ЦИНКОВОГО КОНЦЕНТРАТА В КИПЯЩЕМ СЛОЕ
2.1. ОПИСАНИЕ ТЕХНОЛОГИЧЕСКОГО ПРОЦЕССА
Для интенсификации многих технологических процессов широко применяют метод так называемого кипящего слоя. Кипящий слой получают в печах продуванием воздуха снизу через слой мелкого материала. При этом зерна материала находятся в постоянном движении в потоке воздуха, слой материала как бы кипит. Кипящий слой обладает основными свойствами жидкости: текучестью, способностью принимать форму сосуда, в котором он находится. Крупным преимуществом данного состояния материала является резкое увеличение поверхности соприкосновения материала с воздухом, что и приводит к интенсификации технологического процесса.
В цветной металлургии печи кипящего слоя применяют для обжига медных, никелевых, молибденитовых и цинковых концентратов, для сушки различных материалов, для возгонки сурьмы и т.д. Рассмотрим основные принципиальные вопросы автоматизации процесса обжига цинкового концентрата.
На рис. 2.1 представлена схема цепи аппаратов процесса обжига цинковых концентратов в кипящем слое. Цинковый концентрат подвергается обжигу для перевода сульфида цинка в окись и частично в сернокислый цинк.
Полученный в печи огарок выщелачивается затем серной кислотой, а газы с содержанием SO2 до 8–10 % используют в сернокислотном производстве. При окислении сульфидов в печи выделяется значительно больше тепла, чем необходимо для поддержания требуемой температуры (930–950 оС), поэтому часть тепла приходится выводить из слоя. Для этого могут быть применены кессоны, змеевки с водой, впрыск воды в печь.
|
|
Из расходного бункера I концентрат подается ленточным питателем II в форкамеру печи III. Форкамера (подготовительная камера) служит для образования кипящего слоя, для предварительного подогрева материала. Из форкамеры материал перетекает в собственно печь IV, где и происходит основной процесс обжига. В бетонный под печи вмонтированы воздушные сопла, создающие скорость воздушной струи до 10–12 м/с. Воздух к соплам подводится от воздуходувки VII через распределительные воздушные коробки. Для более равномерного распределения дутья по участкам пода воздухораспределительные коробки секционированы. При среднем размере зерен материала около 2–3 мм давление воздуха в распределительной коробке составляет 10–20 кПа. На 1 кг концентрата расходуется примерно 2 м3 воздуха. Высота кипящего слоя в этих условиях достигает 1,0–1,3 м. В нормальном режиме топливом для процесса служит сам концентрат. Материал постепенно перемещается в кипящем слое по направлению от форкамеры к сливному порогу V. В процессе движения сульфиды окисляются и готовый огарок ссыпается через сливной порог в смывной желоб VI. Струя отработанного электролита, содержащего кислоту H2SO4, смывает огарок по желобу в цех выщелачивания.
|
|
Печь кипящего слоя является типичной беспламенной печью. Отходящие газы в печи не охлаждаются и имеют на выходе температуру до 850–900 оС. Для нормальной работы всех последующих устройств необходимо снизить температуру до 450–550 оС. Первая пылеосадительная камера VIII является одновременно и холодильником. Наличие мелких фракций в концентрате обуславливает унос значительного количества огарка с уходящими газами. Иногда до половины всего материала уносится в газоходы. Для улавливания ценной пыли из газов устанавливается мощная пылеосадительная система. На схеме показана часть этой системы: циклон IX и электрофильтр X. Пыль из бункеров пылеочистки собирается шнеком XI и подается в смывной желоб, а газ поступает на сернокислотное производство. Разрежение перед эксгаустером XII составляет 1200–1300 Па. Температура газа за батарейным циклоном не превышает 300–350 оС. Для отвода избыточного тепла от кипящего слоя в рассматриваемой схеме предусмотрены кессоны с водяным охлаждением.
