ОБОРУДОВАНИЕ, ПРИБОРЫ, МАТЕРИАЛЫ,
Министерство образования и науки Украины Севастопольский национальный технический университет
МЕТОДИЧЕСКИЕ УКАЗАНИЯ
К выполнению лабораторных работ № 9 - 12
По дисциплине «Материаловедение и
Технология конструкционных материалов»
для студентов инженерных специальностей,
обучающихся по направлениям:
6.050502 «Инженерная механика»,
6.070106 «Автомобильный транспорт»,
6.051201 «Судостроение и океанотехника»
дневной и заочной форм обучения
Часть 2 -
«Термическая обработка сплавов»
Севастополь
2009
УДК 669.584 (046)
Методические указания к выполнению лабораторных работ по дисциплине «Материаловедение и технология конструкционных материалов» для студентов дневной и заочной форм обучения направления 6.050502 «Инженерная механика», 6.070106 «Автомобильный транспорт», 6.051201 «Судостроение и океанотехника»: в 3 ч. / Сост. Л.Б.Шрон, Г.П. Резинкина, В.Б Богуцкий, Э.С. Гордеева – Севастополь: Изд-во СевНТУ, 2009.Ч.2: Термическая обработка стали. - 32 с.
Целью издания методических указаний является помощь студентам в самостоятельном изучении научных и практических основ материаловедения и технологии материалов.
Рассмотрены и утверждены на заседании кафедры «Технология машиностроения» СевНТУ (протокол № 9 от 08.04. 2009 г.)
Допущено учебно-методическим центром СевНТУ в качестве методических указаний.
|
|
Рецензент:
Ю.К.Новоселов д.т.н., профессор кафедры «Технология машиностроения»
СОДЕРЖАНИЕ
Лабораторная работа № 9Термическая обработка дуралюмина марки Д16 | 4 |
Лабораторная работа № 10Термическая обработка стали | 9 |
Лабораторная работа № 11Закалка углеродистых сталей на мартенсит от различных температур нагрева | 17 |
Лабораторная работа № 12Микроструктура и свойства сталей после поверхностной закалки и химико-термической обработки | 2 23 |
Библиографический список | 29 |
Лабораторная работа № 9
ТЕРМИЧЕСКАЯ ОБРАБОТКА ДУРАЛЮМИНА
МАРКИ Д16
ЦЕЛЬ РАБОТЫ
Изучить влияние закалки и старения на структуру и свойства дуралюмина марки Д16.
ТЕОРЕТИЧЕСКИЙ РАЗДЕЛ
Термической обработкой называется совокупность операций нагрева, выдержки и последующего охлаждения твердых металлических материалов с целью получения заданных свойств за счет изменения структуры. Существуют следующие основные виды термической обработки: отжиг, нормализация, закалка, отпуск, старение.
Различают два вида закалки: с полиморфными и без полиморфных превращений. Закалка с полиморфными превращениями характерна для черных металлов, без полиморфных – для большинства цветных.
|
|
Закалка без полиморфных превращений заключается в фиксации при комнатной температуре (после охлаждения) состояния, соответствующего состоянию при температуре нагрева под закалку.
Дуралюмин марки Д16 содержит (3,8 - 4,9) % Cu; (1,2 - 1,8) % Mg и (0,3 -0,9) % Mn и подвергается упрочняющей термической обработке, заключающейся в закалке без полиморфных превращений с последующим старением.
В исходном отожженном состоянии сплав Д16 имеет двухфазую структуру: α-фазу и CuAl2 в виде сетки по границам зерен α –фазы, где α – твердый раствор меди в алюминии, а CuAl2 - химическое соединение (интерметаллид). В α-фазе при комнатной температуре согласно диаграмме состояния Al – Cu растворено 0,5 % меди, а в CuAl2 - 3,5%.
Закалка сплава Д16 производится при нагреве сплава до температуры на 30…50 0С выше критической точки (505±10 0С), выдержке при этой температуре для сквозного прогрева и завершения фазовых превращений с последующим резким охлаждением (обычно в воде) до комнатной температуры.
