ОСОБЕННОСТИ УПРАВЛЕНИЯ ХИМИКО-ТЕХНОЛОГИЧЕСКИМ ПРОЦЕССОМ
ТЕМА 1
ВВЕДЕНИЕ В СИСТЕМЫ УПРАВЛЕНИЯ ХИМИКО-ТЕХНОЛОГИЧЕСКИМИ ПРОЦЕССАМИ
ЗНАЧЕНИЕ АВТОМАТИЧЕСКОГО УПРАВЛЕНИЯ ДЛЯ РАЗВИТИЯ ХИМИЧЕСКОЙ ПРОМЫШЛЕННОСТИ НА СОВРЕМЕННОМ ЭТАПЕ
Наука об автоматических системах управления химико-технологическими процессами изучает законы их построения и действия, методы исследования и настройки.
Технический уровень химической промышленности на современном этапе ее развития во многом определяется уровнем управления. Без наличия необходимых средств автоматической диагностики химико-технологического процесса и автоматического управления им в принципе невозможен технический прогресс в химической промышленности. Современное химическое или нефтехимическое производство является высокоавтоматизированным производством. Информационная мощность крупного химического предприятия, оцениваемая количеством измеряемых параметров, составляет более 1500. Автоматическое управление химическим производством позволяет значительно увеличить производительность труда и, что имеет особое значение для химической промышленности, повышает социальную эффективность труда, т. е. облегчается труд обслуживающего персонала, улучшаются санитарно-гигиенические условия их работы, повышается культурный и профессиональный уровень специалистов. На химических предприятиях появились работники, владеющие компьютерами, специалисты по информационным технологиям. Автоматическое управление химическим производством позволяет не только улучшить качество производимой продукции, снижая ее себестоимость, но и уменьшить отрицательное воздействие химического предприятия на окружающую среду.
|
|
Таким образом, понятия технический прогресс и уровень автоматического управления в химической промышленности неотделимы.
Возможности автоматического управления (с использованием микропроцессорной техники) в химической технологии:
• автоматический пуск и останов химического производства;
• автоматический контроль технологических параметров;
• автоматическое прогнозирование ведения технологического процесса;
• поддержание заданных (оптимальных) технологических режимов;
• повышение качества производимой продукции;
• повышение производительности технологического оборудования и увеличение объема производимой продукции;
• снижение затрат сырья, материалов и энергии на производство единицы продукции;
• безопасное ведение химико-технологического процесса (уменьшение вероятности нарушения технологического режима, приводящее к нанесению вреда обслуживающему персоналу, оборудованию, окружающей среде);
|
|
• увеличение надежности химико-технологических процессов и в целом химико-технологической системы (сокращение простоев оборудования из-за неполадок и увеличение межремонтных сроков работы технологического оборудования);
• предупреждение загрязнения окружающей среды промышленными отходами и стоками.
КРАТКИЙ ОЧЕРК ИСТОРИИ РАЗВИТИЯ СИСТЕМ АВТОМАТИЧЕСКОГО УПРАВЛЕНИЯ
В истории развития САУ можно условно выделить четыре исторических периода:
• греческая и арабская цивилизации (III век до н. э.—1200 год н. э.);
• промышленная революция в Европе (с третьей четверти XVIII века, хотя корни ее прослеживаются и в начале XVII века);
• начало массовых коммуникаций (1910—1945);
• век освоения космоса, компьютерный век (с 1957 г. по наши дни).
