Переход к суперсверхкритическим параметрам пара
СПЭ лекция № 1
Основные пути совершенствования энергетического оборудования классических ТЭС
Производство электроэнергии в России базируется на использовании классических ТЭС и ТЭЦ, работающих на органическом топливе. Несмотря на то, что в последние годы в России все шире вводятся ПТУ и ГТУ, классические ТЭС доминируют и еще долгие годы будут доминировать в теплоэнергетике России. Тем более это относится к ТЭС, работающим на твердом топливе, массовое использование для которых парогазовых технологий пока дело отдаленного будущего. Поэтому понимание тех резервов, которые пока еще не используются при создании и эксплуатации традиционных ТЭС, а также тенденций их развития представляется очень важным.
КПД нетто энергоблока как составной части ТЭС определяется соотношением:
![]() |
|
где Nс.н/Nэ — доля собственных электрических нужд Nс.н; Nэ — мощность на зажимах электрогенератора; hк — КПД котла; hпту — КПД паротурбинной установки.
На рис. 10.1 показана доля собственных нужд энергоблоков и ТЭС с поперечными связями. В среднем по России они составляют 5,8 %, наибольшие значения соответствуют старым ТЭС на начальное давление 90 ат и энергоблокам, работающих на угле.
Экономичность котлов, работающих на газе, составляет 90—93 %, а малых котлов, работающих на твердом топливе может быть менее 80 %. Имеются отдельные ТЭС, на которых КПД котлов достигает 95—96 %.
|
|
Наименьшую экономичность имеют паротурбинные установки: их КПД не превышает 45 %. Это связано не с несовершенством оборудования, а с законами термодинамики: тепло конденсации пара, отработавшего в турбине и передаваемого охлаждающей воде в конденсаторе, составляет половину теплоты, поступившей в котле от топлива к рабочему пару.
Низкое значение КПД ПТУ и обусловливает эффективность его первоочередного повышения. Конечно, и уменьшение расхода электроэнергии на привод питательных, циркуляционных и конденсатных насосов, на систему маслоснабжения, охлаждения генераторов, и повышение КПД котла играет большую роль в экономии топлива, однако эффект от этого меньше, чем от повышения КПД ПТУ. Поэтому именно паротурбинной установке ниже уделяется основное внимание.
Основными потенциальными методами повышения экономичности ПТУ являются:
а) аэродинамическое совершенствование паровой турбины;
б) совершенствование термодинамического цикла, главным образом, путем повышения параметров пара, поступающего из котла, и снижения давления пара, отработавшего в турбине;
в) совершенствование и оптимизация тепловой схемы и ее оборудования.
|
|
Сравнительный анализ технического уровня отечественных и зарубежных паровых турбин
Речь идет о сравнении отечественных и зарубежных паровых турбин, имеющих одинаковое назначение, одинаковые начальные параметры пара, близкую номинальную мощность, подсоединенных к примерно одинаковым электрогенераторам. Если сказать еще короче, то нас будет интересовать качество проточной части и совершенство собственно конструкции паровой турбины.
Выше уже отмечалось высокое совершенство паровой турбины. Еще раз подчеркнем ее исключительную роль в процессе выработки электроэнергии: если путем ее совершенствования удается увеличить мощность паровой турбины на 1 %, то КПД ТЭС возрастет также на 1 %; если же на той же ТЭС сэкономить 1 % топлива в котле, то ее КПД возрастет только на 0,4 %, так как КПД преобразования теплоты в работу находится на уровне 40 %.
Совершенствование турбины — это самый универсальный способ повышения экономичности ТЭС: он всегда дает эффект вне зависимости от параметров пара, тепловой схемы, условий эксплуатации и т.д.
Наибольшие потери возникают при течении пара в сопловых и рабочих решетках, особенно в ЦВД и ЦНД, где оно носит явно выраженный пространственный характер и точный расчет которого затруднителен.
|
|
Вторыми по значению являются так называемые потери с выходной скоростью. Объем пара, покидающего ЦНД огромен (напомним, что при давлении за последней ступенью 4 кПа объем, занимаемый 1 кг пара, составляет 29 м3), а площадь для выхода пара из каналов рабочих лопаток последней ступени ограничена их прочностью. Поэтому средняя скорость пара, покидающего ступень, может превышать 300 м/с, энергия этого пара не используется для выработки мощности и поэтому теряется.
