Определение типа производства
Тип производства представляет собой комплексную характеристику технических, организационных и экономических особенностей производства, обусловленных степенью специализации, сложностью и устойчивостью изготовляемой номенклатуры изделий, размером и повторяемостью выпуска продукции.
Основным показателем, характеризующим тип производства, является коэффициент закрепления операций, который определяется как отношение числа всех различных технологических операций, выполняемых или подлежащих выполнению в течение месяца, к числу рабочих мест.
В теории и практике различают три типа производства: единичное, серийное и массовое.
Единичное производство характеризуется малым объемом выпуска одинаковых изделий.
Серийное производство характеризуется производством нескольких однородных типов изделий, периодически повторяющимися партиями или сериями.
Массовое производство характеризуется большим объемом выпуска изделий, непрерывно изготовляемых продолжительное время, в течение которого на большинстве рабочих мест выполняется одна рабочая операция по детальной специализацией участков.
Определяем размер партии деталей
=
=395 штук, (6)
где N – годовая программа выпуска, штук;
α – количество дней запаса деталей на складе;
ф – количество рабочих дней в году.
|
|
Принимаем 400 штук.
Анализ базового технологического процесса
Таблица 4 - Базовый технологический процесс
№ операции | Наименование и содержание операции | Модель оборудования |
005 | Контроль | Стол контролера |
010 | Отрезная | ВТС |
015 | Токарно-револьверная | 1Г340П |
020 | Токарно-револьверная | 1Г340П |
025 | Вертикально-сверлильная | 2С132 |
030 | Горизонтально-фрезерная | 6М83Г |
035 | Горизонтально-фрезерная | 6М82Г-1 |
040 | Слесарная | КЗ 7409 А |
045 | Промывка | 65-330 |
050 | Контроль | Плита 2-2-1600x1000 |
Выбор заготовки, ее технико-экономическое обоснование
Технико – экономическое обоснование выбора заготовки для изготовления детали «Штуцер» производим учитывая металлоемкость, трудоемкость, себестоимость и конкретные производственные условия. В машиностроении основными видами заготовок для деталей машин являются стальные и чугунные отливки, отливки из цветных металлов и сплавов, штамповки и всевозможные профили проката.
Способ получения заготовок должен быть наиболее экономичным. Для изготовления детали «Штуцер» применяем два способа получения заготовки: из проката и методом горячей объемной штамповки.
|
|
Производим технико-экономическое сравнение двух вариантов изготовления заготовки.
Определение стоимости заготовки из проката
За основу расчета промежуточных припусков принимаем наружный диаметр детали Æ 26мм.
Таблица 5 - Технологический маршрут обработки поверхности
Размер поверхности по чертежу, мм | Параметр шероховатости, Ra. мкм | Квалитет точности | Методы обработки |
Æ 26 | 50 | 17 | Заготовка прокат. Без обработки. |
Определяем припуски на обработку наружной поверхности
2Z = 0 мм [1, стр.41, таб. 3.13]
Припуски на подрезание торцевых поверхностей
Z = 0,5 мм [1, стр.40, таб. 3.12]
Определяем промежуточные размеры обрабатываемых поверхностей согласно маршруту технологического процесса.
(7)
где - диаметр детали, мм;
2Z - припуск на обработку, мм.
= 26 + 0 = 26 мм
По ГОСТ 2590-2006 определяем размер горячекатаного проката обычной точности
|
|
мм
Определяем общую длину заготовки
, (8)
где - длина детали, мм;
- припуск на подрезку торцов, мм.
= 23 + 2 · 0,5 = 24 мм, принимаем 24 мм
Определяем объем заготовки с учетом плюсовых отклонений
, (9)
где p – 3,14;
D - диаметр заготовки, см;
L - длина заготовки, см .
V =
13,13 см
Определяем массу заготовки по формуле
, (10)
где - плотность стали, кг/см3 ;
Vз.п – объем заготовки прокат, см .
= 0,00785 · 13,13 = 0,11 кг
Определяем коэффициент использования материала
, (11)
|
|
где - масса детали, кг;
- масса заготовки из проката, кг .
Ким = = 0,64
Определяем стоимость заготовки из проката
(12)
где С - оптовые цены на сортовой материал, руб.;
С - 0,137 ×400 руб. [1, стр.143, пр. 8]
m - масса заготовки из проката, кг;
С - оптовые цены на лом и отходы углеродистых черных металлов, руб.
С = 28,1 × 400 руб. [1, стр.141, пр. 7]
С = 0,137 · 400 · 0,11 - (0,11 – 0,07) ·
= 6,58 руб.
2.3.2 Определение стоимости заготовки изготовленной методом горячей объемной штамповки на горизонтально-ковочной машине (ГКМ)
Техническая характеристика заготовки:
- класс точности Т4; [7, прил.1, таб.19, стр.28]
- группа стали M2; [7, таб.1, стр. 8]
- степень сложности определяется путем вычисления отношения массы поковки к массе геометрической фигуры, в которую вписывается форма поковки [7, прил. 2, стр. 29]
Определяем массу геометрической фигуры в которую вписывается форма поковки mф
, (13)
где p – 3,14;
D – наружный диаметр детали, см;
L – длина детали, см;
ρ - плотность стали, кг/см3.
см3
Определяем расчетную массу поковки
m = m
· К
, (14)
где m - расчетная масса поковки, кг;
m - масса детали, кг;
К - расчетный коэффициент.
К = 1,3 – 1,6 [7, с.31, прил. 3]
m = 0,07 · l,3 = 0,09 кг
Определяем отношение mn/mф, затем определяем степень сложности
=0,90 (15)
Степень сложности – С1 [7, прил. 2, стр. 29]
Определяем исходный индекс 8 [7, табл. 2, стр. 10]
Разрабатываем эскиз на штампованную заготовку [1, стр.45]
Рисунок 1- Рабочий чертёж заготовки
Прошивается отверстие в золовке штамповке, если диаметр отверстия
больше 25 мм, а длина отверстия L<2Dотв
Определяем основные припуски на размеры: [7, стр. 12, таб. 3]
Диаметр 26 мм, параметр шероховатости 50 мкм, припуск 0 мм;
Длина 14 мм, параметр шероховатости 6,3 мкм, припуск 1,1 мм;
Диаметр 20 мм, параметр шероховатости 12,5 мкм, припуск 0,9 мм;
Длина 9 мм, параметр шероховатости 6,3 мкм, припуск 1,1 мм;
Определяем размеры поковки, мм:
Диаметр 26 + 0 · 2 = 26, принимаем 26;
Длина 14+ 1,1 · 2 = 16,2, принимаем 16,5;
Диаметр 20 + 0,9 · 2 = 21,8, принимаем 22;
Длина 9+ 1,1 = 10,1, принимаем 10,55.
