СПИСОК ИСПОЛЬЗОВАННЫХ ИСТОЧНИКОВ. 1 Целевое назначение процесса .3
СОДЕРЖАНИЕ
1 Целевое назначение процесса………………………………………………....3
2 Сырье процесса………………………………………………………………...5
3 Современные катализаторы процесса алкилирования……………………...6
4 Условия проведения процесса………………………………………………..9
5 Химизм процесс.................................................................................................12
6 Кинетика процесса…………………………………………………….………17
7 Целевые и побочные продукты………………………………………………18
Список использованных источников……………………………………….….19
ЦЕЛЕВОЕ НАЗНАЧЕНИЕ ПРОЦЕССА
Алкилирование – это процесс, обозначающий введение алкильного заменителя в органическую молекулу.
Главными агентами можно назвать алкены, спирты, кетоны, сульфиды, алкилгалогениды. Также в эту группу можно с уверенностью вписать эфиры, альдегиды и диазоалканы.
К катализаторам алкилирования относятся кислоты Льюиса, минеральные кислоты и целиоты. Кроме того необходимо отметить, что алкилирование довольно часто применяется в различных промышленностях, таких, например, как химическая и нефтехимическая.
Сам процесс в первую очередь направлен на то, чтобы получить высокооктановые компоненты бензина для автомобиля из непредельных углеводородных газов. Самым главным в процессе является реакция соединения алкана и алкена. При этом алкен получают с числом атомов углерода равным сумме атомов углерода в исходном алкене и алкане. Молекулы исходного сырья также как и молекулы алканов будут иметь изо-строение.
|
|
Необходимо отметить, что себестоимость данного вещества довольно велика. Для подготовки алкилирования необходимо использовать такое сырьё, как бутан-бутиленовую фракцию (ББФ). Её необходимо для начала очистить от сернистых соединений. Данные соединения чаще всего представлены меркаптанами. Для очистки ББФ используют определённый метод. Данный метод заключается в щелочной экстракции меркаптанов, а в дальнейшем осуществляется регенерация щёлочи.
Известно, что первая промышленная установка сернокислотного алкилирования была введена в эксплуатацию в США в 1938-ом году, именно оттуда и берёт своё начала алкилирование, как процесс в нефтехимической промышленности. Целевым продуктом в начале прошлого века был только лишь компонент авиатоплива и исключительно в послевоенные годы на базе газов каталитического крекинга алкилирование стали использовать для улучшения моторных качеств товарных и марочных автобензинов.
Из всего вышеизложенного ясно следует, что алкилирование – это довольно серьёзный процесс, который необходимо осуществлять во многих случаях.
|
|
СЫРЬЕ ПРОЦЕССА.
В промышленных условиях в качестве сырья применяют узкие фракции углеводородов.
Из парафинистых углеводородов наибольшее практическое значения для алкилирования имеет изубутан, фракцию С3‒С5 попутных нефтяных газов и газов нефтепереработки используют для получения изобутана. Высокое давление паров (520 кПа при 38°С) ограничивает возможность применения непосредственно как комплекта моторных топлив. При дефиците изобутана иногда в промышленных процессах алкилирования к изобутану добавляют изопентан (не более 20%).
Качество получающегося при сернокислотном алкилировании изобутана снижается в зависимости от используемого олефина в следующей последовательности:Бутилен-2 – бутилен-1 – изобутилен-2 – метилбутан-1 – 2-метилбутилен-2 – пентен-2 – пропилен. Примерно в такой же последовательности увеличивается расход изобутана и серной кислоты. В связи с этим в промышленных условиях алкилируют изобутан смесью бутиленов, которая может быть получена во вторичной переработки нефти: термическом и каталитическом крекинге, деструктивной перегонке тяжёлых остатков, коксовании, гидроформинге, гидрокрекинге.
|
|
Смесь, поступающая на алкилирование, содержит избыток изобутана. При использовании бутан-бутиленового сырья избыток изобутана составляет 10 – 15%. Часто принимают смесь пропилена и бутиленов, содержащую до 30% пропилена.
Современные катализаторы процесса алкилирования
Осуществление реакции алкилирования в присутствии жидких кислот(серной и фтористоводородной) – традиционная для мировой практикитехнология этого процесса. В мире эксплуатируется около 100 установокфтористоводородного и около 200 установок сернокислотного алкилирования общей мощностью 60 млн. тонн в год. Наращиваниемощностей процесса алкилирования за счет жидкокислотных технологий(фтористоводородноеисернокислотноеалкилирование) – наиболее дорогостоящий и наименее целесообразный способ реализации структурнойперестройки нефтеперерабатывающей отрасли России. Одной из основныхпричин этого является высокие затраты на обеспечение катализаторамитрадиционных процессов алкилирования [13,14].
