Описание служебного назначения и особенности конструкцииизделия
Содержание
ВВЕДЕНИЕ. 7
1. ОБЩИЕ ВОПРОСЫ ПРОЕКТА. 9
1.2. Описание служебного назначения и особенности конструкции изделия. 10
1.3. Краткая характеристика существующего технологического процесса. 14
1.4. Определение типа производства, его характеристика и расчет такта выпуска. 16
2. ТЕХНОЛОГИЧЕСКАЯ ЧАСТЬ. 17
2.2. Анализ технических условий, предъявляемых к изделию. 19
2.3. Обоснование метода получения заготовки и описание технических условий на нее. 20
2.4. Технологический анализ материала изделия. 22
2.5. Выбор и обоснование технологических баз. Разработка теоретических схем базирования. 25
2.6 Разработанный технологический процесс обработки с указанием применяемого оборудования. 34
2.7. Расчет режимов резания. 36
2.8. РАСЧЕТ ПРИПУСКОВ. 43
3. РАСЧЕТ УЧАСТКА. 48
3.2 Система обеспечения участка инструментом. 49
3.3. Система удаления отходов. 50
4.ПРИМЕНЕНИЕ СКОРОСТНОГО ШЛИФОВАНИЯ. 51
4.2. Скоростное шлифование. 53
4.3. Шлифовальные станки для скоростного шлифования. 54
4.4. Абразивный инструмент применяемый для высокопроизводительных методов шлифования. 56
4.5. Анализ методов шлифования, влияющих на точность обработки. 61
4.6. Качество поверхностного слоя после шлифования. 62
4.7 Влияние режимов и методов правки на качество шлифования. 65
4.8. Правка шлифовального круга с помощью профильно-вращательного приспособления. 69
4.9. Влияние смазочно-охлаждающей жидкости (СОЖ) на качество шлифования деталей. 71
|
|
4.10. Заключение. 74
5. Автоматизирующие устройства. 76
5.2. Прибор активного контроля для определения износа центровых сверл. 78
6.Специальные средства технологического оснащения. 79
6.2. Описание конструкции и условия работы контрольного приспособления. 87
7.ОРГАНИЗАЦИОННО-ЭКОНОМИЧЕСКАЯ ЧАСТЬ. 88
7.1. Общие положения. 89
7.2. Система управления цеха. 91
7.3. Исходная информация. 93
7.4. ЭКОНОМИЧЕСКАЯ ЧАСТЬ. 94
7.4.1 Определение такта выпуска. 96
7.4.2 Расчет потребного количества станков для механической обработки по операциям. 97
7.4.3 Экономическое обоснование эффективности совершенствования процесса шлифования. 99
7.4.4. Определение суммы капитальных вложений. 102
7.4.5. Расчет заработной платы основных рабочих. 103
7.4.6. Стоимость силовой эл. энергии. 105
7.4.7. Затраты на амортизацию оборудования. 106
7.4.8. Затраты на эксплуатацию производственных площадей. 107
7.4.9. Затраты на текущий ремонт оборудования, на его содержание и обслуживание. 108
7.4.10. Затраты на содержание и ремонт оборудования. 111
7.4.11 Определение экономической эффективности проектного технологического процесса. 112
7.4.12 Метод ремонта «против потока». 114
8. БЕЗОПАСНОСТЬ ЖИЗНЕДЕЯТЕЛЬНОСТИ И ОХРАНА ОКРУЖАЮЩЕЙ СРЕДЫ. 115
|
|
8.1.2. Разработка мероприятий, направленных на улучшение условий труда 117
8.1.2. Анализ технологического процесса по вредным факторам для окружающей среды. 120
8.1.3. ТРЕБОВАНИЯ БЕЗОПАСНОСТИ ПРИ РАБОТЕ НА МЕТАЛЛООБРАБАТЫВАЮЩИХ СТАНКАХ. 123
8.1.4. Мероприятия по обеспечению требуемого состояния пожарной безопасности. 128
8.1.5. ВЫВОДЫ. 130
8.2. ОХРАНА ОКРУЖАЮЩЕЙ СРЕДЫ. 131
8.2.1. Актуальные проблемы охраны окружающей среды, и оценка экологичности технологического процесса изготовления детали. 132
8.2.2. Очистка промышленных выбросов в атмосферу от пыли. 133
8.2.3. Выводы. 135
Выводы по проекту. 136
Список использованной литературы.. 138
ВВЕДЕНИЕ.
