ВКАЗІВКИ ЩОДО ВИКОНАНАЯ ОКРЕМИХ РОЗДІЛІВ РОБОТИ
Міністерство освіти і науки, молоді та спорту України
ОДЕСЬКИЙ НАЦІОНАЛЬНИЙ ПОЛІТЕХНІЧНИЙ
УНІВЕРСИТЕТ
МЕТОДИЧНІ ВКАЗІВКИ
до курсової роботи з дисципліни
«АВТОМАТИЗАЦІЯ ПРОЦЕСІВ МЕТАЛООБРОБКИ»
Одеса: ОНПУ, 2012
Міністерство освіти і науки, молоді та спорту України
ОДЕСЬКИЙ НАЦІОНАЛЬНИЙ ПОЛІТЕХНІЧНИЙ
УНІВЕРСИТЕТ
МЕТОДИЧНІ ВКАЗІВКИ І ЗАВДАННЯ
до курсової роботи з дисципліни
«АВТОМАТИЗАЦІЯ ПРОЦЕСІВ МЕТАЛООБРОБКИ»
для студентів напряму 6.050702 – електромеханіка усіх форм навчання
для спеціальностей 7.05070204, 8.05070204
«Електромеханічні системи автоматизації та електропривод»
Затверджено
на засіданні кафедри електромеханічних систем
з комп’ютерним управлінням
Протокол № 2 від 11.09.2012
Одеса: ОНПУ, 2012
Методичні вказівки і завдання до курсової роботи з дисципліни «Автоматизація процесів металообробки» для студентів напряму 6.050702 усіх форм навчання – електромеханіка / Укл. В.А. Водічев.– Одеса: ОНПУ, 2012. – 16 с.
Укладач: Водічев В.А., докт. техн. наук, проф.
Методичні вказівки містять завдання і порядок виконання курсової роботи з дисципліни «Автоматизація процесів металообробки» . Завдання базуються на основі знань, які студенти набули при вивченні дисципліни. Призначаються для студентів денної та заочної форми навчання.
|
|
ЗМІСТ
1 Мета, зміст та оформлення курсової роботи..…………………………………..………….…4
1.1. Мета курсової роботи…………………………………………………………………….…4
1.2. Зміст роботи….…………………………………………………………………………...…4
1.3. Оформлення розрахунково-пояснювальної записки …………………………....……..…4
2 Завдання на роботу……………………………………………………………………...….….5
3 Вказівки щодо виконання окремих розділів роботи………………………………………...7
3.1. Опис конструкції верстата та технологічного процесу, формулювання
вимог д електропривода………………………………………………………………………...7
3.2. Вибір системи електропривода та приводного двигуна, розрахунок
параметрів силового ланцюга електропривода…………………………………………….…7
3.3. Розрахунок параметрів регуляторів та ланцюгів зворотних зв'язків
регульованого електропривода..………………………………………….………………….…8
3.4. Вибір структури системи управління технологічним процесом
металообробного верстата..………………………………………….…………….……………8
3.5. Розрахунок та побудова статичних характеристик системи управління
технологічним процесом..………………………………………….………………………..…10
|
|
3.6. Розрахунок перехідних процесів у системі управління технологічним
процесом металообробки..………………………………………….……………………….…14
3.7. Інженерна оцінка спроектованої системи………………………………………………..15
Список літератури..………………………………………….………………………………….16
МЕТА, ЗМІСТ ТА ОФОРМЛЕННЯ КУРСОВОЇ РОБОТИ
1.1. Мета курсової роботи
Мета курсової роботи – закріплення, систематизація та розширення знань, отриманих під час вивчення дисципліни "Автоматизація процесів металообробки", придбання навичок прийняття та обґрунтування технічних рішень при виборі системи електропривода, елементної бази та розрахунку всіх елементів автоматизованої системи управління (АСУ) технологічним процесом металообробки.
1.2. Зміст роботи
1.2.1. Опис конструкції верстата та технологічного процесу, формулювання вимог до електричного приводу головного руху чи подачі.
1.2.2. Вибір системи електропривода та приводного двигуна, розрахунок параметрів силового ланцюга електропривода.
1.2.3. Розрахунок параметрів регуляторів та ланцюгів зворотних зв'язків регульованого електропривода.
1.2.4. Вибір структури системи управління технологічним процесом металообробного верстата.
|
|
1.2.5. Розрахунок та побудова статичних характеристик системи управління технологічним процесом.
