Конструкции грохотов
1.4.1. Грохоты неподвижного типа
Неподвижные колосниковые грохоты представляют собой колосниковые решетки, устанавливаемые под углом 25–30о при грохочении углей и до 40–45о при грохочении нерудных строительных материалов, различных руд. Ширина грохота обычно равна двум – трем размерам максимального куска горной породы, а длина – удвоенной ширине грохота. Схема такого грохота представлена на рис. 1.2, а.
Рис. 1.2. Устройство и принцип действия:
а – колосниковой решетки; б – дугового (криволинейного) грохота
Площадь решетки колосникового грохота определяется по формуле
м2, (1.4)
где Q исх – часовая нагрузка на грохот по исходному сырью, м3/ч;
γн – насыпная плотность исходного сырья, т/м3;
а – ширина щели между колосниками, м.
Исходный материал загружается на верхнюю часть решетки и движется вниз самотеком. При этом нижние классы в основном проваливаются через зазоры между колосниками. Для увеличения производительности и эффективности грохочения, особенно глинистых и влажных материалов, применяют решетки с консольно-закрепленными колосниками, вибрирующими при движении материала, что обеспечивает самоочистку просеивающей поверхности.
Преимуществами колосниковых грохотов являются простота устройства и обслуживания, отсутствие энергозатрат, возможность изготовления на предприятиях из старых рельсов, балок и т.п., возможность загрузки непосредственно из автомашин, железнодорожных вагонов, шахтных скипов.
|
|
Недостатком их является низкая эффективность грохочения, обычно не превышающая 50–70 %. Поэтому неподвижные колосниковые грохоты обычно используют для выделения наиболее крупных кусков и в тех случаях, когда низкая эффективность грохочения (например, перед первой стадией дробления) не оказывает существенного влияния на последующий процесс переработки полезного ископаемого (рис. 1.2, б).
Дуговые (криволинейные) грохоты предназначены как для мокрого грохочения тонкого и мелкого материала крупностью от 0,1 до 3 мм, так и обезвоживания материала. Рабочее сито представляет собой часть цилиндрической поверхности радиусом 500–1200 мм с центральным углом 90–270 о. Сито щелевое набирается из проволок нержавеющей стали трапециевидного сечения. У классификационных дуговых сит щели между проволоками расположены поперек набегающего потока пульпы, а у обезвоживающих сит – вдоль потока. Пульпа подается на сито в верхнем конце тангенциально и подвергается воздействию центробежной силы инерции и силы тяжести. Возникающая при этом центробежная сила способствует эффективному выделению воды и мелкого продукта через щелевые отверстия сита, которые при обезвоживании продукта располагаются вдоль, а при грохочении – поперек потока пульпы. В последнем случае крупность частиц подрешетного продукта класса – 0,5 мм примерно в 2,5 раза меньше ширины щелей сита.
|
|
На дуговые сита можно подавать пульпу с разным содержанием твердого (от 7 до 70 % твердого по массе). Эффективность грохочения зависит от характеристики крупности исходного материала, размера щели сит, разжижения пульпы и др. Эффективность грохочения (извлечения) по самым мелким классам прямо пропорциональна извлечению воды в нижний продукт. На практике эффективность грохочения по классу номинальной крупности следующая: на ситах со щелью 1 мм – 90 %, 0,7–0,3 мм – 70 %.
Производительность дугового сита по исходной пульпе пропорциональна площади живого сечения сита и скорости подачи пульпы
Q = c.F ж. с. .v м3/ч, (1.5)
где с – коэффициент пропорциональности, равный 160–200;
F ж.с– площадь живого сечения сита, м2 (для щелевых сит F ж.с = 0,3–0,4);
v – скорость подачи пульпы, м/с, v = 3–8 м/с.
Удельная объемная производительность по исходной пульпе на 1 м2 общей рабочей площади сита составляет 150–200 м3/ч.
Дуговые сита применяют на рудных обогатительных фабриках для классификации в цикле измельчения (например, калийных солей), обесшламливания и классификации шлама, обезвоживания и других целей.
|
|
Конический и цилиндрический грохоты (рис. 1.3) представляют собой конструкцию, состоящую из соответствующего внешнего корпуса, внутри которого соосно вмонтирована решетка из щелевидных сит с размером щели 0,5–2 мм. Пульпа подводится под напором по касательной к верхней конической или цилиндрической части внутрь решетки.
Под действием центробежной силы поток получает вращательное движение и по спирали опускается в низ конической части, где и разгружается в качестве надрешетного, более крупного, продукта. Нижний, более мелкий, продукт проходит через щели решетки во внешний кожух вместе с основной массой воды и выходит через нижний выгружной патрубок.
