МЕТОДИЧЕСКИЕ УКАЗАНИЯ ПО ВЫПОЛНЕНИЮ РАЗДЕЛОВ КУРСОВОГО ПРОЕКТА
Введение
Сборочные единицы, которые выдаются студентам для выполнения курсового проекта, являются составными частями реальных изделий, выпускаемых заводами, относящимися к определенным отраслям машиностроения. Во введении необходимо кратко отразить значение отрасли и изделия для народного хозяйства России.
Расчет объема выпуска СЕ. Выбор типа производства. Расчет такта и размера партии выпуска СЕ
Объем выпуска СЕ рассчитывается по формуле, учитывающей:
1) объем выпуска изделий (указанный в задании на проект);
2) количество СЕ, идущих на одно изделие;
3) количество СЕ, изготавливаемых в качестве запасных частей.
Количество запасных частей может задаваться в абсолютных величинах либо в процентах от объема выпуска СЕ на основную программу. Рекомендуется эту величину принимать по данным завода-изготовителя.
Тип производства (массовый, серийный, единичный) выбирается с учетом объема выпуска изделий, трудоемкости их изготовления, массы и в соответствии с рекомендациями [1, 2, 3, 4, 9].
На данном этапе величина трудоемкости изготовления принимается ориентировочно по сведениям завода. По аналогии с заводом может также приниматься и тип производства.
Разработка технологического процесса сборки СЕ
1. Описание служебного назначения СЕ
Под служебным назначением СЕ понимается четко сформулированная задача, для решения которой предназначается СЕ. Эта формулировка должна также содержать все дополнительные условия и требования, которые эту задачу уточняют и конкретизируют. Например: сведения о производимой продукции; сведения о передаваемой энергии (мощность, число оборотов и т. д.); требуемая производительность, надежность и долговечность СЕ; режим работы; состояние окружающей среды; требования к внешнему виду, безопасности работы, удобству и простоте обслуживания и управления, уровню шума, коэффициенту полезного действия, степени механизации и автоматизации и т.п. [1, 3, 4, 9].
|
|
2. Технические условия и нормы точности на СЕ и их связь со служебным назначением СЕ
Технические условия и нормы точности СЕ являются прямым следствием, отражением служебного назначения СЕ. Необходимо все технические условия на СЕ классифицировать по соответствию их тем или иным требованиям служебного назначения СЕ. В первую очередь необходимо уделить внимание нормам точности и тем техническим условиям, которые содержат количественные показатели. Далее следует дать описание связи качественных технических условий с требованиями служебного назначения.
3. Выбор методов достижения требуемой точности СЕ
По указанию руководителя выбирается норма точности, которую надо выдержать при сборке для обеспечения служебного назначения СЕ. Составляется размерная цепь, с помощью которой достигается эта норма точности. Заданная норма точности представляет задачу, которую надо решить при сборке изделия, поэтому размер или относительный поворот поверхностей (или осей) деталей, оговоренный нормой точности, является замыкающим звеном размерной цепи [5, 8, 9, 12, 15].
|
|
4.Предварительный выбор вида и организационной формы сборки
Необходимо выбрать вид сборки (поточная или непоточная) и организационную форму (неподвижная или подвижная), так как от этого зависит решение последующих задач, этот выбор является предварительным и будет уточнен в последующем после проектирования технологического процесса сборки и его нормирования. На данной этапе решение может приниматься по аналогии с организацией сборки на заводе-изготовителе и с учетом принятого в проекте объема выпуска [1, 3, 4, 5, 9].
5. Анализ технологичности конструкции СЕ
Конструкция сборочной единицы является технологичной, если она соответствует требованиям изготовления, эксплуатации и ремонта наиболее производительными и экономичными способами при заданных условиях производства. Степень этого соответствия выясняется путем анализа технологичности конструкции СЕ [1, 2, 4, 5, 6, 9].
|
|
6. Выбор методов контроля качества сборки СЕ
Дать описание методов контроля СЕ по всем основным техническим условиям и нормам точности с эскизами, поясняющими процесс контроля и применяемые при этом инструменты и приспособления [1, 2, 3, 4, 5, 9, 17].
7. Выбор методов балансировки и испытания изготовленной СЕ
Неуравновешенностью (дебалансом) называют состояние вращающихся частей машины или СЕ, называемых роторами, характеризующееся распределением масс, вызывающим в процессе вращения переменные нагрузки на опорах ротора иего изгиб.
Балансировка - это определение значений и углов дебалансов ротора и уменьшение их корректировкой его массы до допустимого значения дебаланса для условий эксплуатации данной машины.
Балансировку СЕ разделяют на статическую и динамическую.