|
|
2.2. АНАЛИЗ ПРОЦЕССА ОБЖИГА В ПЕЧИ КС КАК ОБЪЕКТА АВТОМАТИЗАЦИИ
Основным параметром процесса обжига является температура слоя. Повышение температуры может вызвать частичное расплавление материала и спекание его в крупные куски, из-за чего нарушается кипящий слой. Снижение температуры ведет к неполному окислению сульфидов, т.е. к уменьшению производительности печи. Поскольку топливом для печи служит концентрат, то температура слоя зависит и от его качества. Режим отъема тепла от слоя также отражается на температуре в печи. Таким образом, поддержание постоянной температуры слоя может быть осуществлено воздействием либо на загрузку материала, либо на режим отъема тепла. Первый метод чаще применяют на отечественных предприятиях: он прост, надежен и хорошо освоен. Тем не менее, система автоматического регулирования температуры слоя управлением загрузкой концентрата имеет принципиальные недостатки. Объект регулирования – обжиговая печь – обладает большой постоянной времени, что вызывает значительное запаздывание в системе регулирования. Кроме того, по данным технологических испытаний, при отсутствии серьезных возмущений в системе регулирования, поддержание температуры слоя в пределах ±10 оС вызывает колебания расхода материала до ±3 %. Такая неравномерность хода печи, т.е. неравномерность ее производительности и концентрации сернистого газа за печью, неблагоприятно отражается на последующих процессах.
|
|
Для того чтобы уменьшить колебания производительности печи, вызываемые системой регулирования температуры слоя, целесообразно использовать схему стабилизации подачи материала с коррекцией по температуре слоя. Такая двухкаскадная схема регулирования применяется при наличии значительного запаздывания в линии питатель – загрузочная воронка печи.
Охлаждение слоя с помощью кессонов не позволяет решить вопрос автоматического регулирования температуры воздействием на количество отбираемого тепла. Изменение подачи воды в кессоны быстро сказывается лишь на температуре периферийных слоев материала в печи. А датчик системы регулирования устанавливают обычно почти в центре печи.
Проведенные исследования показали, что для высокотемпературных процессов при температуре слоя выше 600 оС более эффективным оказывается регулирование температуры слоя загрузкой, а не отъемом тепла. При высоких температурах в печи оптимальный диапазон регулирования требует отбора слишком большого количества тепла, что по технологическим нормам недопустимо.
Контроль температуры в нескольких точках кипящего слоя необходим как для настройки системы регулирования подачи материала, так и для правильного ведения технологического процесса обжига. Четыре – шесть термопар устанавливают перпендикулярно стенкам печи так, что рабочие концы их размещались в разных точках слоя.
Воздух, поступающий в печь, необходим для образования кипящего слоя и для окисления сульфидов. Технологические расчеты показывают, что для образования слоя обычно требуется несколько больше воздуха, чем для окисления сульфидов, т.е. для горения материала в печи. Следовательно, система автоматического регулирования подачи воздуха должна обеспечить необходимую высоту кипящего слоя. Высота слоя, видимо, зависит от давления воздуха в распределительной коробке печи, от количества и гранулометрического состава материала в рабочей камере печи. Последний параметр не поддается измерению, а количество материала в печи можно определить по величине загрузки. Считая, что фракционный состав материала остается примерно постоянным, можно выбрать два регулирующих импульса: расход концентрата и давление воздуха перед соплами. Оба варианта нашли применение на предприятиях.
Известны схемы автоматического регулирования подачи воздуха по расходу концентрата в печь, по соотношению расходов концентрат – воздух, по давлению воздуха в распределительной коробке печи, по схеме стабилизации. Последние две схемы используют несколько чаще первых двух, так как они позволяют лучше стабилизировать высоту слоя. От высоты кипящего слоя в печи в значительной мере зависит безаварийность работы установки. Небольшое повышение слоя, связанное с увеличением расхода воздуха, приводит к выносу весьма значительной части материала в газовый тракт, к забиванию газоходов и пылеосадительных устройств. Снижение слоя может вызвать уменьшение производительности печи и даже аварийную остановку ее из-за забивания воздушных сопел. Поэтому колебания давления воздуха, резко отражающиеся на высоте слоя, недопустимы.
