Отзыв о преддипломной практике
Отчет
По производственной практике
(преддипломной)
Выполнил студент
Группы ТАВХ491
Костикова А.С. « 17»мая 20 20 г.
Проверил
Тарасова О.И. «____»___________ 20 ___ г.
2020
СОГЛАСОВАНО УТВЕРЖДАЮ
Председатель ЦК спец.23.02.06 Зам.директора по УПР
И.Н.Костикова ________О.Н.Пикалов
06.04 2020 г. 06.04 2020г.
РАБОЧАЯ ПРОГРАММА
Производственной(преддипломной) практики студента(ки) Тамбовского техникума железнодорожного транспорта –филиала РГУПС
Костиковой Анастасии Сергеевны группы ТАВХ 491
специальности 23.02.06 «Техническая эксплуатация подвижного состава железных дорог»
|
|
направляемого на практику :
Производственный участок Тамбов пассажирское вагонное депо Воронеж – структурное подразделение Приволжского филиала АО «ФПК»
Сроки проведения с «20» апреля 2020г.по «17» мая 2020 г.
Продолжительность 4 недели
Содержание производственной практики(преддипламная)
№ п/п | Дата (период) | Наименование выполняемых работ | Профессиональный модуль | Коли-чество недель |
1. | 20.04 - 26.04 | Общее ознакомление с организацией работы производственного подразделения (депо, ПТО, вагонного участка, завода и т.д.) | - | 1 |
2. | 27.04 - 10.05 | Ознакомление с организацией работы одного из участков производственного подразделения (по теме дипломного проекта) | - | 2 |
3. | 11.05 - 17.05 | Сбор материала по выполнению дипломного проекта | - | 1 |
Индивидуальные вопросы, подлежащие разработке:
Введение
1.Характеристика предприятия
2.Технологический процесс
3.Охрана труда
В соответствии с рабочей программой студент должен составить отчет в электронном (презентация, видеоролики, фото) или письменном виде (15-20 листов формата А4) о прохождении практики. Форма и содержание отчета согласуется с руководителем практики от техникума.
|
|
Примечание: Оценка по практике выставляется посредством дифференциального зачета на основании документов: характеристики (отзыва) от руководителя со стороны производства; отчета по практике и аттестационного листа.
Руководитель практики________________________
Содержание
ВВЕДЕНИЕ 3
1. ХАРАКТЕРИСТИКА ПРЕДПРИЯТИЯ 5
2. ТЕХНОЛОГИЧЕСКИЙ ПРОЦЕСС 7
3. ОХРАНА ТРУДА 25
ВВЕДЕНИЕ
Перед железнодорожным транспортом поставлены три главные задачи: полное, своевременное и качественное удовлетворение нужд экономики и населения в перевозках, выход на передовые позиции в мире по большинству объемных, качественных и экономических показателей и дальнейший прогресс в социальной сфере.
Назначение вагонного хозяйства заключается в обеспечении железных дорог исправным вагонным парком, удовлетворяющим требованиям безопасности движения, сохранения перевозимых грузов, а также в создании удобств при перевозке пассажиров. Поэтому главной задачей хозяйства является поддержание высокого уровня работоспособности грузовых и пассажирских вагонов в условиях непрерывного их эксплуатирования.
|
|
Основные направления технического процесса в отрасли: интенсивная подготовка обращения нового подвижного состава; в первую очередь расширение полигона обращения 8-осных полувагонов и цистерн, 4-осных вагонов, с перспективными параметрами и повышенными прочностными характеристиками; которые способствуют увеличению провозной и пропускной способности железных дорог благодаря возможности удлинения участков безопасного движения поездов, увеличения их скорости и веса.
Намечается существенное обновление вагонного парка путем изъятия из обращения вагонов устаревших конструкций, что позволит значительно улучшить работоспособность подвижного состава и обеспечить более высокий уровень проследования поездов по графику. Принимаются меры по повышению надежности вагонов новой постройки и выполнению установленного объема работ по
повышению модернизации вагонов рабочего парка при поступлении их
в капитальный ремонт. Одновременно будет совершенствоваться система периодического ремонта вагонов на основе широкого внедрения поточных методов, применения современных средств механизации и автоматизации производственных процессов.
|
|
Для повышения качества ремонта большое значение имеет уровень техники организации и технологии вагоноремонтного производства.
Восстановление работоспособности вагонного парка и поддержание его в технически исправном состоянии осуществляется вагоноремонтными заводами и вагонными депо при планово-предупредительном и текущим ремонте вагонов.
В сложных условиях эксплуатации колесные пары испытывают большие статические и динамические нагрузки, которые приводят к образованию различных дефектов. Существующая на железной дороге система выявления дефектов и устранения их в процессе освидетельствования и ремонта колесных пар направлена на обеспечение надежной работы подвижного состава.
Передовые методы своевременного выявления дефектов колесных пар в процессе движения поездов является основой предупреждения аварий и крушений.
Качество и эффективность ремонта и формирование колесных пар во многом зависит от исполнителей и организаторов производства в колесных цехах, от их знаний передовых технологий и прогрессивных методов труда.
1 ХАРАКТЕРИСТИКАПРЕДПРИЯТИЯ
Производственный участок Тамбов пассажирского вагонного депо Воронеж – структурного подразделения Приволжского филиала АО «Федеральная пассажирская компания» - предназначен для выполнения планового ремонта вагонов, ремонта и комплектования вагонных узлов и деталей колесных пар, технического обслуживания.
Пассажирский вагонный участок Тамбов до последнего времени являлось в основном эксплуатационном. В 1997 году в связи со снижением пассажира-оборота и в целях уменьшения эксплуатационных расходов произведено объединение пассажирского вагонного депо Тамбов и Мичуринск. В настоящее время вагонный участок Тамбов производит деповской ремонт, техническое обслуживание, эксплуатацию и экипировку пассажирских вагонов, и техническое обслуживание грузовых вагонов.
Для выполнения этих работ участок имеет в своем составе следующие производственные подразделения:
- Цеха деповского ремонта вагонов на станции Мичуринск.
- Пункт технического обслуживания пассажирских вагонов на станции Мичуринск.
- Участок экипировки пассажирских вагонов на станции Тамбов.
- Резерв проводников, цех текущего обслуживания ТО-3 на станции Тамбов. Пункты технического обслуживания грузовых поездов на ст. Тамбов, Кирсанов, Обловка.
Участок экипировки пассажирских вагонов обеспечивает комплектование вагонов постельными принадлежностями и другим инвентарем.
