Технические средства автоматизации. Nbsp; МИНИСТЕРСТВО ОБРАЗОВАНИЯ РОССИЙСКОЙ ФЕДЕРАЦИИ МОСКОВСКИЙ ГОСУДАРСТВЕННЫЙ УНИВЕРСИТЕТ ТЕХНОЛОГИЙ И УПРАВЛЕНИЯ (образован в 1953
Nbsp; МИНИСТЕРСТВО ОБРАЗОВАНИЯ РОССИЙСКОЙ ФЕДЕРАЦИИ МОСКОВСКИЙ ГОСУДАРСТВЕННЫЙ УНИВЕРСИТЕТ ТЕХНОЛОГИЙ И УПРАВЛЕНИЯ (образован в 1953 году) __________________________________________________________
Кафедра систем управления
Дистанционное Сист.уп.-15.22.2102.зчн.плн.
обучение Сист.уп.-15.22.2102.зчн.скр.
В.Е. Жужжалов, В.В. Солдатов,
В.В. Маклаков, М.В. Жиров
ТЕХНИЧЕСКИЕ СРЕДСТВА
АВТОМАТИЗАЦИИ
Учебно-практическое пособие
Для студентов специальности 2102
Www.msta.ru
4424
Москва – 2004
УДК 621.01
© Жужжалов В.Е., Солдатов В.В., Маклаков В.В., Жиров М.В. Технические средства автоматизации. Учебно-практическое пособие. – М.: МГУТУ, 2004.
В учебно-практическом пособии в кратком и систематическом виде изложено содержание курса «Технические средства автоматизации». После каждой темы даны вопросы и тесты, позволяющие контролировать степень усвоения учебного материала.
Пособие предназначено для студентов специальности 2102.
Авторы: Жужжалов Валерий Евгеньевич, Солдатов Виктор Владимирович,
Маклаков Владимир Васильевич, Жиров Михаил Вениаминович
Рецензенты: д.т.н., профессор, зав. каф. автоматизации биотехнических
систем МГУ ПБ Попов В.И.,
|
|
д.т.н., ведущий научн. сотр. ИПУ РАН Цветков А.В.
Редактор: Свешникова Н.И.
©Московский государственный университет технологий и управления, 2004.
109004, Москва, Земляной вал, 73
СОДЕРЖАНИЕ
Введение 4
Тема 1. Этапы развития и принципы формирования состава технических средств автоматизированных систем управления 4
Тест 1 9
Тема 2. Технические средства автоматизированных систем
управления 10
Тест 2 19
Тема 3. Электродвигательные исполнительные механизмы 19
Тест 3 39
Тема 4. Электромагнитные исполнительные механизмы 40
|
|
Тест 4 46
Тема 5. Электромеханические муфты 46
Тест 5 57
Тема 6. Релейные исполнительные механизмы 58
Тест 6 69
Ответы на тесты 69
Итоговый тест 70
Список литературы 72
ВВЕДЕНИЕ
Автоматизация является одним из важнейших факторов роста производительности труда и повышения качества выпускаемой продукции. Непременным условием ускорения темпов роста автоматизации является развитие и совершенствование ее технических средств, к которым относятся все устройства, входящие в систему управления и предназначенные для получения информации, ее передачи, хранения и преобразования, а также для осуществления управляющих воздействий на объект управления. Эти воздействия осуществляются с помощью исполнительных механизмов и регулирующих органов, описанию которых посвящено данное пособие.
|
|
Основное внимание уделяется электромеханическим исполнительным механизмам, т.к. они получили широкое распространение на практике, благодаря удобству преобразования электрических сигналов устройства управления –регулятора в требуемое механическое перемещение регулирующего органа, изменяющего материальные и энергетические потоки в управляемом объекте.
ТЕМА 1. ЭТАПЫ РАЗВИТИЯ И ПРИНЦИПЫ ФОРМИРОВАНИЯ СОСТАВА ТЕХНИЧЕСКИХ СРЕДСТВ АВТОМАТИЗАЦИИ
Этапы развития технических средств автоматизации. Развитие технических средств автоматизации является сложным процессом, в основе которого лежат экономические интересы и технические потребности автоматизируемых производств, с одной стороны, и те же интересы и технологические возможности производителей технических средств автоматизации, – с другой. Первичным стимулом развития является повышение экономической эффективности работы предприятий, благодаря внедрению новых, более совершенных технических средств автоматизации.
|
|
В развитии экономических и технических предпосылок внедрения и использования автоматизации технологических процессов (ТП) можно выделить следующие этапы:
1. Начальный этап, для которого характерны избыток дешевой рабочей силы, низкая производительность труда, малая единичная мощность агрегатов и установок. Благодаря этому самое широкое участие человека в управлении ТП, т.е. наблюдение за объектом управления, а также принятие и исполнение управляющих решений, на данном этапе было экономически оправданным. Механизации и автоматизации подлежали только те отдельные процессы и операции, управление которыми человек не мог осуществлять достаточно надежно по своим психофизиологическим данным, т.е. технологические операции требовавшие больших мускульных усилий, быстроты реакции, повышенного внимания и др.
2. Переход к этапу комплексной механизации и автоматизации производства произошел благодаря росту производительности труда, укрупнению единичной мощности агрегатов и установок, развитию материальной и научно–технической базы автоматизации. На этом этапе, при управлении ТП человек–оператор все более занимается умственным трудом, выполняя разнообразные логические операции при пусках и остановах объектов, особенно при возникновении всевозможных непредвиденных обстоятельств, предаварийных и аварийных ситуаций, а также оценивает состояние объекта, контролирует и резервирует работу автоматических систем. На данном этапе формируются основы крупносерийного производства технических средств автоматизации, ориентированного на широкое применение стандартизации, специализации и кооперации. Широкие масштабы производства средств автоматизации и специфика их изготовления приводят к постепенному выделению этого производства в самостоятельную отрасль.
3. С появлением управляющих вычислительных машин (УВМ) начинается переход к этапу автоматизированных систем управления технологическими процессами (АСУТП), совпавший с началом научно–технической революции. На данном этапе становится возможной и экономически целесообразной автоматизация все более сложных функций управления, осуществляемая с использованием УВМ. Но, поскольку УВМ тогда были весьма громоздкими и дорогими, то для реализации более простых функций управления достаточно широко применялись и традиционные аналоговые устройства автоматики. Недостатком таких систем была их невысокая надежность, т.к. вся информация о ходе ТП поступает и обрабатывается УВМ, при выходе которой из строя, ее функции должен был взять на себя оператор–технолог, контролирующий работу АСУТП. Естественно, что в таких случаях качество управления ТП значительно снижалось, т.к. человек не мог осуществлять управление столь же эффективно, как УВМ.
4. Появление относительно недорогих и компактных микропроцессорных устройств позволило отказаться от централизованных систем управления ТП, заменив их распределенными системами, в которых сбор и обработка информации о выполнении отдельных взаимосвязанных операций ТП, а также принятие управленческих решений осуществляется автономно, локальными микропроцессорными устройствами, получившими название микроконтроллеров. Поэтому надежность распределенных систем значительно выше, чем централизованных.
5. Развитие сетевых технологий, позволившее связать в единую корпоративную сеть многочисленные и удаленные друг от друга компьютеры, с помощью которых осуществляется контроль и анализ финансовых, материальных и энергетических потоков при производстве предприятием продукции, а также управление ТП, способствовало переходу к интегрированным системам управления. В этих системах с помощью весьма сложного программного обеспечения совместно решается весь комплекс задач по управлению деятельностью предприятия, включая задачи учета, планирования, управления ТП и др.
6. Повышение быстродействия и других ресурсов микропроцессоров, используемых для управления ТП, позволяет в настоящее время говорить о переходе к этапу создания интеллектуальных систем управления, способных принимать эффективные решения по управлению предприятием в условиях информационной неопределенности, т.е. нехватке необходимой информации о факторах, влияющих на его прибыль.
Методы стандартизации и структура технических средств автоматизации. Экономика отрасли, производящей средства автоматизации требует достаточно узкой специализации предприятий, выпускающих крупные серии однотипных устройств. В то же время с развитием автоматизации, с появлением новых, все более сложных объектов управления и увеличением объема автоматизируемых функций возрастают требования к функциональному разнообразию устройств автоматизации и к разнообразию их технических характеристик и конструктивных особенностей исполнения. Задача уменьшения функционального и конструктивного многообразия при оптимальном удовлетворении запросов автоматизируемых предприятий решается при помощи методов стандартизации.
Решениям по стандартизации всегда предшествуют системные исследования практики автоматизации, типизация имеющихся решений и научное обоснование экономически оптимальных вариантов и возможностей дальнейшего сокращения многообразия применяемых устройств. Принимаемые при этом решения после их практической проверки оформляются обязательными к исполнению государственными стандартами (ГОСТ). Более узкие по сфере применения решения могут оформляться и в виде отраслевых стандартов (ОСТ), а также в виде имеющих еще более ограниченную применимость стандартов предприятий (СТП).
Агрегатирование – принцип формирования состава серийно изготавливаемых средств автоматизации, направленный на максимальное удовлетворение запросов предприятий–потребителей при ограниченной номенклатуре серийно выпускаемой продукции.
Агрегатирование базируется на том, что сложные функции управления можно разложить на простейшие составляющие (также, как, например, сложные вычислительные алгоритмы можно представить в виде совокупности отдельных простейших операторов).
Таким образом, агрегатирование основывается на разложении общей задачи управления на ряд простейших однотипных операций, повторяющихся в тех или иных комбинациях в самых различных системах управления. При анализе большого количества подобных систем управления можно выделить ограниченный набор простейших функциональных операторов, на комбинации которых строится практически любой вариант АСУТП. В результате формируется состав серийно изготавливаемых средств автоматизации, включающий такие конструктивно завершенные и функционально самостоятельные единицы, как блоки и модули, приборы и механизмы.
Блок – конструктивное сборное устройство, выполняющее одну или несколько функциональных операций по преобразованию информации.
Модуль – унифицированный узел, выполняющий элементарную типовую операцию в составе блока или прибора.
Исполнительный механизм (ИМ)– устройство для преобразования управляющей информации в механическое перемещение с располагаемой мощностью, достаточной для воздействия на объект управления.
В соответствии с принципом агрегатирования системы управления создаются путем монтажа модулей, блоков, приборов и механизмов с последующей коммутацией каналов и линий связи между ними. В свою очередь, сами блоки и приборы создаются также путем монтажа и коммутации различных модулей. Модули же собираются из более простых узлов (микромодулей, микросхем, плат, устройств коммутации и т.п.), составляющих элементную базу технических средств. При этом изготовление блоков, приборов и модулей осуществляется полностью в заводских условиях, в то время как монтаж и коммутация АСУТП полностью завершается лишь на месте ее эксплуатации. Такой подход к построению блоков и приборов получил название блочно–модульного принципа исполнения технических средств автоматизации.
Применение блочно–модульного принципа не только позволяет проводить широкую специализацию и кооперирование предприятий в рамках отрасли, производящей средства автоматизации, но и ведет к повышению ремонтопригодности и увеличению коэффициентов использования этих средств в системах управления. Обычно предприятия, выпускающие средства автоматизации промышленного назначения, специализируются на изготовлении комплексов или систем блоков и приборов, функциональный состав которых ориентирован на реализацию каких–либо крупных функций или подсистем АСУТП. При этом в рамках отдельного комплекса все блоки и приборы выполняются совместимыми по интерфейсу, т.е. совместимыми по параметрам и характеристикам сигналов–носителей информации, равно как и по конструктивным параметрам и характеристикам устройств коммутации. Принято называть такие комплексы и системы средств автоматизации агрегатными или агрегатированными.
В России производство средств автоматизации промышленного назначения осуществляется в рамках Государственной системы приборов и средств автоматизации промышленного назначения (или сокращенно ГСП). ГСП включает все средства автоматизации, отвечающие единым общим технологическим требованиям к параметрам и характеристикам сигналов–носителей информации, к характеристикам точности и надежности средств, к их параметрам и особенностям конструктивного исполнения.
Унификация средств автоматизации. Унификация – сопутствующий агрегатированию метод стандартизации, также направленный на упорядочение и разумное сокращение состава серийно изготовляемых средств автоматизации. Она направлена на ограничение многообразия параметров и технических характеристик, принципов действия и схем, а также конструктивных особенностей исполнения средств автоматизации.
Сигналы – носители информации в средствах автоматизации могут различаться как по физической природе и параметрам, так и по форме представления информации. В рамках ГСП применяются в серийном производстве средств автоматизации следующие типы сигналов:
- электрический сигнал (напряжение, сила или частота электрического тока);
- пневматический сигнал (давление сжатого воздуха);
- гидравлический сигнал (давление или перепад давлений жидкости).
Соответственно в рамках ГСП формируются электрическая, пневматическая и гидравлическая ветви средств автоматизации.
Наиболее развитой ветвью средств автоматизации является электрическая. В то же время широко используются и пневматические средства. Развитие пневматической ветви ограничивается относительно низкой скоростью преобразования и передачи пневматических сигналов. Тем не менее в области автоматизации пожаро- и взрывоопасных производств пневматические средства находятся, по существу, вне конкуренции. Гидравлическая ветвь средств ГСП не получила широкого развития.
По форме представления информации сигнал может быть аналоговым, импульсным и кодовым.
Аналоговый сигнал характеризуется текущими изменениями какого–либо физического параметра–носителя (например, мгновенными значениями электрического напряжения или тока). Такой сигнал существует практически в каждый данный момент времени и может принимать любые значения в пределах заданного диапазона изменений параметра.
Импульсный сигнал характерен представлением информации только в дискретные моменты времени, т.е. наличием квантования по времени. При этом информация представляется в виде последовательности импульсов одинаковой продолжительности, но различной амплитуды (амплитудно-импульсная модуляция сигнала) или одинаковой амплитуды, но разной продолжительности (широтно-импульсная модуляция сигнала). Амплитудно-импульсная модуляция (АИМ) сигнала применяется в тех случаях, когда значения физического параметра–носителя информации могут изменяться со временем. Широтно-импульсная модуляция (ШИМ) сигнала используется, если физический параметр–носитель информации может принимать лишь некоторое постоянное значение.
Кодовый сигнал представляет собой сложную последовательность импульсов, используемую для передачи цифровой информации. При этом каждая цифра может быть представлена в виде сложной последовательности импульсов, т.е. кода, а передаваемый сигнал является дискретным (квантуется) и по времени, и по уровню.
В соответствии с формой представления информации средства ГСП подразделяются на аналоговые и дискретно-цифровые. К последним относятся также средства вычислительной техники.
Все параметры и характеристики сигналов–носителей информации в средствах ГСП унифицированы. Стандартами предусматривается использование в аналоговых средствах следующих видов электрических сигналов:
- сигнал по изменению силы постоянного тока (токовый сигнал);
- сигнал по изменению напряжения постоянного тока;
- сигнал по изменению напряжения переменного тока;
- частотный электрический сигнал.
Сигналы постоянного тока используются чаще. При этом токовый сигнал (с большим внутренним сопротивлением источника) применяется для передачи информации в относительно длинных линиях связи.
Сигналы переменного тока редко используются для преобразования и передачи информации во внешних линиях связи. Это связано с тем, что при сложении и вычитании сигналов переменного тока необходимо выполнить требование синфазности, а также обеспечить подавление нелинейных искажений гармоник тока. В то же время при использовании этого сигнала легко реализуются задачи гальванического разделения электрических цепей.
Электрический частотный сигнал является потенциально наиболее помехоустойчивым аналоговым сигналом. В то же время получение и осуществление линейных преобразований этого сигнала вызывает известные затруднения. Поэтому частотный сигнал не получил широкого распространения.
Для каждого вида сигналов установлен ряд унифицированных диапазонов их изменений.
Стандарты на виды и параметры сигналов унифицируют систему внешних связей или интерфейс средств автоматизации. Такая унификация, дополненная стандартами на устройства коммутации блоков друг с другом (в виде системы разъемов), создает предпосылки для максимального упрощения проектирования, монтажа, коммутации и наладки технических средств систем управления. При этом блоки, приборы и прочие устройства с одинаковым типом и диапазоном параметров сигналов на входах–выходах стыкуются путем простого соединения разъемов.
Вопросы для самоконтроля:
1. В чем сущность принципа агрегатирования?
2. В чем заключается блочно–модульный принцип исполнения технических средств автоматизации?
3. Из чего собираются модули?
4. Что понимается под блоком?
5. Для чего предназначен исполнительный механизм?
ТЕСТ 1.
Из предложенных Вам ответов на данный вопрос выберите правильный.
1.1.Сколько существует этапов развития средств автоматизации?
а) 4.
б) 5.
в) 6.
1.2.Когда начинается этапавтоматизированных систем управления технологическими процессами (АСУТП)?
а) С появлением управляющих вычислительных машин.
б) С расширением масштабов производства.
в) С появлением автоматических регуляторов.
1.3. При помощи каких методов решается задача уменьшения функционального и конструктивного многообразия технических средств управления?
а)Методов стандартизации..
б) Методов безотказности.
в) Методов ремонтопригодности.
1.4.Что являетсянаиболее развитой ветвью средств автоматизации?
а) Электрическая.
б) Пневматическая.
в) Гидравлическая.
1.5. Какой вид сигналов представляет собой сложную последовательность импульсов?
а) Аналоговый.
б) Кодовый.
в) Импульсный.
ТЕМА 2. ТЕХНИЧЕСКИЕ СРЕДСТВА АВТОМАТИЗИРОВАННЫХ
СИСТЕМ УПРАВЛЕНИЯ
Структура комплекса АСУТП. Рассмотрим типовую структуру комплекса автоматизированной системы управления технологическими процессами (АСУТП), характерную для различных отраслей промышленного производства.
