Технології Нанесення лакофарбних покриттів
Для того щоб покриття забезпечувала зазначені властивості, необхідно щоб товщина висохлої плівки була дорівнює 100-120 мкм (для площі в 1м2 порядку 200 мл фарби). У разі використання рідкої фарби на вертикальній поверхні, необхідно буде нанести близько 4-5 шарів. Даний результат можна отримати і за один прохід, використовуючи високоякісні тиксотропні фарби. Дана фарба розріджується при механічному впливі і гусне в стані спокою
37 . Технологі ї покриття деталей пластмасамиВідновлення деталей напилюванням пластмасВідновлення зношених деталей до номінального або ремонтного розміру часто застосовують напилювання пластмас.Сутність методу в наступному: деталь, після проведення відповідних підготовчих операцій, нагрівають до температури точки плавлення порошку, застосовуваного для напилювання. Звичайно ця температура становить 553...573 ДО (280...300°С). Після нагрівання деталь опускають у порошок, що перебуває у зваженому стані в повітряному потоці. Порошок пластмаси, стикаючись із деталлю, осідає на її поверхню й спікається. Товщина шаруючи пластмаси залежить від часу напилювання й від теплоємності деталі.Ємність для порошку відділяється від ємності для повітря за допомогою перегородки.Завданням поділяючої перегородки є рівномірна подача повітря в ємність із порошком. Потік повітря приводить порошок у зважене (псевдозжижений) стан. Сама перегородка може бути виготовлена з пористої кераміки, але для цієї мети придатна й повсть товщиною близько 10 мм. Над перегородкою на висоті близько 10 мм доцільно встановити металеву сітку, що запобігає падіння деталі на перегородку. Тим самим виключається склеювання деталі з перегородкою.Для покриття пластмасою деталей великого розміру порошок насипають прямо на нагріту деталь, повільно обертаючи її при цьому.
Пластмаси для напилювання вибирають із поліамідів, які під дією теплоти плавляться. Залежно від вимог до покриттів із пластмас можна застосовувати різні наповнювачі, наприклад дисульфід молібдену й графить, які змінюють і поліпшують деякі фізико-механічні властивості покриттів.
Технологія напилювання пластмас наступна:1) очищення, знежирення деталі (наприклад, трихлоретиленом);
|
|
2) дефектація деталі;3) підготовка поверхонь, що покриваються, яка включає в себе механічну обробку, зняття фасок 2...5 мм, а також підвищення шорсткості поверхні шляхом піскоструминної обробки;4) нагрівання деталі до температури плавлення пластмаси, звичайно до 473...573 К, тобто 200...300°С;5) напилювання пластмаси. Воно може бути здійснено приміщенням деталі у зважений порошок пластмаси або насипанням порошку на деталь при повільному обертанні її;6) охолодження деталі при відсутності руху повітря;7) обробка деталі до необхідного розміру;8) контроль якості покриття.Між шаром пластмаси й основним матеріалом утвориться адгезійне з'єднання. Тому необхідно прагнути до того, щоб дотична поверхня була найбільша. Для цієї мети застосовують піскоструминну обробку.Основною умовою міцного з'єднання є правильно підібрана температура нагрівання. Результати досвідів показали, що найбільш високі міцносні властивості забезпечуються при температурі 553...573 К (280...300°С) (рис. 115). Розмір часток порошку також значно впливає на міцність зчеплення (рис. 116). Перед напилюванням порошок пластмаси необхідно висушити. Температура сушіння близько 343...353 К, тобто 70...80°З, а час сушіння близько 24 год.
|
|
38. Електрофізичне та електрохімічне розмірне оброблення деталей Постійне зростання вимог до якості і надійності виробів зумовлює створення нових методів розмірної обробки та застосування технологій, які забезпечують підвищення стійкості деталей до зношування, корозійної стійкості до дії агресивних речовин та покращання інших експлуатаційних показників. До таких методів обробки, які вже знайшли досить широке застосування в сучасному машинобудуванні, належать електрофізичні та електрохімічні методи обробки.
