Description of shore pipeline engineering standards
Pipeline design and engineering in terminals is most often covered by standards developed jointly by the American Standards for Testing and Materials (ASTM) and the American Society of Mechanical Engineers (ASME). Another similar organisation is the American National Standards Institute (ANSI). Of course, national codes are also consulted. According to the American standards, depending on the product being handled, differing design factors prevail. In this regard petroleums have been divided into four classes: A, B, C, and D, respectively. LPG and ammonia, for example, fall into Class D which is the category carrying the highest risk.
Pipelines which run outside terminal compounds are normally designed in accordance with ASTM/ASME standards B31.4 and B31.8. In the area of the ship/shore interface these standards may only need to be addressed by terminals when considering pipework to jetties and on the jetty itself. These standards consider population densities and provide guidance for extra precautions as pipelines traverse areas of differing population levels. Also considered in the standards are practical difficulties such as the design requirements at road crossings.
External damage is a major cause of pipeline failures and specific precautions against this should be addressed. In particular, pipelines on jetties should be suitably protected against damage by vehicles.
Most pipelines within terminals are designed and engineered to the ANSI/ASME B31.3. In addition to the general engineering aspects, as covered in B31.3, design limits such as temperature and pressure for a particular pipeline are specified in ANSI B16.5. The standards also address maximum working conditions and provide design characteristics for pipes, flanges, fittings, reducers, gaskets and bolting. It is this latter standard which identifies flange pressure/temperature ratings such as Class 150 and Class 300 either of which may be found in terminals depending on the working pressure of the system.
Surge pressures
When a terminal is being designed, the proposed pipeline system for liquefied gases should be subject to hydraulic analysis. At this time the question of surge pressure
Figure 5.17 Bursting disc for surge pressure relief
ought to be covered by the establishment of the MAIP (Maximum Allowable Incidental Pressure). Pressure surges in pipelines are created by changes in the momentum of the moving stream. An example of an event causing a surge is sudden valve closure.
|
|
Surge pressures are particularly critical for pipelines transporting liquids. This is because of the density of liquid, and its low compressibility as compared to vapour. Pressure surges are additional to the maximum working pressure. They can be very high. They travel at the speed of sound in the liquid and reverberate from one end of the closed section to the other.
On this subject, it is worthy of note that surge pressures can be more severe when pumping liquefied gas cargoes as compared to other products. This is because gas cargoes are only ever in association with their own gas. Products such as oil cargoes may mix with air or inert gas and, even in very small admixed quantities, this effect can produce significant buffering.
To cater for surge pressures, the standard used should allow for a maximum short-term over-pressure. This short-term limited pressure rating is to cover anticipated surges and other variations.
Methods of limiting high surge pressures include adjusting valve closing times and special fast-response pressure relief systems. In addition, mountings for pipelines on the jetty should be properly engineered to protect the jetty structure from shock loads. For further reading on this subject Reference 2.25 is recommended.
The danger of surge pressure generation may be greatly minimised by providing surge pressure relief of the loading pump and loading line. There are various means of achieving this relief. One such is by means of a kick-back pipeline to a storage tank at the pump discharge; another system is that outlined in Figure 5.17. Here, surge protection is provided by bursting discs. Liquid released is collected in a surge drum which is held under a nitrogen or a product vapour blanket. Liquid collected is normally returned to the loading line or drained to blow-down and vapours are normally vented to the vapour recovery system or to a flare (see also 4.1.3, 4.9.2, 6.6.4 and 10.5).
5.3.3 Pumps, compressors and heat exchangers
Within terminals, centrifugal pumps are normally used for pumping operations when loading ships. These pumps may be inside or outside of the tank and are usually of the following types:—
|
|
• Deepwell pumps
• Vertical in-line pumps
• Horizontal foot-mounted pumps, or
• Submerged pumps within the tank
The type of pump used depends on the installation and type of storage.
Product flow can normally be controlled by a flow control valve. Where refrigerated tanks are situated at some distance from the jetty, it is normal to provide a re-circulation facility for maintaining the product pipeline at a low temperature between cargo transfers. This minimises vapour generation in the ship or shore tank during early stages of cargo transfer.
Дата добавления: 2018-02-28; просмотров: 844; Мы поможем в написании вашей работы! |
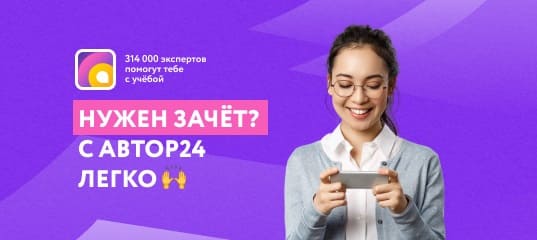
Мы поможем в написании ваших работ!