Эта структура должна содержать следующие подсистемы:
1. Полевое оборудование, включающее в себя интеллектуальные средства измерения, контроля, регулирующие отсечные и запорные клапаны, электроприводы.
2. Кабельные линии связи, кроссовое оборудование.
3. Барьеры искробезопасности, нормирующие преобразователи.
4. Программируемые контроллеры, модули ввода - вывода аналоговых и дискретных сигналов.
5. Операторские станции – компьютеры, устройства на магнитных носителях, мониторы, печатающие устройства и так далее.
6. Кабельные, оптоволоконные и радиоканалы связи.
7. Система пожарной автоматики и контроля загазованности.
8. Система бесперебойного электропитания.
При построении АСУТП 70 – 80 % стоимости приходится на полевое оборудование. При построении АСУТП рекомендуется максимально использовать приборы, максимально использовать интеллектуальное оборудование, использовать fieldbus.
Полевое оборудование. При строительстве новых объектов необходимо использовать современные интеллектуальные приборы. Необходимо сокращать разнообразие типов измерительных приборов и оценивать трудозатраты на их обслуживание.
Рассмотрим рекомендации по измерительным приборам:
1. Измерение температур. В качестве преобразователей температуры рекомендуется использовать измерительные преобразователи с токовым выходом 4 - 20 мА, работающие в комплекте с платиновыми терморезисторами или термопарами. Предпочтение надо отдавать измерителям, сделанным в единой сборке с чувствительным элементом и установленным непосредственно на объекте. Исключения могут составлять только преобразователи, работающие в агрессивной среде. Измерительные преобразователи должны иметь искрозащищенный выход 4 - 20 мА.
2. Измерение расхода. Используется метод измерения расхода с использованием диафрагмы. Измерение уровня производится буйковыми датчиками, ультразвуковыми, датчиками давления и т.д. В нефтегазовой промышленности используются сигнализаторы уровня и содержания воды в нефти. Сигнализаторы взрывоопасной концентрации газов, датчики содержания кислорода в дымовых газах.
3. Регулирующие отсечные клапаны. Применяемые клапаны по своему назначению делятся на три группы:
а) регулирующие;
б) отсечные в схемах блокировки;
в) отсечные, используемые для дистанционного управления в качестве запорных органов.
Кабели оптические.Как только не называют их, эти кабели! И волоконно-оптические, и оптиковолоконные, и файбер-оптик, и даже ВОЛС. Между тем, еще с начала семидесятых они носят красивое имя - оптические. И действительно, есть только два широких класса кабелей связи - электрические иоптические. (Это - как разделы физики: электричество и оптика, очень просто). И передают они, соответственно, электрические и оптические сигналы.
Задуманы оптические кабели очень давно, но не было подходящих материалов. Наконец, в начале 70-х годов, после многолетних и трудоемких поисков, было создано волокно с потерями света при передаче менее 20 дБ/км. С тех пор, около четверти века, оптоволокно покоряет просторы Земли на суше и на море.
Сначала были проложены соединительные линии между АТС в городах, а затем началось строительство междугородных и международных оптических кабельных магистралей. В последнее десятилетие массово строят морские и океанские межматериковые линии, причем Россия принимает в этом деле достаточно большое участие, чему наилучший пример – Транссибирская оптическая магистраль.
Рис. 2.1. Типичный световод.
Типичный световод состоит из сердцевины и оболочки. У сердцевины показатель преломления чуть-чуть больше, чем у оболочки, из-за чего световой луч испытывает практически полное внутреннее отражение на границе сердцевина-оболочка. Выполняется и сердцевина, и оболочка из кварцевого стекла. Поверх световода обычно накладывают несколько слоев защитных покрытий, улучшающих его механические и оптические характеристики. Световод со всеми этими покрытиями называют оптическим волокном. Делают световоды из полимерных материалов.
Конструкции световодов и оптических волокон очень много, но основных типов два: многомодовый и одномодовый. Диаметр сердцевины у многомодовых волокон в десятки раз превышает длину волны передаваемого излучения, из-за чего по волокну распространяется несколько типов волн (мод). Окна прозрачности кварца, из которого изготовлены световоды, находятся в области длин волн 0,85; 1,3; 1,55 мкм, а стандартные диаметры сердцевины многомодовых волокон - 50 и 62,5 мкм, вот и сравните!
У одномодового волокна диаметр сердцевины находится обычно в пределах 5-10 мкм (АТ&Т, например, стандартизировала 8,3 мкм). Это волокно называют одномодовым в соответствии со сложившейся традицией, т.е. условно: для того, чтобы по волокну передавался только один тип волны (одна мода), размер сердцевины должен быть еще меньше. Диаметр кварцевой оболочки световода тоже стандартизован и составляет 125 мкм.
Для связи на короткие расстояния чаще всего используют многомодовые волокна - они все же проще в монтаже и эксплуатации. На дальние расстояния употребляют одномодовые волокна - они имеют значительно меньшее затухание и уменьшенную дисперсию светового импульса, хотя их сложнее и монтировать, и эксплуатировать.
Параметр «затухание» характеризует ослабление мощности светового потока при передаче по оптическому волокну. Он подобен параметру электрических кабелей и также измеряется в дБ/км. Дисперсия импульса - это его «размывание» при распространении по оптоволокну. Поначалу высокий и стройный, импульс при передаче оседает и толстеет. Если два импульса расположены рядом, то по мере прохождения по волокну из-за дисперсии они наползают друг на друга и в конце концов перестают различаться Дисперсия импульса зависит от затухания, микронеоднородностей, микротрещин, от внутренней структуры материала световода и еще от многих-многих факторов, о которых уже написано множество статей и диссертаций.
Рис. 2.2. Конструкция сложного оптического кабеля.
Световые импульсы образуются при модуляции источника излучения - лазера или светодиода. Для передачи от источника к волокну очень важна апертура, т. е. действующий раскрыв на входе световода. Апертура зависит от размера сердцевины волокна и от согласования источника с оптоволокном. При неудачном согласовании лишь небольшая доля мощности от передатчика попадает в световод, а остальная энергия отражается. Наоборот, если апертура хорошо согласована с источником, то такое сочетание очень эффективно: вся энергия попадает в световод.
Голый световод плохо переносит всяческие воздействия - изгибы растяжения, влагу, и поэтому его покрывают защитными материалами (лаками, пластиками), окружают кевларовыми волокнами. И хотя сам световод имеет диаметр 125 мкм, с покрытиями его размер достигает 0,5 мм и более. В таком виде оптоволокно уже можно помещать в кабель теперь оно сможет противостоять внешним воздействиям. При конструировании кабеля принимают еще дополнительные меры по защите волокон: упрятывают оптические волокна в толстые пластиковые трубки, рядом укладывают упрочняющие стальные и пластмассовые стержни, а весь внутренний объем кабельной оболочки часто заполняют гидрофобным (водоотталкивающим) материалом или толстыми и прочными пучками пластиковых волокон.
Конструкции оптических кабелей различны. Встречаются кабели с небольшим количеством волокон. Но чаще они представляют собой сложные агрегаты, содержащие множество оптических волокон, помещенных в специальные модули, дополненные еще различными несущими, защитными, питающими и другими элементами (рис. 2.3) Все зависит от назначения оптического кабеля. Есть конструкции, где оптические волокна лежат свободно в трубках и "звездочках", но есть и такие, где они крепко зажаты в прозрачной ленте из пластмассы. В линиях связи широко применяются оба типа кабеля.
Рис. 2.3. Конструкция оптического кабеля.
Крайне важна заделка оптоволокна в разъем - ведь от этого зависит эффективность перехода световых импульсов в местах соединений. Поэтому во всех инструкциях по волоконно-оптическим линиям связи на подготовку и заделку оптических разъемов обращают особое внимание. Заделанный в разъеме конец оптоволокна герметизируют клеем, эпоксидной смолой или другим заполнителем. Затем пристальное внимание обращается обычно на радиус изгиба оптического кабеля. При недостаточно большом радиусе изгиба увеличивается затухание тракта, а при слишком маленьком возможны поломки световедущих частей оптических кабелей.
Рис. 2.4. Заделка оптоволокна в разъем.
Операция по изгибанию оптического кабеля выполняется не как с медными кабелями (просто в пространстве), а на специальной полке, где аккуратно изогнутые кольца и петли из оптического кабеля тщательно закрепляют. Само собой разумеется, что и соединители для оптических линий изготавливают более тщательно, чем обычные, а заделку в них оптоволокна выполняют часто под микроскопом, оснащенным хорошим дисплеем.
Итак, теперь мы представляем себе, что такое оптическое волокно и оптический кабель. Каковы же их возможности по передаче информации? Уже давно и успешно по оптоволокну передают потоки в 155 Мбит/с - в системах связи это первая ступень синхронной цифровой иерархии. Недавно освоили вторую ступень - 622 Мбит/с и быстро осваивают третью - 2,5 Гбит/с (в России такая оптическая линия намечена между Москвой и Петербургом). Поговаривают и о четвертой ступени (10 Гбит/с), но действующих линий с таким темпом нет.
Честно говоря, когда думаешь о подобных потоках информации - дух захватывает. Но ведь еще недавно мы только мечтали о 100 Мбит/с, а теперь это уже пройдено. Со временем потребности людей и компьютеров растут!
Распределенные системы управления. Распределенная система управления состоит из нескольких компонент – одна или несколько операторских станций и несколько станций управления. Рассмотрим функции, выполняемые операторской станцией:
1. Отображение информации об управлении технологическим объектом на экране, ввод команд при помощи клавиатуры, печать отчетов о состоянии технологического объекта.
2. Регистрация отклонений параметров технологического объекта.
3. Выполнение математических расчетов, долговременное хранение информации, обмен информацией со станциями управления и обмен с вышестоящими системами управления.
Станции управления технологическим процессом выполняют следующие функции:
1. Ввод сигналов от датчиков, установленных на объекте управления.
2. Логическая или арифметическая обработка сигналов, вывод управляющих воздействий.
3. Регулирование, включение – выключение.
В качестве аппаратуры для построения операторских станций рекомендуется использовать компьютеры на базе процессоров Intel (IBM совместимые компьютеры). Компьютеры IBM делятся на две группы: офисные и промышленные. Промышленные компьютеры имеют конструкцию, защищающую их от вредных воздействий окружающей среды ( колебания температуры, запыленность и загазованность воздуха, вибрации и так далее ). Вследствие этого промышленные компьютеры стоят дороже офисных. В настоящее время на рынке очень много различных компьютеров. Одно из существенных их различий – тип шины. Есть шины офисные и промышленные. В таблице 2.1 приведены стандарты различных шин.
Таблица 2.1. Стандарты шин.
Тип шины | Фирма изготовитель | Площадь печатной платы (кв. дюймы) | Разрядность, бит | Скорость обмена, Mb/s | Поддержка многопроц. |
ISA | Intel | 62 | 16 | 8 | нет |
EISA | Intel | 62 | 32 | 32 | да |
STD | Intel | 26 | 8/16 | 4 | нет |
STD 32 | Intel | 26 | 32 | 32 | да |
VME | Motorola | 24 | 16 | 20 | да |
Шина STD 32.Эта шина является аналогом шины EISA. На этой шине строятся промышленные компьютеры. Она имеет другой формат печатной платы и другие разъемы (для большей надежности). Конкурентом является шина VME (Motorola).
Программируемые контроллеры, используемые в станции управления, должны отвечать следующим требованиям:
1. Контроллеры должны иметь модульную структуру и набор модулей различной производительности. Они должны иметь различное число входов и выходов – от 5 - 10 до 1000 - 2000.
2. Они должны иметь в своем составе модули ввода - вывода для аналоговых дискретных сигналов.
3. Должны иметь в своем составе коммуникационные модули, позволяющие использовать различные каналы связи для обмена данными.
4. Должны работать в тяжелых производственных условиях. Рабочий диапазон температур: - 40 - +50 градусов Цельсия. Должны иметь низкую стоимость и иметь систему автоматизации программирования.
Наиболее полно этим требованиям удовлетворяют контроллеры фирм Control Microsystems (Канада) с контроллером “ Telesafe “ и Koya (Япония) с контроллером “Direct logic”.
Программное обеспечение АСУТП.Программное обеспечение современной АСУТП должно состоять из следующих компонент:
1. Операционная система реального времени для ПЛК ( программного логического контроля ).
2. Система программирования и отладки прикладных программ для ПЛК.
3. Комплекты прикладных программ для ПЛК, реализующих функции для конкретной АСУТП.
4. Операционные системы для промышленного компьютера.
5. Системы для конфигурирования и выполнения на промышленном компьютере функций человеко-машинного интерфейса, сбора, обработки данных и супервизорного управления конкретным технологическим объектом. Эти системы программирования называются системами SCADA.
Наличие современной системы программирования является одним из самых главных факторов при выборе базиса построения АСУТП.
Система программирования должна позволять:
1. Написание программ на технологических языках высокого уровня. Для непрерывных процессов – это язык функциональных блоков, а для последовательных алгоритмов – это язык лестничных схем.
2. Система программирования должна выполняться под Windows, иметь режим отладки, позволяющий производить выполнение программы по ее исходному тексту.
3. Система должна позволять записывать в память контроллера через каналы связи все изменения в программе без ее остановки.
Исполнительные механизмы.Исполнительные механизмы (ИМ) являются одними из последних звеньев систем автоматического регулирования и управления и обычно предназначены для управления регулирующими органами, непосредственно воздействующими на режимы работы объектов управления. Регулирующими органами могут быть различного рода дроссельные заслонки, клапаны, задвижки, шиберы, направляющие аппараты и другие элементы, способные производить изменение количества энергии или рабочего вещества, поступающего в объект управления. При этом перемещение рабочих органов может быть как поступательным, так и вращательным в пределах одного или нескольких оборотов.
В промышленном и сельскохозяйственном производстве можно встретить самые разнообразные по своей природе потоки веществ, и для каждого применяется соответствующий его характеру регулирующий орган.
Для твердых веществ штучного вида (например, корнеклубнеплоды) используются скребковые или ленточные питатели, для волокнистых веществ (солома, силос) – биттерные питатели, для мелких хорошо сыпучих (зерно, гранулы) – тарельчатые питатели и заслонки. Потоки смесей твердых веществ различной консистенции регулируют специальными устройствами, например, двух вальными шнеками.
Устройства для регулирования потока жидких веществ выбирают в зависимости от их вязкости. Для тестообразных (навоз, кормосмеси) используют шнековые или скребковые питатели, для полужидких (кормосмеси 70 % влажности) – насосные установки, для жидких (вода) – насосы, клапаны, задвижки.
Потоки газообразных веществ регулируют включением или отключением компрессорных или вентиляционных установок, а также при помощи газовых клапанов, заслонок и т.д.
Энергетические потоки и воздействия регулируют по видам энергии следующими устройствами:
1. Механическими – редукторами, вариаторами, муфтами;
2. Электрическими – автотрансформаторами, электронными усилителями;
3. Тепловыми – через устройства массообмена.
Наиболее часто регулирующий орган является неотъемлемой частью самого ИМ и рассматривается как единое вместе с ним устройство. В других случаях регулирующий орган установлен на объекте управления и является его составной частью.
Расположение ИМ в общей функциональной схеме аналоговой системы управления по отклонению показано на рис. 2.5.
![]() |
Рис. 2.5.
В общем случае ИМ состоит (рис. 2.6) из совокупности следующих элементов: исполнительного двигателя – источника силового воздействия на рабочий орган; передаточного или преобразовательного устройства - предназначенного для получения определенной скорости, направления и характера перемещения рабочего органа, располагающегося между исполнительным двигателем и рабочим органом; конечных выключателей - ограничивающих перемещения рабочего органа и фиксирующих его крайние положения в схемах управления и автоматического регулирования; элементов управления (пускателей, реле, золотников, клапанов и др.), защиты (предохранительных и переливных клапанов, муфт ограничения крутящего момента и др.), сигнализации и контроля (дистанционных указателей положения и др.).
Рис. 2.6. Функциональная схема исполнительного механизма.
Принято различать ИМ по следующим признакам:
1. По виду математического описания:
а) линейные;
б) нелинейные.
2. По виду сигналов:
а) непрерывные;
б) релейные;
в) вибрационные.
3. По виду используемой энергии:
а) электрические;
б) пневматические;
в) гидравлические;
г) комбинированные.
Следует отметить, что к ИМ обычно предъявляются весьма жесткие требования, т.к. условия эксплуатации управляемых производственных объектов зачастую далеки от идеальных (широкие пределы изменения влажности и температуры, наличие примесей, пыли, агрессивных газов, воздействие резко переменных нагрузок, вибраций и т. п.).
Вопросы для самоконтроля:
1. С помощью каких устройств регулируют потоки газообразных веществ?
2. С помощью каких устройств регулируют энергетические потоки?
3. Из каких элементов состоит исполнительный механизм?
4. По каким признакам принято различать исполнительные механизмы?
5. Какие требования предъявляются к исполнительным механизмам?
ТЕСТ 2.
Из предложенных Вам ответов на данный вопрос выберите правильный.
2.1.Какой вид оптического кабеля используют для связи на короткие расстояния?
а) Одномодовые волокна.
б) Многомодовые волокна.
в) Инфра-волокна..
2.2.Какова пропускная способность оптоволоконной линии между Москвой и Петербургом?
а) 622 Мбит/c.
б) 2.5 Гбит/c.
в) 10 Гбит/c.
2.3.Для чего предназначены исполнительные механизмы?
а) для управления регулирующими органами.
б) для внесения изменений в работу контроллера..
в) для сбора информации.
2.4.Какие наиболее важные требования предъявляют к исполнительным механизмам?
а) компактность.
б) устойчивая работа в агрессивных условиях (широкие пределы изменения влажности и температуры, наличие примесей, пыли).
в) энергосбережение.