В нашем случае целесообразно применять стабилизацию подачи воздуха. Коррекция по импульсу от давления в воздухораспределительной коробке вводится в регулятор постоянства расхода воздуха. Построение двухкаскадной системы регулирования позволяет учесть и расход, и давление воздуха.
Тяговый режим печи связан с состоянием кипящего слоя, так как унос мелких фракций из слоя зависит от разрежения под сводом печи. Нулевая линия, на которой давление равно атмосферному, располагается обычно на 0,5–1,0 м выше уровня слоя. Перемещение нулевой линии вверх, связанное с уменьшением разрежения под сводом, может вызвать выбивание газов из неплотностей печи. Снижение нулевой линии, соответствующее увеличению разрежения в печи, приводит к повышенному уносу мелкого материала. Работа пылеосадительных камер и циклонов тоже зависит от тягового режима. Все это обуславливает необходимость автоматического регулирования разрежения в печи. Нормально разрежение под сводом составляет 80–120 Па.
Контроль разрежений по газовому тракту необходим не только для настройки системы автоматического регулирования тяги, но и для проверки состояния газоходов и пылеуловителей. Увеличение перепада разрежений на любом участке газоходной системы свидетельствует о забивании его, а уменьшение перепада может означать появление неплотностей на данном участке. Разрежение желательно контролировать в четырех точках: за печью, за пылевой камерой, за циклоном и перед эксгаустером.
Процентное содержание SO2 в отходящих газах – важный показатель работы серно-кислотной установки. Наиболее полное выжигание серы повышает качество огарка и положительно отражается на экономических показателях серно-кислотного производства.
Температура отходящих газов при продвижении их по газовому тракту снижается с 850–900 оС в печи до 250–300 оС перед эксгаустером. Контроль температур по газовому тракту позволяет следить за работой холодильника, наличием подсосов в газоходах и т.д. Температура должна контролироваться в четырех точках: в печи, перед холодильником, за ним и перед эксгаустером.
Хотя водоохлажадемые кессоны печи и не используют для автоматического регулирования температуры слоя, непрерывный контроль работы их необходим. Нормально температура воды на выходе из кессонов составляет 80–85 оС. Повышение этой температуры может вызвать парообразование внутри кессона, а образование паровой подушки на внутренней стенке приводит к прожогу его. Таким образом, аварийный выход кессона из строя является следствием недостаточной подачи воды. Снижение температуры воды на выходе из кессона означает, что подача воды в него слишком велика, а это неэкономично. Расход воды в кессоны, давление воды на входе и на выходе из них также являются показателями режима работы системы охлаждения. Прожог одного из кессонов может вызвать увеличение расхода воды в систему и снижение давления во входной линии по сравнению с обычным давлением, равным 0,1–0,15 МПа, поэтому необходим контроль и стабилизация расхода воды. Забивание одной из линий подвода воды вызывает повышение давления перед кессонами.
Печь кипящего слоя имеет обычно несколько кессонов, а все описанные ранее устройства установлены на общей линии. Между тем неправильный режим работы только одного из кессонов не всегда заметно отражается на параметрах общей магистрали. Ввиду этого установка измерителей температуры и давления на каждом кессоне резко повысила бы надежность работы системы охлаждения. Такая сложная схема контроля требует слишком больших затрат. Кроме контроля основных параметров режима работы кессонов, иногда осуществляется автоматическое регулирование подачи воды в них по температуре отходящей воды. Однако установка даже простых регуляторов прямого действия на каждом кессоне экономически нецелесообразна, а один регулятор на общей линии не обеспечивает достаточно надежного и устойчивого регулирования.