Определяем допускаемые отклонения размеров, мм:
Ø26 16,5
Ø22
10,5
[7, стр. 17 таб. 8]
Разбиваем заготовку на условные фигуры и определяем объем этих фигур с учетом плюсовых допусков [1, стр.45]
Рисунок 2 - Элементы заготовки для определения объёма
Определяем объем отдельных элементов заготовки V1,V2
, (16)
где p – 3,14;
D – диаметр поверхности заготовки, см;
L – длина поверхности заготовки, см;
см3
см3
Определяем общий объем
, (17)
см3
Определяем массу заготовки штамповка
, (18)
где ρ – плотность стали, кг/ см ;
V – объем заготовки штамповка, см .
кг
Определяем коэффициент использования материала
, (19)
где m - масса детали, кг;
m - масса заготовки штамповка, кг.
Определяем стоимость заготовки штамповка
, (20)
где С - оптовая цена за 1 кг горячештамповочных заготовок, руб.
С = 0,638 × 400 руб. [1, стр.143, прил. 8]
m - масса заготовки штамповка, кг;
С - оптовые цены за 1 тонну на лом и отходы углеродистых черных металлов, руб.
С = 28,1 × 400 руб. [1, стр.141, прил. 7]
руб.
Определяем годовую экономию материала от выбранного варианта изготовления заготовки
Э =(m
- m
) · N, (21)
где m - масса заготовки прокат, кг;
m - масса заготовки штамповка, кг;
N – годовая программа выпуска, штук.
Э = (0,11– 0,11) · 20000 = 0 кг
Определяем экономический эффект по стоимости изготовления заготовки
Э =(С
-С
) · N, (22)
где С - стоимость заготовки штамповка, руб.;
С - стоимость заготовки прокат, руб.;
N – годовая программа выпуска, штук.
Э = (27,63 – 6,58) · 20000 = 421000 руб.
Таблица 6 – Наиболее выгодный способ получения заготовки
Показатели | Вид заготовки | |
прокат | штамповка | |
1. Масса детали, кг | 0,07 | |
2. Масса заготовки, кг | 0,11 | 0,11 |
3. Коэффициент использования материала | 0,63 | 0,63 |
4. Стоимость заготовки, руб. | 6,58 | 27,63 |
5. Экономический эффект от материала заготовки, кг | 0 | |
6. Экономический эффект от стоимости, руб. | 421000 | |
7. Наиболее выгодный способ получения заготовки | + |
2.4 Разработка маршрута обработки детали
2.4.1 Технологический процесс обработки детали
Таблица 7 – Маршрут обработки детали
№№ операции | Наименование и содержание операции | Модель станка | Режущий инструмент | Приспособление |
005 | Отрезная | ВТС-50 | ||
1 .Установить и закрепить заготовку | Зажим при станке | |||
2. Отрезать заготовку в размер L=1000 на 33 детали | Пила 2257-0156 ГОСТ 4047-82 | |||
010 | Токарно-винторезная с ЧПУ | 16К20Ф3С32 | ||
1.Установить деталь, закрепить | Патрон 7100-0005 ГОСТ 2675-80 | |||
2. Подрезать торец «как чисто», точить фаску 2*300 | Резец 2102-0055 Т15К6 ГОСТ 18877-73 | |||
3.Сверлить центровое отверстие Ф3,15 | Сверло 2317-0006 ГОСТ 14952-75 | |||
4.Сверлить отверстие Ф11+0,52 в размер L14±0,215 | Сверло 2301-0063 ГОСТ10903 -77 | |||
5. Зенковать фаску 1*450 | Зенковка 2353-0136 ГОСТ 14953-80 | |||
6. Сверлить отверстие Ф 7+0,36 | Сверло 2301-0007ГОСТ10903 -77 | |||
7. Отрезать деталь в размер 24,5-0,62 | Резец 2130-0009 Т15К6 ГОСТ18884-73 | |||
015 | Токарно-винторезная с ЧПУ | 16К20Ф3С32 | ||
1.Установить деталь, закрепить | Патрон 7100-0005 ГОСТ 2675-80 | |||
2. Подрезать торец в размер 23±0,26, точить поверхность до Ǿ 20-0,52, выдерживая размер 9±0,18, точить фаску 3*450 | Резец 2102-0055 Т15К6 ГОСТ 18877-73 | |||
020 | Вертикально-сверлильная | 2С132 | ||
1.Установить деталь и закрепить | Патрон при станке | |||
2. Нарезать резьбу М12*1-6Н | Метчик 2620-1719 ГОСТ 3266-81 Метчик 2620-1717,2 ГОСТ3266-81 | |||
025 | Горизонтально-фрезерная | 6М83Г | ||
1.Установить и закрепить деталь | Приспособление ТТ222-4231 Втулка разрезная цеховая | |||
2.Фрезеровать лыски в размер 22±0,26 | Фреза 2240-0214 ГОСТ28527-90 Фреза 2240-0214 ГОСТ28527-90 |
Продолжение таблицы 7
№№ операции | Наименование и содержание операции | Модель станка | Режущий инструмент | Приспособление |
030 | Горизонтально-фрезерная | 6М82Г-1 | ||
1.Установить деталь и закрепить | Патрон при станке | |||
2.Фрезеровать поверхность R10 | Фреза 2223-0503 ГОСТ20537-75 | |||
035 | Контроль | |||
1. Проверить размеры согласно чертежа. | Плита 2-2-1600х1000 ГОСТ10905-86 |
2.4.2 Расчет припусков ( по округленным нормативам )
Припуски определяются табличным и расчетно-аналитическим методом. Припуск - это излишний слой материала, необходимый для получения заданных размеров и чистоты поверхностей деталей. Разность размеров заготовки и детали определяет величину припуска.
Величина припуска зависит от ряда факторов: материал заготовки и способ ее изготовления, размеры заготовки, требования в отношении качества поверхности и точности размеров детали.
Табличным методом определяются припуски на основании стандартов. Данный метод применяется в единичном и серийном производстве.