2.5 Чем регулируют потоки газообразных веществ?
а) включением или отключением компрессорных или вентиляционных установок.
б) автотрансформаторами.
в) редукторами.
ТЕМА 3 ЭЛЕКТРОДВИГАТЕЛЬНЫЕ ИСПОЛНИТЕЛЬНЫЕ
МЕХАНИЗМЫ
Виды электродвигательных ИМ. Электродвигательные ИМ (ЭИМ) получили наибольшее распространение в системах промышленной и сельскохозяйственной автоматики. Чаще всего в ЭИМ малой мощности (до 1000 Вт) применяются двухфазные асинхронные двигатели или двигатели постоянного тока, а в более мощных – трехфазные с короткозамкнутым или фазным ротором. Для уменьшения выбега двигателя и улучшения качества регулирования используется электрическое торможение. Конструктивно ЭИМ обычно выполняют с вращательным движением выходного вала и реже – с поступательным перемещением выходного штока.
В зависимости от типа регулирующего органа различают однооборотные, многооборотные, шаговые и постоянно вращающиеся ЭИМ. Однооборотные - с углом поворота выходного вала до 360° применяют обычно в приводе таких регулирующих органов, как заслонки, краны, шибера и т.п. Многооборотные - используют для перемещения регулирующих органов в форме запорных вентилей, дросселей и задвижек. Выходной вал у них может совершать большое число оборотов и одновременно поступательно перемещать регулирующие органы. Шаговые – применяют для преобразования импульсных сигналов управления в фиксированный угол поворота, т.е. на каждый импульс механизм делает строго заданный угловой шаг. У постоянно вращающихся - крутящий момент от вала электродвигателя к регулирующему органу передается обычно через электромагнитную муфту. Направление и скорость вращения выходного вала муфты регулируют, изменяя ток возбуждения муфты.
Основными техническими требованиями, предъявляемыми к ЭИМ, являются:
- статическая устойчивость и линейность механических характеристик во всем диапазоне изменения управления;
- линейная зависимость угловой скорости вращения ротора от величины управляющего сигнала во всем рабочем диапазоне;
- высокое быстродействие по отношению к динамическим параметрам объекта управления;
- большой пусковой момент;
- малая мощность управления при значительной механической мощности на валу электродвигателя;
- отсутствие самохода, т.е. малый остаточный вращающий момент при отсутствии сигнала управления;
- высокая надежность;
- малые габариты, размеры и масса;
- высокие эксплуатационные свойства (КПД, ресурс работы).
Электродвигатели постоянного тока. Двигатели постоянного тока ЭИМ наиболее полно удовлетворяют требованиям, предъявляемым к исполнительным элементам систем. Для стационарных объектов сельскохозяйственного производства эти ИМ применяются ограниченно, в основном в единичных случаях. В сельском хозяйстве, например, они широко используются только при управлении мобильными машинами и агрегатами.
По способу возбуждения двигатели делятся на исполнительные двигатели с электромагнитным возбуждением и с возбуждением от постоянных магнитов. Двигатели с электромагнитным возбуждением выполняются с независимым, последовательным и смешанным возбуждением. Из всего многообразия исполнительных двигателей постоянного тока необходимо выделить бесколлекторные двигатели и двигатели с печатной обмоткой якоря. Управление двигателями постоянного тока может быть непрерывным и импульсным.
Электродвигателем постоянного тока с независимым возбуждением можно управлять как со стороны якоря, так и со стороны обмотки возбуждения. При управлении электродвигателем со стороны якоря обмотка возбуждения запитывается неизменным напряжением постоянного тока и создает постоянный поток возбуждения. К якорной цепи электродвигателя подводится управляющее напряжение постоянного тока. При управлении электродвигателем со стороны обмотки возбуждения цепь якоря питается от сети неизменным напряжением постоянного тока, а управляющее напряжение, создающее регулируемый поток возбуждения, подается на обмотку возбуждения. При этом способе управления требуется меньшая мощность сигнала цепи управления, что позволяет использовать в качестве оконечных усилителей электронные, магнитные, полупроводниковые и другие маломощные усилители.
К недостаткам управления электродвигателем со стороны обмотки возбуждения относятся малый диапазон изменения скорости, нелинейность статических характеристик, увеличение порядка уравнения движения электродвигателя и регулирование скорости только в сторону ее увеличения.
В системах автоматического управления широкое распространение получил способ управления двигателем со стороны якоря, так как он позволяет получить широкий диапазон регулирования скорости, плавность регулирования, относительную линейность статических характеристик, большее быстродействие.
К исполнительным двигателям с якорным управлением относятся двигатели с постоянными магнитами. Их статические характеристики аналогичны характеристикам двигателя с электромагнитным возбуждением при якорном управлении. Преимущество двигателей с постоянными магнитами состоит в том, что они не требуют источника питания обмотки возбуждения, имеют больший КПД и быстродействие, магнитный поток практически не зависит от температуры двигателя. Особо высокие показатели по быстродействию у двигателей с полым немагнитным якорем, в который впрессована обмотка управления. К недостаткам двигателей с постоянными магнитами относятся старение магнитов, используемых для полюсов. В настоящее время выпускается большая серия двигателей с постоянными магнитами ДПМ.
Для увеличения быстродействия исполнительных двигателей применяют двигатели постоянного тока с плоским якорем (серия ПЯ), на котором обмотка нанесена печатным способом - рис.3.1.
Рис. 3.1. Электродвигатель постоянного тока с печатной обмоткой якоря.
Электрическая машина выполняется не с цилиндрическим воздушным зазором, а с плоским. Якорь 1 представляет собой тонкий диск, выполненный из немагнитного материала (текстолита, алюминия), с обеих сторон которого находятся проводники - обмотка 2. Отдельные проводники соединяются друг с другом через сквозные отверстия в диске 3. Электродвигатели с печатной обмоткой мощностью до 200 Вт не имеют специального коллектора. Роль коллектора выполняют активные части проводников, находящихся на одном торце диска. По поверхности торца диска скользят серебряно-графитовые щетки 4. Возбуждение двигателя осуществляется постоянным магнитом с полюсными наконечниками 5, имеющими форму кольцевых сегментов. Иногда оно может осуществляться и электромагнитами. Магнитный поток возбуждения проходит аксиально через два воздушных зазора, немагнитный диск с печатной обмоткой и замыкается по кольцам из магнитомягкой стали 6. При протекании тока по обмотке на валу двигателя создается вращающий момент, расположенный в плоскости диска якоря.
Так как секции печатной обмотки одновитковые, а количество секций ограничено размерами диска, то электродвигатели с печатной обмоткой выполняют обычно на низкое напряжение сети. Для увеличения мощности электродвигателя в некоторых конструкциях применяют многодисковое исполнение якоря. Тогда электродвигатель представляет собой совокупность нескольких электрических машин, собранных в одной магнитной системе.
Для обеспечения демпфирования якорь выполняют из немагнитного проводящего материала - алюминия. Вихревые токи в теле якоря образуют тормозной момент, пропорциональный скорости вращения. Между обмоткой и диском устанавливается почти полное потокосцепление, следовательно, индуктивность обмотки практически равна нулю и сопротивление является чисто активным.
Электромеханическая постоянная времени за счет малого момента инерции дискового якоря снижается до 0,01...0,02 с, что является одним из основных преимуществ рассматриваемых двигателей. Кроме того, из-за незначительной индуктивности обмотки якоря коммутация не сопровождается искрением. Проводники печатной обмотки находятся в значительно лучших условиях охлаждения, чем проводники, уложенные в пазы обычного якоря. Это позволяет повысить плотность тока в них и управлять электродвигателем с помощью полупроводниковых усилителей. Механизированное изготовление обмоток якоря удешевляет электродвигатель.
К недостаткам таких электродвигателей по сравнению с обычным двигателем следует отнести более низкий КПД из-за увеличения магнитного зазора машины, ограниченную долговечность вследствие износа контактирующей поверхности проводников обмотки якоря и критичность к перегрузкам по току вследствие ограничения допустимой плотности тока через печатные обмотки, что в ряде случаев ведет к усложнению схемы управления электродвигателями.
Одним из существенных недостатков исполнительных двигателей постоянного тока является наличие скользящего контакта между щетками и коллектором, создающего искрение и радиопомехи. Надежность двигателей относительно низка из-за быстрого износа щеток, особенно при высоких скоростях вращения якоря. Существуют условия эксплуатации, когда коллекторные двигатели постоянного тока неприменимы. С целью устранения названных недостатков щеточно-коллекторный узел двигателя постоянного тока заменяют более надежной полупроводниковой схемой, управляемой сигналами датчика углового положения ротора. Бесколлекторный электродвигатель постоянного тока состоит (рис. 3.2) из двигателя (Д), полупроводникового коммутатора (К) и датчика углового положения ротора (ДП).
Рис. 3.2. Структурная и электрическая схемы бесколлекторного двигателя
постоянного тока.
В отличие от коллекторного двигателя постоянного тока бесконтактный двигатель имеет обмотку якоря на статоре I и систему возбуждения с постоянными магнитами на роторе II. Ротор выполняется, как правило, явно полюсным с одной парой полюсов из постоянного магнита. Обмотка состоит из трех секций, соединенных в звезду. И подключенных к транзисторному коммутатору. С осью ротора двигателя жестко связан якорь датчика углового положения III с тремя чувствительными элементами 1, 2, 3, расположенными друг относительно друга под углом 120 электрических градусов. Чувствительные элементы датчика управляют токами баз транзисторов VT1, VT2, VT3 полупроводникового коммутатора IV.
В положении ротора, указанном на схеме, якорь датчика углового положения взаимодействует с чувствительным элементом 1, который поддерживает в открытом состоянии транзистор VT1. Ток, протекающий по статорной обмотке 1, взаимодействует с полем постоянного магнита, в результате чего к ротору прикладывается момент, направленный по часовой стрелке. Под воздействием этого момента ротор двигателя вращается в том же направлении, увлекая за собой якорь датчика. Обмотка 1 подключена к источнику питания U на интервале 120 электрических градусов, совпадающим с угловым размером сектора якоря датчика положения ротора. После поворота на 120 электрических градусов происходит отключение обмотки 1 и подключение обмотки 2, так как якорь датчика углового положения взаимодействует с чувствительным элементом 2, который открывает транзистор VT2 коммутатора. Таким образом, поворот ротора на 120 электрических градусов приводит к скачкообразному перемещению поля статора. Вращение ротора будет продолжаться потому, что происходит последовательное подключение обмоток статора электродвигателя к источнику питания, что обеспечивается благодаря воздействию на коммутатор сигнала обратной связи, снимаемого с датчика углового положения ротора.
Тип обмотки статора электродвигателя и способ ее подключения к источнику электропитания определяют количество переключающих транзисторов коммутатора, а также число чувствительных элементов датчика ДП. Для уменьшения пульсаций момента на валу двигателя за один оборот количество обмоток должно быть большим. Чем больше число обмоток, тем лучше пусковые свойства и равномернее работа машины. Возрастание количества обмоток приводит к увеличению числа чувствительных элементов датчика положения и полупроводникового коммутатора. Поскольку элементы коммутатора имеют меньшую надежность по сравнению с другими частями электродвигателя, а масса и габариты коммутатора соизмеримы с массой и габаритами двигателя, то для электродвигателей небольшой мощности целесообразно применение двух - трех обмоток.
В рассматриваемых двигателях возможна однополупериодная коммутация, при которой ток по обмотке протекает в одном направлении и двухполупериодная коммутация, когда ток по обмотке меняет направление, т.е. обмотка используется в течение полного оборота ротора.
Двигатели с реверсивным питанием имеют преимущество перед аналогичными двигателями с нереверсивным питанием, обусловленное лучшим использованием меди обмоток и активных частей и более высоким КПД. Однако усложнение схемы коммутатора (количество элементов возрастает вдвое и конструкции датчика положения такого двигателя по сравнению с нереверсивным заставляют отдавать ему предпочтение только в тех случаях, когда предъявляются высокие требования к габаритам, массе, величине пульсаций момента и значению КПД двигателя. Для электродвигателей малой мощности более рациональна однополупериодная коммутация.
Обмотка статора бесконтактного электродвигателя может выполняться либо замкнутой, либо разомкнутой. Замкнутая обмотка требует двухполупериодного питания, что усложняет коммутирующее устройство, но улучшает использование материала двигателя. В бесконтактном двигателе постоянного тока можно выделить две цепи, воздействующие на коммутатор. Первая цепь - источник питания транзисторов U, вторая - обратная связь, идущая с датчика положения ротора и воздействующая на базу того или иного транзистора. Отсюда вытекают два способа управления скоростью двигателя: путем изменения напряжения U источника питания и путем воздействия на сигнал обратной связи двигателя.
Реверсирование двигателя может быть осуществлено полупроводниковым коммутатором путем взаимного переключения начала и концов обмоток либо путем переключения чувствительных элементов датчика положения или входных цепей транзисторов.
Таким образом, наряду с основной функцией переключения обмоток по сигналам датчика положения полупроводниковый коммутатор регулирует скорость вращения ротора, осуществляет реверс, пуск и остановку двигателя. Цепи коммутации обмоток статора могут быть выполнены на транзисторных, тиристорных и магнитно-транзисторных ключах.
Одним из основных узлов бесколлекторных двигателей постоянного тока является датчик углового положения ротора. В качестве таких датчиков могут применяться магниторезисторы, датчики Холла, радиоактивные элементы, емкостные, трансформаторные, индуктивные датчики, фоточувствительные устройства.
Датчики положения ротора должны удовлетворять требованиям бесконтактности, высокой надежности, малой массы и габаритов, стабильности выходного сигнала, высокой чувствительности к угловому положению ротора, малому потреблению энергии и хорошему согласованию с входными цепями коммутатора.
Применение бесконтактных коммутаторов обмоток двигателя постоянного тока приводит к более высокой стоимости и большим габаритам по сравнению с коллекторными двигателями той же мощности. Однако возрастание габаритов и стоимости оправдывается увеличением срока службы и надежности бесколлекторных двигателей постоянного тока.
Шаговые исполнительные двигатели. шаговым двигателем называется электродвигатель с прерывистым вращением ротора под действием дискретного электрического сигнала, подаваемого на обмотки управления. в качестве шаговых двигателей получили широкое распространение многофазные синхронные двигатели с активным (возбуждением) и реактивным (невозбужденным) ротором. шаговые двигатели отличаются от обычного синхронного в основном формой напряжения, подводимого к фазным (управляющим) обмоткам. шаговые двигатели применяются с электронным коммутатором, который подает на обмотки управления прямоугольные импульсы. последовательность подключения обмоток и частота импульсов соответствует заданной команде. каждому импульсу управления соответствует поворот ротора на фиксированный угол, называемый шагом двигателя, величина которого строго определена его конструкцией и способом переключения обмоток. скорость вращения пропорциональна частоте, а суммарный угол поворота - числу импульсов управления. при изменении последовательности подключения к обмоткам управляющих импульсов по произвольному закону шаговый двигатель работает в режиме слежения, воспроизводя сложное движение с точность до одного шага. шаговый двигатель совместно с коммутатором можно отнести к системам частотного регулирования синхронного электродвигателя с возможностью изменения частоты до нуля. при снятии управляющих импульсов шаговый двигатель фиксирует конечные координаты углового перемещения с точностью до долей шага без применения датчиков обратной связи, что упрощает систему управления. в сельском хозяйстве эти двигатели им применяются в основном в составе сау технологическими производственными процессами, аналогичным промышленности (например, микроклимат, тепловые процессы и др.).
Рассмотрим принцип действия и особенности основных физических процессов шаговых двигателей на примере двухфазной двухполюсной синхронной машины с активным ротором.
При подаче постоянного напряжения указанного знака на фазу А (рис. 3.3) возникает намагничивающая сила статора FА, которая в результате взаимодействия с полем постоянного магнита ротора создает синхронизирующий момент. Под действием этого момента ротор займет положение, при котором его ось совпадет с осью фазы А. При отключении фазы А и подключении фазы В вектор намагничивающей силы статора повернется на 90° по часовой стрелке, возникнет синхронизирующий момент, под действием которого ротор вновь повернется на 90°. Для следующего поворота ротора на 90° по часовой стрелке необходимо подать на фазу А напряжение противоположного знака и т. д.
Рис. 3.3. К принципу действия двухфазного шагового двигателя.
При рассмотренном способе переключения обмоток, который можно представить в виде последовательности +А, +В, -А, -В, шаг двигателя равен 90°. Шаг двигателя можно уменьшить в два - раза, если переключение обмоток выполнить в другой последовательности: (+А), (+А, +В), (+В), (+В, -А), (-А), (-А, -В), (-В), (-В, +А), т. е. на некоторых шагах происходит подключение двух фаз одновременно. Такая коммутация фаз уменьшает шаг до 45°.
Управление шаговым двигателем может быть однополярным или pазнополяpным, симметричным или несимметричным, потенциальным или импульсным. При однополярном управлении напряжение, подводимое к фазе, изменяется только по величине от нуля до +U. Разнополярное управление предполагает изменение напряжения от -U до +U. Управление называется симметричным, если для каждого устойчивого состояния возбуждается одинаковое количество фаз. Если возбуждается разное число обмоток, то управление будет несимметричным. В рассмотренном примере шагового двигателя управление является разнополярным симметричным при шаге 90° и несимметричным при шаге 45°.
При потенциальном управлении напряжение на обмотках изменяется только в моменты поступления управляющих импульсов. В отсутствие сигнала управления обмотки находятся под постоянным напряжением, которое фиксирует положение ротора. При импульсном управлении обмотки статора находятся под напряжением только в моменты поворота ротора, а затем напряжение снимается и ротор фиксируется в определенном положении реактивным моментом.