Такие грохоты чаще всего применяются для предварительного обезвоживания мелких концентратов и удаления из них шламов. При добыче песчано-гравийной смеси гидромеханизированным способом пульпу (гидросмесь) направляют в конический грохот для разделения гравия и песка.
Рис. 1.3. Устройство и принцип действия конического грохота
1.4.2. Подвижные вибрационные грохоты механического типа
|
|
Плоские качающиеся грохоты (рис. 1.4) устанавливаются под углом 8–12о к горизонту на упругих опорах или подвешиваются на специальных упругих подвесках и приводятся в возвратно-поступательное движение от кривошипно-шатунного механизма.
Рис. 1.4. Схема плоского качающегося грохота:
1 – эксцентриковый приводной механизм; 2 – короб с ситом; 3 – подвеска
При этом величина хода и траектория движения короба не зависят от загрузки грохота. Исходный материал крупностью до 350 мм (оптимальная крупность 40–50 мм) загружается в верхнюю часть короба и за счет сил инерции перемещается к его разгрузочному концу. Плоские качающиеся грохоты работают обычно на режиме с подбрасыванием материала, который является весьма эффективным.
Недостатком плоских качающихся грохотов является их неуравновешенность. При качаниях короба грохота, имеющего большую массу, возникают значительные силы инерции, которые передаются на элементы привода и опорные конструкции.
Гирационные (полувибрационные) грохоты (рис. 1.5) в подвесном и опорном исполнении характеризуются круговыми движениями короба с ситом в вертикальной плоскости, вызываемыми эксцентриковым валом. Грохот состоит из неподвижной сварной рамы 1, подвижного короба с ситами 2, эксцентрикового вибровозбудителя 3 и привода 4. Короб пружинами 6 удерживается в заданном положении. Ось вибровозбудителя проходит через центр тяжести короба. В его загрузочной части имеется приемный лоток. Сито грохота, устанавливаемого наклонно под углом 20–30о к горизонту, остается параллельным самому себе в течение всего оборота вала. В результате такого движения короба материал на сите встряхивается, разрыхляется и продвигается вниз по уклону сита, подвергаясь рассеву.
Рис. 1.5. Схема гирационного (полувибрационного) грохота:
1 – сварная рама; 2 – короб с ситом; 3 – эксцентриковый вал; 4 – привод
(клиноременная передача); 5 – подшипники; 6 – амортизаторы (пружины);
7 – диски; 8 – дебалансы
При движении короба грохота по круговой траектории возникает центробежная сила
(1.6)
так как
где М – масса движущегося короба с грохотимым материалом;
v – окружная скорость эксцентрикового вала;
е – эксцентриситет эксцентрикового вала;
n – частота вращения вала, мин-1.
Переменная по направлению радиальная центробежная сила инерции, передаваемая на подшипники вала и на неподвижную раму грохота, могла бы вызывать колебания опорных конструкций и неблагоприятные условия работы подшипников. Для уравновешивания этой силы на валу закрепляются два диска 7 с дополнительными грузами (дебалансами) 8. Радиус r вращения (установки) центра тяжести грузов и их массу m подбирают таким образом, чтобы соблюдалось равенство
, (1.7)
где m – масса одного неуравновешенного груза.
Соблюдение указанного равенства обеспечивает эффективность процесса грохочения и стабильность работы подшипниковых узлов.
Гирационные грохоты изготовляются различных конструкций и размеров, легкого, среднего и тяжелого типов. Эксцентриситет вала грохота 1,5–6 мм, частота вращения вала 750–1000 мин-1. Эти грохоты находят применение для грохочения крупнокускового материала (до 400 мм) на решетах с отверстиями до 150–200 мм, но могут быть использованы для грохочения среднего по крупности и мелкого материала.
Преимуществом гирационных грохотов является стабильность колебательных режимов, не зависящих от массы материала на сите. Ударные нагрузки от загружаемого материала полностью воспринимают подшипники эксцентрикового вала и могут быть применены для весьма тяжелых условий работы. К недостаткам применяемых в нерудной промышленности гирационных грохотов следует отнести сложность ремонта и обслуживания, значительную массу.
Инерционные грохоты с простым дебалансным вибратором (рис. 1.6) совершают эллиптические колебания короба под действием неуравновешенных масс дебалансов, устанавливаемых на валу. Короб грохота 1 с ситом 2 подвешивается или устанавливается на пружинах (рессорах) 3 под углом 15–30о к горизонту. На коробе грохота установлены два подшипника 4, в которых установлен вал 5 с закрепленными на нем дисками 6, имеющими неуравновешенные грузы – дебалансы 7. Вал приводится во вращение от электродвигателя, установленного на неподвижной опоре, при помощи клиноременной передачи 8.
