировки атомов меди (зоны Гинье – Престона) и частицы фазы по сравнению с отдельными атомами меди в пересыщенном твердом растворе
.
К алюминиевым сплавам, упрочняемым термической обработкой, относятся дуралюмины и некоторые другие сплавы. Основой дуралюминов является система алюминий – медь – магний. В зависимости от химического состава дуралюмины выпускаются разных марок: 1110(Д1), 1160 (Д16) и др. В скобках указано старое буквенное обозначение дуралюминов. Дуралюмины обладают малой коррозионной стойкостью и для повышения стойкости против коррозии листовые полуфабрикаты покрывают с обеих сторон тонким слоем чистого алюминия (плакирование). Небольшие добавки марганца вводятся в дуралюмин для повышения коррозионной стойкости и измельчения структуры. Марганец также значительно упрочняет полуфабрикаты из дуралюмина, изготовляемые способом горячего прессования на прессах, т.е. выдавливанием металла из замкнутой полости сквозь отверстие в матрице. Упрочняющее действие марганца объясняется тем, что марганец затрудняет процессы рекристаллизации металла при нагреве и способствует сохранению текстуры деформации.
Для ковки и штамповки применяются сплавы системы алюминий – магний – кремний – медь марок АК7ч, АК9ч и др. Из этих сплавов отливают крупные слитки – заготовки и из них изготовляют поковки и штамповки сложных форм и больших габаритов (до 1,0…1,5 тонн). Высокопрочные сплавы марки 1950(В95) и др. созданы на основе системы алюминий – цинк – магний – медь и обладают наибольшей прочностью ( до 490…540 МПа,
=7…12%) среди деформируемых сплавов алюминия. Из этих сплавов изготовляют крупные поковки, прессованные профили и прутки, листы, проволоку.
Один из таких сплавов марки 1933 с дополнительным введением циркония поставляется в виде поковок и штамповок, в том числе толщиной 200 мм и более. Сплав 1933 применяется для производства силовых деталей фюзеляжей самолетов. Начиная с 2002 года этот сплав используется в производстве серийных европейских аэробусов, в том числе модели А-340 на 380 человек. Он применен и при изготовлении аэробуса А-380, впервые начавшего полеты в 2006 году.
В авиационной и космической технике получили применение сплавы с литием, например, сплавы алюминий – медь – литий марки 1450 и алюминий – магний – литий марки 1420. Добавки лития позволяют уменьшить массу материала, повышают модуль упругости.
Литейные сплавы
Литейные сплавы предназначены для производства фасонных отливок путем литья в землю, кокиль и под давлением. Эти сплавы должны обладать хорошими литейными свойствами (жидкотекучесть, образование плотных отливок, стойкость против усадочных трещин). В качестве литейных сплавов алюминия применяются сплавы алюминий – кремний (силумины), алюминий – медь и алюминий – магний.
Силумины. Сплавы алюминия с 4…13% кремния марки АК12 и др. являются широко распространенными литейными сплавами. Диаграмма, состояния алюминий – кремний приведена на рис.115. Система алюминий – кремний относится к случаю почти полной нерастворимости компонентов в твердом состоянии с образованием эвтектики (смеси 88% - твердого раствора кремния в алюминии и 12% кремния) при 577
С.
Микроструктура силуминов состоит из грубоигольчатой эвтектики и кристаллов - твердого раствора на основе алюминия; механические свойст-
![]() | ва силумина невысокие ( ![]() ![]() |
рование сопровождается переохлаждением сплава, и сплавы заэвтек- тического состава становятся по структуре доэвтектическими. Измельчение кремния объясняется тем, что натрий образует на поверхности кристаллов пленки и таким образом затрудняет рост кристаллов.
Силумины хорошо свариваются и вследствие малой усадки почти не дают трещин от усадочных напряжений. Недостатком силуминов является
Рис.116. Схема микроструктуры немодифицированного (а) и модифицированного (б) силумина.
большая склонность их к образованию окисных пленок и к поглощению газов, поэтому в случае литья в землю и кокиль сплав отличается повышенной пористостью.
Для повышения механических свойств силумины легируют магнием и медью. В этих легированных силуминах образуются соединения Mg Si, CuAl
, растворимость которых в алюминии уменьшается с понижением температуры. Поэтому отливки из легированных силуминов могут подвергаться термической обработке: закалке с 520…530
С и старению при 150…180
С с выдержкой 10…30 часов. Легированные силумины с добавками 0,2…0,4% магния обладают хорошими литейными и высокими механическими свойствами(
=196…245 МПа,
=2…5%). С увеличением содержания магния в сплаве повышается газонасыщенность и в отливках образуются поры. Борьба с пористостью производится путем кристаллизации под давлением. Эти силумины применяются для отливки крупных нагруженных деталей двигателей (блоки цилиндров, картеры и др.). Легированный силумин с добавками 2…3% меди обладает высокими литейными свойствами и применяется для отливок сложной конфигурации (арматура двигателей и др.).
Сплавы алюминия с магнием являются наиболее прочными среди литейных сплавов алюминия ( =350 МПа) и имеют высокую коррозионную стойкость. По своим литейным свойствам они значительно уступают силуминам вследствие отсутствия эвтектики и имеют малую жидкотекучесть. Сплавы алюминия с магнием сильно окисляются и в отливках часто образуются включения окислов, снижающие прочность. Для уменьшения окисления при плавке и литье плавка ведется под слоем флюса и в сплавы добавляется небольшое количество бериллия. Эти сплавы применяются для отливки ответственных деталей и узлов самолета.