1.2.6. Розрахунок перехідних процесів у системі управління технологічним процесом металообробки.
1.2.7. Інженерна оцінка спроектованої системи управління.
1.3. Оформлення розрахунково-пояснювальної записки
Курсову роботу подають до захисту у вигляді пояснювальної записки обсягом до 30 аркушів формату А4 (210х297 мм) з рамкою та штампом встановленого зразка.
Пояснення та описи дають коротко, не припустиме скорочення слів, за виключенням загальноприйнятих, наприклад: ККД, ЕРС. Розрахункові формули записують у літерному вигляді, а потім - окремим рядком у цифрах. Після кінцевого результату вказують одиницю виміру. Результати розрахунків, що повторюються, наводять у формі таблиць. Рисунки та таблиці повинні мати номер і змістовний підпис. Список літератури складають у відповідності до діючого стандарту.
ЗАВДАННЯ НА РОБОТУ
2.1. Розробити АСУ електроприводом головного руху лоботокарного верстата з підтримкою постійної швидкості різання при зміні діаметру обробки.
Базова модель верстата 1А693.
|
|
Технічні дані | Варіанти завдань | ||||
1 | 2 | 3 | 4 | 5 | |
Потужність приводу головного руху, кВт | 20 | 22 | 30 | 26 | 24 |
Частота обертання шпинделя, об/хв. | 1,6-315 | 1-100 | 0, 8-63 | 1-80 | 1-150 |
Найбільший діаметр обробки, мм | 1250 | 2000 | 3200 | 2000 | 2000 |
Діапазон безступінчастого регулювання швидкості приводу головного руку | 1:3 | 1:3 | 1:4 | 1:3,5 | 1:4 |
2.2. Розробити АСУ електроприводом головного руху токарно-карусельного верстата з підтримкою постійної швидкості різання при зміні діаметра обробки.
Базова модель верстата 1512.
Технічні дані | Варіанти завдань | ||||
6 | 7 | 8 | 9 | 10 | |
Потужність приводу головного руху, кВт | 30 | 32 | 36 | 45 | 55 |
Частота обертання планшайби, oб/хв | 5-250 | 4-200 | 1,6-80 | 0,66-62,1 | 0,46-42,5 |
Найбільший діаметр оброблюваної деталі, мм | 1000 | 1000 | 1600 | 2000 | 2500 |
Діапазон безступінчастого регулювання швидкості приводу головного руку | 1:3 | 1:3 | 1:4 | 1:3,5 | 1:4 |
2.3. Розробити АСУ електроприводами обертання стола та поперечної подачі плоскошліфувального верстата з круглим столом та горизонтальним шпинделем з підтримкою постійної швидкості деталі та постійної подачі на оберт стола.
Базова модель верстата 3Д740В.
Технічні данні | Варіанти завдань | ||||
11 | 12 | 13 | 14 | І5 | |
Потужність приводу стола, кВт | 2,0 | 1,5 | 2,5 | 2,0 | 3,0 |
Потужність приводу поперечної подачі, кВт | 1,5 | 1,0 | 2.0 | 1,5 | 2,5 |
Діаметр стола, мм | 400 | 400 | 400 | 800 | 1000 |
Частота обертання стола, об/хв. | 15-180 | 1 5-180 | 15-180 | 8-96 | 5-30 |
2.4. Розробити АСУ електроприводом подачі стола фрезерного верстата, що забезпечує підтримку постійної потужності різання.
Базова модель верстата 6Р82.
Технічні дані | Варіанти завдань | ||||
16 | 17 | 18 | 19 | 20 | |
Потужність приводу головного руху, кВт | 1,5 | 3,0 | 2,5 | 3,4 | 4,5 |
Потужність приводу подачі, кВт | 0,37 | 0,75 | 0,55 | 1,5 | 1,0 |
Частота обертання шпинделя, об/хв | 40-2000 | 20-2000 | 31-1600 | 25-1250 | 25-1251 |
Швидкість подачі, мм/хв. | 16-710 | 29-1120 | 25-1250 | 20-1500 | 25-1251 |
2.5. Розробити АСУ електроприводом відрізного верстата, що забезпечує підтримку постійної потужності різання.
