Liquid stripping for Type 'C' tanks
For ships having Type 'C' cargo tanks a cargo stripping line is often provided (see Figure 4.1).
By pressurising the cargo tanks on these ships, (using the cargo compressor) residual liquid can be lifted from the tank sump into the stripping line and thence to deck level. It may then be stored temporarily in a chosen cargo tank for returning to the shore. Alternatively, it may be stored in a deck-mounted pressure vessel provided for the purpose. This draining should continue until all liquid cargo is removed from the cargo tanks, as checked through the bottom sampling line. The compressor pressure necessary to remove residual liquid will depend on the specific gravity of the cargo and the depth of the tank (see Figure 7.14).
Figure 7.14 Removal of cargo liquid residue by pressurisation
Liquid freeing for other tank types
For ships with Type 'A' or 'B' tanks the removal of all cargo liquid residues is not possible by pressurisation. Instead, cargo liquid residues must be vaporised. This is normally achieved using puddle heating coils.
When puddle heating coils are used, the heat source in the coils is hot gas discharged from the cargo compressor. Vapour is drawn from the cargo tank atmosphere and passed through the compressor where the heat of compression causes increased vapour temperatures. By by-passing the condenser, hot vapour can be led directly to the heating coil system and heat is transferred to the liquid cargo residue. In this way remaining liquid is evaporated and an effect of the heat transfer is to turn the hot vapour in the coils into liquid which is then normally piped to a deck-mounted tank.
An alternative to the use of puddle heating coils is to supply hot cargo vapours (from the compressor) directly to tank bottoms. However, as already covered earlier in this section, this results in much slower evaporation of remaining liquids than the method described above as the hot gas only flows over the surface of the liquid pool rather than causing boiling within it. This method is used, however, on LNG carriers not fitted with puddle heating and on some smaller ships where increasing temperature on special cargo grades could be problematic.
When a ship is at sea, in order to finalise either type of operation, cargo tank vapour is normally sent to the vent riser. Alternatively, it may be condensed and pumped into deck storage or overboard. If the ship is in port, as venting to atmosphere is seldom allowed, the condensate is usually pumped to the shore or put into deck storage. (See 7.3)
|
|
When all tanks have been satisfactorily liquid-freed, pipework and other in-line equipment must be blown free from liquid and drained through the appropriate drain valves.
7.9.2 Warming-up
When cargo tanks have to be fully ventilated with fresh air, it is often necessary, depending on tank temperatures and design considerations, to warm-up the tanks
prior to inerting. This is achieved by controlled circulation of warm cargo vapours through the tanks and is done before inerting takes place.
As for the cool-down (see 7.4), the rate of warm-up should be carefully controlled in accordance with the shipbuilder's guidance.
Warming up is vital where cargo tanks are at very low temperatures, for example on board LNG ships. On such ships, compressors and heaters are operated to circulate warm gas. First, this evaporates any residual liquid and, thereafter, the whole tank structure is warmed to ambient conditions.
If warming up to ambient temperature is not carried out, freezing of carbon dioxide from within the inert gas can result. (Moreover, greater volumes of inert gas will be required at low temperatures.)
7.9.3 Inerting — after discharge
Removal of cargo vapours with inert gas is carried out to reduce gas concentrations to a level where aeration can take place without the tank atmosphere passing through the flammable envelope (see Figure 2.19). The level to which the hydrocarbon vapour must be reduced varies according to the product and details of the varying flammable envelopes for each product are given in Reference 2.1. In general, when inerting in this way, it is necessary to reduce the hydrocarbon content in the inert atmosphere to about 2 per cent before air blowing can begin. (Although this is conservative for methane, it is in accord with common practice).
Дата добавления: 2018-02-28; просмотров: 855; Мы поможем в написании вашей работы! |
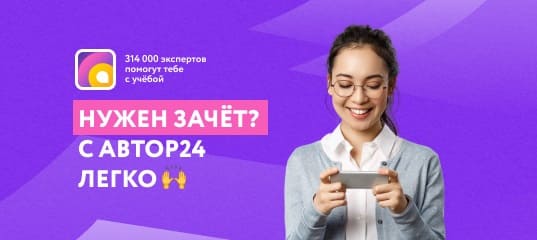
Мы поможем в написании ваших работ!