Прогрссивные способы изготовления отливок
евозможно расширять объем производства металлов беспредельно, потребности которого все возрастают. Это кроме огромных капиталовложений, еще ведет к истощению недр и загрязнение биосреды. Это все приводит к тому, что необходима разработка процессов металлообработки и машиностроительной конструкции, которые позволили бы резко сократить расход металла.
1.Применение прогрессивных методов формообразования металла, т.е расширение производства прогрессивных заготовок, т.е таких, размеры и форма которых максимально приближены к размерам детали ( изделия), увеличение доли точных отливок, заготовок полученных прокаткой на специальных станках взамен штамповки, точных поковок и тд. Известно, что около 70% отливок (по массе) получают литьем в песчанно-глинистые формы.
При этом способе отливки имеют рыхлости, пустоты, включения, раковины и большой разброс величин основных параметров. Кроме этого изготовление модели и стержни – ручной труд, модель можно использовать 500 раз. На каждую тонну отливок необходимо до 12 тонн песка и глины.
Применение литья в оболочковые формы. Оболочки в 15-20 раз прочнее, 8-10 раз снижается расход формовочной смеси на тонну литья. Отливки получаются очень точными , с чистой поверхностью, припуски на механическую обработка уменьшаются вдвое.
Благодаря разработке промышленного метода получения этилсиликата, исходного материала для связующих растворов, склеивающих огнеупорную пыль в прочные литейные оболочковые формы.
|
|
А) литье в оболочковые формы по выплавляемым моделям.
Б) литье в кокили ( металл литейной формы ).
В) литье под давлением ( малые детали групп ).
Г) центробежное литье.
Однако наряду с достижениями необходимо отметить ряд недостатков. До сих пор при конструировании деталей машин не учитываются специфические требования технологических процессов, автоматизации: детали часто нетехнологичны и ориентированны на традиционное изготовление, в том числе на обработку резанием. Недостаточен выпуск специального оборудования, удовлетворяющего требованиям современной технологии, автоматизации, эргономики и экономики.
Путь к малоотходному и безотходному производству лежит через существенное сокращение производственного цикла изготовления деталей – точные заготовки.
Порошковая металлургия – один из наиболее рациональных путей экономии металла, мало операционной технологии. Статистические данные показывают, что перевод 1т деталей на изготовление методом компактирования порошка экономит 2,5т проката, а с учетом металлургического передела – 2,9т стали. Кроме того спеченные детали обеспечивают больший срок службы , чем детали из проката или литья.
|
|
Например, стойкость инструмента из порошковой быстрорежущей стали в 5-6 раз выше.
Перспективы в изготовлении биметаллических и многослойных изделий (сталь- медь ).
Преимущества очевидны, однако объем производства по сравнению с прокатом мал. Трудности - малый объем получения качественных порошков, сложность оборудования и оснастки для компактирования.
Одно из направлений повышения эксплуатационной надежности и стойкости деталей машин и инструмента – создание на их поверхности износостойких покрытий.( метод карбонатриации ).
Метод диффузионного борирования ( 100 – 150 мкм).
Нанесение на рабочей поверхность карбидных, карбомитридных и нитридных покрытий жест костным методом, диффузионным насыщением из порошков и паст, химическим и физическим осаждением из газовой фазы позволяет получать покрытия с высокой твердостью и износостойкостью,
Особенности получения отливок из чугуна,стали,цветных металлов и сплавов.
Кристаллизация и структурообразование чугуна. Чугун представ- ляет собой сплав железа с углеродом, которого он содержит в пределах от 2,6
до 4,5 %. В чугуне всегда имеются примеси: 0,5–3,5 % Si; 0,3–1,5 % Mn; до 1,0
|
|
% Р и до 0,15 % S. Для улучшения качества чугуна в него могут вводиться легирующие примеси (Ni, Cr, Сu, Mo и др.) – от десятых долей процента до 15–
20 % в специальных чугунах.
Наиболее важный этап кристаллизации чугуна – эвтектическое пре- вращение, при котором происходит распад жидкости на аустенит и высоко- углеродистую фазу. Последняя и определяет структуру чугуна. Он будет бе-
лым, если высокоуглеродистой фазой является цементит, или серым, если высокоуглеродистой фазой является графит. В половинчатом чугуне наряду с графитом находится цементит.
Влияние химического состава на литейные и механические свой- ства чугуна. Углерод и кремний – графитизирующие элементы. Для боль- шинства отливок применяют чугуны с содержанием углерода от 2,7 до 3,6 %. Чем больше содержание углерода, тем больше жидкотекучесть чугуна и ни- же температура плавления. С увеличением общего содержания углерода по- нижается механическая прочность чугуна, так как при этом увеличивается количество графита, снижающего прочность металлической фазы. Содержа- ние кремния обычно составляет не более 2,5 %. Марганец и сера – это эле- менты, тормозящие графитизацию. Увеличение содержания марганца спо- собствует повышению твердости чугуна и ухудшению обрабатываемости. При повышении содержания серы увеличивается усадка чугуна, снижается его жидкотекучесть, повышается хрупкость. Содержание серы обычно нахо- дится в пределах 0,1–0,12 %. Фосфор, подобно сере, уменьшает раствори- мость углерода в жидком чугуне. Повышение содержания фосфора увеличивает жидкотекучесть чугуна, но при этом возрастает хрупкость металла. Со держание фосфора не превышает 0,25 %, но в отливках для художественного литья и в тонкостенных отливках для предметов народного потребления с целью повышения жидкотекучести содержание фосфора увеличивают до 1,0– 1,5 %.
