Метод расчета прокаливаемости на основе химического состава стали
Лабораторная работа 13
Испытания стали на прокаливаемость
Методом торцевой закалки
Цель работы
Изучить методы испытаний стали на прокаливаемость.
Получить практические навыки проведения испытаний методом торцевой закалки.
Освоить расчетный метод определения прокаливаемости стали.
Задание
Охарактеризовать факторы, влияющие на кинетику изотермического превращения переохлажденного аустенита.
Определить степень прокаливаемости различных марок стали.
Оценить влияние легирующих элементов на прокаливаемость стали.
Определить расчетным методом полосу прокаливаемости стали (по заданию преподавателя).
Общие сведения
Под закаливаемостью понимают способность стали повышать твердость в результате закалки.
Закаливаемость стали определяется, в первую очередь, содержанием в стали углерода. Чем больше в мартенсите углерода, тем больше его твердость. Легирующие элементы оказывают относительно небольшое влияние на закаливаемость.
Прокаливаемостью называют способность стали получать закаленный слой с мартенситной или троостито-мартенситной структурой и высокой твердостью, простирающейся на ту или иную глубину. За глубину закаленного слоя обычно принимают расстояние по сечению детали от поверхности до района с полумартенситной структурой (50% мартенсита и 50% троостита).
Диаметр заготовки, в центе которой после закалки в данной охлаждающей среде образуется полумартенситная структура, называют критическим диаметром D50. Величина критического диаметра определяет размер сечения изделия, прокаливающегося насквозь, т. е. получающего высокую твердость по всему сечению, а после отпуска – и высокие механические свойства по всему сечению.
|
|
Прокаливаемость тем выше, чем меньше критическая скорость закалки, т. е. чем выше устойчивость переохлажденного аустенита. Поэтому все факторы, уменьшающие величину критической скорости закалки (повышающие устойчивость переохлажденного аустенита), увеличивают прокаливаемость.
Легированные стали вследствие более высокой устойчивости переохлажденного аустенита и, соответственно, меньшей критической скорости охлаждения, прокаливаются на большую глубину, чем углеродистые. Сильно повышают прокаливаемость марганец, хром, молибден и малые присадки бора (0,003 – 0,005%). Прокаливаемость особенно возрастает при введении в сталь нескольких легирующих элементов. Критический диаметр легированной стали может достигать нескольких сотен миллиметров.
Необходимо отметить, что устойчивость переохлажденного аустенита повышается только при том условии, что легирующие элементы растворены в аустените. В случае, если они присутствуют в виде избыточных фаз (карбидов, нитридов, карбонитридов и т. п.), то могут увеличить критическую скорость закалки, так как служат готовыми зародышами, облегчающими распад аустенита. Карбиды (карбонитриды) титана, ниобия и ванадия при нормально принятом ( для углеродистых сталей) нагреве под закалку обычно не растворяются в аустените и понижают прокаливаемость.
|
|
Сильно влияет на прокаливаемость величина зерна аустенита. В углеродистой стали при укрупнении зерна от 8-го номера до 1-2 глубина закаленного слоя возрастает в 2-3 раза. Поэтому повышение температуры и увеличение длительности нагрева при закалке приводят к росту величины прокаливаемости.
Прокаливаемость стали в небольших сечениях (Æ до 15 – 25мм) можно практически определить по виду излома закаленных образцов или по распределению твердости по сечению. Для этого образец ломают или разрезают и по диаметру сечения определяют твердость.
Прокаливаемость стали по стандарту находят методом торцевой закалки (по Джомини). Цилиндрический образец определенной формы и размеров (диаметр 25 мм, длина 100 мм), нагретый до заданной температуры, охлаждают водой с торца на специальной установке. После охлаждения измеряют твердость по длине (высоте) образца. Так как скорость охлаждения убывает по мере удаления от торца, то будет уменьшаться и твердость.
|
|
Рисунок 1 . Схема испытания стали на прокаливаемость методом
торцевой закалки
Результаты испытаний выражают графически в координатах твердость-расстояние от торца. На Рис.1а представлены результаты подобных испытаний для двух сталей – углеродистой и низколегированной с одинаковым содержанием углерода. Из рисунка видно, что легирование, не изменяя начальную твердость, существенно увеличивает прокаливаемость.
Для более детальной оценки прокаливаемости стали целесообразно на этот рисунок нанести значение твердости полумартенситной зоны.
|
|
На практике с достаточной точностью критический диаметр может быть определен по Рис. 3.
|
|
|

Для этого на оси абсцисс надо отложить расстояние от охлаждаемого торца до пересечения с кривой закалки в масле или в воде. Горизонталь, проведенная от этой точки до ординаты, укажет величину D50.
Значение критического диаметра зависит не только от химического состава и структуры стали, но и от характера охлаждающей среды. Для возможности сравнения между собой различных сред вводится понятие интенсивности охлаждения Н. Значения этой величины для ряда сред представлены в Табл. 1.