Простейшие автоматические регуляторы и устройства применялись еще до новой эры. Известно, что системы регулирования с обратной связью применялись в III веке до нашей эры, например, для автоматического регулирования уровня воды в водяных часах с помощью поплавкового регулятора, чтобы повысить точность их показаний. Водяные часы представляют собой два резервуара. В первом резервуаре водяных часов уровень воды должен бытьпостоянным, постоянство его иподдерживает поплавковой регулятор.Этот постоянный уровень обеспечивает постоянство расхода водыво второй резервуар через трубу, расположенную в днище первогорезервуара. Уровень воды во втором резервуаре, таким образом,зависел от времени истечения воды из первого резервуара. Так былреализован принцип регулирования с обратной связью. Поплавковыерегуляторы использовались для регулирования уровня масла влампах для освещения, для дозированного разлива вина.
|
|
В средние века применялись центробежные регуляторы хода водяных мукомольных мельниц. В 1657 г. X. Гюйгенс предложил маятниковый регулятор хода для механических часов. В это же время были изобретены регуляторы температуры (для поддержания температуры при плавке металлов в печах; в инкубаторах для выведения цыплят — 1624 г.). В конце XVIII века в Америке регуляторы температуры применяются в химических печах, в производстве стали и фарфора.
Появление паровых машин приводит к изобретению регуляторов давления. В 1681г. изобретен первый предохранительный клапан для сброса давления пара. К первым промышленным регуляторам относят автоматический поплавковый регулятор уровня в паровом котле паровой машины, построенной в 1765 г. И.И. Ползуновым, и центробежный регулятор скорости для стабилизации угловой скорости вращения вала паровой машины, сконструированный Д. Уаттом (1788).
|
|
Вновь пробуждается интерес к регуляторам уровня. Слесарь Томас Креппер за изобретения сливных бачков с регуляторами уровня в 1775 г. возводится в рыцарское достоинство английской королевой Викторией.
Большой вклад в разработку и создание регуляторов для различных целей внесли русские ученые И.А. Вышнеградский, Н.Е. Жуковский, A.M. Ляпунов и др.
Исследования И.А. Вышнеградского и Д. К. Масквелла в области устойчивости и качества процессов регулирования положили начало развитию теории автоматического регулирования.
Отправной точкой предыстории теории автоматического управления можно считать 1868 г., когда Д.К. Максвелл выполнил первый строгий математический анализ устойчивости системы управления с обратной связью. Он исследовал влияние параметров системы на устойчивость и показал, что система устойчива, если корни характеристического уравнения имеют отрицательные действительные значения. Независимо от Д.К. Максвелла в 1877 г. И.А. Вышнеградский исследовал устойчивость регуляторов. В 1893 г. А. Б. Стодола впервые вводит понятие постоянной времени системы и предлагает оценивать устойчивость системы по устойчивости характеристического уравнения. В 1892 г. A.M. Ляпунов опубликовал в России свое знаменитое сочинение «Общая задача об устойчивости движения». На Западе теория устойчивости по Ляпунову становится известной лишь в 1960 г. и получает свое признание. В 1892—1898 гг. английский инженер О. Хевисайд исследует переходные характеристики систем, вводя понятие передаточной функции.
В 1909 г. в России издается первый русский учебник по теории регулирования Н.Е. Жуковского «Теория регулирования хода машин».
В 1932 г. американский ученый X. Найквист предложил для оценки устойчивости систем частотный критерий устойчивости. В 1940 г. X. Боде исследовал устойчивость замкнутых систем, используя такие понятия, как коэффициент усиления и запас устойчивости по фазе. Н. Минорский (1922), рассматривая нелинейные эффекты в замкнутых системах, впервые использует пропорционально-интегрально-дифференциальный регулятор. X. Хазен (1934) опубликовал теорию сервомеханизмов (исполнительных механизмов).
До 50-х годов прошлого века классической теорией автоматического регулирования (ТАР) было принято называть теорию устойчивости и качества процессов в системе объект—регулятор, базирующуюся на рассмотрении обыкновенных, преимущественно линейных, дифференциальных уравнений. ТАР тесно соприкасается с теорией устойчивости движения «в малом» А.М. Ляпунова, но имеет выраженную инженерную направленность.
