СПИСОК РЕКОМЕНДУЕМОЙ ЛИТЕРАТУРЫ. Федеральное агентство по образованию
Федеральное агентство по образованию
Государственное образовательное учреждение
высшего профессионального образования
«Кузбасский государственный технический университет»
Кафедра технологии машиностроения
РАЗРУШАЮЩИЕ МЕТОДЫ ИСПЫТАНИЙ КОНТРОЛЯ
КАЧЕСТВА СВАРНЫХ СОЕДИНЕНИЙ
Методические указания к практическому занятию по курсам
«Методы контроля качества сварных соединений» для студентов специальности 150202(120500) «Оборудование и технология сварочного производства»
| Составитель А. Н. Смирнов |
Утверждены на заседании кафедры Протокол № 2 от 27.09.2006 | |
Рекомендованы к печати учебно-методической комиссией специальности 150202 Протокол № 2 от 28.09.2006 | |
Электронная копия находится в библиотеке главного корпуса ГУ КузГТУ |
Кемерово 2006
ЦЕЛЬ РАБОТЫ
Целью работы является изучение основных требований к методам разрушающих испытаний сварных соединений, условиям проведения испытаний и оценке их результатов.
ТЕОРЕТИЧЕСКИЕ ПОЛОЖЕНИЯ
В настоящих методических указаниях изложены методы определения механических свойств сварного соединения в целом и его отдельных участков, а также наплавленного металла при всех видах сварки металлов и их сплавов.
2.1. Виды испытаний и их область применения
Согласно ГОСТ 6996-66 механические свойства сварных соединений определяют при следующих видах испытаний: а) испытании металла различных участков сварного соединения и наплавленного металла на статическое (кратковременное) растяжение; б) испытании металла различных участков сварного соединения и наплавленного металла на ударный изгиб (на надрезанных образцах); в) испытании металла различных участков сварного соединения на стойкость против механического старения; г) измерении твердости металла различных участков сварного соединения и наплавленного металла; д) испытании сварного соединения на статическое растяжение; е) испытании сварного соединения на статический изгиб (загиб); ж) испытании сварного соединения на ударный разрыв.
|
|
Испытания проводятся при определении качества продукции и сварочных материалов, пригодности способов и режимов сварки, при установлении квалификации сварщиков и показателей свариваемости металлов и сплавов.
Виды испытаний и типы образцов предусматриваются в стандартах и технических условиях на продукцию. Допускается применять образцы и методы испытаний по международным стандартам ИСО 4136, ИСО 5173, ИСО 5177.
2.2. Отбор образцов
Образцы для испытаний отбирают из проб, вырезанных непосредственно из контролируемой конструкции или от специально сваренных для проведения испытаний контрольных соединений.
|
|
При выполнении контрольных соединений характер подготовки под сварку, марка и толщина основного металла, марки сварочных материалов, положение шва в пространстве, начальная температура основного металла, режим сварки и термической обработки должны полностью отвечать условиям изготовления контролируемого изделия или особому назначению испытания.
Для контрольных соединений, выполняемых дуговой, электрошлаковой и газовой сваркой из плоских элементов, ширина каждой свариваемой пластины, если нет иных указаний в стандартах или другой технической документации, должна быть не менее:
50 мм – при толщине металла до 4 мм;
70 мм " " " св. 4 до 10 мм;
100 мм " " " " 10 " 20 мм;
150 мм " " " " 20 " 50 мм;
200 мм " " " " 50 " 100 мм;
250 мм " " " " 100 мм.
Ширина контрольного соединения, выполненного из круглого или фасонного проката, должна быть не менее двух диаметров или ширин элементов.
Вырезку заготовок для образцов из проб и контрольных соединений рекомендуется выполнять на металлорежущих станках. Допускается вырезать заготовки на ножницах, штампах, кислородной, плазменной, анодно-механической и другими методами резки.
|
|
Правка контрольного соединения или пробы, отбираемой от контролируемой конструкции, не допускается. Разрешается править готовые образцы вне их рабочей части. При испытании сварных соединений из труб допустимость правки образцов оговаривается стандартами или другой технической документацией.
Если нет иных указаний в стандартах или другой технической документации, то стрела прогиба на длине 200 мм (рис. 1) не должна превышать 10% от толщины металла, но не более 4 мм.
Рис. 1. Стрела пригиба
Несовпадение плоскости листов h в стыковых соединениях (рис. 2) не должно превышать 15% от толщины листа, но не более 4 мм.