В настоящее время ежегодный объем продаж катализаторов намировом рынке составляет около 2 млрд. долларов США из которых, надолю катализаторов алкилирования приходится 34% [15,16]. Совокупныезатраты промышленности на приобретение катализаторов алкилированиявыше, чем на катализаторы для таких крупнотоннажных процессов, какриформингигидроочисткавместе взятые, и лишь немного уступают затратам на катализаторы крекинга,мдоля которых в объеме годовых продаж составляет 43%. В то же времямощности процессов алкилирования в десятки раз меньше мощностейосновных процессов нефтепереработки.Причиной столь высокого уровня затрат является большой удельныйрасход серной кислоты, который в ≈ 1000 раз превышает расходыкатализаторов риформинга и в 100 раз превышает расходы катализаторовкрекинга. Расход серной кислоты в процессе алкилирования составляет 80-100 кг на одну тонну целевого продукта [17,18].
|
|
Высокий удельный расход катализаторов алкилирования являетсяосновным, но не единственным недостатком этого процесса. К другимнедостаткам относятся:
- высокая токсичность и коррозионная агрессивность фтористоводороднойи серной кислот;
- необходимость утилизации отработанных кислот;
- необходимость выделения и последующей нейтрализации алкилата изреакционной смеси;
3.1 Гомогенные катализаторы алкилирования.
В качестве гомогенных катализаторов в промышленности используютсерную кислоту и фтороводород.
Активность гомогенного катализатора алкилирования определяется егоактивностью. Фтороводород обладает значительно меньшей протонирующейактивностью, чем серная кислота – для 100%-ых кислот на два порядка ниже.Однако уровень значений диэлектрических постоянных таков, что в обеихкислотах концентрация ионных пар незначительна. Значительно болеевысокие плотности, вязкость и поверхностное натяжение серной кислотынамного усложняют создание высокой поверхности раздела между фазамикислота-углеводороды по сравнению со фтороводородом. Особенно важнымотличием фтороводорода является значительно большая (примерно на порядок) растворимость в нём изобутана. Скорость растворения алкенов вкислотах гораздо больше, чем изобутана .
В результате большей скорости растворения и растворимости изобутана в фтороводороде соотношение изобутан:алкен в реакционной зоне(в плёнке кислоты, в которой идёт реакция) значительно выше, чем в случаесерной кислоты. Поэтому роль побочных реакций при применении в качествекатализатора фтороводорода меньше, чем при катализе серной кислотой. Врезультате выход основных продуктов реакции при фтороводородномалкилировании значительно выше, чем при сернокислотном.Считается, что технология сернокислотного алкилирования являетсяболее безопасной по сравнению со фтороводородным алкилированием. Впроцессе сернокислотного алкилирования образуется большое количествоотработанной серной кислоты, которое необходимо регенрировать. Необходимость транспортировки отработанной и свежей кислоты наустановку регенерации создаёт определённые сложности. Однако никаких серьёзных улучшений в сернокислотном алкилировании по проблемерегенерации отработанной кислоты так и не было разработано.Несмотря на ряд существенных преимуществ фтороводорода передсерной кислотой как катализатора алкилирования высокая токсичностьограничивает применения фтороводородного алкилирования [19].
Реакция алкилирования изобутана олефинами сопровождается выделением большого количества тепла, которое необходимо отводить иззоны реакции. В производственной практике нашли применение два методаотвода тепла:
1) отвод тепла через поверхность теплообмена, расположенную внутриреактора; в этом случае используются замкнутые холодильные циклы сприменением специальных хладагентов – аммиака, пропана;
2)отвод тепла путем испарения в реакционном пространстве компонентов, участвующих в реакции, например, изобутана; в этом случаеповерхность теплообмена не нужна, что значительно упрощает конструкцию реактора.
В обоих случаях для создания развитой поверхности контактамежду сырьем и кислотой внутри реактора устанавливается перемешивающие устройства.
3.2 Гетерогенные катализаторы алкилирования.