Статическую балансировку применяют для СЕ, у которых L/D<3 и скорость вращения V<6 м/с. Если L/D>3 и V>6 м/с, необходима динамическая балансировка. Дебалансы уменьшают с помощью корректирующих масс, которые можно добавлять к ротору или удалять из тела ротора, а также перемещать по нему [1, 2, 4, 17].
|
|
8. Анализ базового технологического процесса сборки СЕ. Разработка технологической схемы последовательности сборки СЕ
Последовательность сборки СЕ определяется ее конструктивными особенностями и принятыми методами обеспечения заданной точности. Начинать сборку следует с установки на сборочном стенде или конвейере основной базирующей детали. В ряде случаев роль базирующей детали может выполнять комплект или даже более сложное соединение деталей. Смонтированные в первую очередь сборочные единицы и детали не должны мешать установке последующих деталей и сборочных единиц. В первую очередь необходимо монтировать сборочные единицы и детали, выполняющие наиболее ответственные функции в СЕ. При наличии параллельно связанных размерных цепей сборку следует начинать с установки тех сборочных единиц и деталей, размеры или относительные повороты поверхностей которых являются общими звеньями и принадлежат большому количеству размерных цепей [13, 17].
9. Нормирование процесса сборки. Составление циклограммы
сборки
Нормирование состоит в определении времени выполнения сборки по переходам, сформированным при разработке последовательности сборки [1, 2, ,3, 9]. На этом этапе определяется только оперативное время сборки, т.е. сумма основного и вспомогательного времени на выполнение перехода. Оперативное время определяется по нормативам на слесарно-сборочные работы, которые могут быть различными в зависимости от типа производства (единичное и мелкосерийное, серийное, крупносерийное и массовое), от степени расчленения норм (дифференцированные и укрупненные) и от масштаба применения (общемашиностроительные, отраслевые, заводские).
Далее составляется циклограмма сборки, которая представляет графическое изображение длительности сборки и в совокупности с технологической схемой сборки является основой для технолога при формировании сборочных операций [3].
10. Формирование сборочных операций, операций технического контроля и окончательный выбор организационной формы сборки.
Используя технологическую схему и циклограмму сборки, следует принять окончательное решение о виде сборки (поточная или непоточная) и организационной форме (подвижная или неподвижная).
В случае подвижной сборки также надо решить, будет ли перемещение объекта непрерывным или прерывистым и как технически оно будет осуществляться (конструкция конвейера и т. п.) [3, 4, 5, 13].
Для решения этих вопросов необходимо объединить переходы в операции, т. е. сформировать сборочные операции. Эта работа выполняется параллельно с выбором вида сборки, так как от соотношения длительности операций и заданного такта выпуска, возможности их синхронизации по времени и т. п. зависит решение о возможности применения поточной организации труда. На сформированные операции необходимо рассчитать нормы времени, учитывающие все остальные (помимо оперативного) затраты времени [5]. Дать описание контрольных операций и средств их технологического оснащения [1, 2, 3, 5].
11. Выбор методов окраски и консервации изготовленной СЕ
В соответствии с требованиями конструкторской документации изделие может быть подвергнуто окраске лакокрасочными покрытиями. Процесс нанесения лакокрасочных покрытий состоит из трех этапов: подготовки поверхности, ее окраски и сушки. Подготовка поверхности под окраску включает: очистку, выравнивание, грунтовку, шпаклевку с последующим шлифованием. Окраска осуществляется одним или несколькими слоями ручным способом, распылением в электростатическом поле, окунанием, обливанием с электрофорезом и т. д. Сушку различают естественную и искусственную [1, 2, 3, 5]. Консервации подвергают все обработанные поверхности, не имевшие лакокрасочного покрытия [1, 2, 3, 4, 5].
12. Технологические карты сборки и контроля. Разработка эскизов и чертежей наладок по операциям
Окончательный вариант технологического процесса сборки документально оформляется на стандартных технологических картах.
Вначале помещается маршрутная карта технологического процесса, в которую заносятся все операции сборки и контроля данной СЕ, включая транспортную, мойку, балансировку, консервацию, упаковку и т.д. Нумерация операций ведется по порядку цифрами 0, 5, 10, и т. д.
Оформление операционной карты сборки начинается на заглавном листе и продолжается, при недостаточности строк переходов, на следующих листах. Все графы операционной карты должны быть заполнены согласно [1, 2, 8], а сами карты подписаны студентом и руководителем проекта.
В операционную карту записываются все переходы и приемы работы в порядке последовательности их выполнения на данной операции. Содержание переходов и приемов записывается в повелительном наклонении неопределенной формы. Все переходы нумеруются в нарастающем порядке, по всем позициям и установкам.
Силовые параметры сборки, в том числе усилия запрессовки, клепки, длина рабочего хода сборочного инструмента, оборудование и режимы сварки, совместной механической обработки отдельных деталей, собранных в СЕ, проставляются в соответствующие графы бланка [1, 2, 8].
В данном разделе записки необходимо произвести расчет силовых параметров сборки, который в зависимости от конструкции СЕ включает [1, 2, 3]:
- расчет усилий запрессовки соединений деталей СЕ с гарантированным натягом с учетом температурного и силового воздействия;
- расчет величины допустимой силы затяжки и наибольшего момента затяжки резьбового соединения;
- расчет необходимого усилия при выполнении клепанных соединений;
- определение длины рабочего хода при сопряжении собираемых деталей.
При одновременной сборке нескольких СЕ данные об этом должны содержаться в тексте перехода.
На контрольные операции составляют инструкционные карты, в которых подробно указывают метод и последовательность контроля, используемые средства контроля.