Культура обслуживания пассажиров в поездах до значительной степени зависит от своевременного снабжения их высококачественными постельными принадлежностями, съемным инвентарём. Работа экипировочных цехов по подготовке пассажирских вагонов в рейс производится в соответствии с графиком утверждённого технологического процесса согласованного с расписаниями движения поездов. Постельное белье и др. инвентарь выдается на
каждый вагон по действующим нормам.
На участке экипировки производится техническое обслуживание, экипировка пассажирских вагонов приписанных к вагонному депо.
Техническое обслуживание производится на пунктах прилегающих к участку общей длинной 3361м.
Эти пути оснащены необходимым оборудованием и устройствами в их числе - моечная машина.
Междупутья заасфальтированы, что создает хорошие условия для осмотра, ремонта и экипировки вагонов.
На путях имеется устройство для снабжения вагонов водой, проложен кабель с разборными колонками для обеспечения энергией, а так же воздуховод с разборными колонками для зарядки и опробованием тормозов. Источником сжатого воздуха
2 ТЕХНОЛОГИЧЕСКИЙ ПРОЦЕСС
Подготовка средств контроля включает в себя:
· внешний осмотр и подготовку к работе дефектоскопа, НУ, вспомогательных приборов и устройств;
· приготовление и проверку выявляющей способности магнитного индикатора;
· проверку работоспособности (порога чувствительности) средств контроля;
· проверку наличия на рабочем месте средств для очистки деталей, необходимого слесарного инструмента, переносного светильника, лупы, мелков и т.п.
При проведении проверки работоспособности средств контроля с помощью СОП и искусственными дефектами проверку выявляющей способности магнитных индикаторов допускается не проводить.
При внешнем осмотре дефектоскопа и вспомогательных приборов и устройств проверяют:
· целостность корпусов блока питания ,НУ и других узлов;
· надежность соединения шнура питания и соединительных кабелей;
· надежность заземления;
· исправность подвижных узлов/механизмов зажима и поворота контролируемых деталей; перемещения соленоидов; шарнирных и раздвижных полюсов электромагнитов и постоянных магнитов).
Перед проведением контроля детали должны быть очищены до металла. При этом с контролируемой поверхности должны быть удалены ржавчина, шлак, окалина, загрязнения, смазка, слой старой растрескавшейся краски и другие покрытия, мешающие проведению контроля.
При очистке деталей применяют волосяные и металлические щетки, скребки, губки, ветошь и салфетки, не оставляющие ворса на очищаемой поверхности.
Перед проведением контроля проводят осмотр поверхности деталей с применением, при необходимости луп. При этом выявляют наличие рисок, задиров, забоин, электроожогов и других видимых глазом дефектов.
Выявление при осмотре дефекты устраняют зачисткой или другими методами.
Детали с обнаруженными при осмотре недопустимыми дефектами контролю не подлежат.
Контроль проводим тремя методами:
· Магнитопорошковый;
· Вихретоковый;
· Ультразвуковой.
Магнитный вид НК
Магнитопорошковый контроль основан на притяжении магнитных частиц силами неоднородных магнитных полей, возникающих над дефектами в намагниченной детали.
При контроле выявляются поверхностные дефекты типа нарушении сплошности металла:
· трещины различного происхождения.
Результаты контроля зависят от магнитных свойств материала, формы, размеров и шероховатости, местоположения и направления дефектов и т. д.
Свойства контроля.
При магнитопорошковом контроле применяют переносные, передвижные и стационарные дефектоскопы и НУ (намагн. устройство).
В зависимости от принципа действия в состав дефектоскопа входят:
· блок питания или управления;
· НУ (соленоиды, л. магниты, кабели или стержни, катушки);
· Вспомогательные устройства и приспособления.
К вспомогательным средствам относятся:
· устройства для нанесения магнитных индикаторов на контролируемую
· поверхность деталей;
· устройства для осмотра поверхности деталей;
· приборы и устройства для проверки режима намагничивания и степени размагничивания деталей;
· приборы и устройства для проверки выявляющей способности магнитных индикаторов.
Магнитные индикаторы - это порошки и суспензии (черные, цветные и люминесцентные)
В качестве дисперсной среды для приготовления магнитных суспензий используют технические масла, дизельное топливо, смеси масел с дизельным топливом или керосином с последующим добавлением в воду с кондиционирующими добавками.
Подготовка к провидению контроля.
Подготовка средств контроля включает в себя:
· внешний осмотр и подготовка дефектоскопа, намагничивающих устройств, вспомогательных приборов и устройств;
· проверка работоспособности;
· наличие средств для очистки, лампы, лупы, мела и т. д.
· При внешнем осмотре дефектоскопа и вспомогательных приборов проверяют:
· целостность корпусов блока питания;
· надежность соединения шнуров и соединительных кабелей;
· заземление;
· исправность подвижных узлов.