2.3. ВЫБОР СИСТЕМ АВТОМАТИЧЕСКОГО КОНТРОЛЯ
И РЕГУЛИРОВАНИЯ
Проведенный анализ особенностей процесса обжига цинкового концентрата в печи кипящего слоя показывает, что для обеспечения нормальных условий протекания процесса, а также исходя из особенностей динамики процесса, и кроме того, учитывая наличие или отсутствие специальной аппаратуры, предназначенной для автоматического контроля различных технологических параметров, целесообразно в проекте автоматизации предусмотреть следующие системы автоматического контроля и регулирования технологических параметров, значения которых характеризуют печь обжига цинкового сульфидного концентрата как объекта автоматизации:
1. Системы автоматического регулирования
– температуры кипящего слоя в печи;
– расхода воздуха в распределительную коробку печи;
– разрежения под сводом печи.
2. Системы автоматического контроля
– температуры в различных точках кипящего слоя;
– разрежения по всей длине газоходного тракта;
– расхода воды на кессоны;
– содержания SO2 в отходящих газах;
– давления воздуха в распределительной коробке печи.
Номинальные значения выходных параметров данного объекта автоматизации приводятся в табл. 2.1.
В соответствии с требованиями, определяющими оптимальные условия протекания процесса обжига цинкового сульфидного концентрата в печи кипящего слоя, разработана функциональная схема автоматизации, представленная на рис. 2.2.
Таблица 2.1
№№ п/п | Наименование параметра | Единица измерения | Номинальная величина |
1. | Температура кипящего слоя | оС | 930–950 |
2. | Расход воздуха в печь | м3/ч | Зависит от производительности печи |
3. | Разрежение под сводом печи | Па | 80–120 |
4. | Температура в различных точках кипящего слоя | оС | 930–950 |
5. | Разрежение по всей длине газоходного тракта (от печи до эксгаустера) | Па | от 80–120 до 1200–1300 |
6. | Температура по всей длине газоходного тракта ( от печи до эксгаустера) | оС | от 850–900 до 250–300 |
7. | Расход воды на кессоны | м3/ч | Зависит от производительности печи |
8. | Температура воды на выходе из кессонов | оС | 80–85 |
9. | Содержание SO2 в отходящих газах | % | 8–10 |
10. | Давление воздуха в распределительной коробке печи | кПа | 10–20 |
Схема включает все вышеперечисленные системы автоматического контроля и регулирования и построена главным образом по принципу стабилизации основных параметров процесса с введением коррекций в отдельных случаях. Как известно, это не наилучший вариант схем автоматизации технологических процессов. Сложность процесса обжига в кипящем слое и взаимосвязанность подавляющего большинства параметров его заставляют создавать схемы комплексного регулирования. В настоящее время для печей кипящего слоя разрабатывают специальные оптимизаторы, которые получив информацию о параметрах объекта, будут вырабатывать оптимальные задания регуляторам загрузки, подачи воздуха, тяги, впрыска воды и т.д.
2.4. ОПИСАНИЕ СИСТЕМ АВТОМАТИЧЕСКОГО КОНТРОЛЯ
И РЕГУЛИРОВАНИЯ
2.4.1. Система автоматического регулирования
температуры кипящего слоя в печи
Расход материала измеряют ленточным весоизмерителем (поз. 1а) и вторичным прибором (поз. 1б), а температуру в слое – термопарой (поз. 1в) и потенциометром (поз. 1г). С показывающих и самопишущих приборов 1б и 1г электрические сигналы подаются на автоматический регулятор (поз. 1д), который через блок ручного управления (поз. 1е) и пусковое устройство (поз. 1ж) осуществляет изменение скорости вращения электродвигателя (поз. 1 з), приводящее к изменению расхода шихты в печь.
