Inerting prior to loading ammonia
Modern practice demands that ships' tanks be inerted with nitrogen prior to loading ammonia. This is so, even though ammonia vapour is not readily ignited.
Inert gas from a combustion-type generator must never be used when preparing tanks for ammonia. This is because ammonia reacts with the carbon dioxide in inert gas to produce carbamates. Accordingly, it is necessary for nitrogen to be taken from the shore as shipboard nitrogen generators are of small capacity.
The need for inerting a ship's tanks prior to loading ammonia is further underscored by a particular hazard associated with spray loading. Liquid ammonia should never be sprayed into a tank containing air as there is a risk of creating a static charge which could cause ignition. (Mixtures of ammonia in air also introduce an additional risk as they can accelerate stress corrosion cracking — see 2.3.)
7.3 GASSING-UP
Neither nitrogen nor carbon dioxide, the main constituents of inert gas, can be condensed by a ship's reliquefaction plant. This is because, at cargo temperatures, each is above its critical temperature and is, therefore, incondensible. Accordingly, removal of inert gas from the cargo tank is necessary. This is achieved by gassing-up, using vapour from the cargo to be loaded at ambient temperature and venting the incondensibles to atmosphere so that subsequently the reliquefaction plant can operate efficiently.
Similarly, on changing grade, without any intervening inerting, it may first be necessary to remove the vapour of the previous cargo with vapour of the cargo to be loaded. The basic principles discussed previously in respect of inerting methods apply equally
to this type of gassing-up. However, when gassing-up, there is usually a greater density difference between cargo vapours — see Table 2.5 — than is the case when inerting from air. (See 9.7.3 and 9.7.4 for measuring progress in this operation).
7.3.1 Gassing-up at sea using liquid from deck storage tanks
Gassing-up at sea is a procedure normally only available to fully refrigerated, or semi-pressurised ships. Such carriers are often equipped with deck tanks which may have a compatible cargo in storage. In this case, either vapour or liquid can be taken from the deck tanks into the cargo tanks.
Liquid can be taken directly from deck storage through the tank sprays (with the exception of ammonia). This is done at a carefully controlled rate to avoid cold liquid striking warm tank surfaces. In this case, vapour mixing occurs in the cargo tanks and the mixed vapours can be taken into other tanks (when purging in series) or exhausted to the vent riser.
|
|
Alternatively, liquid from the deck storage tanks can be vaporised in the cargo vaporiser and introduced gradually into the top or bottom of the cargo tank, depending on vapour density, to displace the existing inert gas or vapour to other tanks or to the vent riser.
Only when the concentration of cargo vapour in the tanks has reached approximately 90 per cent (or as specified by the compressor manufacturer) should the compressor be started and cool-down of the system begin.
7.3.2 Gassing-up alongside
Gassing-up operations which take place alongside are undertaken using cargo supplied from the shore. At certain terminals, facilities exist to allow the operation to be carried out alongside but these terminals are in a minority. This is because the venting of hydrocarbon vapours alongside a jetty may present a hazard and is, therefore, prohibited by most terminals and port authorities.
Thus, well before a ship arrives in port with tanks inerted, the following points must be considered by the shipmaster:—
• Is venting allowed alongside? If so, what is permissible?
• Is a vapour return facility to a flare available?
• Is liquid or is vapour provided from the terminal for gassing-up?
• Will only one tank be gassed-up and cooled down initially from the shore?
• How much liquid must be taken on board to gas-up and cool-down the remaining tanks?
• Where can the full gassing-up operation be carried out?
Before commencing gassing-up operations alongside, the terminal will normally sample tank atmospheres to check that the oxygen is less than five per cent for LPG cargoes (some terminals require as low as 0.5 per cent) or the much lower concentrations required for chemical gases such as vinyl chloride — see Table 2.3(b).
Where no venting to atmosphere is permitted, a vapour return facility must be provided and used throughout the gassing-up operation. In this case, either the ship's
Figure 7.3(a) Gassing-up cargo tanks using liquid from shore
|
|
Figure 7.3(b) Gassing-up cargo tanks using vapour from shore
cargo compressors or a jetty vapour blower can be used to handle the efflux. Some terminals, while prohibiting the venting of cargo vapours, permit the efflux to atmosphere of inert gas. Thus, if a displacement method of gassing-up is used — see 7.2.3 — the need for vapour return to shore may be postponed until cargo vapours are detected at the vent riser. This point may be considerably postponed if tanks are gassed-up one after the other in series.
Where a terminal supplies a liquid for gassing-up, it should be loaded at a carefully controlled rate. It is then passed through the ship's vaporiser. Alternatively, the liquid may be allowed to vaporise in the ship's tanks. If vapour is supplied, this can be introduced into the tank at the top or bottom depending on the vapour density (see Table 2.5). Figures 7.3(a) and 7.3(b) show typical gassing-up operations using liquid from shore and vapour from shore, respectively.
When a ship arrives alongside with tanks containing a cargo vapour which requires to be replaced with the vapour of a different grade, then the terminal will normally provide a vapour return line. The vapours taken to the shore will be flared until the desired vapour quality is achieved in the tanks. At this point cool-down can begin.
If facilities, such as a vapour return line, are not available for the ship to gas-up alongside, it is common practice for the ship to prepare one cargo tank and to take sufficient liquid to complete the operation elsewhere. The ship then leaves the berth for a designated anchorage or proceeds to sea. The ship returns to the berth after having gassed-up and cooled-down all cargo tanks.
Recent developments have been made in LPG vapour recovery systems. Such systems are using the energy obtained from vapourising liquid nitrogen to reliquefy the cargo vapour returned from the ship, either during gassing-up operations or during inerting operations, (see 7.9.3) thus avoiding any venting of hydro carbon gases. The skid mounted unit would recieve liquid nitrogen from a truck, vapourise it for delivery to the ship and at the same time reliquefy the return cargo vapour for storage and further usage.
7.4 COOL-DOWN
Дата добавления: 2018-02-28; просмотров: 757; Мы поможем в написании вашей работы! |
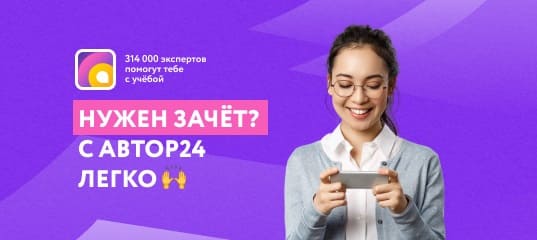
Мы поможем в написании ваших работ!