Технологические карты | ||||||
| Контроль магнитопорошковый | Листов |
| |||
Деталь: ось (средняя часть) Узел: колесная пара | Марка стали: Ос.В ГОСТ 4828-83 Тверд. HRC: 20 Шероховатость: Ra 2,5 мкм | Способ контроля: СПП Н, А/м 20 Длина зоны ДН, мм. 110...130 | Лист 10 | |||
Тип вагона: пассажирский, грузовой | Согласно РД 32.159-2000 | Требования документов по техническому обслуживанию и ремонту | ||||
Технологические операции | Средства контроля | |||||
1. Подготовка детали к контролю. 1.1. Установить колесную пару на роликовые опоры. 1.2.Очистить среднюю часть оси от грязи и смазки. 1.3. Осмотреть контролируемую поверхность с целью выявления видимых глазом дефектов. Примечание: оси с обнаруженными при осмотре недопустимыми дефектами магнитопорошковому контролю не подлежат. 1.4. Протереть контролируемую поверхность ветошью, смоченной в суспензии. 2. Операции контроля. 2.1. Опустить седлообразный соленоид над средней частью оси на расстояние 130... 150 мм от ступицы одного из колес так, чтобы между дугой соленоида и поверхностью оси был зазор 40... 60 мм. 2.2. Включить соленоид. 2.3. Нанести суспензию на ось (для новых осей — на основе МИНК-030, для старогодных — МИНК-010) в пределах зоны ДН слева от соленоида до ступицы и справа от соленоида. 2.4. После стекания суспензии в течение 5... 10 сек осмотреть поверхность средней части оси с двух сторон от соленоида. Выключить соленоид. 2.5. Переместить соленоид вдоль оси на расстояние 110... 130 мм от предыдущего положения и повторить операции по п.п. 2.1-2.4. 2.6. Переместить соленоид на расстояние 350...370 мм и повторить операции 2.1-2.4 2.7. Последовательно перемещая соленоид вдоль оси на расстояния 110... 130 и 350.. .370 мм относительно предыдущего положения, провести контроль по п.п. 2.1-2. всей поверхности средней части оси до ступицы следующего колеса. 2.8. Повторить контроль по п.п. 2.1-2.7, дважды провернув колесную пару на 120°±10°. 2.9. Для размагничивания включить соленоид и провести его по всей длине средней части оси от ступицы одного колеса к другому. Переместить соленоид к середине средней части оси, остановить и поднять на 0,3...0,5 м от оси. 2.10. Выключить соленоид. 2.11. Удалить с поверхности средней части оси остатки суспензии, протерев ее ветошью. 2.12.Занести в журнал результаты контроля. | Средства для очистки: обтирочный материал, щетка волосяная Дефектоскоп: МД-12ПС, Магнитный индикатор: кем МИНК-010 (30±5 г), кем МИНК-030 (40±5 г) Вода питьевая до 1 л Вспомогательные средства: распылитель, лампа переносная (12В), лупа, мел, поддон | Виды работ, при которых проводится контроль: при всех видах освидетельствования колесных пар Зоны контроля: все открытые поверхности средней части оси Критерии браковки: трещины на средней части оси не допускаются (ЦВ/3429) | ||||
Эскиз детали, схема намагничивания |
| |||||
| ||||||
| Контроль магнитопорошковый | Листов | ||
Деталь: ось (шейка и предподступичная часть) Узел: колесная пара | Марка стали: Ос.В ГOCT 4828-83 Тверд.Н11С: 20 Шероховатость: Ra 2,5 мкм | Способ контроля: СПИ Н, А/см 20 Длина зоны ДН, мм: 110... 130 | Лист 11 | |
Тип вагона: пассажирский, грузовой Согласно РД 32.159-2000 | Требования документов по техническому обслуживанию и ремонту | |||
Технологические операции | Средства контроля | |||
1. Подготовка детали к контролю: 1.1. Очистить шейки оси от грязи и смазки. 1.2. Осмотреть контролируемую поверхность с целью выявления видимых глазом дефектов. Примечание: оси с обнаруженными при осмотре недопустимыми дефектами магнитопорошковому контролю не подлежат. 1.3.Протереть контролируемую поверхность ветошью смоченной в суспензии. 2. Операции контроля: 2.1. Подвести соленоид к шейке оси так, чтобы она входила в отверстие соленоида на 30-50 мм (рис.1). 2.2. Приподнять соленоид так, чтобы зазор между корпусом соленоида и контролируемой поверхностью шейки оси был не менее 40 мм. 2.3. Включить вращение колесной пары. 2.4. Включить соленоид. 2.5. Нанести суспензию на шейку и предподступичную часть. 2.6. Дать стечь суспензии в течение 10... 15 сек. и осмотреть поверхность шейки. 2.7. При стекании суспензии переместить соленоид к ступице колеса и вернуть в исходное положение по п. 2.1. 2.8. Осмотреть шейку и предподступичную часть при вращении оси, обращая внимание на галтели шеек и предподступичной части. 2.9. Выключить соленоид и остановить вращение оси. 2.10. Для размагничивания установить соленоид на середине шейки оси. Включить соленоид и медленно отвести его на расстояние не менее 0,5 м. Выключить соленоид. 2.11. Удалить с поверхности шейки оси остатки магнитного порошка, протерев ее ветошью и далее салфеткой. 2.12. Занести в журнал результаты контроля. | Средства для очистки: обтирочный материал, щетки волосяные, моющие средства Дефектоскоп МД-12ПШ, Магнитный порошок ТУ 6-36- 05800165-1009-93 Магнитный индикатор: суспензия: магнитный порошок 25±5 г трансформаторное масло - 0, 3 л керосин - 0, 7 л B спомогательные средства: лампа переносная (12В), лупа, мел | Виды работ, при которых проводится контроль: При всех видах освидетельствования колесных пар со снятием внутренних и лабиринтных колец роликового подшипника. Зоны контроля: поверхности шейки и предподступичной части оси, галтели. Критерии браковки: Трещины на шейке и предподступичной части оси не допускаются (ЦВ/3429) | ||
Эскиз детали, схема намагничивания | ||||
| ||||
Предприятие: Тамбовский ВРЗ ОАО «ВРМ» | Контроль магнитопорошковый | Листов | ||||
Дата «__»_____200_г. | Деталь: стопорная планка Узел: буксовый узел с роликовыми подшипниками | Марка стали: сталь 3 ГОСТ 380-71 Тверд.HRC 30 Шерохов. не более Ra 2,5 мкм | Способ контроля: СПП II, А/см 20 Длина зоны ДН, мм: 100 | Лист 12 | ||
Тип вагона: пассажирский, грузовой | Согласно РД 32.159-2000 | Требования документов по | ||||
Технологические операции | Средства контроля | техническому обслуживанию и ремонту | ||||
1.Подготовка детали к контролю 1.1 .Очистить планки от грязи и смазки 1.2.0смотреть поверхность планок с целью выявления видимых глазом дефектов. Примечание: стопорные планки с обнаруженными при осмотре недопустимыми дефектами магнитопорошковому контролю не подлежат. 1.3.Обезжирить контролируемую поверхность ветошью, смоченной в суспензии. 1.4.Уложить в 2 - 3 ряда 8-12 деталей на подставку из немагнитного | Средства для очистки: обтирочный материал, щетки волосяные Дефектоскоп МД-12ПШ Магнитный индикатор: KMC МИНК-030 30±5 г. Вода питьевая до 1л. Вспомогательные средства: распылитель, лампа переносная, лупа, мел, поддон, подставка из неметаллического материала. | Виды работ, при которых проводится контроль: При всех видах планового ремонта вагонов Зоны контроля: вся поверхность. Критерии браковки: Трещины не допускаются (ЦВ/3429) | ||||