Таким образом, в системе осуществляется стабилизация расхода шихты в печь с коррекцией по температуре в слое.
2.4.2. Система автоматического регулирования расхода воздуха в распределительную коробку печи
Расход воздуха измеряют комплектом приборов, включающим сужающее устройство (поз. 2а), дифманометр (поз. 2б) и вторичный прибор (поз. 2в), а давление воздуха в распределительной коробке печи – бесшкальным манометром (поз. 2г) и вторичным прибором (поз. 2д). С вторичных приборов сигналы подаются на автоматический регулятор (поз. 2е), а затем через блок ручного управления (поз. 2ж) и магнитный пускатель (поз. 2з) – на исполнительный механизм (поз. 2и), перемещающий регулирующий орган (поз. 2к), который изменяет расход воздуха в печь.
В этой системе предусмотрена стабилизация подачи воздуха с коррекцией по импульсу давления в воздухораспределительной коробке. Построение каскадной системы регулирования в данном случае связано с желанием учесть и расход, и давление воздуха.
2.4.3. Система автоматического регулирования разрежения
под сводом печи
Импульс по разрежению отбирается в центре свода печи, если газы из печи отводятся сверху, и в точке свода, смещенной в сторону газохода, при боковом отводе газов. В комплект системы регулирования входят: бесшкальный дифманометр (поз. 3а), вторичный прибор (поз. 3б), автоматический регулятор (поз. 3в), блок ручного управления (поз. 3г), магнитный пускатель (поз. 3д) и исполнительный механизм (поз. 3е). Исполнительный механизм по сигналу с регулятора поворачивает заслонку (поз. 3ж) на газопроводе перед эксгаустером, изменяя величину тяги.
2.4.4. Система автоматического контроля в различных
точках кипящего слоя
Несколько термопар (поз 4а) устанавливают перпендикулярно стенкам печи так, что рабочие концы их были в разных точках слоя. В комплекте с термопарами работает многоточечный потенциометр (поз. 4б).
2.4.5. Система автоматического контроля разрежения
по длине газоходного тракта
Отборные устройства для контроля разрежения устанавливают в четырех точках: за печью, за стояком, за циклоном и перед эксгаустером. Наглядное представление о тяговом режиме печи дает четырехточечный вторичный прибор (поз. 5б), на которой поступают унифицированные сигналы с манометров – преобразователей (поз. 5а).
2.4.6. Система автоматического контроля температуры
по всей длине газоходного тракта
Температура контролируется в трех точках (после стояка, после циклона и перед эксгаустером) с помощью термопар (поз. 6а) и многоточечного потенциометра (поз. 6б).
2.4.7. Система автоматического контроля расхода воды
на кессоны
Контроль осуществляется комплектом, включающим сужающее устройство (поз. 7а), дифманометр (поз. 7б) и вторичный показывающий и самопишущий прибор (поз. 7в).
2.4.8. Система автоматического контроля температуры воды на выходе из кессонов
Контроль температуры осуществляется с помощью термометра сопротивления (поз. 8а) и электронного моста (поз. 8б).
2.4.9. Система автоматического контроля содержания SO2
в отходящих газах
Контроль концентрации сернистого газа осуществляется с помощью газоанализатора (поз. 9а, 9б) со вторичным прибором (поз. 9в).
Дата добавления: 2018-02-28; просмотров: 1343; Мы поможем в написании вашей работы! |
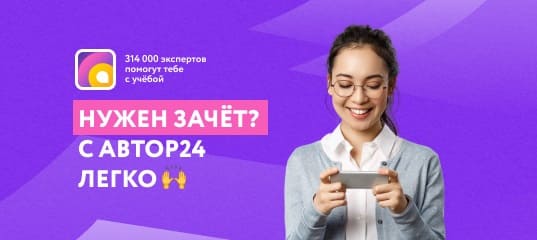
Мы поможем в написании ваших работ!