Титан и его сплавы
Современная техника, особенно высокоскоростная авиация и ракетостроение, нуждается в прочных и легких материалах. Основой таких новых конструкционных материалов, сочетающих высокую прочность с относительно малой плотностью и высокой коррозионной стойкостью, послужил титан. Промышленное производство металлического ковкого титана было начато в 1948 г. способом восстановления четыреххлористого титана магнием: 2Mg + TiCl
2MgCl
+Ti. Процесс ведется в атмосфере защитного нейтрального газа – аргона. При повышенных температурах титан активно соединяется с кислородом, азотом и углеродом и становится хрупким, поэтому проведение процесса на воздухе невозможно. В результате восстановления получают порошкообразный титан в виде губки. Для получения компактного титана титановая губка переплавляется в электродуговых печах в атмосфере аргона или в вакууме. После переплавки титан достаточно пластичен и может быть подвергнут обработке давлением в холодном и горячем состояниях (ковке, прокатке, вытяжке и т.д.). Из титана получают листы, прутки, профили, проволоку и др.
Технический титан содержит до 0,2% кислорода, до 0,1% азота, небольшие примеси других элементов и имеет прочность =440…550 МПа и
=25% (титан марки ВТ1-0). Титан высокой чистоты имеет умеренную прочность (
= 245…284 МПа) и высокую пластичность (
=56…64%). В обычной атмосфере титан стоек по отношению к окислению до температур 400..500
С. Следует подчеркнуть высокую коррозионную стойкость титана к действию ряда кислот и морской воды. Плотность титана 4,505 г/см
. Титан существует в двух аллотропических формах: Ti
с гексагональной решеткой (до 882
С) и Ti
с объемноцентрированной кубической решеткой (882… 1660
С).
Сплавы титана. В зависимости от структуры различают три группы сплавов:
1. Сплавы со структурой твердого раствора на основе Ti
.
2. Сплавы со структурой твердого раствора на основе Ti
.
3.Сплавы со структурой +
.
Структуру твердого раствора получают при добавках к титану алюминия, ванадия и др. элементов. Такие сплавы имеют высокую пластичность и хорошо обрабатываются давлением. Они получили широкое применение для изготовления листов, профилей, труб и выдерживают температуры нагрева до 350…400
С. Сплавы со структурой
- раствора используются для летательных аппаратов при сверхзвуковых скоростях полета (обшивка, силовые детали).
Большинство примышленных сплавов титана относится к сплавам со структурой +
и содержит около 3…9% легирующих элементов (марганец, молибден, ванадий и др.). Эти сплавы используются для изготовления поковок, прутков. Упрочнение сплавов производится путем термической обработки – закалки и старения. Рассмотрим термическую обработку на примере сплавов титана с марганцем. Диаграмма состояния титан – марганец приведена на рис.116. Система титан – марганец относится к случаю ограниченной растворимости с наличием эвтектоидного превращения при 550
С
(интерметаллическое соединение). Эвтектоидное превраще- ние протекает чрезвычайно медленно и в случае охлаждения вместе с печью не происходит.
![]() | Закалка титановых сплавов с содержанием более 4% Mn производится путем нагрева в область ![]() ![]() ![]() ![]() ![]() ![]() |
При последующем старении (нагрев до температур ниже области ) из твердого раствора
выделяются мелкодисперсные включения
- раствора, упрочняющие сплав (
). Если старение производится при низких температурах, то при распаде
- раствора вначале выделяется промежуточная хрупкая фаза
и сплав становится хрупким. В этом случае образование
- раствора происходит лишь при длительных выдержках:
Во избежание хрупкости старение проводится при повышенных темпе-
![]() | ратурах и длительных мно- гочасовых выдержках. Схема термической обработки тита- новых сплавов приведена на рис. 117.
Сплавы со структурой твердого раствора ![]() |
Медь и ее сплавы
Медь отличается высокой электропроводностью и теплопроводностью, достаточно высокой коррозионной стойкостью и хорошей пластичностью в горячем и холодном состоянии. Благодаря высокой электропроводности медь в виде проволоки, полос, ленты широко применяется в электротехнике для изготовления проводников тока. Трубы из меди применяются в теплотехнике и холодильных установках. Ввиду невысокой прочности медь ограниченно применяется в качестве конструкционного материала, и используются сплавы меди с цинком, алюминием, оловом и другими элементами.
Большое влияние на свойства меди оказывают примеси. Особо вредными примесями являются висмут и свинец. Эти элементы в меди почти не растворяются и образуют с медью легкоплавкие эвтектики с температурой плавления 270 и 326 С. Во время горячей прокатки эти эвтектики расплавляются, разъединяют кристаллы и приводят к разрушению меди (горячеломкость). В высших сортах меди допускается не более 0,002% висмута и 0,005% свинца.
Хрупкость меди придает сера, находящаяся в виде химического соединения Cu S. Это соединение образует с медью хрупкую эвтектику Cu +Cu
S. Кислород в виде Cu
O также образует хрупкую эвтектику Cu+ Cu
O. Кислород является причиной образования « водородной болезни» меди. При нагреве меди в восстановительной атмосфере водород проникает в медь, взаимодействует с кислородом и образует водяные пары. Пары воды в меди не растворяются и стремятся выделиться из нее, приводя к образованию микротрещин.
Дата добавления: 2018-04-05; просмотров: 1966; Мы поможем в написании вашей работы! |
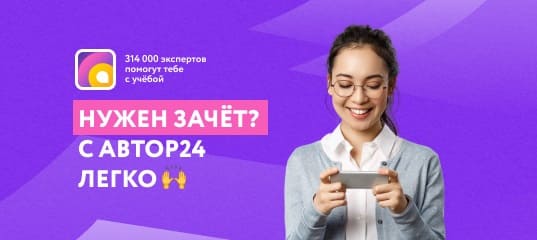
Мы поможем в написании ваших работ!