Третьими по значению являются паразитные протечки пара мимо сопловых и рабочих решеток (рис. 10.2): периферийная, корневая (у корня рабочих лопаток), диафрагменная. Пар протечек не поступает на рабочие лопатки ступени и потому не производит работы.
Аэродинамическое совершенствование турбин за рубежом в последние 20 лет было связано, прежде всего, с практическим внедрением в реальные конструкции предложений, большинство из которых сделано еще советскими учеными 30—35 лет назад, к которым отечественное турбостроение в силу объективных причин оказалось невосприимчивым.
Отметим наиболее важные разработки.
Саблевидные сопловые лопатки. Традиционно сопловые лопатки выполняют прямыми (см.рис. 6.3) и устанавливают их радиально. Связано это с простотой изготовления диафрагм.
|
|
Саблевидными лопатками называются изогнутые лопатки, напоминающие по внешнему виду саблю (в зарубежной литературе используются термины «банановая» и «трехмерная»). Пока саблевидные лопатки используют только для сопловых решеток.
Сопловые саблевидные лопатки устанавливают вполне определенно: корневые сечения наклоняют в окружном направлении в сторону вращения рабочего колеса, а периферийные, наоборот, навстречу вращению. Общий вид диафрагм с саблевидными лопатками показан на рис. 10.3.
Саблевидные сопловые лопатки впервые предложены в 1962 г. в России (кафедра паровых и газовых турбин МЭИ) профессором М.Е. Дейчем и ныне академиком РАН Г.А. Филипповым, а впервые использованы в мощных турбинах фирмой Siemens в середине 80-х годов прошлого столетия. Сейчас их используют все ведущие мировые производители турбин, кроме России.
По разным оценкам повышение экономичности ступени при использовании саблевидных лопаток составляет 1,5—2,5 % (относительных). Поэтому наиболее эффективно их применение для последних ступеней ЦНД мощных паровых турбин, поскольку мощность этих ступеней составляет примерно 10 МВт для турбин ТЭС и 20 МВт для турбин АЭС, а суммарное число таких ступеней в турбине 6—8. Если все ступени ЦНД выполнить с саблевидными сопловыми лопатками, то КПД ЦНД возрастет на 1,5—2,5 %, что с учетом доли выработки мощности в ЦНД даст выигрыш в экономичности всей турбины в 0,5—0,8 %. Выигрыш при использова нии саблевидных лопаток возникает вследствие того, что уменьшается доля пара, протекающего через корневую и периферийную зону ступени, где обтекание ступеней хуже (рис. 10.4).
Фирма Siemens использует аналогичные «трехмерные» лопатки для ЦВД и ЦСД (рис. 10.5), где лопатки имеют малую длину, но зато относительно большую зону высоких потерь в корневой и периферийных зонах. Для создания таких лопаток фирма выполнила обширное компьютерное моделирование облопачивания, испытала его в четырехступенчатой паровой экспериментальной турбине, после чего оно стало основным для мощных паровых турбин. По оценкам фирмы Siemens использование пространственных лопаток в ЦВД и ЦСД позволяет увеличить их КПД на 1—2 % по сравнению с цилиндрами, созданными в 80-е годы прошлого века.
На рис. 10.6 показано три последовательных модификации рабочих лопаток для ЦВД и первых ступеней ЦНД паровых турбин для АЭС фирмы GEC-Alsthom: обычная («радиальная») лопатка постоянного профиля (рис. 10.6, а), используемая в наших турбинах; саблевидная лопатка (рис. 10.6,б) и, наконец, новая лопатка с прямой радиальной выходной кромкой (рис. 10.6, в). Новая лопатка обеспечивает КПД на 2 % больший, чем исходная (рис. 10.6, а).
Меридиональное профилирование. Первые ступени паровых турбин, особенно на сверхкритические параметры пара имеют очень малую высоту сопловых и рабочих лопаток. Для повышения КПД таких решеток еще в 60-е года XX в. кафедра паровых и газовых турбин МЭИ предложила так называемое меридиональное профилирование сопловых каналов, при котором (рис. 10.7) верхний (меридиональный) обвод канала выполняется не цилиндрическим или коническим, а суживающимся.
Меридиональное профилирование впервые исследовано в МЭИ, и раз личные типы решеток испытаны в экспериментальной турбине. Для малых высот решеток (менее 25 мм) меридиональное профилирование дает относительное повышение КПД ступени более 2 %, а для высоты 10 мм относительное повышение КПД составляет около 3 %. Промышленное применение меридионального профилирования осуществлено в 90-х годах фирмами Toshiba и General Electric (рис. 10.7). Для реализации меридионального профилирования требуется технология изготовления сопловых решеток с фигурным (нецилиндрическим и неконическим) периферийным обводом.