В результате резкого переохлаждения в структуре не происходит выделения твердой дисперсной фазы CuAl2 из a- фазы, т.к. не успевает произойти диффузионное перераспределение химических элементов в атомно-кристаллической решетке, и, как следствие, фиксируется твердый раствор a. По сравнению с равновесной (0,5 % Cu) при комнатной температуре в такой a- фазе содержится 4% меди, а следовательно, она является пересыщенным твёрдым раствором и поэтому обозначается a/ (равновесная- a). Пересыщение a/- фазы создаётся при отсутствии полиморфных превращений в основном металле (алюминии). Таким образом, после закалки сплав имеет структуру a/ - фазу.
|
|
В закалённом состоянии сплав обладает невысокой прочностью (твёрдостью) и хорошей технологической пластичностью (хорошо прокатывается, штампуется, в т.ч. в холодном состоянии).
Старение заключается в длительной изотермической выдержке (до 4…7 суток) закалённого сплава при климатических температурах (естественное или холодное старение), либо при повышенных (до 200 0С) температурах (искусственное или горячее старение) за гораздо более короткие сроки.
Дело в том, что a/- фаза является термодинамически нестабильной и поэтому склонна к самопроизвольному распаду с выделением твёрдых дисперсных частиц CuAl2 равномерно в объёме зёрен α-фазы.
Процесс распада протекает в несколько стадий с увеличением количества частиц CuAl2 в зерне, пока содержание [ Cu ] в a- фазе не достигнет практически равновесного значения (0,5 %). Такое строение сплава принято называть дисперсионной структурой, которая видна только под электронным микроскопом.
|
|
Поэтому термообработка, состоящая из закалки с последующим старением, получила название «дисперсионного твердения», т.к. упрочняющую фазу переводят в высокодисперсное состояние.
Сплавы, упрочнение которых осуществляется старением, называют стареющими.
Если с увеличением времени выдержки или температуры при искусственном старении происходит укрупнение частиц CuAl2 и падение прочности металла, то этот процесс называют «перестариванием».
Прочность сплава (sв) после закалки с естественным старением составляет порядка 450 МПа.
ОБОРУДОВАНИЕ, ПРИБОРЫ, МАТЕРИАЛЫ,
НАГЛЯДНЫЕ ПОСОБИЯ
3.1. Печи муфельные, нагретые до температур 505, 350, 200 и
100 0С.
3.2. Твердомер Роквелла со стальным шариковым индентором.
3.3. Образцы дуралюмина марки Д16 в количестве 6 штук.
3.4. Сосуд с водой для закалки дуралюмина.
3.5. Клещи для загрузки образцов в печь и выгрузки их из печи.
3.6. Плакаты: № 1 «Диаграмма состояния части системы Al - Cu», «Графики термообработки сплава с 4 % Cu»; № 2 «Изменение дисперсной структуры в процессе старения сплава Д16».
ПОРЯДОК ВЫПОЛНЕНИЯ РАБОТЫ
4.1. Изучить настоящее методическое указание.
4.2. Получить у лаборанта образцы в количестве 6 штук из сплава Д16.
4.3. Зарисовать таблицу 1 - Результаты эксперимента.
4.4. Замерить твёрдость полученных образцов. Результаты измерения занести в таблицу 1.
Таблица 1- Результаты эксперимента
№ образца
| HRB сплава исход- ная | Режим закалки | HRB сплава после закалки
| Режим старения | HRB сплава после старе-ния | ||||
t, 0С | τ, мин | Охлаждающая среда | t, 0С | τ, мин | Охлаждаю-щая среда | ||||
1 | 505 | вода | 20 | 30 | воздух | ||||
2 | 505 | вода | 100 | 10 | воздух | ||||
3 | 505 | вода | 100 | 20 | воздух | ||||
4 | 505 | вода | 100 | 30 | воздух | ||||
5 | 505 | вода | 200 | 30 | воздух | ||||
6 | 505 | вода | 350 | 30 | воздух |
4.5. Загрузить клещами последовательно 6 образцов в термическую печь с температурой 505 ± 10 0С. Выдержать образцы в печи в течение 8…10 мин.
4.6. Перенести нагретые образцы в сосуд с водой, где они охлаждаются до комнатной температуры.
4.7. Замерить твёрдость закалённых образцов. Результат занести в таблицу 1.
4.8. Произвести естественное старение одного закалённого образца, для чего выдержать его при комнатной температуре в течение 30 мин.
4.9. Замерить твёрдость естественно состаренного образца. Результат занести в таблицу 1.