Таблица 8 - Табличный метод расчета припусков
Вид операции. | Точность заготовки. | Расчетные припуски, мм | Расчетные размеры, мм | Допуск,Тd, мм | Dmax,мм | Dmin, мм | 2Z max,мм | 2Z мin,мм |
Наружная поверхность L=23±0,26 |
25±1,05 | |||||||
Заготовка прокат | 17 | 1,0 | 23,74 | 2,10 | 25,84 | 23,74 | _ | _ |
Токарная черновая | 14 | 1,0 | 22,74 | 0,52 | 23,26 | 22,74 | 2,58 | 1,0 |
Проверка: разность суммы максимальных и минимальных припусков равно разности допуска заготовки и допуска детали.
S Z max – S Z min= Тзаг. – Тдет (23)
2,58 – 1,0 = 2,10 – 0,52
1,58 мм =1,58 мм
2.4.3 Расчет режимов резания (на две операции по нормативам)
Разработка технологического процесса механической обработки заготовки обычно завершается установлением технологических норм времени для каждой операции.
Режимные параметры выбираются таким образом, чтобы была обеспечена наибольшая производительность труда при наименьшей себестоимости данной технологической операции. Эти условия удается выполнить при работе инструментом рациональной конструкции найвыгоднейшей геометрии с максимальным использованием всех эксплуатационных возможностей станка.
При определении режимов резания пользуемся табличным методом, как наиболее простым и дающим возможность ускорить разработку технологических
процессов и сократить сроки подготовки к запуску изготовления изделия.
2.4.3.1 Расчёт режимов резания на операцию 015 – токарно-винторезная с ЧПУ
Содержание операции:
Переход 1
Установить, закрепить и снять заготовку
Переход 2
Подрезать торец в размер 23±0,26, точить поверхность до Ǿ 20-0,52, выдерживая размер 9±0,18, точить фаску 3*450
1) Нормирование основного времени
1.1) Выбор режущего инструмента
2 переход – резец проходной отогнутый, материал режущей части Т15К6, φ=45° [4, карта 7, стр.34]
Выбираем номер эскиза резца 2, тип конструкции резца М [4, карта 8, стр.43]. Оценка в баллах 4 [4, карта 9,стр.45]
Геометрические параметры лезвия инструментов: α = 6°; γ = 10°; fo =1,2 мм. [4, карта 11,стр.50]
1.2) Определяем глубину резания
t2 = (D-d)/2, (24)
где D – диаметр до обработки, мм;
d – диаметр после обработки, мм.
t2 = (26-20)/2=3мм
1.3) Определяем подачу S
S2Т= 0,50 мм/об [4, карта 12, стр. 58]
Расчетная подача
S2р=S2·КS0·КS1·КS2·КS3·КS4·КS5·КS6=0,50 · 1,2 · 0,9 · 1,4 · 0,75 · 1,0 · 1,0 · 0,7=
0,39 мм/об, (25)
где S2т – табличная подача, мм/об;
КS0 – поправочный коэффициент; [4, карта 12, стр. 59]
КS1КS2, КS3, КS4, КS5, КS6 – поправочные коэффициенты. [4, карта 12, стр.70-73]
Корректируем подачу
S2n= 0,40 мм/об
1.4) Определяем скорость резания
V2т= 145 м/мин [4, карта 12, стр. 60]
Расчетная скорость резания
V2р=V2т·Кv0·Кv1·Кv2·Кv3·Кv4·Кv5·Кv6=145 · 1,1 · 1,15 · 1,2 · 1,05 · 1,0 · 0,9 · 1,0 · 1,0 = 208,0 м/мин, (26)
где V2т – табличная скорость резания, м/мин;
Кv0 – поправочный коэффициент; [4, карта 12, стр. 61]
Кv1, Кv2, Кv3, Кv4, Кv5 – поправочные коэффициенты. [4, карта 12, стр. 73-75]
1.5) Определяем частоту вращения
n= 1000*Vр, (27)
pD
где V- расчетная скорость резания, м/мин;
π-3.14;
D - диаметр до обработки, мм.
n2= 1000*208= 2547 мин -1
3,14* 26
Корректируем частоту вращения по паспортным данным [10, прил.1, стр. 422]
n2n= 800 мин -1
1.6) Определяем фактическую скорость резания
Vф= pDnn , (28)
1000
где V – расчетная скорость резания, м/мин;
p – 3,14;
D – диаметр до обработки, мм;
nп – частота вращения шпинделя по паспорту, мин-1 .
V2ф= 3.14* 26* 800 = 65,3м/мин
1000
1.7) Определяем мощность, затрачиваемую на резание
Nт2=1,5кВт. [4, карта 12. стр. 76]
Расчетная мощность, затрачиваемая на резание
Nр=Nт · К, (29)
где Nт-табличная мощность резания, кВт;
К- поправочный коэффициент на мощность резания.
Nр=1,5 · 1.05=1,58 кВт. [4, карта 12. стр. 77]
Проверяем станок по мощности [10, прил. 1. стр. 421]
Nр≤Nдв · η , (30)
где Nдв- мощность двигателя, кВт;
η -КПД станка.
1,58 кВт ≤11 · 0,75=8,25 кВт.
В связи с тем, что Nр меньше допустимой, то обработка возможна на всех переходах.
1.8) Определяем основное время
Т0= Lрез/(Sп · nп) · i , (31)
где Lрез. – длина рабочего хода инструмента, мм;
Lрез.= L+ lвр.+ lпер, (32)
где L – длина обрабатываемой поверхности, мм;
lвр – врезание резца, мм; [4, прил. 6, стр. 168]
lпер. – перебег резца, мм;
Sn – подача по паспорту, мм/об;
nп – частота вращения шпинделя по паспорту, мин-1;
i – количество проходов.
Т02=((26-7)/2+12+8)/0,4 · 800=29,5/320=0,10мин.
Т0=Т02=0,10мин.
2.4.3.2 Расчёт режимов резания на операцию 025 – горизонтально-фрезерная
Содержание операции:
Переход 1
Установить, закрепить и снять заготовку
Переход 2
Фрезеровать 2 лыски, выдерживая размер 1=22±0,26
1) Нормирование основного времени
1.1) Выбор режущего инструмента.