Увеличение кольцевой площади выхода пара из турбины. Эта мера приводит к уменьшению потерь с выходной скоростью, пропорциональных квадрату площади выхода. Максимальную площадь выхода в 11,3 м2 имеет турбина ЛМЗ К-1200-240, рабочая лопатка последней ступени которой имеет длину 1,2 м при среднем диаметре 3 м. Эта титановая лопатка создана более 20 лет назад и долгое время она была мировым рекордсменом. Несколько лет назад фирма Siemens создала новую лопатку (рис. 10.8) с площадью выхода 12,5 м2 (при длине 1143 мм). Лопатка выполнена из высокопрочной стали с содержанием хрома в 16 % (напомним, что стальная лопатка с 12 % хрома турбин мощностью 300—800 МВт ЛМЗ имеет длину 0,96 м и площадь выхода 7,48 м2).
Очень характерным примером целесообразности использования более длиной лопатки последней ступени и перехода на саблевидные лопатки, может служить модернизация турбины пылеугольного энергоблока ТЭС Enstedvarker (Дания), которая позволила увеличить его мощность с 630 до 660 МВт, т.е. уменьшить удельный расход тепла на 4,6 %, что эквивалентно экономии 60 тыс. т угля в год с соответствующим уменьшением вредных выбросов в окружающую среду.
Увеличение длины рабочих лопаток последних ступеней — одна из типичных мер поддержания экономичности морально стареющих турбин. К сожалению, подобные меры для наших турбин не реализованы, хотя имеются полноценные разработки, например для турбин мощностью 200 МВт.
Применение периферийных разношаговых многоступенчатых уплотнений в ЦВД и ЦСД. Разношаговые многогребенчатые уплотнения впервые, по-видимому, были применены фирмой Siemens с числом гребешков 12 на роторе и 9 на статоре (рис. 10.9).
Турбины фирмы Siemens имеют в ЧВД и ЧСД так называемое реак тивное облопачивание, и для него разношаговые многогребенчатые уплотнения используются на периферии рабочих лопаток и между направляющими аппаратами и ротором. В наших турбинах периферийные уплотнения ступеней, через которые проходит основная протечка, имеют всего несколько гребней.
Многогребенчатые периферийные уплотнения с числом гребней 9 применяет для активных турбин японская фирма Toshiba.
Известна разработка реактивного ЦВД для турбины К-300-240, выполненная ЛМЗ, в которой предлагается использовать многогребенчатые уплотнения.
По сравнению с традиционными уплотнениями, применяемыми в ЦВД и ЦСД отечественными производителями турбин, многогребенчатые уплотнения имеют следующие особенности.
Существенно большее число гребней: 8—12 по сравнению с традиционными двумя, иногда тремя гребнями. При прочих равных условиях это дает снижение потерь от протечки более чем в 2 раза.
Возможность выполнить примерно вдвое меньший радиальный зазор, что обусловлено наличием гарантированного зазора между гребнями ротора и статора и отсутствием опасности задевания между гребнями. Это дает снижение утечек еще примерно в 2 раза. Таким образом, примене ние многогребенчатых надбандажных уплотнений позволяет сократить утечки пара через периферийные зазоры в 4—5 раза, что дает существенный выигрыш в относительном внутреннем КПД ступени, зависящий от ее параметров. Например, для первых ступеней ЦВД турбины К-300-240 ЛМЗ утечка через периферийные уплотнения при традиционных двухгребешковых уплотнениях составляет примерно 3 %. Уменьшение утечки в 4—5 раз дает увеличение КПД ступени на 2—2, 5 %.
Отсутствие опасности задеваний как при радиальном, так и осевом относительном смещении ротора и статора, т.е. новые уплотнения отлича ются высокой степенью сохранности в условиях эксплуатации, что приводит к увеличению средней экономичности турбоустановки в период между ремонтами.
Новые уплотнения наряду с малыми утечками снижают опасность возникновения так называемых самовозбуждающихся колебаний ротора турбины.
Новые уплотнения могут быть применены практически во всех турбинах в качестве надбандажных уплотнений не только для новых турбин, но и при реконструкциях и ремонтах.