Машиностроение является базовой отраслью народного хозяйства и в ней сосредоточен большой научно-технический и производственный потенциал. Для нее создается благоприятная обстановка для воплощения на практике мероприятий, способных каким-либо образом повышать объем и качество выпускаемой продукции.
Основными способами повышения производительности в машиностроении являются наиболее широкое использование новейших разработок в области технологии, автоматизации и механизации производственных процессов.
Правильное решение выбора технологического процесса и учет достижений научной и технической мысли решает вопрос о продолжительности производственного цикла и точности выпускаемой продукции.
|
|
В своем дипломном проекте я постараюсь на базе существующего метода изготовления на автомобильном заводе поворотного кулака автомобиля получить усовершенствованный технологический процесс, который позволит значительно сократить трудоемкость изготовления и себестоимость продукции и принесет значительный экономический эффект.
Дипломное проектирование является завершающим этапом обучения. Цель дипломного проектирования - закрепление теоретических знаний по общемеханическим и специальным дисциплинам, развитие и закрепление навыков самостоятельной инженерной работы.
Данный дипломный проект направлен главным образом на разработки технологического процесса изготовления поворотного кулака левого автомобиля и средств технологического оснащения, обеспечивающих повышение производительности труда, качество продукции, снижение себестоимости и материалоемкости, а также улучшения условий труда. Поворотный кулак является одной из специфичных деталей, соединяющих в себе требования, предъявляемые к технологии обработки валов (цапф) с одной стороны, и рычагов (фланцевая часть) - с другой. Поэтому данная деталь требует особого отношения и при производстве должны быть учтены все требования, заложенные конструкторами в чертеже.
|
|
Кроме того, деталь все время в процессе эксплуатации подвержена воздействиям ударных нагрузок, что в свою очередь, определяет выбор материала и метод получения первичной заготовки.
Для повышения производительности труда в проекте предлагается применение скоростного шлифования на операциях окончательной обработки.
Качество и точность преобладающего большинства деталей машиностроения обеспечивается на всех операциях технологических процессов. В автомобильной промышленности более 30 % общей суммы трудоемкости изготовления деталей приходится на долю шлифовально-доводочных операций. Однако проведенные исследования и анализ действующего производства показали, что существующие процессы шлифования обладают низкой производительностью.
Поэтому внедрение прогрессивных методов шлифования является актуальной задачей развития научно-технического прогресса на сегодняшний день.
ОБЩИЕВОПРОСЫПРОЕКТА.
1.1 Исходная информация для разработки дипломного проекта.
Программа выпуска деталей: 200 000 штук в год (с учетом запасных частей).
Чертежи детали и заготовки поворотного кулака правого (левого) переднего управляемого моста автомобиля.
Заводской технологический процесс получения заготовки поворотного кулака.
Заводской технологический процесс механической обработки поворотного кулака.
Описание служебного назначения и особенности конструкцииизделия.
Получившие наибольшее распространение на грузовых автомобилях управляемые неразрезные ведомые мосты состоят из балки 10, шкворней, поворотных кулаков с цапфами 14, шкворневых втулок, упорных подшипников 4, 5, рычагов рулевых тяг и, продольной и поперечной рулевых тяг, опорных дисков тормозов (рисунок 1.1).
Поворотные кулаки, шкворни и ступицы колес передних мостов автомобилей являются одними из наиболее ответственных деталей, к прочности и долговечности которых предъявляют повышенные требования.
