Переработка газов ПГУ на химическую продукцию
Министерство образования и науки Российской Федерации
Федеральное государственное бюджетное образовательное учреждение высшего образования
«СИБИРСКИЙ ГОСУДАРСТВЕННЫЙ ИНДУСТРИАЛЬНЫЙ УНИВЕРСИТЕТ»
Реферат
По дисциплине: «Физико-Химическая Геотехнология»
Тема: Основные технологические схемы ПГУ.
Подготовил:
Студент гр. ЗГД – 12
Шифр: 12241
Колохматов А.И.
Принял:
Ст. преподаватель
Чижик Ю.И.
Новокузнецк 2018г.
Содержание
Введение......................................................................................................3
1.1. Основные понятия и представления..................................................4
1.2.Технология ПГУ...................................................................................6
1.3. Переработка газов ПГУ на химическую продукцию.....................11
Заключение................................................................................................14
|
|
Список литературы...................................................................................15
Введение
Быстрое развитие производственных сил, связана с большим расходом топлива и углеводородного сырья, неравномерность и сложность добычи горючих ископаемых сопровождается ростом цен и увеличение транспортных расходов и материальных затрат.
В химической индустрии наиболее неотложной задачей является перевод угольной базы производства связанного азота, синтетического метанола. Этот перевод сулит уменьшать крупнотонажность химических предприятий от сезонных колебаний в снабжении природным газом, освободить от применения значительных количеств жароупорных легированных сталей.
Переход на твердое топливо несёт и ряд негативных явлений для промышленного производства. Анализ, подготовка производства и преодоление трудностей является задачей науки.
Работа с твердым топливом в аппаратурно-техническом плане сложнее, чем с жидкими и газообразными углеводородами. Добыча и транспортировка твердого топлива, его сушке, измельчение, подача в газогенератор, удаление золы, очистка технологического газа все это требует помощи механических и технологических приспособлений. Кроме того, все технологические операции требуют энергетических затрат.
|
|
Таким образом, переход на новую сырьевую базу связан: с ростом удельных капитальных затрат, уменьшение КПД процесса, увеличение расхода рабочей силы на тонну конечного продукта. Но с какими бы затратами не был связан этот переход, его нельзя рассматривать как альтернатива, это неизбежная необходимость. И чем раньше будет развита подготовка к этому переходу, тем он пройдет более безболезненно. Наиболее важным звеном при решении задачи- это проблема газификации твердого топлива- получение генераторного газа.
Основные понятия и представления
Существует технология, стоящая особняком к теме добычи метана из угольных пластов — подземная газификация угля (ПГУ), не являющаяся технологией добычи метана. ПГУ — это способ разработки угольных месторождений, основанный на превращении угля в горючий газ в недрах на месте залегания, где метаноносность каменного угля, являющаяся усложняющим фактором при шахтной добыче, используется для повышений энергетического КПД процесса ПГУ. В упрощенном виде процесс ПГУ представляет собой горящий под землей угольный пласт, продуктом горения которого является газ, в котором содержание метана составляет лишь несколько процентов, а основными горючими компонентами являются окись углерода (CO) и водород (H2). Газ подземной газификации углей обладает всеми преимуществами газообразного топлива. Несмотря на то что теплотворность газа ПГУ примерно восемь раз ниже теплотворности природного газа, по условиям сжигания данный газ ненамного отличается от природного.
|
|
Подземная газификация представляет собой термохимический процесс превращения угля в горючие газы, пригодные для энергетических или химико-технологических целей. Идея подземной газификации угля принадлежит Д.И. Менделееву, который еще в 1888 г. писал: «Настанет, вероятно, со временем даже такая эпоха, что угля из земли вынимать не будут, и там, в земле, его сумеют превращать в горючие газы и их по трубам будут распределять на далекие расстояния». Им же сформулирован основной принцип ПГУ: «Пробурив к пласту несколько отверстий, одно из них должно назначать для введения — даже вдувания воздуха, другое для выхода, даже вытягивания (например, инжектором) горючих газов, которые затем легко провести даже на далекие расстояния к печам». Известный английский химик В. Рамсей предложил вести процесс газификации угля через одиночные обособленные скважины (рис.1).
|
|
В 1934 г. сотрудники Донецкого углехимического института предложили и на Горловской станции осуществили новый способ ПГУ. По наклонному пласту параллельно прошли две выработки, которые в нижней части сбиты горизонтальной выработкой, а в верхней соединены скважинами с поверхностью. В одну скважину подавалось дутье, из другой отводился горючий газ. Этот поточный метод ПГУ явился основой для всех последних технологий ПГУ в различных условиях залегания угольных пластов (рис.2).