Твердые катализаторы для алкилирования изобутана исследуютсяболее 30 лет. Это AlCl3, модифицированный ZrO2, гетерополикислотывольфрамовогоряда,жидкиекислоты,иммобилизованныенаSiO2,полимерах, цеолитах [24]. Твердые катализаторы могут увеличиватьселективность процесса, они более экологичны. Главный недостаток твердыхкатализаторов – малое число активных центров на 1 г катализатора. Так, в 1гH2SO4 содержится ≈ 20·10-3моль кислотных центров, а в 1г твердогокислотного катализатора – лишь < 10-3 моль, из которых только 20–30% являются достаточно сильными, чтобы катализировать реакцию алкилирования [25] Также большой проблемой твердых катализаторовявляется блокирование пор коксом, с их последующей дезактивацией. И поэтому время жизни твердого катализатора может ограничиваться несколькими минутами [26].
Указанныенедостаткипрепятствоваливнедрениютвердыхкатализаторов в промышленных масштабах. Большинство исследований вэтом направлении не вышли за пределы лабораторных испытаний.
Несмотрянатакоеразнообразиевисследованияхновыхтвердыхкатализаторов процесса алкилировния, ни один из них пока ещё не можетсоперничать с серной или фтороводородной кислотой ни по качествуалкилата, ни по стоимости эксплуатации.
УСЛОВИЯ ПРОВЕДЕНИЯ ПРОЦЕССА
3.1 Качество сырья
Обычно изобутан алкилируют этиленом или пропиленом. Т.к. процесс проводят в присутствии кислотных катализаторов, то в сырье строго ограничивают содержание соединений проявляющих основные свойства (соединения N2 и щелочи). Так же ограничивают содержание влаги и сернистых соединений.
При алкилировании изобутана бутиленами ограничивают содержание углеводородов С3 и С5, т.к. испарение легких С3 приводит к увеличению объема, тяжелых С5 – к перераспределению бутилена.
В основном в качестве сырья используют газы каталитического крекинга, термокрекинга, коксования и иногда пиролиза. В газе пиролиза содержатся диены, которые образуют сложные продукты взаимодействия с серной кислотой, которая остается в кислой фазе и разбавляют кислоту, что приводит к её перерасходу.
3.2 Катализаторы
Применяются серная и фтороводородная кислота. Растворимость изобутана в Н2SО4 невелика и приблизительно в 30 раз ниже, чем в НF. Олефины в этих кислотах растворяются достаточно хорошо и быстро. В этой связи концентрация изобутана на поверхности раздела фаз намного меньше концентрации олефинов, что обусловливает большую вероятность протекания реакций полимеризации олефинов. Поэтому процесс необходимо вести при постоянном перемешивании.
По совокупности каталитических свойств НF более предпочтителен, чем Н2SО4.
Процессы фтористоводородного алкилирования характеризуются следующими основными преимуществами по сравнению с сернокислотным:
‒ меньший выход побочных продуктов;
‒ повышенный выход алкилата и более высокое его качество;
‒ меньший расход кислоты;
‒ более высокая температура процесса (25 – 40 °С) вместо 7 – 10 °С и т.д.
Однако большая летучесть и высокая токсичность фтороводорода ограничивают его более широкое применение в процессах алкилирования.
3.3 Температура
Процесс сероводородного алкилирования низкотемпературный и оптимальная t=10 °С. Чем ниже t, тем выше скорость основных реакций, но она ограничивается высокой вязкостью кислоты. Чем выше t, тем выше скорость побочных реакций. Поэтому на установках, необходимо ограничить съём тепла, что достигается путем частичного испарения реакционной смеси.
3.4 Давление
При жидкофазном алкилировании давление не оказывает существенного влияния на процесс.При алкилировании изобутанабутиленами
р=0,35 – 0,42МПа. Если сырье содержат ППФ, то давление в реакторе несколько повышают.
3.5 Соотношение изобутан-олефин
Избыток изобутана интенсифицирует целевую и подавляет побочные реакции алкилирования. Однако чрезмерное повышение этого соотношения увеличивает капитальные и эксплуатационные затраты. Поэтому поддерживать его выше 10: 1 не рентабельно.
3.6 Соотношение катализатора к сырью
Соотношение катализатор:сырье должно быть в оптимальных пределах, при которых достигается максимальный выход алкилата высокого качества. Оптимальное значение этого отношения составляет около 1,5.
ХИМИЗМ ПРОЦЕСС
Реакция алкилирования по Фриделю-Крафтсу обратима. Обычные правила ориентации соблюдаются здесь только до тех пор, пока процесс протекает при кинетически контролируемых условиях, следовательно, реакция должна быть вовремя прервана, что удается только в том случае, если скорость реакции можно поддерживать маленькой, т.е. если работают при мягких условиях (при низкой температуре и с малыми количествами катализатора).