На фланце поворотного кулака устанавливают опорный диск, который крепят болтами или заклепками, а на их цапфовой части подшипники и ступицы колес. К ступицам колес прикрепляют тормозные барабаны и диски колес. К нижней части поворотного кулака крепят боковые рычаги трапеции, шарнирно соединенные с поперечной рулевой тягой, а к верхней части поворотного кулака - рычаг, шарнирно связанный с продольной рулевой тягой. С поворотными кулаками рычаги связаны конусными и шпоночными соединениями.
Поворотный кулак (рисунок 1.2) состоит из цапфы 1, фланца 2, верхней и нижней шкворневых проушин 3, в которых имеется отверстие А, для крепления боковых рычагов трапеций и рулевой тяги.
Конструктивное исполнение фланцев - прямоугольное, с четырьмя резьбовыми отверстиями для крепления опорных дисков тормозов.
Верхняя и нижняя части фланца поворотного кулака переходят в шкворневые проушины с цилиндрической поверхностью, расположенные под углом к плоскости фланца, что обеспечивает необходимый наклон шкворня. Радиусы закруглений в месте перехода от фланца к шкворневым проушинам обеспечивают устранение зон с различными изменениями напряжений.
Поворотные кулаки изготавливаются из легированной конструкционной
хромистой среднеуглеродистой стали 40Х на горизонтально-ковочных машинах
Рисунок. 1.1 - Передняя ось автомобиля:
1—ступица; 2—крышка; 3 — винт; 4 и 5 — подшипники ступицы; 6 — манжета; 7 — диск переднего тормоза; 8 и 13 — болты; 9 — регулировочный упор поворотного кулака; 10 — балка передней оси; 11—грязезащитный щит; 12 — обойма манжеты; 14 — поворотный кулак; 15 — регулировочная гайка подшипника; 16 — упорная шайба
Рисунок 1.2 – поворотный кулак
(ГКМ), что позволяет получить заготовку с минимальными припусками на механическую обработку, требуемой точностью и шероховатостью. В этом случае обеспечивается также волокнистая структура материала поворотного кулака, что обуславливает его высокое сопротивление усталости и оптимальные физико-механические свойства. Поковку подвергают термообработке (нормализация) и затем обрабатывают на автоматической линии.
Основные усталостные напряжения и разрушения поворотного кулака (около 70%) происходят в зоне галтели на участке перехода от цапфы к фланцу. Повышают предел выносливости этого сопряжения при помощи конструктивно и технологически различных мероприятий, таких, как накатка, повышающая предел выносливости на 50%, а долговечность - в 4,3 раза при сохранении тех же размеров.
Технологичность конструкции.
Данное изделие относится к классу поворотных кулаков. Оно принадлежит к конструктивно сложным деталям, т.к. состоит из цилиндрической части - называемой цапфа - медленно переходящей через галтель в «прямоугольную» часть - называемую фланцем, которая имеет сложную конструкцию, переходящую в шкворневые проушины, расположенные под углом к плоскости фланца.
Сложность при изготовлении заключается в том, что необходимо получение специальной поковки на горизонтально-ковочных машинах, которые позволяют получить заготовку нужной формы с минимальными припусками на механическую обработку, требуемой точностью и шероховатостью, а также получение оптимальных физико-механических свойств с последующей термообработкой и упрочнением поверхностного слоя дробью.
При механической обработке получение очень точных размеров, расположения поверхностей, изготовление поверхностей сложной формы, сверлении несквозных отверстий, фрезерование специальных площадок под крепление.
Изготовление специальных рабочих приспособлений, специальных контрольно-измерительных приспособлений. Создание специальной автоматической линии.
Дата добавления: 2018-04-04; просмотров: 350; Мы поможем в написании вашей работы! |
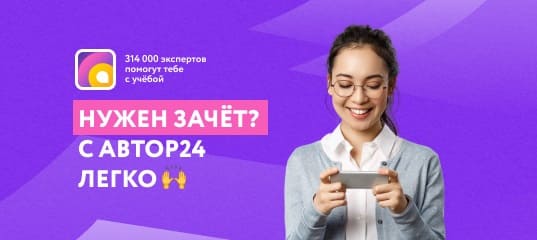
Мы поможем в написании ваших работ!