Базова модель верстата 8А631
Технічні дані | Варіанти завдань | ||||
21 | 22 | 23 | 24 | 25 | |
Потужність приводу головного руху, кВт | 2,8 | 4,5 | 7,5 | 10 | 18,5 |
Потужність приводу подачі, кВт | 0,53 | 1,1 | 1,6 | 2,5 | 4,5 |
Діаметр диска, що пиляє, мм | 350 | 510 | 800 | 1010 | 1430 |
Найбільший діаметр деталі, що розрізається, мм | 110 | 160 | 280 | 350 | 500 |
Найбільша швидкість подачі, мм/хв. | 600 | 550 | 650 | 450 | 500 |
Для вибору варіанта завдання група ділиться на 5 підгруп. Кількість студентів у кожній підгрупі, що виконують кожну групу варіантів завдань для одної базової моделі верстата, визначається округленням до найближчого цілого числа результату ділення за формулою N/5, де N – кількість студентів у навчальній групі. Кожному студенту у підгрупі надається варіант завдання у послідовності, що наведена в підрозділах 2.1 – 2.5.
ВКАЗІВКИ ЩОДО ВИКОНАНАЯ ОКРЕМИХ РОЗДІЛІВ РОБОТИ
3.1. Опис конструкції верстата та технологічного процесу, формулювання вимог до електропривода
У цьому розділі потрібно вивчити технологічний процес на запропонованому верстаті з використанням літератури [1, 2]. Зрозуміти місце та роль механізму у цьому технологічному процесі. Сформулювати вимоги до електропривода механізму відповідного робочого руху верстата з точки зору необхідного діапазону регулювання швидкості, стабільності швидкості, плавності її регулювання, умов регулювання (постійний момент чи потужність), потрібної якості перехідних процесів при регулюванні швидкості.
3.2. Вибір системи електропривода та приводного двигуна, розрахунок параметрів силового ланцюга електропривода
У більшості випадків вимоги, що ставлять механізми робочих рухів металообробних верстатів, можуть бути задовільнені якимось з комплектних електроприводів, які випускаються серійно електротехнічними підприємствами: ЕТУ, ЕПУ, ЕШІР, ЕШІМ, ЕПБ, "Розмір 2-М". Схеми управління регульованих електроприводів для машинобудування наведені у [3].
Зроблений студентом вибір типу комплектного електропривода узгоджується з керівником проекту.
У механізмах робочих рухів металообробних верстатів доцільно застосовувати двигуни тих типів, що рекомендовані в технічних паспортах відповідних комплектних електроприводів. Потужність обраних двигунів має відповідати варіанту завдання.
Після вибору двигуна і типу комплектного електропривода можна визначити конкретно, на які струм та напругу потрібний перетворювач. При необхідності для узгодження напруги двигуна з вихідною напругою перетворювача застосовують узгоджуючий трансформатор, який обирають з каталогів та довідників [4] виходячи з необхідної потужності, напруги і струму.
У разі відсутності необхідності використання узгоджуючого трансформатора слід зважити на доцільність застосування струмообмежуючих реакторів. При застосуванні електроприводів постійного струму, що побудовані за системою "тиристорний перетворювач – двигун", може виявитись необхідність застосування згладжуючого дроселя.
3.3. Розрахунок параметрів регуляторів та ланцюгів зворотних зв'язків регульованого електропривода
При виконанні цього розділу необхідно вивчити структуру системи управління обраного комплектного електропривода, наприклад за літературою [1,3]. При цьому звернути увагу на те, які у системі управління використані регулятори та датчики. Розрахувати коефіцієнти передачі датчиків та параметри регуляторів, що забезпечують потрібні статичні та динамічні характеристики електропривода при регулюванні швидкості. При цьому доцільно використовувати посібники [1, 5, 6].
3.4. Вибір структури системи управління технологічним процесом металообробного верстата
Запропоновані варіанти завдань вимагають розробити автоматизовану систему управління технологічним процесом, яка забезпечує стабілізацію швидкості чи потужності різання. Роботу щодо вибору структури системи необхідно почати з вивчення технологічних основ її застосування та ознайомлення з можливими варіантами реалізації таких систем [1,6]. Після чого зупинитися на одному з варіантів системи, який найбільш відповідає вимогам технологічного процесу даного верстата. Скласти функціональну схему системи та дати роз'яснення процесів, що відбуваються при її роботі. Визначити вимоги до окремих елементів системи, необхідні для їх робочого проектування чи придбання у вигляді функціонально закінчених виробів. Розробити принципові електричні схеми кожного елемента системи (датчика, функціонального перетворювача, регулятора), вказати рівні вхідних та вихідних величин, діапазони їх зміни. Приділити увагу сполученню окремих елементів системи між собою.