Алкилирование изобутана алкенами идет с выделением от 75 до
95 кДж/моль теплоты в зависимости от вида алкена и образующегося изоалкана. В зависимости от строения применяемого бутена и получающегося УВ изменение энергии Гиббса в стандартных условиях положительна при температуре 142 – 295°С. Алкилирование протекает по карбокатионному механизму.
1 стадия: протонирование алкенов
При высоком соотношении изобутана и бутена в реакционной зоне бутильный катион в основном реагирует с изобутаном.
Возможна так же изомеризация бутильного катиона
Образовавшийся по реакции (2) и (2а) изобутильный и бутильный катион вступают в реакцию с бутеном.
Образовавшийся октильный ион может вступать в следующие реакции: при высокой концентрации в реакционной среде изобутана при отрыве гидрид-иона образуются 2,2,3 – триметилпентан
До реакции (4) октильный ион может изомеризоваться
Стабилизация активных ионов приводит к образованию из ионов I и II, образовывается 2,2,4-триметилпентана. Из ионов IV 2,2,4-триметилпентана, из иона V 2,3,3-триметилпентана.
Октильные ионы также могут распадаться. Однако ионы I и II могут распадаться только с отрывом метильного иона, что в условиях процесса практически невозможно.
Распад карбокатиона V с отрывом метильного иона также мало вероятно. Наиболее вероятен в условиях процесса алкилирования, распад октильно-
го иона IV с образованием пентена и изопропилового карбокатиона.
Распад иона III на состав продуктов реакции не влияет.
При реакции октильного карбокатионов с бутеном образуются додецильные ионы .
Додецильные карбокатионы могут вступать в реакции анологичные реакциям октильного иона (4,6).
По реакции (6а) наиболее вероятное образование третичных карбокатионов С5, С6 и С7 и соответственно алкенов С7, С6 и С5. Образование иона С8 не влияет на состав конечных продуктов реакции, а образование ионов С1, С2 и С3 практически не происходит и м/т не учитываться. Образующиеся алкены и карбокатионы реагируют аналогично 2-бутену и третичному карбокатиону. Карбокатионы могут передать протон водорода остатку кислоты:
Образовавшиеся алкены вступают в реакцию алкилирования изобутана также как и исходный бутен. Так же кроме реакции присоединении (3) возможны и другие реакции, при взаимодействии карбокатиона с алкенами.
При увеличении концентрации изобутана и карбокатиона реагирует по реакции обратной прямой реакции (9). Также возможны следующие реакции с карбокатионом
Образовавшийся олефин реагирует по следующим направлениям
(11)
В результате реакций (10) и (11) образуется сложная смесь УВ включающая циклоалканы, циклоалкены и диены.
Карбокатионы могут также отрывать гидрид ион у третичного атома С продуктов реакции с последующим вступлением образовавшихся карбокатионов уже рассмотренных реакций. Сочетание реакции (3,4,5) дает цепной процесс, который описывается уравнением
iC4H10 + C4H6 → iC8H18
С реакцией (4) для октильных карбокатионов конкурируют реакции (6,7,8а,9), эти реакции не желательны. Чем больше отношение изобутана к бутилену, тем меньше протекают реакции (7,9). Увеличение концентрации изобутана в реакционной зоне подавляет также молекулярные реакции карбокатионов (6,8).
Для подавления расходования продуктов в реакционной зоне также должно быть высокое соотношение изобутана к изооктану. При высоком отношении изобутана к бутилену и малой концентрации бутилена в реакционной зоне должен быть третичный бутильный карбокатион, превращающийся по реакции (8) в 2-метилпропен, который затем вступает в следующую реакцию:
В этом случае происходит самоалкилирование по суммарной реакции:
2 iC4H10 + C4H8 → iC8H18 +C4H10
Таким образом наряду с основной реакцией алкилирования изобутана алкенами могут протекать побочные реакции, приводящие к образованию более легких и более тяжелых, чем сырьевой продукт.