Применение регулируемых диафрагменных уплотнений в ЧВД и ЧСД. Диафрагменные уплотнения турбин российских производителей турбин выполняются с плоскими окружными пружинами (см. рис. 6.8), прижимающими сегменты уплотнения к валу с фиксацией малых радиальных зазоров. При пусках и остановках турбины, когда возникает повышенная вибрация вала, могут возникать задевания гребней о ротор с их износом и появлением значительных протечек пара. По опыту General Electric на турбине 500 МВт с совмещенным ПВСД при номинальном радиальном зазоре в уплотнениях 0,38 мм после 5 лет эксплуатации зазор увеличился до 1,52 мм, что привело к снижению экономичности турбины на 0,35 %.
В последние годы ряд фирм, в частности General Electric и Toshiba, используют так называемые регулируемые уплотнения.
Идея регулируемых уплотнений (рис. 10.10) состоит в том, что при пуске турбины сегменты уплотнений в диафрагмах отжимаются пружинами таким образом, что образуются большие радиальные зазоры и это обеспечивает отсутствие задеваний при пуске. После синхронизации турбины в полость пазов под сегменты уплотнений подается пар повышенного давления (большего, чем давление в проточной части уплотнений) и этим давлением сегменты уплотнений отжимаются к центру вала, и зазоры уменьшаются до номинального значения. Таким образом обеспечивается сохранность уплотнений при переходных режимах и малые зазоры, а следовательно, малые протечки.
Уплотнения устанавливаются на участках вблизи середины пролета ротора, где смещение максимальные. Окупаемость затрат при замене старых на более сложные новые уплотнения по данным фирмы составляет период менее 1 года.
Для условий России применение таких уплотнений наиболее целесообразно на турбинах мощностью 300—800 МВт производства ЛМЗ.
Рассмотренные способы усовершенствования элементов отечественных паровых турбин могут быть реализованы без существенного изменения традиционной технологии, освоенной на российских предприятиях-производителях паровых турбин, и не требуют применения новых неосвоенных материалов.
При таком комплексном усовершенствовании общее повышение экономичности, по существу, получается суммированием экономических эффектов от отдельных рассмотренных мер. Оценка показывает, что существующие меры совершенствования ЦНД могут дать суммарное снижение удельного расхода тепла турбоустановкой более чем на 3 %.
Таблица 10.1 Способ повышения КПД турбины | Экономия топлива, % |
Проектирование проточной части с использованием трехмерной методики расчета | 0,75 |
Использование улучшенных дозвуковых и трансзвуковых турбинных решеток | 1,23 |
Оптимизация периферийного обвода сопловых и рабочих решеток | 0,80 |
Увеличение числа гребней в уплотнениях ступеней | 0,50 |
Использование регулируемых зазоров в уплотнениях | 0,35 |
Организация направленных корневых межвенцовых протечек в ступенях дисковой конструкции | 0,60 |
Использование закрученных сопловых и рабочих лопаток с переменным углом по вращению (трехмерные лопатки) | 0,85 |
Оптимизация последней ступени ЦНД | 0,15 |
Использование новых клапанных систем | 0,20 |
Совершенствование внутреннего тракта турбины (входных, выходных диффузоров, переходных патрубков и т.д.) | 0,22 |
Использование совершенных систем влагоудаления | 0,05 |
Оптимизация регулирующей ступени | 0,40 |
Всего | 6,10 |
В табл. 10.1 приведены примерные значения экономии топлива в ПТУ при использовании различных способов повышения КПД турбины. Видно, что эта экономия может достигать 6 %, хотя на практике эти мероприятия в полной мере по разным причинам не реализованы ни в одной турбине западного и отечественного изготовления.
СПЭ лекция 2
Переход к суперсверхкритическим параметрам пара
История развития энергетики — это история повышения параметров пара. С начала 60-х годов XX в. в СССР начался быстрый переход от докритических параметров (13 МПа, 540 °С/540 °С) к сверхкритическим (СКД — 24 МПа, 540 °С /540 °С), и к концу 80-х годов энергетика СССР имела опыт освоения и использования энергоблоков СКД больший, чем какая-либо страна. Переход к энергоблокам СКД происходил в упорной борьбе мнений: и тогда, и даже сейчас имеются убежденные противники энергоблоков СКД, хотя опыт энергетики всего мира показал целесообразность их использования. В настоящее время мировая теплоэнергетика уже сделала реальные шаги к массовому переходу к энергоблокам супер-сверхкритических параметров (ССКП): 30 МПа, 600 °С, а затем 35 МПа, 650 °С. В зарубежной печати имеются сообщения о работе над энергоблоком на начальную температуру 720 °С. Как это принято в последних зарубежных публикациях, под ССКП будем понимать параметры, соответствующие давлению более 24 МПа и/или температуре более 565 °С.
