Современные технологии монтожа и ремонта
Монтаж судовых механизмов производят не непосредственно на опорных поверхностях фундаментов, а на компенсирующих звеньях, т.е. на подкладках. Это происходит из-за трудности взаимной пригонки больших опорных поверхностей фундаментов и корпусов устанавливаемых механизмов, а также зачастую из-за необходимости соосного монтажа взаимосвязанных механизмов. Подкладки должны обеспечивать надёжное крепление и минимальную трудоёмкость монтажа механизма. Также при выборе материала основное значение имеет неизменяемость механических характеристик и формы подкладок под нагрузкой при различных условиях эксплуатации.
В развитии способов крепления судовых механизмов могут быть выделены следующие основные этапы:
крепление на подкладках из твёрдого дерева и парусины;
крепление без подкладок;
крепление на металлических подкладках;
крепление с применением пластмасс.
Первые паровые машины ставились главным образом на подкладки из твёрдого дерева (бакаут, бук, дуб, тик, ясень), и только крупные машины, мощностью в несколько тысяч л.с., ставились на металлические клинья.
Длительный опыт эксплуатации тяжёлых машин, установленных на деревянных подкладках, показал, что после нескольких лет эксплуатации деревянные подкладки садятся, фундаментные болты ослабевают и возникают трещины в чугунных фундаментных рамах. Это обстоятельство побудило совершенно отказаться от установки машин даже средних мощностей на деревянные подкладки и к тридцатым годам прошлого века такой вид крепления являлся редким исключением.
|
|
Для решения технологических проблем, возникающих при монтаже судовых механизмов, а именно, исключения обработки и пригонки сопрягаемых поверхностей элементов узлов крепления, как в России, так и зарубежом проводились исследования и были выполнены разработки способов крепления механизмов с применением пластмасс.
Приоритет в области разработки креплений из пластмасс принадлежит российским разработчикам. В 1955–1958 году ЦНИИТС разработаны два способа монтажа судовых механизмов на подкладках из пластмассы БКД и ФМВ (рис. 1, з).
Пластмасса БКД (бакелит – контакт – дерево) имеет небольшую стоимость и включает в свой состав жидкий бакелит, керосиновый контакт Петрова и древесные опилки. Вследствие низкого предела прочности и значительной линейной усадки при отверждении пластмассы происходили перемещения механизмов от положения, достигнутого при базировании, что определило возможность ее применения только при монтаже вспомогательных нецентруемых механизмов с жестким корпусом, например шпилек, лебёдок и насосов. А также подкладки из пластмассы БКД применялись взамен крепления механизмов на деревянных и выравнивающих подкладках.
|
|
Недостатки пластмассы БКД были устранены при разработке пластмассы ФМВ (формируемая малоусадочная волокнистая). Для уменьшения линейной усадки пластмассы и соответственно повышения точности установки механизмов в ее состав ввели «жесткие» наполнители – рубленое стекловолокно и пушённое асбестовое волокно. Увеличение числа компонентов состава вызвало некоторое усложнение процесса приготовления состава (для смешивания состава потребовалось применение специального смесителя). Формование подкладок в монтажном зазоре производится путем прессования струбциной в раздвижной
форме (рис. 4, а) или с помощью пресса в нераздвижной форме (рис. 4, б).
Рис. 4. Установка механизма на подкладках из пластмассы ФМВ
а – использование раздвижных форм; б – использование шприц-пресса
1 – отжимной болт; 2 – форма; 3 – болт; 4 – рама механизма; 5 – термоэлектронагреватель (для подогрева подкладок при отрицательной температуре); 6 – опорная поверхность фундамента; 7 – струбцина; 8 – деревянная пробка; 9 – винтовой шприц-пресс; 10 – неразъемная круглая форма
|
|
Однако разработка пластмассы ФМВ не позволила в полной мере решить задачу повышения точности установки механизмов. В процессе отверждения состава происходила просадка механизма, а при прогреве механизма – ослабление затяжки крепежных деталей. Для уменьшения этих негативных явлений в технологический процесс монтажа механизма потребовалось ввести дополнительные операции: применение двукратного термостатирования пластмассы с нагревом до 50±5°С и выполнение центровки со смещением, учитывающим линейную усадку, усилие затяжки, нагрузку от массы механизма, высоту подкладки, температуру на опорной поверхности.
