Подготовка промежуточных ковшей
Промежуточные ковши, подаваемые на разливку, должны иметь исправный кожух, прочищенные выпарные отверстия. В ковшах не должно быть посторонних предметов, отходов огнеупоров на дне и в каналах дозаторов, скрапин на кожухе около дозирующих узлов и на фланцах. Не допускать подачу на разливку промежуточных ковшей с дозирующими узлами, имеющими сколы, трещины. Ответственным за качество подготовки промежуточных ковшей является мастер разливки.
Футеровка промежуточных ковшей не должна иметь трещин или отслоений.
Перед установкой промежуточного ковша на разливочную тележку разливщику с помощью редуктора перевести механизмы центровки тележки в среднее положение по меткам.
Разливщику проверить выставку дозаторов относительно центров кристаллизаторов с помощью калиброванных металлических штырей и отцентровать ковш механизмами центровки тележки.
Разливщикам стали выходные отверстия дозаторов промежуточных ковшей заткнуть снизу металлическими пробками с установленными на концах бумажными трубками, внутренняя полость которых на 1/3 их высоты заполнить стартовой смесью. Смесь не должна окомковываться (оценка визуально).
Промежуточные ковши должны быть накрыты недеформированными, очищенными от скрапа футерованными крышками. На ручьях № 3, 4 должны быть установлены кварцевые вставки высотой 180 мм.
|
|
Разогрев промежуточных ковшей производить разливщику стати па тележке в резервной позиции в соответствии с требованиями ТИ 105-СТ.ЭС-10. Температура рабочей поверхности футеровки промежуточных ковшей должна быть в пределах от 1100 до 1200 °С (разогрев ведется в автоматическом режиме с выводом визуализации температуры на монитор ЭВМ ГПУ МНЛЗ).
Перед запуском МНЛЗ должны быть подготовлены к разливке и исправны все шесть ручьев. Сведения о готовности узлов, механизмов и систем к разливке передавать оператору главного поста управления (ГПУ), который поддерживает постоянную связь со сталеварами УПК и в случае задержки в подготовке МНЛЗ докладывает мастеру МНЛЗ.
5.2
Изм. |
Лист |
№ докум. |
Подпись |
Дата |
Лист |
17 |
ОПП-150101-71913106-41 |
Основными условиями осуществления стабильного процесса непрерывной разливки являются:
- Своевременная подача на разливку металла, выплавленного в шахтной печи
и обработанного в соответствии с действующими технологическими инструкциями
|
|
и операционными картами.
- Тщательная подготовка к приему плавки сталеразливочных и промежуточных ковшей в соответствии с действующими технологическими инструкциями.
· Подготовка и проверка всех узлов, механизмов и контрольно-измерительных приборов (КИП) МНЛЗ перед разливкой в соответствии с действующими технологическими инструкциями.
· Выполнение в процессе разливки требований настоящей инструкции и инструкций по охране труда.
· Требования к газообразному аргону установлены в ТИ 105-СТ.ЭС-55 «Эксплуатация и ремонт трубопроводов и оборудования, работающих с продуктами разделения воздуха электросталеплавильного цеха».
Перед установкой промежуточного ковша над кристаллизаторами произвести следующие операции:
· Операторам МНЛЗ включить насосы подачи воды на кристаллизаторы и вторичное охлаждение, проверить отсутствие воды в аварийной емкости, включить воду на охлаждение оборудования. Запрещается запуск ручья МНЛЗ при расходе воды на охлаждение кристаллизатора менее 50 м3/'ч и при неисправных приборах КИПиА для контроля расхода и давления воды.
· Уточнить на дисплее передачу информации о плавке, давлении воды, температуры и расхода воды на входе в кристаллизатор
|
|
· Проверить готовность всех механизмов с визуализации на мониторе компьютера.
· Оператору ГПУ ввести в ЭВМ номер плавки, код марки стали, длину мерного реза заготовок.
· Оператору МНЛЗ установить расходы воды на кристаллизаторы и зоны вторичного охлаждения, а также расход синтетического разливочного масла, в соответствии с параметрами операционных карт.