|
|
Легирующими элементами являются: никель – подобно кремнию гра- фитизатор, способствующий разложению цементита, содержание никеля в
серых чугунах составляет 0,3–0,4 %; хром – препятствует графитизации, уве- личивает твердость и устойчивость против износа, его обычно вводят в чугун вместе с никелем. При этом достигается измельчение графита и выравнива- ние твердости в тонких и толстых сечениях.
Влияние скорости охлаждения на свойства чугуна. Чем больше скорость охлаждения, тем больше углерода оказывается в связанном состоя- нии, в виде цементита, поэтому в тонкостенных отливках возможен отбел. В толстостенных отливках, которые охлаждаются медленнее, наоборот, боль- шая часть углерода выделяется в виде крупных пластинок графита, механи- ческие свойства таких отливок низкие.
Классификация и свойства отливок из чугуна. Отливки из серого чугуна с пластинчатым графитом используются главным образом в качестве деталей машин, определяющим для оценки качества чугуна для отливок этой
группы являются его механические свойства, регламентируемые ГОСТ 1412-85. Отливки малой или средней прочности изготавливают из чугунов марок СЧ 10, 15, 20 (условное обозначение марки включает буквы СЧ – серый чугун и цифровое обозначение величины минимального временного сопротивления при растяжении в МПа•10-1); отливки повышенной прочности – из низколе- гированных и модифицированных чугунов СЧ 25, 30, 35.
Отливки из чугуна с шаровидной формой графита делят в зависимо- сти от технологических методов получения структуры на отливки из ковкого чугуна и отливки из высокопрочного модифицированного чугуна. Отливки из ковкого чугуна имеют структуру (хлопьевидный графит), получаемую спе- циальным отжигом отливок, имеющих в литом состоянии структуру белого чугуна. Ковкий чугун в основном используется как конструкционный мате- риал, обладающий ценной комбинацией свойств прочности и пластичности (чугун назван «ковким» из-за способности пластически деформироваться в горячем состоянии, однако, практически такой обработке он не подвергает- ся). Ковкий чугун применяют для изготовления мелких, тонкостенных отли- вок для сельскохозяйственных машин и автомобилей. Согласно ГОСТ 1215- 79 (изменен в 1991 г.), отливки из ковкого чугуна маркируют двумя буквами КЧ, далее следуют две цифры – первая характеризует временное сопротивле- ние при растяжении, а вторая – относительное удлинение, %.
Отливки из высокопрочного модифицированного чугуна имеют шаро- видную форму графита в результате введения в жидкий чугун модификато- ров: Mg, Ca, Li, Na и др. Наибольшее применение получил магний, при со- держании которого 0,03–0,05 % графит кристаллизуется в чугуне в виде ша- ровидных включений (глобулей). Такой чугун называют магниевым. В отли- чие от КЧ получение шаровидной формы графита в ВЧ (высокопрочный чу- гун) практически не ограничивается толщиной стенки и массой отливки. Вы- сокопрочный чугун широко применяется для отливки деталей металлурги- ческого оборудования, к которым предъявляются специальные требования (например, жаропрочность). Согласно ГОСТ 7293-85 маркируют его буква- ми ВЧ, далее следует цифра, характеризующая временное сопротивление при растяжении.
В белом чугуне нет графита, весь углерод находится в виде цементита,
поэтому излом его не серый, что характерно для СЧ и ВЧ, а блестящий бе- лый. Белый чугун применяют как материал, обладающий высокой стойко- стью при абразивном износе и сухом трении (детали дробильного оборудо- вания – щеки дробилок, бронь шаровых мельниц, мелющие шары, лопатки шнеков, детали шламовых насосов). Вследствие повышенной хрупкости бе- лого чугуна и трудностей его механической обработки широко используют отливки, в которых отбеленный слой получают только на рабочей поверхно- сти (сердцевина из СЧ), например, прокатные валки, крановые колеса. Для осо- бо жестких условий эксплуатации применяют легированный белый чугун, на- пример, хромоникелевый чугун «нихард», содержащий до 5 % Ni и 2–2,5 % Cr.
Плавку чугуна осуществляют в вагранках (коксовых, коксогазовых, газовых), а также в электрических печах (индукционных и дуговых).
Дата добавления: 2018-04-04; просмотров: 906; Мы поможем в написании вашей работы! |
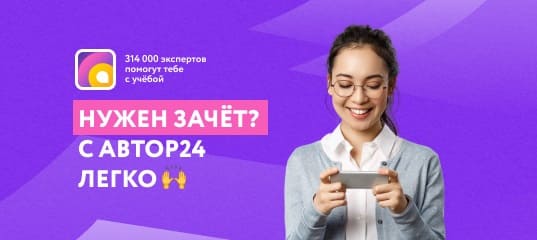
Мы поможем в написании ваших работ!