4.10. Произвести искусственное старение пяти образцов:
4.10.1. Загрузить в печь с температурой 100 0С три закалённых образца и выдержать в печи в течение 10 минут (первый), 20 минут (второй), 30 минут (третий). После выдержки в печи образцы охладить на воздухе и замерить твёрдость. Результат занести в таблицу 1.
4.10.2. Загрузить в печь с температурой 200 0С один закалённый образец и выдержать в течение 30 минут. После выдержки образец охладить на воздухе и замерить твёрдость. Результат занести в таблицу 1.
4.10.3. Загрузить в печь с температурой 350 0С один закалённый образец и выдержать в течение 30 минут. После выдержки образец охладить на воздухе и измерить твёрдость. Результат занести в таблицу 1.
4.11. По результатам эксперимента построить графики зависимости твердости сплава от времени старения (t = 10, 20, 30 минут) при температуре старения 100 0С и от температуры старения (t = 100, 200, 350 0С) при выдержке 30 минут.
4.12. Зарисовать в тетради диаграмму части системы Al - Cu.
4.13. Зарисовать в тетради график термической обработки сплава Д 16.
4.14. Сделать выводы по работе.
СОДЕРЖАНИЕ ОТЧЁТА
5.1. Наименование работы.
5.2. Цель работы.
5.3. Таблица1- Результаты эксперимента.
5.4. Рисунок1 - График зависимости твёрдости от времени выдержки при старении при температуре 100 0С (время выдержки 10, 20, 30 мин).
5.5. Рисунок 2 - График зависимости твёрдости от температуры старения с выдержкой 30 мин. (температура старения 20, 100, 200 и 350 0С).
5.8. Выводы по работе.
КОНТРОЛЬНЫЕ ВОПРОСЫ
6.1. В чем сущность закалки дуралюминов и ее цель?
6.2. Как выбрать температуру нагрева сплава под закалку?
6.3. Какие свойства приобретает сплав Д16 после закалки?
6.4. В чем сущность естественного и искусственного старения и его цель?
6.5. Какая разница между искусственным и естественным старением?
6.6. Как изменятся свойства сплава в процессе старения?
6.7. Что такое перестаривание?
6.8. Почему фаза состава Cu Al2 называется упрочняющей?
6.9. В чем разница в структуре и свойствах сплава Д16 в отожженном и состаренном состояниях?
6.10. Укажите на диаграмме Al - Cu фазовые линии и критические точки, их координаты. С каким содержанием меди, сплавы упрочняются термообработкой?
Лабораторная работа № 10
ТЕРМИЧЕСКАЯ ОБРАБОТКА СТАЛИ
ЦЕЛЬ РАБОТЫ
Изучить влияние различных видов термической обработки (отжига, нормализации, закалки, отпуска) на структуру и свойства углеродистой стали.
ТЕОРЕТИЧЕСКИЙ РАЗДЕЛ
Термическая обработка является важной операцией на различных этапах технологического цикла изготовления многих деталей. Сочетанием химического состава (марки) стали и выбором необходимого способа термической обработки можно достичь наиболее высоких механических свойств деталей и машин.
Термическая обработка состоит из трех циклов: нагрев материала до расчетной температуры, выдержка при этой температуре и охлаждение с заданной скоростью. Различают 4 основных вида термической обработки:
- Отжиг
- Нормализацию
- Закалку
- Отпуск.
Отжиг и нормализация относятся к предварительной термообработке, которая используется для заготовок. Закалка и последующий отпуск относятся к окончательнойтермообработке, которая используется для готовых изделий.
Отжиг заключается в нагреве стали до расчетных температур, выдержке при этой температуре и медленном охлаждении вместе с печью. Нагрев при отжиге может производиться ниже или выше температур фазовых превращений.
Различают отжиг I и II рода.
Отжиг I рода проводят, как правило, ниже температур фазовых превращений. К отжигу первого рода относят:
- отжиг для снятия остаточных напряжений (для отливок, сварных изделий, деталей после обработки резанием, где из-за неравномерного охлаждения, неоднородной пластическойдеформации возникли остаточные напряжения);
- рекристаллизационный отжиг (для снятия наклепа холоднодеформированной стали);
- диффузионный отжиг (для слитков и отливок из легированной стали с целью получения однородного химического состава).
Отжиг II рода:
Различают следующие виды отжига II рода: полный, неполный, изотермический.
