Коэффициент использования станка по мощности
KN = ,
где KN – коэффициент использования станка по мощности; Np – мощность
резания, кВт, Np = 2,56 кВт; Nст– мощность главного привода станка, кВт, Nст= 7,5 кВт; η – КПД станка.
KN = =0,43
Чем ближе KN к 1, тем более полно используется мощность станка. В
нашем случае коэффициент использования станка по мощности не достаточно
высок.
ПРИЛОЖЕНИЯ
Таблица 1П. Отличительные признаки резцов
Таблица 2П. Выбор типовых марок твердого сплава
Таблица 3П. Размеры проходных отогнутых резцов с пластинкой из твердого сплава
Примечание. В таблице приведены выдержки из ГОСТ 18877-73 для токарных проходных отогнутых резцов общего назначения с углом врезки пластинки 0º и углами в плане φ = φ1 =45º.
Таблица 4П. Формы передней поверхности
Таблица 5П. Углы режущей части резцов
Таблица 6П. Значения углов φ и φ1
Таблица 7П. Геометрические параметры режущей части резца с неперетачиваемыми пластинками
Таблица 8П. Припуски на обработку наружных цилиндрических поверхностей
Примечание: 1. При обработке детали с уступами припуск выбирают по отношению к общей длине детали.
2. Припуски на чистовое обтачивание даны при условии, что заготовка
подвергается черновому обтачиванию.
Таблица 9П. Подачи при чистовом точении
Примечания: 1. Подачи даны для обработки сталей с σв = 700-900 МПа и чугунов; для сталей с σв =500-900 МПа значения подач умножать на коэффициент Кs = 0,45; для сталей с σв = 900-1000 МПа значения подач умножать на коэффициент Кs =/,25.
|
|
2. При обработке стали со скоростью V > 50 м/мин подачу увеличивать, вводя поправочный коэффициент 1,25.
3 Радиус при вершине резца ориентировочно равен: 0,4-0,8 для резцов сечением до 12 х20ми; 1,2 1,6 мм для резцов сечением до 30x30 мм; 2,0-2,4 мм – для резцов сечением 30х45 мм и более.
Таблица 10П Подачи при черновом наружном точении резцами с пластинками из твердого става
и из быстрорежущей стали
Примечания: 1. Нижние значения подач соответствуют меньшим размерам державки резца и более прочным обрабатываемым
материалам, верхние, значения подач – большим размерам и державки резца и менее прочным обрабатываемым материалам.
2. При обработке жаропрочных сталей и сплавов подачи свыше 1 мм/об не применять.
3 При обработке прерывистых поверхностей и на работах с ударами табличные значения подач следует умножать на коэффициент
0,75-0,85.
4. При обработке закаленных сталей табличные значения подачи уменьшать, умножая на коэффициент 0,8 для стали с HRC 44-56 и на 0,5
для стали с HRC 57-62.
Таблица 11П. Значения коэффициента и показателей степени в формулах
скорости резания
* без охлаждения; ** с охлаждением.
|
|
Примечания:
1. При внутренней обработке (растачивание, прорезавши канавок в
отверстии, внутреннем фасонном точении) принимается соответствующая скорость
резания для наружной обработки с введением поправочного коэффициента 0,9.
2. При обработке без охлаждения конструкционных и жаропрочных сталей и стального
литья всеми видами резцов из быстрорежущей стали вводить на скорость резания
поправочный коэффициент 0,8. При отрезании и прорезании с охлаждением резцами T5K10 конструкционных сталей и стального литья вводить на скорость резания поправочный коэффициент 1,4.
3.При обработке резцами из быстрорежущей стали термообработанных сталей скорость резания для соответствующей стали уменьшить, вводя поправочный коэффициент: 0,95 – при нормализации; 0.9 – при отжиге; 0,8 – при улучшении.
Таблица 12П. Поправочный коэффициент Kμv, учитывающий влияние физико-механических, свойств обрабатываемого материала на скорость резания
Примечания: 1. σв и НВ – фактические параметры, характеризующие обрабатываемый материал, для которого рассчитывается скорость резания.
2. Коэффициент Kr и показатель степени nv см. в табл. 13.
Таблица 13П. Значение коэффициента Kr и показатели степени nv в формуле для расчета
|
|
коэффициента обрабатываемости Kμv
Таблица 14П. Поправочный коэффициент Knv учитывающий влияние состояния поверхности заготовки на скорость резания
Таблица 15П. Поправочный коэффициент Kuv, учитывающий влияние инструментального
материала на скорость резания
Таблица 16П. Поправочные коэффициенты, учитывающие влияние
параметров резца на скорость резания
Таблица 17П. Поправочный коэффициент Kоv, учитывающий влияние
вида обработки на скорость резания
Таблица 18П. Значения коэффициента и показателей степени в формулах составляющих силы резания при точении
Таблица 19П. Поправочный коэффициент Кμр., для стали и чугуна, учитывающий влияние качества обрабатываемого материала на силовые зависимости
Таблица 20П. Величины силы резания Рz, допускаемые прочностью пластинок твердого сплава
Таблица 21П. Поправочные коэффициенты, учитывающие влияние геометрических
параметров режущей части инструмента на составляющие силы резания при обработке
стали и чугуна
Таблица 22П. Вспомогательное время на установку, выверку и снятие детали
Таблица 23П. Вспомогательное время на рабочий ход
|
|
Таблица 24П. Вспомогательное время на измерения
Таблица 25П. Подготовительно-заключительное время
ПАСПОРТНЫЕ ДАННЫЕ ТОКАРНЫХ СТАНКОВ
Частота вращения шпинделя, об/мин, в числителе и наибольший допустимый момент на
шпинделе, Нм, в знаменателе
Мощность электродвигателя главного движения, КПД станка, значения продольных
и поперечных подач, а также значения допустимых усилий подач токарных станков.