Под термином «подземная газификация угля» понимают процесс получения из угля газа, а под термином «подземный газогенератор» — часть угольного пласта, в которой ведется газификация. Важнейшими элементами подземного газогенератора являются каналы газификации, образуемые по простиранию или по падению пласта. В них совершается взаимодействие кислорода, подаваемого в каналы, с твердой фазой (с углем и различными химическими элементами окружающих пород). Войдя в канал газификации, кислород подогревается. Двигаясь далее, он вступает в реакцию с углеродом угля, образуя окись и двуокись углерода. Образовавшаяся двуокись углерода, а также водяной пар, поступающий из угольного пласта и окружающих пород, движутся далее по угольному каналу, омывают его раскаленную поверхность и частично восстанавливаются углеродом (соответственно до окиси углерода и водорода). При дальнейшем движении по каналу горючие газы нагревают уголь, в результате чего происходит термическое разложение его горючей массы с выделением летучих, поступающих в газовый поток. Далее эта смесь газов, имеющая еще достаточно высокую температуру, омывает остальную поверхность канала, производя подсушку угля. Таким образом, процесс газообразования в канале газификации можно условно разбить на четыре зоны: окисления (или горения), восстановления, термического разложения угля и сушки. Общий баланс энергии реакций автотермичен.
Рисунок 1 – Схема подземной газификации угля (по В. Рамсею)
1 — обсадная колонна; 2 — дутьевая колонна; 3 — цементация; 4 — кровля; 5 — уголь; 6 — газ; 7 — дутье; 8 — выгазованное пространство
Рисунок 2 – Принципиальная схема бесшахтного газогенератора на наклонных угольных пластах:
1—вертикальные дутьевые скважины; 2—водоотливные скважины; 3—наклонные дутьевые скважины; 4 — наклонные газоотводящие скважины
Технология ПГУ
Создание каналов в угольном пласте. Процесс прожига в угольном пласте канала очагом горения, который перемещается навстречу дутьевому потоку или по его направлению, называется фильтрационной сбойкой скважин. В первом случае сбойку называют противоточной, во втором—прямоточной. Противоточная фильтрационная сбойка осуществляется следующим образом. Бурится и обсаживается ряд скважин. Необсаженной остается только нижняя часть. Затрубное пространство тампонируется. Затем приступают к отжатию влаги из пласта. Для этого нагнетают дутье в две, три или во все скважины (в зависимости от наличия дутья и принятого порядка сбойки). После предварительной сушки прекращают нагнетание дутья в одну из скважин, называемую розжиговой, соединяют с атмосферой и зажигают угольный пласт. Развитие очага горения обеспечивается сравнительно непродолжительным нагнетанием дутья в розжиговую скважину и ее периодической разгрузкой (продукты горения выбрасываются в атмосферу). После достижения устойчивого горения угля из розжиговой скважины в течение всей сбойки отводится газ. Дальнейшее горение угля поддерживается за счет кислорода дутья, нагнетаемого в соседние скважины и фильтрующегося в направлении к очагу горения. Завершающий этап сбойки для всех углей характеризуется резким падением давления, бурным выделением газов и повышением их качества. С этого момента канал считается готовым для ведения процесса газификации. Фильтрационная сбойка на новых участках может вестись в одном, двух, трех или четырех направлениях одновременно. При наличии вблизи сбиваемой скважины выгазованного пространства сбойку ведут непосредственно на него и сбоечные газы смешиваются с газами газификации. На скорость сбойки и удельный расход дутья влияют зольность угля, его пористость и проницаемость, характер почвы и кровли пласта, интенсивность нагнетания дутья, мощность пласта и его обводненность, расстояние между скважинами, состав дутья и др. Фильтрационная сбойка от дутьевой скважины, расположенной между сбиваемой и газоотводящей скважинами и предназначенной для нагнетания дутья на газификацию, выгоднее, чем от газоотводящей.
При прямоточной сбойке угольный пласт зажигается в забое сбиваемой скважины, в которую нагнетается дутье. Образующиеся при этом газы распространяются по порам и трещинам пласта. Прямоточная сбойка применяется в редких случаях (в основном при первичном розжиге), так как она сопровождается уменьшением проницаемости пласта из-за конденсации паров воды и смолы в порах и кливажных трещинах.
