Образование аустенита при нагреве стали У8
При многих видах термической обработки сталь нагревают до температур, соответствующих существованию аустенита (процесс аустенитизации).
Образование аустенита при нагреве является диффузионным процессом и подчиняется основным положениям теории кристаллизации.
При нагреве эвтектоидной стали (0,8% С) несколько выше критической точки А1 (727 °С) перлит (феррито-карбидная структура) превращается в аустенит:
ФP + Fе3С → АS.
Превращение состоит из двух одновременно протекающих процессов: полиморфного α → γ-перехода и растворения в аустените цементита.
При нагреве доэвтектоидной стали выше точки А1 после превращения перлита в аустенит образуется двухфазная структура – аустенит и феррит.
При дальнейшем нагреве в интервале температур А1–А3феррит постепенно растворяется в аустените. При температуре А3 феррит исчезает, а концентрация углерода в аустените соответствует содержанию его в стали. Аналогично протекает превращение и в заэвтектоидной стали. При температуре несколько выше А1 (727 °С) перлит превращается в аустенит, содержащий 0,8 % С. В интервале температур А1–Асm происходит растворение избыточного цементита. Выше температуры Асm будет только аустенит, содержание углерода в котором соответствует его содержанию в стали.
Аустенит при температурах несколько выше Ас1 (727 °С) содержит ~ 0,8 % С. Зародыши аустенита образуются на границе раздела феррита и цементита (рис. 4.15, в), где наличие дефектов уменьшает работу образования зародыша аустенита. При росте зародыша когерентность α- и γ-решеток нарушается, сдвиговый механизм заменяется нормальным механизмом роста и зерна аустенита приобретают равноосную форму. Образовавшийся аустенит неоднороден по содержанию углерода. В участках, прилегающих к частицам цементита, концентрация углерода в аустените выше (точка бна рис. 4.15, а), чем в участках, прилегающих к ферриту (точка в на рис. 4.15, а).
|
|
Под влиянием этого градиента перепада концентрации происходит диффузия атомов углерода в аустените в направлении от границы с цементитом к участкам, граничащим с ферритом, что приводит к нарушению равновесия на межфазных поверхностях между аустенитом и указанными фазами. Восстановление равновесия достигается в результате дальнейшего растворения цементита в аустените и перехода атомов углерода в феррит, что облегчает превращение его в аустенит.
Мартенситное превращение при охлаждении аустенита.
При очень высоких степенях переохлаждения аустенита резко снижается диффузионная подвижность атомов. (В частности, у эвтектоидной стали она близка к нулю при температуре 240°С). При таких температурах g-железо превращается в a-железо, а весь растворенный в g-железе углерод не успевает покинуть раствор и перенасыщает a-железо. Перенасыщенный раствор углерода в a-железе называют мартенситом.
|
|
Мартенсит - неравновесная фаза. В равновесии a-железо растворяет максимум 0,006% углерода, а мартенсит может содержать углерода столько, сколько его было в исходном аустените. В результате этого решетка a-железа теряет кубичность и становится тетрагональной. Из-за этого появляются избыточные внутренние напряжения, и мартенсит оказывается очень твёрдой и хрупкой фазой.
Мартенситное превращение наблюдается при скоростях охлаждения аустенита выше критической (vкр). При таких скоростях охлаждения удаётся обойти зону перлитного превращения 3 и попасть в зону мартенситного превращения 5 (рис. 7.2.).
Мартенситное превращение начинается при температуре МН и заканчивается при температуре МК. Его особенностью является то, что оно идёт только при непрерывном охлаждении. Остановка в охлаждении приводит к стабилизации аустенита, и последующее охлаждение уже не приводит к его распаду. Превращение имеет бездиффузионный, сдвиговый характер. Поэтому кристаллическая решетка мартенсита оказывается строго ориентированной по отношению к решетке исходной фазы - аустенита. Превращение идёт с большой скоростью (≈1000 м/с). Зёрна мартенсита растут до пересечения с границами зёрен аустенита, а последующие его пластины вырастают под углом 60° или 120° к первоначальным.
|
|
7.5 Превращения при отпуске закалённых сталей
Структура стали после закалки является неравновесной. Она содержит метастабильную фазу – мартенсит, для которого характерна искажённая кристаллическая решётка и избыточные внутренние напряжения. При отпуске, предполагающем нагрев закалённых сталей, структура становится более равновесной.
Отпуск проводят при температурах ниже температур фазовых превращений. При нагреве закалённых сталей до температур порядка 200°С избыточный углерод частично выходит из мартенсита и образуются необособленные карбиды. В результате тетрагональность решётки мартенсита уменьшается и получается мартенсит отпуска. Он отличается меньшей твёрдостью и большей пластичностью. При температуре нагрева стали порядка 400°С избыточный углерод полностью покидает мартенсит и образует цементит. В результате формируется структура троостита отпуска (т.е. мелкозернистая смесь феррита с цементитом). При нагреве закалённых сталей до температур порядка 600°С наблюдается укрупнение (путём объединения) зёрен образующего цементита, в результате формируется структура сорбита отпуска. Сорбит и троостит отпуска отличаются от обычного пластинчатого сорбита и троостита зернистым строением. Такая структура обеспечивает сталям более высокую вязкость и пластичность.
|
|
Отжиг и нормализация стали.
Отжиг состоит в нагреве сталей до определённых температур с последующей выдержкой и медленным охлаждением их в печи. В результате отжига сталь приобретает равновесную структуру, свободную от остаточных напряжений.