2 переход – 2 фрезы дисковые трёхсторонние Ø 100, материал режущей части Т15К10,обработка без охлаждения [4,карта 9, стр. 206]
Геометрические параметры лезвия инструмента
= 60°,α= 10°,γ = 20°,z = 60
1.2) Определяем глубину резания
t2 = 2 мм
1.3) Определяем подачу зуб [4,карта 1, стр. 295]
SzТ2= 0,012 мм/зуб
Расчетная подача [4,карта 1, стр. 295]
Szр2=SzТ2·КS1·КS2·КS3·КS4·КS5·КS6=0,012 · 1,0 · 1,2 · 0,8 · 1,0 · 1,0 · 1,0=
0,011 мм/зуб (33)
где SzТ2 – табличная подача, мм/об;
КS1, ·КS2, ·КS3, ·КS4, ·КS5, ·КS6 – поправочные коэффициенты. [4, карта 1, стр. 295-296]
1.4) Определяем подачу на 1 оборот фрезы
S02 = Szp2 · z = 0,011 · 60 = 0,66 мм/об, (34)
где Szp2 - расчетная подача, мм/зуб;
Z- число зубьев фрезы.
1.4) Определяем скорости резания Vрез
VТ2= 54 м/мин [4, карта 2, стр. 297]
Расчетная скорость резания
Vр2=VТ2·Кv1·Кv2·Кv3·Кv4·Кv5·Кv6 = 54 · 1,3 · 1,3 · 1,15 · 0,8 · 1,0 · 1,3=
41,9 м/мин , (35)
где V2т – табличная скорость резания, м/мин;
Кv1·Кv2·Кv3·Кv4·Кv5·Кv6 – поправочные коэффициенты. [4, карта 2, стр.298 - 299]
1.5) Определяем частоту вращения
n= 1000*V2р, (36)
pD
где V2р- расчетная скорость резания, м/мин;
π-3.14;
D - диаметр фрезы, мм.
n2= 1000*41,9= 213 мин -1
3,14* 100
Корректируем частоту по паспортным данным [10, прил.1 стр.422]
nп = 200 мин -1
1.6) Определение фактической скорости резания
Vф= pDnn , (37)
1000
где nп – частота вращения фрезы, мин -1;
p – 3,14;
D – диаметр фрезы, мм.
Vф=3,14* 100* 200 = 16,4 м/мин
1000
1.7) Определяем минутную подачу
SМ = So·nп =0,66 · 200 =132 мм/мин, (38)
где S20 – подача на 1 оборот фрезы, мм/об;
nп – частота вращения фрезы по паспорту, мин-1
Корректируем минутную подачу по паспортным данным [10, прил. 1, стр. 422]
SМп = 125 м/мин
1.8) Определяем фактическую подачу на зуб
S2z = S2Мп /z×nn , (39)
где S2Мп – минутная подача по паспорту, мм/мин;
Z – число зубьев фрезы;
nn – частота вращения фрезы по паспорту станка, мин-1.
Sz2 =125 / 60×200 = 0,01 мм/зуб
1.9) Определение мощности, затрачиваемой на резание [4, карта 2, стр. 297]
Nт2 = 6,6 кВт
Расчетная мощность, затрачиваемая на резание
Np2 = Nт2 · KN · KN · KN1 · KN2 · KN3 · KN4 · KN5 · KN6 · KN7 · KN8 = 6,6 · 1,3 · 0,9 · 1,3 · 1,3 · 0,3 · 1,4 · 1,0 · 1,3 = 5,48 кВт, (40)
где N2т -табличная мощность резания, кВт.;
KN ,KN ,KN1,KN2, KN3, KN4,KN5, KN6, KN7, КN8- поправочные коэффициенты на мощность резания. [4, карта 2, стр.298-299]
Проверяем станок по мощности [10, прил. 1, стр. 422]
Nр2≤Nдв · η =7,5 · 0,8 =6 кВт. (41)
где Nдв-мощность двигателя, кВт;
η-КПД станка.
В связи с тем, что мощность резания меньше допустимой, то обработка
возможна.
1.10) Определение основного времени
Т0= Lрез/(Sп*nп)*i , (42)
где i – количество проходов.
Lрез. – длина рабочего хода инструмента, мм;
Lрез.= L+ lвр.+ lпер, (43)
где L – длина обрабатываемой поверхности, мм;
lвр – длина врезания, мм;
lпер. – длина перебега, мм;
Sn – подача по паспорту, мм/об;
nп – частота вращения шпинделя по паспорту, мин-1;
Т02=(23+17)/125=0,32мин.
Таблица 9 - Сводная таблица режимов резания
N0 операции. | Наименование и содержание операции. | Модель станка. | t, мм. | S, мм/об. | V, м/мин | n, мин-1 | Т0, мин |
015
| Токарно-винторезная с ЧПУ | 16К20Ф3С32 | |||||
1. Установить и закрепить деталь | |||||||
2. Подрезать торец в размер 23±0,26, точить поверхность до Ǿ 20-0,52, выдерживая размер 9±0,18, точить фаску 3*450 | 2 | 0,40 | 65,3 | 800 | 0,10 | ||
025 | Горизонтально-фрезерная | 6М83Г | |||||
1.Установить и закрепить деталь | |||||||
2. Фрезеровать 2 лыски, выдерживая размер 1=22±0.26 | 2 | 0,66 | 16,4 | 200 | 0,32 |
2.4.4 Расчет норм времени (на две операции по таблицам)
2.4.4.1 Расчёт норм времени наоперацию 015 Токарно-винторезная с ЧПУ
1) Определяем основное время
Т0=Т02=0,10мин.
2) Определяем машинно-вспомогательное время на выполнение автоматических вспомогательных ходов и технологические паузы
Тм.всп.хх= Lхх/(Sму)*i , (44)
где Lхх– длина пути автоматического вспомогательного хода , мм;
Sму – минутная подача ускоренного хода, мм/мин.; [3, приложение 46, лист 5,стр. 458]
i – число участков автоматических вспомогательных ходов.
Тм.всп.хх=50/4800+87/2400+62/4800+84/2400=0,01+0,04+0,01+0,04= 0,10 мин.
3) Определяем машинно-вспомогательное время на автоматическую смену инструмента
Т м.всп.и =0,02+0,03=0,05 мин.
4) Определяем машинно-вспомогательное время
Тм.всп=Тм.всп..хх+Т м.всп.и , (45)
где Тм.всп.хх - машинно-вспомогательное время на выполнение автоматических вспомогательных ходов и технологические паузы, мин.;
Тм.всп.и - машинно-вспомогательное время на автоматическую смену инструмента, мин. [3, приложение 46, лист 5,стр. 458]
Тм.всп=0,10+0,05=0,15 мин.