Целесообразность постепенного перехода к энергоблокам ССКП в России в настоящее время обусловлено следующими обстоятельствами.
1. Повышение параметров пара — это один из наиболее эффективных способов повышения КПД ТЭС. Для условий России, где климатические условия позволяют иметь глубокий вакуум в конденсаторе, главными мерами являются повышение параметров пара и введение второго промперегрева. Необходимо также подчеркнуть, что повышение параметров дает эффект независимо от типа используемого топлива. Это подтверждает как опыт и намечаемые перспективы американской и датской энергетики, ставящей перед собой создание высокоэкономичных пылеугольных энергоблоков, так и Японии, где повышение параметров происходит и на энергоблоках, работающих на сжиженном газе.
2. Переход к ССКП дает значительный эффект не только в традиционных технологиях сжигания топлива, но и во всех комбинированных парогазовых технологиях с развитой паротурбинной частью: уже сейчас за рубежом ведутся работы по использованию в паротурбинной части утилизационных ПГУ пара СКД и ССКП, они с успехом могут использоваться в ПГУ со сбросом газов ГТУ в котел, с вытеснением паровой регенерации, с использованием газификации в кипящем слое под давлением и низкотемпературной ГТУ и т.д.
3. Повышение параметров пара и, как следствие, уменьшение тепловых выбросов — главный путь решения глобальной экологической проблемы потепления климата.
4. Повышение начальных параметров при традиционном способе сжигания — это наиболее простой и действенный способ вовлечения в энергетику наименее «благородного» топлива — твердого, запасов которого хватит на сотни лет. Нет сомнения в том, что твердое топливо будет в перспективе вытеснять жидкое и газообразное.
К сожалению, российская энергетика в части освоения ССКП существенным образом отстает от энергетики развитых стран. Если оставить в стороне кризисные явления в стране, которые не могут не затронуть энергетику, то повышение параметров сдерживается целым рядом обстоятельств.
Основным энергетическим топливом в России является природный газ, который наиболее целесообразно использовать в ПГУ с котлом-утилизатором. Уже сегодня работающие ПГУ этого типа имеют КПД, превышающий 58 %. Конечно, внедрение аналогичных установок в энергетику России было бы самым оптимальным. Однако отсутствие в России налаженного производства современных высокотемпературных ГТУ мощностью 150—200 МВт не позволяет надеяться на массовое внедрение ПГУ даже в ближайшее десятилетие. Еще длительное время в России будут вводиться традиционные энергоблоки на газе, повышение экономичности которых очень важно. Вместе с тем в современных ПГУ уровень температуры за газовой турбиной уже достиг 580 °С, и начальные параметры ПТУ ПГУ уже таковы (11 МПа, 540 °С/540 °С), что целесообразно перейти к повышенным температурам пара даже в ПГУ утилизационного типа.
Использование твердого топлива на ТЭС в России сегодня ограничено, его запасы сосредоточены в основном в восточных регионах, где он сравнительно дешев. Эти обстоятельства порождают вполне обоснованные сомнения в наличии сегодня в России «ниши» для энергоблоков ССКП. К этому следует добавить, что в качестве конкурентов традиционному сжиганию твердого топлива выступают и другие способы сжигания — внутри-цикловая газификация и сжигание вциркулирующем кипящем слое при атмосферном давлении или под давлением.
Парогазовые установки с внутрицикловой газификацией твердого топлива наиболее целесообразны для каменного угля. Существует, по крайней мере, пять различных вариантов технологий газификации, а имеющиеся установки являются демонстрационными.
ПГУ с газификатором с кипящим слоем под давлением и ГТУ, питаемой продуктами сгорания газификатора, при традиционных параметрах ПТУ (даже СКД) в принципе не может обладать высокой экономичностью из-за малой степени бинарности и низкого КПД ГТУ из-за малой начальной температуры перед газовой турбиной. Он оценивается примерно в 40—43 %.
Из-за нестабильности цен в сегодняшней России выполнить полноценное технико-экономическое обоснование строительства энергоблока ССКП не представляется возможным. Однако и без расчетов ясно, что доля твердого топлива будет увеличиваться за счет вытеснения жидкого топлива, дефицит газа будет расти и как следствие твердое топливо будет дорожать и переход к ССКП станет экономически целесообразным даже в условиях России.