материала (рис.1) | Эскиз детали, траектория сканирования | |||||
2.0перации контроля. 2.1.Отвести соленоид в крайнее правое положение. 2.2.Установить соленоид так, чтобы один конец подставки с деталями входил в отверстие соленоида на 30...50 мм. 2.3.Включить соленоид. 2.4.Нанести суспензию на детали в пределах зоны ДН. 2.5.После стекания суспензии в течение 5... 10 сек. осмотреть поверхность планок в пределах зоны ДН. 2.6.Медленно переместить соленоид вдоль деталей, нанося суспензию перед соленоидом в пределах зоны ДН. 2.7.После стекания суспензии в течение 5... 10 сек. осмотреть поверхность деталей. 2.8.Выключить соленоид. 2.10.Повернуть детали на 180° и повторить контроль по п.п. 2.2. -2.8. 2.11.Удалить с поверхности деталей остатки суспензии, протерев их ветошью. 2.12.Занести в журнал результаты контроля. | | |||||
Предприятие: Тамбовский ВРЗ ОАО «ВРМ» | Контроль магнитопорошковый | Листов | |||
Дата «__»______200_г. | Деталь: ось (подступичная часть) Узел: колесная пара | Марка стали: Ос. В ГОСТ 4828-83 Тверд. HRC 20 Шероховатость: Ra 2,5 мкм | Способ контроля: СПП Н, А/см 20 Длина зоны ДН, мм: 110...130 | Лист 13 | |
Тип вагона: пассажирский, грузовой | Согласно РД 32.159-2000 | Требования документов по техническому обслуживанию и ремонту | |||
Технологические операции | Средства контроля | ||||
1.Подготовка детали к контролю. 1.1. Очистить подступичную часть оси от грязи и смазки. 1.2. Осмотреть контролируемую поверхность с целью выявления видимых глазом дефектов. Примечание: оси с обнаруженными при осмотре недопустимыми дефектами магнитопорошковому контролю не подлежат. 2.Операции контроля. 2.1. Подвести соленоид к подступичной части оси так, чтобы она входила в отверстие соленоида на 30-50 мм (рис.1). 2.2. Установить соленоид так, чтобы зазор по окружности между корпусом соленоида и контролируемой поверхностью подступичной части оси был симметричен (допускается чтобы зазор между соленоидом и поверхностью оси сверху был больше, чем снизу). 2.3. Включить соленоид. 2.4. Нанести суспензию на поверхность подступичной части оси в пределах зоны ДН. 2.5. Дать стечь суспензии в течении 10-15 сек. и осмотреть поверхность подступичной части. 2.6. Медленно переместить соленоид вдоль подступичной части оси, нанося суспензию на участок оси в пределах зоны ДН и осматривая поверхность за движущимся соленоидом. Довести соленоид до конца подступичной части, прекратить нанесение суспензии, выключить соленоид и вернуть в исходное положение. 2.7. Ось повернуть дважды на 120° (1/3 часть окружности) и для каждого положения повторить контроль по п.п. 2.1 —2.6. 2.8. Для размагничивания установить соленоид над подступичной частью оси, включить намагничивающий ток. 2.9. Плавно переместить соленоид к шейке оси и отвести от нее на расстояние не менее 0,5 м. 2.10. Выключить соленоид. 2.11. Удалить с поверхности шейки оси остатки суспензии, протерев ее салфеткой. 2.12. Занести в журнал результаты контроля. | Средства для очистки: Ветошь, салфетки х/б, щетка волосяная Дефектоскоп МД-12ПЭ, Магнитный индикатор: суспензия: порошок магнитный черный ТУ 6-36-05800165-1009-93 (25±5) г трансформаторное масло - 0,3 л керосин -0,7 л Вспомогательные средства: Лампа стационарная (12В), лупа, мел | Виды работ, при которых проводится контроль: Перед запрессовкой колес. Зоны контроля: вся поверхность подступичной части оси. Критерии браковки: Трещины на подступичной части оси не допускаются (ЦВ/3429) | |||
Эскиз детали, схема намагничивания | |||||
| |||||
Предприятие: Тамбовский ВРЗ ОАО «ВРМ» | Контроль вихретоковый | Листов | |||||
Дата «__»_____200_г. | Деталь: колесо цельнокатаное Узел: колесная пара | Сталь марки 1 и сталь марки 2 ГОСТ 10791 , IIRC 20, Rz> 80 Сталь марки Т-ТУ 0943-157-01124324-2003, НВ 320-360, Rz> 80 | Лист 14 | ||||
Тип вагона: пассажирский, грузовой | Согласно РД 32.150-2000 | Требования документов по техническому обслуживанию и ремонту | |||||
Технологические операции | Средства контроля | ||||||
1.Подготовка детали к контролю 1.1. Осмотреть поверхность диска, обода и ступицы с целью выявления видимых глазом дефектов. При наличии вздутий или надрывов краски в виде линии длиной более 50 мм удалить отслоения краски и отметить это место мелом. Примечание: колеса с обнаруженными при визуальном осмотре трещинами вихретоковому контролю не подлежат. 2. Операции контроля 2.1. Установить порог чувствительности дефектоскопа с помощью стандартного образца С-ОП-НО-037 на искусственном дефекте ИД5. 2.2. Установить ВП на наружную поверхность обода и провести круговое сканирование на расстоянии 5...8 мм от фаски (рис.1) 2.3. Установить ВП на внутреннюю поверхность обода и провести круговое сканирование на расстоянии 5...8 мм от внутренней кромки обода (рис.2). 2.4. Провести зигзагообразное сканирование с шагом 5...8 мм приободной зоны диска с внутренней стороны колеса и зоны перехода от диска к ступице с наружной стороны колеса (рис. 3; а, б и в). 2.5. Провести круговое сканирование ступицы на расстоянии 5...8 мм от кромки по образующей и по торцу ступицы (рис. 4; а, б) с обеих сторон колеса. 2.6. Установить порог чувствительности дефектоскопа с помощью стандартного образца СОП-1Ю-037 на искусственном дефекте ИДЗ. 2.7. Установить ВП на наружную поверхность обода в зоне клеймения и провести сканирование вокруг этой зоны (рис.5). 2.8. При срабатывании светового и звукового индикаторов в какой-либо зоне на поверхности колеса необходимо сканировать этот участок повторно не менее трех раз, отметить мелом места срабатывания индикаторов. 2.9. Очистить отмеченные мелом места от остатков лакокрасочного покрытия, сканировать повторно не менее трех раз и осмотреть с применением лупы и переносной лампы. 2.10. При необходимости подтверждения результатов контроля применять МПК. 2.11. Занести результаты контроля в рабочий журнал. | Средства для очистки: обтирочный материал, щетки волосяные, металлический скребок, напильник Дефектоскоп: ВД-113.5, ВД-113 Стандартный образец: СОП-НО-037 Вспомогательные средства: лампа переносная, лупа, мел | Виды работ, при которых проводится контроль: при всех видах освидетельствования колесной пары Зоны контроля: обод, приободная зона диска, зона перехода от диска к ступице и кромки ступицы Критерии браковки: согласно инструкции I I.B/3429 | |||||
Эскиз детали, траектория сканирования | |||||||
| |||||||
Деталь: колесо цельнокатаное Узел: колесная пара | Контроль вихретоковый | Лист 15 |
|
Эскиз детали, схема расположения предполагаемого дефекта | |||
| |||
|
| Контроль магнитопорошковый | Листов | |||
Дата | ИД на контроль: | Узел: буксовый подшипник | Материал: сталь ШХ15СГ | Способ | Лист |
«__»______ | ЦВ/3429 | Деталь: | Шероховатость Ra 1,25 | контроля: | 16 |
РД 32.174-2001 ,РД 32.159-2000 | внутреннее кольцо подшипника | Цвет светлый | СОН, | ||