Наприклад, система, що стабілізує швидкість деталі на шліфувальному верстаті з круглим столом, може бути побудована за функціональною схемою рис. 3.1. Верстат має два приводи подачі, що побудовані за системою ТП-Д.
Перший привод, з двигуном М1, призначений для обертання стола C, а другий, з двигуном М2, – для переміщення шліфувальної бабки Б з шліфувальним кругом К. Система забезпечує стабілізацію швидкості у точці контакту деталі з шліфувальним кругом та величини подачі на один оберт стола. Швидкість деталі V залежить від кутової швидкості стола w та радіуса обробки R, який змінюється при переміщенні бабки упоперек стола. Для контролю радіуса R застосовано датчик ДР, який зв'язано з валом двигуна механізму подачі через редуктор. Напруга Uдр з виходу датчика ДР надходить на функціональний перетворювач ФП, який формує напругу Uфп від'ємного зворотного зв'язку. Напруга Uзw, що задає швидкість приводу стола, формується підсилювачем П з підсумкового сигналу різниці між напругою Uзw max завдання швидкості деталі та напругою зворотного зв'язку Uфп. Для забезпечення стабілізації подачі на один оберт стола напруга Uзs, що задає швидкість приводу подачі, формується за допомогою тахогенератора BR, який встановлено на валу двигуна М1, що обертає стіл через
редуктор Р.
Один із варіантів функціональної схеми системи, що забезпечує стабілізацію потужності різання на фрезерному верстаті, подано на рис. 3.2.
Тут зображені два приводи. Перший, з двигуном М1, побудований за системою ТП-Д, забезпечує подачу стола С верстата з заготівкою З. Другий, з асинхронним двигуном М2, обертає фрезу Ф. Потужність різання залежить від багатьох факторів і змінюється головним чином під впливом зміни глибини та ширини фрезерування. Для компенсації впливу цієї збурювальної дії на потужність фрезерування потрібно автоматично змінювати швидкість подачі стола. Для контролю потужності фрезерування застосовано датчик ДП активної потужності асинхронного двигуна М2 головного руху верстата.
Напруга Uдп датчика ДП разом з напругою Uк корегувального пристрою КП надходить на функціональний перетворювач ФП, який формує напругу Uтз від'ємного технологічного зворотного зв'язку. Сигнал Uзw завдання швидкості подачі є підсумковим сигналом різниці між напругою Uзmax завдання найбільшої швидкості подачі та напругою Uтз.
Електричні принципові схеми елементів систем необхідно розробити на основі визначених вимог до кожного елемента. При цьому потрібно використовувати сучасну елементну базу. Окремі технічні рішення щодо реалізації датчиків, перетворювачів та регуляторів наведені у літературі [1].
3.5. Розрахунок та побудова статичних характеристик системи управління технологічним процесом
Основою розрахунку статичних характеристик системи має бути структурна схема для усталеного режиму роботи системи. Ця схема складається на основі розробленої функціональної схеми. Далі потрібно визначити коефіцієнти передачі окремих ланок структурної схеми, розрахувати параметри настройки функціональних перетворювачів, скласти алгебраїчні рівняння, що відображають зв'язок між вихідною координатою системи і збурювальною дією, та на їх основі побудувати статичні характеристики замкнутої системи.
Так, для системи, що зображена на рис. 3.1. може бути складена структурна схема для усталеного режиму роботи (рис. 3.3.).
Коефіцієнт передачі електропривода обертання стола
де wmax – максимальна швидкість двигуна стола, рад/с,
Uз max – максимальна напруга завдання швидкості, В.
Коефіцієнт механічної передачі
де ір – передавальне число редуктора механізму, обертання стола.
Коефіцієнт підсилення підсилювача
де Vз max, Vз - максимальна і фактична задані швидкості деталі, м/с.
Коефіцієнт передачі датчика радіуса обробки
де Uдр max – максимальна вихідна напруга датчика, В,
Rmax – максимальний радіус обробки, м.
Закон зміни напруги Uзw завдання швидкості w двигуна стола в залежності від радіуса обробки R для підтримки постійної величини швидкості деталі, що дорівнює Vз, має вигляд
Для забезпечення такої напруги Uзw необхідний функціональний перетворювач ФП, напруга якого Uфп у функції радіуса R змінюється за законом
чи
де Uзv max – напруга завдання максимальної швидкості деталі.