Таблица 1
Движение | Интенсивность закалки Н | |||
воздух | масло | вода | соленая вода | |
Отсутствует | 0,02 | 0,25-0,30 | 0,9-1,0 | 2,0 |
Слабое | ---- | 0,30-0,35 | 1,0-1,1 | 2,0-2,2 |
Среднее | ---- | 0,35-0,40 | 1,2-1,3 | ---- |
Хорошее | ---- | 0,40-0,50 | 1,4-1,5 | ---- |
Сильное | ---- | 0,50-0,80 | 1,6-2,0 | ---- |
Резкое | 0,08 | 0,80-1,10 | 4,0 | 5,0 |
Следует заметить, что колебания в химическом составе, различная циркуляция охлаждающей среды и другие факторы могут существенно изменить прокаливаемость стали одной и той же марки, но разных плавок. Поэтому прокаливаемость стали характеризуют не кривой, а так называемой полосой прокаливаемости (Рис.4).
|





|
Сравнивая рисунки 3 и4 видим, что в легированной стали твердость по мере удаления от торца спадает не так круто, то есть ее прокаливаемость выше
Имея полосу прокаливаемости, можно считать, что при любых изменениях химического состава в пределах марочного состава прокаливаемость данной марки стали всегда будет находиться в пределах этой полосы.
Метод расчета прокаливаемости на основе химического состава стали
Этот расчетный метод был разработан на основе статистического анализа тысяч термических обработок сотен различных марок углеродистых и низколегированных сталей. В Табл. 2 представлена область химических составов этих сталей.
Таблица 2
Элемент | Диапазон, % | Элемент | Диапазон, % |
Углерод | 0,1...0,70 | Хром | £ 1,35 |
Марганец | 0,50...1,65 | Никель | £ 1,50 |
Кремний | 0,15...0,60 | Молибден | £ 0,55 |
Расчет прокаливаемости начинается с определения идеального критического диаметра стали. Идеальный критический диаметр Dи- это диаметр круглого стального стержня, у которого при закалке в идеальном охладителе в центре стержня образуется полумартенситная структура (50% мартенсита и 50% троостита). В свою очередь идеальный охладитель - это среда, в которой поверхность закаливаемой детали мгновенно принимает температуру охладителя. Иными словами - это охлаждающая среда, для которой интенсивность охлаждения Н равна бесконечности (обычная вода обладает характеристиками, близкими к идеальному охладителю)
Расчет идеального диаметра Dи, для сталей, не содержащих бора, основан на данных Табл.3 и П.1, где представлены факторы - множители для каждого компонента стали. Эти факторы, перемножаясь, дают значение Dи. В этой таблице значения Dи получаются в дюймах. Чтобы получить значения в миллиметрах, нужно умножить на 25,4.
Влияние фосфора и серы не учитывается, так как они, действуя в противоположном направлении в отношении прокаливаемости, практически друг друга нейтрализуют.
При определении прокаливаемости стали следует учитывать размер зерна. Все нижеприведенные расчеты относятся к зерну 7-го номера. Как известно, при уменьшении размера зерна прокаливаемость уменьшается.
Далее рассмотрим пример расчета Dи для хромомолибденовой стали типа 20ХМ.
Таблица 3
Элемент | Содержание,% | Фактор-множитель (из Табл.П. 2) |
Углерод | 0,22 | 0.119 |
Марганец | 0,80 | 3,667 |
Кремний | 0.18 | 1.126 |
Никель | 0.10 | 1.036 |
Хром | 0.43 | 1.929 |
Молибден | 0,25 | 1,75 |
Медь | 0,10 | 1,04 |
Отсюда Dи = 0,119*3,667*1,126*1,036*1,929*1,75*1,04 =1.79дюймов, в переводе на систему СИ: 1,79дюймов =45,5 мм.
Бор играет особую роль среди легирующих элементов, увеличивающих прокаливаемость стали. Достаточно ввести в сталь несколько тысячных долей процента бора и прокаливаемость стали резко увеличивается. Поэтому идеальный критический диаметр (Dи) для борсодержащих сталей подсчитывается особым образом.
Для примера рассмотрим сталь следующего состава, приведенного в Табл. 4:
Таблица 4
C, % | Mn, % | Si, % | Ni, % | Cr, % | Mo, % | B, % | Dи, мм |
0,29 | 1,25 | 0,20 | 0,13 | 0,07 | 0,03 | 0,0015 | 31,5 |
В Табл.4 Dи = 31,5 – рассчитанный по вышеописанной схеме идеальный критический диаметр данной стали без учета наличия бора.
Затем рассчитаем фактор легированности FL: FL = рассчитанный Dи (без бора) / фактор–множитель для углерода = 31,5 мм / 0,157*25,4 = 8.
Далее, определим фактор-множитель для бора из Табл.П. 2. Для нашего примера (содержание углерода в стали 0,29 % , а фактор легированности FL = 8) фактор-множитель для бора равен 2.36 (с интерполяцией).
После этого можно рассчитать идеальный критический диаметр для стали с бором: (Dи) В = Dи (без бора) * фактор-множитель для бора = 31,5 * 2,36,
(Dи) В = 74,3 мм
Дата добавления: 2023-01-08; просмотров: 41; Мы поможем в написании вашей работы! |
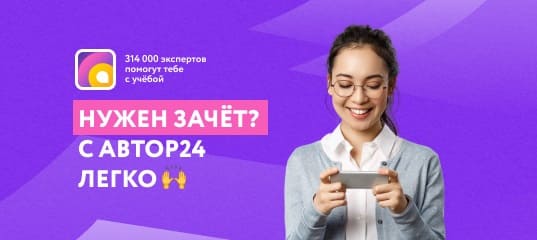
Мы поможем в написании ваших работ!