По команде мастера МНЛЗ начинается разливка стали из стальковша. После наполнения промковша открываются стопора и производится наполнение кристаллизатора жидким металлом. При наполнении кристаллизатора металлом до уровня 120-150 мм от верхней
Изм. |
Лист |
№ докум. |
Подпись |
Дата |
Лист |
18 |
ОПП-150101-71913106-41 |
|
|
При разливке на МНЛЗ для защиты металла от взаимодействия с окружающей средой применяется специальная шлакообразующая смесь (С – 15-20%; CaO – 26,0-32,0%; SiO2 – 30,0-36,0%; Al2O3 – 6,5-8,0%; F – 4,0-4,5%; Na+ - 3,5-4,0%; K+ - 0,7-1,0%). Подача шлакообразующей смеси производится следующим образом:
- при стабильной разливке по мере расходования защитной смеси новые небольшие порции равномерно засыпают по поверхности ранее образованного слоя смеси. Толщина шлакового покрова в кристаллизаторе поддерживается в пределах 30 мм.
- При остановках машин или продолжительной разливке со скоростью менее или равной 0.3 м/мин. толщину слоя защитной засыпки кратковременно увеличивают. После этого проверяется отсутствие под защитным покровом плавающей металлической корочки, которую удаляют при её наличии.
- Запрещается перемешивать слой защитной смеси с поверхностным слоем жидкого металла, также не допускается бурление металла в кристаллизаторе и его оголение.
При окончании разливки плавки закрывается шиберное устройство сталеразливочного ковша. Поворотом подъемно-поворотного стенда ковш переедается в раздаточный пролет для кантовки шлака и дальнейшей обработки. Скорость разливки плавно снижается до 0.3-0.4 м/мин. и заканчивается разливка из промковша.
Раскрой непрерывного слитка производится в соответствии с заказами в зависимости от того, на каком стане будет проходить дальнейшая обработка заготовки. Длины заготовок установлены следующие: 1820 мм; 1900мм; 1950 мм. Для увеличения ресурса работы ножниц, длина порезки слитка может быть увеличена вдвое с последующей порезкой таких слитков кислородом.
Изм. |
Лист |
№ докум. |
Подпись |
Дата |
Лист |
19 |
ОПП-150101-71913106-41 |
1- ковш; 2- промежуточное разливочное устройство; 3- кристаллизатор; 4- затвердевающий слиток; 5- тянущие валки; 6- форсунки; 7- зона резки; 8- газовый резак
Рисунок 1 – Схема машины непрерывного литья заготовок
Порезанные на МНЛЗ заготовки маркируются и передаются в термообрубное отделение. В термообрубном отделении заготовки охлаждаются до температуры окружающей среды; производится отбраковка заготовок. В случае поступления заготовок нестандартной длины производится их резка на заготовки требуемой длины.
Разливка стали на УНРС
Разливку стали (открытие шибера) начинать по команде старшего разливщика. В нижнем положении сталеразливочного ковша на стенде полностью открыть шиберный затвор. Проверку работы шиберного затвора на полное перекрытие струи производить после наполнения промежуточного ковша на 1/2 его высоты (оценка визуально). Разливщикам стали на ручьях открыть в ручном режиме стопор и начать наполнение металлом кристаллизатора. Включить подачу воды в систему вторичного охлаждения слитка и на охлаждение оборудования. Объемный расход воды поддерживать с помощью АСУ ТП в соответствии с заданной программой. Опробование крытая
Изм. |
Лист |
№ докум. |
Подпись |
Дата |
Лист |
20 |
ОПП-150101-71913106-41 |
Первые порции смеси давать в районе стопора, остальную массу смеси - в район металлоприемника после погружения нижнего среза трубы в жидкий металл.
Разливщику стали зеркало металла в промежуточном ковше засыпать защитной шлакообразующей смесью.
Уровень металла в промежуточном ковше после проверки работы шиберного затвора и крытая стопора разливщику на отметке «+14 м» довести до рабочего уровня (не ниже 150 мм от верхнего среза ковша, оценка визуально). Стенд со сталеразливочным ковшом опустить в крайнее нижнее положение. Разливщикам стали произвести регулировку подачи аргона на сталеразливочный ковш и стопор-моноблок. При этом объемный расход газа устанавливается до небольшого «пробулькивания» газа в месте погружения трубы, но без оголения металла пекле расплавления смеси, а также небольшое «пробулькивание» газа в месте погружения погружного стакана в кристаллизаторе, но без оголения зеркала металла после расплавления смеси (оценка объемного расхода аргона визуально).