Рис. 2. Несовпадение плоскости листов
Термическую обработку, если она оговорена НТД, проводят до чистовой обработки образцов. Термической обработке могут подвергаться пробы, контрольные соединения или вырезанные из них заготовки для образцов. В случае нормализации или закалки термическая обработка заготовок для образцов не допускается.
|
|
2.3. Условия проведения испытаний и оценка их результатов
Если нет других указаний в стандартах или другой технической документации, то испытания на статическое (кратковременное) растяжение и статический изгиб проводят не менее чем на двух образцах; на ударный изгиб, на стойкость против механического старения и ударный разрыв - не менее чем на трех образцах; измерение твердости - не менее чем на четырех точках для каждого участка сварного соединения. Если размеры сварного соединения исключают возможность размещения четырех точек, то допускается уменьшить их количество в соответствии с реальными возможностями.
Результаты по всем видам испытаний определяют как среднее арифметическое результатов, полученных при испытании всех образцов. Если нет указаний в соответствующих стандартах или другой технической документации, то для всех видов испытаний, кроме испытаний на статический изгиб и измерения твердости, допускается снижение результатов испытаний для одного образца на 10% ниже нормативного требования, если средний арифметический результат отвечает нормативным требованиям. Допускаемое снижение результатов испытания образцов на статический изгиб и при измерении твердости должно оговариваться в соответствующих стандартах или другой технической документации. При испытании на ударный изгиб допускаемое снижение ниже нормативных требований устанавливается не более 5 Дж/см (0,5 кгс·м/см
).
Результаты испытаний считают неудовлетворительными, если не выполняются вышеуказанные требования или в изломе образца, или на его поверхности выявлены кристаллизационные или холодные трещины (кроме случаев, когда наличие трещин допускается соответствующей НТД). При неудовлетворительных результатах испытания повторяют на удвоенном количестве образцов. Если в изломе образца, результаты испытания которого считают неудовлетворительными, обнаружены дефекты основного металла или сварного соединения (кроме трещин), его исключают из оценки и заменяют одним новым образцом.
Общие результаты испытаний определяют по показаниям, полученным при повторных испытаниях. Результаты повторных испытаний являются окончательными.
2.4. Испытание металла различных участков сварного
соединения и наплавленного металла на статическое
(кратковременное) растяжение
При испытании металла на статическое (кратковременное) растяжение определяют следующие характеристики механических свойств:
- предел текучести физический , МПа (кгс/мм
) или предел текучести условный
, МПа (кгс/мм
);
- временное сопротивление , МПа (кгс/мм
);
- относительное удлинение после разрыва (на пятикратных образцах) , %;
- относительное сужение после разрыва, , %.
Испытания проводят для металла шва, металла различных участков зоны термического влияния наплавленного металла при всех видах сварки плавлением.
Форма и размеры образцов, применяемых для испытания, должны соответствовать рис. 3 или рис. 4. и табл. 1.
Допускается увеличение размера диаметра образца и его высоты.
Рис. 3. Образцы I, II, III типа
Рис. 4. Образцы IV, V типа
Таблица 1
Размеры образцов в мм
Тип образца | ![]() | ![]() | ![]() | ![]() | ![]() | ![]() | ![]() | ![]() | ![]() | ![]() |
I | 3±0,1 | - | 0,03 | 6 | 4 | 2 | 1 | 15 | 18 | 30 |
II | 6±0,1 | - | 0,03 | 12 | 10 | 2,5 | 1,5 | 30 | 36 | 61 |
III | 10±0,2 | - | 0,04 | 16 | 10 | 3 | 3 | 50 | 60 | 86 |
IV | 6±0,1 | 10 | 0,03 | М12 | 15 | 5 | 5 | 30 | 36 | 86 |
V | 10±0,2 | 12 | 0,04 | М16 | 15 | 5 | 5 | 50 | 60 | 110 |
Примечание. - допускаемая разность наибольшего и наименьшего диаметров на длине рабочей части образца.
Для испытаний, проводимых при нормальной или пониженной температуре, применяют образцы всех типов. При испытании при повышенной температуре применяют образцы типов IV и V.
Рабочее сечение образцов всех типов должно полностью состоять из металла испытуемого участка. В головках образца допускается наличие металла других участков сварного соединения.
При однопроходных швах образцы, вырезаемые из различных участков шва, имеют практически одинаковые механические свойства. При многопроходных швах характеристики механических свойств в различных участках шва различны. Место вырезки образцов из многопроходных швов оговаривается стандартами или другой технической документацией. При отсутствии специальных указаний образцы вырезают у поверхности шва.