Гидравлический разрыв угольного пласта. Одним и основных недостатков процесса гидроразрыва угольного пласта является отсутствие четкой его направленности. Чтобы обеспечить направленность, прибегают к одновременному нагнетанию воды и разгрузке скважины, на которую необходимо осуществить гидроразрыв. Эксплуатационные затраты при гидроразрыве каменноугольного пласта и последующей огневой проработке щелей гидроразрыва в 3—4 раза ниже затрат при воздушной фильтрационной сбойке.
Направленное бурение скважин особенно широкое распространение получило на крутых угольных пластах, где каналы газификации обычно располагаются по падению пласта. Но имеется также и опыт бурения горизонтальных скважин по простиранию угольного пласта. Буровые каналы (как и щели гидроразрыва) требуют последующей огневой проработки, которая осуществляется либо путем розжига пласта в точке входа скважины в уголь, либо путем подтягивания очага горения со стороны выгазованного пространства.
Электросбойка (процесс создания канала в угольном пласте в результате теплового воздействия электрического тока на уголь) осуществляется с помощью опущенных в скважину электродов, концы которых входят непосредственно в угольный пласт. При включении электродов в цепь в угольном пласте происходит выделение паров воды и продуктов сухой перегонки угля с образованием кокса. В итоге уголь становится хорошим проводником тока, что обеспечивает тепловой пробой пласта. Электросбойка получила применение на Шатской и Ангренской станциях подземной газификации. Важное ее преимущество—высокая направленность.
Конструкция подземных газогенераторов. Различают наземную и подземную части газогенераторов. К наземной части относятся головки дутьевых и газоотводящих скважин, трубопроводы для подвода дутья к скважинам, газопроводы, аппараты для очистки и охлаждения газа, обслуживающие газогенератор. Сюда же входят приборы для контроля и управления работой отдельных скважин и газогенератора в целом. Подземная часть газогенераторов включает дутьевые и газоотводящие скважины, каналы газификации, а также водоотливные, дренажные и наблюдательные скважины (если они требуются).
Все подземные газогенераторы можно подразделить на газогенераторы с изолированными каналами и каналами, объединенными посредством единого канала розжига. На рисунке 3 показаны конструктивные элементы подземного газогенератора с изолированными каналами. Подготовительные работы при устройстве такого газогенератора состоят в следующем. В наклонном или крутом пласте каналы газификации располагаются по падению пласта. В начале бурится газоотводящая скважина, которая обсаживается колонной металлических труб, а затрубное пространство тампонируется цементным раствором. Затем приступают к бурению канала газификации заданной длины и дутьевой скважины. Забои дутьевой скважины и канала газификации соединяют либо с помощью фильтрационной сбойки, либо гидроразрывом. После этого приступают к огневой проработке канала. Если пласт горизонтальный или пологий, каналы газификации подготавливаются бурением. Для пластов мощностью 2—10 м рекомендуемая длина газогенератора 400—500 м (по падению пласта). Размер по простиранию зависит от производительности газогенератора, при этом следует учитывать, что наилучшее качество газа получается при интенсивности процесса, равной 20 тыс. м3 газа на 100 м длины по простиранию (для пластов мощностью 2 м) и 80—100 тыс. м3 (для пластов мощностью 8—10 м). Диаметр дутьевых скважин должен быть не менее 250—300 мм, а газоот-водящих — 350—400 мм. Расстояние между газоотводящими скважинами, т.е. между каналами газификации, должно быть в пределах 50—60 м.
Рисунок 3 – Конструкционный элемент подземного газогенератора с изолированными каналами газификации и наклонными дутьевыми скважинами
1 — поверхность земли; 2 — выход пласта под насосы; 3 — наклонная газоотводная скважина; 4 — наклонная скважина для нагнетания дутья; 5, 6 — концы обсадных колонн
Наклонные крутые пласты могут разрабатываться и по простиранию пласта.
Конструкция подземных газогенераторов для горизонтальных и пологих угольных пластов может иметь прямой или боковой газоотводы. В первом случае на месторождении бурятся ряды скважин по квадратной или прямоугольной сетке. Расстояние между скважинами в каждом ряде колеблется от 25 до 60 м и выбирается в зависимости от степени выгазования угля. В газогенераторах данной конструкции каждая скважина поочередно выполняет функции дутьевой и газоотводящей. В противоположность этому в газогенераторах с боковым газоотводом одни скважины служат в качестве дутьевых, другие — только для отвода газа.