При розрахунку доцільно прийняти Ку=1, Vз max, =Vз, Uзv max = 10 В.
Остання формула дозволяє побудувати характеристики ФП у вигляді Uзw(R) та Uфп(Uдр), де Uдр = kдр∙R – напруга на виході датчика радіуса.
Для спрощення технічної реалізації ФП необхідно здійснити кусково-лінійну апроксимацію залежності Uфп(Uдр) трьома ділянками прямих ліній та розрахувати параметри настройки ФП, що забезпечать таку апроксимацію.
Статичну характеристику замкнутої системи у вигляді залежності швидкості деталі V від радіуса обробки R розрахувати з використанням рівняння
у якому для кожної ділянки апроксимації залежності Uфп(Uдр) виразити Uфп рівнянням відповідної прямої лінії
де коефіцієнт kфп та величина зміщення сфп мають бути визначені окремо для кожної з трьох ділянок апроксимації. При радіусах обробки менших за
стабілізація швидкості V неможлива. Тому статична характеристика замкнутої системи має бути побудована для випадку роботи привода робочого руху верстата на одній ступені коробки швидкостей і діапазон зміни радіусів обробки дорівнює діапазону електричного безступінчастого регулювання швидкості електроприводу, що вказаний у варіанті завдання.
Статична характеристика при R < Rmin описується виразом
Для системи стабілізації потужності обробки, що зображена на рис. 3.2, складають структурну схему для усталеного режиму роботи (рис 3.4).
![]() |
Коефіцієнт механічної передачі електропривода подачі стола визначають за формулою
де Smax – максимальна швидкість подачі стола, мм/хв.
Для реалізації такого коефіцієнту потрібно визначити параметри кінематичного ланцюга відповідно до рівняння
де tв – крок гвинта,
ір – передаточне число редуктора
Коефіцієнт передачі датчика потужності
де Uдпmax – максимальна напруга на виході датчика потужності, В;
Рzmax – максимальна потужність різання (може бути прийнята такою, що дорівнює 1.5–2∙Рzз, де Рzз – задана величина потужності).
Функціональний перетворювач, що реалізує типову нелінійність типу "зoнa нечутливості", поданий на структурній схемі рис. 3.4 напругою порівняння Uп та пропорційною ланкою з коефіцієнтом kфп. Напруга порівняння
Для визначення коефіцієнтів передачі процесу обробки kп та функціонального перетворювача kфп потрібно провести розрахунок статичних характеристик розімкнутої системи у вигляді залежності потужності Рz від швидкості подачі S. Це можна зробити з використанням формул [7]
Головна складова сили різання
,
Потужність обробки в усталеному режимі роботи
.
Швидкість подачі
де tp – глибина фрезерування, мм; В – ширина фрезерування, мм; Dф – діаметр фрези, мм; n – частота обертання фрези, об/хв; z – кількість зубів фрези; Sz – подача на зуб, мм/зуб; Cp, q, x, y, u, w — коефіцієнти і показники степеня, які залежать від оброблюваного матеріалу і інструмента; Kp — коефіцієнт, що враховує умови обробки [7].
Характеристики Pz(S) розрахувати для трьох значень глибини tр, (чи ширини В) обробки. За графіком, що відповідає максимальній збурювальній дії (глибині чи ширині обробки), визначити при максимальній величині швидкості подачі Smax максимальну потужність різання у розімкнутій системі Рz max, та розрахувати максимальний коефіцієнт передачі процесу обробки
а також статичну похибку потужності у розімкнутій системі
Задаючись потрібною величиною статичної похибки Δ у замкнутій системі, розрахувати потрібну для забезпечення такої похибки величину коефіцієнта підсилення розімкнутої системи
Визначити потрібний коефіцієнт передачі функціонального перетворювача, що забезпечить потрібну величину похибки Δ у замкнутій системі
На основі структурної схеми (рис. 3.4) може бути одержане рівняння статичної характеристики замкнутої системи Pz(kп):
де Uзmax=Smax/(КепКпм); kп – коефіцієнт передачі процесу обробки.