В конце 50-х—начале 60-х годов появляются работы Л.С. Понт-рягина, Р. Беллмана, Р. Калмана, которые заложили основы современной теории автоматического управления. Использование математических моделей не только на стадии проектирования, но и в процессе функционирования систем является одной из характерных черт современной теории автоматического управления. Важным разделом современной теории автоматического управления является оптимальное (и субоптимальное) оценивание параметров и характеристик по экспериментальным данным — идентификация.
Автоматическое регулирование и управление перестает быть скорее искусством и становится наукой с появлением электронной вычислительной техники.
Первая электронная вычислительная машина (ЭВМ) была создана в 1945 г. в США под руководством американских ученых Дж.В. Моучли и Д.П. Эккерта и предназначалась для расчета баллистических таблиц (машина была построена по заказу артиллерийского управления). ЭВМ содержала 18 тысяч электронных ламп и потребляла 150 кВт. Быстродействующая электронная счетная машина (БЭСМ) была сконструирована в начале 50-х годов прошлого века в СССР коллективом ученых, во главе которых стоял академик С.А. Лебедев.
В 1960 г. разработано второе поколение компьютеров с использованием полупроводниковой технологии. С 1965 г. начинает развиваться миникомпьютерная технология, а в 1969 г. В. Хофф изобрел микропроцессор. В 1970—1980-е годы получает развитие идея об использовании цифровых компьютеров для управления в промышленности, особенно химической. Основная мотивация такого подхода — развитие ядерной технологии. К 1983 г. появляются первые персональные компьютеры. Проектирование современных систем управления при наличии прикладных пакетов компьютерных программ, включая такие, как ORACLS, Program CC, Control-C, PC-Matlab, MATRIXX, Easy5, SIMNON и др., становится доступным для рядового инженера.
Американский ученый Норберт Винер (1894—1964) был одним из создателей кибернетики (от греч. kibernos — рулевой, кормчий) — науки об общих законах управления. Кибернетика стала теоретической базой создания и внедрения автоматизированных систем управления (АСУ).
ОСОБЕННОСТИ УПРАВЛЕНИЯ ХИМИКО-ТЕХНОЛОГИЧЕСКИМ ПРОЦЕССОМ
Под химико-технологическим процессом (ХТП) понимают определенную последовательность процессов (химических, физико-химических, их сочетаний) целенаправленной переработки исходных сырья и веществ в продукт. Химическое производство представляет собой совокупность процессов и операций, осуществляемых в аппаратах и машинах и предназначенных для целенаправленной переработки исходных веществ и сырья в продукты путем химических превращений.
Вопросам управления в химической технологии придается особое значение. Это, в первую очередь, связано со следующими особенностями ХТП:
1) сложность и высокая скорость протекания ХТП;
2) агрессивность и токсичность перерабатываемых веществ;
3) взрыво- и пожароопасность перерабатываемых веществ;
4) высокие (или низкие) температуры; высокие (сверхвысокие) давления или глубокий вакуум;
5) высокая чувствительность ряда ХТП к нарушениям технологического режима и т. д.
Необходимо учитывать и такое важное обстоятельство для управления: не все технологические параметры (показатели), которыми необходимо управлять в процессе, доступны непосредственному и непрерывному измерению. Из практики эксплуатации ХТП известно, что такому измерению трудно поддаются показатели состава и качества перерабатываемого сырья, а также показатели состава и качества получаемого продукта. Даже в случае прямого и непрерывного измерения, например расходов материальных потоков, как следует из сведения материальных балансов, на крупных химических предприятиях потери исходного сырья и веществ, конечных продуктов достигают 2,0...2,5 %.
Необходимо также помнить, что управление будет более эффективным, если выбранный управляемый параметр чувствителен к условиям проведения ХТП. Тогда даже небольшие отклонения текущих значений управляемого параметра от заданного вызовут к действию систему управления.