Рис. 1.6. Схема инерционного грохота с простым дебалансным вибратором:
1 – короб; 2 – сито; 3 – пружины (рессоры); 4 – подшипники; 5 – вал; 6 – диски;
7 – дебалансы; 8 – привод
Дебаланс при вращении развивает радиально направленную вращающуюся центробежную силу инерции
(1.8)
которая заставляет короб грохота описывать эллиптическую траекторию.
Условие равновесия для данного грохота:
Ма = 2mr, (1.9)
где М – полная масса короба с нагрузкой;
а – амплитуда колебаний короба грохота (радиус круговых качаний).
Как видно из уравнения (1.9), амплитуду колебаний короба можно регулировать изменением массы дебалансных грузов или радиуса их вращения r. В то же время, при перегрузке грохота (увеличение М) амплитуда колебаний грохота будет уменьшаться и эффективность грохочения ухудшается. В этом состоит главный недостаток таких грохотов.
Инерционные грохоты с простым дебалансным вибратором применяются преимущественно для мелкого грохочения (на ситах 2–6 мм). Частота колебаний при грохочении мелкого материала 1000 мин-1, диаметр круговой траектории 5–7 мм, наиболее частый угол наклона 15о. Привод вала вибратора выполняется с учетом того, что осью вала описывается круговая траектория вместе с коробом. Поэтому электродвигатель через клиноременную передачу вращает промежуточный вал, соединенный карданным валом с валом вибратора.
В инерционных самоцентрирующихся грохотах (рис. 1.7) в отличие от грохотов с простым дебалансом, используется вал с эксцентриковыми заточками, диаметрально противоположно которым расположены делабансные грузы маховиков, уравновешивающие центробежную силу инерции, короба с нагрузкой при вращении вала: короб грохота 1 наклонно подвешивается к неподвижным поддерживающим конструкциям при помощи пружин 2.
Рис. 1.7. Схема инерционного самоцентрирующегося грохота:
1 - короб с ситом; 2 - пружины; 3 - подшипники; 4 - эксцентриковый вал;
5 - маховики; 6 - дебалансы; 7 - шкив клиноременной передачи;
8 – электродвигатель
В подшипниках 3, жестко укрепленных в коробе, смонтирован вал с эксцентриковыми заточками 4. На концах вала насажены маховики 5 с дебалансными грузами 6. На валу также укреплен шкив 7, приводимый во вращение клиноременной передачей от электродвигателя, установленного на неподвижной опоре 8.
Круговые качания короба обусловлены взаимодействием двух вращающихся масс: одна из них представлена коробом грохота, подвешенным на пружинах; другая – дебалансными грузами, укрепленными на валу, вращающемся в подшипниках, соединенных с коробом. Дебалансные грузы подбираются такими, чтобы их центробежная сила инерции уравновешивала центробежную силу, развиваемую коробом грохота при вращении на радиусе, равном эксцентриситету, т.е.
Me = 2mr, (1.10)
где М – полная масса короба с нагрузкой;
e – эксцентриситет вала;
m – масса одного дебалансного груза;
r – расстояние от центра массы дебалансных грузов до оси вращения.
В этом случае короб описывает круговые движения вокруг теоретической оси О - О, совпадающей с осью приводного шкива, которая в процессе работы остается неподвижной в пространстве. Отсюда грохотам с таким приводом дано название «самоцентрирующиеся».
Незначительные отклонения от «равновесной», т.е. условия Me = 2mr, массы дебалансных грузов или массы короба с нагрузкой вызывают дополнительные круговые движения центра вала малого радиуса, которые не оказывают влияния на работу гибкой передачи от электродвигателя и сам процесс грохочения. Поэтому считается, что самоцентрирующиеся грохоты не нуждаются в тщательном подборе дебалансных грузов и это является их существенным преимуществом перед традиционными грохотами, в которых тщательная балансировка дебалансов обязательна.
Инерционные грохоты широко применяют на всех стадиях грохочения. Производят инерционные грохоты тяжелого, среднего и легкого типов. На грохотах тяжелого типа возможен рассев руды и материалов плотностью до 2500 кг/м3 и крупностью до 1300 мм, на грохотах среднего типа – плотностью до 1600 кг/м3 с фракциями до 150–300 мм, легкого типа – плотностью 1000 кг/м3 и крупностью до 100–200 мм.