Способ управления шаговым двигателем оказывает влияние на сложность электронного коммутатора. Для простоты схемы электронного коммутатора наиболее удобной является потенциальная схема управления с симметричной однополярной коммутацией обмоток.
Шаговый двигатель с электронным коммутатором характеризуется рядом величин, определяющих возможности его применения:
1. Числом устойчивых электрических состояний n, которое кратно или равно числу управляющих обмоток m. Так n = m используется при однополярной коммутации и симметричном способе управления. n = 2*m при разнополярной коммутации с симметричным управлением или при однополярной коммутации для несимметричного способа управления. n = 4*m для несимметричной разнополярной коммутации. Разделение фазной обмотки на две секции с поочередным включением секций позволяет увеличить число устойчивых состояний. В многополюсной электрической машине число n возрастает пропорционально числу пар полюсов ротора.
2. Механическим шагом двигателя - это углом между двумя устойчивыми соседними состояниями
a = 2 p/ (n p),
где: n - число устойчивых состояний; р - число пар полюсов ротора. Этот же угол в электрических градусах будет равен
aэ = a×p =2 p / (n×p).
3. Синхронизирующим моментом – зависимостью момента, развиваемого двигателем, от углового положения ротора. Для шаговых двигателей с симметричным ротором эта функция близка к синусоиде. Пусковым моментом является максимальный момент нагрузки, при котором двигатель на очередном цикле коммутации вращается без потери шага. Этот момент равен ординате точки пересечения кривых синхронизирующего момента для двух устойчивых соседних состояний. Интервал значений углового положения ротора, в пределах которого ротор возвращается в исходное положение, является зоной статической устойчивости двигателя. Эта зона равна (-p)...(p) для двигателя с симметричным ротором.
4. Частотой приемистости fn – максимальной частотой следования импульсов управления, при которой двигатель входит в синхронизм без потери шага. Частота приемистости пропорциональна динамической добротности шагового двигателя, определяемой отношением -Mп/J, и обратно пропорциональна шагу двигателя. При одной и той же добротности и величине шага частота приемистости растет с увеличением числа обмоток управления. Это объясняется тем, что при пуске ротор за первые тактовые импульсы может отрабатывать не полные шаги, а вращаться с некоторым запаздыванием относительно магнитодвижущей силы статора, оставаясь в пределах зоны устойчивости при каждом очередном переключении обмоток управления. Частота приемистости зависит от момента нагрузки на валу и электромагнитной постоянной времени обмоток управления.
5. Электромагнитной постоянной времени, определяемой отношением индуктивного сопротивления обмотки управления к ее активному сопротивлению.
6. Собственной частотой колебаний wо, которой называется угловая частота колебаний ротора двигателя около устойчивого положения при отсутствии момента нагрузки. Знание wо необходимо при определении частоты управляющих импульсов, при которой возможно явление резонанса. При резонансе амплитуда колебаний ротора резко возрастает, и двигатель выпадает из синхронизма.
7. Механической характеристикой шагового двигателя, которой называется зависимость момента, развиваемого двигателем, от частоты управляющих импульсов. Механическая характеристика имеет падающий характер, так как с ростом частоты сказывается запаздывание в нарастании тока за счет индуктивности обмоток управления. На некоторой предельной частоте момент двигателя становится равным нулю.
Наряду с магнитоэлектрическими шаговыми двигателями с активным ротором находят широкое применение индукторные и реактивные двигатели.
Индукторные шаговые двигатели имеют ферромагнитный ротор из магнитомягкой электротехнической стали. На роторе находятся равномерно расположенные зубцы zp, на статоре - гребенчатые зубцовые зоны, смещенные относительно друг друга на угол 2×p/(m×zp).
Ротор возбуждается со стороны статора постоянной составляющей тока в фазах. Возбуждение ротора может осуществляться также постоянными магнитами статора или отдельной обмоткой возбуждения .
Реактивные шаговые двигатели по конструкции аналогичны индукторным, однако они не имеют возбуждения ее стороны статора. Статор трехфазного реактивного шагового двигателя имеет шесть полюсных выступов с гребенчатыми зубцовыми зонами (рис. 3.4). Обмотки управления могут иметь два независимых вывода или соединяются в звезду с выведенной общей точкой.
Особенность реактивного шагового двигателя состоит в том, что потоки, образованные постоянными составляющими тока в обмотках управления, не замыкаются через воздушный зазор и не участвуют в электромеханическом преобразовании энергии. Трехфазные реактивные шаговые двигатели допускают как однополярную, так и разнополярную, симметричную и несимметричную коммутации.
Рис. 3.4. Схема конструктивного исполнения реактивного редукторного
шагового двигателя.
Для увеличения быстродействия шагового двигателя уменьшают шаг двигателя путем использования электромагнитной редукции. Размеры зубцов ротора равны размерам зубцов статора. Одна пара зубцов ротора coocна с зубцами одной пары полюсных выступов статора, а остальные зубцы ротора смещены на l/p часть зубцового деления по отношению к зубцам других пар полюсных выступов. При поступлении очередного сигнала управления происходит поворот м.д.с. статора на 60° и реактивный момент поворачивает ротор на 1/3 зубцового деления в положение наибольшей магнитной проводимости относительно возбужденной пары полюсов, т. е. на угол, значительно меньший угла поворота м.д.с. Например, при zp = 60° с числом пар полюсов статора, равным трем, угол поворота ротора будет
a = 2p/(n×p) = 360°/(3×60°) = 2°.
Уменьшение шага двигателя позволяет повысить скорость отработки управляющего сигнала и частоту приемистости. Однако использование электромагнитной редукции приводит к уменьшению синхронизирующего момента.
Шаговые двигатели с активным ротором типа ДШ имеют шаг 22,5°, создают вращающий момент до 20 кг/см с частотой приемистости при нагрузке до 400 шаг/с. Реактивные редукторные шаговые двигатели типа ШДР обладают меньшим вращающим моментом, но большим быстродействием при шаге, равном 3°, и частоте приемистости до 1000 шаг/с. Первая группа применяется в качестве исполнительных двигателей силовых электроприводов с программным управлением. Вторая группа шаговых двигателей применяется в информационно-измерительных устройствах, внешних устройствах вычислительных машин и других системах, где не требуется большой вращающий момент.
Построение замкнутых систем автоматики с шаговыми двигателями является нецелесообразным, т.к. улучшенные качества замкнутых систем легче достигаются при использовании регулируемых двигателей непрерывного действия. Шаговые двигатели имеют более низкие энергетические показатели, чем регулируемые двигатели непрерывного действия. Кроме того, с увеличением габаритов ШД снижается допустимая частота, что приводит к увеличению шага при заданной скорости исполнительного органа.
Примером ШД, выпускаемых промышленностью, могут быть двигатели ШД-2-1, ШД-2-6, ШДА-3-1 и ШДА-3-6 с угловым моментом шагом 15°, номинальным моментом 0,1 – 10 Н×м и частотой приемистости 110...600 шаг/с; ШД параметрического типа с ферромагнитным зубчатым ротором ШДР-50/1800 и ШДИ-1 с угловым шагом 3°, номинальным моментом 1...2,5 Н∙м и частотой приемистости 450...1000 шаг/с. Технические данные шаговых двигателей приведены в табл. 3.1.
Таблица 3.1. Шаговые электродвигатели.
Тип двигателя | m | a | Mmax | Mн | Jнг | Jр | ¦им | ¦п | I | U |
РШД-10 | 4 | 3 | 1,4 | 0,55 | 8,0 | — | — | 400 | — | 27 |
РШД-20 | 4 | 3 | 10 | 2,5 | 5,0 | — | — | 850 | — | 27 |
РШД-30 | 4 | 3 | 400 | 100 | 390 | — | — | 250 | — | 24 |
ЭШД-26 | 2 | 22,5 | 10 | 4,0 | 1,2 | — | — | 700 | — | 24 |
ЭШД-27 | 2 | 22,5 | 180 | 60 | 120 | — | — | 280 | — | 48 |
ЭШД-31 | 2 | 22,5 | 300 | 100 | 370 | — | — | 200 | — | 48 |
ДШ-0,1А | 4 | 22,5 | 8,0 | 1,0 | 19 | 19 | 400 | 300 | 0,6 | 27 |
ДШ-1А | 4 | 22,5 | 60 | 10 | 420 | 420 | 200 | 150 | 2,7 | 27 |
ДШ-6А | 4 | 18 | 260 | 60 | 3900 | 3900 | 100 | 80 | 5,0 | 27 |
ШДА-3 | 4 | 22,5 | 7,0 | 2,5 | 20 | 20 | 320 | 130 | 0,37 | 28 |
ШДА-6 | 4 | 22,5 | 41 | 16 | 100 | 97 | 260 | 120 | 1,65 | 28 |
ШДР-231 | 4 | 9 | 1,25 | 0,4 | 0,4 | 0,83 | 1500 | 700 | 0,35 | 28 |
ШДР-523 | 4 | 3 | 16 | 4,0 | 45 | 2,8 | 1500 | 600 | 1,0 | 28 |
ШД-1С | 4 | 15 | 1,0 | 0,4 | 0,5 | 14 | — | 100 | 0,08 | 27 |
ШД-3С | 4 | 15 | 17 | 2,5 | 20 | 100 | — | 100 | 0,19 | 24 |
ЩДА-3-2 | 3 | 15 | 4,0 | 0,4 | 3,0 | 6,5 | — | 450 | 0,5 | 27 |
ШДА-3-4 | 3 | 15 | 25 | 4,0 | 25 | 47 | — | 150 | 1,0 | 27 |
ШД-2 | 3 | 16 | 150 | 30 | 50 | 300 | — | 200 | 8,3 | 12 |
ШД-5 | 3 | 1,5 | 10 | 5,0 | 50 | 55 | 1400 | 1200 | 2,0 | 27 |
ДШМ-16-4 | 4 | 22,5 | 2,8 | 1,0 | 1,0 | — | — | 430 | 1,9 | 27 |
ДШИ-72-3 | 4 | 5,0 | 2,2 | 0,4 | 0,16 | — | — | 1000 | 0,74 | 27 |
Примечания: m – число фаз (обмоток управления); a –одиночный шаг ротора, в градусах; Mmax, Mн – соответственно максимальный статический синхронизирующий момент и номинальный вращающий момент, в 10-2 Нм; JнгиJр – соответственно номинальный момент инерции нагрузки и момент инерции ротора, в 10-7кг×м2; ¦им и ¦п – соответственно максимально допустимая частота следования импульсов управления и частота приемистости, в герцах; I – ток фазы в режиме фиксированной стоянки, в амперах; U – напряжение питания, в вольтах.
Исполнительные двигатели переменного тока. эим с электродвигателями переменного тока наиболее широко применяются в системах сельскохозяйственной автоматики. в них используются асинхронные трехфазные и однофазные электродвигатели. однофазные двигатели применяются в маломощных им (до 600 вт), а трехфазные - при мощностях свыше 500 вт.
Однофазные асинхронные электродвигатели имеют по две обмотки – возбуждения и управления. обмотка возбуждения подключается к сети переменного тока, а на обмотку управления подается входной сигнал от усилительного устройства. этот двигатель можно рассматривать как апериодическое звено, если выходная величина – угловая скорость ротора. если выходным параметром является угол поворота ротора – это два последовательно соединенных звена, одно – апериодическое и другое – интегрирующее. по сравнению с двигателями постоянного тока однофазные двигатели имеют больший удельный объем на единицу мощности и меньший кпд, однако простота их конструкции обеспечивает высокую надежность в эксплуатации и малые затраты на обслуживание.
Асинхронные трехфазные электродвигатели имеют передаточную функцию аналогичную передаточной функции однофазных двигателей. коэффициент передачи, значения электромагнитной и электромеханической постоянных времени этих передаточных функций в обоих случаях определяют по паспортным данным двигателя и механическим характеристикам двигателя и рабочей машины общепринятыми методами.
В основном в электродвигательных им используются реверсивные привода. для их управления применяются как контактные, так и бесконтактные схемы, а также и их сочетание.
По характеру действия электродвигательные им подразделяются на позиционные и пропорциональные.
Конструкция им позиционного действия такова, что с их помощью рабочие органы можно устанавливать только в определенные фиксированные положения. чаще всего таких положений два: “открыто” и “закрыто”. в общем случае возможно и существование многопозиционных им. эти им обычно не имеют датчика обратной связи для получения сигнала о положении рабочего органа, в них используются в основном конечные выключатели для ограничения перемещения рабочего органа при подаче сигнала управления. они применяются в основном в дискретных системах управления.
Им пропорционального действия конструктивно таковы, что обеспечивают в заданных пределах установку рабочего органа в любое промежуточное положение с учетом величины и длительности управляющего сигнала. они содержат датчик обратной связи, характеризующий местоположения рабочего органа, и широко применяются в системах автоматики непрерывного действия. в качестве датчиков обратной связи в этих им применяются потенциометрические реостатные и индукционные датчики, выходной сигнал которых прямо пропорционален величине отклонения рабочего органа от исходного положения. чаще всего, в им устанавливается два одинаковых датчика, один из которых используется для осуществления обратной связи по положению рабочего органа в системе автоматического регулирования, а второй - для дистанционного указания его положения. нередко датчики обратной связи и конечные электрические выключатели конструктивно объединены в один узел, унифицированный для различных типов им.
В сельскохозяйственном производстве наряду с общепромышленными ИМ применяют специализированные ИМ для управления задвижками различных типов, перекидными клапанами и т.д. Наиболее распространенные ИМ – задвижка зерновая ТЭА-15 с приводом ТЭА-14М; ИМ с оперативным контролем и регулированием степени открытия типа РИМЗ (регулируемый ИМ задвижек). Вместо ТЭА-14М выпускают привод Е8-УРВ, который отличается только модулем шестеренной передачи ротора, в результате чего этот ИМ имеет меньшую массу и габариты.
На рис. 3.5 приведена кинематическая схема комбинированного ИМ типа ПР-М с установкой его на двухседельном регулирующем клапане.
Он имеет асинхронный электродвигатель 1, шестеренчатый редуктор 2 для передачи крутящего момента от электродвигателя 1 на диск выходного устройства 3, или шестерню 4, обеспечивающую возвратно-поступательное движение рейки 5 и сочлененного с ней штока 6 клапанов 7.
Рис. 3.5. Кинематическая схема электродвигательного ИМ.
Схемы дистанционного управления ИМ с двухфазным конденсаторным и трехфазным асинхронным электродвигателями приведены на рисунках 3.6 и содержат кнопки дистанционного управления SВ1—SB3, которыми отключаются и включаются обмотки катушек КМ1 и КМ2 реверсивного магнитного пускателя. Отключение электродвигателя в крайних положениях «вправо» и «влево» осуществляется конечными выключателями SQ1 и SQ2. Конечные выключатели 1 (рис.3.7) устанавливаются в корпусе ИМ и срабатывают при нажатии на них одного из кулачков 6, поворачивающихся вместе с выходным валом 5 ИМ. При отходе кулачка 6 от выключателя 1 подвижный контакт 7 возвращается в исходное положение. В связи с тем, что для электродвигательных ИМ характерен выбег выходного вала. Кулачки 6 воздействуют на контакты конечных выключателей 1 через гибкие пластины, что препятствует поломке конечных выключателей 1. Величину углов поворота вала ИМ, при которых срабатывают конечные выключатели 1, можно вручную регулировать поворотом кулачков 6 на оси вала. Каждый кулачок 6 закрепляется стопорным болтом 4.
Рис. 3.6. Принципиальные схемы управления электродвигателями ИМ:
а – однофазовый привод ИМ; b – трехфазовый привод ИМ.
Следует отметить, что используется также вариант подключения конечных выключателей в цепь обмоток ИМ, изображенный штриховыми линиями, при этом контакты SQ1 и SQ2 из цепей катушек КМ1 и КМ2, естественно, исключаются (КV1, КV2- контакты реле регулятора).
Для уменьшения угла выбега ИМ после отключения его электродвигателя от сети параллельно одной из фаз обмотки статора трехфазного двигателя через размыкающие контакты КМ1.6 и КМ2.6 магнитного пускателя включается электрический конденсаторный тормоз С2. Электродвигательные ИМ могут быть не только устройствами позиционного действия, а снабженные датчиками 2 (реостатами) обратной связи по положению выходного вала используются системах управления, обеспечивая законы П, ПИ и ПИД–регулирования.
Рис. 3.7. Кинематическая схема узла коммутации электродвигателя ИМ
и узла реостата ОС.
Ползунок 3 (см. рис. 3.7) датчика ОС закреплен через кронштейн на выходном валу ИМ. Сам реостат 2 неподвижно закреплен на корпусе ИМ. При этом он может быть использован для подключения прибора-указателя положения РО, например вольтметра со шкалой, отградуированной в процентах степени открытия РО. Положение ползунка реостата 2 и величины углов поворота вала ИМ, при которых срабатывают выключатели, можно вручную регулировать поворотом кронштейна и кулачков 6 на оси вала 5, каждый из которых закрепляется стопорным болтом 4.
Разработан и выпускается промышленностью целый ряд многооборотных электрических ИМ с постоянной скоростью вращения выходного вала. Несмотря на конструктивные и схемные различия, все эти ИМ в общем случае позволяют производить: дистанционный или автоматический пуск и остановку электропривода в любом промежуточном положении РО, автоматическую остановку электропривода при чрезмерном возрастании крутящего момента, дистанционную световую сигнализацию крайние положений РО, местное и дистанционное определение любого промежуточного положения РО, электрическую блокировку данного электропривода с другими механизмами и агрегатами, ручное управление ИМ при помощи маховика.
Основные характеристики однооборотных и многооборотных ИМ приведены в таблицах 3.2 и 3.3 соответственно.
Таблица 3.2. Однооборотные ИМ.