После отжига углеродистой стали образуются структуры, указанные на диаграмме состояния железо – цементит. После отжига сталь обладает низкой твердостью и прочностью при высокой пластичности. Фазовая перекристаллизация, происходящая при отжиге, измельчает зерно стали и устраняет различные структурные дефекты.
Отжиг в промышленности в большинстве случаев является предварительной термической обработкой. Отжигу подвергают отливки, поковки, прокат для улучшения обрабатываемости резанием.
Полный отжигзаключается в нагреведоэвтектоидной стали на (30 – 50) 0С выше точки АС3, выдержке при этой температуре для полного прогрева и завершения фазовых превращений в объеме металла и последующем медленном охлаждении. При этом происходит полная фазовая перекристаллизация стали.
При нагреве до температуры выше точки АС3 на (30 – 50) 0С образуется аустенит, характеризующийся мелким зерном, и поэтому при охлаждении возникает мелкозернистая структура, обеспечивающая высокую вязкость и пластичность.
Полному отжигу обычно подвергают сортовой прокат, поковки и фасонные отливки из доэвтектоидных сталей.
Для заэвтектоидных сталей полный отжиг на производят, т.к. после него цементит (Fe3C) выпадает на границам зерен пластинчатого перлита в виде сетки, что охрупчивает сталь.
Неполный отжиготличается от полного тем, что сталь нагревают до более низкой температуры (немного выше точки АС1).
Для доэвтектоидных сталей неполный отжиг иногда применяют для повышения обрабатываемости резанием. Однако при неполном отжиге происходит частичная перекристаллизация стали только вследствие превращения перлит – аустенит. Феррит не подвергается перекристаллизации, образуется разнозернистая структура: зерна перлита мелкие, а феррита – крупные. В связи с этим неполный отжиг доэвтектоидных сталей применяют в том случае, если исходная заготовка не имеет очень крупного зерна.
Для заэвтектоидных сталей применяют только неполный отжиг. В этих сталях нагрев несколько выше точки АС1 (обычно на (10 –30) 0С) вызывает практически полную фазовую перекристаллизацию стали и позволяет получить зернистую структуру перлита вместо пластинчатой. Такой отжиг называют сфероидизацией или отжигом на зернистый перлит.
Охлаждение при сфероидизации медленное. Оно должно обеспечить распад аустенита на феррито-карбидную структуру, сфероидизацию и коагуляцию образовавшихся карбидов, при охлаждении с печью до 620 – 680 0С, дальнейшее охлаждение до комнатной температуры происходит на воздухе.
Сталь со структурой зернистого перлита имеет более низкую твердость, чем со структурой пластинчатого перлита, поэтому обрабатывается резанием лучше.
Отжигу на зернистый перлит подвергают заготовки из инструментальных и подшипниковых сталей.
Изотермический отжиг.В этом случае сталь нагревают, как и для полного отжига, и сравнительно быстро охлаждают (переносом в другую печь) до температуры ниже точки АС1 (обычно ≈ 650 0С) и назначают изотермическую выдержку для полного распада аустенита, после чего следует охлаждение на воздухе.
Преимущество изотермического отжига заключается в уменьшении длительности процесса и получении более однородной структуры.
Изотермический отжиг улучшает обрабатываемость резанием, чистоту поверхности и уменьшает деформацию при последующей термической и химико-термической обработке.
Этот вид отжига используют для поковок и других заготовок небольших размеров.
Нормализация заключается в нагреве доэвтектоидной стали до температуры, превышающей точку АС3 на 50 0С, а заэвтектоидной стали выше АСm также на 50 0С (до полной аустенизации), непродолжительной выдержке для прогрева стали и завершения фазовых превращений и охлаждении на воздухе. Нормализация вызывает полную фазовую перекристаллизацию стали и устраняет крупнозернистую структуру, полученную при литье, прокатке, ковке или штамповке.
Назначение нормализации различно в зависимости от состава стали. Для низкоуглеродистых сталей нормализацию применяют вместо отжига для ускорения процесса.
Для заготовок из среднеуглеродистых сталей нормализацией заменяют более дорогую термообработку – улучшение (закалка + высокий отпуск). По сравнению с отожженной сталью нормализованная сталь имеет более высокую твердость, а по сравнению с улучшенной меньшую пластичность и ударную вязкость.
Для заэвтектоидных сталей нормализацию проводят для устранения цементитной сетки, образовавшейся при медленном охлаждении.
