МЕРЫ КОНТРОЛЯ КАЧЕСТВА САРНЫХ СОЕДИНЕНИЙ
Nbsp; ОБЩИЕ СВЕДЕНИЯ В зависимости от требований к сварным соединениям и категории их ответственности устанавливается определенная система организации контроля качества продукции на предприятии. В основу этой системы положена классификация видов технического контроля по отдельным признакам. 1. По стадиям технологического процесса контроль разделяют на: входной (предварительный); операционный (текущий); окончательный (готовой продукции). К входному контролю предъявляют основной и сварочный материалы (присадочную проволоку, флюсы, газы, электроды), полуфабрикаты и комплектующие. Под термином предварительный контроль понимают не только проверку материала, но и работоспособности сварочного оборудования и квалификации исполнителей работ. Операционному контролю подвергают технологические процессы по отдельным операциям маршрутной технологии после её завершения или во время исполнения. 2. По объему контролируемой продукции: сплошной; выборочный. Сплошной контроль выполняют для ответственных сварных конструкций. Выборочный – при контроле изделий крупносерийного и массового производства. 3. По месту проведения контроля: стационарный; подвижный (скользящий). Стационарный контроль производится на специальном оборудованном контрольном пункте или в специальном помещении (например, рентгеноконтроль выполняют в изолированных боксах). Подвижный контроль производится непосредственно на рабочем месте (например, ультразвуковой контроль). 4. По характеру контроля: инспекционный; летучий. Под инспекционным контролем понимают выборочный контроль продукции специальными лицами (инспекторами) для дополнительной проверки качества проконтролированной продукции. Летучий контроль выполняется с произвольной периодичностью, носит инспекционный характер и выполняется работниками ОТК. При этом контролируется соблюдение технологических процессов (контроль технологической дисциплины), например, последовательность выполнения швов, соблюдение правил хранения и условий транспортировки изделий на соответствие требованиям технической документации. При проверке соблюдения технологического процесса особое внимание уделяется рациональной организации рабочих мест, которая предполагает наличие необходимой технологической документации, оснастки и контрольно-измерительных приборов и инструмента и их состояния, соблюдения правил и норм техники безопасности, состояние рабочего места и соответствие его требованиям технологической документации. Такую проверку часто называют контролем производственной дисциплины. 5. По цели контроля: приемочный; статистический. Приемочный контроль проводится с целью отделения годной продукции от брака. Статистический контроль используется в крупносерийном и массовом производстве в системе управления качеством продукции. Статистический контроль является средством профилактического воздействия на ход технологического процесса с целью его корректировки и исключения появления брака. 6. По возможности использования проконтролированной продукции: разрушающий [1] и неразрушающий. Разрушающий контроль применяют для получения контролируемых количественных показателей продукции. В некоторых случаях контроль проводят с частичным нарушением целостности материала изделия, т.е. путем испытаний без разрушения изделия. Неразрушающий контроль не оказывает влияния на целостность продукции и косвенно характеризует ее качество. 7. По средствам контроля и получения информации: визуальный; инструментальный. Визуальному контролю подвергают 100% изделий. Инструментальный контроль является более совершенным, т.к. осуществляется с помощью разнообразных технических средств контроля. Технические средства контроля можно разделить на следующие группы. 1. По характеру измерения контролируемого параметра: контрольно-измерительные инструменты и приборы; контрольно-сортирующие устройства. Контрольно-измерительные средства являются основными средствами контроля. Контрольно-сортирующие средства предназначены для сортировки объектов контроля по двум группам: годен, негоден; либо по нескольким группам, исходя, например, из геометрических размеров. 2. По степени воздействия на ход технологического процесса: средства пассивного контроля; средства активного контроля. Средства пассивного контроля относятся к обычным контрольноизмерительным средствам, фиксирующим полученный результат или контрольно-сортирующим устройствам. Средства активного контроля встраиваются в технологическое оборудование и используются для непосредственного управления технологическими процессами. При достижении предельных значений контролируемых параметров эти устройства автоматически управляют режимом работы оборудования, обеспечивают заданную точность, и обладают значительно большей эффективностью предупреждения брака. 