КИНЕТИКА ПРОЦЕССА
Сама реакция алкилирования идет очень быстро, сильно ускоряется при механическом перемешивании или интенсивном барботировании газообразных олефинов через реакционную массу и протекает в диффузионной или близкой к ней области. Ее скорость повышается при росте давления, но мало зависит от температуры, имея низкую энергию активации. При этом сохраняется обычная зависимость в реакционной способности олефинов — более сильная, чем различие в их растворимости. Видимо, лимитирующей является стадия диффузии олефина через пограничную пленку каталитического комплекса хлорида алюминия, в которой протекают все реакций. В отличие от этого, переалкилирование идет значительно медленнее и существенно ускоряется при повышении температуры, так как имеет энергию активации ~63 кДж/моль.
Обе реакции замедляются при постепенном дезактивировании катализатора, но особенно сильно падает скорость переалкилирования. В результате в реакционной смеси будет накапливаться значительное количество полиалкилбензолов, не успевающих вступить в обратимую реакцию переалкилирования.
Во избежание этого приходится ограничивать подачу реагентов, и, следовательно, возможность интенсификации процесса лимитируется самой медленной реакцией переалкилирования.
На дезактивирование катализатора кроме примесей реагентов влияет накопление некоторых побочных продуктов алкилирования, способных прочно связывать А1С13или образовывать стабильные σ-комплексы, с трудом отдающие свой протон молекуле олефина. Такими веществами при низкой температуре, когда переалкилирование идет медленно, являются полиалкилбензолы, а при высокой температуре — полициклические ароматические соединения и смолы. В результате оказывается, что оптимальные производительность и расход катализатора при получении этил- и изопропилбензола достигаются при некоторой средней температуре («100°С), когда переалкилирование протекает уже достаточно быстро, но полициклических веществ, дезактивирующих катализатор, получается еще мало.
ЦЕЛЕВЫЕ И ПОБОЧНЫЕ ПРОДУКТЫ
Продукцией процесса сернокислотного алкилирования являются лёгкий и тяжёлый алкилаты, пропан, н-бутан, изобутан (при избыточном содержании в исходном сырье). Характеристика лёгкого алкилата (до 180 °С),используемого как высокооктановый компонент бензинов: плотность 690 –
720 кг/м3, октановое число 91 – 95 (по моторному методу), иодное число менее 1%, содержание фактических смол менее 2 %.
Тяжёлый алкилат, выкипающий в интервале температур 185 – 310 °С, плотностью 790 – 810кг/м3 применяется в качестве компонента дизельного топлива и растворителя для различных целей.
Целевой продукт алкилирования – изооктан – содержит смесь изомеров 2,2,4-; 2,2,4-, 2,3,4-, 2,3,3-триметилпентан. Причина лежит в особенностях механизма реакции, осложненной процессами изомеризации. Общепринято, что каталитическое алкилирование изоалканов идет через промежуточные образования ионов карбония.
В результате побочных реакций получаются ненасыщенные полимеры, ухудшающие качество алкилата и ведущие к повышенному расходу катализатора.
СПИСОК ИСПОЛЬЗОВАННЫХ ИСТОЧНИКОВ
1 Ахметов С. А. и др.Технология и оборудование процессов переработки нефтии газа: Учебное пособие / С. А. Ахметов, Т. П. Сериков, И. Р. Кузеев,М. И. Баязитов; Под ред. С. А. Ахметова. ‒ CПб.: Недра, 2006. ‒
868 с.; ил.
2 Магарил Р. 3. Теоретические основы химических процессов переработки нефти: Учебное пособие для вузов. ‒ Л.: Химия, 1985, 280 с.
3 Агабеков В.Е., Косяков В.К., Ложкин В.М. Нефть и газ. Добыча, ком-плексная переработка и использование. Мн.: БГТУ, 2003. 376 с.; табл. 36, ил. 27, библиогр. 61 назв.
4 Капустин В. М., Гуреев А. А.Технология переработки нефти. В 2 ч. Часть вторая. Деструктивные процессы. ‒ М.: КолосС, 2007. ‒ 334 с.: ил.
5 Гуреев А.А. Производство высооктановых бензинов Химия 1981 год-224 с.
Дата добавления: 2018-02-28; просмотров: 411; Мы поможем в написании вашей работы! |
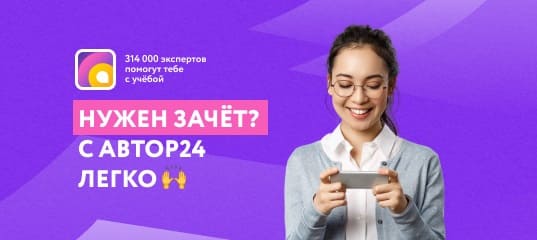
Мы поможем в написании ваших работ!