Система выгазования угольных пластов - это определенный порядок проведения подготовительных и огневых работ во времени и пространстве. Подготовительные работы включают бурение скважин, подготовку каналов газификации, обеспечение водоотлива. Под огневыми работами подразумевается собственно процесс газификации угля.
Выгазование наклонных и крутых пластов можно вести либо по восстанию, либо по простиранию. Выбор той или иной системы зависит от технических, технологических и экономических факторов, таких, как наличие технических средств для бурения скважин и подготовки каналов газификации, рациональная длина последних с точки зрения полноты выгазования угля и устойчивости качества газа, размеры единовременных капитальных затрат на строительство подземных газогенераторов.
При сплошной системе выгазования капитальные затраты на 1 т запасов, подготовленных к газификации, минимальны, но начальная величина этих затрат может оказаться большой. При этажной системе удельные капитальные затраты увеличиваются, однако при этом получается газ стабильного состава благодаря периодическому приближению подачи дутья к угольному массиву. Обе системы требуют применения конструкций газогенераторов, обеспечивающих отвод газа в угольный массив.
Выгазование пластов по простиранию может вестись от центра участка к его границам, от границ участка к центру и от одной границы участка к другой. Во всех этих системах могут применяться конструкции газогенераторов с отводом газа в угольный массив или в выгазованное пространство.
При отработке свиты пластов выбор системы выгазования усложняется, так как необходимо снизить до минимума потери газа и водопритока в подземный газогенератор, а также обеспечить благоприятные условия для бурения скважин.
Процесс сдвижения пород при подземной газификации происходит обычно с малой скоростью и весьма плавно. Отработка свиты пластов снизу вверх предпочтительнее.
Технологическая схема станции подземной газификации. Станции подземной газификации могут производить газ энергетический и технологический, совместно и раздельно. Наиболее простую технологическую схему имеет станция, производящая энергетический газ на воздушном дутье. В ее состав входят четыре цеха — компрессорный, газогенераторный, очистки и охлаждения газа, транспортирования газа.
В компрессорном цехе устанавливаются компрессоры двух типов — высокого и низкого давления. Первые предназначаются для подачи в подземный газогенератор дутья высокого давления (50—600 Па) на фильтрационную сбойку или проработку каналов газификации. Компрессоры низкого давления (турбовоздуходувки) подают дутье на газификацию под давлением 15—20 Па. Из компрессорного цеха дутье поступает в газогенераторный цех по двум системам трубопроводов и далее подводится к соответствующим скважинам.
Для отбора газа из газоотводящих скважин служат коллекторы из металлических труб. Дутьевые и газовые коллекторы не являются постоянными сооружениями и периодически переносятся по мере отработки запасов угля. На каждом газовом коллекторе устанавливаются циклоны — аппараты для улавливания крупной пыли, выносимой с газом из газоотводящих скважин. Далее газ направляется в цех охлаждения и очистки.
Предварительное охлаждение газа может производиться непосредственно в газоотводящих скважинах. Для этого в каждую из них опускается водоподающая трубка диаметром 12—18 мм с распылителем на конце. В состав цеха охлаждения и очистки газа входят холодильники — скрубберы, градирня, циркуляционная система охлаждающей воды, отстойники, электрофильтры, установка сероочистки. Вначале газ поступает в скрубберы, где охлаждается до температуры 30°—35° С и одновременно дополнительно очищается от пыли и частично от смолы. Далее он поступает в электрофильтры, где окончательно очищается, а после этого — в скрубберы сероочистки для извлечения сероводорода. Затем он направляется в транспортный цех, где установлены турбогазодувки, подающие газ потребителям.
Вместо сооружения компрессорного цеха целесообразно перейти к установке передвижных компрессоров у скважин. Отказ от централизованной подачи воздуха в подземный газогенератор может дать ряд выгод. Во-первых, отпадает необходимость в сооружении воздухопроводов; во-вторых, в скважины будет поступать воздух непосредственно из компрессоров, где он будет нагреваться, что приведет к улучшению теплового баланса подземного газогенератора.
