Требования технологичности изделия при сборке, эксплуатаций и ремонте.
Основные требования технологичности сборки:
1. создание возможности независимой сборки сборочных единиц, а также независимо друг от друга и одновременного монтажа их на базовую деталь изделия;
2. обеспечение возможности сборки без пригоночных работ и без совместной механической обработки собираемых деталей;
3. стремление к уменьшению количества наименований деталей и уменьшению их общего количества;
4. обеспечение высокого уровня взаимозаменяемости, стандартизаций, унификаций и нормализаций сборочных единиц и деталей;
5. наличие удобных сборочных баз; для достижения точности взаиморасположения необходимо совмещать сборочные и измерительные базы; совмещение установочных, технологических и измерительных баз обеспечивает высокую точность обработки, а совмещение со сборочными базами обеспечивает более высокую точность сборки;
6. обеспечение сборки без сложных приспособлений предпочтительно с одной стороны путем осуществления простых движений;
7. исключение необходимости разборок и регулировок;
8. обеспечение возможности удобного и свободного подвода высокопроизводительного механизированного инструмента к местам соединения деталей и возможности транспортировки;
9. предусмотреть применение несложных приспособлений, простых инструментов при обслуживаний и ремонте.
Требования технологичности при обслуживаний и ремонте:
1. характеристика условий эксплуатаций и ремонта;
|
|
2. условия выполнения работ по технологическому обслуживанию и ремонту, в том числе квалификация и состав персонала эксплуатирующего и ремонтирующего изделия;
3. система материально – технического обеспечения, эксплуатаций и ремонта;
4. средняя трудоемкость ремонта и технического обслуживания
5. ограничение номенклатуры специального инструмента и приспособлений при техническом обслуживаний и ремонте;
6. ограничение типоразмеров крепежных деталей;
7. широкое использование стандартизованных и унифицированных частей изделия;
8. требования к рациональным методам и средствам контроля технического состояния изделия в процессе эксплуатаций и ремонта;
9. требования к допустимости, легкосъемности и взаимозаменяемости деталей, сборочных единиц при техническом обслуживаний и ремонте;
10. требования к выполнению регулировочно – доводочных работ при техническом обслуживаний и ремонте;
11. требования к конструкций изнашивающихся деталей в смысле приспособленности к восстановлению с применение прогрессивной технологий восстановительных работ.
32) Погрешности, связанные с упругими и тепловыми деформациями технологическ системы.
Технологическая система (станок, приспособление, инструмент, деталь) представляет собой упругую систему, в которой влияние сил резания и закрепления, инерционных и других сил приводит к образованию погрешностей форм и размеров обрабатываемых деталей.
|
|
2схемы обработки цилиндрической детали: с закреплением в центрах и в трехкулачковом токарном патроне, которые иллюстрируют возникающие упругие деформации
, а также обусловленные ими погрешности формы детали (бочкообразность и конусообразность).
Упругие деформации обусловлены отжатиями основных узлов и отдельных элементов технологической системы, а также контактными деформациями и в общем случае могут достигать 20…40% от суммарной погрешности обработки.
Нестабильность сил резания из-за колебаний снимаемого припуска, твердости материала, различная жесткость детали при обработке - обуславливают неравномерность упругих деформаций.
Для количественной оценки упругих деформаций технологической системы используют понятия жесткость и податливость.
Жесткостью систем ы называется способность системы оказывать сопротивление деформирующим силам.
жесткость технологической системы определяется как отношение составляющей силы резания, направленной по нормали к обрабатываемой поверхности, к смещению режущей кромки инструмента относительно обрабатываемой поверхности заготовки в том же направлении:
где jсист - жесткость технологической системы, Н/мм;
РУ - радиальная составляющая силы резания, Н; У - упругие деформации технологической системы (смещение режущей кромки инструмента), мм.
Для удобства расчетов часто используется величина обратная жесткости, которая называется податливостью.
Жесткость новых станков токарной группы составляет Jст = 20000 - 40000 Н/мм, для некоторых типов станков Jст = 100000 Н/мм (шлифовальные и координатно-расточные станки).
Таким образом, погрешности от упругих деформаций зависят, и определяется жесткостью технологической системы СПИД.
где, l - длина заготовки, мм;
E - модуль упругости 1-го рода, H/мм2;
J - момент инерции поперечного сечения заготовки, мм2 (для круглых заготовок J = 0,05d4);
d - номинальный диаметр детали, мм.
Тогда жесткость заготовки будет равна:
Погрешности от тепловых деформаций системы
Источниками тепловыделения в технологической системе являются:
" трение стружки о переднюю поверхность режущего инструмента;
" трение задней поверхности режущего инструмента по обработанной поверхности детали;
" потери на трение в подвижных механизмах станка (подшипниках, зубчатых передачах и т.п.),
" тепловыделение из зоны резания.
Весь расчет чаще всего сводится к определению тепловых деформаций инструмента.
Выделяющееся в зоне резания тепло частично уносится с СОЖ, частично рассеивается в окружающем пространстве, а также передается заготовке, режущему инструменту и станку. Это приводит к разогреву станка, заготовки и режущего инструмента и нарушению взаимного положения заготовки и режущей кромки инструмента.
Наибольшее влияние на точность механической обработки оказывают тепловые деформации режущего инструмента и обрабатываемой заготовки; влиянием остальных составляющих, как правило, можно пренебречь.
Тепловые деформации обрабатываемой заготовки (детали) ТД зависят от количества теплоты, поступающей в заготовку из зоны резания, массы и удельной теплоемкости материала заготовки. Количественно они могут быть определены по зависимости.
где α - температурный коэффициент линейного расширения материала заготовки;
d - диаметр обрабатываемой заготовки, мм;
- соответственно исходная и текущая (в i-й момент времени) температура детали.
Тепловые деформации инструмента ТИ, приводят к удлинению державки, а следовательно, к смещению режущих кромок и изменению размеров обрабатываемых заготовок, т.е. образованию погрешности обработки.
Тепловое равновесие (при котором прекращается удлинение резцов) наступает примерно через 12...24 минут непрерывной работы, а общее тепловое равновесие всей технологической системы наступает примерно через 2-3 часа работы.
Практически же в условиях производства неизбежны перерывы в работе, поэтому с учетом перерывов станок и инструмент успевают охладиться
Для снижения влияния тепловых деформаций инструмента и обрабатываемой детали
на точность механической обработки применяют: различные смазочно-охлаждающие жидкости.
Погрешности обработки, вызванные тепловыми деформациями могут достигать 30...40% от суммарной погрешности обработки.
При обработке среднеуглеродистых сталей диаметром до 50 мм, их температурные деформации могут достигать 20-25 мкм.
|
|
|
|
Дата добавления: 2015-12-21; просмотров: 16; Мы поможем в написании вашей работы! |
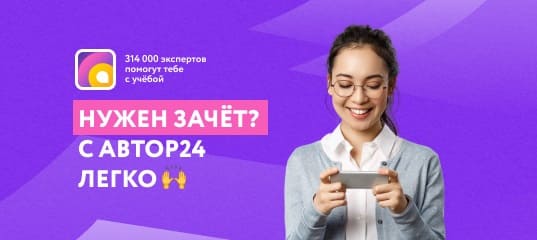
Мы поможем в написании ваших работ!