Подержание рабочего уровня металла в промежуточном ковше, контролирует разливщик, управляющий шиберным затвором. Не допускается снижение рабочего уровня. В переходных режимах при разливке «плавка на плавку» допускается снижение уровня металла в промежуточном ковше, но не ниже чем до 1/3 его высоты.
Разливщику стали наполнение кристаллизатора производить не быстрее, чем за 40 с с подтормаживанием струи. Уровень металла в кристаллизаторе постепенно довести до рабочего (50-100 мм от верхней кромки, оценка визуально).
Начальная скорость разливки 0,2 м/мин. Оператору ПУ-1 плавно увеличить скорость до рабочей в течение 1,0-1,5 минут (оценка визуально): скорость разливки увеличивать на 0,1 м/мин через каждые 10-15 секунд (оценка визуально). Разливщику стаж ручья задавать шлакообразующую смесь в кристаллизатор небольшими порциями, рассыпая по всему зеркалу металла. Смесь задавать отпарированными совками только после заглубления в металл верхней кромки выходных отверстий погружного стакана.
Объемный расход аргона подаваемого на погружной стакан (стопор-моноблок) после выхода на рабочую скорость, регулирует разливщик стали. Объемный расход поддерживается от 10 до 40 л/мин (от 3 до 15 делений шкалы ротаметра РМ-5, установленного на отметке УНРС «+12 м»). В процессе разливки периодически контролировать поступление аргона в систему защиты на участке промежуточный ковш - кристаллизатор путем кратковременного повышения расхода аргона. При появлении
Изм. |
Лист |
№ докум. |
Подпись |
Дата |
Лист |
21 |
ОПП-150101-71913106-41 |
Перепад температур охлаждающей воды на входе и выходе с каждой стенки кристаллизатора не должен превышать 10 °С. При стабильной разливке по мере расходования защитной смеси равномерно рассыпать ее новые небольшие порции по поверхности металла в кристаллизаторе, поддерживая состояние «черного мениска» и не допуская видимого проплавления смеси (оценка визуально). При этом не допускать:
• бурления и оголения мениска металла в кристаллизаторе;
• перемешивания слоев шлаковой засыпки с поверхностным слоем металла;
• подачи смеси «навалом» на любой участок поверхности металла.
Периодически проверять наличие грубых шлаковых корок (гарнисажа) в углах и около стенок кристаллизатора и удалять их по мере образования кислородной трубкой длиной 1,8-2,0 м.
В процессе разливки непрерывнолитые слябы на внешней МГР УНРС разрезать на мерные длины согласно заказов Дирекции по производству. Порезку производит оператор в следующем порядке:
· Оператору ПУ-2 после отрезания затравки настроить прибор мерного реза (ПМР-2) для порезки слябов длиной от 4500 до 8500 мм в зависимости от заданного раскроя.
· При расчете длины отрезаемого сляба учитывать припуск на усадку по 10мм на каждый метр длины горячего сляба и припуск на каждый рез на внутренней и внешней газорезке по 20 мм. Например, при заданном раскрое 4000 мм расчет производить в следующем порядке:
4000 мм + 4000 мм + 20 мм + 20 мм + 10 х 8 мм = 8120 мм.
На приборе регистрации мерной длины задать 8120 мм.
Резаки подвести и остановить у края заготовки. Порезку заготовки производить двумя резаками с двух сторон навстречу друг другу. В случае необходимости порезку можно производить одним резаком.
После окончания поступления металла из сталеразливочного ковша разливщику закрыть шиберный затвор, снять с шибера гидроцилиндр и с помощью крана передать ковш в пролет для слива шлака в шлаковую чашу, после чего ковшевому оценить состояние футеровки (оценка визуально).
Изм. |
Лист |
№ докум. |
Подпись |
Дата |
Лист |
22 |
ОПП-150101-71913106-41 |
Схема установки непрерывной разливки стали представлена на рисунке 2.
1 — сталеразливочный ковш; 2 — промежуточный ковш (предназначен для снижения и стабилизации напора металла, поступающего в кристаллизатор, и для распределения металла по нескольким кристаллизаторам на многоручьевых установках); 3 — кристаллизатор; 4 — зона вторичного охлаждения с устройствами для направления заготовки и подачи воды; 5 — тянущие валки; 6 — слиток; 7 — устройство для разрезки заготовки (кислородные резаки или ножницы); 8 — устройство для выдачи заготовки.