Различают отжиг первого и второго рода. Отжиг первого рода не связан с фазовыми превращениями в сталях. В зависимости от назначения отжиг первого рода может быть либо диффузионным, либо рекристаллизационным, либо отжигом для снятия внутренних напряжений.
Диффузионный отжиг применяют для устранения неоднородности слитков стали по химическому составу. С этой целью образец нагревают до температур порядка 1000°С и выдерживают при данной температуре до тех пор, пока диффузионные процессы в образце не приведут к выравниваю химического состава слитка (т.е. к устранениюликвации).
Рекристаллизационный отжиг производят с целью устранения наклёпа в деформированных сталях. Как известно, в ходе холодной пластической деформации сталей развивается наклёп. Зёрна материала вытягиваются в направлении деформации, твёрдость и прочность стали возрастает, а её пластичность снижается. При нагреве деформированных сталей до температур рекристаллизации наблюдается процесс образования новых округлых зёрен взамен старых вытянутых зёрен. В ходе рекристаллизации твёрдость и прочность сталей уменьшается, а пластичность возрастает, приобретая значения, близкие к тем, которые были до деформации. Температуры, при которых наблюдается рекристаллизация сталей, превышают 400°С.
Отжиг для снятия внутренних напряжений применяется с целью устранения в сталях механических напряжений, возникших в результате обработки давлением, резанием, плавлением и так далее. Нагрев в данном случае осуществляется до относительно невысоких температур, не превышающих температур фазовых превращений. По термическому режиму данный отжиг похож на отпуск, но имеет иное назначение.
Отжиг второго рода, напротив связан с фазовыми превращениями в сталях, поэтому его называют также фазовой перекристаллизацией. Он может бытьполным и неполным. Полный отжиг заключается в нагреве стали до температур на 30-50°С выше линии GSE диаграммы состояния железоуглеродистых сплавов (рис. 7.3). Неполный – заключается в нагреве стали до температур на 30-50°С выше линии PSK. После медленного охлаждения с печью сталь при полном отжиге приобретает структуру мелкозернистой смеси феррита с цементитом. Полному отжигу обычно подвергают доэвтектоидные стали с целью измельчения зерен материала и улучшения его пластических свойств. Полный отжиг приводит к улучшению обрабатываемости доэвтектоидных сталей резанием, поэтому относится к подготовительным операциям. Неполному отжигу обычно подвергают инструментальные заэвтектоидные стали. В ходе такого отжига исчезает сетка вторичного цементита, который приобретает округлую зернистую форму. Это благоприятно отражается на механических свойствах сталей, в частности, повышается их ударная вязкость. Такую термическую операцию называют сфероидизирующим отжигом.
Закалка и отпуск стали.
После механической обработки изделие, как правило, подвергается упрочняющей термической обработке.
Наиболее распространенным видом упрочняющей термической обработки углеродистых сталей, содержащих углерода более 0,3 %, является закалка с последующим отпуском.
Закалка—процесс нагрева стали выше точки Ас3 (полная закалка) или Ас1, (неполная) на 30...50°С с последующим быстрым охлаждением. Цель закалки — получение высокой твердости и заданных физико-механических свойств. Способность стали принимать закалку возрастает с увеличением содержания в ней углерода. При содержании углерода менее 0,2 % сталь практически не закаливается.
На рис. 2.10 приведена диаграмма интервалов температур для закалки железоуглеродистых сталей.
Диаграмма интервалов закалочных температур
Доэвтектоидные стали подвергают полной закалке. После охлаждения закаленной детали в воде при комнатной температуре в структуре образуется мелкоигольчатый мартенсит и небольшое количество остаточного аустенита (1...2 %). Нагрев стали при закалке значительно выше критической точки Ас3, (на 150...200 °С) приводит к ее перегреву. В результате получается крупноигольчатый мартенсит, и сталь приобретает пониженную ударную вязкость.
Нагрев доэвтектоидной стали выше точки Ас1, но ниже точки Ас3, приводит к неполной закалке. В структуре такой стали наряду с мартенситом присутствуют участки феррита. Эта сталь имеет пониженную твердость.
На рис приведено схематическое изображение структурных превращений для доэвтектоидных сталей, имеющих место при полной закалке (а)—нагрев до температуры выше точки Ас3, и неполной закалке (б)—нагрев до температуры выше точки Ас1Если заэвтектоидную сталь нагреть выше точки Асm, то в структуре ее будет крупноигольчатый мартенсит с повышенным количеством остаточного аустенита, что приведет к снижению твердости стали. Поэтому все заэвтектоидные стали подвергают неполной закалке. Структура этих сталей состоит из мартенсита и цементита.
Скорость нагрева и время выдержки деталей зависят от размеров, массы деталей, их конфигурации, химического состава материала деталей, от типа нагревательных печей и нагревательных сред.
Дата добавления: 2018-04-04; просмотров: 2611; Мы поможем в написании вашей работы! |
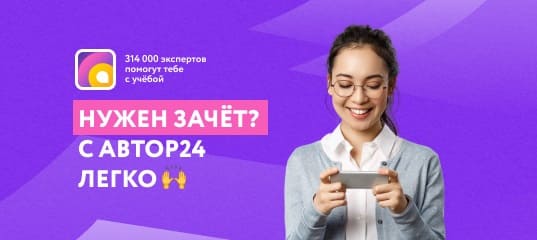
Мы поможем в написании ваших работ!