Техника безопасности при проведении сварочных работ
При производстве сварочных работ лица, занятые на выполнении сварочных работ обязаны применять при работе средства индивидуальной защиты в соответствии с установленными нормами и правилами. Электросварочные работы выполняют током напряжением 70-110 В. Это напряжение опасно для жизни и здоровья людей, поэтому необходимо строго соблюдать правила технической эксплуатации электросварочных установок, а также правила техники безопасности и производственной санитарии при электросварочных работах.
При проведении электросварочных работ непосредственно на машине необходимо выполнить следующие действия:
· Перед началом работы заземлить раму машины и кузов
· Топливный бак закрыть листом железа или асбеста от попадания на него искр
· При сварочных работах под топливным баком или поблизости от него бак необходимо снять.
Для проведения сварочных работ в местах недоступных непосредственно с земли разрешается работать только с лестницы-стремянки.
Основную опасность при проведении газосварочных работ представляют:
· Отравление ацетиленом при вдыхании
· Ожоги брызгами расплавленного металла
· Взрывоопасность ацетилена при нагревании и избыточном давлении
· Взрывоопасность смесей ацетилена с кислородом и воздухом
· Взрывоопасность кислородных баллонов.
Кислородные баллоны окрашивают в голубой цвет, а ацетиленовые - в белый. Хранят газовые баллоны в вертикальном положении и отдельно друг от друга: порожние и наполненные, кислородные и ацетиленовые. Баллоны с газом должны быть укомплектованы навернутыми предохранительными колпаками. Совместная перевозка кислородных и ацетиленовых баллонов запрещается. В летнее время баллоны следует защищать от действия прямых солнечных лучей. При выполнении газосварочных работ сварщики и резчики должны предохранять глаза защитными очками закрытого типа со стеклами со специальными светофильтрами.
|
|
Часть 3. Наварка поврежденных поверхностей.
Наиболее распространенным и простым способом восстановления деталей машин является электродуговая наплавка (наварка). Наплавка – это нанесение слоя металла на поверхность заготовки или изделия посредством сварки плавлением (ГОСТ 2601-84). Восстановительная наплавка (наварка) применяется для восстановления первоначальных размеров изношенных или поврежденных деталей. Наплавка деталей и восстановление изношенных деталей наплавкой – эффективный и экономичный способ продления срока службы деталей машин. В зависимости от наличия технологической оснастки и материалов, необходимых для ремонтных работ применяют наплавку: 1) под слоем флюса; 2) вибродуговую в среде углекислого газа, в потоке воздуха и водяного пара; 3) электроконтактную сварку. Наплавка может производиться в один или несколько слоев на различные поверхности: плоские, цилиндрические, конические и другие сложные формы поверхности. Толщина слоя наплавки может изменяться в широких пределах – от долей миллиметра до десятков миллиметров. При наплавке поверхностных слоев, химический состав наплавленного металла существенно отличается от химического состава основного металла. Для правильной организации деталей к наплавке и выполнения наплавочных работ необходимо после осмотра и замеров износа деталей составить карту технологического процесса ремонта. В ней должны быть отражены:1) причины и характер износа; 2) условия работы деталей; 3) объем работ; 4) вид и способ наплавки; 5) марка и диаметр электродов или проволок; 6) режим и технология наплавки; 7) время на выполнение работ; 8) последовательность операций; 9) припуск на механическую обработку;10) необходимость предварительной и последующей термической обработки.
|
|
Контроль качества сварных соединений
1. Контроль качества сварных соединений, проводимый при изготовлении, реконструкции, ремонте, монтаже службой контроля продукции (ОТК), должен осуществляться внешним осмотром и измерениями, механическими испытаниями, методами неразрушающего контроля, предусмотренными нормативными документами.
|
|
2. Контроль качества сварных соединений должен проводиться после проведения термической обработки (если она является обязательной для данного сварного соединения). Результаты контроля сварных соединений должны быть зафиксированы в соответствующих документах (журналах, картах и т.п.).
3. Все сварные соединения подлежат внешнему осмотру и измерениям с целью выявления в них следующих возможных наружных дефектов:
а) непараллельности или неперпендикулярности осей соединяемых элементов;
б) смещения кромок соединяемых элементов;
в) отступления размеров и формы швов от чертежей (по высоте, катету и ширине шва, по равномерности усиления и т.п.);
г) трещин всех видов и направлений;
д) наплывов, подрезов, прожогов, незаваренных кратеров, непроваров, пористости и других технологических дефектов.