3. По степени автоматизации: ручные; механизированные; автоматические. Средства ручного контроля используют там, где применение механизированных автоматических контрольных устройств затруднено или практически невозможно. Эффективность использования автоматических контролирующих устройств обусловлено возможностью получения документа или протоколирования результатов контроля. При использовании механизированных средств контроля протоколирование результатов контроля осуществляет контролер. Технический контроль в сварочном производстве разделяют на входной, операционный и приемочный. К входному контролю относят контроль основных и сварочных материалов и полуфабрикатов, предназначенных для использования при изготовлении изделий, а также предварительный контроль сварочного оборудования и квалификации сварщиков. Входной контроль основных и сварочных материалов имеет целью не допустить использование некачественной продукции поставщика, поступившей к изготовителю сварных изделий. Целью предварительного контроля является оценка работоспособности сварочного оборудования и допуск производственного персонала к выполнению сварочных работ. Система операционного контроля предусматривает контроль технологического процесса и продукции во время выполнения или после завершения технологической операции. Контроль технологического процесса сварки включает контроль подготовки свариваемых деталей, их сборки под сварку, непосредственно процесса сварки и полученных сварных соединений. Приемочный контроль сварных изделий включает внешний осмотр изделия и определение его размеров, а также испытания (неразрушающие для всех изделий и разрушающие для определенного объема выборки). При приемочном контроле проверяется соответствие изготовленной продукции требованиям НТД (нормативно-технической документацией) и принимается решение о её пригодности к использованию. Таким образом, учитывая особые требования к изготовлению сварных изделий, организация технического контроля в сварочном производстве должна быть направлена не только на приемочный контроль продукции, но и на контроль всех стадий производственного процесса её изготовления, а также всех факторов, влияющих на качество продукции. КОНТРОЛЬ ОСНОВНЫХ МАТЕРИАЛОВ На первом этапе основной материал проверяют на наличие сертификата, заводской маркировки и товарного знака изготовителя. В сертификате указывается марка и химический состав, номер плавки, масса и номер партии, результаты всех испытаний, соответствующих стандарту на материал, номер стандарта, тип профиля и размеры. После контроля сертификата металл подвергают внешнему осмотру с целью выявления поверхностных дефектов, искажения формы и др. В случае отсутствия дефектов металл сортируют по типоразмерам и маркируют. Под типоразмером металла понимают металл конкретного типа (формы) и исполнения с определенными значениями контролируемых параметров, например, лист определенной толщины. Маркировку металла выполняют ударным способом (клеймом), электрогравировкой и нанесением краской марки металла, например, вдоль продольной кромки листа. Материал хранится в закрытых помещениях в устойчивых штабелях или на стеллажах. Основной материал принимают партиями и, если он не соответствует требованиям технической документации, то составляется актрекламация (претензия) предприятию - изготовителю материала. Проверенный металл подвергают пробной сварке, после которой проводят механические или технологические испытания, анализ химического состава и металлографический анализ сварного шва. В основном металле могут быть дефекты, связанные с отливкой слитка [2] и вызванные его последующей обработкой давлением [3]. К дефектам слитка относят: горячие и холодные трещины; газовую пористость и усадочные раковины; неметаллические включения и оксидные пленки и др. Дефекты литья при последующей обработке слитков давлением приводят к образованию расслоений, волосовин, раскрытию трещин при горячей деформации и другим дефектам. Под расслоениями понимают цепочку неметаллических частиц после прокатки. Волосовины – мелкие трещины, образовавшиеся из газовых пузырей или неметаллических включений при обработке давлением. При обработке давлением качественного металла могут образоваться дефекты, связанные только с технологией обработки металла давлением. К таким дефектам относят: закаты (складки); вмятины; риски; ковочные трещины и др. Под закатом понимают вдавленные в поверхность металла заусенцы, возвышения, бугорки. Вмятины образуются на поверхности в виде местных углублений, вызываемые попаданием посторонних частиц на поверхность металла или валков. Риски – дефекты в виде канавок на поверхности заготовок при прокатке. Грубые дефекты выявляются визуально, а более мелкие – методами дефектоскопии. Не выявленные и не устраненные дефекты в основном металле могут привести к их раскрытию при сварке и появлению новых дефектов в сварном шве на их основе. В соответствии с общей квалификацией дефекты в основном металле являются металлургическими дефектами, т.к. они возникают при литье и обработке давлением, относящихся к металлургическим процессам. КОНТРОЛЬ КАЧЕСТВА СВАРОЧНЫХ МАТЕРИАЛОВ Контроль качества сварочных материалов так же, как и основного материала включает: 1. проверку наличия сертификата; 2. проверку сохранности упаковки и наличия на ней этикеток; 3. внешний осмотр; 4. пробную сварку с испытанием полученных сварных соединений (проверка технологических свойств сварочных материалов). сварочным материалам относят электроды, присадочную прово- локу, флюс и защитные газы. Электроды принимают партиями. Они упакованы в пачки, которые имеют этикетку с указанием марки, стандарта, завода-изготовителя. Контроль внешнего вида осуществляют выборочным путём определенного количества электродов из пачки. При этом контролируют наличие на поверхности рисок, трещин, сколов покрытия, пор. На каждый из дефектов устанавливаются нормы бракования. Затем проверяют прочность покрытия путём изгиба электрода и падения его на стальную плиту с высоты (0,5÷1 м). Проверяют покрытия на влагостойкость после пребывания в воде в течение суток. Контролируют разнотолщинность покрытия по длине электрода. При проведении пробной сварки оценивают: лёгкость зажигания дуги; стабильность горения дуги; степень разбрызгивания металла; равномерность плавления покрытия; отделимость шлака и т.