Рисунок 2 – Схема установки непрерывной разливки стали.
Разливщику стали отключить систему автоматического поддержания уровня (АПУ) и вручную закрыть стопор, убрать с ручья датчик АПУ, снять погружной стакан, промежуточный ковш перевести в положение над шлаковней для слива шлака. В
Изм. |
Лист |
№ докум. |
Подпись |
Дата |
Лист |
23 |
ОПП-150101-71913106-41 |
Металл в кристаллизаторе металлическим прутком интенсивно перемешать до появления усадки, механизм качания кристаллизатора выключить.
Вывод сляба из кристаллизатора производить со скоростью 0,1 м/мин с расходом воды на вторичное охлаждение, установленным для скорости 0,2 м/мин.
Изм. |
Лист |
№ докум. |
Подпись |
Дата |
Лист |
24 |
ОПП-150101-71913106-41 |
Улучшение показателей работы и снижение себестоимости стали в электросталеплавильном производстве имеет большое значение для повышения экономической эффективности работы металлургического предприятия.
Основными составляющими себестоимости 1т слитков (литой заготовки) являются: стоимость основных материалов, расходуемых на плавку, - металлической шихты, раскислителей и легирующих добавок (ферросплавов); стоимость добавочных материалов (железной руды иди агломерата, извести, доломита, магнезита, плавикового шпата, кокса, древесного угля, шамота и др.); расходы по переделу (по процессу выплавки, внепечной обработки и разливки стали), которые складываются из стоимости технологического топлива, энергетических затрат, стоимости электродов, пара, воды, огнеупоров, изложниц, вспомогательных материалов, запасных частей и амортизационных отчислений, а также из заработной платы.
К технологическому топливу относят электроэнергию, мазут, коксовый, доменный и природный газ для отапливания нагревательных печей и устройств (сушка и нагрев ковшей, надставок, центровых и др.). Энергетические затраты учитывают стоимость технологической электроэнергии и энергии, расходуемой на электродвигатели (механизмы поворота печи, перемещения электродов, движения фурм и пр.), а также затрат на производство пара, сжатого воздуха и воды.
При выплавке в дуговых печах низколегированных сталей почти половину себестоимости слитков составляют стоимость передела и общезаводские расходы. При выплавке легированной и высоколегированной стали удельный вес металлической шихты, раскислителей и легирующих добавок возрастает соответственно до 80 и 95%, а стоимость передела и общезаводские расходы уменьшаются до незначительной величины (20...5)%.
Важным резервом снижения себестоимости слитков является дальнейшее уменьшение расхода ферросплавов путем точного взвешивания, рационального использования отходов собственного производства и привозного лома легированных сталей и сплавов; выплавки металла с содержанием легирующих элементов ниже среднего заданного предела; широкой применения внепечной обработки, обеспечивающей минимальные угары легирующих элементов; повышения выхода годного путем сокращения брака, литников, скрапа и недоливков.
В стоимости передела заметную роль играют накладные расходы, подразделяемые на цеховые, общезаводские и внепроизводственные (коммерческие). Уменьшение расходов по переделу, и в частности накладных расходов, способствует снижению себестоимости стали и сплавов. Номенклатура накладных цеховых расходов имеет следующий вид: зарплата цехового персонала с начислениями (инженерно-технические
Изм. |
Лист |
№ докум. |
Подпись |
Дата |
Лист |
25 |
ОПП-150101-71913106-41 |
Накладные общезаводские расходы включают заработную плату работникам заводоуправления и начисления на нее; подъемные при перемещении работников с предприятия; расходы по командировкам; конторские и. почтово-телеграфные расходы; содержание легкового транспорта; содержание и амортизация зданий, конторских помещений и инвентаря заводоуправления; содержание зданий, сооружений и инвентаря общезаводского назначения, заводских складов, общезаводских лабораторий и т.д., расходы по рационализации и изобретательству, разные обязательные отчисления, налоги и сборы; текущие ремонты; расходы по испытаниям и исследованиям; расходы по специальным видам охраны предприятия; расходы по охране труда и благоустройству; расходы по производственному обучению и производственной практике учащихся школ и студентов; прочие расходы.
К внепроизводственным (коммерческим) расходам относят отчисления на финансирование научно-исследовательских работ; затраты на содержание вне заводских базисных складов и перевалочных пунктов; отчисления на подсобное хозяйство; стоимость погрузки и перевозки металлопродукции к месту сбыта.