Тип | Номин. вращ. момент, Н×м | Угол поворота вых. вала, град. | Время одного обор. вых. вала, с | Номин. мощность электрода, кВт | Сопротивл. датчика об. связи, Ом |
МЭК-10К/120 | 10 | 0 - 90 0 - 270 | 120 | 0,019 | 120 |
МЭК-25К/40 | 25 | 0 - 90 0 - 270 | 40 | 0,27 | 120 |
МЭК-63/100 | 63 | 0 - 90 0 - 270 | 100 | 0,12 | 120 |
МЭО-160/100К | 160 | 0 - 90 0 - 240 | 100 | 0,27 | 250 |
МЭО-1000/250К | 1000 | 0 - 90 0 - 240 | 250 | 0,4 | 250 |
Таблица 3.3. Многооборотные ИМ.
Тип | Номин. вращ. момент, Н×м | Время одного обор. вых. вала,с | Ном. мощность электродв., кВт |
1 | 2 | 3 | 4 |
МЭМ-0,63/1 | 0,63 | 1,0 | 0,12 |
МЭМ-1,6/2,5 | 1,6 | 2,5 | 0,05 |
1 | 2 | 3 | 4 |
МЭМ-4/6,3 | 4,0 | 6,3 | 0,12 |
МЭМ-10/1 | 10,0 | 1,0 | 0,6 |
МЭМ-25/2,5 | 25,0 | 2,5 | 0,4 |
Методика выбора электродвигательных исполнительных механизмов.Анализ тенденций в отечественных и зарубежных системах автоматизации технологических процессов, в том числе и в сельскохозяйственном производстве показывает, что в них все более широко используются электроприводы. Электроприводы новых серий – это приводы с высоко моментными двигателями постоянного тока, асинхронными двигателями, бесколлекторными двигателями постоянного тока и силовыми шаговыми двигателями.
Особенностью электроприводов являются расширенный (до 0,05 Н×м) диапазон малых моментов, повышенная (до 15000 об/мин) максимальная частота вращения, уменьшенная инерция двигателей, возможность встройки в двигатели электромагнитных тормозов и различных датчиков, а также механических и волновых передач.
Основные достоинства электроприводов следующие:
- компактная конструкция двигателей;
- высокое быстродействие;
- равномерность вращения;
- высокий крутящий момент на максимальной скорости;
- высокая надежность (степень защиты 1Р54);
- высокая точность, в том числе за счет возможности применения современных цифровых и вычислительных систем управления;
- низкие уровни шума и вибраций;
- длительная эксплуатация без проверки и обслуживания, особенно при использовании бесколлекторных и асинхронных двигателей ;
- взаимозаменяемость двигателей;
- компактная конструкция усилительно-преобразующих устройств;
- доступность и дешевизна электрической энергии.
К недостаткам электроприводов можно отнести:
- наличие щеток в коллекторах двигателей постоянного тока;
- ограниченное использование во взрывоопасных и пожароопасных средах и помещениях;
- большую зависимость скорости выходного вала от нагрузки, что приводит к необходимости применения дополнительных контуров регулирования привода;
- наличие дополнительной кинематической цепи между электродвигателем и рабочим регулирующим органом.
Выбор электродвигательных ИМ должен начинаться с подробного выяснения технических требований, предъявляемых к этим элементам.
В технических требованиях должны быть указаны:
- статические и динамические параметры элементов (передаточный коэффициент и постоянные времени, время срабатывания и отпускания, допустимая зона нечувствительности и т.д.);
- допустимые пределы изменения указанных выше параметров;
- величины входных и выходных мощностей элементов и интенсивность этих воздействий (величины электрических напряжений или токов, величины скоростей или перемещений и т. д.);
- виды и параметры источников вспомогательной энергии (частота и напряжение электрических источников) и пределы изменения этих параметров в эксплуатации;
- допустимое потребление мощности от источников энергии;
- допустимые габаритные размеры и масса устройства;
- условия эксплуатации (пределы изменения окружающей температуры, давление и влажность воздуха, воздействие условий окружающей среды, воздействие ускорений и т. д.);
- срок службы устройства в заданных условиях эксплуатации;
- требуемая надежность устройства;
- стоимость и т. д.
Основным требованием, предъявляемым к элементам с точки зрения общей системы приборов и средств автоматизации, является требование стандартизации параметров, которые определяют его связи с внешними элементами. Различают три вида внешней связи: информационные (входные и выходные сигналы), энергетические – связи с источниками питания, и вещественные ( конструктивные ) – связи с общей конструкцией, с выходом предыдущего и входом последующего устройств и источниками питания.
Основной задачей энергетического расчета электродвигательных ИМ является выбор серийного исполнительного устройства. Решение этой задачи является итерационным процессом, в результате которого из числа серийных выбирается ИМ, удовлетворяющий техническим требованиям.
На основании технических требований устанавливаются параметры, которым должен отвечать выбираемый двигатель ИМ:
- требуемый вращающий момент (перестановочное усилие);
- угловые (линейные) скорости и ускорения;
- мощность привода;
- оптимальное передаточное число между двигателем и механической нагрузкой.
Для правильного выбора мощности двигателя ИМ требуется иметь приводные характеристики нагрузки или объекта регулирования. Например, для силового привода вращательного действия необходимо знать: момент инерции нагрузки и всех, соединенных и вращающихся с ней частей, моменты трения, внешний возмущающий момент, максимальные значения перемещения, угловые скорости и ускорения нагрузки и т.д. Задача заключается в том, чтобы выбрать двигатель соответствующей мощности, обеспечивающий перемещение механической нагрузки с определенной скоростью и ускорением.
Поэтому при выборе рационального электродвигательного ИМ приходиться взаимосвязано рассматривать конкретные этапы выбора двигателя, соответствующие общей методике выбора электропривода:
1. По роду тока и значению напряжения;
2. По конструктивному исполнению и защите от воздействий окружающей среды;
3. По угловой скорости вращения и ее регулированию;
4. По мощности двигателя, исходя из условий:
а) допустимого нагрева при работе;
б) обеспечения пуска электропривода;
в) обеспечения статической и динамической устойчивости;
г) обеспечения требуемой частоты включений.
5. По виду и уровню схемы управления;
6. По надежности;
7. По экономической эффективности.
Подробно эти вопросы рассмотрены в соответствующих разделах курса по автоматизированному электроприводу.
Электрические схемы управления электродвигательными ИМ должны удовлетворять следующим техническим требованиям:
- питание силовых цепей и цепей управления осуществляется, как правило, от сети переменного тока 380/220 В;
- схемы должны иметь защиту от перегрузок и от коротких замыканий в силовых цепях электропривода, а также в цепях управления и сигнализации;
- при монтаже схем управления и сигнализации контакты аппаратов управления, конечных выключателей, блокировочные цепи, блок - контакты магнитных пускателей и др. должны включаться со стороны фазы, а катушки пускателей - присоединяться к нулевому проводу (это предотвращает ложную работу схемы при появлении “земли” в цепях управления);
- схема управления запорным устройством должна обеспечивать возможность как дистанционного управления со щита или с места, так и автоматического управления по команде от устройства регулирования движение ИМ только во время действия импульса соответственно дистанционного или автоматического управления;
- исключать возможность одновременной подачи командных импульсов от устройств дистанционного и автоматического управления, а также возможность подачи питания на одну из катушек реверсивного магнитного пускателя при обтекании током второй катушки;
- схемы управления с двух или более мест должны быть построены так, чтобы исключить возможность одновременного управления одним устройством из разных пунктов;
- схемы управления должны обеспечить возможность остановки ИМ в любом промежуточном положении, а также возможность последующей посылки команд, как на открытие, так и на закрытие:
а) прекращение ошибочно начатой операции и возврат в исходное положение;
б) «расхаживание» запорного устройства;
в) постепенное открытие или закрытие с непродолжительными остановками в промежуточных положения, если это требуется по условиям технологического процесса;
- нормальная остановка электродвигателя ИМ в положении полного открытия или закрытия должна осуществляться с помощью конечных выключателей, разрывающих цепь соответствующей катушки магнитного пускателя; когда запорные устройства требуют принудительного уплотнения при закрытии, остановка электродвигателя ИМ должна осуществляться посредством контактного устройства муфты предельного момента или токового реле;
- как при ручном, так и при автоматическом управлении схемы должны иметь нулевую защиту;
- при наименьшем количестве сигнальных ламп схема сигнализации положения запорного устройства должна показывать наибольшее количество его состояний (конечные положения, остановка в промежуточном положении, сигнализация хода, направление движения и др.);
- схема контроля состояния регулирующего устройства должна непрерывно фиксировать его положение;
- схемы управления должны быть построены таким образом, чтобы для их реализации требовалось наименьшее количество аппаратуры, кабели с наименьшим количеством жил, конечные выключатели с наименьшим количеством контактов.
Вопросы для самоконтроля:
1. С какой целью применяют шаговые электродвигатели?
2. Чем отличаются однооборотные электродвигательные исполнительные механизмы от многооборотных?
3. Какие виды электродвигателей чаще всего применяются в электродвигательных исполнительных механизмах малой мощности?
4. Что используется для уменьшения выбега двигателя и улучшения качества регулирования?
5. Какие основные технические требования предъявляются к электродвигательным исполнительным механизмам?
ТЕСТ 3.
Из предложенных Вам ответов на данный вопрос выберите правильный.
3.1.Какие виды электродвигательных исполнительных механизмов малой мощности получили большее распространение?
а) трехфазные с короткозамкнутым или фазным ротором.
б) двухфазные асинхронные двигатели или двигатели постоянного тока
в) с поступательным перемещением выходного штока.
3.2.Что понимается под выражением однооборотные электродвигательные исполнительные механизмы ?
а) электродвигатели с углом поворота выходного вала до 360°.
б) выходной вал электродвигателя может совершать большое число оборотов.
в) выходной вал электродвигателя неподвижен.
3.3.В чем преимущество способа управления двигателем со стороны якоря ?
а)он позволяет получить широкий диапазон регулирования скорости.
б) он позволяет добиться плавности регулирования.
в) оба вышеперечисленных варианта.
3.4.Из какого материала выполняют якорь электродвигателя дляобеспечения демпфирования ?
а) алюминий.
б) медь.
в) сталь.
3.5 Каким способом может быть осуществлено реверсирование двигателя?
а)полупроводниковым коммутатором путем взаимного переключения начала и концов обмоток.
б) изменением фазы входного напряжения.
в) изменением величины входного тока.
ТЕМА 4. ЭЛЕКТРОМАГНИТНЫЕ ИСПОЛНИТЕЛЬНЫЕ
МЕХАНИЗМЫ
Общие сведения.В системах автоматического регулирования и управления позиционного принципа действия довольно широкое распространение в качестве исполнительных механизмов получили электромагнитные приводы, преобразующие энергию электрического тока в поступательное движение рабочего органа - так называемые исполнительные электромагнитные механизмы (ЭМИМ).
ЭМИМ служат для преобразования электрического тока в механическое перемещение с целью воздействия на регулирующий орган объекта управления. Они являются наиболее распространенными преобразователями электрического сигнала в механическое перемещение. ЭМИМ получили применение в качестве приводного или управляющего устройства в ряде механизмов, электрических аппаратах и реле. Например, в подъемных и тормозных электромагнитах, в приводах для включения и выключения коммутационных аппаратов, в электромагнитных контакторах, в автоматических регуляторах, в приводах для включения и отключения механических, пневматических и гидравлических цепей, для сцепления и расцепления вращающихся валов, открывания и закрывания клапанов, вентилей, заслонок, золотников на небольшие расстояния до нескольких миллиметров с усилием в несколько десятков ньютонов.
ЭМИМ способны работать как на постоянном, так и на переменном токе. Однако электромагниты постоянного тока применяются намного шире, чем электромагниты переменного тока, поскольку при одинаковых размерах они развивают большее тяговое усилие, имеют более высокую стабильность параметров, конструктивно проще и дешевле. Для их питания используется сеть переменного тока и встроенный выпрямитель.
Характерной особенностью таких устройств является их способность работать только в схемах двухпозиционного (“открыто" – “закрыто”) регулирования или управления. Это объясняется тем, что регулирующий орган (вентиль, клапан и т.д.) может находиться только в двух конечных положениях, соответствующих двум возможным положениям сердечника электромагнита. Например: первое - ток включен, сердечник притянут и клапан открыт; или второе – ток отключен, сердечник не притянут и клапан закрыт.
Принципиально возможно создание многопозиционного (на три положения и более) исполнительного электромагнитного механизма. Однако решение этой задачи сопряжено со значительными трудностями, поэтому широкого распространения многопозиционные приводы не получили.
ЭМИМ по сравнению с электродвигательными ИМ отличаются простотой конструкции и схем управления, меньшими весом и размерами и значительно меньшей стоимостью. Благодаря отсутствию редуктора они более надежны в эксплуатации.
ЭМИМ по принципу действия разделяются на две группы:
- рассчитанные на длительное обтекание катушки соленоида электрическим током; при подаче напряжения питания якорь соленоида втягивается (при этом, например, клапан открывается), а возвращается он в исходное положение при снятии напряжения (клапан закрывается). Основными недостатками при этом являются постоянное потребление электроэнергии и ложные срабатывания при исчезновениях питающего напряжения.
- с кратковременным обтеканием катушек соленоида электрическим током; они состоят из двух электромагнитов – тягового и защелки. Тяговый электромагнит предназначен для втягивания якоря соленоида, напряжение питания на его катушку подается кратковременно. Удерживание якоря в рабочем состоянии после обесточивания тяговой катушки осуществляется механически специальной защелкой. Возврат в исходное состояние осуществляется путем кратковременной подачи напряжения на катушку электромагнита защелки, которая освобождает возвратную пружину и якорь соленоида закрывается.
По назначению ЭМИМ различают на:
- удерживающие, предназначенные для фиксации положения ферромагнитных тел, например электромагниты для подъема предметов из ферромагнитных материалов. Они не совершают работы, от них требуется лишь определенная сила, на которую они рассчитываются.
- приводные, которые служат для перемещения исполнительных устройств, например клапанов, золотников, заслонок. Они используются также в контакторах, электромагнитных муфтах и др. Эти электромагниты совершают определенную работу и поэтому рассчитываются на определенную силу и перемещение.
По роду тока в обмотке различают электромагниты постоянного и переменного тока. Электромагниты постоянного тока делятся на нейтральные, не реагирующие на полярность напряжения питания, и поляризованные, реагирующие на полярность напряжения питания.
По конструктивному исполнению различают электромагниты:
- клапанные, с внешним притягивающимся якорем; они имеют небольшое перемещение якоря (единицы миллиметра) и развивают большое усилие;
- прямоходовые, с поступательным движением якоря; они называются соленоидными электромагнитами, имеют большой ход якоря и обладают высоким быстродействием.
Электромагниты постоянного и переменного тока. Прямоходовые электромагниты могут быть переменного (однофазные и трехфазные) и постоянного тока. Их основные характеристики – ход якоря, зависимость между перемещением якоря и тяговым усилием, зависимость между положением якоря (его перемещением) и расходом электроэнергии и время срабатывания. Эти характеристики зависят от формы магнитопровода, состоящего из ярма и якоря, расположения намагничивающих обмоток и рода питающего тока (переменного или постоянного).
В зависимости от хода якоря (его максимального перемещения) различают короткоходовые (рис. 4.1 а) и длинноходовые (рис. 4.1 b,c) электромагниты.
Рис. 4.1. Формы магнитопроводов и тяговые характеристики электромагнитов:
а – короткоходовых; b и c – длинноходовых.
Электромагниты должны отвечать следующим требованиям:
1. Выбираемая конструкция должна соответствовать длине хода, тяговой силе и заданной тяговой характеристике. Для больших тяговых сил и малой длины хода якоря используют короткоходовые (рис. 4.1 а), а для небольших тяговых сил и значительных ходов якоря - длинноходовые электромагниты (рис. 4.1 b), для больших перемещений якоря - электромагниты с замкнутым цилиндрическим магнитопроводом и квазипостоянной тяговой силой (рис. 4.1 c).
2. Для быстродействующих систем необходимо применять электромагниты с шихтованным магнитопроводом, а для замедленных систем - с не шихтованным магнитопроводом и поворотным якорем с массивной медной гильзой.
3. Число циклов срабатывания должно быть меньше допустимого.
4. Электромагниты переменного тока при одинаковых совершенных механических работах потребляют электроэнергии больше, чем электромагниты постоянного тока.
5. Электромагниты должны быть удобными в эксплуатации и простыми в обслуживании.
Выбор электромагнита осуществляют по напряжению, току и потребляемой мощности. После выбора электромагнита рассчитывают его обмотки на нагрев, считая, что средняя допустимая температура нагрева 85...90°С.
Основные характеристики применяемых электромагнитов приведены в табл. 4.1 и 4.2 соответственно на постоянном и переменном токе.
Таблица 4.1. Характеристики электромагнитов переменного тока.
Тип элек-тромагнита | Тяговое усилие, Н | Ход якоря, мм | Потреб.мо-щность, Вт | Время втя-гивания, с | Время от-падания, с |
МП 100 | 250 | 2 | 140 | 0,12 | 0,1 |
МП 200 | 1000 | 3 | 290 | 0,25 | 0,2 |
МП 300 | 2150 | 4 | 510 | 0,4 | 0,35 |
КМП 2 | 115 | 40 | 350 | 0,4 | 0,1 |
КМП 6 | 720 | 120 | 950 | 2,5 | 0,5 |
ВМ 12 | 65 | 40 | 210 | 0,8 | 0,2 |
ВМ 16 | 280 | 120 | 425 | 23,5 | 1,0 |
Передаточная функция ЭМИМ имеет вид:
W(p) = Y(p)/U(p) = Kм/ ((Tэ×p+1)×(T2×T1×p2+T2×p+1)),
где Y- перемещение якоря; Tэ= L0 / R0 - постоянная времени электромагнита; L0 и R0 -индуктивность и активное сопротивление катушки электромагнита, соответствующие начальному положению якоря; Т1 = ; m - масса подвижных частей;
- жесткость пружины; Т2 = Kд /
; Kд - коэффициент демпфирования; Kм= 2K0/(
×K0) - коэффициент передачи электромагнита; K0 - коэффициент пропорциональности между тяговым усилием электромагнита и током Ik в его катушке.