200_ г. | упорное кольцо подшипника | Твердость HRC 63 | Н 180 Л/см | ||
Тип вагона: грузовой, пассажирский | Согласно РД 32.159-2000 | ||||
Средства контроля | Требования документов по техническому обслуживанию и ремонту | ||||
Средства для очистки: | Виды работ, при которых проводится НК: | ||||
Обтирочный материал, щетка волосяная. | При полном освидетельствовании колесной пары. | ||||
Дефектоскоп ПР Рэ 2667, СОП | Зоны контроля: внутреннее кольцо | - внутренняя и наружная поверхность, | |||
Магнитный индикатор: | упорное - вся поверхность | ||||
Порошок магнитный черный | Критерии браковки: | ||||
ТУ 6-36-05800165-1009-93 5 гр. | Трещины не допускаются (З-ЦВРК-2001) | ||||
Керосин | 1 л. | ||||
Вспомогательные средства: лупа, мел | |||||
Технологические операции | |||||
1. Подготовительные операции | |||||
1.1 .Кольца, подлежащие контролю, должны быть очищены от грязи, смазки, ржавчины и обезжирены. Подготовленные детали | |||||
подать на стол-накопитель и размагнитить. | |||||
1.2.Осмотреть контролируемую поверхность с целью выявления видимых глазом дефектов. | |||||
1.3.Включить дефектоскоп. | |||||
1.4.Проверить работоспособность системы с помощью СОГ1, проведя контроль по той же технологии, что и проверяемое кольцо. | |||||
2.Операции контроля. | |||||
2.1.11ровести циркулярное намагничивание каждого кольца в 2-х взаимно перпендикулярных сечениях не менее чем тремя импульсами. При этом смещение | |||||
токопроводящего стержня от центральной оси детали должно быть минимальным. | |||||
2.2.Уложить кольца на решетку емкости таким образом, чтобы кольца не касались друг друга (не более 7 шт). | |||||
2.3. Включить вращение емкости для обеспечения перемешивания суспензии | |||||
2.4.11огрузить предварительно намагниченные детали в емкость с суспензией па 1.. .2 минуты | |||||
2.5.Выключить вращение емкости. | |||||
2.6.Через 5... 10 сек. после остановки вращения поднять решетку с кольцами. | |||||
2.7.Осмотреть поочередно каждое кольцо, используя при необходимости лупу. | |||||
2.8.При отсутствии дефектов произвести размагничивание кольца на размагничивающем устройстве. |
Деталь: кольцо внутреннее, упорное Узел: буксовый подшипник | Контроль магнитопорошковый | Лист 17 |
Эскиз детали, схема намагничивания | ||
|
| |||||||
| Контроль магнитопорошковый | Листов | |||||
Дата «__»__________ 2007г. | Деталь: Ось чистовая РУ1111 Узел: Колесная пара | Марка стали: Ос. В ГОСТ 4828-83 Тверд. HRC: 20 Шероховатость: Ra 2,5 мкм Цвет: светлый | Способ контроля: СПП Н, А/см 20 Длина зоны ДН, мм: 50 ... 70 | Лист 18 | |||
Тип вагона: пассажирский, грузовой | Согласно РД 32.144-2000, РД 32.159-2000 | Требования документов по | |||||
Технологические операции | Средства контроля | техническому обслуживанию и ремонту | |||||
1. Подготовка к контролю 1.1. Установить ось на роликовые опоры. 1.2. Проверить работоспособность системы контроля на ОСО-Г-110. КЗ. 1.3.Осмотреть контролируемую поверхность с целью выявления видимых глазом дефектов. 1.4.Протереть контролируемую поверхность ветошью, смоченной в суспензии. 2.0перацин контроля: 2.1. Установить соленоид над осью у торца (рис. 1), при этом зазор между осью и соленоидом обеспечивается конструкцией установки. 2.2. Включить соленоид. 2.3. Нанести суспензию на участок оси в пределах зоны ДН с внешней стороны НУ. 2.4.После стекания суспензии в течение 5-10 с. осмотреть | Средства для очистки: обтирочный материал, щетки волосяные, моющие средства Дефектоскоп МД-12ПС, МЭД-120, ОСО-Г- 110 Магнитный индикатор: суспензия порошок магнитный черный ТУ 6-36-05800165-1009-93 (25±5) г трансформаторное масло - 0,3 л керосин -0,7 л Вспомогательные средства: распылитель, лампа переносная (12В), лупа, мел | Виды работ, при которых проводится контроль: приемочный контроль Зоны контроля: Вся поверхность, кроме торцевых частей Критерии браковки: Трещины на оси не допускаются (ЦВ/3429) | |||||
поверхность оси в пределах зоны ДН. |
| Эскиз детали, траектория сканирования | |||||
2.5. Медленно переместить соленоид вдоль оси, одновременно нанося суспензию перед соленоидом в пределах зоны ДН (рис.2). 2.6.Осмотреть поверхность оси за движущимся соленоидом, обращая внимание на галтели шейки и предподступичной части. 2.7. Довести соленоид до другого торца оси. Начальное и конечное положения соленоида относительно двух торцов оси должно быть симметрично. 2.8. Прекратить нанесение суспензии, выключить соленоид. 2.9. Повторить контроль оси еще два раза п.п. 2.2-2.8, поворачивая ее на 120°±10°. При необходимости подтверждения результатов контроля воспользоваться переносным электромагнитом МЭД120. 2.10. Для размагничивания оси установить соленоид над одной из подступичной частей оси, включить соленоид. Медленно переместить его к шейке оси и отвести от нее на расстояние не менее 0,5 м. Выключить соленоид. Установить соленоид над другой подступичной част ью и повторит ь операцию. 2.11. Удалить с поверхности оси остатки суспензии, протерев ее ветошью. 2.12. Оформить результаты контроля. | | ||||||
| ||||||
| Контроль вихретоковый | Листов | ||||
Дата «__»____200_г. | Деталь: ролики подшипника Узел: подшипник | Марка стали: сталь ШХ15СГ Твердость 63 HRC Шероховатость: Ra 1,25 мкм. Цвет светлый | Лист 19 | |||
Тип вагона: пассажирский, грузовой Согласно РД 32.150-2000 | Требования документов по техническому обслуживанию и ремонту | |||||
Технологические операции | Средства контроля | |||||
1.Подготовка к работе 1.1. Проверить соединение электромеханического и электронного блоков жгутами. 1.2. Проверить заземление корпуса электронного блока. 1.3. Переключить тумблер СЕТЬ электронного блока в положение BK Л. При этом на панели электронного блока должны светиться все светодиодные индикаторы питания. 1.4. Нажатием кнопки РЕЖИМ+ перевести дефектоскоп в режим ввода текущей даты и времени. При необходимости выполнить коррекцию даты и времени. После нажатия кнопки > откорректировать текущее время кнопками 0-9. 1.5. Нажатием кнопки РЕЖИМ+ перевести дефектоскоп в режим ввода технологической информации для СОП. После нажатия кнопки > ввести номер комплекта СОП, поставляемого в комплекте дефектоскопа. После окончания ввода номера СОП нажать кнопку >. 1.6. Нажатием кнопки РЕЖИМ+ перевести дефектоскоп в состояние тестирования СОП.При этом убедиться в нормальном заряде аккумуляторной батареи. 1.7. Подающую кассету с комплектом СОП состыковать с направляющими электромеханического блока. 1.8. Нажатием кнопки ПУСК начать тестирование СОП. 1.9. При получении положительных результатов тестирования комплекта СОП дефектоскоп готов к контролю цилиндрических роликов подшипников. 2. Операции контроля. 2.1. Нажать кнопку РЕЖИМ - и перевести дефектоскоп в состояние готовности к вводу технологической информации для роликов.