Интерес к повышению начальных параметров существовал всегда. Он увеличивался всякий раз с ростом цен на топливо и появлением новых, более жаропрочных материалов и снижался с появлением новых более дешевых видов топлива, например ядерного. Не претендуя на полноту обзора освоения ССКП, поскольку число работ на эту тему, по-видимому, превышает несколько сотен, отметим главные вехи.
История освоения ССКП насчитывает уже почти 40 лет. Она началась с создания в США энергоблока Эддистоун-1 мощностью 325 МВт на параметры 35,9 МПа, 648 °С /565 °С /565 °С.
В 1966 г. на Каширской ГРЭС началась опытно-промышленная экс плуатация паровой турбины СКР-100-300, построенной ХТЗ на начальные параметры 29,4 МПа, 650 °С с противодавлением 3,03 МПа. В течение ряда лет отечественная теплоэнергетика получала уникальный опыт работы на ССКП. На протяжении 1967—1971 гг. было проведено 60 кампаний работы энергоблока, причем максимальная длительность непрерывной работы составила 50 сут. Была проверена эксплуатационная надежность основных узлов, выполненных из различных сталей аустенитного класса, исследованы их температурные режимы. Среди многих оригинальных технических решений, разработанных для турбины СКР-100-300, следует выделить систему охлаждения ротора и статора, разработка которой представляет серьезную проблему и сегодня.
Эксплуатация турбоагрегатов на ССКП, построенных в 50—60-е годы XX в., внесла серьезный научно-технический вклад в развитие мировой теплоэнергетики. Некоторые агрегаты уже выработали свой ресурс и выведены из эксплуатации, но другие продолжают работать. В частности, энергоблок Эддистоун-1 с несколько пониженными относительно проектных значениями начальных параметров (33,62 МПа, 609 °С) планируется эксплуатировать даже в начале нашего столетия, когда срок его службы превысит 40 лет.
В 1978 г. Научно-технический совет Минэнергомаша СССР, обобщив результаты работы энергоблока с турбиной СКР-100 на Каширской ГРЭС, сделал уверенный вывод о технической возможности создания надежных и высокоэффективных паровых котлов и турбин для энергоблоков мощностью 800 МВт и более на начальные параметры 30 МПа, 650 °С. Было выполнено расчетное обоснование и эскизное проектирование котла паропроизводительностью 2400 т/ч на кузнецком угле и турбины типа К-800-30-650 с промежуточным перегревом до 565 °С. С учетом ряда дополнительных усовершенствований энергоблок К-800-30-650 должен был дать экономию до 130 тыс. т условного топлива в год по сравнению с типовым энергоблоком К-800-23,5.
В 1986 г. японская фирма Mitsubishi на электростанции Вакамацу начала эксплуатацию паровой турбины с противодавлением мощностью 50 МВт с температурой свежего пара и пара промперегрева 593 °С. На этом агрегате фирма вела исследования надежности узлов, работающих при высоких температурах. Результаты исследований использованы при разработке турбоагрегата мощностью 700 МВт на начальные параметры 24,6 МПа, 538 °С/593 °С для энергоблока Хекинен-3, введенного в эксплуатацию в 1993 г.
Первым энергоблоком ССКП нового поколения по праву должен считаться энергоблок Кавагое-1 на параметры 30,5 МПа, 566 °С/566 °С/566 °С. Пробный пуск и синхронизация осуществлены в конце декабря 1988 г., номинальная нагрузка при номинальных параметрах пара достигнута 3 февраля 1989 г., а с 30 июня 1989 г., после проведения необходимых испытаний, началась промышленная эксплуатация энергоблока.
В июне 1992г. введен энергоблок Кавагое-2, аналогичный Кавагое-1. В июле 1992 г. был испытан, а в апреле 1993 г. принят в коммерческую эксплуатацию энергоблок Хекинен-3 (Япония) мощностью 700 МВт на параметры пара 25 МПа, 538 °С/593 °С. При разработке турбины использованы все последние достижения в области материалов, аэродинамики и технологии, а также исследований систем охлаждения на энергоблоке Вакамацу.
В Европе и в Японии введены новые энергоблоки ССКП: в 1997— 1998 гг. два энергоблока на ТЭС Конвой (Дания) мощностью 400 МВт на параметры 29 МПа, 582 °С/580 °С/580 °С, в 1995 г. на ТЭС Любек (Германия) на параметры 27,5 МПа, 580 °С/600 °С, в 1997 г. на ТЭС Матсуура на параметры 25,6 МПа, 593 °С/593 °С/593 °С.