Таблица 4.2. Характеристики электромагнитов переменного тока.
Тип электромагнита | Момент тяговый, Н×м | Момент массы якоря, Н×м | Угол поворота якоря, град. | Потреб. мощн. при вкл., В×А | Потреб. мощн. при откл., В×А | Время втяги- вания, с | Время отпада-ния, с |
КМТ3А | 350 | 125 | 50 | 19000 | 550 | 0,08 | 0,06 |
КМТ4А | 700 | 240 | 50 | 38000 | 1700 | 0,14 | 0,08 |
КМТ6А | 1150 | 460 | 60 | 85000 | 3000 | 0,25 | 0,12 |
КМТ7А | 1400 | 520 | 80 | 110000 | 3500 | 0,35 | 0,14 |
МО-100Б | 550 | 50 | 7,5 | 2100 | 400 | 0,30 | 0,02 |
МО-200Б | 2000 | 360 | 5,5 | 4000 | 650 | 0,05 | 0,04 |
Если постоянная времени ОУ значительно больше постоянных времени ЭМИМ (Тэ, Т1, Т2), то его передаточная функция может быть представлена безынерционным усилительным звеном:
W(p) = Kм.
Расчет электромагнитных исполнительных механизмов. В задачу расчета ЭМИМ входит нахождение конструктивных размеров и обмоточных данных электромагнитов, соответствующих заданным условиям работы устройства.
Обычно исходными условиями являются:
- противодействующая (механическая) характеристика, полученная расчетным или экспериментальным путем;
- напряжение и ток входного сигнала, подаваемого на обмотку;
- временные параметры;
- габариты, вес и стоимость.
Кроме того, необходимо учитывать основные условия эксплуатации: температуру окружающей среды, влажность, запыленность, наличие вибраций.
К основным показателям ЭМИМ относятся:
- условная полезная работа
A = F×L,
где F – тяговое усилие при определенном положении якоря; L – величина хода якоря;
- показатель весовой экономичности электромагнита, который характеризуется коэффициентом
Кэ= m/A,
где m - масса электромагнита;
- конструктивный фактор
Кф= ,
где Fн - начальное тяговое усилие.
Обобщенным показателем является показатель добротности магнитной системы
Кd= A/(m×P×u),
где P – потребляемая мощность; u – превышение температуры обмотки над температурой окружающей среды.
При прочих равных условиях, т. е. при одинаковых значениях магнитного потока и геометрических размерах, тяговое усилие электромагнита постоянного тока в два раза больше, чем у электромагнита переменного тока.
При выборе конструктивного фактора следует иметь в виду, что длина сердечника электромагнита растет пропорционально увеличению величине хода якоря, а поперечное сечение его пропорционально корню квадратному из требуемой величины электромагнитного тягового усилия. На основании опыта проектирования рекомендуются следующие значения kф: для прямоходового электромагнита – 400; для клапанного – 2900.
Расчет обмоток на нагрев проводят, считая, что средняя допустимая температура нагрева uдоп= 85...90 0С. Температуру нагрева определяю по приращению сопротивления обмотки
u = ( Ru- R0) / (R0 × a ) + u0 ,
где Ru - сопротивление нагретой обмотки; R0 - сопротивление обмотки при 20 0С ; u0 - температура окружающей среды ; a - температурный коэффициент сопротивления обмоточного провода.
Превышение температуры нагрева над допустимой приводит к сокращению срока службы и разрушению изоляции обмотки.
Рабочий цикл ЭМИМ состоит из трех периодов: срабатывания, включенного состояния и возврата в исходное положение. После включения электромагнита происходит нарастание тока в его обмотке до величины тока трогания, когда электромагнитная сила преодолевает внешнее сопротивление и якорь приходит в движение. На якорь электромагнита кроме силы электромагнитного притяжения действуют противодействующая сила статического сопротивления, сила вязкого трения и сила инерции. Оценка времени движения якоря проводится в предположении неизменности динамического усилия на протяжении всего хода якоря и отсутствии вязкого трения.
С учетом изложенного время втягивания можно определить как
Тв= ,
где Fc - противодействующая сила статического сопротивления; а время отпадания равно
То= .
Вопросы для самоконтроля:
1. Укажите характерную особенность электромагнитных исполнительных механизмов?
2. Способны ли электромагнитные исполнительные механизмы работать на постоянном токе?
3. Как различаются электромагнитные исполнительные механизмы по конструктивному исполнению?
4. Каким образом различаются электромагнитные исполнительные механизмы по принципу действия?
5. Каким образом различаются электромагнитные исполнительные механизмы по назначению?
ТЕСТ 4.
Из предложенных Вам ответов на данный вопрос выберите правильный.
4.1.Для чего служат исполнительные электромагнитные механизмы?
а) для преобразования электрического тока в механическое перемещение.
б) для торможения электродвигателя.
в) для управления электродвигателем.
4.2.В чем различия исполнительных электромагнитных механизмов по сравнению с обычными исполнительными механизмами?
а) ЭМИМ по сравнению с электродвигательными ИМ отличаются простотой конструкции и схем управления.
б) меньшими весом и размерами и значительно меньшей стоимостью. Кроме того, благодаря отсутствию редуктора они более надежны в эксплуатации.
в) оба вышеперечисленных варианта.
4.3. В чем особенность нейтральных электромагнитов постоянного тока?
а) они не реагируют на полярность напряжения питания.
б) они позволяют добиться плавности регулирования.
в) они потребляют малую мощность.
4.4.В чем особенность соленоидных электромагнитов постоянного тока?
а) они имеют большой ход якоря и обладают высоким быстродействием.
б) они имеют поступательные движения якоря.
в) они имеют небольшое движение якоря.
4.5 Сравните потребление электроэнергии электромагнитами переменного и постоянного тока при одинаковых совершенных механических работах?
а) электромагниты переменного тока потребляют меньше электроэнергии, чем электромагниты постоянного тока.
б) электромагниты переменного тока потребляют больше электроэнергии, чем электромагниты постоянного тока.
в) электромагниты переменного тока потребляют такое же количество электроэнергии, как и электромагниты постоянного тока.
ТЕМА 5. ЭЛЕКТРОМЕХАНИЧЕСКИЕ МУФТЫ
Муфта – устройство, служащее для сцепления двух валов, т.е. для передачи вращающего момента с одного вала (ведущего) на другой (ведомый). Ведущий вал вращается приводным двигателем, а ведомый вал связан с нагрузкой. Муфта называется электромеханической, если для передачи механического момента используются электрические явления. Управление муфтой осуществляется при этом с помощью электрического сигнала, следовательно, она представляет собой преобразователь электрического сигнала в механический вращающий момент. Так как развиваемая на ведомом валу мощность много больше мощности управляющего сигнала, электромеханическая муфта осуществляет также и усиление мощности сигнала. Двигатель, вращающий ведущий вал, в энергетическом отношении играет ту же роль, что и источник питания в обычном электрическом усилителе. В обоих случаях входной электрический сигнал управляет потоком мощности от этого источника. Электромеханические муфты нашли свое применение в ряде систем сельскохозяйственной автоматики и в качестве регулируемых электроприводов сельскохозяйственных машин.
Муфты бывают релейного действия, осуществляющие жесткое сцепление валов при подаче сигнала, и непрерывного действия, осуществляющие гибкое сцепление, когда скорость ведомого вала зависит от величины входного сигнала и эта зависимость может быть предоставлена плавной статической характеристикой «скорость ведомого вала - входной сигнал». Для автоматических систем основной интерес представляют муфты гибкого сцепления.
Электромеханические муфты применяются в качестве исполнительных элементов. Они заменяют исполнительный двигатель с управляемой скоростью вращения, позволяя применять в качестве приводных двигателей нерегулируемые электрические и неэлектрические двигатели. Такая замена, как правило, упрощает схему и конструкцию автоматической системы в целом, повышает ее надежность.
Однако основное преимущество электромеханических муфт перед обычным управляемым электродвигателем в их большем быстродействии. Это объясняется тем, что момент инерции вращающихся частей муфты, связанных с ведомым валом, можно сделать значительно меньше момента инерции приводного двигателя, определяющего быстродействие системы управления скоростью нагрузки при воздействии на двигатель, а не на муфту.
Электромеханические муфты применяются в диапазоне мощности от нескольких ватт (например, в маломощных следящих системах приборного типа) до десятков тысяч киловатт (в электроприводах прокатных станов, металлорежущих станков, в приводах гребных винтов на судах).
Исполнительные механизмы с электромеханическими муфтами отличаются от электродвигательных ИМ более простой конструкцией, низкой стоимостью, высокой надежностью и долговечностью и меньшей экономичностью при большом диапазоне регулирования скорости вращения.
Их применение оказывается чаще всего целесообразным в тех механизмах, где стоимость израсходованной энергии составляет небольшую долю себестоимости продукции. В этих случаях повышение надежности, а, следовательно, уменьшение простоев и брака, как правило, окупает увеличение расхода энергии, а низкая себестоимость этих ИМ приводит к минимуму расчетных затрат. Кроме того, рациональной областью их применения являются механизмы с вентиляторным моментом нагрузки, пропорциональным квадрату скорости вращения.
По принципу действия электромеханические муфты делятся на два основных типа: электромеханические муфты трения (ЭМТ) и электромеханические муфты скольжения (ЭМС). Они в большинстве случаев выполняют две основные функции:
1.Соединение и разъединение приводного двигателя с рабочим механизмом;
2. Регулирование скорости вращения рабочего механизма независимо от скорости вращения приводного двигателя (как правило, при ее постоянной величине).
Электромеханические муфты трения. В муфтах трения вращающийся момент на ведомом валу создается за счет силы трения. Электромеханические муфты трения в свою очередь подразделяются на муфты сухого трения и ферропорошковые (магнитоэмульсионные) муфты трения.
Электромеханические муфты сухого трения. Принцип действия муфты сухого трения иллюстрируется рис. 5.1а. Муфта состоит из двух половин 1 и 2 (полумуфт), на которых укреплены диски трения 3 из фрикционного материала. Одна полумуфта может перемещаться вдоль своего вала на шпонке, другая соединена со своим валом жестко. Если прижать обе половины муфты друг к другу, то неподвижный до этого ведомый вал станет вращаться заодно с ведущим, т.е. произойдет сцепление валов за счет силы трения, препятствующей проскальзыванию дисков трения друг относительно друга.
Рис. 5.1. Принцип действия муфт сухого трения:
а – реверсивной, b – нереверсивной.
На рис. 5.1b показан принцип действия реверсивной муфты трения, позволяющей изменять направление вращения ведомого вала. Она представляет собой комбинацию двух простых нереверсивных муфт: ведомый диск 1 находится между двух ведущих дисков 2 и 3, вращающихся в разные стороны. Направление вращения ведомого диска можно менять, прижимая его то к одному, то к другому ведущему диску. Ведущие диски приводятся во вращение или двумя отдельными двигателями или одним общим. В последнем случае один из дисков соединяется с двигателем через зубчатую передачу, изменяющую направление его вращения по сравнению с другим диском.
Если необходимо быстро тормозить, то ведомый вал муфты трения комбинируют с тормозом. Такая комбинированная муфта выглядит как реверсивная (рис. 5.1 b), только второй ведущий диск в этом случае заменяется неподвижным диском, жестко укрепленным на основании муфты. Торможение ведомого диска осуществляется путем прижатия его к этому неподвижному диску.
Прижатие частей муфты друг к другу может осуществляться, например, с помощью гидравлического или пневматического сервомотора. Тогда мы имеем соответственно гидравлическую или пневматическую муфту трения с гидравлическим или пневматическим управлением. Если же части муфты сжимаются с помощью какого-либо электромеханического преобразователя, то получается электромеханическая муфта трения.
Основное распространение получили электромеханические муфты трения с электромагнитным управлением, где для сцепления обеих половин муфты применяется электромагнит. Наиболее быстродействующие электромеханические муфты трения выполняются с магнитоэлектрическим управлением. В этом случае вместо электромагнита применяется магнитоэлектрический преобразователь электрического сигнала в перемещение и силу.
На рис. 5.2а показан фрагмент простейшей нереверсивной муфты трения с электромагнитным управлением. Она представляет собой электромагнит, состоящий из якоря 1 и магнитопровода 2 с обмоткой 3. Подвод тока в обмотку осуществляется с помощью двух контактных колец со щетками.
Рис. 5.2. Муфта трения с электромагнитным управлением:
а – однодисковая, b – многодисковая; 1 – якорь, 2 – магнитопровод, 3 – обмотка, 4 – диски трения, 5 – контактное кольцо.
На магнитопроводе и якоре укреплены диски трения 4. Якорь может перемещаться вдоль одного вала на шпонке. Магнитопровод укреплен на другом валу жестко. Якорь оттягивается от магнитопровода возвратной пружиной (она на рисунке не показана). Поэтому при отсутствии тока в обмотке ведомый вал неподвижен. При подаче входного сигнала на обмотку якорь притягивается к магнитопроводу и происходит сцепление валов.
Муфты трения с электромагнитным управлением бывают однодисковыми (рис. 5.2 а) и многодисковыми (рис. 3.2 b). Многодисковыми делают мощные муфты для уменьшения их габаритов.
На рис. 5.3 показан вариант муфты трения с электромагнитным управлением и неподвижной обмоткой. Такие муфты не только свободны от скользящих контактов для подвода тока в обмотку, но и обладают большим быстродействием (имеют меньшую постоянную времени обмотки). Но зато они отличаются повышенными размерами обмотки из-за увеличенного воздушного зазора.
Рис. 5.3. Муфта трения с электромагнитным управлением и неподвижной катушкой: 1 – обмотка, 2 – магнитопровод, 3 и 4 – полумуфты, 5 – диски трения
В электромагнитных муфтах трения применяют, как правило, электромагниты постоянного тока, поскольку они обладают известными преимуществами перед электромагнитами переменного тока. При наличии сигнала переменного тока в электромагниты постоянного тока встраивают выпрямитель.
Расчет муфты трения с электромагнитным управлением состоит из расчета поверхностей трения и расчета электромагнита. Исходными данными являются величина вращающего момента, который должен передаваться муфтой, и габариты муфты. Рассмотрим порядок расчета муфты на примере дисковой муфты.
Передаваемый муфтой вращающий момент
,
где m - число поверхностей трения, определяемое числом дисков трения; Кр = (R1/R2)×Ктр– расчетное отношение; Ктр - коэффициент трения, зависящий от материала дисков и состояния их поверхностей; R1и R2 - внутренний и наружный радиусы дисков трения; р - давление, с которым диски прижимаются электромагнитом.
Задавшись наружным радиусом дисков трения R2, можно найти число поверхностей трения m, необходимое для передачи заданного вращающего момента M, или задавшисьm, можем найти R2.
Тяговое усилие от электромагнита, определяется как
.
Далее проводится расчет электромагнита. Для уменьшения размеров обмотки, ограниченных допустимым ее нагревом, в мощных муфтах устраивают жидкостное охлаждение. Менее мощные просто снабжают ребрами, повышающими охлаждения.
Ориентировочные значения входящих в формулы величин:
коэффициент трения Ктр для трущихся тел из стали, чугуна, бронзы примерно равен 0,1 - 0,2; для специальных фрикционных материалов типа ферродо его значение берут равным 0,4 - 0,8; отношение Кр берут равным 0,3-0,6; величина давления p=2¸3 кг/см.
Рассмотрим динамику работы электромеханической муфты трения. Переходный процесс от момента подачи напряжения на обмотку муфты, когда ведомый вал неподвижен, до установления постоянной скорости вращения ведомого вала состоит из следующих трех этапов.
Первый этап - от подачи входного напряжения до момента соприкосновения поверхностей трения - представляет собой этап срабатывания электромагнита. Его продолжительность равна времени срабатывания электромагнита. При необходимости его уменьшения применяют обычные способы изменения временных параметров электромагнитов.
Второй этап заканчивается полным сцеплением поверхностей трения. Это этап, на протяжении которого прекращается скольжение ведомого вала относительно ведущего. Однако переходный период этим не заканчивается, так как в результате сцепления полумуфт, к двигателю, вращающему ведущий вал и работавшему ранее вхолостую, оказывается приложенной нагрузка ведомого вала. Поэтому после второго этапа наступает третий этап, представляющий собой переходный процесс для приводного двигателя, вызванный набросом нагрузки.
Полное время срабатывания муфты с электромагнитным управлением, равное сумме времен всех трех этапов переходного процесса измеряется сотыми и десятыми долями секунды.
Рассмотренные муфты трения применяются, главным образом, для жесткого соединения валов. Однако и с их помощью можно осуществить плавное изменение установившегося значения скорости ведомого вала путем импульсного управления муфтой. В этом случае входной сигнал представляет собой импульсы напряжения, следующие с постоянной частотой, За время импульса муфта срабатывает и ведомый вал начинает разгоняться; за время паузы между импульсами происходит отпускание муфты и торможение вала. При этом скорость ведомого вала колеблется относительно некоторого среднего значения с частотой следования управляющих импульсов.
Величиной этого среднего значения можно управлять, изменяя скважность выходных импульсов.
Электромеханические муфты скольжения. Наибольшее применение в промышленности и в сельском хозяйстве нашли ИМ с ЭМС и автоматическим регулятором скорости, обеспечивающим ее жесткие механические характеристики.