5) Определяем время цикла автоматической работы станка по программе
Тц.а=Тосн+Т м.всп, (46)
где Тосн - основное время автоматической работы станка по программе, мин.;
Тм.всп - машинно-вспомогательное время, мин.
Тц.а=0,10+0,15=0,25 мин.
6) Нормирование вспомогательного времени
Твсп=Туст+Тв.оп+Тизм, (47)
где Туст - время на установку детали, мин.; [3, карта 3,стр. 52]
Тв.оп - вспомогательное время, связанное с операцией, мин.; [3, карта 14, стр. 79]
Тизм - время на контрольные измерения, мин. [3, карта 15, стр. 80,84]
Туст=0,10мин.
Тв.оп=0,32+0,15+0,03=0,50 мин.
Тизм=0,08+0,07+0,06=0,21 мин.
Твсп=0,10+0,50+0,21=0,81 мин.
7) Определяем оперативное время
Топер=Тц.а +Твсп=0,25+0,81=1,06 мин., (48)
где Тосн - основное время, мин.;
Твсп - вспомогательное время, мин.
8) Определяем штучное время
Тшт=(Тц.а+Ктв*ТТвсп)*(1+(аобсл+аотл)/100), (49)
где Тц.а- время цикла автоматической работы станка по программе, мин.;
Ктв- коэффициент на вспомогательное время; [3, карта 1,стр.50]
(аобсл + аотл ) – время на обслуживание рабочего места, отдых и личные потребности. [3, карта 16, стр. 90]
Тшт= (0,25+0,81*0,81)*(1+8/100)=0,98 мин.
9) Нормирование подготовительно-заключительного времени [3, карта 21-22 стр.96-103]
Тпз=Тпз1+Тпз2+Тпз.пр., (50)
где Тпз1- подготовительно-заключительное время на организационную обработку, мин.;
Тпз2- подготовительно-заключительное время на наладку станка, приспособлений, инструмента, программных устройств, мин.;
Тпз.пр- подготовительно-заключительное время на пробную обработку детали, мин.
Тпз= 4+9+2+2+4+0,2+6,8+0,5+1,0+1,5+1,5+0,4+6+0,3+2,2=41,4 мин.
10) Определяем штучно-калькуляционное время
Тшт.к.=Тшт+Тпз/n, (51)
где Тшт- штучное время, мин.;
Тпз- подготовительно-заключительное время, мин.;
n- количество деталей в партии, штук.
Тшт.к=0,98+41,4/400=1,08 мин.
2.4.4.2 Расчёт норм времени наоперацию 025 Горизонтально-фрезерная
1) Определяем основное время
Тосн=Т02=0,32 мин.
2) Нормирование вспомогательного времени
Твсп=Туст=Тв.оп+Тизм, (52)
где Туст - время на установку детали, мин.; [3,карта 3, стр. 52]
Тв.оп - время связанное с операцией, мин.; [3,карта 20, стр. 227]
Тизм - время на контрольные измерения, мин. [3,карта 15, стр. 80,84]
Туст=0,09+0,8=0,89 мин.
Тв.оп=0,06+0,05+0,05=0,16 мин.
Тизм=0,11 мин.
Твсп=0,89+0,16+0,11=1,16 мин.
3) Определяем оперативное время.
Топер=Тосн+Твсп=0,32+1,16=1,48 мин., (53)
где Тосн - основное время, мин.;
Твсп - вспомогательное время, мин.
4) Определяем штучное время
Тшт=(Т0+Ктв· ТТвсп) · (1+(аобсл+аотл)/100)), (54)
где Т0-основное время, мин.
Ктв- коэффициент на вспомогательное время; [3, карта 1, стр.50]
(аобсл + аотл ) – время на обслуживание рабочего места, отдых и личные потребности. [3, карта 16, стр. 90]
Тшт= (0,32+0,81·1,16) · (1+7/100)=1,36 мин.
5) Нормирование подготовительно-заключительного времени
Позиция 1,2,3,4,5,13,16,25,34. [3, карта21-22, стр.96-103]
Тпз=4+10+2+2+0,8+0,15+0,3+0,2=21,45 мин.
6) Определяем штучно-калькуляционное время
Тшт.к.=Тшт+(Тпз/n) , (55)
где Тшт. - штучное время мин;
Тпз- подготовительно-заключительное время мин;
n- количество деталей в партии штук.
Тшт.к=1,36+21,45/400=1,41 мин.
Таблица 10 - Сводная таблица норм времени
№ и наименование операции | Т ![]() | Т ![]() | Т ![]() | Т ![]() | Т ![]() | Т ![]() | Т ![]() | Т ![]() | Т ![]() |
015 Токарно-винторезная с ЧПУ | 0,10 | 0,15 | 0,25 | 0,81 | 1,06 | 0,09 | 0,98 | 41,40 | 1,08 |
025 Горизонтально-фрезерная | 0,32 | - | - | 1,16 | 1,48 | 0,12 | 1,36 | 21,45 | 1,41 |
2.5 Разработка карты наладки для станков с ЧПУ
Расчетно-технологическая карта составляется технологом, содержит технологическое решение, принятое на предыдущих этапах технологической проработки и законченный проект обработки детали на станке с ЧПУ в виде графического изображения траектории движения инструмента со всеми необходимыми пояснениями и размерами.
Оформление расчетно-технологической карты производится в следующей последовательности:
1) Деталь вычерчивается в прямоугольной системе координат. Выбирается исходная точка обработки.
2) Намечается расположение зон крепления в соответствии с рекомендациями по выбору оснастки.
3) Наносится траектория движения центра инструмента в системе координат.
4) На траектории движения инструмента отмечаются и обозначаются
цифрами так называемые «опорные точки» траектории и ставятся стрелки, указывающие направление движения.
5) Указываются места контрольных точек, в которых предусматривается кратковременная остановка инструмента с целью проверки точности обработки программы рабочими органами станка.
6) Указываются режимы резания по участкам обработки.
7) Особо обозначаются опорные точки координату, которых можно определить измерением непосредственно на карте наладки.
