Примеры расчета сварных соединений, выполненных дуговой сваркой
Рассмотрим два примера расчета угловых швов, очерченных по равнобедренному треугольнику.
Пример 1 (рис. 4.34 а). Швеллер №12 прикреплен к листу лобовым и фланговым швами. Сварка ручная (β=0,7). Определить напряжение в швах при Р=180 кН.
Площадь сечения лобового шва, имеющего катет шва К=5 мм,
Fл=lβК=12·0,7·0,5=4,2 см².
Площадь сечения двух фланговых швов при К = 8 мм
Fфл = 2 lβК = 2·20·0,7·0,8 = 22,4 см².
Площадь сечения всех угловых швов прикрепления
F = Fл + Fфл =4,2 + 22,4 = 26,6 см².
Напряжение среза в швах
τ =Р/ F =0,18/0,00266 = 67,7 МПа.
Пример 2 (рис. 4.34 б). Уголок 90Х90 мм имеет площадь сечения F = 15,6 см². Допускаемое напряжение в металле уголка [σ]р =200 МПа, допускаемое напряжение среза в шве [τ'] =120 МПа. Спроектируем сварное соединение, равнопрочное уголку; сварка однопроходная полуавтоматическая (β = 0,8).
Допускаемое растягивающее усилие в уголке
Р=[σ] р ·F =200· 15,6·10 -4 = 0,312 МН.
Проектируем лобовой шов с катетом К = 9 мм.
Усилие, допускаемое на лобовой шов, равно
Рл=[τ'] lβКл= 120 · 0,8 · 0,009 · 0,09 = 0,078 МН.
Остальная часть усилия должна быть передана на фланговые швы:
Pфл= Р-Рл= 0,234 МН.
Усилие, передаваемое на шов 1,
Р1=0,7Рфл = 0,164 МН.
Катет шва 1 принимаем К = 12 мм, тогда требуемая длина
L1 = Р1/(βК [τ']) = 0,164/(0,8 · 0,012 · 120) = 0,142 м.
Принимаем l1 = 14 см.
Усилие, передаваемое на шов 2,
Р2=0,3Рфл= 0,07МН.
Катет шва 2 принимаем К = 9 мм, тогда требуемая длина шва
|
|
L2 = Р2/(βК [τ']) = 0,07/(0,8 · 0,009 · 120) =0,08 м.
Принимаем l2 = 8 см.
Примеры 3-6 предлагаются для самостоятельной работы по расчету угловых швов.
Пример 3 (рис. 4.34 в). Полоса сечением 300Х12 мм прикреплена к листу фланговыми и косыми швами с катетами К = 12 мм и лобовым швом с катетом К = 8 мм. Определить допускаемое усилие Р, если [τ'] = 120 МПа; сварка автоматическая (β = 1).
Пример 4 (рис. 4.34 г).
Определить требуемые длины фланговых швов для прикрепления двух тяг уголкового профиля 100Х100 Х 8 мм. Площадь сечения тяги F = 15,6 см². Поддерживаемый груз Р = 200 кН, сварка полуавтоматическая (β = 0,8).
Пример 5 (рис. 4.34 д). Определить число сварных точек для прикрепления к листу швеллера № 6,5 площадью сечения F = 8,28 см² и толщиной стенки 4,5 мм при условии Р = 100 кН с допускаемым напряжением на срез точки [τ']= 90 МПа и произвести их расстановку с учетом t, t1 и t2.
Рис. 4.34. Примеры расчета сварных соединений
Пример 6 (рис. 4.34 е). Полоса сечением 200Х12 мм приваривается к листу. Усилие Р = 500 кН, допускаемое напряжение шва [τ'] = 130 МПа. Определить количество наплавленного металла при швах в форме равнобедренного треугольника с катетами К, равными 8 и 12 мм; сварка ручная (β = 0,7).
|
|
Соединения при сварке пластмасс
Сварка горячим воздухом. При сварке воздух, нагретый в специальной горелке до 250-300°С, в зоне сварки несколько охлаждается. Сварка осуществляется присадочным прутком, подающимся в разделку шва вручную или полуавтоматом.
Сварка нагревательным элементом. Позволяет сваривать угловые, тавровые и стыковые соединения.
При сварке трубопроводов из полиэтилена широко применяется способ с применением закладных нагревателей (рис. 4.35), который позволяет поддерживать стабильные параметры процесса нагрева, обеспечивать высокий уровень механизации сварочных работ, значительно увеличивать производительность труда и сокращать продолжительность монтажа трубопровода в сложных монтажных условиях.
Рис. 4.35. Схема электромуфтовой сварки с закладным нагревателем:
1 – закладной нагреватель; 2 – электрокабель; 3 – сварочный аппарат; 4 – полиэтиленовая труба; 5 – электромуфта
Другим примером сварки нагретым элементом является электроимпульсная сварка очень тонких пленок толщиной в сотые доли миллиметра. При этом узкая металлическая лента прижимается к нахлестке соединяемых пленок, нагревается током и быстро охлаждается. Соединения обладают достаточной прочностью.
|
|
Сварка токами высокой частоты. Этим способом сваривают поливинилхлорид, полиамид и др. Разогрев соединяемых деталей производится роликами, через которые пропускается ток высокой частоты.
Сварка трением. Трением сваривают стыковые соединения преимущественно тел вращения: стержней круглого сечения, труб.