|
|
Значною перевагою цих методів перед різанням є:
• можливість обробки профілів складної форми копіюванням форми інструмента;
• здатність до обробки матеріалів будь-якої твердості і в’язкості;
• можливість обробки криволінійних і спіральних отворіа виконання дуже малих отворів, вузьких і глибоких шліців;
• відсутність спотворень структури матеріалів, з яких виготовляють деталі;
• можливість використання інструментів, які поступаються за міцністю матеріалам, що піддаються обробці;
• підвищення продуктивності праці та спрощення обладнання при обробці особливо складних профілів деталей.
Всі види електрофізичних та електрохімічних методів обробки можна поділити на такі категорії: електророзрядні, електрохімічні, ультразвукові, променеві та комбіновані.
В усіх цих методах обробки зняття припуску відбувається за рахунок електричної або хімічної ерозії, а отже, загальним недоліком методів обробки, які розглядаються, є суттєве підвищення енергоємності процесів. Але з економічного погляду цей недолік повністю виправдується підвищенням продуктивності праці та наявності можливості автоматизації виробничих процесів. Вважається, що техніко-економічний ефект від застосування фізико-хімічних методів обробки полягає в тому, що час обробки фасонних поверхонь зменшується в 2 - 3 рази, а складних - в 5-10 разів порівняно з обробкою різанням.
|
|
ЕЛЕКТРОХІМІЧНА ОБРОБКА МЕТАЛІВ
Методи електрохімічної обробки матеріалів засновані на хімічних процесах, що виникають у результаті проходження електричного струму через ланцюг, утворений провідниками (електродами) і рідиною ,що знаходиться між ними (електролітом). Принципові схеми такого ланцюга (електролітичного осередку, ванни) показані на рис.10.
У цій главі розглянуті лише ті методи електрохімічної обробки , при яких відбувається видалення деяких кількостей металу з оброблюваної заготовки і їхній перехід у неметалічний стан.Основна увага виділена розмірній електрохімічній обробці.
Особливості електрохімічної розмірної обробки:
продуктивність обробки досягає 50 000 мм3/мин і вище;
чистота обробленої поверхні звичайно знаходиться в межах 2.5 .0.63;
відсутність електрода інструмента;
із збільшенням продуктивності підвищуються чистота поверхні і точність обробки;
необхідність очищення електроліта;
необхідність видалення водню з робочої камери ( при видаленні 1 кг сталі виділяється біля 0.5м3 водню);
висока енергоемність процесу (1000 а.ч на 1 кг знятого металу).
Принципово механізм електрохімічного профілювання перебуває в тому , що поверхня заготовки, зазнаючи електрохімічного розчинення в якості анода, одержує на різних ділянках різну щільність струму , відповідно відстаням від профільного катода. У результаті розчинення на цих ділянках відбувається з різною швидкістю і приводить до утворення профілю, що представляє собою зворотне зображення катода.
Відповідно цій схемі здійснюються всі операції електрохімічного профілювання, копіювання і т.д , що приводять до зміни форми заготовки.
Рис.10. Принципова схема електролітичного осередку і процесу електролізу:
1 - ванна; 2 - електроліт; 3 - катод; 4 – анод
лектроліти для електрохімічної розмірної обробки.
Принципово анодне розчинення може відбуватися в будь-якому електроліті, що утворить із металом добре розчинні у воді з'єднання. Практично найбільш поширені деякі розчини, зокрема розчин хлористого натрію.
Водяний розчин хлористого натрію (повареної солі) придатний для електрохімічної обробки стали 50, ОХНЗМ, 40Х, жароміцних нікелевих сплавів, а при добавці їдкого натра - для обробки металокерамічних вольфрамокобальтових сплавів. Позитивні сторони такого електроліту - низька вартість і тривала працездатність. Останнє пояснюється тим, що хлористий натрій безупинно відновлюється в розчині. При використанні водяних розчинів хлористого натрію для обробки деталей із нержавіючої сталі (наприклад, Х18Н9Т) можливе зниження корозійної стійкості при низьких густинах струму. На інших металах цього не спостерігається.