2.2. Ввести вместо номера вагона нули. | Средства для очистки: обтирочный материал, щетки волосяные Дефектоскоп ВД-211.5 Стандартный образец СОП-НО-903 Вспомогательные средства: лупа, мел | Виды работ, при которых проводится контроль: При полном освидетельствовании колесной пары Зоны контроля: цилиндрическая поверхность Критерии браковки: Согласно инструкции 3- ЦВРК | ||||
Контроль магнитопорошковый | Листов | |||
НД на контроль: ЦВ/3429 РД 32.174-2000 РД 32.159-2000 | Узел: буксовый подшипник | Материал: сталь ШХ15СГ Шероховатость Ra 1,25 Цвет светлый Твердость HRC 63 | Способ контроля: СОН, Н 180 А/см | Лист 21 |
Деталь: Наружное кольцо подшипника | ||||
Тип вагона: грузовой, пассажирский | Согласно РД 32.159-2000 | |||
Средства контроля | Требования документов по техническому обслуживанию и ремонту | |||
Средства для очистки: Обтирочный материал, щетка волосяная. Дефектоскоп УМДП-01, СОП Магнитный индикатор: Порошок магнитный черный ТУ 6-36-05800165-1009-93 5 гр. Керосин 1 л. Вспомогательные средства: лупа, мел | Виды работ, при которых проводится НК: При полном освидетельствовании колесной пары. Зоны контроля: Вся поверхность Критерии браковки: Трещины не допускаются (З-ЦВРК-2001) | |||
Технологические операции | ||||
1. Подготовительные операции 1.2. Проверить уровень магнитной суспензии в баке: он должен быть ниже уровня крышки на 30 мм. 1.3. Перемешать магнитную суспензию в течение 5.. . 10 мин. Кольцо протереть ветошью. 1.4. Установить контрольное кольцо подшипника на опорные ролики так, чтобы оно находилось в центре соленоида. 1.5. Подвести кронштейн с соленоидом к кольцу подшипника. 1.6. Плотно прижать контактный стержень к площадке головки, повернув рукоятку на себя. 1.7. Перевести ручку галетного переключателя из среднего положения в положение «НАМАГНИЧИВАНИЕ». 1.8. Нажать кнопку «ЗАРЯД» и удерживать ее в нажатом положении до тех пор, пока показания вольтметра достигнут напряжения 280В. 1.9. Повторить п. 1.7. дважды, обеспечивая намагничивание детали 3-мя импульсами. 1.10. Освободить контактный стержень при помощи рукоятки эксцентрикового прижима, отвести кронштейн с соленоидом от опоры. 1.10.Полить кольцо магнитной суспензией. 1.11. Сравнить получившийся индикаторный рисунок с дефектограммой. 1.12. Размагнитить КО, поместив его в горизонтальной плоскости на кронштейне внутри соленоида, включить режим «РАЗМАГНИЧИВАНИЕ». Показание амперметра должно быть не менее 18А. Медленно и плавно повернуть ручку автотрансформатора против часовой стрелки до упора. Повернуть кольцо в горизонтальной плоскости на 90°. Переходе поворотом кольца па 90° и плавным поворотом ручки трансформатора против часовой стрелки повторить дважды. |
Деталь: кольцо наружное | ||
Узел: буксовый подшипник | Лист 22 | |
2.Операции контроля | ||
2.1.Установить проверяемое кольцо подшипника на опорные ролики, зацентровав его. | ||
2.2.Подвести намагничивающий соленоид к кольцу подшипника. Затянуть рукоятку эксцентрикового прижима. | ||
2.3.Перевести ручку галетного переключателя в положение «НАМАГНИЧИВАНИЕ». | ||
2.4.Нажать кнопку на пульте управления «ЗАРЯД» и удерживать ее до достижения напряжения 280В. | ||
2.5.Отпустить кнопку «ЗАРЯД» и дважды повторить подачу импульса. | ||
2.6.0свободить контактный стержень при помощи рукоятки эксцентрикового прижима и отвести кронштейн с соленоидом от опоры. | ||
2.7.Перевести галетный переключатель в исходное (среднее) положение. | ||
2.8.Нанести магнитную суспензию на верхнюю часть кольца. | ||
2.9.После стекания суспензии визуально проконтролировать наличие валиков магнитного порошка на поверхностях колец. | ||
2.10.Повернуть дважды кольцо по часовой стрелки на 120° с повторением переходов 2.8, 2.9 , обеспечив полный контроль поверхности | ||
2.11.При отсутствии дефектов произвести размагничивание кольца. | ||
2.12.0твести размагничивающий соленоид от кольца подшипника. | ||
2.13.Промыть кольцо подшипника в керосине, протереть ветошью. | ||
2.14.Занести результаты контроля в рабочий журнал. | ||
Эскиз детали, схема намагничивания | ||
|
|
Колёсная пара |
Листов |
|
Лист 23 | ||||||||
| ||||||||||||
Обод колеса |
| |||||||||||
| Наименование операции | Наименование, марка материала | ||||||||||
| Контроль ультразвуковой | Сталь марки 1 и сталь марки 2 ГОСТ 10791 , HRC 20, Rz> 80 Сталь марки Т- ТУ 0943-157-01124324-2003, НВ 320-360, Rz > 80 | ||||||||||
Наименование оборудования | НД на контроль | Обозначение ИОТ | ||||||||||
Дефектоскоп ультразвуковой типа УДС2 - 32,ПЭП П121 -2,5-40-. Устройство сканирования УСК-4, СО-2 (СО-ЗР) | Технологическая инструкция ТИ 07.16-98 | НОТ Р—068— 022 | ||||||||||
Контролируемый объект № черт | Объем контроля | Угол ввода а, град | Частота f, МГц | Поверхность сканирования | Браковочная чувствительность, дБ | Зона контроля | Особые указания | |||||
100.10.001-01 100.10.001-02 100.10.001-03 100.10.001-04 13.45.1042-01 | 100% | 40 | 2,5 | Внутренняя грань обода | Устанавливается по эталонному отражателю СО-2 (СО-ЗР) | Устанавливается в соответствии с картой эскизов | Контроль проводится в соответствии с ТИ 07.16-98 | |||||