Снижения накладных расходов и себестоимости продукции достигают сокращением непроизводительных затрат (штрафы за перепростой вагонов, пени и неустойки по договорам, недостача материалов и пр.); снижением до минимума административно-управленческих расходов (уменьшение командировок, сокращение управленческого персонала, экономия канцелярских товаров и пр.); уменьшением расходов на погрузочно-разгрузочные работы путем их механизации и роботизации и более рационального использования всех видов транспорта для перевозки материалов (использование автомобильного и водного транспорта, широкое применение контейнеров и т.п.).
Эффективными мероприятиями в снижении себестоимости являются переход электросталеплавильных цехов и отдельных участков на хозяйственный расчет и организация малых предприятий. При этом повышается личная материальная заинтересованность работников цеха и участков в экономном расходовании средств и материалов.
Изм. |
Лист |
№ докум. |
Подпись |
Дата |
Лист |
26 |
ОПП-150101-71913106-41 |
ПОКАЗАТЕЛИ | ДЕКАБРЬ | 2006 | ||||
ФУКС 1 | ФУКС 2 | Цех | ФУКС 1 | ФУКС 2 | Цех | |
СДАЧА | ||||||
ПЛАН, т | 90 000 | 88 000 | 178 000 | 1 024 000 | 976 000 | 2 000 000 |
ФАКТ, т | 91 597,585 | 92 006,712 | 183 604,297 | 1 007 719,487 | 947 105,415 | 1 954 824,902 |
ОТКЛОНЕНИЕ, т | 1 597,585 | 4 006,712 | 5 604,297 | -16 280,513 | -28 894,585 | -45 175,098 |
% ВЫПОЛНЕНИЯ | 101,78 | 104,55 | 103,15 | 98,41 | 97,04 | 97,74 |
незав. на нач. месяца | 691,131 | 6 667,082 | 7 358,213 | |||
в т.ч. товара | ||||||
незав. на конец месяца | 1 254,147 | 5 162,223 | 6 416,370 | |||
в т.ч. товара | ||||||
адъюстаж: незав. на нач. мес. | 497,460 | |||||
адъюстаж: незав. на кон. мес. | 1 280,512 | |||||
ВЫПЛАВКА | ||||||
ПЛАН, т | 90 000 | 88 000 | 178 000 | 1 026 000 | 978 000 | 2 004 000 |
ФАКТ, т | 92 160,601 | 90 501,853 | 182 662,454 | 1 006 357,454 | 948 345,904 | 1 954 703,358 |
ОТКЛОНЕНИЕ, т | 2 160,601 | 2 501,853 | 4 662,454 | -19 642,546 | -29 654,096 | -49 296,642 |
% ВЫПОЛНЕНИЯ | 102,40 | 102,84 | 102,62 | 98,09 | 96,97 | 97,54 |
Обработка на УПК | 88 639,400 | 94 023,054 | 182 662,454 | 980 800,791 | 973 902,567 | 1 954 703,358 |
Обработка на УВС | 73 697,234 | 659 485,754 | ||||
ОТЖИГ | 9 758,563 | 115 767,634 | ||||
БРАК, т | 1 185,171 | 11 481,412 | ||||
% БРАКА | 0,65 | 0,59 | ||||
СДАЧА | ||||||
СЛЯБЫ | 9 642,551 | 86 609,997 | 96 252,548 | 112 070,853 | 865 137,506 | 977 208,359 |
СОРТ 100 | 60 207,125 | 4 205,914 | 64 413,039 | 723 821,217 | 67 569,180 | 791 390.397 |
СОРТ 150 | 21 747,909 | 1 190,801 | 22 938,710 | 171 827,417 | 14 398,729 | 186 226.146 |