Аналогичные процессы монтажа на пластмассовых подкладках были разработаны для зарубежного судостроения. Примерами этих разработок могут служить пластмассы CHOCKFAST ORANGE (США), EPOCAST 36 (Германия) и EPY (Польша), получившие общее название – литьевые пластмассы. Российские литьевые пластмассы марок БМ-1 и БМ-2 (быстроотвердевающая монтажная) были разработаны в 1980–1983 гг. Николаевским филиалом ЦНИИТС (рис. 5).
а)
б)
Рис. 5. Формование компенсирующего звена из пластмассы БМ-1
а) через окно в боковой стенке формы; б) через отверстие под крепёжный болт
1 – лапа механизма; 2 – фундамент; 3 – болт крепёжный; 4 – пластмасса; 5 – форма; 6 – пресс для запрессовки пластмассы; 7 – щелевая насадка; 8 – приспособление для фиксации пресса; 9 – пробка деревянная
|
|
При разработке литьевых пластмасс по сравнению с пластмассой ФМВ было уменьшено до двух количество компонентов и снижена вязкость состава в жидкотекучем состоянии. Совокупность свойств литьевых пластмасс обеспечила возможность заполнения монтажных зазоров самотёком. Для заполнения монтажный зазор (рис. 6) ограничивают путем установки вдоль лапы механизма металлической полосы и уплотнения других сторон пространства подкладкой из
пенополиуретановой ли полиэтиленовой пленки
.
Рис. 6. Литая фундаментная подкладка из пластмассы
1 – лапа механизма; 2 – фундамент; 3 – металлическая полоса; 4 – деталь крепёжная; 5 – подкладка из пластмассы; 6 – форма из пены
При применении литьевых пластмасс введено ограничение удельных нагрузок на подкладку. Установленные ограничения составляют: 5 МПа – для главных механизмов, 15 МПа – для нецентруемых механизмов. Приведенные значения допускаемых нагрузок существенно отличаются от допускаемых нагрузок пластмассы ФМВ (40 МПа), что обусловило увеличение расхода пластмассы и высокую стоимость монтажа механизма.
Разработка литьевых пластмасс позволила существенно улучшить технологические свойства пластмассовых подкладок. Однако при их разработке не удалось избежать основных недостатков, характерных для отечественной пластмассы ФМВ – просадки механизма в процессе отверждения состава и ослабление затяжки крепежных деталей при прогреве механизма.
Меры, предлагаемые поставщиками литьевых пластмасс для уменьшения влияния указанных факторов на точность установки механизма аналогичны применяемым при монтаже механизмов на подкладках ФМВ. Это введение дополнительных операций, а именно, выполнение центровки со смещением и применение термостатирования пластмассы. Однако приведенные меры не являются достаточно эффективным средством для обеспечения заданной точности установки механизма.
Выбор величины смещения при монтаже механизмов на пластмассовых подкладках существенно усложняется разбросом в два раза значений линейной усадки пластмассы и разбросом фактических толщин подкладок до 30–40 мм. Это приводит к тому, что упреждающее смещение механизма рассчитывают, как правило, применительно к узлам крепления расположенным в непосредственной близости к фланцу отбора мощности. Для расчетных узлов крепления погрешность сборки по параметру сближение механизма с фундаментом достигает 0,05–0,1 мм, а для узлов крепления удаленных от фланца отбора мощности еще больших значений.
Для исключения недостатков пластмассовых подкладок в 1970–1987 годах ЦНИИТС разработан способ крепления на металлических подкладках со слоем полимерного материала, получивший сокращенное наименование – «клин с полимером». Целью разработки являлось повышение точности установки механизмов и снижение затрат на монтаж механизмов. Практическое применение этой технологии позволило в 1987 г. исключить пластмассу ФМВ из отечественного судостроения.