Задаючи величини kп < kпmax розрахувати цю характеристику при Рz > Pzз. При Рz < Pzз система є розімкнутою, і її статична характеристика описується формулою
3.6. Розрахунок перехідних процесів у системі управління технологічним процесом металообробки
Перехідні процеси у системах управління процесом металообробки розраховують на персональному комп’ютері. Попередньо потрібно скласти структурну схему системи (рис. 3.5, рис. 3.6), де врахувати сталі часу окремих ланок. На основі структурної схеми складають рівняння математичної моделі системи та програму моделювання, за якою виконують розрахунок перехідних процесів.
Структурна схема для моделювання системи стабілізації швидкості (рис. 3.1) може бути складена у вигляді, що наведений на рис. 3.5. Моделі електроприводів стола ЕПС і поперечної подачі ЕПП мають бути складені за структурними схемами відповідних комплектних електроприводів з урахуванням розрахованих параметрів силових ланцюгів, регуляторів та ланцюгів зворотних зв'язків, а також з урахуванням обмеження вихідних напруг регуляторів. При моделюванні мають бути розраховані графіки швидкості деталі (чи різання для інших верстатів) V та радіуса обробки R у функції часу t.
Структурна схема для моделювання системи стабілізації потужності (рис. 3.2) наведена на рис. 3.6.
Модель електропривода стола складається, як вказано вище, для схеми рис.3.5. Процес обробки поданий на структурній схемі рис. 3.6 трьома ланками. Перша дозволяє визначити подачу на зуб Sz = S/nф∙z, друга визначає потужність Рz , третя враховує сталі часу Тр процесу обробки.
Датчик потужності поданий на схемі рис. 3.6 аперіодичною ланкою зі сталою часу Тдп. Для забезпечення стійкості системи та потрібної якості перехідних процесів застосовано корегувальний пристрій КП, для якого можна прийняти коефіцієнти kк1=kк2=20 і сталі часу Tк1=Тк2= 0,005 с.
![]() |
При моделюванні мають бути розраховані графіки потужності обробки Рz, швидкості подачі S та збурювальної дії (tp чи В) в функції часу t.
3.7. Інженерна оцінка спроектованої системи
У цьому розділі потрібно підбити підсумки роботи. Вказати, з якою точністю підтримує розроблена система вихідну координату в усталеному режимі, яка забезпечується величина перерегулювання у перехідних режимах, яке додаткове обладнання повинен придбати чи розробити замовник такої системи для її реалізації та, який корисний ефект він при цьому отримає.
Список літератури
1. Браницкий Р., Водичев В. А., Шапарев Н. К. Электрооборудование станков и автоматизация металлообработки. – Зелена Гура: Изд-во Высш. Инж. шк., 1996. – 239 с.
2. Чернов Н. Н. Металлорежущие станки. – М.: Машиностроение, 1988. – 418 с.
3. Методические указания. Схемы регулируемых электроприводов для машиностроения по курсу "Системы управления электроприводами" для студентов специальности 21.05 / Сост. Л. П. Петров. – Одесса: ОГПУ, 1995. – 20 с.
4. Комплектные тиристорные электроприводы: Справочник/ И. X. Евзеров, А.С. Горобец, Б. И. Мошкович и др. /Под ред. В.М. Перельмутера. – М.: Энергоатомиздат, 1988. – 319 с.
5. Методические указания "Инженерная методика синтеза систем управления регулируемыми электроприводами" по курсу "Системы управления электроприводами" для студентов, специальности 7.092208 / Сост. Л. П. Петров. – Одесса: ОГПУ, 1996, – 33 с.
6. Шапарев Н. К. Расчет автоматизированных электроприводов систем управления металлообработкой. – К.: Лыбидь,1992. – 272 с.
7. Справочник технолога – машиностроителя. В 2-х т. Т.2/ Под ред. А.Г. Косиловой, Р.К. Мещерякова. – М.: Машиностроение, 1986. – 496 с.
Дата добавления: 2018-04-04; просмотров: 195; Мы поможем в написании вашей работы! |
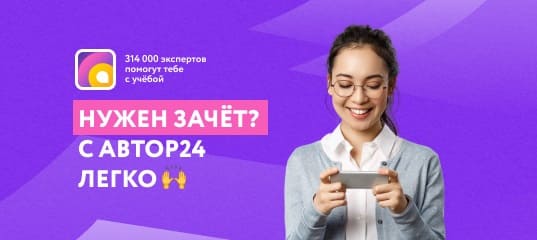
Мы поможем в написании ваших работ!