Перед внешним осмотром поверхность сварного шва и прилегающих к нему участков основного металла шириной не менее чем по 20 мм в обе стороны от шва должна быть очищена от шлака, брызг, натеков металла и других загрязнений.
|
|
Осмотр и измерение стыковых сварных соединений расчетных элементов должны производиться по всей протяженности соединения. Если внутренняя поверхность сварного соединения недоступна для осмотра, осмотр и измерение производятся только с наружной стороны.
4. Контроль сварных соединений просвечиванием должен проводиться в соответствии с ГОСТ 7512, ультразвуковой контроль - с ГОСТ 14782 и другими нормативными документами. Контроль сварных соединений элементов расчетных металлоконструкций проводят только после устранения дефектов, выявленных внешним осмотром. При этом обязательному контролю подвергают начало и окончание сварных швов стыковых соединений поясов и стенок коробчатых металлоконструкций балок, колонн, стрел.
При любом методе контроля суммарная длина контролируемых участков сварных соединений устанавливается нормативными документами и должна составлять не менее:
50% от длины стыка - на каждом стыке растянутого пояса коробчатой или решетчатой металлоконструкции;
25% от длины стыка - для всех остальных стыковых соединений;
25% от длины шва - для других видов сварных соединений, указанных в рабочих документах.
Перед проведением просвечивания соответствующие участки сварного соединения должны быть промаркированы с таким расчетом, чтобы их можно было легко обнаружить на снимках.
5. Оценка качества сварных соединений по результатам внешнего осмотра и неразрушающего контроля должна производиться в соответствии с техническими условиями на изготовление, реконструкцию, ремонт, монтаж кранов, которые должны содержать нормы оценки качества сварных соединений, исключающие выпуск изделий с дефектами, снижающими их прочность и эксплуатационную надежность.
6. В сварных соединениях не допускаются следующие дефекты, браковочные признаки которых превышают величины, указанные в нормативных документах:
а) трещины всех видов и направлений, расположенные в металле шва, по линии сплавления и в околошовной зоне основного металла, в том числе микротрещины, выявляемые при микроскопическом исследовании;
б) непровары (несплавления), расположенные на поверхности по сечению сварного соединения;
в) непровары в вершине (корне) угловых и тавровых соединений, выполненных без разделки кромок;
г) поры, расположенные в виде сплошной сетки;
д) подрезы и наплывы (натеки);
е) незаваренные кратеры;
ж) свищи;
з) незаваренные прожоги в металле шва;
и) прожоги и подплавления основного металла (при стыковой контактной сварке труб);
к) смещения кромок выше нормы, предусмотренной чертежами.
7. Качество сварных соединений считается неудовлетворительным, если в них при любом виде контроля будут обнаружены внутренние или наружные дефекты, выходящие за пределы норм, установленных нормативными документами на изготовление, реконструкцию, ремонт и монтаж.
8. При выявлении во время неразрушающего контроля недопустимых дефектов в сварных соединениях контролю должно быть подвергнуто все соединение. Дефектные участки сварных швов, выявленные при контроле, должны быть удалены механическим способом и переварены.
Контрольные вопросы:
1. В соответствии с какими нормативными документами должны выполняться сварочные работы
2. Какие требования предъявляются к сварочным материалам
3. При каких условиях производится выполнение сварочных работ
4. Назначение маркировки, применяемой для сварных соединений
5.Перечислить последовательность операций, указанных в технологической карте производства сварочных работ
6. Какие требования предъявляются к сварочным работам при ремонте металлоконструкций
7. Назовите последовательность операций (технологию) заварки трещин элементов металлоконструкций
8.Что такое наплавка и для чего она применяется
9. Назвать методы контроля сварных соединений
10. Какие дефекты не допускаются в сварных соединениях
Литература:
Дополнительная литература: Охрана труда на автомобильном транспорте: учеб. Пособие для нач. проф. Образования / В.С. Кланица – М: Издательский центр «Академия», 2010.
Интернет – ресурсы: www.websvarka.ru
Дата добавления: 2022-12-03; просмотров: 26; Мы поможем в написании вашей работы! |
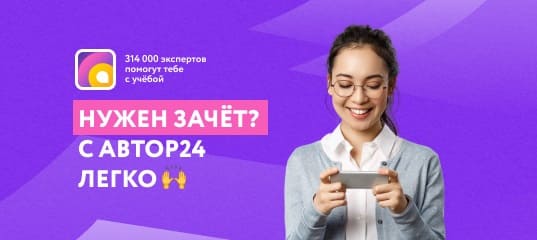
Мы поможем в написании ваших работ!