В узлах крепления (рис. 1, и) предусматривается установка металлических подкладок с зазором относительно присоединительных поверхностей механизма и фундамента и последующее заполнение этого зазора отверждающимся полимерным материалом. Подкладки изготавливаются меньше фактического размера монтажного зазора на величину 0,4–0,5 мм. При установке подкладок значения зазоров составляют от 0,15 до 2 мм, что позволяет компенсировать погрешности сопряжения механизма с фундаментом и исключить операции обработки фундаментов и пригонки сопрягаемых поверхностей узлов крепления.
На основании выполненных исследований удалось обнаружить парадоксальный эффект, заключающийся в том, что полимер хорошо заполняет все микронеровности, увеличивает площадь контакта, а тонкий его слой, не превышающий 0,1 – 0,5 мм, практически не деформировался и не приводил к снижению прочности соединения. Также значительно снизился расход дорогостоящей пластмассы.
По первоначальной технологии монтажа (рис. 7) все подкладки устанавливались в монтажный зазор с предварительно нанесённым полимерным материалом. Полимерный материал наносился шпателем или кистью на обе стороны подкладки и поверхность фундамента тонким слоем без пропусков. После установки подкладки на место, отверстие лапы механизма заполнялось полимерным материалом в количестве 20–30 г и уплотнялось небольшим усилием с помощью металлического или деревянного стержня до выхода излишков в монтажный зазор. При установке в монтажный зазор подкладок с заранее просверленными отверстиями, последние глушились деревянными пробками (рис. 7, б). Для исключения сдвига подкладки после её установки, пробку смещали вниз в отверстие фундамента на 3 – 6 мм (рис 7, в).
Рис. 7. Установка подкладки со слоем полимерного материала
а – при отсутствии отверстия в подкладке; б – с отверстием в подкладке; в – со смещённой вниз пробкой для исключения сдвига подкладки со своего места
1 – стержень; 2 – лапа механизма; 3 – подкладка; 4 – фундамент механизма; 5 – полимерный материал; 6 – деревянная пробка
Заполнение зазора между стенкой отверстия и стержнем болта полимерным материалом по первоначальной технологии выполнялось при помощи шприца и кольцевой насадки (рис. 8).
Уменьшение толщины слоя пластмассы с 30–50 мм до 0,15–2 мм позволило избежать просадки механизма, обусловленной линейной усадкой пластмассы. Так, если при использовании пластмассовых подкладок расчетная усадка составляет 0,06–0,10 мм, то при использовании технологии «клин с полимером» менее 0,004 мм. Соответственно, при использовании технологии «клин с полимером» нет необходимости выполнять упреждение просадки механизма для исключения влияния усадки пластмассы при отверждении и выполнять термостатирование пластмассы.
Факт отсутствия сближения механизма с фундаментом неоднократно подтвержден практикой монтажа механизмов. Отсутствие сближений механизма с фундаментом отмечалось в частности при монтаже гребных электродвигателей на ледоколах проекта 97Н, дизель-генераторов 8NVD36 и 6VD26/20 РТМ типа «Атлантик» и РТМС типа «Прометей», при установке секций главных двигателей 8ZD72/48 на РМТС «Атлантик-супертраулер», главных двигателей пр. 12911 и др.
Отсутствие просадки стыка при использовании в соединениях тонких слоев пластмассы подтверждается экспериментальными исследованиями разработчиков литьевой пластмассы EPY.
Дата добавления: 2016-01-04; просмотров: 17; Мы поможем в написании вашей работы! |
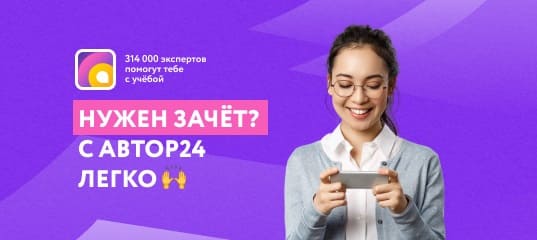
Мы поможем в написании ваших работ!