Для испытаний стыковых сварных соединений выполненных из листовых материалов ГОСТом предусмотрены плоские образцы нескольких типов. При испытании определяют прочность наиболее слабого участка стыкового или нахлесточного соединения или прочность металла шва в стыковом соединении.
2.5. Испытания металла различных участков сварного
соединения и наплавленного металла на ударный изгиб
(на надрезанных образцах)
При испытании на ударный изгиб определяют ударную вязкость или работу удара, или процентное соотношение хрупкой и вязкой составляющих поверхности излома для металла шва, наплавленного металла, зоны сплавления и различных участков околошовной зоны при толщине основного металла 2 мм и более.
Ударную вязкость определяют в Дж/см (кгс·м/см
), если нет указаний в соответствующих стандартах или другой НТД.
Для испытания применяют образцы, форма, размер и качество поверхности которых соответствуют указанным на рис. 5 (образцы с U-образным надрезом) или рис. 6 (образцы с V-образным надрезом). Предпочтительными являются образцы с V-образным надрезом.
Условное обозначение ударной вязкости или работы удара включает: символ ударной вязкости (КС) или работы удара (К); вид надреза (концентратора) (U, V); температуру испытания (температуру 20 °С не проставляют); максимальную энергию удара маятника (максимальную энергию 300 Дж не проставляют); тип образца (типы образцов VI и IX не проставляют); место расположения надреза (Ш - шов, ЗС - зона сплавления, ЗТВ - зона термического влияния, t - расстояние от границы сплавления до оси надреза). Значение t оговаривают в стандартах или другой технической документации. При расположении надреза поперек металла шва, зоны сплавления или зоны термического влияния в конце обозначения ставят букву П.
a – толщина основного металла, мм
Рис. 5. Образцы с U-образным надрезом
a – толщина основного металла, мм
Рис. 6. Образцы с V-образным надрезом
Примеры условных обозначений:
– Ударная вязкость, определяемая на образце типа VII, при температуре 100 °С, при максимальной энергии удара маятника 150 Дж, с надрезом вида U, расположенным по зоне сплавления:
КСU 150 УПЗС.
– Ударная вязкость, определяемая на образце типа XI, при температуре минус 40 °С, при максимальной энергии удара маятника 50 Дж, с надрезом вида V, расположенным по зоне термического влияния на расстоянии (t мм) от границы сплавления до оси надреза:
КСV 50 XI ЗТВt.
– Ударная вязкость, определяемая на образце типа VI, при температуре 20 °С, при максимальной энергии удара маятника 300 Дж, с надрезом вида U, расположенным по металлу шва:
КСUШ.
– Ударная вязкость на образце типа IX, при температуре
20 °С, при максимальной энергии удара маятника 300 Дж, с надрезом вида V, расположенным поперек металла шва:
КСVШ П.
Образцы различных типов дают несравнимые между собой результаты испытаний. Для отдельных случаев могут быть экспериментально установлены частные переводные коэффициенты.
В зависимости от цели испытания надрез располагают по металлу шва, по зоне сплавления и в различных участках металла околошовной зоны на расстоянии t от границы сплавления. Место расположения надреза и расстояние t от границы сплавления до оси надреза оговаривают в НТД.
При однослойных швах образцы, вырезаемые из различных участков, имеют практически одинаковую ударную вязкость. При многослойных швах ударная вязкость металла различных участков отличается друг от друга. Место вырезки образцов оговаривается стандартами или другой технической документацией. При отсутствии таких указаний образцы вырезают у поверхности шва.
2.6. Испытания металла различных участков сварного
соединения на стойкость против механического старения
Стойкость против механического старения характеризуется изменением ударной вязкости металла, подвергнутого старению по сравнению с ударной вязкостью его в исходном состоянии. О стойкости металла против механического старения судят по выраженному в процентах отношению этих величин или по абсолютному (нормативному) значению ударной вязкости после старения. Испытания проводят для металла шва и различных участков металла околошовной зоны.
Заготовки подвергают искусственному старению по методике: деформация растяжением из расчета получения (10 ± 0,5)% остаточного удлинения в пределах расчетной длины , ограниченной кернами или рисками. Рекомендуется на поверхности образцов через каждые 10 мм наносить риски для проверки равномерности деформации по длине расчетной части.
