Схема установки для автоматичной наплавке деталей вращение под слоем флюса?
Схема наплавки деталей под слоем флюса: 1 - кассета с проволокой;2 - бункер с флюсом;3 - направляющиймундштук;4 - механизм подачи электродной проволоки;5 - деталь;6 - поддон;7 - выпрямитель;8 - пневмосистема для возвращения осыпавшегося флюса в бункер (применяется при больших программах наплавки).
137. Почему повышается качество шва под слоем флюса?
В зоне горения дуги образуется полость, заполненная парами металла, флюса и газами. Их давление поддерживает флюсовый свод, образующийся над сварочной ванной. Расплавленный флюс в результате значительно меньшей плотности всплывает на поверхность расплавленного металла шва, покрывает его плотным слоем и препятствует разбрызгиванию жидкого металла.
Почему повышается производительность труда при автоматической наплавке деталей под слоем флюса?
Производительность процесса по машинному времени повышается в 6... 12 раз. Это достигается за счет использования больших плотностей тока в электродной проволоке (например, при ручной сварке, d3=3 мм, плотность тока, А/мм2 - 11... 18; под флюсом - 50... 85А/мм2), соответственно, сила тока, А - 80. ..130 и 350. ..600. Такое повышение абсолютного значения тока и его плотности в электроде возможно благодаря наличию плотного слоя флюса вокруг зоны сварки, что предотвращает выдувание жидкого металла шва из сварочной ванны и сводит потери, на угар и разбрызгивание до 1 . . .3 %.
|
|
Почему снижается стоимость сварочных работ при автоматической наплавке деталей под слоем флюса?
Меньшая стоимость сварочных работ: - сокращается расход электродной проволоки на угар, разбрызгивание; устраняются расходы, на изготовление электродов;- сокращаются расходы электроэнергии вследствие величения теплового К.П.Д. дуги с 0,25 до 0,68;сокращается трудоемкость сварочных работ, а следовательно, сокращаются расходы по зарплате.
Основные отрицательные стороны автоматической наплавки деталей под слоем флюса?
К недостаткам следует отнести: снижение усталостной прочности; - значительный нагрев детали: возможно коробление; большая зона термического влияния;- невозможность наплавки деталей диаметром менее 40мм по причине стекания наплавляя много металла и флюса с поверхности восстанавливаемой детали. Для предотвращения стекания наплавку ведут со смещением электрода с зенита в сторону, обратную направлению вращения детали (для деталей диаметром 50... 150мм смещение электрода лежит в пределах З...8мм);- необходимость в отдельных случаях повторной термической обработки детали: требуется специальные устройства для ведения всех швов, кроме горизонтальных.
|
|
Номенклатура ремонтируемых деталей наплавкой «под флюсом?
Для наплавки под слоем флюса цилиндрических, конических, лицевых наружных и внутренних поверхностей деталей диаметром 50. . .800 мм и длинной до 1300 мм, а также плоских деталей -400x300 мм.
Чем руководствуются при выборе проволоки и флюса для автоматической наплавки деталей под слоем флюса?
Наиболее широко в ремонтном производстве для восстановления деталей из углеродистых и низколегированных сталей используют высококремнистые марганцовистые плавленые флюсы АН-348А, ОСЦ-45 и др.Для сварки легированных сталей используют плавленые флюсы с ограниченной концентрацией окиси кремния и окиси марганца (АН-10, АН-15, АН-30, ОФ-6 и др.). Более эффективными возможностями для легирования через флюсы обладают керамические флюсы (АНК-18, АНК-19 и др.).
Для сварки малоуглеродистых сталей используют проволоку Св-08, Св-08А, Св-08ГА и др. Для наплавки под слоем флюса используют также порошковые проволоки ПП-ЗХ2В8, ПП-1ОХВ14 и др. и сплошные или порошковые ленты толщиной 0,3... 1 мм и шириной 20... 100 мм.
Дата добавления: 2018-02-28; просмотров: 682; Мы поможем в написании вашей работы! |
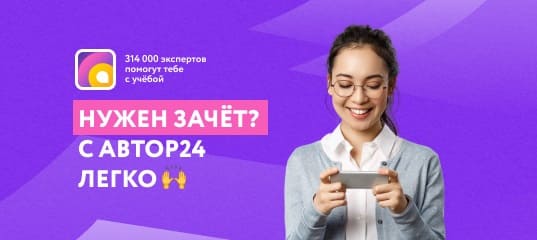
Мы поможем в написании ваших работ!