В настоящее время практически все ведущие турбостроительные фирмы создают паровые турбины ССКП нового поколения.
Целесообразность перехода к ССКП необходимо оценивать по многим факторам: экономичности, капиталовложениям, экологичности, эксплуатационным затратам, маневренности, экономичности на частичных нагрузках и т.д., причем все оценки необходимо делать в сравнении с альтернативными установками, например, ПГУ с внутрицикловой газификацией, ПГУ с циркулирующим кипящим слоем, а когда используется природный газ — и с утилизационными ПГУ.
Эффект от повышения параметров пара приведен в десятках работ. Остановимся на данных, где этот эффект представлен в наиболее наглядной форме (рис. 10.11). Видно, что в рамках температур, давно освоенных в Японии (566 °С), при переходе от 24,1 до 31 МПа и при введении второго перегрева можно суммарно сэкономить более 4 % топлива по сравнению с параметрами 24,1 МПа, 538 °С/566 °С, причем эффект будет таким же, если оставаться при начальном давлении 24,1 МПа, но поднять температуры перед цилиндрами до 593 °С. Освоенные материалы и имеющийся опыт эксплуатации позволяют уже сегодня перейти к температурам 593 °С, повысив КПД еще на 1,5 %.
Эти расчетные данные полностью подтверждены испытаниями и опытом эксплуатации энергоблоков Кавагое-1 и Кавагое-2, на которых получена экономия топлива в 5 % по сравнению с обычными энергоблоками СКД на 24 МПа, 538 °С/566 °С.
Сопоставление энергоблоков на ССКП с другими технологиями приведено в табл. 10.2.
Таблица 10.2 Показатель | Энергоблок ССКП1 | ПГУ с внутрицикловой газификацией2 | ПГУ с кипящим слоем3 |
Мощность нетто, МВт | 385 | 417 | 460 |
Начальная температура перед газовой турбиной, °С | — | 1260 | 870 |
Параметры пара, МПа/°С: |
| ||
свежий пар | 29/582 | 12,5/510 | 29/580 |
первый промежуточный перегрев | 80/580 | 29/510 | 94/580 |
второй промежуточный перегрев | 23/580 | — | 29/580 |
Температура, °С: |
| ||
питательной воды | 298 | 133 | 315 |
уходящих газов | 105 | 80 | 105 |
Мощность собственных нужд, МВт | 30 | 65 | 22 |
КПД ПТУ нетто, % | 47,0 | 47,3 | 48,0 |
Стоимость электроэнергии, % | 100 | 120—125 | 107 |
Капитальные вложения, % | 100 | 160—170 | 145 |
Годовые эксплуатационные издержки при работе 5500 ч/год | 100 | 105 | 111 |
Выбросы: |
| ||
SO2, Мг/МДж | менее 70 | менее 22 | менее 70 |
NO2 Мг/МДж | менее 70 | менее 62 | менее 70 |
твердые частицы, мг/м3 | менее 25 | менее 1 | менее 5 |
Характерно, что ПГУ с кипящим слоем предусматривает использование в паротурбинной части ССКП и, по-видимому, только при этих условиях она может быть конкурентоспособна по отношению к другим установкам. Из табл. 10.2 также видно, что по экономичности, эксплуатационным издержкам и стоимости электроэнергии все три типа установок примерно равноценны, особенно с учетом точности выполнения расчетов. При этом, конечно, подразумевается, что нет никаких проблем с созданием и производством высокотемпературных ГТУ, что, как указывалось выше, является весьма серьезной проблемой для энергомашиностроения России. Капиталовложения в ПГУ с внутрицикловой газификацией и ПГУ с кипящим слоем в 1,5 раза выше, чем в энергоблоки ССКП, и это обстоятельство, с учетом отсутствия производства высокотемпературных ГТУ в России делает весьма целесообразным освоение ССКП в нашей стране.
Одним из основных требований к оборудованию ССКП является сохранение таких эксплуатационных показателей, как надежность, экономичность на частичных режимах, маневренность на уровне не худшем, чем у энергоблоков СКД. Известно, что противники создания энергобло ков СКД в качестве аргумента в первую очередь выдвигали невозможность обеспечить именно эти эксплуатационные характеристики. Однако опыт освоения энергоблоков СКД показал, что при нормальной эксплуатации они не уступают энергоблокам докритического давления. К сожалению, работа энергоблоков ССКП (Эддистоун-1, СКР-100) в первое время сопровождалась появлением трещин в паровпускных элементах, выполненных из аустенитных сталей, вследствие как их неблагоприятных физико-механических характеристик, так и несовершенства методов расчета долговечности с учетом переходных режимов, и неотработанностью режимов пуска.