д. После сварки сварные соединения разрушают и осматривают изломы, проводят механические испытания [1], химические и металлографические исследования. После проверки электроды хранятся в герметичных контейнерах в сухих помещениях. При длительном хранении электроды перед сваркой просушивают. Сварочную проволоку поставляют в бухтах, катушках или кассетах. Проволока снабжена металлическими бирками, в которых указан стандарт, марка и завод-изготовитель. Каждая партия имеет сертификат. При поступлении проволоки производят её очистку от противокоррозионных смазок и окислов. Очистку от смазок окислов и красок выполняют механическими или химическими способами. После очистки, проволока наматывается на кассеты. При намотке осуществляют контроль за поверхностными дефектами. В некоторых случаях проводят химический анализ проволоки и затем осуществляют пробную сварку с анализом химического состава и механических свойств наплавленного металла. При сварке обращают внимание на свойства дуги, шлака, характер плавления. Проволока должна храниться на складах в условиях, исключающих ржавление и загрязнение поверхности. С целью исключения образования ржавчины используют специальную омедненную проволоку. Порошковую проволоку при длительном хранении обязательно следует прокаливать и проверять механические и технологические свойства при сварке образцов. Сварочный флюс упаковывают в герметичные мешки, которые проверяют на наличие этикеток. В этикетках указаны марка, стандарт и завод-изготовитель. Сварочный флюс контролируют на размер зерна путём просеивания через сито с ячейками, соответствующими верхнему и нижнему пределам размеров зёрен. Затем флюс проверяют на содержание влаги. Влажность не должна превышать 0,1 %. Пробу массой 100 грамм просушивают при температуре 300 °С и взвешивают через определенные интервалы времени. Просушивание прекращают, когда результаты взвешивания становятся одинаковыми. Количество влаги определяется по разности между первым и последним взвешиванием. Флюс используют одновременно с проволокой при пробной сварке. При выполнении сварки оценивают устойчивость горения дуги, а после сварки отделимость шлаковой корки при небольшом простукивании шва резиновым молотком. В необходимых случаях контролируют механические свойства и химический состав наплавленного металла. Флюс более чувствителен к влаге, чем электрод. Поэтому флюс должен храниться в герметичных ёмкостях и перед сваркой обязательно подвергаться просушиванию. Защитный газ поставляют в баллонах, снабжённых этикетками, в которых указаны марка, химсостав, завод-изготовитель. Газ по этикеткам проверяют на наличие примесей. Газ контролируют на наличие влаги путём подачи струи на фильтровальную бумагу. При наличии влаги газ пропускают через осушитель. На принятые сварочные материалы работниками ОТК составляется приемочный акт. На некачественные материалы составляется рекламационный акт, направляемый изготовителю.
|
|
|
|
|
|
|
|
СВЕДЕНИЯ О СВАРОЧНЫХ ДЕФЕКТАХ
Под дефектом понимают каждое отдельное несоответствие продукции установленным требованиям. Дефекты в сварных соединениях по происхождению можно разделить на металлургические и технологические.
Металлургические дефекты возникают при изготовлении отливок и дальнейшей их прокатке или прессовании.
К технологическим дефектам относят дефекты, полученные при механической и термической обработке материалов, а также формообразовании свариваемых элементов методами гибки, штамповки и т.д. технологическим дефектам относятся также и сварочные дефекты, которые классифицируют на дефекты подготовки, сборки и самого процесса сварки.
Дефекты в сварных соединениях можно разделить на три группы:
1. дефекты – несплошности сварного шва или сварных точек (на их долю приходится примерно 50 % всех дефектов);
2. дефекты – искажения формы и отклонения геометрических размеров сварного шва или сварных точек (примерно 25 % всех дефектов);
3. дефекты – несоответствия химического состава и структуры металла сварного шва или зоны термического влияния.
Дефекты – несплошности сварки плавлением классифицируются по следующим признакам: • по возможности выявления: явные; скрытые.
Явные дефекты выявляют внешним осмотром, а скрытые – методами неразрушающего контроля.
• по возможности устранения: исправимые; неисправимые.
Дефекты типа сквозных трещин и прожогов являются, как правило, неисправимыми и изделия с такими дефектами подлежат бракованию, т.е. доработка их не допускается.
• по протяжённости: одиночные (отдельные); непротяжённые (расположены компактно); протяжённые (вытянутые в линию).
Примером одиночных дефектов является отдельная пора или включение. К компактно расположенным дефектам относят группу из нескольких пор, расстояние между которыми не более 2–3 их диаметров. Примером протяженных дефектов является цепочка пор образующаяся, например, при дуговой сварке алюминиевых сплавов и располагающаяся вдоль линии сплавления.