ВЫПЛАВКА | ||||||
СЛЯБЫ | 10 148,567 | 84 923,898 | 95 072,465 | 112 559,133 | 866 366,074 | 978 925,207 |
СОРТ 100 | 60 207,125 | 4 205,914 | 64 413,039 | 723 821,217 | 67 488,308 | 791 309,525 |
СОРТ 150 | 21 804,909 | 1 372,041 | 23 176,950 | 169 977,104 | 14 491,522 | 184 468,626 |
ОСЕДАНИЕ (СЛЯБЫ) ТОВАРНЫЕ СЛЯБЫ ТОВАРНЫЕ СОРТ. ЗАГОТОВКИ |
| 121,025 | ||||
15 002,922 |
Таблица 3 – Показатели выплавки
ПОКАЗАТЕЛИ | ЕД. ИЗМ | ДЕКАБРЬ | 2006 | ||||||||||||
ПЕЧЬ 1 | ПЕЧЬ 2 | ИТОГО | ПЕЧЬ 1 | ПЕЧЬ 2 | ИТОГО | ||||||||||
Выплавка | тн | 92160,601 | 90501,853 | 182662,454 | 1006357,454 | 948345,904 | 1954703,358 | ||||||||
Количество плавок | пл | 760 | 747 | 1507 | 8377,000 | 7894,000 | 16271,000 | ||||||||
Календарное время | сут. | 31 | 31 | 62 | 350,570 | 352,190 | 702,760 | ||||||||
Холодные простои | сут. | 1,29 | 1,93 | 3,22 | 21,820 | 24,530 | 46,350 | ||||||||
Номинальное время | сут. | 29,71 | 29,07 | 58,78 | 328,750 | 327,660 | 656,410 | ||||||||
Горячие простои | сут. | 2,04 | 1,15 | 3,19 | 33,590 | 32,940 | 66,530 | ||||||||
Фактическое время | сут. | 27,67 | 27,92 | 55,59 | 295,160 | 294,720 | 589,880 | ||||||||
Фактическое время | час. | 664,08 | 670,08 | 1334,16 |
| 7073,280 | 14157,120 | ||||||||
Выплавка в кал.сутки | тн | 2972,92 | 2919,41 | 5892,34 | 2870,63 | 2692,71 | 5563,34 | ||||||||
Среднее значение | 2946,17 | 2781,47 | |||||||||||||
Выплавка в факт.сутки | тн | 3330,70 | 3241,47 | 3285,89 | 3409,53 | 3217,79 | 3313,73 | ||||||||
Средний вес плавки | тн | 121,26 | 121,15 | 121,21 | 120,13 | 120,14 | 120,13 | ||||||||
Длительность плавки | мин | 52,43 | 53,82 | 53,12 | 50,74 | 53,76 | 52,20 | ||||||||
Время под током | мин | 34,22 | 32,98 | 33,60 | 32,46 | 32,128 | 32,32 | ||||||||
Бестоковая пауза | мин | 18,21 | 20,84 | 19,52 | 18,28 | 21,63 | 19,89 | ||||||||
Время под током за месяц | час. | 433,45 | 410,60 | 843,92 | 4531,778 | 4226,989 | 8764,356 | ||||||||
Расход жидкого чугуна | кг/т | 185,94 | 175,190 |
Таблица 4 – Брак по печам
ВИДЫ БРАКА | ДЕКАБРЬ | 2006 | ||||||
Печь 1 | ФУКС 2 | ФУКС 1 | ИТОГО | Печь 1 | ФУКС 2 | ФУКС 1 | ИТОГО | |
| СЛИТКИ | |||||||
БЛЮМИНГА | ||||||||
АВАРИЙНЫЙ | ||||||||
СКРАПА | ||||||||
СТРИППЕРА | ||||||||
| СЛЯБЫ | |||||||
ЛПЦ-1 | 50,521 | 50,521 | 524,783 | 524,783 | ||||
ЛПЦ-2 | 54,640 | 54,640 | ||||||
ЛПЦ-3 | ||||||||
БЛЮМИНГА | ||||||||
АВАРИЙНЫЙ | 2,000 | 2,000 | 136,000 | 136,000 | ||||
СКРАПА | 103,000 | 103,000 | ||||||
СЛЯБА | 389,868 | 389,868 | 3 952,281 | 3 952,281 | ||||
| СОРТОВАЯ | |||||||
АВАРИЙНЫЙ | 70,000 | 70,000 | 326,000 | 326,000 | ||||
СКРАПА | 50,000 | 50,000 | ||||||