8) В порядке оформления наносятся дополнительные данные: буквенная или цифровая последовательность обработки, параметры инструмента и так далее.
|
2.6 Разработка управляющей программы для станков с ЧПУ
Под ЧПУ оборудования понимают управление при помощи программ, заданных в алфавитно-числовом коде. При обработке на станках с ЧПУ инструмент перемещается по задаваемым в программе траекториям. При этом, например, для токарных станков программируется перемещение вершины резца, а для фрезерных – перемещение оси фрезы. Ось фрезы перемещается по эквидистанте, т. е. линии или поверхности, отстоящей от обрабатываемой поверхности на постоянную величину, равную радиусу фрезы. На обрабатываемом контуре выделяются опорные точки, которые представляют собой те точки контура, в которых он изменяет свой характер.
Управляющая программа для станка с ЧПУ - это совокупность элементарных команд исполнительным механизмам станка, записанных в
кодированном виде и в технологической последовательности обработки детали. Причем вид элементарных команд зависит от типа системы ЧПУ и кодового языка или языка программирования, принятого для данной системы.
По способу подготовки и ввода управляющей программы различают так называемые оперативные системы ЧПУ (в этом случае управляющую программу готовят и редактируют непосредственно на станке, в процессе обработки первой детали из партии или имитации ее обработки) и системы, для которых управляющая программа готовится независимо от места обработки детали. Причем независимая подготовка управляющей программы может выполняться либо с помощью средств вычислительной техники, входящих в состав систем ЧПУ данного станка, либо вне ее (вручную или с помощью системы автоматизации программирования).
Устройства, выдающие управляющие воздействия на исполнительные органы станка в соответствии с управляющей программой и информацией о состоянии управляемого объекта, называют устройствами числового программного управления УЧПУ.
Станок 16К20ФЗС32 оснащен УЧПУ модели 2Р-22. По виду обработки геометрической информации, устройство 2Р-22 является контурным (Ф3), следовательно, его можно применять для обработки на станке таких деталей, как в данной курсовой работе.
Устройство обеспечивает одновременное управление с круговой и линейной интерполяцией по двум координатным осям.
015 Токарно-винторезная с ЧПУ
Переход 1
Установить, закрепить и снять заготовку
Переход 2
Подрезать торец в размер 23±0,26, точить поверхность до Ǿ 20-0,52,
выдерживая размер 9±0,18, точить фаску 3*450
O; PROGRAMMA
N10 T1
N15 S600 M 03
N20 G0 G97 x24 z0
N25 G1 x 20 z0 F0.40 M08
N30 G41 x0 z0
N35 G41 x0 z0
N40 G1 X20 z-9
N45 x100 z100 М08
N50 M5
N55 M30
3 КОНСТРУКТОРСКАЯ ЧАСТЬ
3.1 Режущий инструмент
3.1.1 Описание конструкции
При разработке технологического процесса обработки заготовки выбор режущего инструмента, его вида, конструкции и размеров в значительной мере предопределяется методами обработки, свойствами обрабатываемого материала, требуемой точностью обработки качеством обработанной поверхности заготовки.
Режущий инструмент желательно применять стандартный как более дешевый, но можно разработать специальный комбинированный, фасонный инструмент, позволяющий совмещать обработку нескольких поверхностей, сокращая тем самым основное время. Правильный выбор режущей части инструмента имеет большое значение для повышения производительности и снижения себестоимости обработки. Выбор материала для режущего инструмента зависит от формы и размеров инструмента, материала обрабатываемой заготовки, режимов резания и типа производства.
3.1.2 Расчет исполнительных размеров
Для проектирования технологического процесса детали «Штуцер» я применяю резцы: проходной отогнутый, резец подрезной, резец отрезной, сверло центровочное, сверло спиральное, метчик, фрезы дисковые.
Рассчитать и сконструировать токарный проходной отогнутый резец с пластинкой из твердого сплава для операции 015 Токарно-винторезная с ЧПУ, переход 2 - подрезать торец в размер 23±0,26, точить поверхность до Ǿ 20-0,52,
выдерживая размер 9±0,18, точить фаску 3*450. Диаметр заготовки D = 26 мм, глубина резания t =2 мм, подача S = 0,40 мм/об, вылет резца из резцедержателя l = 60 мм, v=65,3 м/мин, главный угол в плане ϕ = 45°. Материал заготовки сталь 20 с σв = 650 МПа.
В качестве материала для корпуса резца выбираем углеродистую сталь 50 с = 650 МПа и допустимым напряжением на изгиб
= 200 МПа.
2) Определяем главную составляющую силу резания
(56)
где t - глубина резания, мм;
Sо - подача, мм/об;
С - коэффициент; [12,таб.17,стр.269]
х, у,n - показатели степени; [12,таб.17,стр.269]
К - поправочный коэффициент; [12,таб.18,стр.271]
V – скорость резания, м/мин.
СPz = 300; XPz = 1,0; YPz = 0,75; nPz = -0,15.
KPz = KмPz ·KφPz ·KγPz ·KrPz ·KλPz·Kh3Pz, (57)
где KмPz - поправочный коэффициент на характеристику механических
свойств обрабатываемой стали с σв=650 МПа
Кмpz = np; np=0,75 (58)
Кмpz = 0,75=1,22
KφPz - поправочные коэффициенты в зависимости от главного угла в плане φ= 450 ; KφPz = 1,00;
KλPz - поправочные коэффициенты в зависимости от величины
наклона главной режущей кромки λ = 0° ;KλPz = 1,00;
KrPz - поправочные коэффициенты в зависимости от величины радиуса закругления при вершине резца r = 1,0 мм; KrPz = 0,94;
KγPz - поправочные коэффициенты в зависимости от величины
переднего угла γ= 5°; KγPz = 1,05;
Kh3Pz - поправочные коэффициенты в зависимости от величины износа резца по задней поверхности h3=0 мм; Kh3Pz = 1,00.
KPz = 1,22·1,0·1,0·0,94·1,0·1,05 =1,149
Рz =10 ∙300∙ 2,01,0 ∙0,4 0,75∙ 65,3 -0,15 ·1,149 =1790 Н
3) При условии, что h = l,6b, ширина прямоугольного сечения корпуса резца
, (59)
где b - ширина прямоугольного сечения корпуса резца, мм;
Pz - тангенциальная сила резания, кгс;
1 - вылет резца, мм;
σ - допустимое напряжение на изгиб, кгс/мм
.