• по форме: плоскостные (трещины, непровары); объёмные (поры, включения).
Плоскостные дефекты являются самыми опасными дефектами в связи с концентрацией напряжения в их зоне.
• по месту расположения: наружные (поверхностные); внутренние (подповерхностные и глубинные); сквозные.
Дефекты могут располагаться и в различных зонах сварного соединения, т. е. в шве по границе сплавления или в околошовной зоне.
Приведенная классификация дефектов позволяет оптимизировать выбор методов неразрушающего контроля.
При оценке качества продукции по её дефектности необходимо нормировать характеристики допустимых дефектов. Эти характеристики классифицируют на абсолютные, относительные и статистические.
абсолютным характеристикам относят линейные размеры дефектов (длина, высота, глубина), их количество в сварном шве и расстояние между ними (для единичных дефектов). Для компактно расположенных дефектов определяют площадь дефектного участка, а для протяжённых дефектов определяют их суммарную длину.
Относительные характеристики дефектности используют для сравнительной оценки различных технологических решений, например, при выборе метода и режимов обработки.
К относительным характеристикам относят такие величины, как отношение линейных размеров дефектов, или суммарную их длину, или число дефектов, к единичной длине или толщине сварного шва.
Под единичной длиной сварного шва понимают или один погонный его метр, или – 100 мм (для коротких швов).
Относительной характеристикой является также площадь дефектного участка, отнесённая к площади поперечного сечения шва для компактно расположенных дефектов.
К статистическим показателям дефектности относят, например, суммарную длину дефектов по длине шва, отнесённую к общему числу дефектов. Статистические показатели используют при анализе большого числа сварных соединений (100…1000) в крупносерийном и массовом производстве.
Нормы допустимых дефектов устанавливают в нормативнотехнической документации.
ДЕФЕКТЫ СВАРНЫХ СОЕДИНЕНИЙ
Дефекты сварных соединений являются следствием неправильного выбора или нарушения технологического процесса изготовления сварной конструкции, применения некачественных сварочных материалов и низкой квалификации сварщика.
Дефекты сварки плавлением классифицируют по месту расположения на поверхностные, внутренние и сквозные.
К поверхностным дефектам относят: непровары в корне шва; подрезы; наплывы; кратеры; занижение (ослабление) лицевой поверхности шва; вогнутость корня шва; смещение сваренных кромок; резкий переход от шва к основному металлу (неправильное сопряжение сварного шва); брызги металла; поверхностное окисление; поверхностные трещины.
К внутренним дефектам относят: поры; включения; оксидные плёнки; внутренние трещины; непровары по кромке с основным металлом и между отдельными слоями; свищи.
сквозным дефектам относят трещины и прожоги.
Помимо дефектов – несплошностей к дефектам сварки плавлением относят: искажение формы соединения, связанное с деформацией, и несоответствие геометрических размеров сварного шва или точек, регламентированным значениям, установленным НТД.
Непровары (в корне шва, между отдельными слоями по кромке с основным металлом) – дефект в виде местного несплавления вследствие неполного расплавления свариваемых кромок или поверхностей ранее выполненных валиков (рис. 1). Причины образования дефекта – малая погонная энергия, неудовлетворительная подготовка поверхностей, неправильная форма разделки, большая величина притупления, малые зазоры, смещение электрода, некачественная зачистка шва после выполнения прохода. Наиболее характерно при сварке алюминиевых сплавах и под флюсом. Является концентратором напряжения. Трудно выявляются в кольцевых швах. Исправление – подварка с удалением корневой части.
Прожоги (одиночные, протяженные, дискретные) дефект в виде сквозного отверстия, образовавшийся в результате вытекания сварочной ванны Возникает из-за – большой погонной энергии, увеличенного зазора, малой величины притупления и большого смещения кромок, коробления кромок и отставания их от подкладки при сварке. Характерны при сварке тонкостенных элементов, а так же первого (корневого) шва при многослойной сварке. Как правило, брак, если выполняют подварку.
Рис. 1. Непровар
Кратеры – дефекты в виде воронкообразного углубления, образовавшегося в результате внезапного прекращения сварки или быстрого отключения сварочного тока. Образуется в результате нарушения техники сварки, которое приводит к ослаблению сечения. Сопровождается усадкой и трещинами усадочного происхождения. Кратер – концентратор напряжения. Исправление – удаление дефектного участка и заварка. При автоматической сварке используют технологические планки для вывода кратера или плавное отключение тока.