ЭМС в большинстве ИМ выполняют две основные функции:
1. Соединение и разъединение приводного двигателя с рабочим механизмом;
2. Регулирование скорости вращения рабочего механизма независимо от скорости вращения двигателя.
ИМ с ЭМС в сравнении с ЭМТ имеют следующие преимущества:
1. Возможность бесступенчатого регулирования скорости вращения рабочего механизма при постоянной скорости вращения двигателя;
2. Повышенную надежность и долговечность, связанную с отсутствием трущихся фрикционных элементов;
3. Предохранение двигателя и рабочего механизма от перегрузок и поломок, обусловленное ограниченностью величины предельно передаваемого момента;
4. Сглаживание (демпфирование) ударов и колебаний нагрузки, повышающее срок службы рабочего механизма, механических передач и двигателя.
К недостаткам ИМ с ЭМС относятся:
1. Меньшая экономичность, обусловленная наличием потерь скольжения не только во время переходных процессов, но и в установившихся рабочих режимах;
2. Меньшее быстродействие, связанное в большинстве случаев с повышенными значениями электромеханической и электромагнитной постоянных времени;
3. Меньшие значения удельных вращающих моментов, приходящихся на единицу объема или веса муфты.
Приводы с ЭМС по своим конструктивным схемам и устройству механической части отличаются большим разнообразием. Конструктивная схема привода в ряде случаев определяет величину минимального воздушного зазора, что может повлиять на электромагнитные параметры муфты скольжения.
Как правило, ЭМС применяемые для гибкого сцепления валов и плавного регулирования скорости вращения выходного вала, состоят из двух частей: индуктора и якоря. На рис. 5.5 показан вариант такой ЭМС. Индуктор представляет собой электромагнит постоянного тока, магнитный поток которого замыкается через якорь. Пусть, например, индуктор соединен с ведущим валом, а якорь с ведомым валом (может быть и наоборот). При вращении индуктора его магнитное поле будет вращаться относительно якоря. В якоре при этом наводятся токи, которые, взаимодействуя с полем индуктора, создают вращающий момент, увлекающий якорь в движение вслед за индуктором.
Рис. 5.5. Электромеханическая муфта скольжения:
1 – якорь; 2 – индуктор; 3 – контактные кольца; 4 – обмотка индуктора;
5 – полюса индуктора.
Таким образом, эта муфта имеет индукционное управление. Принцип действия ее такой же, как и асинхронного двигателя, только вращающееся магнитное поле создается здесь не переменным многофазным током, а вращением полюсов электромагнита постоянного тока.
В отличие от обычных асинхронных машин, в муфте, изображенной на рис. 5.5, якорь - наружный, а индуктор находится внутри него. Однако делаются муфты и с внутренним якорем. В муфтах скольжения, как и в асинхронных двигателях, якорь выполняется в виде короткозамкнутой обмотки – «беличье колесо», сплошного массивного ротора, а в быстродействующих маломощных муфтах в виде полого ротора - стакана.
Рис. 5.6. Статические характеристики ЭМС.
На рис. 5.6 показаны типичные статические характеристики муфты скольжения: зависимость скорости ведомого вала от момента на нем при разных значениях тока в обмотке индуктора. Если известна зависимость момента сопротивления нагрузки от скорости ее вращения Mс= f(ω) (пунктир на рис. 5.6), то, нанеся такую зависимость в той же системе координат, по точкам пересечения характеристик муфты и нагрузки можно построить результирующую статическую зависимость скорости вращения нагрузки от тока в обмотке индуктора ω = f(I) или напряжения на ней.
ЭМС позволяют регулировать скорость нагрузки в диапазоне примерно 1:10. Такие муфты выполняются на мощности от десятков ватт до тысяч киловатт. Как и муфты трения, они могут быть сделаны реверсивными.
Кроме того, применяются комбинированные муфты, где объединены муфта скольжения с муфтой трения, последняя служит для жесткого соединения валов после разгона нагрузки, осуществляемого с помощью муфты скольжения.
Динамика муфты скольжения описывается такими же уравнениями, что и ферропорошковой муфты трения.
Серийно выпускавшие комплектные привода серии ПМС состоят из электродвигателя, муфты скольжения индукторного типа и автоматического регулятора скорости. Они имеют шесть типоразмеров на вращающие моменты от 1,7 до 30 Н×м, могут использоваться в различных производственных механизмах с постоянным и вентиляторными моментами нагрузки. Технические данные этих приводов приведены в таблице 5.1.
В последствии привода с ЭМС серии ПМС были заменены на более совершенные в конструктивном плане привода серии ПМС - М, имеющие в основном аналогичные технические характеристики.
ЭМС серии ИМС также имеют шесть типоразмеров на моменты от 70 до 1600 Н×м и предназначены для использования в качестве силового электропривода, они применяются в основном для механизмов с вентиляторной нагрузкой. Особенностью их конструкции является открытое исполнение, что требует при монтаже применение защитных ограждений, а также они поставляются без приводного электродвигателя. В сельскохозяйственной автоматике привода серии ИМС практически не используются.
Таблица 5.1. Технические данные приводов серии ПМС.
Показатели | ПМС -0,17 | ПМС -0,4 | ПМС - 0,6 | ПМС - 1 | ПМС - 2 | ПМС - 3 |
1 | 2 | 3 | 4 | 5 | 6 | 7 |
Номинальный момент, Нм | 1,7 | 4 | 6 | 10 | 20 | 30 |
Диапазон регулирования скорости, об/мин | 200 – 1100 | 200 – 1200 | 200 – 1300 | 250 – 1300 | 250 – 1300 | 270 – 1350 |
Число витков обмотки | 800 | 770 | 880 | 846 | 880 | 900 |
Диаметр провода, мм | 0,51 | 0,64 | 0,69 | 0,86 | 1,0 | 1,1 |
Сопротивление обмотки, Ом | 20 | 15 | 19 | 13 | 12 | 10 |
Номинальный ток возбуждения, А | 1,2 | 1,5 | 1,7 | 2,0 | 2,0 | 2,2 |
Мощность электродвигателя, кВт | 0,27 | 0,6 | 1,0 | 1,7 | 2,8 | 4,5 |
Номинальная скорость вращения электродвигателя, об/мин | 1460 | 1410 | 1410 | 1440 | 1440 | 1455 |
Вес привода, кг | 20 | 45 | 54 | 120 | 145 | 300 |
Использование электромагнитных муфт скольжения. ЭМС широко используются в качестве исполнительных элементов как в устройствах с регулируемым электроприводом, так и в системах автоматического управления. Они применяются для плавного изменения скорости вращения, обеспечивают безударный пуск рабочих механизмов с большими маховыми массами, используются для ограничения и регулирования вращающего момента и в других случаях.
Плавное регулирование скорости вращения. Из рассмотрения принципа действия ЭМС видно, что изменение ее скорости вращения возможно за счет соответствующего изменения тока возбуждения муфты. В связи с мягкими естественными характеристиками приходится применять замкнутую систему автоматического регулирования скорости вращения. При этом за счет автоматического изменения тока возбуждения, компенсирующего отклонение скорости вращения от заданной, могут быть обеспечены жесткие механические характеристики ЭМС. Изготовляются комплектные электроприводы с использованием ЭМС, состоящие из асинхронного двигателя, ЭМС и автоматического регулятора. Остановимся на энергетических показателях такого электропривода.
Мощность потерь на скольжение расходуется на нагревание активной поверхности якоря. При увеличении скольжения увеличивается ЭДС, наводимая в якоре, что вызывает увеличение вихревых токов. В результате джоулевые потери возрастают, вызывая нагрев якоря.
Мощность потерь ЭМС подсчитывается по формуле
; кВт,
где M - передаваемый момент, кгм; - скорость вращения электродвигателя, об/мин;
– скольжение ЭМС
;
- скорость вращения ведомой части муфты.
Коэффициент полезного действия муфты (без учета вентиляционных потерь и потерь на возбуждение) равен
,
где – КПД электродвигателя.
Полученное выражение показывает, что КПД муфты тем ниже, чем больше ее скольжение.
Коэффициент мощности привода с ЭМС зависит не от скорости вращения, а от передаваемого момента. Также как у асинхронного короткозамкнутого двигателя при полной загрузке муфты по моменту ее максимален и равен номинальному значению
электродвигателя. Энергетические параметры привода с ЭДС при различных режимах показаны на рис. 5.7. Последний режим работы (рис. 5.7 в) соответствует вентиляторной нагрузке. Абсолютные потери при этом не превышают 17 % максимальной мощности, передаваемой муфтой. Для этого режима выпускаются муфты как малой, так и большой мощности.
Для работы при постоянном моменте в связи с большими потерями на скольжение мощность, передаваемая муфтой, не должна превышать 3-4 кВт. Увеличение предельной мощности допустимо только для случаев повторно-кратковременного режима работы или режима, когда основное время работы происходит при малых значениях скольжения.
Рис. 5.7. Энергетические параметры ЭМС в различных режимах работы:
а – М = const; б – Р = const; в – ;
1 – потребляемая мощность; 2 – потери в муфте; 3 – полезная мощность на
ведомом валу; 4 – КПД муфты.
Вопросы для самоконтроля:
1. Какие электромагниты применяют, как правило, в электромагнитных муфтах трения?
2. Как определить передаваемый муфтой вращательный момент?
3. Как определяется тяговое усилие от электромагнита?
4. Охарактеризуйте этапы переходного процесса от момента подачи напряжения на обмотку муфты, когда ведомый вал неподвижен, до установления постоянной скорости вращения ведомого вала.
5. Какими преимуществами обладают электромагнитные муфты скольжения по сравнению с электромагнитными муфтами трения?
ТЕСТ 5.
Из предложенных Вам ответов на данный вопрос выберите правильный.
5.1.Для чего служит муфта?
а) служит для сцепления двух валов, т.е. для передачи вращающего момента с одного вала (ведущего) на другой (ведомый).
б) служит для торможения электродвигателя.
в) служит для изменения скорости вала двигателя.
5.2.В чем особенность муфт релейного действия?
а) они осуществляют жесткое сцепление валов при подаче сигнала
б) они могут сделать значительно меньше момента инерции.
в) муфты релейного действия способны выдерживать значительные перегрузки.
5.3.Чем отличаются исполнительные механизмы с электромеханическими муфтами от электродвигательных?
а) более простой конструкцией, низкой стоимостью, высокой надежностью и долговечностью.
б) более сложной конструкцией, высокой стоимостью.
в) они потребляют малую мощность.
5.4.сколько бывает видов муфт с электромагнитным управлением?
а) 2.
б) 3.
в) 4
5.5 В каких механизмах применение электромеханических муфт наиболее целесообразно?
а) В тех механизмах, где стоимость израсходованной энергии составляет небольшую долю себестоимости продукции.
б) В тех механизмах, в которых повышение надежности, а, следовательно, уменьшение простоев и брака, как правило, окупает увеличение расхода энергии.
в) В тех механизмах, в которых низкая себестоимость этих ИМ приводит к минимуму расчетных затрат.
ТЕМА 6. РЕЛЕЙНЫЕ ИСПОЛНИТЕЛЬНЫЕ МЕХАНИЗМЫ
В системах автоматики широко применяются элементы и устройства дискретного принципа действия. Среди этих устройств одной из самых больших групп являются реле. В системах управления и регулирования энергетических электрических и энергомеханических потоков энергии релейные элементы применяются не только как промежуточные и усилительные устройства автоматики, а также они часто используются как оконечные выходные элементы этих систем. В этом случае релейные элементы выполняют функции исполнительных механизмов и называются релейными исполнительными механизмами (РИМ). В настоящем пособии рассматриваются лишь те релейные элементы, которые используются в системах автоматики в качестве РИМ.
В связи с широким внедрением полупроводниковой интегральной техники область применения электромеханических устройств значительно сузилась, но общее количество используемых реле из года в год растет, причем в сельскохозяйственной автоматике они продолжают оставаться основными элементами. Это объясняется тем, что электромеханические устройства по сравнению с бесконтактными имеют ряд уникальных свойств: полное отсутствие гальванической связи между входными и выходными сигналами; возможность коммутации как постоянных, так и переменных токов; допустимость значительных перегрузок в цепи контактов, как по току, так и по напряжению; малые потери мощности в контактном переходе; бесконечное отношение сопротивлений контакта в разомкнутом и замкнутом состояниях; независимость от воздействия электрических и магнитных полей; нечувствительность к температурным перегрузкам; высокая электрическая прочность; простота в обслуживании и эксплуатации; значительно низкая стоимость, чем у других типов реле и т. д.
В качестве РИМ в системах автоматики широко применяются: электромагнитные реле, электромагнитные пускатели и контакторы, герконовые реле и другие.
Общие сведения.Классификация электрических реле по принципу их действия приведена на рис. 6.1.
![]() |
Рис. 6.1. Классификация электрических реле по принципу действия.
Характеристики основных типов электрических реле приведены в таблице 6.1.
Таблица 6.1. Электрические реле.
Тип реле | Мощность срабатывания, Вт | Коммутируемая мощность, Вт | Коэффициент усиления по мощности, Кр | Время срабатывания, мс |
Электромагнитные | 10-3 - 103 | 0,1 - 104 | 10 - 105 | 1 - 200 |
Магнитоэлектрические | 10-9 - 10-4 | 0,1 - 2,0 | 104 - 108 | 10 - 500 |
Электронные | 10-12 - 10-8 | 10-3 - 102 | 104 - 108 | 10-6 - 10-5 |
Герконовые | 10-4 - -10-3 | 0,1 - 103 | 104 - 106 | 10-3 - 10-2 |
РИМ представляет собой совокупность электромагнита, который выполняет роль управляющего устройства, и перемещаемой им механической нагрузки. Нагрузкой при этом могут быть, например, разрывные контакты (в электромагнитных реле), реакция потока газа или жидкости (в электромагнитных клапанах), регулирующий орган (задвижка или заслонка) вместе с соответствующими возвратными пружинами, противодействующими тяговым усилиям электромагнита. Следовательно, РИМ в системах автоматики могут выполнять самые разнообразные функциональные задачи.
Несмотря на различия в принципе действия и конструкции, свойства реле характеризуются следующими основными параметрами:
1. Срабатывание - (Пср) минимальное значение входного сигнала, при котором происходит переключение контактов реле, оно характеризует чувствительность реле;
2. Отпускание - (Потп) максимальное значение входного сигнала, при котором происходит возврат реле в исходное состояние;
3. Коэффициент возврата - (Кв) связывает параметры срабатывания и отпускания, он равен отношению параметра отпускания к параметру срабатывания (Кв = Потп / Пср);
4. Рабочий параметр - (Пр) это установившееся значение входной физической величины в номинальном режиме;
5. Коэффициент запаса при срабатывании - (Кз.ср) это отношение рабочего параметра к параметру срабатывания (Кз.ср = Пр / Пср);
6. Коэффициент запаса при отпускании - (Кз.отп) это отношение параметра отпускания к рабочему параметру (Кз.отп = Потп / Пр);
7. Время срабатывания - (tср) это интервал времени от момента поступления сигнала управления на катушку реле до момента начала действия контактов реле на управляемую цепь, т. е. до момента их полного замыкания;
8. Время отпускания - (tотп) это интервал времени от момента снятия сигнала управления на катушке реле до момента окончания действия контактов реле на управляемую цепь, т. е. до момента их полного размыкания;
9. Коэффициент усиления по мощности - (Кр) это отношение номинальной коммутируемой контактами реле мощности нагрузки (Рнаг.н) к номинальной потребляемой мощности катушки при срабатывании реле (Ркон.н) , т. е. Кр = Рнаг.н / Ркон.н .
Эксплуатационные параметры РИМ, их надежность и коммутационная способность в основном определяются режимами работы контактных групп реле. Обычно подвижные контактные соединения, применяемые в реле, называют просто контактами. При этом различают разомкнутые, замкнутые и переключающиеся контакты – рис. 6.2.
Рис. 6.2. Схемы контактного устройства:
а - с замыкающимся; б - с размыкающимся;
в - с переключающимися контактами;
1 - подвижный контакт; 2 - неподвижный контакт; 3,4 - плоские пружины;
5 – толкатель.
В процессе работы РИМ контакты могут находиться в одном из 4х состояний: замкнутом, в процессе размыкания, разомкнутом и в процессе замыкания. К тяжелым условиям работы контактов, при которых происходит наибольший износ, относятся их замкнутое состояние, когда через контакты протекает весь ток нагрузки, и процесс размыкания под нагрузкой, когда между контактами возникает дуга.
Условия работы контактов, прежде всего, определяются величиной напряжения в сети, мощностью и характером нагрузки (активная, индуктивная или емкостная), а также частотой коммутации - числом включений и отключений в единицу времени. Контакты принято характеризовать следующими эксплуатационными параметрами: предельными значениями тока, напряжения, мощности и числом включений.
Предельно допустимый ток Iп - определяется температурой нагрева контактов, при которой они еще не размягчаются и сохраняют необходимые физико-химические свойства.
Предельно допустимое напряжение Uп - определяется напряжением пробоя промежутка между разомкнутыми контактами.
Предельно допустимая мощность Рп - это мощность электрической цепи, которую контакты могут разорвать без образования на них устойчивой электрической дуги.
Явление искрения контактов наиболее развито в цепях постоянного тока, так как запасенная в индуктивностях электромагнитная энергия при разрыве цепи, исчезая, прерывается через расходящиеся контакты и вызывает пробой воздушного промежутка. Это сопровождается эрозией, окислением и разрушением контактов. Поэтому предельная допустимая мощность Рп контактов в цепях переменного тока в 2 - 3 раза больше, чем в цепях постоянного тока.
При замыкании контакты работают в облегченном режиме и могут включать мощность, в 2 - 3 раза большую мощности Рп.