Широкое распространение самоцентрирующихся инерционных грохотов обусловлено простотой конструкции, легкостью регулировки, широкой номенклатурой. Ударные нагрузки поступающих на сито кусков материала в значительной степени демпфируются упругими опорами короба. В качестве упругих опор применяют спиральные пружины или пневмобаллоны.
В самобалансных грохотах (рис. 1.8) подвесного или опорного исполнения в качестве приводного механизма используется самобалансный вибратор, устанавливаемый под ситом грохота. Вибратор 4 состоит из двух одинаковых дебалансов 5, вращающихся на параллельных валах в противоположные стороны с одинаковой скоростью. Вибратор смонтирован на опорной раме 3, укрепленной на коробе 1 под углом 35–55о к плоскости сита. При любом положении дебалансных грузов вибратора часть центробежных сил инерции, действующих вдоль оси У, взаимно уравновешивается, а другая часть действует вдоль оси, расположенной, как указывалось, под углом 35–55о к плоскости сита, создавая прямолинейные колебания сита и обеспечивая движение материала на сите с подбрасыванием и энергичным встряхиванием.
Рис. 1.8. Схема вибрационного грохота с самобалансным вибратором:
1 – короб с ситом; 2 – пружины; 3 – опорная рама; 4 – вибратор; 5 – дебалансы
Самобалансные грохоты применяются для грохочения различных руд, углей, нерудных строительных материалов крупностью до 100 мм с амплитудой колебаний сит 8,5–10 мм при частоте 750 мин-1. Кроме того, используют для грохочения влажных и глинистых материалов, операций мокрой классификации, отделения суспензии от продуктов разделения.
Самобалансные грохоты имеют малые габаритные размеры по высоте, сравнительно небольшую металлоемкость, они просты и надежны в эксплуатации, отличаются эффективным режимом грохочения.
Недостатком самобалансного вибратора является его сложность – четыре подшипника для двух валов, пара зубчатых колес, герметичный корпус с масляной ванной.
Резонансные грохоты (рис. 1.9) состоят из двух колеблющихся масс: горизонтального короба с ситами 1 и подвижной рамы 2, удерживаемых и связанных между собой пружинами и амортизаторами.
Рис. 1.9. Схема резонансного грохота:
1 – горизонтальный короб с ситами; 2 – подвижная рама;
3 – пружины и амортизаторы; 4 – упругий приводной механизм
В этих грохотах используется явление резонанса для приведения в колебательное движение массивных коробов и уравновешивания возникающих при этом сил инерции с помощью колеблющейся рамы. Короб получает колебания от упругого приводного механизма, укрепленного на раме. Колебания короба и рамы происходят благодаря чередующимся преобразованиям их кинетической энергии в потенциальную энергию упругих связей, и наоборот. Короб и рама имеют одинаковую частоту колебаний, противоположных по направлению, что обеспечивает уравновешивание их масс.
Амплитуда колебаний короба и рамы, работающих в резонансном режиме, зависит от их масс. Для снижения динамических нагрузок на фундамент уменьшают амплитуду качаний рамы путем увеличения ее массы в 2,5–3 раза по сравнению с массой короба в соответствии со следующим условием:
m 1 a 1 = -m 2 a 2, (1.11)
где m 1 и m 2– массы короба и рамы;
а 1 и а 2 – амплитуды их качаний.
Массы короба и рамы подбирают таким образом, чтобы система работала в резонансном режиме, обеспечивающем минимальный расход энергии. При режимах работы близких к резонансному в результате полного уравновешивания сил инерции удается ликвидировать действие сил на привод. Благодаря этому размеры короба могут быть значительными, что позволяет увеличить производительность грохота и повысить эффективность грохочения.
Достоинствами резонансных грохотов являются их динамическая уравновешенность, большая просеивающая поверхность и производительность, высокая эффективность; недостатки – сложность конструкции (много шарниров, пружин, резиновых упругих элементов), наладки, регулировки, большая металлоемкость. Они применяются для грохочения и обезвоживания различных материалов.
Дата добавления: 2015-12-19; просмотров: 44; Мы поможем в написании вашей работы! |
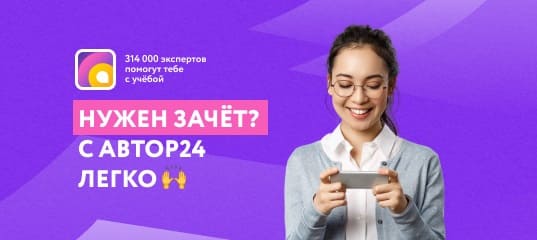
Мы поможем в написании ваших работ!