При записи контрольной операции указывается процент контролируемых СЕ или периодичность контроля (в начале смены, после какого-то периода и т. д.). Эскиз СЕ для контрольной операции вычерчивается на бланках [8]. Рекомендуется на эскизе СЕ проставлять размеры и допуски на сопряженных деталях, имевших прессовые и переходные посадки, размеры контролируемых зазоров, величины допустимого смещения осей сопрягаемых деталей, габаритные размеры СЕ и т. д. На эскизе также приводятся технические условия, подлежащие контролю. Карты и эскизы контрольных операций помещаются вслед за технологическими операциями, после которых предусмотрен контроль согласно маршрутного технологического процесса.
Приводимое в технологических картах описание операций и переходов должно давать в предельно сжатой форме исчерпывающую постановку задачи (что и для чего должно быть сделано) и указания, как, чем и с какими затратами времени эта задача должна быть решена. По указанию руководителя карты могут оформляться не на весь технологический процесс, а выборочно, на отдельные операций сборки и контроля в качестве примера.
В графическую часть проекта выносятся наиболее интересные наладки на операции сборки. Чертежи наладок обычно оформляются на сложные, многопереходные операции сборки, для выполнения которых необходимо применение сборочных приспособлений и оборудования, а также на операции сварки, клепки, заливки герметиком, совместную механическую обработку деталей, собранных в СЕ и др. Наладки на операции сборки выполняются на форматах A1, А2, А4 в зависимости от объема графического материала с оформлением углового штампа. Масштаб выполнения наладок произвольный, но все элементы наладки: детали, инструмент, элементы приспособления выполняются в одном и том же масштабе.
В чертежах наладок необходима схема установки и закрепления собираемой СЕ в приспособлении, установка присоединяемых деталей на позицию сопряжения без и с применением оснастки или оборудования. Эти чертежи должны разрабатываться с достаточной подробностью, позволяющей выявить идею приспособления и оснастки и производить наладку оборудования, а также представить конструкторскую разработку операции с указанием взаимного расположения собираемой СЕ, приспособления, оснастки и оборудования.
Разработка эскизов и чертежей наладок на каждую операцию сборки выполняется на отдельном формате. В чертеже наладок дается изображение сборочной оснастки с указанием ее конструкции и расположения, конструкция оправок, державок и других устройств для установки и закрепления сборочного инструмента с указанием размеров, определяющих положение инструмента друг относительно друга, величины рабочего хода, цикла работы оборудования или головок, направление перемещения СЕ. Инструменты изображаются в положении, определяющем конец перехода сборки.
Для большей наглядности вновь присоединяемые к базовой детали или к базовой СЕ детали изображаются красный цветом.
На чертеже собираемой СЕ указываются только те размеры и посадки сопрягаемых поверхностей, которые выполняются на данном переходе или операции. При необходимости следует давать чертеж собираемой СЕ в нескольких проекциях или показывать отдельные виды.
13. Выбор технических средств технологической оснащенности
Выбор технических средств предопределяет уровень технологической оснащенности операции сборки, а также уровень механизации и автоматизации технологического процесса сборки.
В этом разделе предлагается на основе имеющихся сведений выбрать:
- технические средства (приспособления) для установки и снятия заготовки на операциях сборки (установочно-зажимные приспособления, приспособления для изменения положения сборочных единиц и т.д.);
- технические средства для загрузки и разгрузки деталей и узлов (ориентирующие, загрузочные и разгрузочные устройства и т.д.);
- технические средства для транспортирования деталей с операции на операцию (поворотные столы, контующие устройства, столы для перемещения собираемого узла по двум горизонтальным координатам и т. д.);
- технические средства механизации операций сборки (приспособления для сборки упругих элементов, приспособления для выполнения пригоночных и вспомогательных работ, приспособления с центрирующими элементами, приспособления к прессам для запрессовки, напрессовки и клепки, приспособления для совместной механической обработки деталей при сборке, специальные сборочные головки и т.д.);
- технические средства контроля параметров, обеспечиваемых в процессе сборки (контрольные устройства для пассивного и активного контроля линейных, угловых и других параметров собираемого изделия или СЕ и т. д.).
Для снижения себестоимости сборки и ускорения технологической подготовки желательно максимально использовать универсальные стандартные и унифицированные средства [3].
В случае необходимости применения в проекте специальной оснастки разработать техническое задание (ТЗ) на одно специальное приспособление.
14. Разработка технического задания на проектирование специальной оснастки для сборки или контроля СЕ [18].
Дата добавления: 2018-02-28; просмотров: 263; Мы поможем в написании вашей работы! |
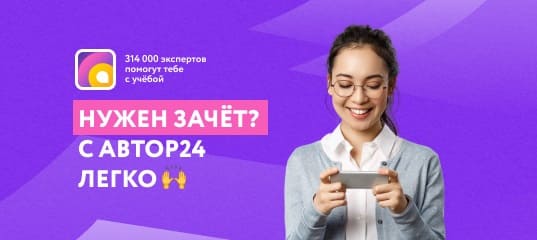
Мы поможем в написании ваших работ!