= 13 мм
Принимаем ближайшее сечение корпуса резца b = 16 мм. Руководствуясь приведенными соотношениями, получаем высоту резца h=1,6·b = 1,6·16 = 25,6 мм. Принимаем h = 25 мм, что соответствует стандартным размерам 25 х 16 по ГОСТ 18877 – 73.
4) Проверяем резец на прочность и жесткость корпуса.
Максимальная нагрузка, допускаемая прочностью резца
, (60)
где b - ширина прямоугольного сечения корпуса резца, мм ;
h - высота сечения резца, мм;
- допустимое напряжение на изгиб, кгс/мм;
1 - вылет резца, мм.
= 555,6 кгс
Максимальная нагрузка, допускаемая жесткостью резца
, (61)
где = 0,1×10
м - допускаемая стрела прогиба резца при черновом точении;
Е = 2×10 МПа = 2×10
Па = 20000 кгс/мм
- модуль упругости материала корпуса резца;
J - момент инерции прямоугольного сечения корпуса, мм ;
1 - вылет резца, мм.
J = , (62)
где b - ширина прямоугольного сечения корпуса резца, мм;
h - высота сечения резца, мм .
J = мм
= 578,7 кгс
Необходимо, чтобы сила Pz была меньше максимально допустимых нагрузок Pz доп и Pz жест или равна им.
P доп. ≥ P
≤ P
жёст. (63)
Резец обладает достаточной прочностью и жесткостью, так как
Pzдоп.> Pz < Pzжест (555,6 > 334,6 < 578,7)
5) Конструктивные размеры резца выбираем по ГОСТ 18877-73; общая длина резца L=140 мм; расстояние от вершины резца до боковой поверхности n = 10 мм; радиус кривизны лезвия rв = 0,4 мм; пластина из твердого сплава l = 16 мм, обозначение пластины 62252 по ГОСТ 25395 -90.
6) По ГОСТ 3882 - 74 выбираем материал режущей части резца - Т15К6.
7) Выбираем форму передней поверхности режущей части резца – криволинейная с отрицательной фаской № VIа по приложению ГОСТ 18877 -73.
8) Геометрические элементы лезвия резца выбираем по справочнику [15, с188-189] ϕ = 45°, ϒф= -5°, ϒ= 10°, α =12°, ϕ1 = 45°, λ=0 °, r=1,0 мм.
3.2 Контрольный инструмент
Измерительные средства, применяемые для контроля деталей, в зависимости от типа производства могут быть как стандартными, так и специальными. Повышение качества продукции машиностроения во многом зависит от правильной организации технического контроля и применения прогрессивных методов контроля.
В зависимости от контролируемых изделий контроль может быть сплошным или выборочным. Сплошной контроль исключает возможность попадания дефектной продукции потребителю, однако этот метод очень трудоемкий и при выпуске большого объема изделий является экономически нецелесообразным. Более рациональным методом в серийном и массовом производстве является выборочный контроль. В качестве измерительных контрольных инструментов могут быть использованы гладкие и резьбовые калибры, шлицевые и шпоночные калибры, шаблоны и т.д.
3.2.1 Описание конструкции
3.2.2 Расчет исполнительных размеров
Для контроля поверхности 22 h14(-0,52) на фрезерной операции я применяю
калибр-скобу.
1) Определить верхние и нижние отклонения вала: [9,таб.3.19,стр.38]
es = 0 мкм =0 мм;
ei = - 520 мкм =-0,52 мм.
2) Определить предельные размеры вала:
Найбольший предельный размер
dmax = d + es = 22 + 0 = 22 мм, (64)
где d – номинальный размер, мм;
es – верхнее отклонение, мм.
Найменьший предельный размер
dmin = d + ei= 22 + (-0,52) = 21,48 мм, (65)
где d – номинальный размер, мм;
ei – нижнее отклонение , мм.
3) Определить исполнительные размеры калибра-скобы [16,таб.1.7,стр.10]
Рабочий проходной размер
Р-ПР = , (66)
Рабочий проходной изношенный размер
Р-ПРи = d + y
, (67)
Рабочий непроходной размер
Р-НЕ = , (68)
где - отклонение середины поля допуска на изготовление проходного калибра, мкм;
- допустимый выход размера изношенного проходного калибра за
границу поля допуска изделия, мкм;
- допуск на изготовление калибров-скоб, мкм.
= 0,036 мм [16,таб.1.5,стр.9]
= 0 мм [16,таб.1.7,стр.10]
= 0,021 мм [16,таб.1.3,стр.8]
Р-ПР = мм
Р-ПРи = 22 + 0 = 22 мм
Р-НЕ = мм
4) Построить схему расположения полей допусков
Рисунок 3 - Схема расположения полей допусков калибра- скобы 22 h14(-0,52)
5 ОХРАНА ТРУДА И ОКРУЖАЮЩЕЙ СРЕДЫ. МЕРОПРИЯТИЯ ПО БЕЗОПАСНОСТИ ЖИЗНЕДЕЯТЕЛЬНОСТИ
Социальное значение охраны труда заключается в содействии росту эффективности общественного производства путём непрерывного совершенствования и улучшения условий труда, повышения его безопасности, снижения производственного травматизма и заболеваемости. Социальное значение охраны труда проявляется во влиянии на изменение трех основных показателей, характеризующих уровень развития общественного производства.
Рост производительности труда в результате увеличения фонда рабочего времени за счёт сокращения внутрисменных простоев путём предупреждения преждевременного утомления, снижения числа микротравм, уменьшения целодневных потерь рабочего времени по причинам временной нетрудоспособности из-за травматизма, профессиональной и общей заболеваемости.
Сохранение трудовых ресурсов и повышение профессиональной активности работающих за счёт улучшения состояния здоровья, увеличения средней продолжительности жизни, что сопровождается увеличением трудового стажа; возможности использования остаточной трудовой активности, опыта и профессиональных знаний пенсионеров на доступных для них работах.
Увеличение совокупного национального продукта за счёт улучшения указанных выше показателей.
Экономическое значение охраны труда определяется результатами изменения социальных показателей, которые определяются следующими экономическими факторами. Повышение производительности труда, а следовательно, и экономических результатов деятельности предприятия за счёт создания комфортных условий для трудовой деятельности, например, путем обеспечения оптимальных параметров микроклимата, освещение и световой
среды, учёта психофизиологических и эргономических особенностей труда, формирование оптимальных режимов труда и отдыха, проведения лечебно-профилактических мероприятий.