После удлинения заготовку подвергают равномерному нагреву в течение 1 ч при температуре 250 °С (523 °К) с последующим охлаждением на воздухе. Из рабочей части заготовок отбирают образцы типа VI или IX, типа VII или X. Ось надреза должна совпадать с осью симметрии шва.
Предусмотренную данным пунктом методику старения применяют для сварных соединений из сталей. Методику старения для других металлов и сплавов, а также иную температуру нагрева или величину деформации для соединений из стали оговаривают стандартами или другой технической документацией.
2.7. Измерение твердости металла различных участков сварного соединения и наплавленного металла.
Твердость измеряют в поперечном сечении сварного соединения в соответствии с рис. 7, 8, 9. Твердость измеряют по Виккерсу (НV), Бринеллю (НВ) и по Роквеллу – шкалам A, B и C (HRA, HRB и HRC), отдавая предпочтение замеру по Виккерсу.
Рис. 7. Схема измерения твердости
Примечание. Линии измерения твердости во всех случаях, кроме позиции УП, проходят через все участки сварного соединения. C – от 2 до 4 мм, C1 – от 10 до 15 мм; a – толщина основного металла, мм; H - толщина углового шва, мм; q – подготовительный участок толщиной не менее пяти слоев; q1 – участок измерения твердости толщиной не менее шести слоев. Для угловых швов, имеющих вогнутую или выпуклую поверхность, величину C отсчитывают от места максимальной вогнутости или выпуклости.
Рис. 8. Схема измерения твердости в непосредственной близости от линии сплавления
При измерении твердости по Виккерсу нагрузка на индентор в зависимости от прочности металла участков сварного соединения и ширины зоны термического влияния должна составлять 98 Н (НV10) или 49Н (НV50). При наличии в стандартах или другой технической документации соответствующих указаний, измеряют твердость по Виккерсу. Нагрузка на индентор при таких замерах может меняться от 0,04 до 4,9 Н. Твердость по Бринеллю и Роквеллу измеряется в соответствии с действующими стандартами
Твердость определяют для соединений, полученных сваркой плавлением или давлением из сталей различных марок и других металлических конструкционных материалов толщиной не менее 1,5 мм.
При измерениях, выполняемых в непосредственной близости от границы сплавления, рекомендуется проводить 2–3 измерения в соответствии с рис. 8.
Твердость по Виккерсу измеряют на микрошлифах или образцах с полированной поверхностью, если очертания шва видны без травления. Шероховатость поверхности таких образцов должна быть от 0,40 до 0,63 мкм. Твердость по Бринеллю или Роквеллу измеряют на макрошлифах или на образцах с шлифованной поверхностью, если очертания шва видны без травления. Шероховатость поверхности таких образцов должна быть от 1,25 до 2,00 мкм. В образцах должна быть соблюдена параллельность рабочей и опорной поверхностей.
2.8. Испытание сварного соединения на статически изгиб
Испытания проводят для стыковых соединений. При испытании определяют способность соединения принимать заданный по размеру и форме изгиб. Эта способность характеризуется углом изгиба a (рис. 9), при котором в растянутой зоне образца образуется первая трещина, развивающаяся в процессе испытания. Если длина трещин, возникающих в процессе испытания в растянутой зоне образца, не превышает 20% его ширины, но не более
5 мм, то они не являются браковочным признаком. Определяют также место образования трещины или разрушения (по металлу шва, металлу околошовной зоны или основному металлу).
В зависимости от требований, установленных соответствующей НТД, испытания проводят до достижения нормируемого угла изгиба или угла изгиба, при котором образуется первая являющаяся браковочным признаком трещина, до параллельности или соприкосновения сторон образца. Угол изгиба при испытании до образования первой трещины замеряют в ненапряженном состоянии с погрешностью до ± 2°.
Рис. 9. Схема испытаний на угол загиба
Форма и размеры плоских образцов должны соответствовать указанным на рис. 10, 11, 12 и в табл. 2.
Толщина образцов типов XXVI, XXVII и XXVIII при толщине основного металла 50 мм должна равняться толщине основного металла. При толщине металла более 50 мм толщину образца устанавливают в НТД. Образцы типов ХХVIа, ХХVIIа и ХХVIIIа, толщина которых меньше толщины основного металла, допускается вырезать в различных участках поперечного сечения сварного соединения. К результатам испытания образцов разных типов устанавливают различные нормативные требования.
Выпуклость шва по обеим сторонам образца снимают механическим способом до уровня основного металла с шероховатостью до 6,3 мкм. В процессе удаления утолщения, если в НТД нет иных указаний, удаляют и подрезы основного металла.