Наплывы на сварном соединении – дефект в виде натекания жидкого металла на поверхность основного или ранее выполненного валика и несплавление с ним (рис. 3). Причины образования дефекта – большой ток, большая скорость сварки, длинная дуга (повышенное напряжение), смещение электрода, большая скорость подачи присадочной проволоки, наклон электрода (неправильное ведение). Возникает с лицевой стороны соединения или обратной из-за некачественного поджатия к подкладке и, как правило, при сварке в горизонтальном и вертикальном положении, а также на спуск и на подъем. Наплывы – концентраторы напряжения. Исправление – зашлифовка.
Подрезы зоны сплавления (односторонний, двухсторонний) – дефекты в виде протяженного углубления вдоль линии сплавления основного металла и шва (рис. 4). Образуется из-за большого тока, большой скорости сварки, длинной дуги, наклона электрода (неправильное ведение). Как правило, возникает при сварке концентрированными источниками в режиме глубокого проплавления, а также при сварке угловых швов. Этот дефект концентратор напряжения. Он приводит к ослаблению сечения. Исправление – заглаживание дугой при неглубоких подрезах и подварка при глубоких подрезах.
Неплавное сопряжение сварного шва – дефект в виде резкого перехода поверхности сварного шва к основному металлу. Причины образования дефекта – несоблюдение техники сварки, большая скорость подачи присадочной проволоки. Концентратор напряжения, который возникает в угловых швах. Исправление – зашлифовка или прокатка роликами.
Рис. 3. Наплывы на сварном Рис. 4. Подрезы зоны соединении сплавления
Брызги металла – дефект в виде затвердевших капель жидкости металла на поверхности сварного соединения. Причины образования дефекта – несоблюдение техники сварки и длинная дуга. Возникает при сварке толстопокрытыми электродами, в СО2 или электролучевой сварке с глубоким проплавлением. Исправление – вырубка.
Вогнутость корня шва – дефект в виде углубления на обратной поверхности сварного одностороннего шва. Причины образования дефекта – большие зазоры и малое притупление. Этот дефект возникает в стыковых и угловых швах, который приводит к ослаблению сечения шва. Исправление – подварка.
Занижение шва – дефект в виде провисания сварного шва. Образуется из-за большого зазора, большого угла разделки кромок, несоблюде-
ния техники сварки. Возникает при сварке алюминиевых сплавов. Исправление – подварка с использованием присадочной проволоки.
Смещение сваренных кромок – дефект в виде несовпадения сваренных кромок по высоте из-за некачественной сборки сварного соединения. Возникает, как правило, при сварке стыковых тонкостенных элементов с нарушением технологии сборки. Является концентратором напряжения. Исправление – подварка
Свищ сварного шва – дефект в виде несквозного углубления в сварном шве, образовавшийся из-за некачественного основного металла или нарушения защиты сварочной ванны (рис. 5). Сопровождает поры и трещины, выходящие на поверхность. Наиболее часто возникают при сварке в СО2. Исправление – подварка с разделкой.
Поверхностное окисление сварного соединения – дефект в виде окисной пленки с различными цветами побежалости на поверхности сварного соединения. Возникает из-за малого расхода защитного газа, наличия примесей в защитном газе, загрязнения поверхности сопла, неправильного подбора диаметра сопла и расстояния его от поверхности металла, отсутствия дополнительных защитных козырьков, нарушения техники сварки. Возникает при сварке активных металлов. Исправление – зачистка поверхности.
Трещины (поверхностные, внутренние, сквозные, продольные, поперечные, разветвленные) – дефект в виде разрыва в сварном шве по линии сплавления или в околошовной зоне (рис. 6). Причины образования – жесткая конструкция изделия, сварка в жестко закрепленных приспособлениях, большой время между сваркой и термообработкой, большая скорость охлаждения, ошибка в проектировании сварного шва (близко расположенные концентраторы), нарушение технологии (температура подогрева, порядок наложения швов), нарушение защиты, некачественный основной металл. Наиболее опасный и недопустимый дефект. Исправление – подварка с предварительной разделкой или засверловкой концов трещины.
Рис. 5. Свищ сварного шва Рис. 6. Трещины
Поры сварного шва (одиночные, рассеянные, скопления, цепочка) – дефект сварного шва в виде полости округлой или продолговатой формы заполненной газом (рис.7). Образуются из-за влажного флюса, отсыревших электродов, некачественной подготовки свариваемых кромок и поверхности сварочной проволоки, увеличенного диаметра электрода, длинной дуги, увеличенной скорости сварки, некачественной защиты сварочной ванны, некачественного основного металла. Возникает при сварке алюминиевых и титановых сплавов, в глубоких стыковых швах, при затруднении дегазации. Приводит к ослаблению сечения и снижению герметичности. Исправление – единичные поры оставляют, во всех остальных случаях подварка.