Модели станков:
А62, 1А62Б, 1А62Г
Мощность электродвигателя главного движения Nэ = 7 кВт; КПД станка η = 0,75.
Продольные подачи: 0,082; 0,088; 0,10; 0,11; 0,12; 0,13; 0,14; 0,15; 0,16; 0,18; 0,20;
0,23; 0,24; 0,25; 0,28; 0,30; 0,33; 0,35; 0,40; 0,45; 0,48; 0,50; 0,55; 0,60; 0,65; 0,71; 0,80; 0,91;
0,96; 1,00; 1,11; 1,21; 1,28; 1,46;1,59.
Поперечные подачи станка: 0,027; 0,029; 0,033; 0,038 0,040; 0,042; 0,046; 0,050; 0,054;
0,058; 0,067; 0,075; 0,079; 0 084; 0,092; 0,10; 0,11; 0,12; 0,13; 0.15; 0,16; 0,17; 0,18; 0,20; 0,22;
0,23; 0,27; 0,30; 0,32; 0,33;'0,37; 0,40; 0,41; 0,48; 0,52.
В62Г
Мощность электродвигателя главного движения Nэ = 7,5 кВт; КПД станка η = 0,786.
Продольные подачи станка; 0,05; 0,06; 0,075; 0,09; 0,1; 0,125; 0,15; 0,175; 0,2; 0,25; 0,3;
0,35; 0,4; 0,5; 0,6; 0,7; 0,8; 1,0; 1,2; 1,4; 1,6; 2,0; 2,4; 2,8.
Поперечные подачи станка 1/2 от Sпрод., т.е. 0,025-1,4.
Наибольшее усилие, допускаемое механизмом продольной подачи - 7500 Н,
поперечной подачи - 2600 Н.
К62
Мощность электродвигателя главного движения Nэ = 10 кВт; КПД станка η = 0,8.
Продольные подачи станка: 0,070; 0,074; 0,084; 0,097; 0,11; 0,12; 0,13; 0,14; 0,15; 0,17;
0,195; 0,21; 0,23; 0,26; 0;28; 0,30; 0,34; 0,39; 0,43; 0,47; 0,52; 0,57; 0,61; 0,70; 0,78; 0,87; 0,95;
1,04; 1,14; 1,21'; 1,4; 1,56; 1,74; 1,9; 2,08; 2,28; 2,42; 2,8; 3,12; 3,48; 3,8; 4,16.
Поперечные подачи станка; 0,035; 0,037; 0,042; 0,048 0,055; 0,06; 0,065; 0,07; 0,074;
0,084; 0,097; 0,11; 0,12; 0,13; 0,14; 0,15; 0,17; 0,195; 0,21; 0,23; 0,26; 0,28; 0,30; 0,34; 0,39; 0,43;
0,47; 0,52; 0,57; 0,6; 0,7; 0,78; 0,87; 0,95; 1,04; 1,14; 1,21; 1,4; 1,56; 1,74; 1,9; 2,08; 1,14; 1,21;
1,4; 1,56; 1,74; 1,9; 2,08.
Наибольшее усилие, допускаемое механизмом продольной подачи - 3600 Н,
поперечной подачи 5500 Н.
К20
Мощность электродвигателя главного движения Nэ = 10 кВт, КПД станка η = 0,75.
Продольные подачи станка: 0,05; 0,06; 0,075; 0,09; 0,1; 0,125; 0,15; 0,175; 0,2; 0,25; 0,3;
0,35; 0,4; 0,6; 0,7; 0,8; 1,0; 1,2; 1,4; 1,6; 2,0; 2,4; 2,8.
Поперечные подачи станка, мм/об: 1/2 от Sпрод., т.е. 0,025-1,4. Наибольшее усилие,
допускаемое механизмом продольной подачи - 6000 Н.
СПИСОК ЛИТЕРАТУРЫ
1. Байкалова В.Н., Колокатов A.M. Методические указания по расчету
(назначению) режимов резаний при точении. М.: МИИСП, 1989.
2. Некрасов СС. Обработка материалов резанием: Учебник. М.:
Агропромиздат, 1996.
3. Краткий справочник металлиста / Под ред. А.Н. Малова. Изд. 2. М.:
Машиностроение, 1971.
4. Справочник технолога машиностроителя. В.2-х т. / Под ред. А.Г.
Косиловой и Р.К. Мещерякова. - 4-е изд., перераб. и доп. М.:
Машиностроение, 1985.
5. Некрасов С.С., Байкалова В.Н. Методические рекомендации по
выполнению домашнего задания по курсу «Обработка конструкционных
материалов резанием». М.: МИИСП, 1988.
6. Некрасов С.С., Байкалова В.Н., Колокатов A.M. Определение
технической нормы времени станочных операций: Методические
рекомендации. М.: MГAУ, 1995.
Дата добавления: 2015-12-17; просмотров: 47; Мы поможем в написании вашей работы! |
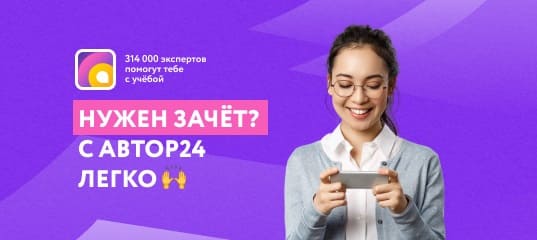
Мы поможем в написании ваших работ!