Увеличение фонда рабочего времени за счёт сокращения времени неявки на работу из-за травм и заболеваний.
Экономия расходов на льготы и компенсации за работу в неблагоприятных условиях труда. Такие разновидности льгот и компенсации, как повышенные тарифные ставки, льготные пенсии, лечебно-профилактическое питание, бесплатная выдача молока, также требуют больших денежных средств. Создание условий, соответствующих допустимым нормативным требованиям, позволяет частично или полностью сократить эти расходы.
Снижение затрат из-за текучести кадров по условиям труда. Тяжелый труд, неблагоприятные санитарно-гигиенические условия труда, монотонность работы и т.п. является немаловажной причиной увольнения работников по собственному желанию.
Текучесть рабочей силы наносит существенный экономический ущерб предприятию, т.к. требуются затраты денежных средств на процесс увольнения – найма, процесс обучения и стажировки вновь поступившего на работу. При этом до приобретения необходимого опыта и навыков производительности труда вновь поступившего на работу невелика.
Обеспечение комфортных условий для трудовой деятельности позволяет повысить качество и производительности труда, обеспечить хорошее самочувствие и наилучшие для сохранения здоровья параметры среды обитания и характеристики трудового процесса. Однако одним из наиболее значимых для обеспечения комфортных условий на рабочем месте являются климатические условия, освещенность и световая среда. В обеспечении безопасности труда большое значение имеет организация рабочего места. При организации рабочего места необходимо обеспечить:
– удобную конструкцию и правильную расстановку верстаков – необходим свободный доступ к рабочим местам, а зона вокруг рабочего места должна быть свободной на расстоянии не менее 1 м;
– рациональную систему расположения на рабочем месте инструмента, приспособлений и вспомогательных материалов.
Мероприятия по защите воздуха от загрязнений, загазованности и заражения:
– усовершенствование технологических процессов в целях уменьшения выбросов в атмосферу дыма, пыли, газов, радиоактивных веществ;
– строительство очистных сооружений;
– улучшение состава топлива и аппаратов для его снижения;
– рациональное размещение источников выброса в атмосферу и расширения площадей зелёных насаждений.
Мероприятия по защите воды включают:
– использование замкнутого цикла водоснабжения на предприятиях;
– комплексную очистку сточных вод.
ЗАКЛЮЧЕНИЕ
В процессе курсового проекта мной была проделана значительная исследовательская и учебно-методическая работа по совершенствованию технологического процесса обработки детали «Штуцер».
Рассмотрел два вида изготовления заготовок: прокат и штамповка. По результатам расчетов получил, что заготовка-штамповка более экономична по
расходу материала и коэффициенту использования материала, но дороже по стоимости. Экономический эффект от выбранного вида изготовления заготовки составляет 421000 рублей при годовой программе выпуска детали 20000 штук.
При разработке нового варианта технологического процесса я использовал концентрацию операций с целью повышения загрузки оборудования и произвел замену станков на более производительные, что позволило уменьшить затраты на заработную плату производительных рабочих, а это в свою очередь снизило себестоимость изготовления детали.
При разработке операций, выполняющихся на токарно-винторезном станке с ЧПУ 16К20Ф3С32 и горизонтально-фрезерном 6М83Г мной вычерчены карты наладки, наладка инструментальная, выполнен расчёт режущего инструмента - резец проходной отогнутый, выполнен расчёт контрольного инструмента – калибр скоба 22h14(-0,52), а также разработан комплект документов на обработку детали.
Список литературы
1 Добрыднев И.С. Курсовое проектирование по предмету «Технология машиностроения». М. Машиностроение. 1985.
2 Босинзон М.А. Современные системы ЧПУ и их эксплуатация. М. Академия. 2006.
3 Общемашиностроительные нормативы времени и режимов резания для нормирования работ, выполняемых на универсальных и многоцелевых станках с ЧПУ.В 2-х частях. Т1,Т.2. М. Экономика 1990
4 Локтев А.Д. Общемашиностроительные нормативы режимов резания. Справочник. В 2-х частях. Т1,Т.2. Машиностроение. 1991
5 Нефёдов Н.А. Дипломное проектирование в машиностроительных техникумах. – М.: Высшая школа, 1986.
6 Зубченко А.С. Марочник сталей и сплавов. 2-е издание. М. Машиностроение. 2003.
7 ГОСТ 7505-89. Поковки стальные штампованные. М. Машиностроение. 1990.
8 ГОСТ 14.209–85.
9 Стандарт СЭВ 144–75 Единая система допусков и посадок СЭВ. Поля допусков и рекомендуемые посадки.
10 Нефедов Н.А., Осипов К.А. Сборник задач и примеров по резанию металлов и режущему инструменту. М. Машиностроение. 1990.
11 Панов А.А. Обработка металлов резанием. Справочник технолога. М. Машиностроение. 1988.
12 Под редакцией Косиловой А.Г., Мещерякова Р.К. Справочник технолога-машиностроителя. В 2-х частях. Т1, 2. М. Машиностроение. 1985.
13 Трудовой кодекс Российской Федерации от 10.10.2008.
14 Девисилов В.А. Охрана труда, Москва, «Форум-Инфра-М» 2013.
15 Адаскин А.М. Современный режущий инструмент. Учебное пособие для СПО. — М. : Издательский центр «Академия», 2013.
16 СТСЭВ 157-75 Калибры гладкие для размеров до 500 мм.
17 Гжиров Р.И. Краткий справочник конструктора, Ленинград: Машиностроение, 2009.
18 Ильянков А.И., Марсов Н.Ю. Метрология, стандартизация и сертификация в машиностроении. Учебное пособие.Практикум. — М. : Издательский центр «Академия», 2014.
19 ГОСТ 7829-70 Поковки из углеродистой и легированной стали, изготовляемые ковкой на молотах.
Дата добавления: 2018-02-28; просмотров: 382; Мы поможем в написании вашей работы! |
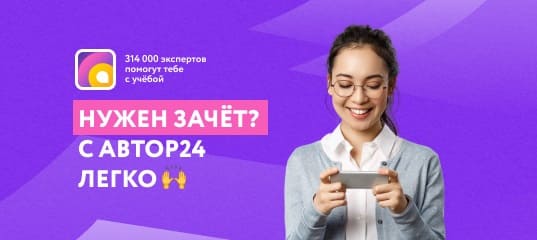
Мы поможем в написании ваших работ!