Для електрохімічної обробки нікелевих сплавів і титана іноді застосовують водяні розчини сірчаної кислоти. Ці розчини забезпечують високу чистоту поверхні і не викликають корозії деталей.
Розчини сірчанокислого натрію придатні для обробки деталей із нержавіючої сталі Х18Н9Т і забезпечують високу швидкість знімання і дзеркальної поверхні виробу.
Електроліти із водяного розчину якої-небудь солі, зокрема хлористого натрію, швидко змінюють свою кислотність (рн) і електропровідність у процесі роботи внаслідок утворення при електролізі лугу і нагромадження її в розчині.
Приклади електрохімічної розмірної обробки.
В даний час електрохімічна розмірна обробка використовується в основному при утворенні отворів і порожнин, профілюванні і формоутворенні копіюванням, видаленні задирок і грата, різанню і довбанні.
Електрохімічна розмірна обробка турбінних лопаток. Принципові схеми двох варіантів операції показані на рис. 11. У першому варіанті (рис. 11, а) заготовка й інструмент протягом всієї операції залишаються нерухомими, а міжелектродний проміжок безупинно збільшується. Цей варіант застосовують головним чином для видалення рівномірного припуску з заготовки, отриманої штампуванням або електроерозійним способом.
Більш поширена обробка рухливими електродами (рис. 11, б). Тут заготовку (анод) установлюють між двома катодами-інструментами, що одержують зустрічне переміщення в напрямку до деталі.
Рuc 11. Принципові схеми електрохімічної обробки турбінних лопаток:
Електрохімічне прошивання отворів і порожнин (свердління, довбання) схематично показані на мал.
Рис. Схема електрохімічного прошивання отворів і порожнин
Електрохімічне утворення кільцевих канавок усередині деталей типу втулок (рис.13). Втулку 1 закріплюють в установочному пристосуванні спеціального двухшпиндельного верстата і підключають до позитивного полюса джерела струму. Усередині деталі встановлюють електрод-інструмент 2, що представляє собою латунний стрижень, покритий на неробочій частині ізоляцією і
з'єднаний із негативним полюсом. Робочу частину електрода-інструмента - неізольоване кільце - установлюють поблизу оброблюваної поверхні.
Рис. 13. Схема електрохімічного утворення кільцевих канавок усередині втулки
У проміжку між електродами (0,4-0,6 мм) із швидкістю 10- 12 м/с протікає електроліт - водяний розчин хлористого натрію. При включенні струму відбувається інтенсивне розчинення частини анодной поверхні, розташованої поблизу робочої частини інструмента, з утворенням кільцевої канавки глибиною 0,2 мм (час обробки 12 сек).
1. Класифікація і особливості електрофізичних та електрохімічних методів обробки
Під загальною назвою електрофізичні та електрохімічні методи обробки матеріалів об'єднані: електрохімічні, электро-хіміко- механічні (анодно-механічні), электроэрозійні, электрогідравлічні, електронно-променеві, плазменні, ультразвукові світлопроменеві і ряд інших методів (див. загальну класифікаційну схему), які відрізняються від механічної обробки різанням або тиском використання в ролі обробного інструмента електричної енергії або специфічних фізичних явищ, створюваних цією енергією.
Дата добавления: 2022-12-03; просмотров: 27; Мы поможем в написании вашей работы! |
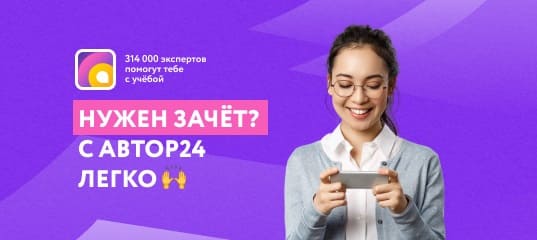
Мы поможем в написании ваших работ!