Рис. 10. образцы типов XXVI, ХХVIа
Рис. 11. Образцы типов XXVII, ХХVIIа, XXVIII
Рис. 12. Образец типа XXVIIIа
Ось, расположенного поперек сварного шва образца, после окончательной обработки должна находиться на его середине.
Таблица 2
Размеры образцов на изгиб в мм
Тип образца | Толщина основного металла и образца a | Ширина образца b | Общая длина образца L | Длина рабочей части образца l | Номер чертежа |
XXVI | 5 | a+15 | 2,5D+80 | 0,33 L | 37 |
Св. 5 до 50 | a+20 | ||||
ХХVIа | До 25 | ![]() | Не более 250 | Не устанавливается | |
XXVII | До 50 | 1,5a, но не менее 10 | 2,5D+80 | 0,33 L | |
ХХVIIа | До 25 | Не менее 1,5a, но не менее 20 и не более 50 | Не более 250 | Не устанавливается | 38 |
XXVIII | До 10 | 20 | 3,0D+80 | 0,33 L | |
Св. 10 до 45 | 30 | ||||
ХХVIIIа | До 40 | 0,7a, но не более 15 | Не более 250 | Не устанавливается | 38а |
Примечания:
1. D – диаметр оправки; lш – максимальная ширина шва.
2. Общая длина образцов типов XXVI, XXVII и XXVIII принята равной не менее указанной величины.
Испытание образцов типов XXVI и ХХVIа проводят, как указано на рис. 13, типов ХХVIIа и XXVIII – на рис. 14, типа ХХVIIIа – на рис.15. Обязательным условием проведения испытаний является плавность возрастания нагрузки на образец. Испытания проводят со скоростью не более 15 мм/мин на испытательных машинах или прессах с использованием опорных роликов.
Диаметр оправки D может изменяться в зависимости от марки стали, толщины листов, способа термообработки и должен оговариваться в соответствующей НТД. При отсутствии специальных указаний диаметр оправки принимают равным двум толщинам основного металла.
Рис. 13. Схема испытаний образцов типов XXVI и ХХVIа
Рис. 14. Схема испытаний образцов типов ХХVIIа и XXVIII
Рис.15. Схема испытаний образцов типа ХХVIIIа
Если заданный угол изгиба превышает 150°, то, изгиб можно продолжать между двумя параллельными нажимными плитами.
Испытания стыковых соединений труб на изгиб при поперечном (круговом) расположении шва проводят на образцах со снятым с наружной стороны утолщением.
При диаметре трубы 20 мм применяют образцы в виде отрезков трубы.
При диаметре трубы св. 20 до 45 мм применяют образцы в виде отрезка труб или плоские (сегментные) образцы.
Испытание труб диаметром 60 мм и менее с поперечным (круговым) и продольным швами можно проводить на образцах, приведенных на рис. 16. Утолщение шва с наружной стороны трубы механическим путем снимают до уровня основного металла.
Рис.16. Образцы на изгиб (сплющивание) типа XXIX
Результаты испытания образцов типов XXIX определяют величиной b (рис. 17) при появлении на поверхности образца трещины. Если трещина не образуется, то испытание проводят до соприкосновения сторон.
Рис. 17. Схема испытания отрезков труб на изгиб (сплющивание)
Испытание проводят путем деформации образца под прессом сжимающей нагрузкой.
2.9. Испытания сварного соединения на ударный разрыв
Испытание на сопротивление ударному разрыву проводят для сварных стыковых соединений листов толщиной до 2 мм. Форма и размеры образца должны соответствовать рис. 18. При испытании материалов высокой прочности разрешается изменять конструкцию захватной части образца.
a – толщина основного металла в мм
Рис. 18. Образец для испытания на ударный разрыв (тип XXXI)
Испытание проводят на маятниковых копрах с приспособлением для закрепления плоских образцов. Удельную ударную работу определяют по формуле
,
где – работа удара, затраченная на разрыв образца, Дж (кгс·м);
– объем расчетной части образца, равный произведению толщины основного металла (
) на расчетную длину и ширину образца, см
(м
).
ПОРЯДОК ВЫПОЛНЕНИЯ РАБОТЫ
Работа выполняется в два этапа.
На первом изучаются теоретические положения, уясняются методы разрушающих испытаний, требования к образцам и условиям испытаний.