Переработка газов ПГУ на химическую продукцию
В практике переработки газов на химическую продукцию используются природный газ, отходы газов металлургических и нефтеперерабатывающих производств, коксовые газы. Основными видами химической продукции, получаемой из газов, являются аммиак и метанол. Основным сырьем для их производства в настоящее время служит природный газ. Схема переработки газа ПГУ приведена на рисунке 4. Одно из основных требований к газу как сырью для химического производства — низкое содержание соединений серы. Как правило (исключая редкие случаи малосернистых газов), это связано с необходимостью предварительной сероочистки газов. В настоящее время для извлечения серы из природного газа применяют физико-химические методы мокрой очистки с использованием в качестве поглотителя растворов этанол-аминов. Выделенный сероводород перерабатывают на серу по методу Клауса.
Хотя сочетанием методов метаноламинового и Клауса получают в мире миллионы тонн серы, данная технология обессеривания газа имеет ряд существенных недостатков: попеременный нагрев и охлаждение поглотительного раствора, что сопряжено с большой энергоемкостью, многостадийностью процесса и загрязнением окружающей среды (до 1 % содержания по объему Н2S). Данный метод целесообразен при очистке газов с высоким содержанием сероводорода и оказался неэкономичным при концентрации его в газе менее 1 % по массе.
Рисунок 4 – Схема подземной газификации сернистого угля на воздушном дутье с переработкой газа на серу и аммиак (по схеме ГИАП)
Более эффективным методом очистки малосернистых газов является окислительный, состоящий из частичного окисления сероводорода до сернистого газа и восстановления из сероводорода серы сернистым газом. Данный метод позволяет получать элементарную серу, исключив одновременно процесс Клауса и доочистку отходящих газов. Основной задачей окислительного метода является подбор окислительного катализатора, который был бы инертен к попутно образующимся сульфатам. Главная трудность получения попутной серы из газов носит экономический характер. Из газов с высоким (2—5%), а также сверхвысоким (до 25%) содержанием сероводорода по объему производство серы представляет самостоятельный интерес как фактор комплексного использования сырья с соответствующей экономической эффективностью. При низком же содержании сероводорода (2 % и менее) затраты (особенно капиталовложения) при существующих методах очистки не могут привести к заметной компенсации. Поэтому необходима разработка высокоэффективных и экономичных методов очистки с получением серы либо серной кислоты.
Экономичное решение проблемы сероочистки газов не только с высоким, но и с низким содержанием сероводорода обеспечит: повышение качества газа; снижение коррозионной способности его при последующем использовании в энергетике и технологической переработке; комплексное использование газа при получении серы в качестве товарного продукта; улучшение атмосферных условий промышленных районов и в конечном итоге – расширение сырьевых источников энергетики и химической промышленности.
Заключение
1.При увеличении водопритока в зону газификации следует принимать меры к активизации процесса подземного горения угля, в частности увеличивать скорость подачи окислителя и применять стимулирующие добавки (углеводороды, кислородное дутье).
2. Повышение теплотворной способности генераторного
газа ведет к увеличению производительности участка подземной газификации по сгоревшему углю; при теплотворной способности газа более 2000 ккал/м3 увеличение скорости сгорания идет почти по экспоненте; увеличение теплотворной способности генераторного газа следует обеспечивать расширение зоны восстановительных реакций и путем
добавления в поступающие газы горючих компонентов,
увеличивающих температуру сгорания угля в недрах.
3. Увеличение скорости сгорания угля в недрах способствует росту выхода газов; при скорости более 0.5 т/ч выход
газов увеличивается с нарастающей скоростью.
Список литературы
1. Аренс В.Ж. Физико-химическая геотехнология Учеб. пособие. - М.: Издательство Московского государственного горного университета, 2001. -656 с.
2. Крейнин Е.В. Подземная газификация углей-М.2013.
3.https://ru.wikipedia.org/
4. http://miningwiki.ru/
Дата добавления: 2018-02-28; просмотров: 277; Мы поможем в написании вашей работы! |
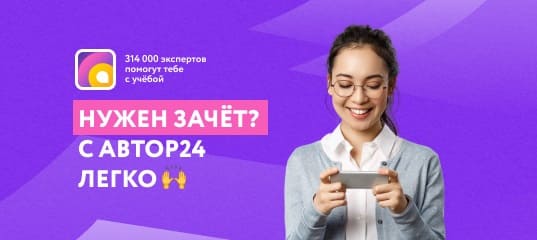
Мы поможем в написании ваших работ!