Во взрывоопасных, химически агрессивных средах и других неблагоприятных условиях применяют вакуумные и ртутные (в частности, герконовые) контакты, размещенные в герметически закрытых стеклянных колбах.
РИМ имеют следующие виды статических характеристик (рис. 6.3):
- релейная нереверсивная (рис. 6.3 а);
- релейная реверсивная (рис. 6.3 б);
- релейная реверсивная двухпозиционная (рис. 6.3 в).
Рис. 6.3. Статические характеристики реле:
а - нереверсивная; б - реверсивная; в - реверсивная двухпозиционная.
Динамические характеристики РИМ, в общем виде описывающие электромагнитные и механические переходные процессы, графическая иллюстрация которых приведена на рис. 6.4, имеют вид
где
и
' - времена трогания соответственно при возрастании и уменьшении рабочего параметра Пр (например, входного напряжения на катушке РИМ);
и
- времена движения соответственно при возрастании и уменьшении Пр; t - постоянная времени обмотки управления; L - индуктивность обмотки управления; R -активное сопротивление обмотки управления; Кз.ср - коэффициент запаса при срабатывании; Кв - коэффициент возврата.
Обычно значениями и
ввиду их малости по сравнению с
и
при проведении практических расчетов пренебрегают. Это объясняется тем, что время перехода подвижных частей РИМ из одного состояния в другое очень мало. Основное время занимает процесс нарастания рабочего параметра (как правило, тока в катушке реле) до значения срабатывания и его уменьшения после отключения до значения отпускания.
С учетом вышеизложенного передаточная функция РИМ имеет вид апериодического звена первого порядка. Это является справедливым как при питании катушки реле постоянным, так и переменным током.
Рис. 6.4. Временные диаграммы срабатывания и отпускания реле:
а,б - процессы в обмотке реле; в - ток I=U/R, протекающий
через омическую нагрузку.
По основным электромеханическим параметрам РИМ рекомендуется предусматривать эксплуатационные запасы. Наличие запасов позволяет повысить надежность работы устройства и компенсировать неизбежные погрешности в определении режимов и условий эксплуатации. Приведенные в таблице 6.2 коэффициенты запаса представляют собой отношение рекомендуемого эксплуатационного значения параметра к максимально допустимому значению по паспортным данным.
Таблица 6.2. Коэффициенты запаса.
Параметр | Коэффициент запаса |
Рабочий ток (напряжение) | 0,9 - 1,0 |
Коммутируемое напряжение | 1,0 |
Коммутируемый ток нагрузки: активной емкостной индуктивной | 0,05 - 0,9 0,05 - 0,7 0,01 - 0,5 |
Время срабатывания и отпускания | 1,2 |
Количество срабатываний | 0,7 |
Определив требуемые параметры РИМ, необходимо по справочнику выбрать соответствующий тип реле и его вид.
Электромагнитные релейные исполнительные механизмы.Из группы РИМ наибольшее распространение получили электромагнитные реле. Они подразделяются на реле постоянного и реле переменного тока. Реле постоянного тока, в свою очередь, подразделяются на нейтральные и поляризованные.
Нейтральные электромагнитные реле одинаково реагируют на полярность входного сигнала постоянного тока (т.е. положение якоря не зависит от направления тока в обмотке реле). Поляризованное реле реагирует на полярность входного сигнала.
По характеру движения якоря электромагнитные нейтральные реле подразделяются на два типа: с поворотным якорем и с втяжным якорем (рис. 6.5).
Обычно сердечник снабжается полюсными наконечниками, что уменьшает магнитное сопротивление рабочего воздушного зазора.
При отсутствии управляющего сигнала якорь удален от сердечника на максимальное расстояние за счет возвратной пружины. В этом случае одна пара контактов замкнута (РК – размыкающиеся контакты), а другая пара - разомкнута (ЗК – замыкающиеся контакты).
Рис. 6.5. Схемы электромагнитных реле:
а, b - клапанного типа; c - с втягиваемым внутрь катушки якорем; 1 - каркас
с обмоткой; 2 - ярмо; 3 - выводы обмотки; 4 - колодка; 5 - контактные пружины; 6 - замыкающийся контакт ЗК; 7 - подвижные контакты; 8 - размыкающиеся контакты РК; 9 - возвратная пружина; 10 - якорь; 11 - штифт отлипания; 12 – сердечник.
Принцип действия реле (рис. 6.5) основан на следующем: при подаче тока в обмотку (катушку) создается магнитный поток, который проходя через сердечник, ярмо, якорь и воздушный зазор d создает магнитное (тяговое) усилие, притягивающее якорь к сердечнику. При этом якорь, воздействуя на колодку, перемещает ее таким образом, что контакты ЗК замыкаются, а РК - размыкаются.
Таким образом, электромагнитное реле состоит из трех основных частей: контактной системы, выполненной из материала нейзильбера, магнитопровода (ярмо, сердечник, якорь), выполненные из мягкой стали, и обмотки (катушки). Магнитную цепь составляют сердечник, якорь, ярмо и воздушный зазор между якорем и сердечником.
Перемещение якоря электромагнитного реле происходит под действием двух сил: силы тяги, обусловленной электромагнитным полем и противодействующей силы, обусловленной упругой деформацией пружин. Обе эти силы зависят от перемещения якоря, т.е. от величины зазора между якорем и сердечником.
Зависимость между электромагнитной силой тяги Fэ и величиной зазора называется тяговой характеристикой реле . Зависимость между противодействующей силой Fм и величиной зазора называется механической характеристикой реле
.
Значение электромагнитной силы при изменении воздушного зазора описывается уравнением
.
Отсюда следует, что электромагнитное (тяговое) усилие (сила притяжения) прямо пропорционально квадрату магнитодвижущей силы (I×W), т.е. не зависит от направления тока в управляющей обмотке, и обратно пропорционально квадрату длины воздушного зазора (d2).
Тяговая характеристика представляет собой гиперболу (теоретическая характеристика уходит в бесконечность при d=0 ), однако практически эта характеристика отличается от гиперболы, что объясняется некоторой приближенностью формулы, не учитывающей магнитное сопротивление стальных элементов магнитопровода (сердечника, ярма и якоря).
Части магнитопровода реле после отключения обмотки питания сохраняют некоторое намагничивание, обусловленное коэрцитивной силой. Это намагничивание при может создавать тяговое усилие, достаточное для удержания якоря в притянутом состоянии. Может произойти так называемое «залипание» якоря. Для исключения «залипания» на вертикальной части якоря против оси сердечника (рис. 6.5 а, b) закрепляется штифт (наклепки или прокладки) из немагнитного материала. При притянутом якоре, благодаря наличию штифта, создается минимальный зазор
. Наличие этого зазора облегчает отход якоря при обесточивании обмотки реле.
По принципу действия реле переменного тока ничем не отличается от электромагнитного реле постоянного тока. Это объясняется тем, что тяговое усилие пропорционально квадрату намагничивающей силы и не зависит от направления тока. Поэтому, хотя переменный ток периодически меняет свое направление, знак тягового усилия не будет зависеть от направления тока, оставаясь неизменным.
Электромагнитная сила, создаваемая обмоткой реле переменного тока равна
,
где - максимальное амплитудное значение электромагнитной силы, создаваемой катушкой реле.
Рис. 6.6. Изменение тока и характеристика реле переменного тока.
Как видно из этой формулы, тяговое усилие колеблется с двойной частотой и не меняет своего знака (рис. 6.6), но дважды за период питающего напряжения обращается в нуль. Следовательно, якорь реле может вибрировать, периодически втягиваться от сердечника противодействующей пружиной, что вызывает дрожание якоря и, как следствие, быстрый износ контактов.
Для устранения этого недостатка используют три способа:
1. Применение утяжеленного якоря.Утяжеленный якорь благодаря большой инерции не может вибрировать с удвоенной частотой ( ), т.е. он не успевает отходить от сердечника в те моменты времени, когда ток в обмотке реле переходит через нуль. Вибрация якоря в этом случае уменьшается. Однако применение утяжеленного якоря вызывает увеличение его размеров, что приводит к уменьшению чувствительности реле, кроме того, габариты, вес и стоимость реле увеличиваются. Значительно ухудшаются временные параметры реле.
2. Применение двухфазного реле.Двухфазное реле имеет две обмотки, расположенные на двух сердечниках, имеющих общий якорь. Обмотки реле соединены параллельно относительно друг друга. В цепь одной из обмоток включен конденсатор С, благодаря чему токи в обмотках реле будут сдвинуты по фазе на угол . Следовательно, и тяговые усилия, развиваемые обмотками будут также сдвинуты по фазе на 90
. Это значит, что в момент, когда тяговое усилие, развиваемое одной обмоткой равно нулю, то тяговое усилие, развиваемое другой обмоткой в этот момент будет иметь максимальное значение. Поэтому в любой момент времени результирующее усилие не будет равно нулю, т. е.
.
Обычно магнитные потоки, развиваемые обмотками реле, равны. Тогда , а результирующее усилие равно
.
3. Применение короткозамкнутого витка.Короткозамкнутый виток (экран) охватывает часть конца сердечника (расщепленный сердечник) и является наиболее эффективным способом устранения явления дребезга контактов у реле переменного тока.
На рис. 6.7а изображена схема реле переменного тока с короткозамкнутым витком. Конец сердечника, обращенный к якорю, расщеплен (пропилен) на две части, на одну из которых надета короткозамкнутая обмотка - экран Э (один или несколько витков). Магнитопровод выполняют из отдельных листов для уменьшения потерь.
Рис. 6.7. Реле переменного тока с короткозамкнутым витком.
Принцип работы реле заключается в следующем. Переменный магнитный поток Фосн основной обмотки Wобм , проходя через разрезанную часть сердечника, делится на две части. Часть потока Ф1 проходит через экранированную половину полюса сердечника S2, в которой размещается короткозамкнутая обмотка (экран), а другая часть потока Ф1 проходит через неэкранированную половину полюса сечением S1 . Поток Ф2 наводит в короткозамкнутом витке ЭДС (eкз), которая создает ток iкз (на рис. 6.10 б разрез паза показан в увеличенном масштабе). При этом возникает еще один магнитный поток Фкз, который воздействует на магнитный поток Ф2 и вызывает отставание этого потока по фазе относительно потока Ф1 на угол φ = =60...80 . Благодаря этому результирующее тяговое усилие Fэ никогда не доходит до нуля, так как оба потока проходят через нуль в разные моменты времени.
Результирующее тяговое усилие, создаваемое обоими потоками, равно
;
Для полного устранения переменной составляющей тягового усилия необходимо выполнить следующие условия
1) чтобы , т.е.
;
2) чтобы фазовый угол между потоками Ф1 и Ф2 был равен
.
Последнее условие выполнить невозможно вследствие наличия активных потерь в короткозамкнутом витке (сопротивление короткозамкнутого витка не может быть равно нулю). Практически фазовый сдвиг может достигать 60-80
и, следовательно, тяговое усилие содержит переменную составляющую, но в меньших пределах, чем у реле, не имеющего короткозамкнутой обмотки и расщепленного сердечника. Среднее тяговое усилие Fэср при наличии экрана меньше тягового усилия Fэoср без экрана. Кроме того, для надежной работы реле необходимо, чтобы минимальное усилие Fэmin было как можно больше, так как именно это усилие определяет допустимую нагрузку реле без вибрации. Величина Fэmin зависит от степени охвата сердечника короткозамкнутой обмотки и других факторов. Опытным путем установлено, что наивыгоднейшие параметры короткозамкнутой обмотки могут быть получены при условии, если площадь поперечного сечения экранированного полюса будет в два раза больше площади поперечного сечения неэкранированного полюса, т.е. S2=2×S1.
Вопросы для самоконтроля:
1. Почему у реле переменного тока знак тягового усилия не зависит от направления тока?
2. С какой целью в реле переменного тока применяют утяжеленный якорь?
3. Сколько обмоток имеет двухфазное реле и как они соединены?
4. Почему магнитопровод реле переменного тока с короткозамкнутым витком выполняют из отдельных листов?
5. Как работает реле переменного тока с короткозамкнутым витком?
ТЕСТ 6.
Из предложенных Вам ответов на данный вопрос выберите правильный.
6.1.Что называется релейными исполнительными механизмами?
а) релейные элементы, выполняющие функции исполнительных механизмов.
б) релейные элементы, служащие для изменения скорости вала двигателя.
в) специальные устройства – герконы.
6.2.В чем особенность релейных исполнительных механизмов?
а) они осуществляют жесткое сцепление валов при подаче сигнала.
б) они представляют собой совокупность электромагнита, который выполняет роль управляющего устройства, и перемещаемой им механической нагрузки
в) они способны осуществлять управление электродвигателем.
6.3.Какова особенность коэффициента возврата?
а) коэффициентом возврата связывает параметры срабатывания и отпускания.
б)коэффициент возврата равен отношению параметра отпускания к параметру срабатывания.
в) верны оба вышеперечисленных варианта.
6.4. сколько бывает состояний у релейных исполнительных механизмов?
а) 2.
б) 3.
в) 4
6.5 на сколько типов по характеру движения якоря подразделяют электромагнитные нейтральные реле?
а) 1.
б) 2.
в) 3.
ОТВЕТЫ НА ТЕСТЫ
ТЕСТ 1.
1.1. в.
1.2. а.
1.3. а.
1.4. а.
1.5. б.
ТЕСТ 2.
2.1. б.
2.2. б.
2.3. а.
2.4. б.
2.5. а.
ТЕСТ 3.
3.1. б.
3.2. а.
3.3. в.
3.4. а.
3.5. а.
ТЕСТ 4.
4.1. а.
4.2. в.
4.3. а.
4.4. а.
4.5. б.
ТЕСТ 5.
5.1. а.
5.2. а.
5.3. а.
5.4. б.
5.5. а.
ТЕСТ 6.
6.1. а.
6.2. б
6.3. в
6.4. в
6.5. б.
ИТОГОВЫЙ ТЕСТ
Из предложенных Вам ответов на данный вопрос выберите правильный.
1. Как называются непрерывно изменяющиеся со временем сигналы?
а) Аналоговыми.
б) Импульсными.
в) Кодовыми.
2. Сколько видов электрических сигналов предусматривается использовать в соответствии с существующими стандартами в аналоговых средствах автоматизации?
а) 2.
б) 3.
в) 4.
3. Почему сигналы переменного тока редко используются для преобразования и передачи информации во внешних линиях связи?
а) Потому что для них трудно выполнить требование синфазности и подавить нелинейные искажения.
б) Ввиду больших потерь передаваемой мощности.
в) Вследствие отсутствия необходимой для этого аппаратуры.
4. Из каких элементов состоит типичный световод?
а) Из изолированного электропровода.
б) Из сердцевины и оболочки.
в) Из оптоволокна.
5. Какой способ управления электродвигателем получил широкое распространение в системах автоматического управления?
а) Метод широтно–импульсной модуляции.
б) Со стороны обмотки.
в) Со стороны якоря.
6. Как влияет на стоимость электродвигателя механизированное изготовление обмоток якоря?
а) Удорожает электродвигатель.
б) Удешевляет электродвигатель.
в) Совершенно не влияет на стоимость электродвигателя.
7. Как увеличить быстродействие шагового двигателя?
а) Увеличив габариты шагового двигателя.
б) Уменьшив его шаг, используя для этого электромагнитную индукцию.
в) Увеличив мощность шагового двигателя.
8. Какое основное требование, предъявляют к техническому устройству с точки зрения общей системы приборов и средств автоматизации?
а) Требование низкой стоимости.
б) Требование стандартизации параметров, которые определяют его связи с другими устройствами.
в) Требование малой металлоемкости.
9. Сколько различают видов внешних связей технических устройств?
а) 1.
б) 2.
в) 3.
10. Какой информацией необходимо располагать для правильного выбора мощности двигателя исполнительного механизма?
а) Иметь данные о приводных характеристиках нагрузки или объекта регулирования.
б) Иметь данные об энергетических потоках в объекте управления.
в) Иметь данные о трении в подшипниках исполнительного механизма.
СПИСОК ЛИТЕРАТУРЫ
1. Федотов А.В. Автоматизация управления в производственных системах. Учебное пособие. – Омск: Изд-во ОмГТУ, 2001.
2. Автоматика. Исполнительные механизмы. / Герасенков А.А., Вихрова Л.Г., Загинайлов В.И., Суворов С.А. – М.: МГУЛ, 2001.
3. Олссон Г., Пиани Д. Цифровые системы автоматизации и управления. – СПб.: Невский диалект, 2000.
4. Штанько Р.И. Электроника, микропроцессорные средства и техника связи. Учебное пособие. – М.: РГАЗУ, 2002.
6. Федотов А.В. Управление оборудованием и технологическими процессами в ГПС. Учебное пособие. – Омск: Изд-во ОмГТУ, 1999.
7. Хомченко В.Г., Голобурдин А.И., Федотов А.В. Автоматизация технологических процессов и производств. Учебное пособие. – Омск: Изд-во ОмГТУ, 1999.
Жужжалов Валерий Евгеньевич, Солдатов Виктор Владимирович,
Маклаков Владимир Васильевич, Жиров Михаил Вениаминович
Технические средства автоматизации
Учебно-практическое пособие
Подписано к печати:
Тираж:
Заказ №
Дата добавления: 2018-02-28; просмотров: 4308; Мы поможем в написании вашей работы! |
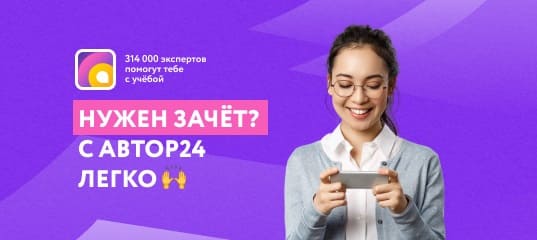
Мы поможем в написании ваших работ!