К энергоблоку Кавагое-1 уже при проектировании предъявлялись по маневренности требования такие же, как и к другим энергоблокам Японии, в частности, ежедневные пуски с учетом большой и возрастающей из года в год неравномерности графика нагрузки. Удовлетворение требований к маневренности энергоблоков ССКП не должно вызывать каких-либо особых проблем.
Возможность обеспечения надежной эксплуатации энергоблоков ССКП подтверждается 13-летним опытом работы энергоблока Кавагое-1. Почти все возникшие неполадки оборудования могли появиться и на обычном энергоблоке СКД.
Определенные резервы повышения экономичности содержатся в снижении конечного давления — давления за турбиной. Уменьшение конечного давления на 1 кПа увеличивает КПД турбоустановок ТЭС примерно на 1 %. Однако с учетом того, что типичное расчетное давление в конденсаторах КЭС составляет 3—5 кПа, становится ясным, что обеспечить снижение давления на 1 кПа — это довольно сложная задача, связанная с необходимостью увеличения и без того огромной поверхности конденсации конденсатора, увеличения расхода дефицитной охлаждающей воды и, в конечном счете — к существенному росту капитальных вложений, которые могут иметь длительный срок окупаемости.
Последний значимый фактор, определяющий экономичность, это температура питательной воды. В теории тепловых циклов показано, что для каждой турбоустановки существует некоторая термодинамически оптимальная температура питательной воды, при которой ее КПД достигает максимального значения. При проектировании турбоустановки фактическую температуру питательной воды принимают меньше термодинамически оптимальной. Это позволяет уменьшить капиталовложения в систему регенерации, но уменьшает ее эффективность.
В табл. 10.3 приведены данные по возможной экономии удельного расхода тепловой энергии турбоустановкой при совершенствовании параметров ее термодинамического цикла.
Таблица 10.3 Мероприятие | Относительное повышение КПД |
Повышение температуры свежего пара | 0,02 % /1 °С |
Повышение давления свежего пара | 0,1%/1МПа |
Повышение температуры промежуточного перегрева | 0,015 %/1 °С |
Использование второго промежуточного перегрева пара | 1,2 % |
Снижение давления в конденсаторе | 1 % /1 кПа |
Повышение температуры питательной воды | 0,02 % /1 °С |
Таблица 10.3 позволяет сразу же сделать несколько важных оценок.
Как отмечалось выше, в начале 70-х годов прошлого века на энергоблоках СКД температура свежего пара и промежуточного перегрева была снижена с 565 до 540 °С, что привело к потере экономичности турбоустановки только по этой причине на значение
![]() |
|
т.е. почти на 1 %. Если оценить количество топлива, дополнительно использованного в топках котлов энергоблоков (а это примерно 3 г условного топлива на каждый 1 кВт·ч выработанной электроэнергии при примерной ежегодной выработке в 300 млрд кВт·ч в течение 30 лет), то его стоимость многократно перекроет затраты на решение проблемы возврата энергоблоков России к параметрам, освоенным 30 лет назад.
Вторая интересная оценка — это экономия топлива при переходе на ССКП. Если с параметров 24 МПа, 540 °С/540 °С перейти на параметры пара 30 МПа, 600 °С/600 °С и повысить температуру питательной воды с 275 до 300 °С, то экономия тепловой энергии составит
![]() |
|
Если при этом использовать еще и второй промежуточный перегрев пара, то экономия тепловой энергии составит 4,4 %.
Подчеркнем, что в этих оценках не учитывается потенциал повышения экономичности, связанный с совершенствованием турбины (см. § 10.3), котла и тепловой схемы.
Дата добавления: 2018-04-04; просмотров: 1659; Мы поможем в написании вашей работы! |
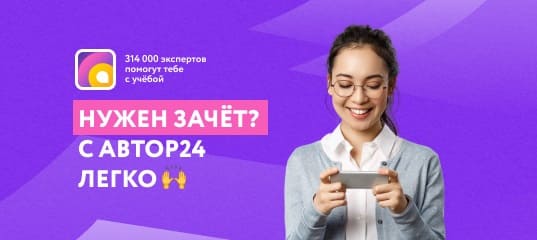
Мы поможем в написании ваших работ!