На втором этапе студент самостоятельно составляет отчет, в котором освящает требования определенного раздела настоящих методических указаний.
ОФОРМЛЕНИЕ ОТЧЕТА
Отчет по практическому занятию оформляется на листах формата А4 и должен содержать:
1. Название и цель занятия.
2. Изложение требований заданного студенту раздела настоящих методических указаний.
КОНТРОЛЬНЫЕ ВОПРОСЫ
1. При каких видах испытаний определяют механические свойства сварных соединений.
2. С какой целью проводятся механические испытания.
3. Какие сварные соединения называются контрольными.
4. При каких условиях разрешается правка образцов для механических испытаний.
5. В каких случаях допускается термическая обработка образцов.
6. Сколько образцов необходимо испытать на ударный разрыв.
7. В каких случаях результаты испытаний считаются неудовлетворительными.
8. Какие характеристики металла определяются при статическом растяжении.
9. Какие виды образцов предусмотрены для сварных соединений, выполненных из листов малой толщины.
10. Какие характеристики определяются при испытании на ударный изгиб.
11. Какие типы надрезов выполняют на образцах для испытания на ударный изгиб.
12. Укажите примеры условных обозначений ударной вязкости.
13. Опишите методику искусственного старения металла.
14. Каким образом определяют стойкость металла сварных соединений против механического старения.
15. Какими методами измеряют твердость сварных соединений, какому методу следует отдавать предпочтение и почему.
16. На каких образцах необходимо измерять твердость по Виккерсу.
17. Какие характеристики определяют при испытании сварных соединений на статический изгиб
18. На каких образцах проводят испытания труб диаметром менее 20мм на статический изгиб.
19. На каком оборудовании проводят испытания сварных соединений на ударный разрыв.
СПИСОК РЕКОМЕНДУЕМОЙ ЛИТЕРАТУРЫ
1. ГОСТ 6996-66. «Сварные соединения. Методы определения механических свойств» (с изменениями).
2. ИСО 4136-89 «Соединения стыковые стальные, выполненные сваркой плавлением. Испытания на растяжение образцов, вырезанных поперек шва».
3. ИСО 5173-81 «Соединения стыковые стальные, выполненные сваркой плавлением. Испытания на изгиб корнем шва или его лицевой поверхностью наружу образцов, вырезанных поперек шва».
4. ИСО 5177-81 «Соединения стыковые стальные, выполненные сваркой плавлением. Испытание на боковой изгиб образцов, вырезанных поперек шва».
5. Металловедение и термическая обработка стали: Справ., изд. 3-е изд., перераб. и доп. В 3-х т. Т. 1. Методы испытаний и исследования / Под ред. Бернштейна М. Л., Рахштадта А. Г. – М. : Металлургия, 1993. – 352 с.
6. Иванова В. С. Разрушение металлов. Серия «Достижения отечественного металловедения. – М. : Металлургия, 1999. –
168 с.
7. Справочник по сварке / А. В. Смирнова, Г. А. Кокорин, С. М. Полонская. – М. : Металлургия, 1985. – 192 с.
Составитель
Смирнов Александр Николаевич
РАЗРУШАЮЩИЕ МЕТОДЫ ИСПЫТАНИЙ КОНТРОЛЯ
КАЧЕСТВА СВАРНЫХ СОЕДИНЕНИЙ
Методические указания к практическому занятию по курсам
«Методы контроля качества сварных соединений» для студентов
специальности 150202(120500) «Оборудование и технология сварочного производства»
Рецензент Князьков В.Л.
Печатается в авторской редакции
Подписано в печать . Формат 60´84/16.
Бумага офсетная. Отпечатано на ризографе.
Уч.-изд. л. 1,5. Тираж 36 экз. Заказ
ГУ КузГТУ. 650026, Кемерово, ул. Весенняя, 28.
Типография ГУ КузГТУ. 650099, Кемерово, ул. Д. Бедного, 4 «А».
Дата добавления: 2018-02-28; просмотров: 314; Мы поможем в написании вашей работы! |
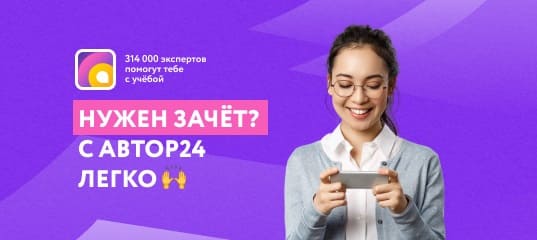
Мы поможем в написании ваших работ!