СЛЯБА | 672,782 | 672,782 | 6 334,708 | 6 334,708 | ||||
БЛЮМИНГА | ||||||||
ИТОГО | 1 185,171 | 1 185,171 | 11 481,412 | 11 481,412 | ||||
% | 0,65 | 0,59 |
Таблица 5 – Всего простоев
ПОКАЗАТЕЛИ | ед. изм. | ДЕКАБРЬ | 2006 | ||||
Печь№1 | Печь№2 | Итого | Печь№1 | Печь№2 | Итого | ||
ВРЕМЯ ПО КАЛЕНДАРЮ | ч:м:с | 744:00:00 | 744:00:00 | 1488:00:00 | 8759:00:00 | 8759:00:00 | 17518:00:00 |
КАПИТАЛЬНЫЙ РЕМОНТ | ч:м:с | 0:00:00 | 0:00:00 | 0:00:00 | 345:21:00 | 306:37:00 | 651:58:00 |
сут. | 0,00 | 0,00 | 0,00 | 14,39 | 12,78 | 27,17 | |
РЕЗЕРВ | ч:м:с | 12:31:00 | 13:20:00 | 25:51:00 | 80:38:00 | 50:25:00 | 131:03:00 |
сут. | 0,52 | 0,56 | 1,08 | 3,36 | 2,10 | 5,46 | |
КАЛЕНДАРНОЕ ВРЕМЯ | ч:м:с | 744:00:00 | 744:00:00 | 1462:09:00 | 8413:39:00 | 8452:23:00 | 16866:02:00 |
31,00 | 31,00 | 60,92 | 350,57 | 352,18 | 702,75 | ||
ИТОГО ПРОСТОЕВ | ч:м:с | 79:53:00 | 74:00:00 | 153:53:00 | 1306:18:00 | 1377:53:00 | 2684:11:00 |
сут. | 3,33 | 3,08 | 6,41 | 54,43 | 57,41 | 111,84 | |
в % к календарю | % | 10,74 | 9,95 | 10,52 | 15,53 | 16,30 | 15,91 |
ХОЛОДНЫЕ ПРОСТОИ | ч:м:с | 30:57:00 | 46:24:00 | 77:21:00 | 524:55:00 | 620:26:00 | 1145:21:00 |
сут. | 1,29 | 1,93 | 3,22 | 21,87 | 25,85 | 47,72 | |
в % к календарю | % | 4,16 | 6,24 | 5,29 | 6,24 | 7,34 | 6,79 |
ГОРЯЧИЕ ПРОСТОИ | ч:м:с | 48:56:00 | 27:36:00 | 76:32:00 | 781:23:00 | 757:27:00 | 1538:50:00 |
сут. | 2,04 | 1,15 | 3,19 | 32,56 | 31,56 | 64,12 |
Изм. |
Лист |
№ докум. |
Подпись |
Дата |
Лист |
28 |
ОПП-150101-71913106-41 |
Изм. |
Лист |
№ докум. |
Подпись |
Дата |
Лист |
29 |
ОПП-150101-71913106-41 |
В ходе производственной практики, наглядно получено представление о сталеплавильных процессах в электросталеплавильном цехе ОАО «Северсталь». Ознакомились с принципом работы цеха, с методами выплавки на электропечах, разливки стали на сортовой МНЛЗ и слябовой УНРС, технологию внепечной обработки металла.
Также были получены технико-экономические показатели работы электросталеплавильного цеха.
Изм. |
Лист |
№ докум. |
Подпись |
Дата |
Лист |
30 |
ОПП-150101-71913106-41 |
1. Явойский В.И.. Металлургия стали [Текст] / Явойский В.И., Кряковский Ю.В., Григорьев В.П. – М.: Металлургия.-1983.-584с. |
2. Воскобойников В.Г. Общая металлургия: Учебник для вузов- 4-е изд., перераб. и доп.[Текст]/ Воскобойников В.Г., Кудрин В.А., Якушев А.М. – М., «Металлургия», 1985. 480 с. |
3. ТИ 105-СТ.ЭС – 36 – 2010 |
4. ТИ СТ.ЭС – 05 – 2009 |
5. ТИ 105 – СТ.ЭС – 22 – 2007 |
Дата добавления: 2022-12-03; просмотров: 88; Мы поможем в написании вашей работы! |
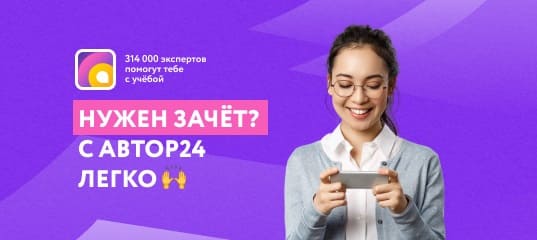
Мы поможем в написании ваших работ!