Закалка –это вид термической обработки, заключающийся в нагреве стали выше критической точки (АС3 для доэвтектоидных и АС1 для заэвтектоидных сталей) на (30 – 50) 0С, выдержке при этой температуре и последующем охлаждении со скоростью равной или больше критической. Критическую скорость закалки обеспечивает охлаждающая среда вода (для углеродистых сталей) или масло (для легированных сталей). Основной структурой закаленной стали является мартенсит закалки, который образуется из аустенита при охлаждении с критической скоростью закалки. Мартенсит закалки – это пересыщенный твердый раствор углерода в Fe-α. Закалка, при которой в результате нагрева образуется только аустенит, называется полной закалкой.
Доэвтектоидные стали с исходной структурой феррит+ перлит при нагреве приобретают аустенитную структуру, которая при последующем охлаждении со скоростью, равной или выше критической превращается в мартенсит закалки.
Заэвтектоидные стали с исходной структурой перлит + цементит нагревают несколько выше АС1 на (10 - 20 0С). При таком нагреве образуется структура аустенит + цементит. После охлаждения структура закаленной стали состоит из мартенсита закалки и нерастворившихся карбидов (цементита). Закалка, при которой при нагреве стали образуется наряду с аустенитом феррит (в доэвтектоидных сталях) или цементит (в заэвтектоидных сталях) называется неполной закалкой.
Таким образом, для доэвтектоидных сталей производится полная закалка, а для заэвтектоидных – неполная закалка.
В углеродистых сталях, которые содержат углерода более 0,6% весь аустенит, который образовался при нагреве, при последующем охлаждении со скоростью, равной или больше критической, не превратится в мартенсит закалки, так как температура конца мартенситного превращения в этих сталях ниже комнатной температуры. Часть аустенита остается не превращенной в мартенсит. Такой аустенит называется остаточным аустенитом. Поэтому структура заэвтектоидной стали после закалки будет состоять из мартенсита закалки, цементита и остаточного аустенита.
Отпуск –это вид термической обработки, который заключается в нагреве закаленной стали ниже критической точки АС1, выдержке при этой температуре и последующем охлаждении с определенной скоростью (углеродистые стали охлаждают на воздухе). Отпуск является окончательной операцией термической обработки, проводится после закалки для обеспечения требуемого уровня эксплуатационнных свойств и снятия закалочных напряжений.
В зависимости от температуры отпуска различают низкий, средний и высокий отпуск.
Низкий отпускпроводится при температуре 150 – 200 0С. При этом виде отпуска снижаются внутренние напряжения, повышается прочность и немного улучшается вязкость стали. Структура стали после низкого отпуска называется мартенситом отпуска. Твердость после этого вида отпуска HRC 58 – 63. При этом виде отпуска твердость наибольшая из всех видов отпуска. Низкому отпуску подвергается режущий и измерительный инструмент из углеродистых и низколегированных сталей.
Средний отпускпроводится при температуре 350 – 500 0С. Такой вид отпуска обеспечивает стали высокий предел упругости, предел выносливости и релаксационную стойкость. Структура носит название троостит отпуска. Твердость после среднего отпуска HRC 40 – 50. Такому отпуску подвергают пружины, рессоры, штампы.
Высокий отпускпроводится при температуре 500 – 650 0С. Высокий отпуск создает наилучшее соотношение прочности и вязкости стали. Структура носит название сорбит отпуска. Твердость после высокого отпуска HRC 35 - 25.
Закалка в сочетании с высоким отпуском называется термическим улучшением. Улучшение в значительной степени повышает конструкционную прочность стали, уменьшая чувствительность к концентраторам напряжений, снижая температуру верхнего и нижнего порога хладноломкости стали. Такому отпуску подвергаются различные конструкционные детали – валы, шестерни и т. д.
Дата добавления: 2018-04-04; просмотров: 276; Мы поможем в написании вашей работы! |
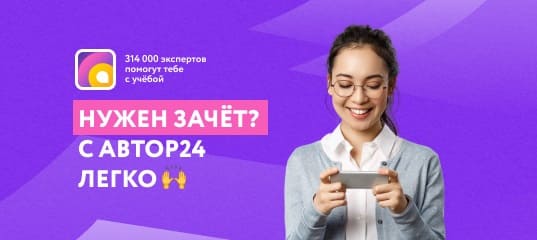
Мы поможем в написании ваших работ!