1. Подготовить дефектоскоп к работе в соответствии с настроечной картой. 2. Установить режим 9 в соответствии с картой эскизов и убедиться в идентичности соответствующих форматов настройки. 3. Подключить ПЭП к разъему «2,5 МГц», установить кассету с ПЭП на предварительно смазанную минеральным маслом контактную поверхность СО-2 в в соответствии с картой эскизов так, чтобы метка на кассете с ПЭП совпадала с направлением прозвучивания, а передняя грань кассеты с ПЭП находилась возле метки 20° на СО и получить эхо-сигнал от бокового цилиндрического отражателя в СО 0 6 мм и на глубине 44 мм. Небольшими перемещениями и поворотами кассеты с ПЭП по поверхности СО, не меняя значения усиления А, убедиться, что максимальное значение, которое принимает параметр К составляет (14±2) дБ. Занести в журнал. 4. Занести значение усиления А в журнал. 5. Провести контроль в режиме 9, сканируя и отмечая мелом участки колеса, соответствующие наличию в стробе эхо сигнала, вызывающего срабатывание звукового индикатора и светового индикатора «ДЕФЕКТ» 6. Небольшими смещениями ПЭП добиться максимальной амплитуды эхо-сигнала от дефекта (максимального значения параметра К). Если параметр К равен или превышает 6 дБ. записать значение К в журнал контроля. 7. Колесо браковать, если амплитуда эхо-сигнала превосходит пороговый уровень на 6 дБ (параметр К>6 дБ ) 8. Результаты контроля записать в журнал. | ||||||||||||
| ВРЗ ОАО | Колёсная пара | Листов | Лист 24 | ||||
| Ось колесной пары РУ-1 |
| ||||||
| Наименование операции | Наименование, марка материала | ||||||
| Контроль ультразвуковой | Сталь Ос. В ГОСТ 4728 | ||||||
Наименование оборудования | ПД на контроль | Обозначение ИОТ | ||||||
Дефектоскоп ультразвуковой УДС2 - 32; ПЭП П131 - 2,5 - 0°, П121 - 2,5 - 50° прямой и наклонный; СО-2; КО 07.09.01-РУ-1 | Технологическая инструкция ТИ 07.16-98 | ИОТ Р-068-022 | ||||||
Контролируемый объект № черт | Объем контроля | Угол ввода а, град | Частота f, МГц | Поверхность сканирования | Браковочная чувствительность, дБ | Зона контроля | Особые указания | |
100.10.0 13-5 | 100% | 0; 50. | 2,5 | Зарезьбовая канавка оси, цилиндрическая поверхность шейки. | Устанавливается по эталонному отражателю КО | Устанавливается в соответствии с таблицей | ||
1. Подготовить дефектоскоп к работе в соответствии с настроечной картой. Проверка параметров настройки дефектоскопа производится в режиме 01 А. Подключить к дефектоскопу комбинированный ПЭП, установить тумблер на ПЭП в положение «0» и установить ПЭП на смазанную минеральным маслом зарезьбовую канавку КО 07.09.01-РУ1. Переметая ПЭП, установить его в положение, при котором амплитуда эхо-сигнала от противоположного торца оси максимальная. Установить режим изменения параметра « » (усиление) на экране ЖКИ и довести амплитуду эхо-сигнала до порогового уровня (середина экрана ЭЛТ); при этом должны сработать звуковой и световой индикатор «ДЕФЕКТ» и появится надпись «ДЕФЕКТ» на экране ЖКИ. Установить символьный знак «*» перед словом «ПОИСК» и нажать кнопку [ ВВОД J. При этом на экране ЭЛТ дефектоскопа будет изображена развертка со стробом, длина которого равна зоне контроля в режиме 01А (средняя часть оси и дальняя подступичная часть кроме зоны под внешней кромкой ступицы), и с коротким стробом, в котором находится эхо-сигнал от противоположного торца оси. 11еремещая ПЭП по зарезьбовой канавке, найти такое его положение, при котором амплитуда эхо-сигнала от модели дефекта (пропила) в контролируемой зоне максимальна. При этом на лицевой панели должен светиться индикатор «ДЕФЕКТ», на экране ЖКИ появляются надпись «ДЕФЕКТ», и значения параметров К и R. При запрограммированном значении параметра А, параметр К должен принять значение 6...8 дБ, что свидетельствует о правильной настройке чувствительности. В противном случае - перепрограммировать. Проверить параметры настройки дефектоскопа в режимах 01Б (ближняя шейка и предподступичная часть оси), 15 (ближняя подступичная часть оси под внешней кромкой ступицы), 16 (уточнение результатов УЗК путем сканирования по цилиндрической поверхности средней части оси). 2. Проведение контроля. Выполнить сканирование, перемещая ПЭП по смазанной маслом зарезьбовой канавке контролируемой оси или последовательно устанавливая его в 20 - 25 точках. При появлении в зоне контроля эхо-сигнала от дефекта с амплитудой, превышающей среднюю линию экрана ЭЛТ, на лицевой панели должен светиться индикатор «ДЕФЕКТ», на экране ЖКИ появляются надпись «ДЕФЕКТ», и значения параметров К и R (расстояние до дефекта в мм). 3. Провести контроль с противоположной стороны оси. 4. Ось колесной пары подлежит браковке, если: отсутствует сигнал от противоположного торца оси при сквозном прозвучивании (ослабление сигнала от противоположного торца оси (донного эхо-сигнала) относительно эхо-сигнала, измеренного на СО-2, превышает 22 дБ); в зоне контроля обнаружен эхо-сигнал, имеющий параметр К >6 дБ. Результаты контроля занести в журнал. | ||||||||
3 ОХРАНА ТРУДА
Охрана труда — система сохранения жизни и здоровья работников в процессе трудовой деятельности, включающая в себя правовые, социльно - экономические, санитарно - гигиенические, лечебно - профилактические, реабилитационные и иные мероприятия.