Рис. 7. Поры сварного шва или включения
Включения (шлаковые, оксидные, вольфрамовые, нитридные) – дефекты в виде неметаллических частиц или инородного металла в металле шва (рис. 7). Возникает из-за некачественной подготовки поверхности, некачественного основного металла, нарушения технологии сварки, нарушения защиты сварочной ванны. Имеют сферическую или продолговатую форму, а также в виде прослоек. Является концентратором напряжения. Исправление – подварка с разделкой.
РЕМОНТ НЕ КАЧЕСТВЕННЫХ СВАРНЫХ СОЕДИНЕНИЙ И КОНТРОЛЬ ПОДВАРОК
При обнаружении недопустимых дефектов производят ремонт сварных соединений. Ремонт дефектных участков включает следующие операции:
1. Оформление записи в технологическом паспорте на изделие в графе «ведомость замечаний» о необходимости доработки сварных соединений.
2. Разметка дефектного участка на изделии. При разметке необходимо соблюдать определённые условия. Так длина удаляемого участка должна быть на 10–15 мм больше длины обнаруженного дефекта, а ширина удаляемого участка должна быть такой, чтобы ширина шва после заварки не превышала двойной ширины шва до заварки.
Разметку выполняет слесарь, аттестованный на эту работу. Контроль правильности разметки дефектного участка осуществляет контролер БТК (бюро технического контроля).
3. Разделка (выборка) дефектного участка.
Основными способами разделки являются:
− механические (вырубание пневмозубилом, высверливание, вышлифовка, выфрезеровка);
− термические (воздушно-дуговая, плазменно-дуговая, строжка); Под строжкой понимают поверхностное снятие металла.
4. Обработка поверхности разделки шабером или шарошкой. Шарошка – набор шлифовальных дисков или фрез разного диаметра, насаженных на один вал, а шабер – инструмент в виде заостренного с одной стороны трехгранного напильника.
Обработка поверхности разделки производится с целью устранения острых выступов и углов и обеспечения плавных очертаний разделки, а также удаления науглероженного слоя при термической разделке сталей.
Выборка на всю толщину сварного шва не выполняется. Толщина остающегося металла должна быть не менее 1 мм. После выполнения разделки производится контроль, включая рентгенографический.
5. Заварка дефектного участка. После заварки зачищаются неровности поверхности с сохранением усиления шва.
6. Повторный контроль сварного соединения неразрушающими методами.
В зависимости от степени ответственности сварных соединений допускается 2-х или 3-х кратная подварка дефектного участка. При этом контролируется длина подварки и суммарная длина всех подварок на ремонтируемом изделии. Суммарная длина участков сварных швов с любыми дефекта, подлежащих доработке посредством подварки, не должна превышать 30 % при длине шва 500 мм и 20 % при длине шва более 500 мм.
Дефектные участки со сквозными трещинами не выбирают, а засверливают по концам, отступая от края трещины на 10–15 мм. Диаметр сверла 4–5 мм. Дефектный участок затем проваривают на всю толщину. При толщине металла до 2,5 мм используется сверло диаметром 1,5–2,5 мм.
Непровары в корне шва выбирают, выполняя разделку с обратной стороны сварного шва. Заварку дефектных участков, как правило, осуществляют в основном ручной сваркой. В некоторых случаях, если это допускается, заварку производят на автоматах. В качестве присадочного материала при подварке применяют проволоку той же марки, что и при сварке основного металла. Для алюминиевых сплавов перед подваркой проволоку протравливают и шабрят до металлического блеска. Возбуждение дуги при подварке производят на технологической пластине, а вывод её после окончания подварки выполняют на сварной шов. Вывод дуги на основной металл запрещается. Перед подваркой подбирают режим подварки на технологических образцах, толщина которых равна толщине подвариваемого участка в зоне участка.
При контактной сварке дефектные точки засверливают с установкой на их место заклёпок или заваркой отверстия ручной дуговой сваркой. Если допускается, то ставят повторную точку рядом с первой.
МЕРЫ КОНТРОЛЯ КАЧЕСТВА САРНЫХ СОЕДИНЕНИЙ
Внешний осмотр – выполняют невооруженным глазом или с помощью лупы (не более семикратного увеличения), при этом выявляют трещины, подрезы, наплывы, равномерность шва и размеры его. Эта операция простая, но высокоэффективная.
Механические испытания [1] – это испытания образцов на разрыв, изгиб, ударную вязкость, относительное удлинение, на растяжение выполняются, на ударную вязкость.
Гидравлические испытания – производятся при давлении воды или масла, превышающем рабочее на 25–50 %, с выдержкой в течение определенного времени. Этим испытанием проверяется плотность швов на течи, а также прочность конструкции.
Пневматические испытания – наполнение контролируемой емкости сжатым воздухом (рис. 8). Так, например, испытывают сварные баллоны для пропана. После заполнения воздухом баллон погружают в ванну с водой для проверки плотности, при этом осматривают на наличие воздушных пузырьков. Процесс простой и быстрый, при этом проверяется плотность швов на течи и прочность.