Сварка ультразвуком является одним из прогрессивных способов соединения пластмасс. Она производится по схеме, приведенной на рис. 4.36. Колебания волновода направлены перпендикулярно плоскостям стыкуемых элементов. Сварка обычно производится односторонним способом, но в некоторых случаях целесообразно расположение волноводов с двух сторон.
Рис. 4.36. Схема ультразвуковой сварки пластмасс
Ультразвуком можно сваривать тонкие пленки, а также детали толщиной в несколько миллиметров из различных термопластичных материалов: полистирола, полиэтилена, поливинилхлорида, винипласта и т. п. При ультразвуковой сварке получают нахлесточные и тавровые соединения.
Нахлесточные соединения при сварке ультразвуком могут быть точечными и шовными. Для постановки точек применяют различные системы волноводов, которые ставят сварные точки как по линии, так и по сложному контуру. При этом особенно хорошие результаты получаются при сварке контурными волноводами, имеющими в поперечном сечении круглый кольцевой профиль. Качество соединений, сваренных ультразвуком, определяется продолжительностью процесса, амплитудой колебаний волновода, усилием сдавливания. Ультразвуком можно сваривать несколько пластин, образующих пакет, а также производить сварку в труднодоступных местах (рис. 4.37).
|
|
Рис. 4.37. Ультразвуковая сварка полимеров в труднодоступных местах
Ультразвуком можно осуществлять сварку не только в месте соприкосновения волновода с деталью, но и на некотором расстоянии, которое зависит от свойств полимера и конфигурации конструкции, подлежащие сварке. Сварка ультразвуком широко внедрена в различных отраслях промышленности.
В настоящее время с помощью ультразвуковых колебаний достигнута возможность соединения биологических тканей: костей, мягких тканей.
Болтовые соединения
Болтовые соединения применяются в конструкциях комбинированного характера. Часть соединений, выполняемых в цеховых условиях, проектируются сварными, другая часть, выполняемая на монтаже, - с применении болтов. Как правило, это болты высокой прочности, изготовляемые из стали 40Х, 40ХФА, имеющие предел прочности при растяжении более 1000 МПа. Распределение усилий в сварном соединении с такими болтами происходит более равномерно, чем в сварном соединении с заклепками.
По точности изготовления болты разделяются на ряд групп: болты повышенной точности изготовляются согласно ГОСТ7805-70, болты грубой точности - согласно ГОСТ15589-70. Болты устанавливаются диаметром от 10 до 48 мм при общей длине от 40 до 200 мм.
Болты повышенной точности могут быть поставлены в отверстие с минимальным зазором 0,3 - 0,5 мм. Это обеспечивает передачу усилия в результате плотного соприкосновения болтов с деталями.
В некоторых случаях усилие передается посредством трения. При этом не требуется плотное соприкосновение со стенками отверстия и, следовательно, упрощаются сборочные операции.
В строительных конструкциях расчет болтовых соединений на срез (рис.4.38) производится по формуле
τ = Р/(іπd²/4) ≤ Rбср, (4.48)
где і - число болтов; d - диаметр болтов; Р - усилие.
Расчет на смятие производится по формуле
σсм = Р/(іds) ≤ Rбсм, (4.49)
где s - наименьшая толщина соединяемых частей;
расчет на растяжение - по формуле
σбр = Р/(іπd²/4) ≤ Rбр. (4.50)
Расчетные сопротивления на срез Rбср в зависимости от марки стали принимаются от 150 до 300 МПа, на растяжение Rбр - от 170 до 400 МПа, на смятие Rбсм - от 380 до 740 МПа.
Расчет высокопрочных болтов, работающих посредством трения, производится с учетом усилия натяжения болта
Рб = 0,65σбв Fбн, (4.51)
где σ бв - предел прочности болта; Fбн - его площадь сечения по внутреннему диаметру.
Усилия, которые воспринимаются трением, составит
N = Рб f m, (4.52)
где m = 0,9 - коэффициент условий работы; f - коэффициент трения.
При отсутствии обработки соединяемых поверхностей f = 0,25;
при обработке щетками f = 0,35; при огневой обработке f = 0,40.
Рабочее усилие, воспринимаемое одним болтом,
N = 0,65σбв Fбн f m. (4.53)
Применение высокопрочных болтов облегчает условие монтажа и нередко оказывается рациональным с позиции повышения работоспособности конструкции при действии переменных и ударных нагрузок.
Высокопрочные болты могут быть рекомендованы не только для стальных конструкции, но и для конструкций из алюминиевых сплавов, например, АМг6, Д1Т, Д16Т и др. Применяют болты из сплавов АВТ1, В94, Д16п и др.
Размещение болтов определяются следующими условиями: минимальное расстояние между центрами 3,5 d максимальное расстояние между центрами в крайних рядах 5d или 10 s, то же в средних 10 d или 14 s; минимальное расстояние от центра болта до края элемента 2,5 d; максимальное - 6 s.
Здесь d - внешний диаметр резьбы болта; s - наименьшая толщина соединяемых частей.
Дата добавления: 2018-02-28; просмотров: 1382; Мы поможем в написании вашей работы! |
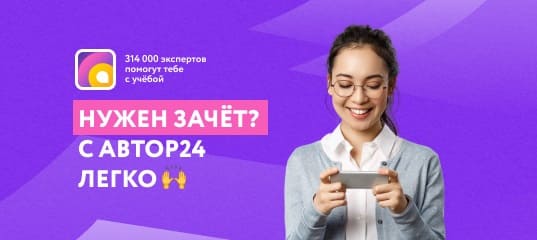
Мы поможем в написании ваших работ!