Для химико-технологических процессов, осуществляемых в крупнотоннажных химических и нефтехимических производствах, характерно запаздывание и параметры (показатели), выбранные для управления, при изменении условий проведения процесса не могут изменяться мгновенно. Невозможность прямых и непрерывных измерений параметров (показателей) процесса, отсутствие мгновенной реакции параметров (показателей) процесса на возмущающие воздействия усложняют систему управления ХТП.
Кроме того, все время необходимо учитывать степень воздействия химических производств на окружающую среду. В этой ситуации системы управления ХТП должны обеспечить безопасность химических производств, постоянно контролировать состав и качество перерабатываемого сырья и веществ, состав и качество конечных продуктов, окружающей среды.
Исходя из изложенных особенностей ХТП, перечислим функции, выполняемые устройствами автоматического управления в химической технологии.
1. Диагностика оборудования, измерение и контроль технологических параметров и определение причин возникновения аварийных ситуаций.
2. Сигнализация (световая и звуковая) при отклонении технологических параметров от заданных режимов и аварийном состоянии оборудования.
3. Логическое управление блокировками и защитой; аварийное отключение (переключение) технологического оборудования.
4. Управление (регулирование) технологическими параметрами.
Современному состоянию работ в области управления соответствуют системы управления, реализуемые посредством цифровых систем. Цифровые системы могут применяться во многих областях управления, таких как автоматическая сигнализация, блокировка, встроенная линеаризация или компенсация сигнала. Однако основная задача систем управления — управление технологическим процессом.
Автоматическое регулирование является частным случаем более общего понятия автоматического управления. Теория автоматического регулирования является основой построения первого уровня управления, а теория автоматического управления — основа всей иерархической структуры информационных процессов управления сложными химико-технологическими объектами.
Теория автоматического управления позволяет изучить свойства системы, которые принято называть: наблюдаемостью, идентифицируемостью, управляемостью и адаптируемостью. АСУ представляет собой сложную динамическую систему, поведение которой в реальных условиях требует соответственно сложного математического описания, больших затрат времени на программирование и т. д. Поэтому для математического описания АСУ необходима некоторая идеализация, следствием которой является получение приближенных результатов. Уточнение их и окончательный выбор параметров системы управления производится с применением средств математического моделирования и вычислительной техники с последующей настройкой параметров регуляторов в реальном масштабе времени (в реальных условиях).
Сущность разработки АСУ заключается в том, чтобы, располагая сведениями о свойствах объекта управления (статических и динамических), а также заданными требованиями к системе управления в целом (запасу устойчивости, надежности, усилению по мощности, качеству и т. д.), подобрать соответствующую элементную базу и составить схему управления, способную действовать в реальных условиях химического производства в соответствии с поставленными требованиями. Естественно, что этот подход предполагает наличие сведений об элементах, устройствах, входящих в состав АСУ, а также то, что они должны рассматриваться во взаимодействии друг с другом, и при этом вся система управления в целом должна быть работоспособна и обладать требуемыми свойствами.
Система автоматического регулирования, как правило, предполагает наличие достаточно сложного логического устройства (автоматического регулятора — управляющего устройства, осуществляющего автоматическое регулирование с помощью аппаратурной реализации алгоритмов управления), вырабатывающего регулирующее воздействие (в соответствии с требуемым законом регулирования) на объект управления в результате сравнения текущего значения регулируемого параметра с заданным.
Управление происходит с заранее заданным алгоритмом.
Дата добавления: 2018-04-04; просмотров: 839; Мы поможем в написании вашей работы! |
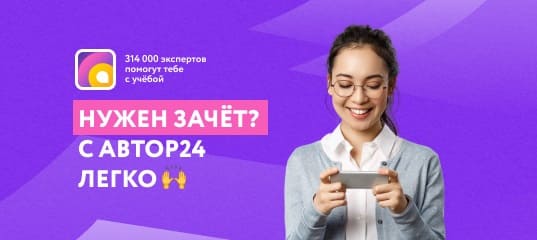
Мы поможем в написании ваших работ!