Рис. 8. Схема испытаний на плотность сварных швов воздухом
Испытания вакуумным способом – метод основан на регистрации падения вакуума в замкнутом объёме контролируемого изделия или на фиксации пробного газа, появившегося в объеме. Процесс непростой, поверхность хорошо промывают растворителями и протирают, а иногда шлифуют до блеска, затем ставят на эту контролируемую поверхность вакуум-камеру с присосками-уплотнениями и образуют вакуум. Наибольшее распространение получил контроль гелиевой камерой с вакуумными присосками. Вакуумная камера переносная и имеет прозрачное смотровое стекло.
Испытание керосином – смачивание сварных швов керосином, выдержка, затем, если имеется неплотность, керосин проступает желтыми пятнами на меловом покрытии с обратной стороны шва. Процесс прост и достаточно надежен. Керосиновая проба эквивалентна 4 кгс/мм2 гидравлического давления.
Испытание аммиаком – испытуемые швы покрывают бумажной или марлевой лентой, пропитанной 5 %-ным водным раствором азотнокислой ртути или фенолфталеином. В изделие нагнетают воздух в смеси с аммиаком до определенного давления. Проходя через неплотности шва, аммиак оставляет на бумаге черные (раствор азотнокислой ртути) или красные (фенолфталеин) пятна.
Испытание с помощью течеискателей. Применяют гелиевые течеискатели, при контроле внутри испытуемого сосуда создают глубокий вакуум, а снаружи сварные швы обдувают смесью воздуха с гелием. Через неплотности гелий проникает внутрь сосуда, а затем в течеискатель, оборудованный аппаратурой для его обнаружения.
Металлографические исследования – это изучение структуры сварного соединения на специальных шлифах под микроскопом с увеличением в 400 раз и более. При необходимости эти структуры фотографируются.
Радиационная дефектоскопия – это просвечивание рентгеновскими лучами (рис. 9). Рентгеновские лучи обладают значительной проникающей способностью и действуют на фотопленку подобно световым. Этими лучами можно просвечивать металл толщиной до 500 мм. При просвечивании лучи направляются перпендикулярно шву. В процессе просвечивания можно производить фотографирование с фиксацией дефектов на фотопленке. Недостатком контроля рентгеновскими и гаммалучами является их опасность при значительных дозах.
Рис. 9. Схема просвечивания рентгеновскими лучами:
1 – рентгеновская трубка; 2 – контролируемый шов;
3 – кассета с фотопленкой
Просвечивание гамма-лучами (рис. 10, рис. 11). Для выявления внутренних дефектов применяют гамма-лучи, возникающие при самопроизвольном распаде некоторых элементов (радий, уран). Для контроля сварных швов используют искусственные радиоактивные вещества (изотопы), например, кобальт-60, цезий-137 и др.
Рис. 10. Схема просвечивания сварного шва:
1 – контейнер; 2 – ампула; 3 – контролируемый шов; 4 – кассета с пленкой
Гамма-излучатели хранятся в специальных защитных контейнерах. Работа с ними регламентируется инструкциями и правилами санитарной инспекции.
Рис. 11. Схема устройства ампулы с радиоактивным веществом:
1 – радиоактивное вещество; 2 – стеклянная ампула; 3 – вата, 4 – латунная или алюминиевая оболочка; 5 – крышка; 6 – свинцовый футляр
Установки рентгеновского и гамма-излучения опасны для людей, поэтому имеют специальную защиту, а работы с их использованием выполняются в отдельных помещениях, оборудованных по специальным правилам.
Ксерорадиационная дефектоскопии заключается в том, что для обнаружения дефекта пользуются пластинкой из стальной или алюминиевой фольги, на поверхность которой нанесен фотопроводниковый слой.
Пластину предварительно заряжают. Под действием рентгеновского или гамма-излучений ксеропластина теряет электрические заряды. Остаточный заряд будет тем меньше, чем больше интенсивность излучения, когда лучи проходят какие-то неплотности, пустоты в металле (шлак, поры и т. п.). Поэтому интенсивность излучения в местах дефектов бывает выше и заряд в этих местах будет меньше. Все это образует в ксеропластине скрытое электростатическое изображение, которое преобразуется в видимое путем его проявления. Оно заключается в том, что пластина со скрытым электростатическим изображением опыляется предварительно электризуемым порошком (мел, тальк и др.).
Преимущество ксерорадиографии перед радиографией – высокая производительность получения снимков и сухое проявление. Этим способом контролируют качество швов и металла до толщины 20 мм.
Ультразвуковая дефектоскопия. Ультразвуковой метод контроля основан на способности ультразвуковых волн отражаться от границы раздела двух упругих сред, обладающих разными акустическими свойствами (рис. 12).