Работа по охране труда в ремонтном вагонном депо Кочетовка направлена на создание благоприятных условий труда, всемерное сокращение ручного и тяжелого физического труда, предупреждение производственного травматизма и профессиональных заболеваний, строгое соблюдение действующих законодательных и нормативных актов по охране труда.
Основной целью управления работой по охране труда на всех уровнях управления и во всех хозяйствах отделения является обеспечение здоровых и безопасных условий труда, предотвращение воздействия на работающих опасных и вредных производственных факторов, предупреждение производственного травматизма и профессиональных заболеваний.
Работа по охране труда в вагонном депо проводится в соответствии с перспективными отраслевыми программами, годовыми программами и планами номенклатурных мероприятий по охране труда, планами организационно-технических, санитарно-гигиенических мероприятий по предупреждению производственного травматизма и дальнейшему улучшению условий труда.
Обеспечение безопасных условий труда, нормализация санитарно-гигиенических условий на рабочих местах, в производственных помещениях и на территориях.
Безопасность условий труда и санитарно-гигиенических условий на рабочих местах в производственных помещениях и на территориях обеспечивает работодатель путем выполнения требований безопасности
труда к организации и содержанию рабочих мест, производственных
помещений, территории, а также соблюдения санитарных норм и мер безопасности при разработке и внедрении технологических процессов и новой техники.
Достигается:
- аттестацией рабочих мест по условиям труда и травмобезопасности;
- своевременным контролем опасных и вредных производственных факторов на рабочих местах;
- сокращением применения материалов и веществ, являющихся источниками опасных и вредных производственных факторов;
- устранением причин возможного возникновения опасных и вредных производственных факторов;
- содержанием в исправном состоянии средств коллективной защиты от опасных и вредных производственных факторов;
- обеспечением работников необходимыми санитарно-бытовыми помещениями и устройствами.
Обеспечение работающих средствами индивидуальной защиты
Обеспечение работников ремонтного вагонного депо Кочетовка, спецодеждой и спецобувью и другими средствами индивидуальной защиты осуществляются в соответствии с установленными нормами за счет средств работодателя.
1. Администрация обязана обеспечить в соответствии с установленными сроками испытания и проверку исправности предохранительных приспособлений, диэлектрических галош и перчаток и т.д.
2. Выдаваемые рабочим и служащим спецодежда, спецобувь и предохранительные приспособления должны отвечать требованиям ГОСТов и технических условий быть пригородными и удобными для пользования.
3. Выдачу, хранение и поддержание в эксплуатационном состоянии средств индивидуальной защиты организует работодатель в установленном порядке.
Требования охраны труда во время работы дефектоскописта.
1. При работе с дефектоскопом следует пользоваться руководством по его эксплуатации.
2.Дефектескописту в процессе работы с дефектоскопом запрещается касаться токоведущих частей и электропневматического привода, а также касаться во время работы движущихся и вращающихся частей.
З.Во время работы не следует подвергать дефектоскоп резким толчкам и ударам.
4.При переносе дефектоскопа на новое рабочее место не допускается свисание и волочение проводов по полу.
5.До начала дефектоскопирования детали должны быть закреплены.
6.Перед проведением дефектоскопирования все детали подлежат обязательной мойке и очистке от загрязнений, краски и ржавчины до основного металла. Зачищать детали от загрязнений дефектоскопист должен в защитных очках.
6.При работе с дефектоскопом должны применяться переносные электрические светильники с напряжением питания не выше 36 В.
7.При работе с дефектоскопом надо следить за тем, чтобы не возникло натяжение сетевого и соединительного провода, а так же не было наездов на них колесной парой или транспортным средством.
8.Если при прикосновении к корпусу прибора ощущается действие электротока, работу следует немедленно прекратить, дефектоскоп отключить от сети и сообщить мастеру участка.
9.По окончанию работы дефектоскоп необходимо отключить от сети. Переносной дефектоскоп необходимо отключать от распределительного щита, чтобы провода не оставались под
напряжением.
Требования охраны труда по окончании работы дефектоскописта.
По окончании работы дефектоскопист должен:
- отключить дефектоскоп или установку от сети, очистить соленоиды и другие устройства, соприкасающиеся с магнитной суспензией, от загрязнений и остатков суспензии и провести профилактические работы в соответствии с тебованиями технической документации на дефектоскоп или установку;
- убрать инструмент, приборы в специально предназначенные для них места или кладовые;
- собрать отходы производства в виде использованной ветоши, отработанных дефектоскопических материалов в металлический ящик с крышкой;
- про окончании работы следует привести в порядок рабочее место, убрать инструменты и приспособления;
- обо всех неисправностях, замеченных во время работы, дефектоскопист должен сообщить мастеру.
Отзыв о преддипломной практике
Костикова А.С. проходила производственную практику (преддипломную) в период с 20 апреля 2020 г. по 17мая 2020г. в производственном участке Тамбов пассажирского вагонного депо Воронеж – структурного подразделения Приволжского филиала АО «ФПК».
В период прохождения практики изучила структуру предприятия, его основные задачи и направления деятельности. Костикова А.С. ознакомился с организацией и технологией работы подготовки пассажирских вагонов в рейс
Показал способность проводить анализ результатов производственно – хозяйственной деятельности производственного участка, трудоемкости операций и работ, нормы расходов и эффективное использование материалов.
Особое внимание в процессе прохождения практики уделено вопросам охраны труда, инструкциям по охране труда рабочих профессий и видам работ.
В период практики Костикова А.С. освоила общие и профессиональные компетенции
Программа преддипломной практики выполнена в полном объёме.
Дата добавления: 2023-01-08; просмотров: 121; Мы поможем в написании вашей работы! |
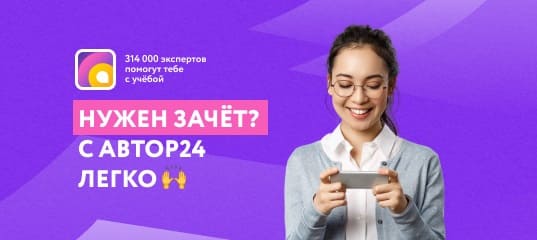
Мы поможем в написании ваших работ!