Рис. 12. Схема ультразвукового контроля:
1 – генератор ультразвуковых колебаний; 2 – пьезоэлектрический щуп;
3 – усилитель; 4 – экран дефектоскопа
Отразившись от нижней поверхности изделия, ультразвук возвратится, будет принят датчиком, преобразован в электрические колебания и подан на экран электроннолучевой трубки. При наличии дефектов ультразвуковые колебания исказятся, это будет видно на экране электронно-лучевой трубки, где появится всплеск – искажение. По характеру и размерам искажений определяют виды и размеры дефектов.
Распространяются колебания в однородных материалах по относительно прямым линиям, а на границе раздела двух разнородных материалов (поры, трещины и др.) происходит их отражение.
Недостаток ультразвукового контроля – в сложности расшифровки дефекта, ограничении для применения на изделиях аустенитных сталей, чугуна, металлов с крупным зерном, невозможности контроля сталей малой толщины (до 4 мм).
Магнитная дефектоскопия. Магнитные методы контроля сварных швов основаны на том, что при прохождении магнитного потока по испытуемому материалу в местах дефектов магнитный поток искривляется, рассеивается и это рассеяние в намагниченном участке изделия обнаруживается специальным прибором – магнитным дефектоскопом.
Если на поверхность контролируемой зоны нанести ферромагнитный порошок (обладающий магнитными свойствами), то над местом расположения дефекта создадутся скопления порошка (рис. 13).
Рис. 13. Схема магнитографического метода контроля:
1 – контролируемый шов; 2 – ферромагнитная пленка или порошок;
3 – электромагнит, 4 – источник постоянного тока
Намагничивание осуществляется пропусканием постоянного тока по детали, созданием магнитного поля вокруг детали.
По неравномерности линий магнитного потока, а значит, по неравномерности расположения порошка, можно судить о наличии дефекта. Магнитные потоки рассеяния преобразуются в электрические сигналы на экране осциллографа.
Магнитным методам контроля могут быть подвергнуты детали только из ферромагнитных материалов, свойства которых обусловлены внутренними молекулярными токами, в основном вращением электронов вокруг собственной оси. Хромоникелевые стали, медь, алюминий немагнитный и магнитному контролю не подлежат.
В зависимости от способа регистрации магнитного потока рассеяния имеется четыре магнитных метода контроля, но в сварочном производстве применяются только два: магнитопорошковый и магнитографический. В первом методе потоки рассеяния выявляются с помощью магнитного порошка, во втором – регистрируются на магнитную ленту.
Капиллярные методы контроля. Существует два метода:
1. люминесцентный (ЛД) (люминесцентная дефектоскопия) основан на свойстве некоторых веществ (люминофоров) светиться при действии ультрафиолетовых лучей;
2. цветная дефектоскопия (ЦД), когда применяются красители, видимые в зоне дефекта при дневном свете.
Капиллярные методы контроля предназначены для обнаружения несплошности в поверхностных слоях изделий, которые состоят в изменении светоотдачи дефектов, заполнением их с поверхности специальными свето- и цвето контрастными индикаторными жидкостями, называемыми пенетрантами. Если в состав пенетранта входят люминесцирующие вещества, т. е. вещества, дающие яркое свечение при облучении их ультрафиолетовым светом, то такие жидкости называются люминесцентными, а метод контроля соответственно – люминесцентным.
Если основой пенетранта являются красители, видимые при дневном свете, то метод контроля называют цветным (цветная дефектоскопия). В ЦД используют красители ярко-красного цвета.
Сущность капиллярной дефектоскопии состоит в следующем. Поверхность изделия очищают от загрязнений, обезжиривают, сушат. После этого на нее наносят слой пенетранта и дают выдержку, чтобы жидкость смогла проникнуть в имеющиеся дефекты. Затем поверхность очищают от жидкости, часть которой остается в полости дефектов. На поверхность изделия после удаления с неё пенетрантов наносят специальный проявляющий материал в виде быстро сохнущей суспензии (каолина, коллодия) или лаковые покрытия. Проявляющий материал вытягивает пенетрант из полости дефектов, оставляя на себе следы расположения дефекта, полностью повторяющие конфигурацию дефекта.
Дата добавления: 2018-04-04; просмотров: 437; Мы поможем в написании вашей работы! |
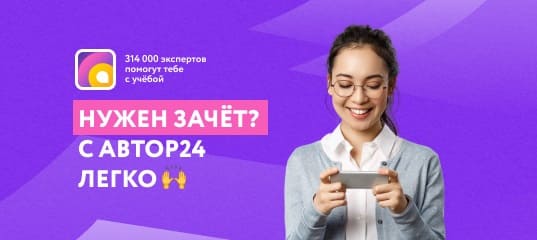
Мы поможем в написании ваших работ!